磁力研磨特点及其关键技术
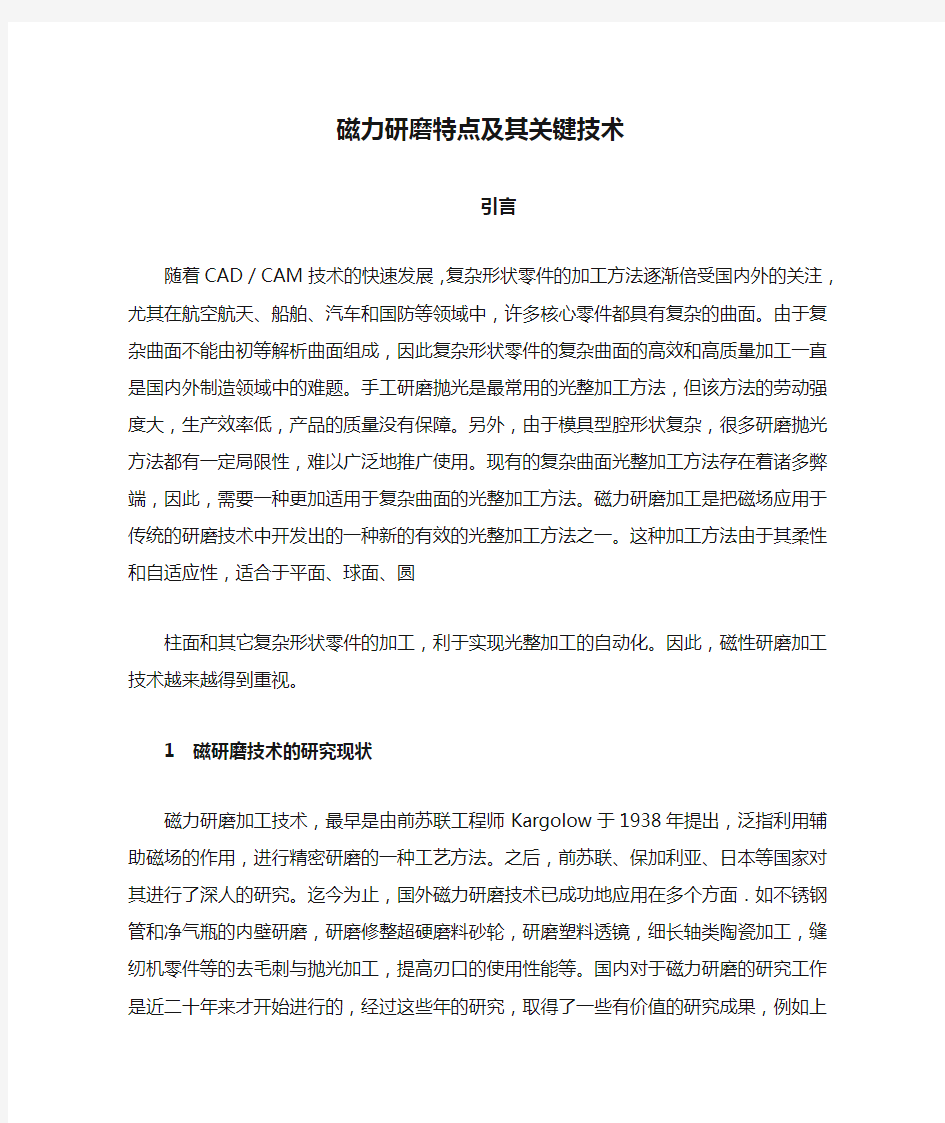

磁力研磨特点及其关键技术
引言
随着CAD/CAM技术的快速发展,复杂形状零件的加工方法逐渐倍受国内外的关注,尤其在航空航天、船舶、汽车和国防等领域中,许多核心零件都具有复杂的曲面。由于复杂曲面不能由初等解析曲面组成,因此复杂形状零件的复杂曲面的高效和高质量加工一直是国内外制造领域中的难题。手工研磨抛光是最常用的光整加工方法,但该方法的劳动强度大,生产效率低,产品的质量没有保障。另外,由于模具型腔形状复杂,很多研磨抛光方法都有一定局限性,难以广泛地推广使用。现有的复杂曲面光整加工方法存在着诸多弊端,因此,需要一种更加适用于复杂曲面的光整加工方法。磁力研磨加工是把磁场应用于传统的研磨技术中开发出的一种新的有效的光整加工方法之一。这种加工方法由于其柔性和自适应性,适合于平面、球面、圆
柱面和其它复杂形状零件的加工,利于实现光整加工的自动化。因此,磁性研磨加工技术越来越得到重视。
1 磁研磨技术的研究现状
磁力研磨加工技术,最早是由前苏联工程师Kargolow于1938年提出,泛指利用辅助磁场的作用,进行精密研磨的一种工艺方法。之后,前苏联、保加利亚、日本等国家对其进行了深人的研究。迄今为
止,国外磁力研磨技术已成功地应用在多个方面.如不锈钢管和净气瓶的内壁研磨,研磨修整超硬磨料砂轮,研磨塑料透镜,细长轴类陶瓷加工,缝纫机零件等的去毛刺与抛光加工,提高刃口的使用性能等。国内对于磁力研磨的研究工作是近二十年来才开始进行的,经过这些年的研究,取得了一些有价值的研究成果,例如上海交通大学进行了物流管道内表面磁力研磨的回转磁场的设计H1;太原理工大学研制了粘结法和热压烧结法制备磁性磨料的工艺,并深入研究了磁力研磨的磨削机理;西安工业学院进行了磁力研磨加工的数值仿真,以及磁屏蔽对内圆磁力研磨加工影响的研究。山东理工大学自行研制了三坐标数字化加工控制磁力研磨机床。由于国内起步比较晚,在理论和实验等方面还和国外有不小的差距,目前还主要处在实验研究的阶段,实际应用的不多,而且深度与国外相比还不够博。因此,本文提出一种复杂曲面磁力研磨加工方法,其加工工具具有磁性磨料的自动更新等功能。
2 加工原理及特点
2.1 加工原理
磁力研磨加工是在强磁场作用下,填充在磁场中的磁性磨料被沿着磁力线的方向排列起来,吸附在磁极上形成“磨料刷”,并对工件表面产生一定的压力,磁极在带动“磨料刷”旋转的同时,保持一定的间隙沿工件表面移动,从而实现对工件表面的光整加工。在加工中
磁性磨粒的受力状态如图" 所示,磨粒受到工件表面法向力和切向力的作用,作用力使磨粒有向切线方向飞散的趋势,但由于磁场效应,磨粒同时还受到沿磁力线方向的一个压向工件的力和沿磁等位线方向的作用力可以防止磨粒向加工区域以外流动,从而保证研磨工作的正常进行。
图1 磁力研磨示意图
1磁性磨粒2 3 磁极4工件
2.2加工特点
(1)磨粒自锐性能好,磨削能力强,加工效率高,可以自动调整研磨切削力,实现对机械零件表面的精密研磨加工。
(2)温升小,工件变形小,切削深度小,加工表面平整光洁,加工精度可达0.01mm。
(3)工件表面的交变励磁,强化了表面电化学过程,改变了表面的应力分布状态,提高了工件表面的物理机械性能。
(4)加工对象适应性强,可以研磨平面、曲面以及复杂形状零件的内外表面,例如弯管、" 型管、异型内表面、小瓶颈零件内表面。
(5)具有交变磁场的磁力研磨装置由于没有运动部件,因而运行可靠,设备的寿命大大提高。但是,由于目前磁性磨料制作成本较高,工件的装夹与去磁问题尚未得到解决,形成批量生产尚有困难。
3典型的加工装置
3.1外圆磁力研磨装置
如图2所示,工件5安装在立式铣床上,在工件与磁极之间的间隙内填入磁性磨料,主轴使工件产生回转和上下进给运动。向线圈通入直流电,即可产生有一定磁感应强度的磁场。实验表明,此方法研磨外圆可使工件表面粗糙度值由1.6um降至0.2um。磨料种类和磁感应强度对研磨效果有较大影响,增加磁感应强度或采用烧结磨料可以提高研磨效率。
图2外圆磁力研磨装置示意图
1线圈2磁极3磁轭4底座5工件6磁性磨料7主轴
3.2内圆表面磁力研磨装置
如图3所示,该装置适用于非磁性物质(如黄铜)圆管等的内表面光整加工。圆管内部装有永磁铁和磁性磨料,磁性磨料吸附在永磁铁的周围,当圆管外部加上永磁铁时,磁性磨料在磁场的作用下对圆管内表面产生一定的压力。该装置的本体可以安装到车床的拖板上,工件由主轴带动作回转运动,永磁铁沿工件轴线方向振动,拖板带动工件作进给运动。黄铜圆管内表面加工后,表面粗糙度值可从7um降至1.3um。
图3内圆表面磁力研磨装置示意图
1永磁铁2磁性磨料3 振动方向4磁极5非磁性管
4 复杂曲面数字化磁力光整加工
对平面或规则曲面(内、外圆面等)的加工通常可采用前述的自动化光整加工装置来完成。而复杂模具的外表面往往以非规则曲面占多数,且模具产品表面光洁度要求非常高,实现自动化光整加工较困难。目前普遍采用手工打磨,造成质量不稳定、效率非常低、人为因素影响较大等缺点。如果能结合曲面数字化方法(接触式、非接触式),
先提取复杂曲面的三维几何数据,通过相应的软件生成曲面的几何模型和数控加工代码,再利用数控磁力研磨光整加工设备完成复杂曲面的自动化光整加工,就可以克服手工光整加工的弱点,大大提高生产效率。山东工程学院的赵玉刚等人已进行了类似的研究,开发了复杂曲面数控磁力研磨加工机床。该机床采用的控制系统是为适应磁力研磨加工工艺特点而自行研制的三坐标数字化仿形加工控制系统。该加工设备除了具有普通三坐标数控铣床控制系统的功能外,还具有曲面示教方式三坐标数字化测量功能、曲面加工轨迹的自动编程和磁性磨料的自动更换功能等。
