合成甲醇催化剂研究进展
二氧化碳加氢合成甲醇催化剂研究进展

1 1 铜 基 催 化 剂 的 活 性 中心 .
氧 化碳气 体被 排放 到 大 气 中 , 对人 类 的生 存 环境 造
成 了严重 的影 响 , 如何 消 除 C 污 染并 加 以综合 利 O
目前 , 于 铜基 催 化 剂 中活 性 中心 的结 构 主要 关 有 3种不 同的观点 :1 C 与 Z O 和( ) 。的 ()u n 或 Al O
具有 比表 面积大 、 分散 度 高和热 稳定性 好 的特点 , 将
成 为一 种发 展趋势 , 今后研 究 的方 向l ] 是 】 。
温丽丹 , 李金 来
( 北工业大学 化工学 院, 河 天津 30 3 ) 0 1 0
摘 要 : 绍 了 C 。 氢 合 成 甲醇 催 化 剂 的研 究 进 展 , 点 对 负 载 型 铜 基 催 化 剂 的 最 新 进 展 进 行 了 介 O 加 重
综述 。 关 键 词 : 氧化 碳 ; 氢 ; 成 甲 醇 ; 应 机 理 ; 化 剂 二 加 合 反 催 中图 分 类 号 :T 2 文 献 标 识 码 : Q2 3 A 文 章 编 号 :0 6— 9 6 2 0 ) 6 0 3— 5 1 0 7 0 ( 0 8 0 —0 3 0
Re e r h pr g e so a a y t f r s nt e i i e ha o s a c o r s n c t l s o y h sz ng m t n l fo r m y r g na i n o a b n d o i h d 0 e t0 f c r o i x de
用 引起 了人 们 的极 大 关 注 。c 是潜 在 的碳 源 , O 甲
醇是 C 1化学 的重 要 产 品 , C 加 氢 制 甲醇 路 线 由 O 的开 发既 可 以 解 决 能 源 问 题 , 能 够 缓 解 “ 室 效 又 温 应 ” 具 有重要 的经济价 值和 现实 意义 。 ,
合成甲醇催化剂还原、钝化的探究

合成甲醇催化剂还原、钝化的探究摘要:甲醇催化剂合成情况的好坏将直接影响甲醇合成系统的运行状况,也关乎甲醇产品的产量及消耗的高低。
基于此,本文主要对合成甲醇催化剂还原、钝化的进行探究.关键词:合成甲醇催化剂;还原;钝化引言甲醇合成系统工艺流程主要是来自合成气压缩机的合成气,经气气换热器A/B 壳程被管壳式甲醇合成塔A/B的高温出塔气预热至200℃左右,进入甲醇合成塔A/B,在铜基催化剂的作用下CO、CO2与H2进行反应生成甲醇和水;甲醇合成塔A/B出口气经气气换热器管程与入塔气换热后,温度降至95℃左右,然后经水冷器ⅠA/B冷却到65℃,再经水冷器ⅡA/B冷却到40℃后,进入甲醇分离器A/B进行气液分离。
甲醇分离器顶部出来的分离掉甲醇的大部分气体作为循环气去合成气压缩机,经合成气压缩机增压并补充新鲜气后送入甲醇合成塔进行下一轮反应;一小部分作为弛放气送往氢回收系统回收H2。
甲醇分离器分离出的粗甲醇则通过一级过滤器和二级过滤器除去其中的固体杂质后送至闪蒸槽,之后粗甲醇经粗甲醇泵送至甲醇精馏系统或粗甲醇罐区。
1催化剂的还原催化剂在还原过程中出水量约为催化剂重量的18×10-2~20×10-2,其中物理水占3×10-2~5×10-2,化学水占13×10-2~15×10-2。
合成甲醇催化剂的还原过程分为初期、主期、末期三个阶段,还原初期是脱除物理水的过程,还原主期是配氢后产生化学水的过程,还原后期是将残余的水分排出的过程。
催化剂还原过程的热量是由开工喷射器提供,以前使用的是中压过热器蒸汽,压力为2.3~2.8MPa,温度为390~420℃,使用的是动力车间锅炉工段经过本装置蒸汽过热器加热后的蒸汽,压力为1.6~2.1MPa,温度为380~390℃。
整个还原过程中要遵循“提氢不提温、提温不提氢”的原则,保持温度平稳上升。
