甲醇催化燃烧
甲醇的催化氧化方程式

甲醇的催化氧化过程
一、氧气在催化剂表面吸附并分解成氧原子
在催化氧化过程中,氧气首先在催化剂表面吸附并分解成氧原子。
这个过程是由催化剂的活性表面完成的,它提供了高能量环境,使氧气更容易活化。
氧原子是由单线态氧分子(O2)分解得到的,这个过程可以表示为:
O2(气态)+ e- + * -> 2O(催化剂表面)
二、甲醇在催化剂表面吸附并发生氧化反应,生成甲醛和水
甲醇在催化剂表面吸附并发生氧化反应,生成甲醛和水。
这个过程可以表示为:
CH3OH(液态)+ O(催化剂表面)-> HCHO(气态)+ H2O(液态)
在这个过程中,甲醇被氧化成甲醛,同时消耗了水。
这个反应是放热的,可以提供足够的能量使反应继续进行。
三、甲醛在催化剂表面吸附并发生氧化反应,生成二甲酸和水
甲醛在催化剂表面吸附并发生氧化反应,生成二甲酸和水。
这个过程可以表示为:
HCHO(气态)+ O(催化剂表面)-> HCOOH(液态)+ H2O(液态)
在这个过程中,甲醛被进一步氧化成二甲酸,同时再消耗一部分水。
这个反应同样是放热的,可以提供足够的能量使反应继续进行。
四、二甲酸在催化剂表面吸附并发生氧化反应,生成二氧化碳和水
二甲酸在催化剂表面吸附并发生氧化反应,生成二氧化碳和水。
这个过程可以表示为:
HCOOH(液态)+ O(催化剂表面)-> CO2(气态)+ H2O(液态)
在这个过程中,二甲酸被彻底氧化成二氧化碳和水。
这个反应同样是放热的,可以提供足够的能量使反应继续进行。
催化燃烧设备的工作原理

催化燃烧设备的工作原理催化燃烧设备是利用化学反应的原理,将有害气体转化为无害气体的装置。
其紧要原理是通过在气体通道中引入催化剂,使得有害气体在催化剂的作用下发生化学反应,以达到去除污染物的目的。
本文将认真介绍催化燃烧设备的工作原理、结构和应用。
催化燃烧设备的工作原理催化燃烧设备的紧要工作原理是通过氧化还原反应(即化学燃烧)将有害气体转化为无害气体。
在化学燃烧过程中,催化剂从催化剂床中吸取氧气并将其供应应有害气体,使其发生氧化反应。
因此,催化剂是催化燃烧设备最紧要的构成部分。
在催化剂的作用下,有害气体化合物(如甲烷、乙烷、苯等)与氧气发生反应,生成二氧化碳和水。
这些无害的反应产物可以通过工业冷却水、冷凝等装置排出。
需要注意的是,在催化燃烧设备中,尽管催化剂是紧要的构成部分,但其不参加实际反应过程。
催化剂只是作为反应过程的触媒,不被消耗或更改。
催化燃烧设备的结构催化燃烧设备的结构特别简单,通常包括6个紧要构成部分:1.气体通道:气体流经该通道,与催化剂发生反应;2.催化剂床:催化剂通常是金属或氧化物,其紧要作用是供应合适的化学反应条件;3.掌控装置:用于掌控工艺参数,保证设备运行效果;4.辅佑襄助燃料供应装置:供应额外的燃料(如天然气、甲醇等),以支持反应过程;5.加热装置:维持设备的高温工作状态;6.排放管道:排放产物和未反应的物质。
通常情况下,催化燃烧设备的外表和其他的反应设备无异。
不过依据实际需要,一些设备还可能带有掌控仪表、防爆设备和注水设备等。
催化燃烧设备的应用由于催化燃烧设备具有高效、节能、绿色、应用等特点,因此在各大领域的应用比比皆是。
例如,在工业领域,催化燃烧设备能够对含有苯、酚、甲苯、甲醛等危害性气体的废气进行处理,避开对大气环境的污染。