内孔研磨超硬材质加工技术
JG-450CP 内孔研磨超硬材质加工技术 1. 内孔研磨超硬材质加工技术: 加工机型:M oore坐标磨床 加工精度:0.002mm 加工刀具:moore钻石砂轮 加工用途:磨头转速分别有40kprm 120 kprm 175 kprm只要针对模具行业中高精度的各种圆孔方孔异性孔盲孔以及线性曲面的加工; 2.加工工件图例: 加工精度:¢10mm ¢3mm的孔加工精度均为0.001-0.002mm 位置精度:0.001-0.002mm 尺寸精度:0.001-0.002mm 3加工流程: ①加工前确认: 确认联络单编号与工件是否一致,工件有无划伤并认真审图 ②选择加工方式选择加工方式 ⑴平行垫块 用平行垫块装夹工件(如图一所示)这样装夹简单快捷容易把工件的平面度扫平,同时用螺丝加紧力大工件不宜松动。但是这样由于加紧力的作用和加工过
程中产生内应力。 ⑵利用V型夹装夹 加工如图二所示工件我们一般采用治具装夹的方法这样做很容易加紧工件容易找坐标但是工件装夹精度和垂直度容易受治具精度的影响同时由于工件壁厚的不同装夹时工件会产生变形。 ⑶利用磁力平台吸磁的方法 该方法可以直接将工件放在磁力平台上利用磁力平台的吸力给工件一个力不使工件移动然后根据加工情况可以采用万能胶水粘在工件四周。如图所示三: 同时当加工一个通孔时必须有让刀部分这就要求磁力平台要沉下去一些,如 图: 4建立加工坐标 ⑴量表的选择: 精度要求在0.002mm以内的选择的刻度为0.001mm的杠杆量表 精度要求在0.002mm以上的选择的刻度为0.002mm的杠杆量表 ⑵建坐标的基本原则 加工工件时外形尺寸要求精度高时,采用用工件外形建立坐标。 当外应精度一般时我们采用工件中精度高的各种孔建立坐标,选择尽可能远的两个孔来建坐标,同时方孔优先于圆孔。 如果工件外形和孔的精度都不高时,使用JG所加工孔建立坐标。
磁力去毛刺研磨机使用工艺【详解】
磁力去毛刺研磨机使用工艺 内容来源网络,由“深圳机械展(11万㎡,1100多家展商,超10万观众)”收集整理!更多cnc加工中心、车铣磨钻床、线切割、数控刀具工具、工业机器人、非标自动化、数字化无人工厂、精密测量、3D打印、激光切割、钣金冲压折弯、精密零件加工等展示,就在深圳机械展. 研磨机操作的关键是要设法得到*的抛光速率,以便尽快除掉磨光时发生的损害层。一起也要使抛光损害层不会影响结尾调查到的安排,即不会构成假安排。 研磨机对非铁类金属或轻铁类金属、硬质塑料等精密零件,去除毛边、倒角、抛光、洗净等均有良好效果。对不规则状零件、孔内、管内、死角、夹缝等皆能研磨加工。本产品加工速度快,操作简单安全,成本低。而且成品加工后不变形,不影响精度。磁力研磨机对压铸五金去除毛边披锋,去除氧化薄膜,工件表面油迹抛光处理,氧化层的去除,均有良好的效果。如精密冲压零件,不锈钢零件,螺丝,锌铝压铸零件,弹簧,弹片零件,电子,计算机,通信零件,自动车零件,航天,医疗零件都能取到良好的抛光作用。 前者需求运用较粗的磨料,以确保有较大的抛光速率来去掉磨光的损害层,但抛光损害层也较深;后者需求运用*细的资料,使抛光损害层较浅,但抛光速率低。处理这个对立的*的方法即是把抛光分为两个期间进行。粗抛意图是去掉磨光损害层,这一期间应具有*的抛光速率,粗抛构成的表层损害是非的思考,不过也应当尽可能小;其次是精抛(或称终抛),其意图是去掉粗抛发生的表层损害,使抛光损害减到*小。 研磨机采用的是同步带传动方式,所以在机器工作时,机器的运转很平稳,机器工作时无振动。因为它运转的平稳性好,所以机器工作时发出的噪音小 研磨机抛光时,试样磨面与抛光盘应肯定平行并均匀地轻压在抛光盘上,留意防止试样
68第八节研磨技术
第八节研磨技术 研磨是精密和超精密零件精加工的主要方法之一,是在精加工,如精车、精磨或精洗加工后的超精加工。研磨加工可使零件获得极高的尺寸精度、几何形状和位置精度,最高的表面粗糙度等级以及提高配合精度。零件的内、外圆表面、平面、圆锥面、斜面、螺纹面、齿轮的齿面及其他特殊形状的表面均可以采用此种方法进行加工。船舶主、副柴油机燃油系统中的三对精密偶件:柱塞—套筒偶件、针阀—针阀体偶件、出油阀—出油阀座偶件的内、外圆表面、圆锥面、平面在制造时都需要采用研磨进行精加工。在针阀—针阀体配合锥面磨损和柴油机的进排气阀配合锥面磨损后均需采用研磨技术进行修复,使配合面恢复密封性能。 进行研磨的零件材料可以是经淬火或未经淬火的碳钢、合金钢、硬质合金,也可以是铸铁、铜及其合金等有色金属材料,或玻璃、水晶和塑料等非金属材料。 灵活的研磨技术是进行精密零件修理的有效方法,尤其是在备件缺乏、时间紧迫的情况下此法尤为重要。例如,主、副柴油机的喷油器故障大多是针阀—针阀体偶件的锥面配合不良引起的,轮机人员须经常进行针阀偶件的研配工作。所以,研磨技术在船上轮机工作中是克服精密设备短缺、延长零件寿命、节省修理费用和保证船舶正常航行的有效工艺,轮机人员应该掌握研磨技术。 一、概述 1.研磨原理 研磨是使零件与研磨工具在无强制的相对滑动或滚动的情况下,通过加入其间的研磨剂的微切削和研磨液的化学作用,在零件表面生成易被磨削的氧化膜,从而加速研磨过程。所以研磨加工是机械、化学联合作用完成的精密加工。 