合成甲醇催化剂本体中有一定量的碳酸盐,在还原中后期会有一定量的CO2生成,而催化剂的活性温度是190℃,在还原中后期,大量的CO2会发生反应,将催化剂的活性激活,此时还原过程会立刻终止,其还原程度就会大大降低。
甲醇合成催化剂运行状况及问题研究

甲醇合成催化剂运行状况及问题研究摘要:本文主要对甲醇合成催化剂问题进行研究,分析甲醇合成催化剂的使用情况以及其中存在的问题,从而提出相应的应对措施,在提升甲醇合成催化剂性能的前提下,延长其使用寿命,希望对相关的工作人员具有一定的参考价值。
关键词:甲醇合成催化剂;化合反应;使用寿命;脱硫剂前言:近年来我国甲醇合成系统的产能逐渐趋于稳定,取得了一定的成效,但是其中仍旧存在一定的问题,例如,甲醇合成催化剂在长时间运行后,其活性就会衰减,令整个甲醇合成系统出现问题,因此,为了确保系统的稳定性,需要加强对甲醇合成催化剂的研究工作,充分发挥其效能。
1甲醇合成系统的工艺简介分析甲醇合成反应的主要原理就是碳氢气体之间的化学反应,由于受到化学反应平衡的制约,其中氢气以及一氧化氮的转化率较低,因此即使甲醇被分离出来后,未参与反应的气体还会返回到甲醇合成塔中,再次发生化合反应,由于甲醇合成系统中主要包含甲醇合成、分离以及循环三个环节。
新鲜气体进入甲醇合成系统前先在脱毒槽进行脱毒,确保新鲜气中硫含量降低至50*10-9以下后,再进入到循环回路中和循环气体混合[1]。
另外,为了避免惰性在系统的回路中聚积,还需要在甲醇合成、降温、分液后驰放气体,可利用前工序的压缩机组回收此股气体,令其返回到系统中,实现循环利用。
2甲醇合成催化剂的运行情况分析2.1系统运行情况分析在实际生产中,甲醇合成系统主要是含有浓度为93.53%的粗甲醇、4.33%的水以及0.23%的杂醇,系统运行的时间越长,则催化剂的活性就会越弱,导致系统在运行过程中发生以下问题:首先是甲醇合成塔的温度会上升,从原本的230℃上升到245℃,同时系统中气体的成分也会发生改变,碳元素的转化率从75%下降至50%。
其次,甲醇合成系统的驰放量也会增加,即使增加压力,也无法提升催化剂的活性。
再次,甲醇合成系统的压力显著上升,而且粗甲醇中乙醇含量也会显著上升,高达3000*10-6,不利于提取出精甲醇,影响其销量。
甲醇合成催化剂的进展

甲醇合成催化剂的进展摘要:本文综述了甲醇合成催化剂的现状,对各种催化剂的性能、特点进行了对比分析,介绍了甲醇合成催化剂的最新技术进展。
关键词:甲醇催化剂1前言甲醇是一种重要化工原料,可广泛用于医药、农药、染料、合成纤维、合成树脂和合成塑料等工业,更重要的是随着石油资源日益短缺,石油价格急剧攀升,甲醇做为可替代能源,大力发展甲醇燃料和甲醇制低碳烯烃及其产品的技术具有巨大的潜力和十分广阔的前景。
充分利用我国丰富的煤炭资源发展合成甲醇具有十分重要的意义。
合成甲醇催化剂是合成甲醇的关键技术之一,本文仅从合成甲醇催化剂的性能参数等方面介绍国内外甲醇催化剂的研究情况和进展[1]。
当代甲醇生产技术以海尔德-托普索(Haldor Topsoe)公司、Kvaerner工艺技术/Synetix公司(英国)、克虏伯-乌德公司、鲁齐油气化学(Lurgi)公司、Synetix公司的技术最为典型。
2甲醇催化剂的现状2.1 锌铬催化剂锌铬(ZnO/Cr2O3)催化剂是一种高压固体催化剂,由德国BASF公司于1923年首先开发研制成功。
锌铬催化剂的活性较低,为了获得较高的催化活性,操作温度必须在590 K~670 K。
为了获取较高的转化率,操作压力必须为25 MPa~35 MPa,故称为高压催化剂。
锌铬催化剂的特点是: a)耐热性能好,能忍受温差在100℃以上的过热过程;b)对硫不敏感;c)机械强度高;d)使用寿命长、范围宽,操作控制容易;d)与铜基催化剂相比较, 其活性低、选择性低、精馏困难(产品中杂质复杂)。
