四氯化硅制备三氯氢硅的冷氢化工艺资料
冷氢化工艺技术方案(成品版-修改)
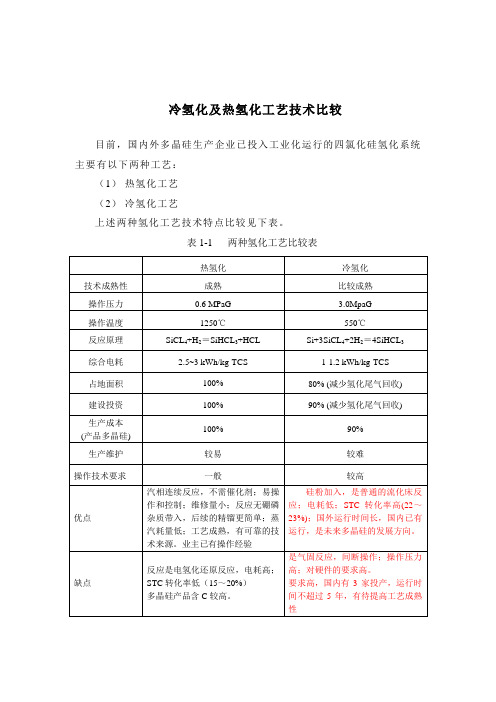
冷氢化及热氢化工艺技术比较目前,国内外多晶硅生产企业已投入工业化运行的四氯化硅氢化系统主要有以下两种工艺:(1)热氢化工艺(2)冷氢化工艺上述两种氢化工艺技术特点比较见下表。
表1-1 两种氢化工艺比较表综上比较,这二者各有其特点。
考虑到低能耗、投资省的优势,建议2.冷氢化工艺技术说明2.1 冷氢化工序原料及装置配置说明冷氢化工序原料来源有以下两种:(1)以外购四氯化硅(STC)为原料,以下简称Case1。
(2)以外购硅粉、液氯为原料、只转化多晶硅装置内部四氯化硅(STC),以下简称Case2。
上述两种原料来源所需多晶硅装置配置的生产工序见下表。
表2-1两种冷氢化来源生产工序配置对照表备注1:粗馏是与精馏相对设立的工序,主要用于处理自冷氢化工序出来的杂质含量比较高的氯硅烷,将其提纯到送入精馏工序作进一步处理的纯度要求。
将粗馏和精馏分开设置的原因是基于冷氢化工序出来的氯硅烷和还原单元返回的氯硅烷是否混合,可根据客户的要求采取灵活的不同精馏工艺路线而设置。
考虑本项目与国内中、东部地区从多的多晶硅生产企业不同,其周边仅有的几家多晶硅生产企业都建设有热氢化单元(如鄂尔多斯多晶硅业有限公司)和冷氢化单元(如内蒙峰威多晶硅业有限公司),没有多余的STC外卖,而长距离外运STC作原料既不可靠,经济上也不合理。
因此,本报告建议二期工程采用以外购硅粉、液氯为原料,只转化多晶硅装置内部四氯化硅(STC)的工艺路线。
本项目二期工程2500吨/年太阳能级多晶硅装置以外购四氯化硅(STC)为原料的总物料平衡图见附图1。
本项目二期工程2500吨/年太阳能级多晶硅装置以以外购硅粉、液氯为原料、只转化多晶硅装置内部四氯化硅(STC)的总物料平衡图见附图2。
2.2 冷氢化单元主要组成冷氢化单元由以下主要工序组成:(1)冷氢化工序(2)粗馏工序(3)配套的中间罐区2.3 冷氢化单元工艺流程简述(1)冷氢化工序工业级硅粉送至硅粉干燥器,干燥后排入硅粉中间仓。
冷氢化技术

冷氢化技术综述(上)20世纪70年代美国喷气推进实验室(JPL)在美国能源部的支持下组织研究新硅烷法工艺过程中,采用多晶硅工厂的副产物四氯化硅(STC)作原料,将其转化为三氯氢硅(TCS),然后将三氯氢硅通过歧化反应生产硅烷。
80年代初,为得到低成本、高纯度的多晶硅,又进行了一系列的研究开发。
其中高压低温氢化工艺(以下简称冷氢化)就是一项能耗最低、成本最小的STC 转化为TCS的工艺技术。
该工艺被UCC(Union Carbide Corporation)公司在80年代中后期进一步的完善,实现了从实验装置到工业化运行的跨越,目前REC 在华盛顿州的多晶硅工厂所采用的此项工艺仍在运行中。
因此,毋庸置疑,冷氢化技术的原创应当是UCC,目前流行的各类流化床冷氢化工艺只是在UCC的基础上“整容,而非变性”(易中天语)!90年代,为了提高多晶硅产品纯度,满足电子工业对多晶硅质量的要求,开发了高温低压STC氢化工艺,这两种工艺的比较如下:综上比较,二者各有优缺点,但低温高压冷氢化工艺耗电量低,在节能减排、降低成本方面具有一定的优势。
国内多晶硅新建及改、扩建单位可以根据项目的具体情况、自身的优势及喜好,择优选定。