1)零件与研磨工具的相对运动 零件与研磨工具不受外力的强制引导,以免引起偏差和缺陷;运动方向周期变换,以使研磨剂均匀分布在零件表面上并加工出纵横交叉的切削痕,均匀研磨零件表面;研磨表面上各点相对于研磨工具表面的滑动路程相等,以达到均匀切削。 2)研磨压力 在实际应用的压力范围内,研磨效率随压力增加而提高。研磨压力取决于零件材料、研磨工具材料和外界压力等因索,一般通过实验确定。常用的压力范围为0.05~0.3MPa,粗研宜用0.l~0.2MPa,精研宜用0.0l~0.1MPa。研磨压力过大,研磨剂磨粒被压碎,切削作用减小,表面划痕加深,研磨质量降低;压力过小则研磨效率大大降低。 3)研磨速度 研磨速度影响研磨效率,一定条件下,研磨速度增加将使研磨效率提高。研磨速度取决于零件加工精度、材质、重量、硬度、研磨面积等。一般研磨速度在10~150m/min。速度过高,产生的热量较多,引起零件变形、表面加工痕迹明显等质量问题,所以精密零件研磨速度不应超过30~60次/min。一般手工粗研往复次数为30~60次/min,精研为20~40次/min。 4)研磨时间 研磨初期,因研磨剂磨粒锋利,微切削作用强,零件研磨表面的几何形状误差和粗糙度得以较快地纠正。随着研磨时间的延长,磨粒钝化,微切削作用下降,不仅零件精度不能提高,反而由于热量增加使之下降。粗研时间取决于研磨剂的切削性能,为提高研磨效率,当研磨剂磨粒钝化,研磨效果差时应立即更换研磨剂。精研时间一般约为1~3min,超过3min 研磨效果不显著。 所以,粗研时选用较粗的研磨剂,较高的压力和较低的速度进行研磨,以期较快地消除
磁力研磨机说明书
顺佳研磨科技有限公司磁力精密研磨机 PRECISION MAGNETIC GRINDER https://www.360docs.net/doc/f55385132.html, 机械原理简介 Mechanic Principle 利用神奇磁场力量传导不锈钢针磨材产生加速旋转动作,高效率达到精密研磨去除毛边和抛光洗净效果 With the use of the magical force of magnetic field, making the stainless steel pins rotate very fast, to de-burr, polish and clean the workpieces high-effectively and precisely. 1、特点Features 1) 卓越快速去除毛边能力,细小内孔、内管、夹缝死角均可高效研磨,绝不变形及伤表面,不影响精度。 Have excellent ability of fast de-burring, high efficiently grinding small inner holes, inner pipes, crevices, etc. Make NO damage to the surface of workpieces, and DO NOT affect the accuracy of workpieces. 2) 加工速度快,一次3~15分钟即可完成,可在机器运转中替换工件。 Fast grinding or polishing, only 3~15 minutes is needed for each time. Workpieces can be changed during the machine running. 3) 操作方面简单,成本低,无污染,不锈钢针为永久性磨材。 Simple and convenient operation, low cost, no pollution. The stainless steel pins are permanent abrasives. 2、用途Application 金饰业打磨洗净工作,成品表面抛光处理,去除氧化薄膜工作,锈蚀去除处理,电镀或喷漆前处理,烧结痕迹处理,零件残磁去除。
磁力研磨机的结构设计
磁力研磨机的结构设计 董瑞宝, 宋庆环, 付云强 (唐山学院,河北唐山063020) 摘要: 磁力研磨技术是新型的光整加工技术,目前在我国尚不普及,没有专用的设备,为了推广该项技术,研制开发了磁力研磨机。在此介绍用CA6140普通车床改装的磁性研磨机的结构设计。 0前言 磁力研磨装置是利用永久磁铁产生强磁场,依靠磁力使磁性研磨粒子贴附在工件表面,当工件与磁极产生相对运动时,磁性研磨粒子对工件表面进行研磨加工。根据磁力研磨特点和待加工工件现状设计不同的磁研磨回路,在现有设备基础上进行改造,针对轴类零件的自身特点,对CA6140车床进行设备改造即可成为专用的磁力研磨装置。 1磁性研磨机的总体结构设计 用CA6140普通车床改装的磁性研磨机结构如图1所示。拆掉CA6140刀架和小滑板部分改造,其中滑板结构,利用其进给机构给磁研磨机构提供相对运动。 磁性研磨机主要由2部分组成: ( 1)磁力研磨装置,在结构中用磁力研磨装置替换了原有的车床小滑板和刀架部分; (2)磁力研磨机的进给装置,在原有车床进给装置的基础上改装的,使其能实现轴向和径向进给的双重功能。 于0104 mm,同时调整导轨与各拖板之间的间隙一定要合适。 214合理选取车刀的几何参数 车削细长轴时,由于工件刚性差,车刀的几何形状对工件的振动有明显的影响。选择车刀的几何形状时应注意的6点见文献[ 1 ]、[ 3 ]。 3结语 通过工艺系统优化,获得了相当满意的效果:(1)工件加工精度与表面粗糙度达到图纸要求;