在烟草加工产业中,也常使用催化燃烧设备去除烟草烤房中的有害化学物质。
此外,催化燃烧设备还广泛应用于锅炉烟气整治、污水处理等领域,成为优化环境、净化大气的紧要设备。
我厂低温甲醇洗尾气中CO处理措施探讨

81我公司为年产100万吨甲醇项目,其中净化装置采用大连理工大学低温甲醇洗净化技术,其岗位任务是:脱除变换气中的H 2S、COS、CS 2等对甲醇合成有害的气体,同时也脱除变换气中带入的饱和H 2O制得:CO 2 <3%(mol)、 总硫<0.1ppm(mol)的合格净化气,满足甲醇合成工段的要求。
富甲醇再生的酸性气组成:H 2S ≥35%(vol.%)为硫回收送出合格的酸性气。
尾气放空筒中排出尾气:符合GB16297-1996《大气污染物综合排放标准》,甲醇含量<190mg/m 3,总硫<20mg/Nm 3(50米高度排放)。
一、解决尾气中CO含量偏高问题的处理措施整体装置于2010年10月建成开车并顺利投产,低温甲醇洗系统实际运行工况达到设计指标。
低温甲醇洗放空筒中排出尾气除主要成份CO 2、N 2外,还含有少量CO、甲醇、H 2、硫化氢等可燃类物质。
其中尾气中的CO含量偏高,经放空筒排放大气后,容易沉积地面,导致生产现场界区内的可燃气体报警仪报警。
本文就解决尾气中CO含量偏高问题的处理措施进行整理。
1.对放空筒进行改造,更换放空筒地点。
将放空筒位置由目前低温甲醇洗现场迁移至距离中心厂区偏远的位置,重新进行配管,并且将放空筒加高至85米。
2.循环气压缩机技改,降低V3002和V3003压力,加大循环闪蒸量。
从工艺流程分析放空尾气中CO、H 2等可燃气体来源,是V3002(1#循环气闪蒸罐)和V3003(2#循环气闪蒸罐)运行压力较高,闪蒸不彻底,最终进入低甲T3002和T3003,随塔顶解吸气进入放空尾气。
循环气压缩机C3001A/B由单机改为双机试运行,机组二段出口活塞杆温度逐步升高至135℃,不满足长期运行条件。
随即联系机组厂家并进行升级改造:(1)对一、二级填料环材质由原普通4F材料升级为日本进口料,升级后填料环的密封性能及自润滑性能均高于原材质,能够有效提高填料整体密封性能,并减小填料环与活塞杆摩擦力,从而达到降低活塞杆温度的目的。
甲醇催化氧化

甲醇催化氧化
甲醇催化氧化是一种常见的有机合成反应,它指的是在甲醇作为起始原料的条件下,通过催化剂的作用,使甲醇在一定的条件下氧化成其他产物。
甲醇催化氧化一般包括一步氧化反应和多步氧化反应。
一步氧化反应指的是将甲醇和氧气在一定的催化剂作用下,直接氧化成其他产物;而多步氧化反应则是在一定的催化剂的作用下,先将甲醇氧化成中间产物,再将中间产物氧化成最终产物。
甲醇催化氧化可以分为有机物的催化氧化反应和金属的催化氧化反应。
有机物的催化氧化反应是指在有机物的催化剂的作用下,将甲醇氧化成其他有机物的反应,例如有机酸、醛、酮、醇等,其中常见的催化剂有碳酸酯、醋酸、酰胺等。
而金属的催化氧化则是指在金属催化剂的作用下,将甲醇氧化成其他有机物,例如醇、醛、酮、酯等,其中常见的金属催化剂有银氧化物、铜氧化物等。
甲醇催化氧化反应的条件是温度、压力和催化剂的作用。
一般情况下,甲醇催化氧化反应的温度范围一般在100-400℃之间,不同的反应所需的温度是不同的,一般要根据实验来确定。