由于在这类催化剂中Cr2O3的质量分数高达10%, 故成为铬的重要污染源之一。
铬对人体是有毒的, 目前该类催化剂已逐步被淘汰。
2.2 铜基催化剂铜基催化剂是一种低温低压甲醇合成催化剂,其主要组分为CuO/ZnO/Al2O3(Cu-Zn-Al),由英国 ICI公司和德国Lurgi公司先后研制成功。
低(中) 压法铜基催化剂的操作温度为210℃~300℃,压力为5MPa~10MPa,其特点是:a)活性好,单程转化率为7%~8%;b)选择性高,大于99%,其杂质只有微量的甲烷、二甲醚、甲酸甲酯,易得到高纯度的精甲醇;c)耐高温性差,对硫敏感。
甲醇合成技术的研究进展
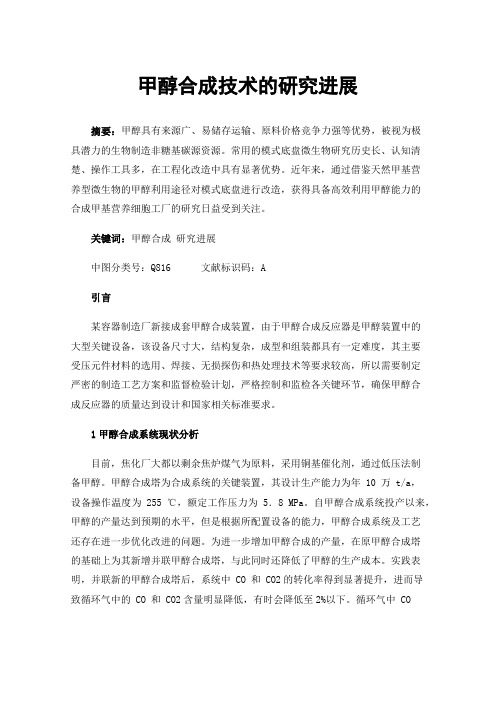
甲醇合成技术的研究进展摘要:甲醇具有来源广、易储存运输、原料价格竞争力强等优势,被视为极具潜力的生物制造非糖基碳源资源。
常用的模式底盘微生物研究历史长、认知清楚、操作工具多,在工程化改造中具有显著优势。
近年来,通过借鉴天然甲基营养型微生物的甲醇利用途径对模式底盘进行改造,获得具备高效利用甲醇能力的合成甲基营养细胞工厂的研究日益受到关注。
关键词:甲醇合成研究进展中图分类号:Q816 文献标识码:A引言某容器制造厂新接成套甲醇合成装置,由于甲醇合成反应器是甲醇装置中的大型关键设备,该设备尺寸大,结构复杂,成型和组装都具有一定难度,其主要受压元件材料的选用、焊接、无损探伤和热处理技术等要求较高,所以需要制定严密的制造工艺方案和监督检验计划,严格控制和监检各关键环节,确保甲醇合成反应器的质量达到设计和国家相关标准要求。
1甲醇合成系统现状分析目前,焦化厂大都以剩余焦炉煤气为原料,采用铜基催化剂,通过低压法制备甲醇。
甲醇合成塔为合成系统的关键装置,其设计生产能力为年 10 万 t/a,设备操作温度为255 ℃,额定工作压力为5.8 MPa。
自甲醇合成系统投产以来,甲醇的产量达到预期的水平,但是根据所配置设备的能力,甲醇合成系统及工艺还存在进一步优化改进的问题。
为进一步增加甲醇合成的产量,在原甲醇合成塔的基础上为其新增并联甲醇合成塔,与此同时还降低了甲醇的生产成本。
实践表明,并联新的甲醇合成塔后,系统中 CO 和 CO2的转化率得到显著提升,进而导致循环气中的 CO 和 CO2含量明显降低,有时会降低至2%以下。
循环气中 CO和 CO2含量的降低,导致合成塔中的 H2过剩,造成合成塔中碳含量与氢含量的严重失衡,最终严重影响甲醇的产量[1]。
2合成甲基营养细胞工厂中构建RuMP同化甲醇2.1增强甲醛受体再生合成甲基营养细胞工厂中甲醛受体Ru5P不足是限制甲醇同化效率的关键原因,阻断F6P进入氧化型磷酸戊糖途径的代谢流,提高非氧化戊糖磷酸途径(non-oxidative pentose phosphatepathway, PPP)相关基因的表达,是增强Ru5P再生的一种策略。
甲醇合成技术的研究进展
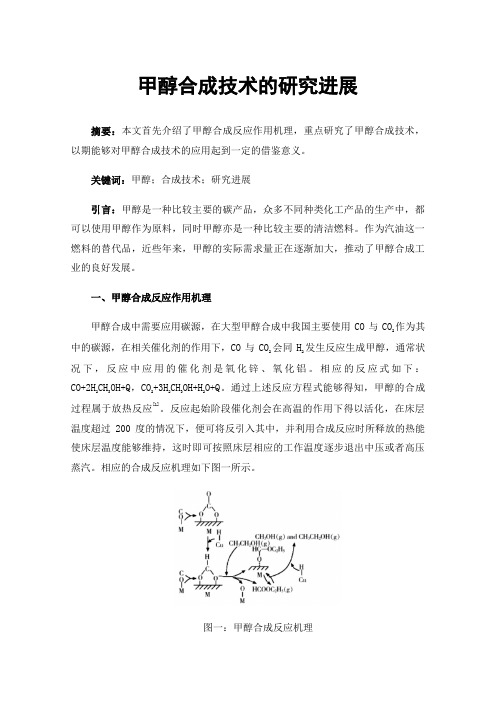
甲醇合成技术的研究进展摘要:本文首先介绍了甲醇合成反应作用机理,重点研究了甲醇合成技术,以期能够对甲醇合成技术的应用起到一定的借鉴意义。
关键词:甲醇;合成技术;研究进展引言:甲醇是一种比较主要的碳产品,众多不同种类化工产品的生产中,都可以使用甲醇作为原料,同时甲醇亦是一种比较主要的清洁燃料。
作为汽油这一燃料的替代品,近些年来,甲醇的实际需求量正在逐渐加大,推动了甲醇合成工业的良好发展。
一、甲醇合成反应作用机理甲醇合成中需要应用碳源,在大型甲醇合成中我国主要使用CO与CO2作为其中的碳源,在相关催化剂的作用下,CO与CO2会同H2发生反应生成甲醇,通常状况下,反应中应用的催化剂是氧化锌、氧化铝。
相应的反应式如下:CO+2H2CH3OH+Q,CO2+3H2CH3OH+H2O+Q。
通过上述反应方程式能够得知,甲醇的合成过程属于放热反应[1]。