(2)反向切削方法的最大直径误差大约是正向切削方法的一半; (3)使用大切削量节约工时成本; (4)由于充分使用了切削液,刀具的耐用度显著提高。 2磁力研磨装置 磁力研磨装置如图2所示。由磁极、支架、微调手轮、联接架等组成。磁极选用的是经过特殊形状设计的2块永久磁铁。通过磁极间产生的磁场来实现磁研磨的全部研磨过程,工作区域就是在这2块磁极之间。支架是用来固定磁极并连接磁力研磨装置和进给装置的。它的一端连接磁极部分,另一端与能产生径向位移的滑块相连,使产生磁力的磁极可以沿着滑道的方向在径向自由移动。滑块沿轨道的自由移动带动支架做径向移动,从而可以根据需要自由调节磁极的位置,同时分开,同时靠近,或同时向一个方向运动。在支架上,设计安装了具有微调作用的微调手轮。由于磁力研磨过程中,加工间隙对研磨效果有很大的影响。通常情况下,要保证加工间隙在2~3mm。为了保证这一加工间隙,设计了微调手轮。在调整好两磁极间的相对距离后,靠微调手轮来调整工件和磁极间的距离误差,使误差达到最小。 磁力研磨的实际工作区域是在一个开放的磁路中进行的,为了尽可能地减小漏磁的影响,在两磁极之间装有连接架,它是由导磁的材料制成。联结架的作用是最大限度地减少漏磁,使集中在加工区域的磁力线分布更为密集。此结构设计简单,可以满足一般轴类零件的表面抛光处理。如光轴类、管类、阶梯轴和螺纹轴等的外表面抛光。
磁力研磨机操作指导书
1.0 目的 确保设备的正常运转、产品的加工精度与加工的合理性,提高生产效率和产品质量;规范安全操作,杜绝安全隐患以达到安全生产。 2.0 适用范围 适用于磁力研磨机所有操作人员。 3.0 权责 3.1 设备使用及日常保养:操作人员。 3.2 设备维修:专业技术人员。 3.3 技术指导及正确操作方法的监督:组长、主管。 4.0 工作流程: 4.1 充分了解设备的性能、结构,遵守安全生产的规程。 4.2 开机前,首先检查设备状态,确认好后才能开启设备。 4.2.1 做好日常保养检点确认; 4.2.2 确认设备是否有异常; 4.2.3 确认设备清洁状况; 4.2.4 确认来料种类。 4.3 研磨加工前研磨针清理。 4.3.1 用电子秤秤好0.6 kg研磨针; 4.3.2 将秤好的研磨针放入磁力研磨抛光机抛光筒内; 4.3.3 在滚筒内倒入清水,倒入的清水只需淹没研磨针即可; 4.3.4 在滚筒内倒入3个瓶盖的清洗液; 4.3.5 将滚筒放到磁力研磨机上旋转2分钟; 4.3.6 将滚筒拿出并倒掉筒内的清水; 4.3.7 将研磨针放到指定区域以备后续使用; 4.3.8 磁力研磨使用的研磨针在清洗过10000PCS的产品后必须重新拿出清洗干净方可再次使用; 4.3.9 磁力研磨针在使用一个星期后必行进行更换,以保证抛光效果。 4.4 设备加工操作步骤如下: 4.4.1 在磁力研磨机滚筒内注入6 kg清水。使用标杆进行测量,当水位到达标杆刻度处停止注水,此时的水量刚 好6kg。 4.4.2 将之前秤好数量且清洗干净的研磨针倒入滚筒内; 4.4.3 将一瓶盖清洗液倒入滚筒内; 4.4.4 将2000 PCS产品倒入滚筒内; 4.4.5 打开磁力研磨机电源; 4.4.6 将磁力研磨机的运行时间设定为8分钟,研磨时设备频率设置在40-50范围内; 4.4.7 按下“启动”按钮,磁力研磨机运转进行研磨加工。 4.5 磁力研磨后处理。
磨床加工方法
磨床加工方法 工件研磨前应粗洗砂轮,进行工件粗磨 平面加工 平面加工分为粗加工和精加工,粗加工时尺寸预留0.15-0.03mm,精加工尺寸到位. 1.加工前,应把工件毛刺打掉,并测其余量. 一般工件进行对称研磨. 2.研磨第一面时,对刀后应提起0.02mm,走一刀后再下刀研,磨般选择高点对刀. 3.根据工件薄决定研磨量及吸磁大小. 4.如果工件面小且厚,则吸磁力大,进入量可多,钽不能超过0.1mm 5.工件面与厚度比例比较大,则吸满磁,进刀量最多可在0.05mm,否则工件会烧伤出现泡痕. 研磨中要加酒精冷却. 6.工件面与厚度比例非常大,即薄形工,件则视情况而减小磁力,或吸磁后完全退磁.此时进入 量在0.01mm以内,且加酒精冷却.如果有变形,则用虎钳夹住研磨.另砂轮要洗粗一些,且多洗几次砂轮. 7.第二面用同样方法研磨,完成工件粗加工.然后进行精加工.方法同上,但进刀量为 0.002-0.005mm. 8.平面的平面度一般应在0.002mm以内. 9.平面上不能有浪痕,烧伤,不能磨痕错乱. 对刀 一.以工件为准 对刀前首先要洗好砂轮侧壁,底部,确定侧壁,底部洗平. 1.平面对刀,即用砂轮底部对刀. 将砂轮摇至工件表面约1mm处,再用眼睛目视砂轮底部离工件表面有一条缝即可,此时砂轮未运转.摇动工件确定未撞上砂轮.将工件表面涂上色笔,打开砂轮,然后慢慢下刀并摇动手轮,直到漆笔被擦掉,x轴归0. 工件表面研磨过,则直接研磨,未研磨过,则应提起0.02mm后再研磨. 2.侧壁对刀.用砂轮侧壁对刀. 与底部对刀差不多,当有一条缝,后打开砂轮,摇动工件,y 轴慢慢进刀,听声音或看漆笔确定是否对上刀.此种对刀法易损伤工件,且不怎么准,非特殊情况不用. 二.以基准块为准 A 基准块 将基准块放于平台上,并靠挡板上,并敲几下,使之紧贴.用细砂轮侧壁(已洗好)碰A面(基准边),如果A面不平,则可用砂轮磨平,研磨量最多可是0.05mm以内,确定A面以后,归0.基准边设置完成,工件可靠在上面进刀研磨.此方法比在工件上对刀要准,且危险程度小.