冷氢化主要反应式如下:Si+ 2H2 + 3SiCl4 < 催化剂 > 4SiHCl3 (主反应)SiCl4+Si+2H2 = 2SiH2Cl2 (副反应)2SiHCl3 = SiCl4+SiH2Cl2 (副反应)典型的冷氢化装置组成如下:一个完整的冷氢化系统大致包括以下6大部分:1、技术经济指标:包括,1)金属硅、催化剂、补充氢气、STC、电力的消耗,2)产品质量指标,3)STC转化率,4)公用工程(氮气、冷却水、冷媒、蒸汽及导热油);2、主装置:包括,1)流化床反应器、2)急冷淋洗器,3)淋洗残液的处理系统,4)气提,5)加热及换热装置;3、原料系统:包括,1)硅粉输送,2)催化剂选用及制备,3)原料气体的加热装置;4、粗分离系统:包括,1)脱轻,2)脱重,3)TCS分离;5、热能回收系统,包括:1)流化床出口氢化气的热量回收,2)急冷塔出口淋洗气的热能回收,氯硅烷物流热量综合利用;热能回收系统,包括:1)流化床出口氢化气的热量回收,2)急冷塔出口淋洗气的热能回收;6、物料处置及回收系统:包括,1)淋洗残液中的氯硅烷回收,2)脱重塔残液中的氯硅烷回收,3)轻组分中的氯硅烷回收,4)固废处理,5)氯硅烷废液处理。
四氯化硅催化氢化制备三氯氢硅

四氯化硅催化氢化制备三氯氢硅龙雨谦;刘颖颖;叶龙泼;付勰;蒋炜;周齐岭;梁斌【摘要】Using HZSM-5 as the support and different metal chlorides as the active components, the different supported catalysts for hydrogenation of silicon tetrachloride to trichlorosilane were prepared by impregnation method. The as-prepared catalysts were characterized by XRD,XPS and BET. The activity of the catalysts was investigated. The results showed that the chlorides of alkaline earth metal, especially barium, exhibited better catalytic activity for the hydrogenation of silicon tetrachloride; the maximum conversion of silicon tetrachloride of 20. 22% and the highest selectivity to trichlorosilane of 83. 01% were attained under the condition of reaction temperature 850℃ and BaCl2 loading 1 % ( mass fraction).%针对四氯化硅氢化反应,采用等体积浸渍法制备了以HZSM-5为载体,金属氯化物为活性组分的负载型四氯化硅氢化反应催化剂,考察了催化剂的催化性能,并进行了相应表征.结果表明,碱土金属氯化物对四氯化硅氢化过程有良好的催化效果,在BaCl2负载质量分数为1%和反应温度850℃条件下,反应最高转化率为20.20%,选择性83.01%.