甲醇合成催化剂分析解析
甲醇合成催化剂失活分析
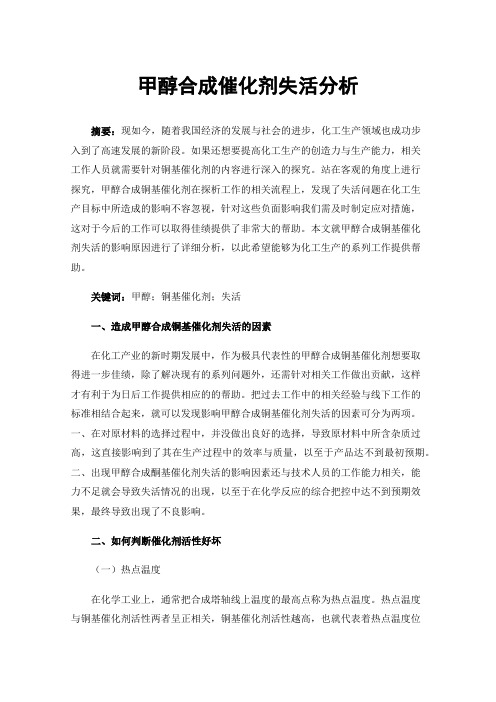
甲醇合成催化剂失活分析摘要:现如今,随着我国经济的发展与社会的进步,化工生产领域也成功步入到了高速发展的新阶段。
如果还想要提高化工生产的创造力与生产能力,相关工作人员就需要针对铜基催化剂的内容进行深入的探究。
站在客观的角度上进行探究,甲醇合成铜基催化剂在探析工作的相关流程上,发现了失活问题在化工生产目标中所造成的影响不容忽视,针对这些负面影响我们需及时制定应对措施,这对于今后的工作可以取得佳绩提供了非常大的帮助。
本文就甲醇合成铜基催化剂失活的影响原因进行了详细分析,以此希望能够为化工生产的系列工作提供帮助。
关键词:甲醇;铜基催化剂;失活一、造成甲醇合成铜基催化剂失活的因素在化工产业的新时期发展中,作为极具代表性的甲醇合成铜基催化剂想要取得进一步佳绩,除了解决现有的系列问题外,还需针对相关工作做出贡献,这样才有利于为日后工作提供相应的的帮助。
把过去工作中的相关经验与线下工作的标准相结合起来,就可以发现影响甲醇合成铜基催化剂失活的因素可分为两项。
一、在对原材料的选择过程中,并没做出良好的选择,导致原材料中所含杂质过高,这直接影响到了其在生产过程中的效率与质量,以至于产品达不到最初预期。
二、出现甲醇合成酮基催化剂失活的影响因素还与技术人员的工作能力相关,能力不足就会导致失活情况的出现,以至于在化学反应的综合把控中达不到预期效果,最终导致出现了不良影响。
二、如何判断催化剂活性好坏(一)热点温度在化学工业上,通常把合成塔轴线上温度的最高点称为热点温度。
热点温度与铜基催化剂活性两者呈正相关,铜基催化剂活性越高,也就代表着热点温度位置越高。
在其床层的上方位置反应物的浓度可以达到最高值,生成物的浓度相反确是最低点,这时所形成的运动反应是最剧烈的,铜基催化剂的温度也因此呈持续上升趋势。
当到达温度巅峰值后,生成物的浓度增加反应物的浓度降低,反应进程开始减慢。
反应的生成物热量被带走,床层的温度逐渐降低。
(二)铜基催化剂床层温差铜基催化剂的床层温度变化过大,就会造成部分床层温度达不到铜基催化剂活性温度的状况出现,这就会出现变化反应都集中在局部活性温度达标的地点,从而释放热量,因此化学反应越剧烈就会带动床层温度变化越大,铜基催化剂的活性温度也就因此变得更好了。
合成甲醇催化剂还原、钝化的探究

合成甲醇催化剂还原、钝化的探究摘要:甲醇催化剂合成情况的好坏将直接影响甲醇合成系统的运行状况,也关乎甲醇产品的产量及消耗的高低。
基于此,本文主要对合成甲醇催化剂还原、钝化的进行探究.关键词:合成甲醇催化剂;还原;钝化引言甲醇合成系统工艺流程主要是来自合成气压缩机的合成气,经气气换热器A/B 壳程被管壳式甲醇合成塔A/B的高温出塔气预热至200℃左右,进入甲醇合成塔A/B,在铜基催化剂的作用下CO、CO2与H2进行反应生成甲醇和水;甲醇合成塔A/B出口气经气气换热器管程与入塔气换热后,温度降至95℃左右,然后经水冷器ⅠA/B冷却到65℃,再经水冷器ⅡA/B冷却到40℃后,进入甲醇分离器A/B进行气液分离。
甲醇分离器顶部出来的分离掉甲醇的大部分气体作为循环气去合成气压缩机,经合成气压缩机增压并补充新鲜气后送入甲醇合成塔进行下一轮反应;一小部分作为弛放气送往氢回收系统回收H2。
甲醇分离器分离出的粗甲醇则通过一级过滤器和二级过滤器除去其中的固体杂质后送至闪蒸槽,之后粗甲醇经粗甲醇泵送至甲醇精馏系统或粗甲醇罐区。