甲醇催化氧化反应的压力一般在1-5MPa 之间,催化剂的选择则是根据反应的工艺要求来确定的,
一般甲醇催化氧化反应中使用的催化剂有银、铜、铁、钯、钴和铬等。
甲醇催化氧化反应是一种重要的有机合成反应,它可以用于制备一系列有机物,如醇、醛、酮、酯、酸等,是有机合成中不可或缺的重要方法。
甲醇催化氧化反应的反应条件要求较为严格,但是反应的效率也比较高,可以大大减少合成时间,并且可以得到高纯度的产物,因此,甲醇催化氧化反应在有机合成中有着极其重要的作用。
用于甲醇生产的煤矿瓦斯气的除氧工艺

用于甲醇生产的煤矿瓦斯气的除氧工艺技术开发与应用 陶鹏万,王晓东(西南化工研究设计院,成都 610225)摘要:煤矿瓦斯气是煤矿伴生气,当其用作化工原料如生产甲醇时,必须将瓦斯气中的甲烷浓缩。
由于其含有氧,给浓缩工艺的安全性造成危害,因此在浓缩之前必须将氧除去。
本文提出了催化燃烧除氧工艺及非催化燃烧除氧工艺,并推荐让瓦斯气通过灼热焦炭的非催化燃烧除氧工艺。
该工艺既脱除了氧,对甲醇生产来讲又给原料气补了碳,可改善生产甲醇原料气的氢碳比,提高甲醇的产量。
关键词:煤矿瓦斯气;甲醇;脱氧;焦炭中图分类号:TQ21 文献标识码:B 文章编号:100129219(2002)03225203收稿日期:2002203205;作者简介:陶鹏万(1941-),男,教授级高工0 前言煤矿瓦斯气是煤矿伴生气,每立方米煤可产瓦斯气15~30m 3。
其典型组成为:CH 420%~30%、N 250%~60%、O 2+Ar 12%~18%。
有的煤矿瓦斯气CH 4含量高达40%以上。
煤矿瓦斯气爆炸是煤矿几大公害之一,但煤矿瓦斯气因含CH 4可作燃料,也可作为化工原料。
对用作化工原料的瓦斯气必须将甲烷浓缩到比较高的浓度。
专利CN 85103557[1]中提出了采用变压吸附工艺浓缩瓦斯气中甲烷的方法,其要求顺向减压步骤释放的废气中所含甲烷浓度必须低于5%,一般控制在011%~3%,以保证运转过程的安全性。
甲烷在空气中的爆炸极限为5%~15%,所以在从瓦斯气中浓缩甲烷的操作过程中,很难既保证产品高的甲烷浓度及高的收率,又保证释放废气中甲烷浓度小于5%。
因此当瓦斯气作为生产甲醇等的化工原料时,在将瓦斯气中的甲烷浓缩之前,必须先除掉其中的氧,以保证安全操作。
为此提出了两种除氧工艺,即催化燃烧除氧工艺及非催化燃烧除氧工艺。
1 催化燃烧除氧工艺利用甲烷和氧燃烧而除去瓦斯气中的氧,其主要反应为: CH 4+2O 2=CO 2+2H 2O (1) CH 4+115O 2=CO +2H 2O(2)上述反应采用的催化剂可以是负载型的钯、铂催化剂,也可以是钙钛矿型复合金属氧化物等非贵金属催化剂。
煤制天然气低温甲醇洗废气处理工艺

煤制天然气低温甲醇洗废气处理工艺摘要:甲醇洗废气处理工艺是以煤制天然气为原料,采用加氢反应器或水解塔,经过预处理,得到CO2、H2O、部分水蒸气及非甲烷总烃等有机气体。
主要污染物是氨或氮。
氨气在高温时氧化为甲烷。
经氨化处理后,CO排放量减少60%~70%左右,剩余甲烷部分在催化燃烧装置中进行焚烧处置。
废气处理工艺主要包括脱硫脱氮脱臭和催化氧化两个步骤,是为了降低污染物排放浓度或者是为了去除部分可吸入颗粒物。