【期刊名称】《工业催化》【年(卷),期】2012(020)008【总页数】5页(P26-30)【关键词】催化化学;四氯化硅;催化氢化;HZSM-5;三氯氢硅;活性评价【作者】龙雨谦;刘颖颖;叶龙泼;付勰;蒋炜;周齐岭;梁斌【作者单位】四川大学化工学院四川省多相流传质与化学反应工程重点实验室,四川成都610065;四川大学化工学院四川省多相流传质与化学反应工程重点实验室,四川成都610065;中国成达工程有限公司,四川成都610041;四川大学化工学院四川省多相流传质与化学反应工程重点实验室,四川成都610065;中国成达工程有限公司,四川成都610041;四川大学化工学院四川省多相流传质与化学反应工程重点实验室,四川成都610065;中国成达工程有限公司,四川成都610041;四川大学化工学院四川省多相流传质与化学反应工程重点实验室,四川成都610065【正文语种】中文【中图分类】O643.36;TQ426.6多晶硅是目前最主要的光伏材料,生产工艺主要为改良西门子法,每生产1 t多晶硅副产15 t以上的四氯化硅[1]。
三氯参考资料氢硅、四氯化硅相关反应
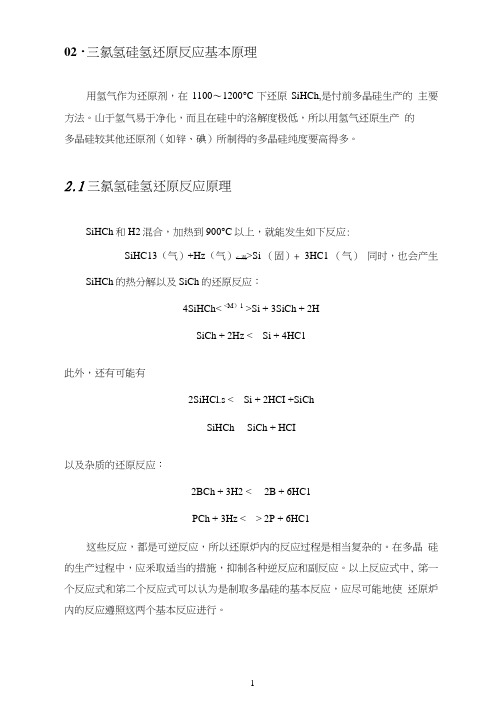
02・三氯氢硅氢还原反应基本原理用氢气作为还原剂,在1100〜1200°C下还原SiHCh,是忖前多晶硅生产的主要方法。
山于氢气易于净化,而且在硅中的洛解度极低,所以用氢气还原生产的多晶硅较其他还原剂(如锌、碘)所制得的多晶硅纯度要高得多。
2.1三氯氢硅氢还原反应原理SiHCh和H2混合,加热到900°C以上,就能发生如下反应:SiHC13(气)+Hz(气)< 观>Si (固)+ 3HC1 (气)同时,也会产生SiHCh的热分解以及SiCh的还原反应:4SiHCh< <M)1 >Si + 3SiCh + 2HSiCh + 2Hz <__Si + 4HC1此外,还有可能有2SiHCl.s <__Si + 2HCI +SiChSiHCh __SiCh + HCI以及杂质的还原反应:2BCh + 3H2 <__ 2B + 6HC1PCh + 3Hz <__> 2P + 6HC1这些反应,都是可逆反应,所以还原炉内的反应过程是相当复杂的。
在多晶硅的生产过程中,应釆取适当的措施,抑制各种逆反应和副反应。
以上反应式中, 笫一个反应式和笫二个反应式可以认为是制取多晶硅的基本反应,应尽可能地使还原炉内的反应遵照这两个基本反应进行。
四氯化硅来源与性质四氯化硅氢化1.1四氯化硅的产生在多晶硅生产过程中,在SiHCh合成工序和氢还原制取多晶硅工序,会产生大量的副产物SiCh,并随着尾气排出。
在氢还原工序中,会发生以下儿个反应:主反应:SiHCh + H2——3HC1+Si副反应:4SiHCh 呦以I > Si + 3SiCh + 2H2SiHCls——Si + 2HCI + SiCh在SiHCh合成工序中主要发生以下反应:主反应:Si + 3HCI ——SiHCh + H2副反应:Si + 4HC1 ——> SiCh + 2HiSiHCh合成中副反应产生的SiCk约占生成物总量的约10% ,在氢还原工序中也有部分SiHCh发生副反应生成了SiCh 0在实际生产中,副反应不可避免,但对工艺过程加以控制,可以尽量减少副反应发生,减少副产物的生成。
四氯化硅制备三氯氢硅新工艺研究

硅 ,不 经过 任 何 处理 , 那 将 会 对 环境 造 成 严 重 污染 。 因
此, 处理 四氯 化硅 的技 术受 到全 世 界的 广泛 关注 。
S i C I + 2 H _ H c l + s i H c 1 ,直 接将 四பைடு நூலகம் 化硅 还 原生 成三 氯
1 四氯 化硅 制备 三 氯氢 硅 的技 术分 析
第3 3 卷 第5 期
2 01 3 年1 0 月
山 西 化
工
V01 . 3 3 N o. 5
0Ct.201 3
SHANXI CHEMICAL I NDUSTRY
科 技 与 开 发
四 氯 化 硅 制 备 三 氯 氢 硅 新 工 艺 研 究
程 永 高
( 邢 台职业技术 学院资源与环境 系,河北 邢 台 0 5 4 0 3 5 )