1催化剂的还原催化剂在还原过程中出水量约为催化剂重量的18×10-2~20×10-2,其中物理水占3×10-2~5×10-2,化学水占13×10-2~15×10-2。
合成甲醇催化剂的还原过程分为初期、主期、末期三个阶段,还原初期是脱除物理水的过程,还原主期是配氢后产生化学水的过程,还原后期是将残余的水分排出的过程。
催化剂还原过程的热量是由开工喷射器提供,以前使用的是中压过热器蒸汽,压力为2.3~2.8MPa,温度为390~420℃,使用的是动力车间锅炉工段经过本装置蒸汽过热器加热后的蒸汽,压力为1.6~2.1MPa,温度为380~390℃。
整个还原过程中要遵循“提氢不提温、提温不提氢”的原则,保持温度平稳上升。
合成甲醇催化剂本体中有一定量的碳酸盐,在还原中后期会有一定量的CO2生成,而催化剂的活性温度是190℃,在还原中后期,大量的CO2会发生反应,将催化剂的活性激活,此时还原过程会立刻终止,其还原程度就会大大降低。
甲醇合成单程转化率-概述说明以及解释

甲醇合成单程转化率-概述说明以及解释1.引言1.1 概述甲醇合成是一种重要的化学反应,其广泛应用于工业生产中。
甲醇是一种重要的有机溶剂和化学原料,其在合成柴油、塑料和涂料等许多领域都具有广泛的应用前景。
甲醇的合成通常通过甲烷的催化转化实现。
在这个过程中,甲烷首先经过氧化反应生成一氧化碳和氢气,然后通过催化剂的作用,再将一氧化碳和氢气转化为甲醇。
然而,甲醇的合成过程中存在许多影响其单程转化率的因素。
首先,催化剂的选择对甲醇合成的单程转化率具有重要影响。
常见的甲醇合成催化剂包括金属氧化物、过渡金属和硅铝酸盐等。
不同的催化剂具有不同的活性和选择性,因此会对甲醇的转化率产生不同的影响。
其次,反应温度也是影响甲醇合成单程转化率的重要因素。
通常情况下,较高的反应温度可以促进甲醇的合成反应,并提高其转化率。
然而,过高的反应温度可能会导致副反应的发生,从而降低甲醇的转化率。
此外,反应物的浓度、反应物之间的摩尔比、催化剂的添加量等因素也会对甲醇合成单程转化率产生影响。
适当地调节这些因素可以提高甲醇的转化率和产率。
综上所述,甲醇合成的单程转化率受到多种因素的影响。
通过深入研究这些因素,并合理调控反应条件,可以有效提高甲醇的合成效率和产量,进一步推动甲醇合成技术的发展和应用。
1.2 文章结构文章结构:本文主要分为三个部分:引言、正文和结论。
引言部分主要对甲醇合成单程转化率进行简要介绍和概述,然后说明文章的结构和目的。
正文部分包括两个小节:甲醇合成的背景和意义以及影响甲醇合成单程转化率的因素。
在第一个小节中,将介绍甲醇合成的背景,并阐述其意义和重要性。
在第二个小节中,将详细探讨影响甲醇合成单程转化率的各种因素,如反应条件、催化剂种类和负载等。
结论部分将对文章进行总结,简要概括讨论的主要内容和结论,强调甲醇合成单程转化率的关键因素。
同时,展望未来的研究方向,指出甲醇合成单程转化率的提高仍面临的挑战和需要深入研究的问题。
通过以上结构,本文将全面系统地介绍甲醇合成单程转化率及其影响因素,为相关领域的研究工作提供参考和指导。
甲醇合成催化剂知识

甲醇合成催化剂知识d i4 X+ }1 z! j0 v1 铜基催化剂的催化原理 + W7 b1 C1 Y9 W4 M1 h)o9 F0 t8 j* c: D q, |6 O 目前,低压甲醇合成铜基催化剂主要组分是 CuO、ZnO和Al2O3,三组分在催化剂中的比例随着生产厂家的不同而不同。