细长薄壁不锈钢管内壁磁力研磨技术的研究
细长薄壁不锈钢管内壁磁力研磨技术的研究3 华东船舶工业学院 王 艳 摘 要 分析了磁性磨料磁力研磨的机理,设计并研制了细长薄壁工件内孔研磨装置,通 过不同磁性磨料的研磨对比实验,证明了选择铝镍钴磁钢粉作为磁性磨料时,对奥氏体不锈钢管内壁具有良好的研磨作用;且通过工艺试验找出了各种因素对加工的影响规律。 Abstract In this paper ,Magnetic Abrasive Finishing (MAF )mechanism is analyzed in detail.At the same time ,thin and long tubing internal finishing apparatus is developed by the author.On the one hand ,a series of comparis on experiments using A1NiC o magnetic abrasive particles improve remarkably the in ternal finishing accuracy of austenitic stainless steel tubings.On the other hand ,a lot of technological experiments are made and the effect of each factor on the machining performance during the process in in 2vestigated. 关键词 磁力研磨 不锈钢管 表面粗糙度 1 引言 随着工业的发展,科学技术的进步,对许多产品的精度与性能提出了越来越高的要 3教育部博士学科点专项科研基金资助项目(97024834)收稿日期:1998-11-25 求。特别是近年来在半导体产业、原子能产业、医疗器械产业、航空航天产业等各种高技术产业中,各种电子零部件及光学零部件日益轻薄、短小、精密化,原器件的净化要求越来越高,随之而来的是更高的表面质量及加工精度的要求。普通研磨加工方法虽然能在然后切割浇口、冒口,即可得到完整的铸造零 件,图4所示为应用该技术而获得的齿轮和整 体叶轮铸件。 图4 铸造零件 5 结论 (1)通过工艺分析,明确了激光烧结快速 成形技术应用于精密铸造的工艺路线和突出 的工艺优势。 (2)采用覆膜树脂砂作为主要原料,适当加入环氧聚脂粉作粘结剂,获得了可供激光烧结精密铸造壳型的粉末材料。采用根据零件的CAD 设计直接进行反型烧结的方法,烧结出了精密铸造壳型。 (3)应用激光烧结精密铸造壳型和传统的砂箱铸造相结合的方法,完成了金属零件的精密铸造。 参 考 文 献 1 宫克强主编.特种铸造.北京:机械工业出版社,1982.2 梁光泽编著.实型铸造.上海:上海科学技术出版社,1986. 3 李传拭编著.造型材料新论.北京:机械工业出版社,1992. 4 冯涛,孙建民,宗贵升.用选择性烧结实现快速精密铸造. 中国机械工程,1997(5) 5 郭永卫.快速成形法及应用可能分析.航空精密制造技 术,1998(1) 6 唐亚新等.激光烧结成形及其在精铸中的应用.机械工艺 师,1998(7)
超精密研磨与抛光技术
少年易学老难成,一寸光阴不可轻- 百度文库 1 超精密研磨与抛光技术 超精密研磨与抛光技术是超精密加工技术的一种。 超精密加工技术指的是超过或达到本时代精度界限的高精度加工。超精密加工其实是一 个相对概念,而且随着工艺技术水平的普遍提高,不同年代有着不同的划分界限,但并无严格统一的标准。从现在机械加工的工艺水平来看,通常把加工误差小于0.01μm、表面粗糙度Ra 小于0.025μm 的加工称为超精密加工。 超精密加工技术起源于20 世纪60 年代初期——美国于1962 年首先研制成功了超精密加工车床。这一技术是为了适应现代高科技发展需要而兴起的,它综合运用了新发展的机械研究成果及现代电子、计算机和测量等新技术,是一种现代化的机械加工工艺。 超精密加工拥有广阔的市场需求。例如,在国防工业中,陀螺仪的加工涉及多项超精密加工技术,因为导弹系统的陀螺仪质量直接影响其命中率——据有关数据,1kg 的陀螺转子,其质量中心偏离其对称轴0.0005μm 就会引起100m 的射程误差和50m 的轨道误差;在信息产业中,计算机上的芯片、磁盘和磁头,录像机的磁鼓、复印机的感光鼓、光盘和激光头,激光打印机的多面体,喷墨打印机的喷墨头等都要靠超精密加工才能达到产品性能要求;在民用产品中,现代小型、超小型的成像设备,如微型摄像机、针孔照相机等同样依赖于超精密加工技术。 我们所说的超精密加工技术,除了超精密研磨和抛光技术外,还包括超精密切削、超精密磨削、超微细加工、光整加工和精整加工等。这几种超精密加工方法能加工出普通精密加工所无法达到的尺寸精度、形状精度及表面粗糙度。 但是,超精密切削、超精密磨削等的实现在很大程度上依赖于加工设备、加工工具,同时还受加工原理及环境因素的影响和限制,所以,现在如果想从这些方面提高加工精度,那是十分困难的。而超精密研磨和抛光技术由于具有独特加工原理,可以实现纳米级甚至原子级的加工,已成为超精密加工技术中的一个重要部分。所以,超精密研磨与抛光技术如今备受关注。 研磨、抛光是历史最悠久的传统工艺。古代石器、玉器及古铜镜等就是通过研磨、抛光制造出来的。自古至今,研磨抛光一直是精密的加工手段,但很多年来其发展是很缓慢的。直到上世纪五十年代,飞速发展的电子工业才为古老的研磨抛光技术带来新的曙光。 超精密研磨和抛光技术,一般特指选用粒径只有几纳米的研磨微粉作为研磨磨料,将其
说明磁力研磨机简介-磁力抛光机
说明磁力研磨机简介 磁力研磨机是在传统研磨机的不足与缺陷上进行改革创新,使精密五金工件内孔、死角、细小夹缝起到明显较好的抛光研磨去处毛刺的效果。采用磁场力量传导至不锈钢磨针使工件作高频率旋转运动;最终达到精密工件快速去除毛刺,污垢的效果。 产品用途 ● 去除批锋毛边毛刺精密研磨。 ● 金饰业打磨洗净工作。 ● 成品表面抛光处理。 ● 去除氧化薄膜工作。 ● 锈蚀去除处理。 ● 烧结痕迹处理。 适用行业及范围 1.精密冲压零件 2.不锈钢零件,螺丝。 3.镁铝压铸零件 4 .锌铝压铸零件 5.精密弹簧,弹片零件 6.电子,计算机,通信零件 7.走心,走刀,CNC自动车床零件 8.航天,医疗零件 适用于金,银,铜,铝,锌,镁,铁,不锈钢等金属类与硬质塑料等非金属类工件的研磨抛光。如:金银首饰、时尚配饰、电子产品金属制件,手机壳,相机壳,精密螺栓、形状复杂的金属制件、文具配件、仪表仪器配 工作原理 磁力研磨机是利用神奇磁场跳跃的力量传导至不锈钢针、磨针、磨材;产生夹带工件高频率旋转流动、振动、换向翻滚,划过工件表面,早工件内孔,内外牙及表面、凹凸面摩擦,达到清洗、去油垢杂质,去除毛刺、研磨等精密抛光效果。 功能介绍 1、调频:用户可根据自身工件大小来调节抛光机运行速度,批量抛光,效果更佳。 2、正反转控制:用户按照自身需求,设定工件抛光正转为多长时间,反转为多长时间,提高抛光效率。 3、定时关机:根据工件大小,材质的不同,用户可设定工件抛光的时间段,时间到了抛光机自动停止运行,给用户带来更大的方便。 特点性能