该热 氢化 技 术 ,目前 国 内多 晶硅 生 产企 业也 采 用较
少 ,主要 原 因如下 :
第一 ,由于 采用 石 墨作 为加 热材 料 ,在 反应 器 内 , 高 温 条 件 下 ,石 墨 可 能 与 原 料 四 氯 化 硅 和 氢 气 发 生 反
・
2 0・
山
西
化
工
2 0 1 3 年1 0 月
优 化 冷氢 化工 艺 的反 应条 件 ,可 以使 用 内 、外表 面
都 均 匀分 布 的硅 化铁 ( 铜 )的金 属 硅粒 子作 为 原料 ,进
行 氢化 反 应 获得 较高 收 率 的三 氯氢 硅 。但是 ,获得 这种 粒 子 较为 困难 。生产 硅化 铁 ( 铜 )的 金属硅 粒 子 主要 的
【 摘要】 四氯化硅是光伏产业的副产物 ,对环境产生严重污染。以四氯化硅合理化利用作为研究对象,分析了四氯化
三氯氢硅的合成工艺
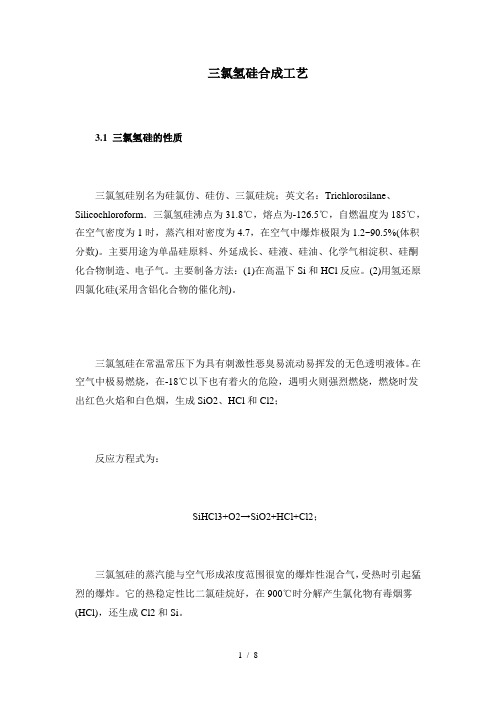
三氯氢硅合成工艺3.1 三氯氢硅的性质三氯氢硅别名为硅氯仿、硅仿、三氯硅烷;英文名:Trichlorosilane、Silicochloroform.三氯氢硅沸点为31.8℃,熔点为-126.5℃,自燃温度为185℃,在空气密度为1时,蒸汽相对密度为4.7,在空气中爆炸极限为1.2~90.5%(体积分数)。
主要用途为单晶硅原料、外延成长、硅液、硅油、化学气相淀积、硅酮化合物制造、电子气。
主要制备方法:(1)在高温下Si和HCl反应。
(2)用氢还原四氯化硅(采用含铝化合物的催化剂)。
三氯氢硅在常温常压下为具有刺激性恶臭易流动易挥发的无色透明液体。
在空气中极易燃烧,在-18℃以下也有着火的危险,遇明火则强烈燃烧,燃烧时发出红色火焰和白色烟,生成SiO2、HCl和Cl2;反应方程式为:SiHCl3+O2→SiO2+HCl+Cl2;三氯氢硅的蒸汽能与空气形成浓度范围很宽的爆炸性混合气,受热时引起猛烈的爆炸。
它的热稳定性比二氯硅烷好,在900℃时分解产生氯化物有毒烟雾(HCl),还生成Cl2和Si。
遇潮气时发烟,与水激烈反应,反应方程式为:2SiHCl3+3H2O→(HSiO)2O+6HCl;在碱液中分解放出氢气,反应方程式为:SiHCl3+3NaOH+H2O→Si(OH)4+3NaCl+H2↑;与氧化性物质接触时产生爆炸性反应。
与乙炔、烃等碳氢化合物反应产生有机氯硅烷,反应方程式为:SiHCl3+CH≡CH→CH2CHSiCl3SiHCl3+CH2=CH2→CH3CH2SiCl3在氢化铝锂、氢化硼锂存在条件下,SiHCl3可被还原为硅烷。
容器中的液态SiHCl3当容器受到强烈撞击时会着火。
可溶解于苯、醚等。
无水状态下三氯氢硅对铁和不锈钢不腐蚀,但是在有水分存在时腐蚀大部分金属。
3.2 三氯氢硅合成的目的和意义本岗位是将干燥的硅粉输送到流化床内,在流化床反应器内,硅粉与氯化氢气体进行合成反应,反应生成的氯硅烷混合单体经过除气、净化、冷却、加压、再冷却后送到脱气塔内,塔顶脱除低沸物氯化氢,氯化氢气体重新返回流化床循环使用,塔底混合单体经单体冷却器冷却后送入混合单体储罐)中供精馏岗位使用。
三氯氢硅合成工艺简述
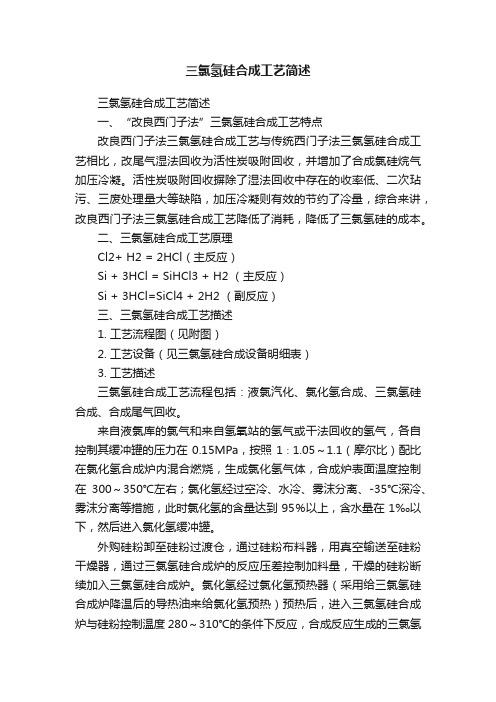
三氯氢硅合成工艺简述三氯氢硅合成工艺简述一、“改良西门子法”三氯氢硅合成工艺特点改良西门子法三氯氢硅合成工艺与传统西门子法三氯氢硅合成工艺相比,改尾气湿法回收为活性炭吸附回收,并增加了合成氯硅烷气加压冷凝。
活性炭吸附回收摒除了湿法回收中存在的收率低、二次玷污、三废处理量大等缺陷,加压冷凝则有效的节约了冷量,综合来讲,改良西门子法三氯氢硅合成工艺降低了消耗,降低了三氯氢硅的成本。