一般来说, CuO的质量分数在40% ~80%, ZnO的质量分数在10% ~30%, Al2O3的质量分数在5% ~10%。
铜基催化剂在合成甲醇时, CuO、ZnO、Al2O3三组分的作用各不相同。
CO和H2在催化剂上的吸附性质与催化剂的活性有非常密切的关系。
在铜基催化剂表面对CO的吸附速率很高,而H2的吸附则比CO 慢得多。
ZnO是很好的氢化剂,可使H2被吸附和活化, 但对CO几乎没有化学吸附,因此可提高铜基催化剂的转化率。
纯铜对甲醇合成是没有活性的,H2和CO合成甲醇的反应是在一系列活性中心上进行的,而这种活性中心存在于被还原的Cu-CuO界面上。
在催化剂中加入少量 Al2O3的首要功能就是阻止一部分氧化铜还原。
当催化剂被还原后,开始进行反应时,合成气中的H2 和CO都是还原剂,有使氧化铜进一步还原的趋势。
这种过度的还原,使得活性中心存在的界面越来越小,催化剂活性也越来越低。
从合成的整个过程来看,随着还原表面向催化剂的内层深入,未还原的核心越来越小,作为被还原的Cu-CuO界面的核心表面积也越来越小,催化剂的活性降低,合成反应速率随之降低。
研究认为,Al2O3在催化剂中作为结构助剂起阻碍铜颗粒烧结的作用, CuO/ZnO/Al2O3催化剂的活性远高于双功能催化剂CuO/ZnO的活性。
q7 h- G8 n9 ]$ B5 m- Q: ?& ]/ D2 铜基催化剂助剂6 j8 } x5 L! ?0 V1 l1 K4 H$ Q! m% g\5 K8 e) C+ g5 A)E! ~ 铜基催化剂助剂的研究是甲醇合成催化剂研究的一个重要课题。
甲醇合成催化剂反应机理及应用1

甲醇合成催化剂的反应机理及应用新疆广汇新能源有限公司新疆哈密839000 杨林君摘要:本文介绍了甲醇合成反应的机理,合成催化剂的制备;对XNC-98催化剂的使用情况做了介绍。
关键词:甲醇合成催化剂甲醇是重要的有机化工原料,碳一化学的母体,广泛用于生产塑料、纤维、橡胶、染料、香料、医药和农药等,还是重要的有机溶剂。
甲醇在发达国家其产量仅次于乙烯、丙烯和苯,居第四位。
甲醇用作汽车发动机燃料,所谓甲醇汽油,今后随着石油不断开采资源日渐减少,直至枯竭,特别在我国少油多煤的资源下,甲醇用作汽车燃料将达亿吨/年以上,跃升化工产品的首位。
研究开发应用推广近代甲醇合成工艺与合成塔技术和建设大型化生产装置,成为我国甲醇工业大发展的必由之路[1]。
随着甲醇工业的发展,以低压法铜基催化剂为代表的甲醇合成技术得到了很大的发展。
国内近年来在合成催化剂的反应机理、性能及应用等方面研究不断深入,开发出具有世界先进水平的合成催化剂。
一甲醇合成反应的机理甲醇合成反应机理与活性中心的研究一直是甲醇合成反应过程的研究重点,其对高效催化剂的开发、实验现象本质特征的解释和反应结果的预测都具有重要意义。
一个合理的甲醇合成反应历程能够为反应条件的优化以及催化剂制备过程等催化体系的改进提供理论依据,为工业化生产提供理论支撑。
按合成甲醇直接碳源的不同,将机理划分为以下3种:CO与CO2共同作为直接碳源机理、CO作为直接碳源机理以及CO2作为直接碳源机理[2]。
1.1 CO直接作为碳源机理长期已来,在铜基催化剂上加氢合成甲醇的碳源问题都是研究者争论的焦点问题。
Herman 等研究了CO/H2体系在Cu/ZnO/Al2O3催化剂上的反应,认为反应的活性中心是Cu+,H2的解离吸附发生在ZnO上,并提出以下反应机理:CO+*(Cu2O)→CO*(Cu2O)H2+2*(ZnO)→2H*(ZnO)CO*(Cu2O)+H*(ZnO)→HCO*(Cu2O)+*(ZnO)H*(ZnO)+HCO*(Cu2O)→CH2O*(Cu2O)+*(ZnO)2H*(ZnO)+CH2O*(Cu2O)→CH3OH*(Cu2O)+2*(ZnO)CH3OH*(Cu2O)→CH3OH+*(Cu2O)式中:*指催化剂的活性吸附位。