关键词:煤制天然气;低温甲醇洗废气;处理工艺一、引言煤制天然气(Synthetic Natural Gas)是一种清洁能源,目前已成为中国能源市场重要组成部分。
由于煤制天然气(CNG)具有较高的经济和环境效益,成为当前备受关注的一种清洁能源。
我国的煤制天然气产业在发展过程中由于缺乏相关标准和规范,严重污染环境,并严重威胁着人民群众生产生活安全。
目前国内天然气市场价格远远低于国外天然气的价格,给我国带来了严重的环境压力,影响了国民经济的可持续发展。
我国对环境保护的要求越来越严格。
对于煤化工而言,不仅是对煤炭的清洁高效利用、优化能源结构、保护环境等方面具有重要意义,同时也对节能减排具有重要意义。
煤制天然气项目在生产过程中会产生一定的废气,其中甲醇洗工艺的废气中含有大量有机废气。
为了降低有害气体(VOCs)排放浓度,防止对环境造成污染和破坏,有必要对其进行处理与治理。
本文对低温甲醇洗废气进行了工艺设计与设备选择,及对工艺运行情况进行评价。
(一)设计方案低温甲醇洗的有机废气通过高温高压下的闪蒸、冷凝、吸附等手段,实现有机废气的净化。
低温甲醇洗的有机废气经过闪蒸后会降低为为1.7万-2.4万(mol/m3),分子量为0.68万-1.6万(mol/m3)的沸石溶液进入 UV吸收塔进行吸收处理后,产生约2.8万 mg/m3 VOCs (VOCs浓度:80 mg/m3)。
UV吸收塔采用中空圆筒造型的不锈钢圆筒,中心设1对排气筒,底部设吸附层对高、低浓度有机废气进行收集。
甲醇的生产工艺流程设计
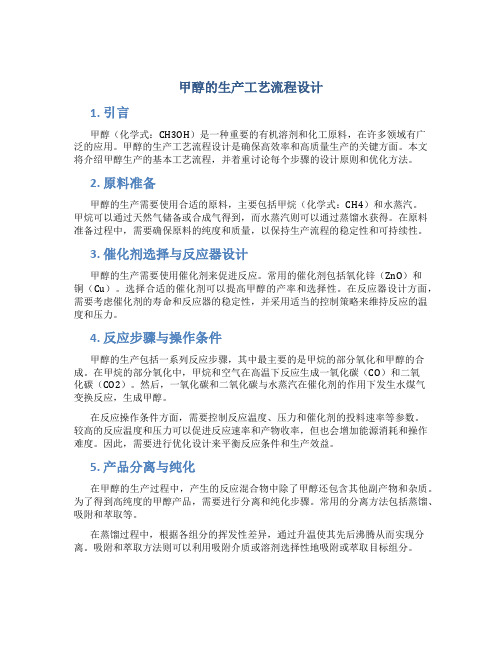
甲醇的生产工艺流程设计1. 引言甲醇(化学式:CH3OH)是一种重要的有机溶剂和化工原料,在许多领域有广泛的应用。
甲醇的生产工艺流程设计是确保高效率和高质量生产的关键方面。
本文将介绍甲醇生产的基本工艺流程,并着重讨论每个步骤的设计原则和优化方法。
2. 原料准备甲醇的生产需要使用合适的原料,主要包括甲烷(化学式:CH4)和水蒸汽。
甲烷可以通过天然气储备或合成气得到,而水蒸汽则可以通过蒸馏水获得。
在原料准备过程中,需要确保原料的纯度和质量,以保持生产流程的稳定性和可持续性。
3. 催化剂选择与反应器设计甲醇的生产需要使用催化剂来促进反应。
常用的催化剂包括氧化锌(ZnO)和铜(Cu)。
选择合适的催化剂可以提高甲醇的产率和选择性。
在反应器设计方面,需要考虑催化剂的寿命和反应器的稳定性,并采用适当的控制策略来维持反应的温度和压力。
4. 反应步骤与操作条件甲醇的生产包括一系列反应步骤,其中最主要的是甲烷的部分氧化和甲醇的合成。
在甲烷的部分氧化中,甲烷和空气在高温下反应生成一氧化碳(CO)和二氧化碳(CO2)。
然后,一氧化碳和二氧化碳与水蒸汽在催化剂的作用下发生水煤气变换反应,生成甲醇。
在反应操作条件方面,需要控制反应温度、压力和催化剂的投料速率等参数。
较高的反应温度和压力可以促进反应速率和产物收率,但也会增加能源消耗和操作难度。
因此,需要进行优化设计来平衡反应条件和生产效益。
5. 产品分离与纯化在甲醇的生产过程中,产生的反应混合物中除了甲醇还包含其他副产物和杂质。
为了得到高纯度的甲醇产品,需要进行分离和纯化步骤。
常用的分离方法包括蒸馏、吸附和萃取等。