反应起始阶段催化剂会在高温的作用下得以活化,在床层温度超过200度的情况下,便可将反引入其中,并利用合成反应时所释放的热能使床层温度能够维持,这时即可按照床层相应的工作温度逐步退出中压或者高压蒸汽。
相应的合成反应机理如下图一所示。
图一:甲醇合成反应机理二、甲醇合成技术研究(一)固定床合成技术自从大型甲醇这一概念被提出,大型甲醇技术就逐步地朝着化的方向发展,许多公司也都相继开展了大型甲醇生产关键技术的研发。
在甲醇规模正逐步向着规模化发展的今日,又因为其相对较小的运行压力,促使装置的体积比较庞大,在此种情况下,大规模甲醇项目大多选择低压法。
从全球范围来看,中低压固定床法制备甲醇的工艺技术目前主要存在Lurgi 中低温法和ICI中低温法,而利用以上两种工艺技术所合成的甲醇产品在全世界的生产量中,占有比重超过了80%。
而我国于上个世纪七十年代建立的生产甲醇装置,便以上述两种工艺技术为主。
相应的固定床工艺技术中包括三菱工艺技术、Linde工艺等,上述工艺技术都是由过往所采用的Lurgi工艺技术或是ICI工艺技术所演变发展而来,从技术上来看,并不具有特别大的先进性差距。
CO2加氢制甲醇催化剂与项目进展
通过对实验数据进行处理和分析,得到了反映催 化剂性能的关键指标,如催化剂的活性、选择性 、稳定性等。
结果分析
通过对实验结果的分析,揭示了催化剂的性能优 势和不足之处,为后续的优化和改进提供了依据 。
项目合作与交流
合作单位
与多家科研单位和企业建立了 紧密的合作关系,共同开展
CO2加氢制甲醇催化剂的研究 和开发。
选择性评价
考察催化剂在不同反应条件下的选择性,确保甲醇为 主要产物。
稳定性评价
通过多次循环反应考察催化剂的稳定性,确保催化剂 长时间使用过程中性能保持稳定。
催化剂活性影响因素
温度
温度过高可能导致催化剂烧结,降低活 性;温度过低则反应速率降低。
原料组成
原料气中H2/CO2比例、杂质成分等 对催化剂活性有很大影响。
案,提高催化剂的性能。
扩大实验规模
02
为了验证催化剂在大规模生产中的应用效果,我们计划在更大
型的装置上进行实验,以确定其在实际生产中的可靠性。
探索工业化应用的可能
03
在实验取得成功后,我们将积极寻求与相关企业和机构合作,
推动该技术的工业化应用。
技术推广与应用前景
01
替代传统甲醇合成技 术
通过实现CO2加氢制甲醇的工业化生 产,可以替代传统的甲醇合成技术, 减少对化石燃料的依赖,降低环境污 染。
反应机理研究
通过对反应机理的研究,明确了反应过程中的关键步骤和影响因素 ,为催化剂的设计和优化提供了理论支持。
催化剂结构与性能关系
通过对催化剂结构与性能关系的深入研究,揭示了催化剂活性中心 的结构特点及其对催化性能的影响。
实验数据与分析
1 2 3
实验数据
甲醇制取低碳烯烃催化剂的制备与改性研究
甲醇制取低碳烯烃催化剂的制备与改性研究催化剂的制备方面,研究人员一般采用溶胶-凝胶法、共沉淀法、物
理混合法等方法来合成催化剂。
其中,溶胶-凝胶法是一种常用的制备方法,可以控制催化剂的粒径、分散度和活性位点的数量。
溶胶-凝胶法的
制备步骤包括溶胶合成、凝胶形成和煅烧三个步骤。
在溶胶合成过程中,
通过调节原料的浓度和反应条件,可以控制溶胶中金属纳米粒子的大小和
分散度。
凝胶形成步骤中,通过调节凝胶前驱体的浓度和pH值,可以控
制凝胶的结构和形貌。
最后,通过煅烧过程,可以获得具有良好结晶性和
活性的催化剂。
催化剂的改性方面,研究人员通过添加助剂或掺杂金属等方法来改善
催化剂的催化性能。
例如,掺杂金属可以改变催化剂的电子结构,提高催
化剂的活性。
添加助剂可以改变催化剂的表面性质,增强催化剂与反应物
的相互作用。
此外,还可以通过调节催化剂的结构和形貌,来改变催化剂
的催化活性和选择性。
目前,研究者对甲醇制取低碳烯烃催化剂的制备和改性进行了广泛的
研究。