二、三氯氢硅合成工艺原理Cl2+ H2 = 2HCl(主反应)Si + 3HCl = SiHCl3 + H2 (主反应)Si + 3HCl=SiCl4 + 2H2 (副反应)三、三氯氢硅合成工艺描述1. 工艺流程图(见附图)2. 工艺设备(见三氯氢硅合成设备明细表)3. 工艺描述三氯氢硅合成工艺流程包括:液氯汽化、氯化氢合成、三氯氢硅合成、合成尾气回收。
来自液氯库的氯气和来自氢氧站的氢气或干法回收的氢气,各自控制其缓冲罐的压力在0.15MPa,按照1∶1.05~1.1(摩尔比)配比在氯化氢合成炉内混合燃烧,生成氯化氢气体,合成炉表面温度控制在300~350℃左右;氯化氢经过空冷、水冷、雾沫分离、-35℃深冷、雾沫分离等措施,此时氯化氢的含量达到95%以上,含水量在1‰以下,然后进入氯化氢缓冲罐。
外购硅粉卸至硅粉过渡仓,通过硅粉布料器,用真空输送至硅粉干燥器,通过三氯氢硅合成炉的反应压差控制加料量,干燥的硅粉断续加入三氯氢硅合成炉。
氯化氢经过氯化氢预热器(采用给三氯氢硅合成炉降温后的导热油来给氯化氢预热)预热后,进入三氯氢硅合成炉与硅粉控制温度280~310℃的条件下反应,合成反应生成的三氯氢硅、四氯化硅、氢气与未完全反应的氯化氢混合气体经漩涡分离器、袋式过滤器,除去粉尘(进废碴淋洗塔)和高氯硅烷,经沉积器、压缩前水冷、压缩前-5℃冷、压缩前-35℃深冷,冷凝下来的氯硅烷通过压缩前合成产品计量罐进入压缩前合成产品贮罐;未冷凝的气体经过活塞压缩机加压,再经过压缩后水冷、压缩后-5℃冷,冷凝下来的氯硅烷通过压缩后合成产品计量罐进入压缩后合成产品贮罐;少量的未凝气体三氯氢硅、四氯化硅和不凝气体氢气、氯化氢,通过管道进入三氯氢硅合成尾气回收系统。
三氯氢硅及合成工艺

三氯氢硅及合成一、三氯氢硅的基本性质三氯氢硅在常温常压下为具有刺激性恶臭、易流动、易挥发的无色透明液体。
分子量:135.43,熔点(101.325kPa):-134℃;沸点(101.325kPa):31.8℃;液体密度(0℃):1350kg/m3;相对密度(气体,空气=1):4.7;蒸气压(-16.4℃):13.3kPa;(14.5℃):53.3kPa;燃点:-27.8℃;自燃点:104.4℃;闪点:-14℃;爆炸极限:6.9~70%;在空气中极易燃烧,在-18℃以下也有着火的危险,遇明火则强烈燃烧,三氯氢硅燃烧时发出红色火焰和白色烟;三氯氢硅的蒸气能与空气形成浓度范围很宽的爆炸性混合气,受热时引起猛烈的爆炸。
它的热稳定性比二氯硅烷好,三氯氢硅在900℃时分解产生氯化物有毒烟雾;遇潮气时发烟,与水激烈反应;在碱液中分解放出氢气;三氯氢硅与氧化性物质接触时产生爆炸性反应。
与乙炔、烃等碳氢化合物反应产生有机氯硅烷;在氢化铝锂、氢化硼锂存在条件下,三氯氢硅可被还原为硅烷。
容器中的液态三氯氢硅当容器受到强烈撞击时会着火。
可溶解于苯、醚等。
无水状态下三氯硅烷对铁和不锈钢不腐蚀,但是在有水分存在时腐蚀大部分金属。
二、三氯氢硅的用途用于有机硅烷和烷基、芳基以及有机官能团氯硅烷的合成,是有机硅偶联剂中最基本的单体,同时也是制备多晶硅的主要原料。
将三氯硅烷与氯乙烯或氯丙烯进行合成反应,再经精馏提纯,得到乙烯基或丙烯基系列硅烷偶联剂产品。
硅烷偶联剂几乎可以与任何一种材料交联,包括热固性材料、热塑性材料、密封剂、橡胶、亲水性聚合物以及无机材料等,在太阳能电池、玻璃纤维、增强树脂、精密陶瓷纤维和光纤保护膜等方面扮演着重要的角色,并在这些行业中发挥着不可或缺的重要作用。