在蒸馏过程中,根据各组分的挥发性差异,通过升温使其先后沸腾从而实现分离。
吸附和萃取方法则可以利用吸附介质或溶剂选择性地吸附或萃取目标组分。
6. 废物处理与环境保护甲醇生产过程中会产生一些废物和副产物,包括气体废料和液体废水。
这些废物需要经过处理和处理,以减少对环境的负面影响。
甲醇制烯烃装置废气处理措施应用

甲醇制烯烃装置废气处理措施应用
甲醇制烯烃装置废气处理是指对甲醇制烯烃装置产生的废气进行处理,以保护环境和人民健康。
废气处理的目标是降低污染物浓度,减少对大气环境的影响。
下面将介绍甲醇制烯烃装置废气处理的一些常用措施和应用。
1. 烟气除尘:烟气除尘是甲醇制烯烃装置废气处理的基本措施之一。
烟气中的固体颗粒物是污染大气环境的主要来源,除尘装置可以将烟气中的颗粒物去除,降低颗粒物排放浓度。
2. 脱硫:脱硫是指将废气中的硫化物去除的过程,主要包括物理吸附和化学吸收两种方法。
脱硫可以减少废气中的硫化物排放量,防止大气酸雨的生成,对环境保护具有重要意义。
4. VOCs治理:VOCs是挥发性有机物的缩写,包括苯、甲苯、二甲苯等有机物,是大气污染的重要组成部分。
甲醇制烯烃装置产生的废气中常含有大量的VOCs,通过采用吸附剂吸附和催化燃烧等方法,可以有效降低VOCs排放浓度,减少对大气环境的影响。
5. 余热回收:甲醇制烯烃装置废气中含有大量的热能,在废气处理的过程中可以通过余热回收,将废气中的热能转化为热水、蒸汽等能源,提高能源利用效率,降低能源消耗和排放。
- 1、下载文档前请自行甄别文档内容的完整性,平台不提供额外的编辑、内容补充、找答案等附加服务。
- 2、"仅部分预览"的文档,不可在线预览部分如存在完整性等问题,可反馈申请退款(可完整预览的文档不适用该条件!)。
- 3、如文档侵犯您的权益,请联系客服反馈,我们会尽快为您处理(人工客服工作时间:9:00-18:30)。
甲醇催化燃烧催化剂研究进展 摘 要:催化燃烧法是目前处理VOCs最有效的方法之一,而本文主要对催化燃烧催化剂进行介绍,并对甲醇催化燃烧催化剂进行重点讨论,并指出这类催化剂的研究方向。 关键词:催化燃烧催化剂;甲醇催化燃烧催化剂;活性组分;载体
全世界约90%以上的能源来自于煤、石油、天然气等化石燃料,但化石燃料资源有限,在几十年内全球石油资源即将耗尽,人类正面临日益严重的能源危机。目前,我国50%以上的石油依靠进口,能源短缺阻碍我国经济快速发展。能源的高效清洁利用和新能源的开发对我国国民经济的持续稳定发展至关重要。 燃烧在现代社会中有着极为广泛的应用,但也因此带来了一系列的问题,如会消耗大量的矿物燃料,同时释放的CO、NOx等物质会导致严重的环境污染。如何提高燃料的燃烧率,减少燃烧对环境产生的污染是当前倍受关注的重要研究课题。 催化燃烧是典型的气—固相催化反应。采用适当的催化剂可降低反应的活化能,使可燃物质在较低的温度200~400℃下分解、氧化的燃烧方法。与传统的火焰燃烧相比,催化燃烧有着很大的优势: (1) 起燃温度低,能耗少,燃烧易达稳定,甚至到起燃温度后无需外界传热就能完成氧化反应。 (2) 净化效率高,污染物(如NOx及不完全燃烧产物等)的排放水平较低。 (3) 适应氧浓度范围大,噪音小,无二次污染,且燃烧缓和,运转费用低,操作管理也很方便。 