一些新型的催化剂,如金属有机框架材料、多孔材料和纳米催化剂等,已经展示出良好的催化性能。
同时,研究者还对催化机理进行了深入
的研究,以进一步优化催化反应的条件和提高催化剂的活性。
总之,甲醇制取低碳烯烃的催化剂制备与改性研究是一个重要的领域。
通过不断地研究和探索,相信会有更加高效、经济和环保的催化剂出现,
为甲醇制取低碳烯烃的工业应用提供更好的选择。
甲醇合成催化剂技术的发展与展望
甲醇合成催化剂技术的发展与展望摘要:目前,甲醇在工业生产中变得越来越为重要,需求量也越来越大。
因此,对于甲醇的合成也就成为了一项课题。
现如今,国内外都积极开展利用甲醇合成过程中所需催化剂的研究,本文也将针对此项技术的发展进行一等的探讨,并对以后甲醇合成催化剂的前景进行了分析,找到催化剂技术发展的最佳途径。
关键词:甲醇催化剂发展展望一、甲醇合成催化剂简介甲醇目前是一种常用的有机化工产品,其用途广泛,也可用作有机化工的原料。
在生产和生活中常常可以看到甲醇的踪影。
譬如农业制药、医学药剂、香料等,直至目前三大合成材料的生成,都需要有甲醇的参与。
随着科学技术的进步,甲醇又有了新的使用方向,对于生物学来说,甲醇可以用来合成人工蛋白;在化学方面,甲醇可以用来做能源,取代汽油。
总之,对甲醇性能的探索与使用正在不断进行中,其越来越突出的优点也在不断被发掘。
甲醇催化剂也在日益凸显着其重要的作用,它在一定程度上衡量了甲醇工业技术水平的。
由于对甲醇需求量的不断上升,对于甲醇合成催化剂的开发也是迫在眉睫的。
无论是我国还是国外,对于甲醇合成催化剂的研发都在不断的进行着,并要求其有更高的效率,在尽可能短的时间内生产更多数量的甲醇,并尽可能使得质量提高。
在生产过程中还需要节约投入的能源,降低生产成本,促进经济效益最大化,使得甲醇工业能够有利发展。
二、国内外甲醇合成催化剂技术的发展状况无论国内还是国外,催化剂的发展都经历了从锌铬催化剂、铜基催化剂、非铜基催化剂到液相催化剂的阶段,在摸索过程中也经历了坎坷,但是最终仍然取得了不错的成果。
就锌铬催化剂而言,这类催化剂是由德国的公司首先研发的,这种催化剂活性较低,操作压力也较小,对于此类催化剂还有一定的毒性,杂质含量也较多,所以这种催化剂已经退出了历史舞台,被工厂所淘汰。
铜基催化剂是由英国与德国公司先后进行研发的,这种催化剂的温度较高,但是操作压力也同样很小,可以说是低压催化剂,相对于锌铬催化剂来说,合成的温度较低,降低了供热的资源,并且对甲醇的生成也起到了促进作用,不仅活性好,选择性也十分高。
关于甲醇合成过程中催化剂的研究
司也随后研制了同类催化剂,其代表产品为CuO/ZnO/Al 2O 3。
在催化合成过程中操作压力为5~10MPa ;温度为200~300℃。
比最初甲醇合成工艺所需的压力和温度要低很多,属于低温低压操作条件的范畴。
这类催化剂的特点是:耐热性能较差、活性较高、选择性也高;但对杂质较为敏感;而这种低压法生产设备的体积大,从而占地面积大、投资也较大。
1.2.3 贵金属负载类催化剂贵金属负载类催化剂是由MgO 、SiO 2、ZrO 2等氧化物作为载体,将某些贵金属负载,通常贵金属选择Pd 、Pt 、Au 等。
其代表产品为PtCr/Si SiO 2、PtW/SiO 2等,这类催化剂的优点主要在于对甲醇的选择性很高,有的催化剂即使在合成过程中其他杂质较多情况下仍然可以保持高选择性以及高转化率。
2 反应条件对甲醇合成催化剂的影响在反应过程中催化剂催化效果的好坏不仅和自身的性质、结构有关,而且反应条件也对催化剂有很大的影响作用。
适宜的反应条件会让催化剂的活性达到最佳状态。
所以在甲醇合成过程中,研究不同反应条件对于催化剂活性的影响很有必要。
2.1 压力对催化剂的影响甲醇合成反应为:CO+2H 2=CH 3OH,该反应的正方向是分子数减少,根据化学平衡相关知识可以知道,当压力增大时反应会向生成反应物方向移动,即有利于甲醇产品的合成。