甲醇合成催化剂失活及影响因素分析
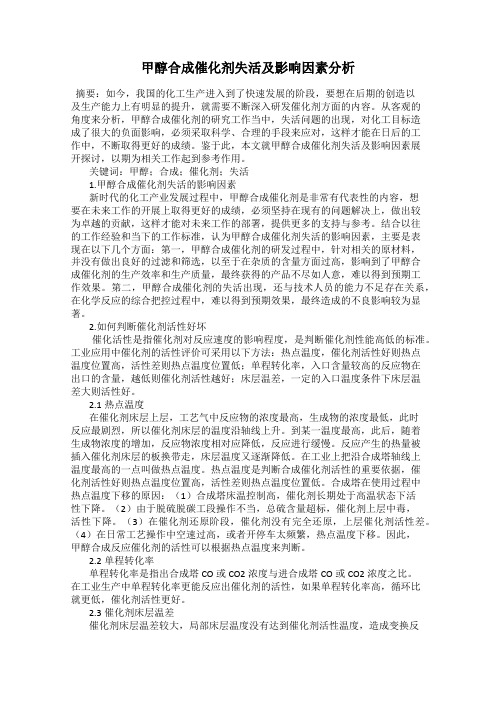
甲醇合成催化剂失活及影响因素分析摘要:如今,我国的化工生产进入到了快速发展的阶段,要想在后期的创造以及生产能力上有明显的提升,就需要不断深入研发催化剂方面的内容。
从客观的角度来分析,甲醇合成催化剂的研究工作当中,失活问题的出现,对化工目标造成了很大的负面影响,必须采取科学、合理的手段来应对,这样才能在日后的工作中,不断取得更好的成绩。
鉴于此,本文就甲醇合成催化剂失活及影响因素展开探讨,以期为相关工作起到参考作用。
关键词:甲醇;合成;催化剂;失活1.甲醇合成催化剂失活的影响因素新时代的化工产业发展过程中,甲醇合成催化剂是非常有代表性的内容,想要在未来工作的开展上取得更好的成绩,必须坚持在现有的问题解决上,做出较为卓越的贡献,这样才能对未来工作的部署,提供更多的支持与参考。
结合以往的工作经验和当下的工作标准,认为甲醇合成催化剂失活的影响因素,主要是表现在以下几个方面:第一,甲醇合成催化剂的研发过程中,针对相关的原材料,并没有做出良好的过滤和筛选,以至于在杂质的含量方面过高,影响到了甲醇合成催化剂的生产效率和生产质量,最终获得的产品不尽如人意,难以得到预期工作效果。
第二,甲醇合成催化剂的失活出现,还与技术人员的能力不足存在关系,在化学反应的综合把控过程中,难以得到预期效果,最终造成的不良影响较为显著。
2.如何判断催化剂活性好坏催化活性是指催化剂对反应速度的影响程度,是判断催化剂性能高低的标准。
工业应用中催化剂的活性评价可采用以下方法:热点温度,催化剂活性好则热点温度位置高,活性差则热点温度位置低;单程转化率,入口含量较高的反应物在出口的含量,越低则催化剂活性越好;床层温差,一定的入口温度条件下床层温差大则活性好。
2.1热点温度在催化剂床层上层,工艺气中反应物的浓度最高,生成物的浓度最低,此时反应最剧烈,所以催化剂床层的温度沿轴线上升。
到某一温度最高,此后,随着生成物浓度的增加,反应物浓度相对应降低,反应进行缓慢。
催化剂甲醇合成
催化剂甲醇合成催化剂甲醇合成是一种重要的工业生产技术,可以用来合成甲醇,还可以制造其他有机化合物。
本文将介绍甲醇合成的催化剂及其原理、工业生产过程和新技术发展趋势。
一、催化剂及其原理甲醇合成的催化剂主要分为金属氧化物催化剂和配合物催化剂两类。
1、金属氧化物催化剂常见的金属氧化物催化剂有氧化铜、氧化铬、氧化钴等。
这些催化剂的原理是,催化剂中的金属离子可以与一氧化碳和氢气发生反应,生成一种中间体(如甲酸、甲酸甲酯等),然后再经过一系列反应,生成甲醇。
2、配合物催化剂配合物催化剂包括贵金属催化剂和非贵金属催化剂。
其中,铑和铱是最常见的贵金属催化剂,非贵金属催化剂主要包括钼、铌、钒等。
这些催化剂的原理是,经过氢气活化后,催化剂能够与一氧化碳和二氧化碳反应,生成甲酸,然后再生成甲醇。
此外,配合物催化剂还可以用于一些特殊反应,比如催化碳氢键的切割。
二、工业生产过程甲醇的工业生产过程主要有两种方法:一是合成气法,即将氢气和一氧化碳反应生成甲醇;二是天然气法,即从天然气中提取甲烷,然后通过一系列化学反应生成甲醇。
合成气法合成气法是目前最常用的甲醇生产方法。