正是由于具备上述优点,催化燃烧既是一种能耗低、效率高、环境友好的有机废弃物治理技术,也是能源利用的最佳途径之一。 催化燃烧技术的核心是选择合适的催化剂。由于催化燃烧温度较高,燃烧反应过程生成大量水蒸汽,且存在少量杂质硫,因此催化燃烧技术对催化剂要求很高,需要催化剂具备低温活性好、高温稳定性高、比表面积大、活性组分高分散度、抗烧结和抗硫中毒能力。 目前,催化燃烧技术备受国内外研究者关注,取得了很多研究成果。近年来,催化剂的研究成果主要为改进催化剂制备条件,选择催化剂新型载体,引入助剂改善催化剂的反应活性、选择性以及研究催化反应机理等。催化燃烧催化剂主要有贵金属催化剂、非贵金属氧化物催化剂,如钙钛矿型催化剂、六铝酸盐类催化剂、尖晶石型复合氧化物催化剂及其它一些过渡金属复合氧化物催化剂。 作为一种低碳化合物,甲醇是一种高效的液体燃料,同时也是许多工业废气的重要组成部分,有效利用甲醇对能源利用和环境保护都具有重大意义。催化燃烧是高效利用甲醇的方法之一,它可以通过催化作用降低甲醇的起燃温度,提高甲醇燃烧的利用率,减少大气污染物的生成。 1 催化燃烧催化剂 1.1 贵金属催化剂 研究表明贵金属催化剂具备很高的催化活性,起燃温度较低,起燃温度与完全燃烧温度之间的温度区间小、不挥发性和硫中毒以及对反应器材质等的要求比较低,成为研究和应用最为广泛的一种催化剂,对其制备规律和反应机理都取得了较多的研究成果,是研究得比较成熟的催化剂。贵金属催化剂所用元素主要有: Pd、Pt、Rh、Au等,其中负载Pd和Pt的催化剂的活性都较高。何洪等[1]制备了Pt、Pd负载在硅铝纤维棉载体上的两种催化剂,研究了这两种贵金属催化剂的活性。结果表明:当负载的Pt的质量分数为1.5%,负载的Pd的质量分数为2%时,催化剂活性最好。1.5%Pt/Z3催化剂的甲烷完全转化温度为600℃,而2%Pd/Z3
催化剂甲烷的完全转化温度仅为450℃。杨玉霞等[2]考察并研究了负载型钯催化
剂对甲烷完全氧化的催化机理,得出结论:富氧条件下,Pd催化剂体系表现出相对较高的甲烷氧化活性。并给出对甲烷催化燃烧的活性顺序为:Pd>Pt>Co3O4>PdO>Cr2O3>Mn2O3>CuO>CeO2>Fe2O3>V2O5>NiO>Mo2O3>TiO2。 载体的种类也会影响催化剂活性。用于氧化的催化剂载体有:Al2O3、SiO2、CeO2、ZrO2、TiO2、Ta2O3和复合氧化物等,最常用的是Al2O3,在Al2O3中引入一些杂离子如Mg2+、Zr2+可改善氧化铝负载体系的催化性能。何湘鄂等[3]对负载Pd的ZrO2和Al2O3混合载体进行研究,发现n(ZrO2)/n(Al2O3)=1/5.8的负载Pd催化剂有助于甲烷催化燃烧催化活性的改善。袁强等[4]用各种氧化物MOx(M=Zr,Fe,Ce,Mg)浸渍法制取负载型Pd催化剂,得出氧化物助剂在催化剂烧制过程中,起到抑制活性成分被烧结和改善甲烷催化燃烧催化剂的活性的作用。Vincent De Jong等[5]研究了Pt负载在γ-Al2O3载体上的催化剂的催化燃烧性能,发现它对氯苯的催化燃烧具有较好的催化活性。Abdu Uahi Nuhu等[6]用沉淀法制备了Au/TiO2催化剂,发现这种催化剂对甲醇氧化反应具有较好的催化活性,并且甲醇完全转化时温度仅在130℃左右。 