三、三氯氢硅生产工艺1、主要化学反应方程式为:Si + 3HCl = SiHCl3 + H2Si + 4HCl = SiHCl4 + 2H22、生产装置主要由氯化氢干燥、三氯氢硅合成、三氯氢硅提纯和分离工序组成。
- 1、下载文档前请自行甄别文档内容的完整性,平台不提供额外的编辑、内容补充、找答案等附加服务。
- 2、"仅部分预览"的文档,不可在线预览部分如存在完整性等问题,可反馈申请退款(可完整预览的文档不适用该条件!)。
- 3、如文档侵犯您的权益,请联系客服反馈,我们会尽快为您处理(人工客服工作时间:9:00-18:30)。
和大家分享一下几个公司的冷氢化工艺;谢谢!洛阳晶辉新能源科技有限公司1、低温氢化技术方案“低温氢化”反应原理为:四氯化硅(SiCl4)、硅粉(Si)和氢气(H2)在500℃温度和1.5MPa 压力条件下,通过催化反应转化为三氯氢硅(SiHCl3)。
化学反应式为:3SiCl4+Si+2H2=4SiHCl3行业“低温氢化”虽然比“热氢化”具有能耗低、设备运行可靠的优点,但是尚存一些不足:(1)实际转化率偏低——四氯化硅(SiCl4)实际转化率一般在18%左右;(2)催化剂稳定性差——导致催化剂寿命短、消耗量大、成本高;特别是催化剂载体铝离子容易造成“铝污染”;(3)设备复杂、系统能耗大——工作温度高,所以氢化炉需要内或外加热,设备复杂,系统无有效的能量回收装置,系统能耗高。
3)“催化氢化”技术方案针对上述四氯化硅(SiCl4)冷、热氢化存在的缺点和问题,洛阳晶辉新能源科技有限公司和中国工程院院士、中石化权威催化剂和化工专家合作,在传统“低温氢化”基础上进行改良,自主创新开发出了新一代“改良低温氢化”技术——“催化氢化”。
(1)“催化氢化”技术路线⌝开发高活性多元纳米催化剂——在现有单活性金属基础上,引入第二活性金属,并采用特殊负载工艺,使活性金属呈纳米状态,提高催化剂活性;开发高稳定性催化剂载体——解决现有催化剂稳定性差问题,延长催化剂使用寿命,同时解决“铝污染”;(2)“催化氢化”技术特点催化剂活性高,特别是反应⌝选择性好——四氯化硅(SiCl4)单程率达到22%,以上(最高可达25%);⌝实现热量耦合、节约能源——需要的外加热量小,减少系统能源消耗;催化剂稳定性好——寿命长、用量小、避免了Al2O3 分解带来的“铝污染”;反应温度进一步降低,反应炉不需要内(或外)加热,并设能量综合回收装置,降低了系统能耗;系统用氢细致划分,由电解氢改良为多晶硅生产过程的回收氢气,既节约了制氢站电解氢的消耗量,同时也有利于提高多晶硅生产中氢气的质量;良好的除尘技术和反应渣吹除技术,保证系统的稳定运行、安全环保,减少了环境污染。
针对本项目,根据行业四氯化硅(SiCl4)“低温氢化”成功应用的实际和向“低温氢化”发展的趋势,首先选择“低温氢化”工艺技术;同时,鉴于“催化氢化”在现有“低温氢化”技术的基础之上实现了改良,具有转化率高、物耗能耗低、使用回收氢气、消除“铝污染”的显著优点,本项目技术方案确定采用“催化氢化”技术。
3.2. 项目生产工艺流程SiCl4“催化氢化”主生产工艺由催化氢化工序、氯硅烷提纯工序组成:1) SiCl4 催化氢化工序工业级硅粉同特定催化剂混合均匀后,装入干燥炉;氢气经加热后,进入干燥炉干燥硅粉、还原催化剂;从干燥炉出来的氢气进入氢气净化装置处理后,返回系统;干燥之后的硅粉、催化剂混合料,暂存于干燥炉,以备反应之用;原料氢(来自多晶硅系统)经压缩机升压到后进入混合器与四氯化硅混合、配比,氢气-四氯化硅混合气体经加热后通入反应炉与来自混合料加入装置的混合料反应生成三氯氢硅(SiHCl3);生成物三氯氢硅(SiHCl3)和未反应的四氯化硅(SiCl4)、氢气(H2)、二氯二氢硅(SiH2Cl2)及少量氯化氢(HCl),经高效过滤器过滤后进入冷凝装置,被冷凝下来三氯氢硅(SiHCl3)、四氯化硅(SiCl4)混合液进入氯硅烷提纯塔,得到三氯氢硅(SiHCl3)和四氯化硅(SiCl4);四氯化硅(SiCl4)返回系统再次循环转化,三氯氢硅(SiHCl3)三氯氢硅进入多晶硅生产系统生产多晶硅;未被冷凝的氢气(H2)和少量二氯二氢硅(SiH2Cl2)及氯化氢(HCl)返回系统。