生产过程主要包括合成气的制备、催化剂的选择和反应的控制。
1、合成气制备合成气制备方法包括煤气、重油和天然气重整、重油催化裂解和煤气化等。
其中,天然气煤气化是最常用的方法。
通过高温高压反应,将天然气转化成含有一氧化碳和氢气的合成气。
2、催化剂选择甲醇合成的催化剂主要是氧化物和配合物催化剂。
目前工业生产中,氧化铜和氧化锌是最常用的催化剂,伴有一些助剂。
3、反应控制甲醇合成的反应控制十分关键。
在反应过程中,必须控制反应温度、压力和催化剂用量等参数,才能获得高质量的甲醇。
天然气法天然气法是一种新兴的甲醇生产方法。
与合成气法相比,天然气法具有取之不尽、用之不竭的优势,并且生产过程更加环保。
1、天然气的处理天然气中的甲烷需要经过催化裂解,生成含有一氧化碳和氢气的合成气。
2、合成气的制备和处理生产过程与合成气法一致。
关于甲醇合成过程中催化剂的研究
司也随后研制了同类催化剂,其代表产品为CuO/ZnO/Al 2O 3。
在催化合成过程中操作压力为5~10MPa ;温度为200~300℃。
比最初甲醇合成工艺所需的压力和温度要低很多,属于低温低压操作条件的范畴。
这类催化剂的特点是:耐热性能较差、活性较高、选择性也高;但对杂质较为敏感;而这种低压法生产设备的体积大,从而占地面积大、投资也较大。
1.2.3 贵金属负载类催化剂贵金属负载类催化剂是由MgO 、SiO 2、ZrO 2等氧化物作为载体,将某些贵金属负载,通常贵金属选择Pd 、Pt 、Au 等。
其代表产品为PtCr/Si SiO 2、PtW/SiO 2等,这类催化剂的优点主要在于对甲醇的选择性很高,有的催化剂即使在合成过程中其他杂质较多情况下仍然可以保持高选择性以及高转化率。
2 反应条件对甲醇合成催化剂的影响在反应过程中催化剂催化效果的好坏不仅和自身的性质、结构有关,而且反应条件也对催化剂有很大的影响作用。
适宜的反应条件会让催化剂的活性达到最佳状态。
所以在甲醇合成过程中,研究不同反应条件对于催化剂活性的影响很有必要。
2.1 压力对催化剂的影响甲醇合成反应为:CO+2H 2=CH 3OH,该反应的正方向是分子数减少,根据化学平衡相关知识可以知道,当压力增大时反应会向生成反应物方向移动,即有利于甲醇产品的合成。
,所以,当压力增大时,甲醇转化率会随着压力的增加而升高。
除此以外,催化剂上反应物的吸附以及生成物的脱附也和压力有关。
实验研究表明,当压力增加10%,甲醇的转化率亦增加10%。
但并非压力一直增加转化率会一直随之增加,和其他对压力有要求的反应一样,压力增加虽然会提高产物转化率,但有一个限值。
对于甲醇生产来讲,当压力超过8MPa ,甲醇转化率反而呈开始下降趋势。
2.2 温度对催化剂的影响温度作为化学反应过程中至关重要的反应条件之一,对于化学反应速率、反应方向都有着很重要的影响作用。
对于使用催化剂的化学反应中,温度更是不能忽视的因素之一。
甲醇合成催化剂的失活分析与对策
甲醇合成催化剂的失活分析与对策摘要:甲醇催化剂的失活在甲醇生产中是个普遍问题,从催化剂各种毒物的中毒机理及来源分析入手,如何合理延长催化剂使用寿命是本文探讨的重点。
关键词:甲醇合成催化剂中毒使用寿命一、引言近年来随着国家能源政策的调整,甲醇市场得到了较大的发展,我国新建了一大批甲醇装置,在原料上以煤为原料逐渐成为主导趋势,技术上合成催化剂由高压锌铬催化剂发展到低温铜基催化剂而且在节能降耗等方面都有了很大的发展,但是就目前各个甲醇厂的实际情况来看,触媒的使用寿命普遍比较短。