1:卓越快速去除工件周边毛刺。包括号细小内孔、管孔、夹缝死角。 2:研磨后的工件不影响原来精度;形状和尺寸都不会有变化。表面粗糙度值可达到Ra0.1- Ra0.01,表面展现光亮金属光泽。 3:时间短。每次处理时间5-20分钟。 4:操作方便简单;工件一次性批量处理,成本极低;无污染;不锈钢针为长久性磨材。 5:轻铁类金属、非铁类金属、硬质塑料等精密零件成品,去除毛边、倒角、抛光、洗净等精密研磨工作一次完成。 6:不规则状零件、孔内、管内、死角、夹缝等皆可研磨加工。 7:加工速度快,操作简易安全,成本低,无须任何耗材。 8:成品加工后绝不变形,绝不损伤表面,绝不影响精度。 9:机种齐全,可设计专用机种。 磁力研磨机与传统研磨机比较 磁力研磨机优点 1、相比其他布轮抛光机等抛光设备,磁力研磨机可批量工件抛光处理,完成抛光后可用筛网批量和钢针分离开来,大大提高工作效率和抛光效果。 2、磁力研磨机针对小五金件,小饰品等死角,内孔处理效果极佳。可达到清除灰尘,去除毛刺,提高产品表面光亮度,这是其他类型抛光设备无法比拟的特点。 3、磁力研磨机操作简单,可一人同时操作多台设备,节省成本。 4、磁力研磨机采用抛光液和钢针,再加上适当自来水来批量抛光工件,不带酸碱性的污水便于处理。 传统研磨机不足与缺陷 1:因为采用石头形状磨料,根本不能做到对内孔,凹凸面、死角、内外螺纹的清洗抛光。只能是表面上的一些处理。 2:研磨抛光时间慢一般要几个小时工作才能完成。 3:成本高,采用石头形状磨料,经过一段时间研磨,需要更换。 4:容易损坏工件,使工件变形,影响精密度 工件使用效果 工件经磁力研磨机处理后表面呈原金属光泽,极具视觉效果;还可释放一部分工件内应力,提高工件机械性能;强化工件表面质量,提高表面性能。 操作方法 调试: 开启机器后,将工件由少倒多放入抛光桶,工件的多少和重量和工件的体型有及到的关系,所以工件慢慢放入到增加,倒工件旋转减慢,但是不可以工件不动,当工件不动旋转时,抛光出来的产品液将不均匀,抛光时间也
磁力研磨
数控磁性研磨装置的研制 苗青甫机教012班 摘要: 概述了磁性研磨加工技术发展,阐述了磁性研磨加工的原理、装置及特点,主要介绍了一种数控磁性研磨机床装置,着重介绍其原理、结构、组成。该机床通过数控编程控制工具磁极与工件的相对运动并使其保持一定间隙,工具磁极高速旋转,利用吸在工具磁极上的磁性磨料对工件表面进行光整加工。 关键词: 磁性研磨磁性磨粒磁力刷磁极电磁屏蔽 Abstract: Grind the processing technical development after summing up magnetic, has explained that grinds the principle , device and characteristic processed in magnetic, introduce a kind of numerical control magnetic grind the lathe device , introduce its principle , structure , make up emphatically mainly. Lathe this through numerical control programming control tool magnetic pole and relative motion and make it keep certain interval of work piece, tool magnetic pole rotate at a high speed, is it suck magnetic abrasive at the magnetic pole exactly process the light to the work piece surface in tool to utilize. Keywords: Magnetic grinding Magnetic grit The magnetic force brushing Magnetic pole Electromagnetic shielding 引言 随着工业的发展,对零件的表面光整加工提出越来越高的要求。在国内外精加工领域中,人们正通过各种渠道,借助多种能量形式,探索新的工艺途径。磁性研磨加工就是人们把磁场应用于传统的研磨技术中,开发出的一种新的研磨技术。 磁性研磨是一种利用磁场中的磁性磨料对具有相对运动的工件表面进行光整加工的新技术,具有表面质量好、适应性能广泛的优点。利用在磁场中的磁性磨料所产生的磁力进行磁性研磨是机械零件表面光整加工的又一新工艺、新技术。目前已对零件的内圆面、外圆面、平面、成型面等表面进行了磁性研磨的开发和研究。从原理上讲,它可以对任何几何形状的表面进行精密光整加工,因此磁性研磨这一新工艺有着十分广阔的应用前景和很好的经济效益。 1 磁性研磨技术的发展历史
磁力研磨机操作规程
SC-04 磁力研磨机操作规程 操作工应认真阅读使用说明书,并经培训合格后方可上岗。 一、设备名称、型号规格、编号 名称:磁力研磨机;型号规格:KH-935;设备编号:HM/S-04 二、操作程序 1.将磨材(不锈钢针)约2KG放入塑胶桶内。 2.放入研磨稀释水(研磨液与水配比1:50),水量应盖过工件及防止针跳出。 3.放入工件(加工物)及放入机器研磨槽中。(容器、时间,速度可随工件的材质、孔径、大小而改变,随着实践,会逐步制订各参数设定的指导意见)。 4.开启启动开关,设备开始运转,自动停止。(运转中,须产出水流,才有效果,如果水是静止的或是缓慢流动就表示工件太多,须放少些工件) 5.研磨完成后拿起容器(研磨完成拿起容器时,务必将机器开动,在运转中取出容器,此时会让工件及针产生脱磁效果,以利分离及工件脱磁) 6.工件及针分离。 7.用水清洗工件,并把研磨针清洗干净。 8.晾干或烘干工件。 三、面板操作说明 1.起动开关(START):运转起动开关按钮,按下时间开始运转并开始计时,即开始研磨。 2.停止开关(STOP):停止运转开关按钮,停止运转并停止计时并归零,研磨停止。 3.电源开闭(POWER SOURCE):电源切于ON时,则电源起动指示灯亮,如长期不使用时请将电源切于OFF状态。机器内部热交换器、电风扇起动运转,有风扇声属于正常。 4.程序时间1(TIMER1)的动作时间设定,此计时间器设定第一时间(T1)的动作时间长短。本计时器单位为分钟(M),设