,所以,当压力增大时,甲醇转化率会随着压力的增加而升高。
除此以外,催化剂上反应物的吸附以及生成物的脱附也和压力有关。
实验研究表明,当压力增加10%,甲醇的转化率亦增加10%。
但并非压力一直增加转化率会一直随之增加,和其他对压力有要求的反应一样,压力增加虽然会提高产物转化率,但有一个限值。
对于甲醇生产来讲,当压力超过8MPa ,甲醇转化率反而呈开始下降趋势。
2.2 温度对催化剂的影响温度作为化学反应过程中至关重要的反应条件之一,对于化学反应速率、反应方向都有着很重要的影响作用。
对于使用催化剂的化学反应中,温度更是不能忽视的因素之一。
- 1、下载文档前请自行甄别文档内容的完整性,平台不提供额外的编辑、内容补充、找答案等附加服务。
- 2、"仅部分预览"的文档,不可在线预览部分如存在完整性等问题,可反馈申请退款(可完整预览的文档不适用该条件!)。
- 3、如文档侵犯您的权益,请联系客服反馈,我们会尽快为您处理(人工客服工作时间:9:00-18:30)。
化学反应工程论文合成甲醇催化剂的研究进展摘要:了解甲醇工业的发展现状及前景。
从催化剂组成、种类、各组分功能及失活方式对甲醇催化剂进行探究,同时探索甲醇合成的新方法和新工艺,并对甲醇合成催化剂的动力学研究进行总结。
关键词:甲醇合成、催化剂种类、失活、三相床、生物质秸秆、动力学1.1甲醇工业发展现状能源问题已经成为制约我国国民经济发展的战略问题。
从国家安全角度看,能源资源的稳定供应始终是一个国家特别是依赖进口的国家关注的重点,是国家安全的核心内容。
随着中国工业化、城市化进程的加快以及居民消费结构的升级,石油、天然气等清洁高效能源在未来中国能源消费结构中将会占据越来越重要的地位。
目前中国石油消费严重依赖进口,石油资源已经和国家安全紧密联系起来,并成为中国能源安全战略的核心o在我国能源探明储量中,煤炭占94%,石油占5.4%,天然气占0.6%,这种“富煤贫油少气”的能源结构特点,决定了我国能源生产与消费以煤为主的格局将长期占主导地位。
国民经济的持续发展,对能源产品尤其是清洁能源的需求持续增长。
结合我国以煤为主的能源结构现状,大力发展煤基能源化工成为我国解决能源问题的主要途径。
以煤气化为核心的多联产系统则是针对我国面临的能源需求增长、液体燃料短缺、环境污染严重等一系列问题,提出的一条解决我国能源领域可持续发展的重要途径煤经气化后成为合成气,净化以后可用于生产化工原料、液体燃料(合成油、甲醇、二甲醚)和电力。
多联产系统所生产的液体燃料,尤其是甲醇和二甲醚可作为煤基车用替代燃料,可以部分缓解我国石油的短缺。
同时,甲醇还可以用来生产烯烃和丙烯,以煤化工产品“替代”一部分传统的石油化工产品,对减少石油的消耗量具有重要意义。
甲醇是一种重要的化工原料,又是一种潜在的车用燃料和燃料电池的燃料,因此合成甲醇的研究和探索在国际上一直受到重视。
特别是近年来,随着能源危机的出现、C1化学的兴起,作为C1化学重要物质的甲醇,它的应用得到不断的开发,用量猛增,甲醇工业得到了迅猛发展,在世界基础有机化工原料中,甲醇用量仅次于乙烯、丙烯和苯,居第四位。
1.2甲醇发展前景甲醇作为一种基础化工原料,在化工、医药、轻纺等领域有着广泛的用途。
主要用于制造甲醛、氯甲烷、醋酸、甲胺、甲基丙烯酸甲酯、甲酸甲酯(MF)、二甲醚(DME)、碳酸二甲酯(DMC)、对苯二甲酸二甲酯(DMT)、甲基叔丁基醚(MTBE)等一系列有机化工产品。
随着甲醇深加工产品的不断增加和化学应用领域的不断开拓,甲醇在许多领域有着广阔的应用前景:(1)甲醇具有高辛烷值,是富含氧燃料,燃烧过程比汽油充分彻底,尾气中CO、S02、NOx及碳氢化合物可显著降低,作为清洁燃料替代汽油或与汽油掺混使用;(2)甲醇燃料电池即将投入商业化运行;(3)甲醇作为裂解原料在变压吸附制氢中得到初步利用;(4)甲醇制取微生物蛋白作为饲料乃至食品添加剂,国外已有工业化装置;(5)甲酸甲酯(MF)、二甲醚(DME)等近年来已成为Cl化学的热点产品;(6)甲醇制汽油(MTG)、甲醇制烯烃(MTO)、甲醇制丙烯的(MTP)技术都有所突破,成为煤制汽油和煤制烯烃的重要途径。