如何延长触媒的使用寿命逐渐成为人们追求的目标。
这其中的主要原因在于,对合成气中的导致甲醇触媒失活的各种物质的毒性机理认识不足,重视不够。
我们厂的触媒平均每三年换一次。
采用的是:低压法甲醇气相合成工艺,催化剂主要是铜系催化剂。
催化剂的组成均在以下基本配比范围内波动:cu/zn/al=6:30:10(摩尔百分比)。
二、催化反应机理催化剂是这样一种物质,它能改变化学反应速度,但其本身的质量和化学性质在反应前后都没有发生改变。
固体催化剂的表面结构是不均匀的,只有表面上某些有特定的原子结构、电荷密度、几何形貌的部位对特定的化学反应才具有催化作用,这些特殊部位称为催化剂的活性中心。
在活性中心上反应物分子先是被吸附在其上面。
被吸附的分子在活性中心表面进行能量交换,形成类似化学键的形式,从而削弱反应分子之间各原子间的化学键能,使分子变形而相互重新结合,完成合成反应;或活性中心与被吸附反应物分子构成配价健,而使反应物分子活化,并促使其在配位上进一步反应,最后转化为反应产物。
催化剂的活性与催化剂活性中心的面积、数量有直接的正比例关系。
活性中心,是催化剂的核心点,与催化剂的组成、制作方法,粘结性、比表面积、晶格结构有关。
延长催化剂活性寿命主要取决于三方面:〈1〉催化剂的稳定性。
〈2〉气体的净化程度、装置的清扫程度。
〈3〉使用条件。
三、催化剂的中毒我们厂低压法合成工艺使用的是cu-zn-al系催化剂,该系催化剂活性高,选择性强,但活性温度范围小,对毒物极为敏感,容易中毒失活,导致催化剂失活的主要因素有以下几个方面: 〈1〉硫化物〈2〉油污〈3〉超温烧结下面分别对上述毒物的来源和催化剂的失活机理及防范措施作以粗浅的分析:1.硫化物1.1硫化物的形态和含量分布硫化物是最常见的毒物,是引起催化剂活性丧失的主要因素。
合成气制甲醇催化剂
合成气制甲醇催化剂合成气制甲醇是一种重要的化工过程,在工业生产和能源转化中有着广泛的应用。
催化剂是合成气制甲醇过程中的关键因素,催化剂的性能直接影响到反应的效率和产物的质量。
本文将介绍合成气制甲醇催化剂的种类、性质、制备方法及应用。
1. 催化剂的种类合成气制甲醇催化剂主要分为三类:Cu/ZnO/Al2O3催化剂、ZnO 催化剂和其他催化剂。
1.1 Cu/ZnO/Al2O3催化剂Cu/ZnO/Al2O3催化剂是目前应用最广泛的合成气制甲醇催化剂。
该催化剂由Cu、ZnO和Al2O3三种组分组成,其中Cu是活性组分,ZnO和Al2O3是助剂。
Cu/ZnO/Al2O3催化剂具有高的甲醇选择性和高的反应活性,同时也具有良好的热稳定性和机械强度。
该催化剂的制备方法主要包括共沉淀法、沉淀法、浸渍法等。
1.2 ZnO催化剂ZnO催化剂是一种比较新型的催化剂,其主要由ZnO组成。
与Cu/ZnO/Al2O3催化剂相比,ZnO催化剂具有更高的CO2选择性和更高的反应速率。
同时,ZnO催化剂也具有良好的热稳定性和机械强度。
该催化剂的制备方法主要包括溶胶-凝胶法、水热法、水热合成-煅烧法等。
1.3 其他催化剂除了Cu/ZnO/Al2O3催化剂和ZnO催化剂外,还有一些其他的催化剂,如Fe催化剂、Co催化剂、Ni催化剂等。
这些催化剂具有不同的催化性能和应用范围,但相对于Cu/ZnO/Al2O3催化剂和ZnO催化剂来说,其应用较为有限。
2. 催化剂的性质合成气制甲醇催化剂的性质主要包括催化剂的化学成分、晶体结构、表面性质、孔结构和热稳定性等。
2.1 化学成分合成气制甲醇催化剂的化学成分是影响其催化性能的重要因素。