1.2 非贵金属催化剂 虽然贵金属催化剂较其它催化剂性能优越,但资源稀少、价格昂贵,限制了其大规模的工业化应用[7,8]。因此,寻找来源丰富、价格低廉、性能相当的非贵金属催化剂,以替代传统的贵金属催化剂用于催化燃烧过程已成为一个重要的研究方向,研究重点集中在过渡金属氧化物催化剂、钙钛矿型催化剂、六铝酸盐类催化剂和尖晶石型复合氧化物催化剂等。 1.2.1 过渡金属氧化物催化剂 近年来,对过渡金属氧化物催化剂的研究越来越多,其载体的种类对催化活性有一定的影响,如:M A Alvarez-Merino等[9]用钨的氧化物负载于从杏仁壳中提取的活性炭(AC)上,制成一系列的WOx/AC催化剂催化燃烧甲苯,发现WOx/AC催化剂比WOx负载于SiO2、TiO2、Al2O3或Y型沸石上的催化剂活性高且反应温度低。 李丽娜等[10]制得Fe2O3质量分数为10%的Fe2O3/YSZ-γ-Al2O3(YSZ:用Y2O3
稳定ZrO2的催化剂载体)催化剂,与负载在γ-Al2O3和ZrO2-γ-Al2O3上的催化剂
相比,其对甲烷催化燃烧的催化活性最佳,且该催化剂的活性与Fe2O3在载体上的分散状况是有关的。 活性组分的量也对催化剂活性有较大的影响。Alfredo L等[11]研究了KNO3/ZrO2催化剂催化氧化煤烟灰的催化性能,发现KnZrO2中KNO3的质量分数为11.5%时,能大大提高煤烟灰的燃烧速率。刘成文等[12]用溶胶-凝胶法和微波技术制备了Ce1-xFexO2复合氧化物。结果发现甲烷催化燃烧催化剂活性顺序为:Ce0.9Fe0.1O>Ce0.8Fe0.2O2>Ce0.6Fe0.4O2>Ce0.5Fe0.5O2>Ce0.7Fe0.3O2。结合XRD和TPD分析,Ce0.9Fe0.1O2和Ce0.8Fe0.2O2形成了单一的立方萤石结构固溶体,而其它的Ce1-xFexO2形成了立方萤石结构固溶体和少量的钙钛矿型 CeFeO3的混合相。 此外,焙烧温度对催化剂活性也有一定的影响。刘长春等[13]采用水热法合成了系列Ce1-xMnxO2-a-T(x=0.0,0.1,0.2,0.3,⋯⋯0.9,1.0;T为焙烧温度:500、650、800、1000℃)复合氧化物催化剂,用于甲烷催化燃烧活性评价结果表明:Ce0.3Mn0.7O2-a-800催化剂表现出较高的甲烷催化燃烧活性,T10=430℃,T90=613℃,催化活性由催化剂的组成(Ce/Mn比例)、氧化还原能力以及焙烧温度等因素共同决定,且经过考察发现在500、650、800和1000℃下焙烧所得的催化剂,随着焙烧温度的提高,催化活性明显降低。 1.2.2 钙钛矿型催化剂 钙钛矿型催化剂通式为ABO3,A一般为碱土金属和稀土金属。通过调节A/B位离子价态,可以改善催化剂性能。 对钙钛矿型催化剂的制备有很多方法。Marco Daturi和Cuido Busca[14]指出,催化燃烧中许多钙钛类过渡金属混合氧化物的通式为LaMO3(M=Fe,Cr,Co和Mn),这些催化剂可用不同方法制得,并发现燃烧催化剂SrZrO3和LaAlO3的合成物与钙钛类催化剂有同晶结构。混合相通式为Sr1-xLaxZr1-xMxO3。LaMnO3钙钛类催化剂可以通过共沉淀干燥或者普通共沉淀法,在773K或973K下焙烧制得。 通过研究发现,钙钛类催化剂的制备方法、焙烧温度及活性组分的不同是会影响其活性的。