2) 氯硅烷提纯工序氯硅烷冷凝料经过提纯1#塔、提纯2#塔两塔连续提纯,控制一定的温度、压力、回流比,提纯1#塔塔顶采出轻组分,塔釜物料进入提纯2#塔,提纯2#塔塔顶采出三氯氢硅(SiHCl3),中层塔板采出四氯化硅(SiCl4)返回催化氢化工序,塔釜采出重组分连同提纯1#塔塔顶采出的轻组分水解或外卖。
3.3. 主要工艺技术指标本项目主要工艺技术指标见下表:序项目技术经济指标备注号1转化SiCl4 量:t/a200002生产SiHCl3 量:t/a 200003单程转化率≥20%4硅粉耗量:t/a11505催化剂耗量:t/a16回收氢气耗量:6200*104Nm3/a电解氢气耗量:736*104Nm3/a8电耗:*104kW.h/a16009残液量:t/a90010低沸物量:t/a300*****公司技术资料四氯化硅高压低温氢化生产工艺技术3.1高压低温氢化工艺概述本建议书提供的氢化工艺反应是在独特的流化床反应炉内、维持高压和一定温度,STC与H2、Si进行反应生成TCS。
为了加速反应的进行和提高反应速率、氢化转化率,另还添加了催化剂。
反应原理如下:STC、H2、Si粉和催化剂作为原料送入氢化反应炉内,Si粉中的一些杂质也进行反应生成金属氯化物。
氢化主要反应如下:Si+ 2H2 + 3SiCl4 催化剂 4SiHCl3SiCl4+Si+2H2=2SiH2Cl22SiHCl3=SiCl4+SiH2Cl2在正常工况运行下,STC的最小转化率η≥24%,通过添加催化剂,可使转化率提高至26~28%。
STC转化率计算方式如下:η= ×100%添加进入反应炉内STC摩尔量流化床内氢化反应发生在近3MPa、500℃条件下。
反应炉的设计制造将要考虑这些因素。
3.2工艺流程及工艺描述本氢化提纯工艺可以被简单称为前段高压、后段低压处理流程。
前端高压处理工艺包括氢化反应炉、固/液杂质收集处理系统和氢气回收循环利用系统。
后段低压处理工艺主要包括TCS杂质去除系统、TCS/STC分离系统和储存系统。
拟选用工艺流程图见图3.1所示。
主要设备表见表3.1所示。
STC通过STC给料泵(P-102)将其从储罐内进行给料,液态STC加料时通过泵加压的压力接近30kg/cm2,STC经两台工艺-工艺热交换器加热。
第一台工艺-工艺热交换器(STC 预热热交换器E-204)将STC加热至150℃。
被预热后的STC经第二台工艺-工艺热交换器(E-203),该热交换器相当于STC的蒸发器,STC 在此被进一步加热到近260℃从而蒸发为气体。
被蒸发后的STC 进入电加热器(STC过热器E-202),STC在此被加热至近运行温度550℃。
H2压缩机(K-101)将H2压力提高至30kg/cm2而进入反应炉。
H2压缩机进料口的H2来自两处,工厂制氢站(在图3.1未显示)和氢化/提纯系统界区内回收循环利用。
经压缩后的H2经缓冲罐(T-103)至电加热器(H2过热器E-201),H2物在此被加热至近550℃。
干燥除去水分后硅粉和催化剂混合后进入硅粉给料罐(T-201)。
通过双锁给料斗加入氢化反应炉(R-203)。
双锁给料斗通入H2使其压力接近30kg/cm2。
位于双锁给料斗与充压的氢化炉之间的耐磨盘阀的开启和关闭使给料斗内的硅粉进入反应器。