Cu/ZnO/Al2O3催化剂的化学成分主要包括Cu、ZnO和Al2O3三种组分,其中Cu是活性组分,ZnO和Al2O3是助剂。
ZnO催化剂的化学成分主要是ZnO。
不同的催化剂化学成分差异较大,其催化性能也存在差异。
- 1、下载文档前请自行甄别文档内容的完整性,平台不提供额外的编辑、内容补充、找答案等附加服务。
- 2、"仅部分预览"的文档,不可在线预览部分如存在完整性等问题,可反馈申请退款(可完整预览的文档不适用该条件!)。
- 3、如文档侵犯您的权益,请联系客服反馈,我们会尽快为您处理(人工客服工作时间:9:00-18:30)。
8.2.3.2装载惰性支撑球
在装载吸收剂前,先将惰性支撑小球填料到容器的底层。
直径为25mm惰性氧化铝瓷球的底层,装载在出口收集器周围和上部到底部正切线200mm以下的部位。
在直径为25mm瓷球上装载100mm厚的一层直径为13mm惰性氧化铝瓷球。
操作人员长期留驻在容器内时非常有必要的。在这种情况下,要表明注意安全的标牌。
人工装载:由容器外的一组工作人员将催化剂倒入10到15公升的吊桶。吊桶通过绳索升至人行通道,随后在降至容器内的操作人员处。朝不同的方向清空吊桶,以保证催化剂均匀铺开。操作人员会使用厚木板分散自身的重量,以避免挤压催化剂。这个方法很简单,还可以为催化剂提供一个低“落差”。
很多容器都将采用惰性小球,从而正确地支撑容器中的催化剂床层。在运行中,为形成平稳的流动,每一层小球在完全铺平后,才能进行下一层的装载,这一点是非常重要的。
有很多装载技术均要求操作者佩戴适当的保护性装备。总的来说,至少需要护目镜,手套,防尘面具和护耳器。催化剂的装载通常是由专门承装商来完成的,因为他们有丰富的装载经验和设备。这里描述一些常用的方法。
在装载前,由调试工程师检验容器,并将在现场检测工艺目标是否贯彻到物理设备上。
热电阻组件通常是比较活跃的部分,不合格的安装会降低运行质量。
对于手孔中的催化剂滞留装置,需检测需检测催化剂排放喷嘴和人行通道。催化剂不能进入喷嘴,通常会采用一种叫做钟形罩的设备。在某些情况下,喷嘴会被填满很小的惰性小球,或被耐火材料挤压,以避免运行过程中的气体分流。
第八部分-催化剂处理
Contents
8.0催化剂处理3
8.1催化剂处理3
8.2催化剂装载3
8.2.1筛选4
8.2.2取样4
8.2.3合成气净化槽4
8.2.4甲醇反应器5
8.3催化剂卸载9
8.3.1合成气净化槽9
8.3.2甲醇反应器9
8.3.3甲醇反应器催化剂氧化10
8.4催化剂保护12
8.0
8.1
通常,催化剂要供应到金属槽或IBCs(中型散装容器)中。催化剂应该储存在干燥建筑,然而,在环境不允许的情况下,要放置在木制托盘上,并严密覆盖以保持干燥。在装载之前,密封盖要一直盖在槽上。开放槽在检测Байду номын сангаас抽样检验完毕后,要重新密封。
软管装载:使用直径为4”的软管,用来引导储水槽中的催化剂从容器顶部流到容器内部的操作工处。软管的重量由容器外部起到保护作用的绳索支撑的,以此满足容器进料时软管收缩的要求。如果使用塑料软管,可以适当地从底部切断来缩短长度。软管的直径不能太大,也不能重于所含的催化剂重量,否则会增加操作难度。软管内要一直保持充分的催化剂,这样,催化剂通过软管开口到催化剂表面,最终落进漏斗里。
适当的筛选方法是将催化剂通过一个斜槽(由适当尺寸2 x2 mm的筛绢制成)。如果使用振动筛的话,筛角和振幅必须具备调节性。通常采用最小振幅。持续进行振动调节,直到确定催化剂在筛选过程中未受到损害为止。仔细观察催化剂和粉煤,确保不会过度覆盖。在筛选的操作过程中,要对收集到的粉尘要进行检验。数量应当低于1%。如果超过这个量,要暂停整个操作过程,重新审核。