2.1催化剂的组成活性组分根据活性组分的不同,CO2 加氢合成甲醇的催化剂可大致分为两大类。
一类是以铜元素作为主要活性组分的铜基催化剂;另一类是以贵金属作为活性组分的负载型催化剂。
铜基催化剂CO2 加氢合成甲醇用铜基催化剂多数是在合成气制甲醇催化剂基础上发展而来。
尽管自20 世纪,60 年代起,以ICI公司为代表生产的Cu/ZnO/Al2O3催化剂就已成为合成气制甲醇的商用催化剂,但有关活性中心的问题,尤其是Cu 在催化反应中的存在状态仍然存在不少争议。
当铜基催化剂用于CO2加氢时,由于CO2 气体自身具有一定的氧化性,该问题变得更为复杂。
一些研究者认为在CO2加氢合成甲醇反应中,铜基催化剂中的铜以Cu0和Cu+(或Cuδ+)的形式存在,这两种形式的Cu 物种均为活性中心。
其依据来自于实验检测与理论计算两方面。
Cu+的检测一般采用XPS 技术。
由于金属Cu 与Cu2O 的键合能(Cu 2p3/2分别为932.6 eV和932.4 eV)十分接近,无法分辨Cu0和Cu+,而金属Cu 和Cu2O 的Auger谱CuKLL 线差别较大(分别为918.65 eV 和917.9 eV),可以区分Cu0和Cu+。
因此,XPS 要与Auger 谱连用。
Słoczyński 等[4]将Cu/ZnO/ZrO2催化剂用于CO2加氢,反应10 天后对催化剂进行检测,发现Cu2O 的存在。
Toyir 等[5-6]采用甲氧基铜、乙酰丙酮锌作前体制备了Cu/ZnO/SiO2催化剂,在反应中检测到Cu+的存在。
他们发现Cu+的存在提高了甲醇的选择性,且Cu+/Cu0的比值可通过改变助剂镓(Ga)的加入量进行调节。
Saito 等[7]也提出了类似观点,并认为当Cu+/Cu0的比值为0.7 时,催化剂的性能最好。
徐征等[8-9]研究了CuO-ZnO 基催化剂上的CO2 加氢反应,认为活性中心是存在于CuO-ZnO固溶体中的Cu-□-Zn-O(□为氧空穴),活性中心的Cu 价态为Cu+和Cu0。
也有作者采用其它技术检测到铜基催化剂中Cu+的存在。
如Fierro等[10]利用H2-CO2-H2 氧化还原循环证实还原后的CuO/ZnO 中Cu 可部分被CO2 氧化,说明有Cuδ+存在,而纯CuO 中的Cu 不存在这种情况。
原位EXAFS 研究表明,Cu/ZrO2 在催化加氢反应中有76%的Cu0被CO2 氧化,其中Cu+占27%,Cu2+占49%[11]。
Arena 等[12]则采用CO 分子作探针分子,通过红外光谱检测到Cu/ZnO/ZrO2催化剂中Cuδ+的形成,指出Cuδ+位于金属氧化物界面上,Cu与ZnO、ZrO2 之间的相互作用有利于Cuδ+的稳定。
此外,密度泛函理论的计算也表明Cuδ+出现在Cu/金属氧化物界面上,甲醇生成反应主要在Cuδ+上进行,而逆水汽反应在Cu0上进行[13]。
Wang 等[14]采用Unity Bond Index-Quadratic Exponental Potential方法对Cu(100)上的CO2 加氢反应进行了理论计算。
结果表明铜晶面上氧的覆盖度与反应性能之间呈一火山型曲线的关系,Cu+/Cu0的比例控制催化反应的活性。
2.2甲醇合成工业催化剂分类以及优缺点锌铬催化剂锌铬(ZnO/Cr2O3)催化剂是一种高压固体催化剂,由德国BASF公司于1923年首先开发研制成功。
锌铬催化剂的活性较低,为了获得较高的催化活性,操作温度必须在590 K-670 K。
为了获取较高的转化率,操作压力必须为25 MPa-35 MPa,因此被称为高压催化剂。