定方法于数字按钮键上下按钮连续调整即可,如动作到设定值时则自动跳至TIMER2(T2)继续运转研磨。 程序时间1(TIMER1、,此开关为设定TIMER1动作时间马达运转方向,切于 REV时为 C.C.W.,切于FWD 时为马达正转方向,也就是顺时钟方向研磨C.W.。 5.TIMER2)的动作时间设定,此计时器设定第二时间(TIMER2)的时间长短,本计时器单位为分钟(M),设定方法于数字按键上下按钮连续调整就可以设定,如设定数值为15,其代表15分钟,上部份显示数值为已经运转的时间,如动作到设定值时,则停止运转并归零。 程序时间2(TIMER2、,此开关为设定TIMER2动作时马达运转方向,切于 REV时为马 FWD 定,设定动作可以正转或反转,也就是设定研磨的方向。 6.频率显示器(FREQ、HZ DISPLAY)及错误信息显示(FAULT INFORMATION): 频率显示器显示设定运转频率值,设定范围是(10~60)HZ。 错误信息显示:按说明书上P13的表“异常发生及处理方法”执行。 本设定显示其他按钮为内部程式参数规划用,请勿乱按,以免改变程序而故障。 7.研磨机完成警报(FINISHED ALARM) 当研磨机完成后,就是总时间计时完成后,完成研磨警示灯(LAMP)闪烁、蜂鸣器(BUZZER)发出声音,此功能3分钟 后自动停止。蜂鸣器发声的功能可选择性使用。 请勿电源开关做急促切换,这样会引发蜂鸣器、警示灯动作,易损坏变频器及其他电器零件。 注意电气零件的防水,湿手切勿操作电气开关。 8. 程序时间(TIMER1)(TIMER2)的运转速度(频率)调整钮: 此调整旋钮为调整设TIMER1和TIMER2的频率,设定范围是(10~60)HZ。 四、脱磁方法 产品研磨后,当工件为导磁材料时务必进行脱磁! 脱磁操作步骤: 1.当研磨完成,机器于停机状态,如欲达脱磁效果,请再按[启动按钮]START,就是让机器于研磨状态下,取下工件(容器),即有脱磁效果。 2.当取下工件(容器)后,按[停止按钮]STOP,让机器停止,以上步骤计时器及其他功能皆正常运作,当STOP时,则恢复停机状态
磁力研磨抛光
磁力研磨抛光在模具自由曲面中的机械和技术研究 关键词:模具自由曲面磁力研磨抛光轨迹生成 摘要:目前为了解决自由曲面抛光的问题,根据对模具抛光弯曲表面的要求,结合电磁场理论,采用磁性磨料,借助磁力完成了模具自由弯曲表面的抛光,引进了在磁场中抛光过程的新工艺,它开始陈述了磁场力的加工特点,分析了抛光工艺过程的主要参数,并实现了对磁性磨料研磨运动轨迹的理解和产生的讨论,提出了通过磁性研磨抛光得到了移除弯曲表面的处理方法。 引言 目前,模具的形状正在变得越来越复杂,其弯曲表面所占的比例在持续增加,为此对模具加工技术提出了更高的要求来保证更高的制造精确度,表面质量和审美表面。随着数值控制、电火花加工和CAD/CAM系统及自动化的应用,这些技术主要是认为实现模具弯曲表面的抛光。但是目前模具抛光的加工过程,主要是依赖于有经验的操作员。抛光时间占据了整个时间的百分之30-50,它变成了模具制造的瓶颈。这就意味着熟练地工作者是不可缺少的,同时这个过程是很费时费力的,并且在抛光后表面质量的稳定性是很难保证的,特别是在抛光的最后阶段,若有一些事情出错,可能会引起整个模具的废弃,这样可能会引起更大的经济损失。 自由表面是复杂的、没有规律的、没有旋转的表面,通常也很难用数学公式和机械运动规则精确地描述。同时磁力抛光有很多优势,比如有很好的灵活性,自我调节控制性等。因此这样能够使复杂形状的表面有更小的粗糙度。通过在这篇文章里介绍的模具磁性研磨抛光的特点,分析了影响磁性研磨抛光及其轨迹的主要参数,提出了在磁性研磨抛光中除掉多余表面得到平整表面的方法。 磁性研磨抛光的原理和特点。磁性研磨抛光的方法是采用磁性研磨剂,通过磁场中磁力的作用,磁性研磨剂工作在表面,同时保持在模具表面和磁极之间间断工作。因此在制造过程中磁粒被有序的安排在沿着磁力线周围。同时形成了磁性刷,在磁力作用下围绕在模具表面。由于磁场和被加工件的旋转会使磁性刷和被加工件的表面产生一个相关的运动,这样可以用磁性研磨剂来抛光被加工件表面。通常在抛光时用一些仪器,例如数字控制磨机或者加工中心。这个基本方法在下图展示:磁性研磨抛光的特点是:1.在加工间隙中,磨粒占据着有磁力的磨粒刷,它的变化随着被加工件的表面轮廓的变化而变化,被加工件的表面轮廓模型其围绕、旋转并不受表面形式的束缚。2.由于在被加工件与磁极之间有一定的间距,因此能保证有一定的灵活性,因此可以应用于任意轮廓的表面。3.因为磁力线可以渗入像X射线的物体,因此磁性颗粒可以进入那些普通刀具不能到达的地方,例如模具腔内,一些弯曲管状体的内部,一些小的瓶颈容器等。4.通过改变外部磁体来改变磁力线的方向,通过固定的表面轨道来控制磁性研磨抛光,从而完成对那些过去不能处理到的领域的抛光。 分析磁性研磨抛光的机制与过程 弯曲表面的磁性研磨抛光。弯曲表面抛光设备通常有三个部分组成,工具是磁极,磁性研磨剂和磁力线圈。磁性研磨剂在电子磁力头的吸引下,通过磁场的形式,安排在刷子的形状里。由于这些抛光工具有很好的灵活性,因此可以更好地与弯曲表面相接触,很适合弯曲表面的抛光。磁头主要像图2那样用在曲面的抛光,这个磁头是个球形,,同时被加工件是个自由曲面,用这种方法保持磁极和旋转车床的中心,使磁极的底部和被加工件保持一定距离,这个距离主要是把研磨剂填充在抛光工具和被加工件之间。如果被加工件表面有很多凹凸面,磁性研磨剂随着表面的改变而改变。甚至被加工件的表面是复杂的自由表面,可以控制一定程度的车床自己的运动轨迹,这也可以使复杂的自由表面得到更好地抛光效果,一些普通的磨削方法不能加工出如此粗糙度如此小的表面。
磁力研磨特点及其关键技术
磁力研磨特点及其关键技术 引言 随着CAD/CAM技术的快速发展,复杂形状零件的加工方法逐渐倍受国内外的关注,尤其在航空航天、船舶、汽车和国防等领域中,许多核心零件都具有复杂的曲面。由于复杂曲面不能由初等解析曲面组成,因此复杂形状零件的复杂曲面的高效和高质量加工一直是国内外制造领域中的难题。手工研磨抛光是最常用的光整加工方法,但该方法的劳动强度大,生产效率低,产品的质量没有保障。另外,由于模具型腔形状复杂,很多研磨抛光方法都有一定局限性,难以广泛地推广使用。现有的复杂曲面光整加工方法存在着诸多弊端,因此,需要一种更加适用于复杂曲面的光整加工方法。磁力研磨加工是把磁场应用于传统的研磨技术中开发出的一种新的有效的光整加工方法之一。这种加工方法由于其柔性和自适应性,适合于平面、球面、圆 柱面和其它复杂形状零件的加工,利于实现光整加工的自动化。因此,磁性研磨加工技术越来越得到重视。 1 磁研磨技术的研究现状 磁力研磨加工技术,最早是由前苏联工程师Kargolow于1938年提出,泛指利用辅助磁场的作用,进行精密研磨的一种工艺方法。之后,前苏联、保加利亚、日本等国家对其进行了深人的研究。迄今为