Tatsuro Miyazaki等[15]研究了负载碱金属碳酸盐的钙钛矿型氧化物催化剂(La0.8Sr0.2Cr0.5Mn0.45Pt0.05O3,LSCMP)在673K~773K对活性炭粒的催化燃烧活性,发现碱金属对活性炭的质量比为0.012时就有很高的转化率,而且在673K时,负载碳酸盐的LSCMP比负载碳酸盐的活性炭的催化活性要高。负载碱金属碳酸盐的LSCMP在较低温度下就有较高的活性。 S Soiron等[16]比较了高温陶瓷与溶胶-凝胶法制得的La0.8Sr0.2MnO3±λ钙钛矿类氧化物在机械化学活化作用下的催化特性。与陶瓷粉末相比其活性有大大的改良。 Stefano Cimino等[17]用负载La的γ-Al2O3对菁青石涂层,再用LaMnO3冲洗具有蜂窝状的菁青石载体。经扫描电镜分析显示,冲洗的催化剂在涂层表面分布均匀,且用催化剂活性等温线测量得出,该钙钛类催化剂在普通老化周期中易降低活性,而在单块集成电路反应器的老化周期中,催化剂不失活。而且,它能使CH4(3%)和O2(10%)在500℃点燃时,甲烷完全转化,且CO和NOx的排放几乎为零。 潘智勇等[18]研究了甲烷在负载型镧锰钙钛矿催化剂(LCFM/-Al2O3)上的低温催化燃烧反应,考察了制备方法,、焙烧温度对催化剂结构和活性的影响。实验结果表明,用浸渍法、焙烧温度高于800℃就能在载体上生成良好的钙钛矿结构,催化剂具有较低的起燃温度并且在高温条件下具有与非负载型镧锰钙钛矿催化剂相当的活性。100h稳定性实验表明LCFM/α-Al2O3催化剂经800℃的高温连续燃烧反100h,催化剂仍保持了原有结构和催化活性,并且没有明显积炭。因此,这种催化剂用于高温燃烧是很有前景的。 K Rida等[19]用溶胶-凝胶法制备了镧铬混合氧化物催化剂LaCrO3。发现在高于700℃ 下焙烧能得到单一的钙钛矿型LaCrO3晶相,且其催化活性达到最佳。而在较低温度下焙烧会产生LaCrO3和LaCrO4混合物,使燃烧体系催化活性受损。另外,S Cimino等[20]制备了一种双位钙钛型催化剂Pd-LaMnO3。发现这种新型催化剂在低温和高温氧化反应中比单独的PdMnO3和LaMnO3的催化剂活性都要高,且其最低点火温度为320℃。 1.2.3 六铝酸盐型催化剂 六铝酸盐型催化剂通式为AAl12O19,A通常是碱金属、碱土金属或稀土金属。六铝酸盐的晶体结构分为磁铅石型和β-氧化铝型,由含有大阳离子的镜面层和Al-O尖晶石单元交替堆积而成,这种特殊的层状结构可以抑制晶粒沿c轴方向的生长,因此六铝酸盐材料表现出很高的热稳定性。六铝酸盐型催化剂具备热稳定性高、挥发性低、机械强度及抗热冲击性能良好等优势,是最具前景的甲烷高温燃烧催化体系[21]。李彤等[22]用共沉淀法制备了CaxLa1-xMnAl11O19系列六铝酸盐催化剂,实验发现适量的Ca2+替代La3+,可以使Ca2+进入六铝酸盐骨架中,形成纯的六铝酸盐相,并显著催化剂的比表面积,从而使得催化剂的催化剂性能大为提高。反相微乳法是近年来发展起来的液相合成大比表面积材料的新方法,其合成的材料均匀性高、比表面积大且能有效控制颗粒的尺寸和形状。张晓红等[23]利用反相微乳法合成铁取代铝元素的单一相LaFeAl11O19催化剂,具有较好的