运行过程中的硅粉是批量加料的,每小时平均在1~2次。
过热的H2和STC按一定比例混合从氢化炉(R-201)底部进入,混合气体在(P-203)的STC/TCS混合液通过喷头进入淋洗塔,保持塔内STC/TCS液位。
喷头规则分布,使进入塔内的气体与塔内液体和补充回流进入的液体充分接触。
经过热量交换和除去未反应硅粉、金属氯化物和部分重组分的气体从塔顶进入热交换器(E-204),在此热交换器内,液态STC被预热,气体进一步冷却至85℃。
随后进入冷却水冷却器(E-205)、-15℃冷凝器(E206)、-65℃冷凝器(E-207)进一步冷却,STC、TCS被完全冷却下来,流入粗TCS(TCSC)再循环储罐(T-203),不凝气体主要是H2、HCl和极少量的TCS,H2经除雾器(B-201)除去液态小液滴后,返回循环利用。
进入T-203内的氯硅烷混合液体一部份再循环至淋洗塔T-202补充其内STC和TCS。
另一部份经过过滤器(F-201)后进入提纯系统的给料罐(T-301)。
至此,本工艺系统前段的高压段处理系统结束。
粗TCS进入后段低压分离/提纯系统。
后段低压分离/提纯系统主要由两台精馏塔(C-301重组分去除塔)(C-302 SCT、TCS分离塔)和中间储罐等组成,粗TCS在C-301塔除去氯硅烷的重组分及HCl后,在C-302塔进行STC 和TCS分离;合格的TCS作为产品(TCSP)储存在TCSP储罐(T-304)中,用泵(P-304)输送至三氯氢硅提纯系统进行提纯,而高纯STC(STCP)存储于STCP储罐(T-104)再作为原料循环至氢化炉继续进行氢化转换。
三、主要技术经济指标表3.1 原料消耗数据表序号[/td][td=1,1,151]名称[/td][td=1,1,173]消耗量(公斤/吨TCS)[/td][td=1,1,142]备注[/td][/tr]1MGS582STC9603H27.8表3.2 能量和公用工程消耗数据表消耗量(公斤/吨序号名称备注TCS)1电800kWh2蒸汽 1.1t1MPa 3冷却水90t 循环4压缩空气2m³5仪表气30m³³6氮气60m³7氢气80m³8冷媒16500kg9冷媒22200kg表3.3 产品质量指标名称含量TCS>98.5%STC<1.5%DCS<0.3%注: 以上指标是根据年处理50000t 四氯化硅量的结果,指标根据四氯化硅处理量的不同,会有变化。
SST冷氢化技术1、工艺描述SST冷氢化技术采用Si+H2+SiCl4+歧化+SiH4精馏提纯+硅烷热分解。
向我方提供的技术如图3-11)氢化主要反应Si+2H2+3SiCl4→SiHCl3吸热反应反应温度600℃反应压力 10转化率21%反应温度对转化率的影响是主要的过程:贮缸内的硅粉干燥除水后一缸一次加入到氢化炉内,属间歇加料方式,非连续式。
H2气用压缩机加压到10barg,并加热到600℃连同SiCl4(泵送、10barg、加热到600℃)混合一起加入到氢化炉内,Si+H2+SiCl4进行吸热反应生成SiHCl3。
SiHCl3混合物经吸收、冷凝、2个精馏塔提纯,得到SiHCl3和SiCl4,SiHCl3送去歧化,SiCl4返回送入氢化炉。
在冷凝分离过程中收集的H2气也返回氢化炉使用。
氢化过程选用的设备如压缩机、泵、反应器、塔器、加热器、冷凝器、换热器、过滤器器和贮罐等共50台(套)。
1)铵催化剂歧化主要反应:4 SiHCl3SiH4+3SiCl转化率:25%催化反应塔内在铵催化剂作用下,将送入的SiHCl3歧化成SiH4,在生成物中含有没有起反应的SiHCl3和反应后生成的SiH4及SiCl4。