锌铬催化剂的特点是: a)耐热性能好,能忍受温差在100℃以上的过热过程; b)对硫不敏感; c)机械强度高; d)使用寿命长,使用范围宽,操作控制容易; d)与铜基催化剂相比较, 其活性低、选择性低、精馏困难(产品中杂质复杂)。
由于在这类催化剂中Cr2O3的质量分数高达10%, 故成为铬的重要污染源之一。
铬对人体是有毒的, 目前该类催化剂已逐步被淘汰。
铜基催化剂是一种低温低压甲醇合成催化剂, 其主要组分CuO/ZnO/Al2O3(Cu-Zn-Al),由英国ICI公司和德国Lurgi公司先后研制成功。
低(中)压法铜基催化剂的操作温度为210℃-300℃,压力为5MPa-10MPa,比传统的合成工艺温度低得多,对甲醇反应平衡有利。
其特点是: a)活性好,单程转化率为7% -8%;b)选择性高,大于99%,其杂质只有微量的甲烷、二甲醚、甲酸甲酯,易得到高纯度的精甲醇; c)耐高温性差,对硫敏感。
钯系催化剂由于铜基催化剂的选择性可达99%以上,所以新型催化剂的研制方向在于进一步提高催化剂的活性、改善催化剂的热稳定性以及延长催化剂的使用寿命。
新型催化剂的研究大都基于过渡金属、贵重金属等,但与传统(或常规)催化剂相比较,其活性并不理想。
例如,以贵重金属钯为主催化组分的催化剂,其活性提高幅度不大,有些催化剂的选择性反而降低。
钼系催化剂铜基催化剂是甲醇合成工业中的重要催化剂, 但是由于原料气中存在少量的H 2S、CS2、Cl2等,极易导致催化剂中毒,因此耐硫催化剂的研制越来越引起人们的兴趣。
天津大学Zhang Jiyan研制出 MoS2/K2CO3/MgO-SiO2含硫甲醇合成催化剂,温度为533K,压力为8.1MPa,空速3000 h-1,φ(H2)∶φ(CO)=1.42,含硫质量浓度为1350 mg/L,CO的转化率为36.1%,甲醇的选择性为53.2%。
该催化剂虽然单程转化率较高,但选择性只有50%,副产物后处理复杂,距工业化应用还有较大差距。
除此之外还有Cu-Zn-Al-V系列的催化剂。
Cu-Zn-Al系铜基催化剂以南化集团研究院为代表的C207、C301、C3011、NC5011、C306和C307型, Cu-Zn-Al-V系铜基催化剂以西南化工研究院为代表的CN J202、C302、C3021、C3022、CN J206和XNC98型。
目前广泛应用的为铜基催化剂。
以后的铜基催化剂研究方向为低温、低压、高活性、高选择性、节能环保为重点。
2.3催化剂各组分功能催化剂各组分功能:CuO:经过还原以后成为催化剂的活性中心,存在于CuO-Cu 的活性界面上。
ZnO:稳定活性中心Cu+(亚铜);保持Cu(铜微晶)的高度分散;活化H2(增加催化剂吸附氢气的速率);吸收合成气中的毒物(吸收后以ZnX存在);Cu/ ZnO 界面形成独特的活性中心(有理论认为反应是双功能,Cu,ZnO参与不同的步骤,构成总的机理);ZnO使Cu的特俗晶面或表面缺陷得到稳定。
Al2O3:对合成反应没有催化活性,但是Al2O3含量在10%左右的时候,催化剂的晶体尺寸减少,铜的表面和催化剂的总表面的比值最大,活性最好。
另外还可以提高催化剂的稳定性(加入Al2O3可以形成作为分散剂和隔离剂的铝酸锌而防止铜粒子的烧结,是高分散Cu/ ZnO的稳定剂)石墨:焙烧之后加入,方便冲模压片成型,具有光泽感。
2.4催化剂失活催化剂失活:催化剂的活性是决定甲醇合成新工艺开发成功与否的关键因素之一。
甲醇生产过程中,常会发生催化剂中毒、高温烧结等现象,这些非正常现象既缩短了甲醇合成催化剂的使用寿命,又影响了甲醇的质量。
影响催化剂使用寿命的因素很多,包括热失活、积炭、中毒失活、污染失活、强度下降等。
热失活催化剂的烧结和热失活是指由高温引起的催化剂结构和性能的变化。
高温除了引起催化剂的烧结外,还会引起催化剂化学组成和相组成的变化。