止,国外磁力研磨技术已成功地应用在多个方面.如不锈钢管和净气瓶的内壁研磨,研磨修整超硬磨料砂轮,研磨塑料透镜,细长轴类陶瓷加工,缝纫机零件等的去毛刺与抛光加工,提高刃口的使用性能等。国内对于磁力研磨的研究工作是近二十年来才开始进行的,经过这些年的研究,取得了一些有价值的研究成果,例如上海交通大学进行了物流管道内表面磁力研磨的回转磁场的设计H1;太原理工大学研制了粘结法和热压烧结法制备磁性磨料的工艺,并深入研究了磁力研磨的磨削机理;西安工业学院进行了磁力研磨加工的数值仿真,以及磁屏蔽对内圆磁力研磨加工影响的研究。山东理工大学自行研制了三坐标数字化加工控制磁力研磨机床。由于国内起步比较晚,在理论和实验等方面还和国外有不小的差距,目前还主要处在实验研究的阶段,实际应用的不多,而且深度与国外相比还不够博。因此,本文提出一种复杂曲面磁力研磨加工方法,其加工工具具有磁性磨料的自动更新等功能。 2 加工原理及特点 2.1 加工原理 磁力研磨加工是在强磁场作用下,填充在磁场中的磁性磨料被沿着磁力线的方向排列起来,吸附在磁极上形成“磨料刷”,并对工件表面产生一定的压力,磁极在带动“磨料刷”旋转的同时,保持一定的间隙沿工件表面移动,从而实现对工件表面的光整加工。在加工中
超精密研磨技术的现状及发展趋势_方海生
[综述?专论] 收稿日期:2006-10-18 基金项目:国家自然科学基金重点项目(50535040) 作者简介:方海生(1970-),男,浙江舟山人,浙江工业大学工程硕士,浙江机电职业技术学院实验师,研究方向为超精密加工。 超精密研磨技术的现状及发展趋势 方海生1,2,胡涤新1,邓乾发1,袁巨龙1 (1.浙江工业大学超精密加工研究中心,浙江杭州 310014; 2.浙江机电职业技术学院,浙江杭州 310053) 摘 要:概述了最近超精密研磨技术的研究动态,介绍了研磨技术的原理、应用和优势,同时介绍了课题组研制的基于修正环在线修整抛光盘技术及专家数据库系统控制的Nanopoli -100智能型纳米级抛光机,结合该领域的最新研究成果,提出了其向高精度、高效率发展的方向。 关 键 词:研磨技术;超精密;Nano po li-100智能型研磨抛光机;发展动向 中图分类号:T G 580 文献标志码:A 文章编号:1005-2895(2007)04-0009-04 0 引 言 研磨是一种重要的精密和超精密加工方法。其定义可以表述为:利用磨具通过磨料作用于工件表面,进行微量加工的过程。根据加工方法的机理和特点,最基本的加工方法可以分为:去除加工、结合加工和变形加工3大类[1]。然而,在最新的多性能复杂形态的元件加工中,往往是上述几种加工法的复合作用。 1 微量材料去除的机械作用及化学作用 设想材料去除的最小单位是1层原子的话,那么,最基本的材料去除是将表面的一层原子与内部的原子切开。机械加工必然残留有加工变质层,加工中还伴随着化学反应等复杂现象[2,3],材料去除的原理是从一层原子到数层原子乃至数十层原子几种状态的复合。 图1 研磨加工的模型 图1所示的是磨粒研磨加工的模型[4]。单个磨粒的磨削模型,可以用磨粒对工件的机械作用的动作来描述,即按摩擦-耕犁-切削的动作顺序进行。在加工中的化学反应结果对材料的去除及减小加工变质层可能是有利的 [5,6] 。 2 研磨技术的发展 研磨加工不仅向更高的加工精度发展,而且其加工质量也在不断提高,且几乎可以加工任何固态材料。许多人从事研磨加工技术,研究的宗旨是进一步提高研磨加工效率、加工精度,降低加工成本[7]。 目前,国内外研磨加工主要还是采用散粒磨料在慢速研磨机上研磨。其特点是加工精度高、加工设备简单、投资少,但是加工精度不稳定、加工成本高、效率低。3 几种纳米级研磨加工方法3.1 弹性发射加工 1-十字;2-数控主轴;3-载荷支撑;4-聚亚酯球;5-工件;6-橡胶垫;7-底座;8-工作台;9-悬浮液;10-容器;11-重心;12-无级变速机 图2 EEM 装置示意图 弹性发射加工装置(Elastic Em ission Machining , 第25卷第4期2007年8月 轻工机械 Light I ndustry Machinery Vol.25No.4 Aug.2007
手工研磨基本方法探析
手工研磨基本方法探析 摘要:研磨是一种精密的切削加工方法,对于配合间隙须长期严格保持不变,需要获得很高尺寸准确度,要求较高的机件接触部位密贴等,均需在研磨加工中予以实现。文章就研磨的必要性、研磨原理、研磨剂、手工研磨等内容进行分析。 关键词:研磨;原理;研磨剂;手工研磨随着生产的发展,大中小企业与日俱增。各种液压设备、压缩空气设备、风动工具、柴油机、汽车、轴承、工具、量具等在国民经济的各个部门中越来越多的被生产或使用,因此在制造和修配方面需要采用研磨的机件也越来越多。尽管磨削技术有了飞跃的发展,但对于更高的技术要求也是力所不及的。在修理工作或在研磨机上无法进行的、研磨结构复杂的零件以及机器磨削难以达到工件精度要求的均需手工研磨。 1 研磨的必要性 在科学技术发展的今天,各种油压设备、压缩空气设备、风动工具、柴油机、汽车、轴承、工具、量具等生产与日俱增,它们越来越广泛的应用于工农业生产中。如油压设备上的油泵体和柱塞、叶片和转子、油缸和活塞、导阀、针阀、滑阀和阀体;压缩空气设备和风动工具上的滑阀、锥形阀、板阀和阀体;柴油机上喷油系统中油泵、油嘴、油泵上的套筒和芯子、油针和油针体;汽车中的双曲线齿轮;滚动轴承的内外座圈、滚珠、滚柱、滚针;量具和刀具中的块规、卡尺、千分尺、样板、铰刀、拉刀等,均需很高的尺寸准确度、形状准确度和很低的表面粗糙度。还有的机件在转动或滑动的情况下,对于间隙的配合要求严格,同时必须长期保持不变,所以在制造和修配方面,对机器各部分机件的精度要求也随之提高。对这些需要获得很高尺寸的准确度、要求较高的机件接触部位等,均需在研磨加工中予以实现。可以说研磨是加工精密零件的主要方法之一。 2 研磨的原理 研磨是比磨削更进一步的精密切削加工方法中的一种。研磨一般是将工件预先经过适当加工,如精车、磨削、铰削、涨孔、挤压、冲压、拉削或切齿等工序以后做最后加工的工序。 研磨是用磨粒通过研具对工件进行微量切削的一种工艺过程。研磨是通过研具在一定压力下与工件加工面作复杂的相对运动而完成的。研具和工件之间的磨粒与研磨剂在相对运动中,分别起机械切削作用和物理、化学作用,使磨粒能从工件表面上切去极薄的一层材料,从而得到极高的尺寸精度和极细的表面粗糙度。工作时在研具和工件之间涂以研磨剂,并施以一定的压力,在一定的相对运动的速度下,二者不断地改变方向作滑动和滚动,使研磨剂与工件表面产生易被磨粒刮去的氧化膜。由于磨粒的位置在不断地变化,得到极为复杂的运动轨迹,使磨粒的一部分嵌入研磨的工具内,这时就像无数把刀子一样,在工件的表面上产生切削作用,这样使工件在研磨前的加工中所留下来的几何形状误差和线痕,得到修整和消除。同时,由于磨料颗粒细小,所以切下来的切屑也特别细小,因此工件由于塑性变形而产生的微观的形状误差变小,位置误差变小,从而获得极其准确的几何形状和在其它机械加工方法中不易达到的表面粗糙度,又能保证极小的尺寸公差。 2.1 研磨过程及研磨余量 一般研磨过程大致分为粗研磨和精研磨两种。粗研磨主要是研去加工余量,精研磨主要用来降低表面粗糙度和提高尺寸精度。