毛刷装载:毛刷装载转化炉管的方法,已经被成功的采用了很多年。这个技术可以用于甲醇1号转化炉管程的装载。要求每500到1000米处,都有嵌入转化炉管程的半刚性柱子(带半刚性毛刷)。当柱子逐步收缩时,添加一定剂量的催化剂。
8.2.1
通常不建议对催化剂进行筛选,因为这样会产生更多的粉尘。倾倒催化剂后,通常在每个槽的底部都会留有50mm的催化剂(绝大部分灰尘会积聚在槽底),所以很有必要对材料进行遮蔽。尽管如此,在催化剂的运送过程中,有时也会不可避免的发生过度磨损的状况,因此,最好在装料之前遮蔽材料。在操作过程中有可能会损害催化剂小球和DPT的质量,所以要特别注意。或者可以在着手工作前请教催化剂供应商。
另一个方法适用于装料时操作员在容器内的情况-----平均铺平到300mm时,从床表面提取代表性样品。每一层提取5份样品,中心位置一个,每90度方向一个。这些单独的样品结合起来,构成该层催化剂的代表性样品。
所有的样品都要标注,这样标签就不会脱落,具体信息也不会被抹去。标签内容包括:
装置,流体和容器
取样时间
最后,在直径为13mm小球顶部,装载100mm厚的直径为6mm的惰性氧化铝瓷球。
每层在铺平后,才能进行下一层的装载。
容器内底部正切线的位置可能不太明显。必要的话,可以参考容器图纸,得到焊接线到正切线之间的距离。
8.2.3.3装载吸收剂
推荐的装载吸收剂的方法是用漏斗和sock。将300mm的吸收剂装载喷嘴直接连接到容器入口喷嘴上方的吸入管路上。这意味着容器的的人行通道仅供容器出入。漏斗安装在装载喷嘴上方,附加到达容器底部的SOCK。Sock的长度是可调节的,采用zipped sock,或者移开底部部件进行调节。SOCK内部为平滑表面,且无磨蚀成分。从容器开口运送吸收剂的速率,通过信号绳或类似工具控制。SOCK的直径不能太大,否则它所承载的吸收剂重量会很难操纵。SOCK内要一直保持填满吸收剂,这样,吸收剂只会落入漏斗,或从SOCK开口落到吸收剂表面。
要尽可能谨慎地处理催化剂。减少对槽的重复处理,不能滚动槽,为此要提供适当的设备。催化剂颗粒不能落在以下段落指定的距离之外。清空槽时,轻微倾斜可限制排放流量。需要进入催化剂容器内时,可使用木板。
8.2
根据正常操作下催化剂的物理性质和流动模式,不同的装载技术用于装置中的每个催化剂。例如,易碎的催化剂要求轻柔的装载方法,而坚硬的催化剂通常可以采用漏斗装载。
取样槽数
催化剂床顶部和底部范围内槽体成分的位置
8.2.3
合成气净化槽内要装载Puraspec2020吸收剂。吸收剂相对较浓,容器内没有复合内件。
8.2.3.1容器装料
容器装料时需要注意的事项:
吸收剂不能自由落在0.5 –1米以外。
吸收剂要均匀分布在整个反应器表面上,避免将粉煤集中在一个区域,直接导致气体分布不均匀。
要记录粉煤的重量,并从槽排放到筛网的催化剂重量中扣除。注意筛网过载,否则将会导致无效筛选。
8.2.2
每次装料时,建议对催化剂进行取样,并由操作者保留,这样可以调查造成意外情况出现的原因。取样的一个方法是在装料程序中,从槽里取样。样品应该从每个取样桶的中心部位而不是末端提取,这样才能够得到具有代表性的材料。接着,这些样品会结合在一起,构成催化剂床中500mm处催化剂的代表样品(重1kg)。在铺平催化剂床,测量完相对深度后,对每一批代表高处和低处的样品进行记录。