甲醇合成催化剂知识
合成甲醇催化剂还原、钝化的探究

合成甲醇催化剂还原、钝化的探究摘要:甲醇催化剂合成情况的好坏将直接影响甲醇合成系统的运行状况,也关乎甲醇产品的产量及消耗的高低。
基于此,本文主要对合成甲醇催化剂还原、钝化的进行探究.关键词:合成甲醇催化剂;还原;钝化引言甲醇合成系统工艺流程主要是来自合成气压缩机的合成气,经气气换热器A/B 壳程被管壳式甲醇合成塔A/B的高温出塔气预热至200℃左右,进入甲醇合成塔A/B,在铜基催化剂的作用下CO、CO2与H2进行反应生成甲醇和水;甲醇合成塔A/B出口气经气气换热器管程与入塔气换热后,温度降至95℃左右,然后经水冷器ⅠA/B冷却到65℃,再经水冷器ⅡA/B冷却到40℃后,进入甲醇分离器A/B进行气液分离。
甲醇分离器顶部出来的分离掉甲醇的大部分气体作为循环气去合成气压缩机,经合成气压缩机增压并补充新鲜气后送入甲醇合成塔进行下一轮反应;一小部分作为弛放气送往氢回收系统回收H2。
甲醇分离器分离出的粗甲醇则通过一级过滤器和二级过滤器除去其中的固体杂质后送至闪蒸槽,之后粗甲醇经粗甲醇泵送至甲醇精馏系统或粗甲醇罐区。
1催化剂的还原催化剂在还原过程中出水量约为催化剂重量的18×10-2~20×10-2,其中物理水占3×10-2~5×10-2,化学水占13×10-2~15×10-2。
合成甲醇催化剂的还原过程分为初期、主期、末期三个阶段,还原初期是脱除物理水的过程,还原主期是配氢后产生化学水的过程,还原后期是将残余的水分排出的过程。
催化剂还原过程的热量是由开工喷射器提供,以前使用的是中压过热器蒸汽,压力为2.3~2.8MPa,温度为390~420℃,使用的是动力车间锅炉工段经过本装置蒸汽过热器加热后的蒸汽,压力为1.6~2.1MPa,温度为380~390℃。
整个还原过程中要遵循“提氢不提温、提温不提氢”的原则,保持温度平稳上升。
合成甲醇催化剂本体中有一定量的碳酸盐,在还原中后期会有一定量的CO2生成,而催化剂的活性温度是190℃,在还原中后期,大量的CO2会发生反应,将催化剂的活性激活,此时还原过程会立刻终止,其还原程度就会大大降低。
XNC-98系列合成甲醇催化剂使用说明书
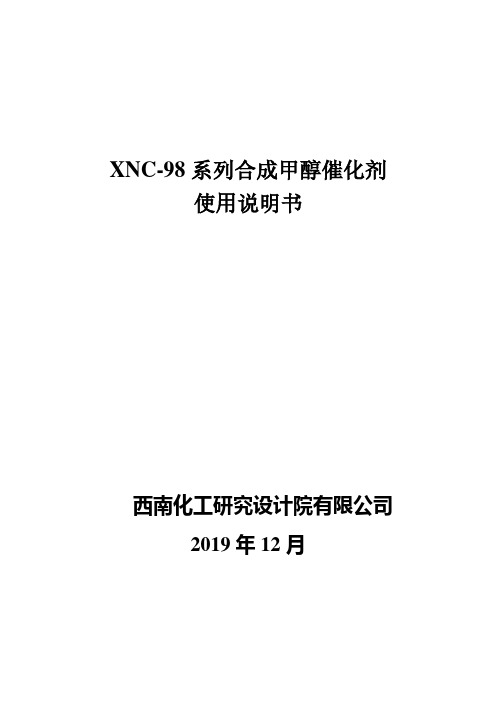
XNC-98系列合成甲醇催化剂使用说明书西南化工研究设计院有限公司2019年12月目次一.催化剂的主要物化特性 (2)二.催化剂的使用条件 (3)三.催化剂装填 (3)四.催化剂的升温、还原 (3)五.操作注意事项 (6)六.停车 (6)七.卸催化剂 (7)八.其他 (7)XNC-98系列合成甲醇催化剂使用说明书XNC-98系列催化剂是我公司研制和开发的一种高活性、高选择性的甲醇合成催化剂。
用于低温低压下由碳氧化物与氢合成甲醇。
可适用于各种类型的甲醇合成反应器。
具有低温活性高、热稳定性好的特点。
常用的操作温度为210~310℃,操作压力3.0~15.0MPa,空速5000~20000h-1(最佳空速8000~12000h-1)。
本催化剂可广泛适用于各种原料生产的合成气。
一.催化剂的主要物化特性1.催化剂主要物理性质外观:有黑色金属光泽的圆柱体外形尺寸(直径×高),mm:6×(4.5~5)堆密度,Kg/L:~1.25径向抗压碎强度,N/cm:≥2002.催化剂化学组成催化剂主要化学组成列于下表:3.催化剂的活性按本催化剂质量检验标准规定,在下述活性检验条件下:催化剂装量:4mL 粒度: 20目~40目反应压力: 5.00±0.05MPa 空速: 10000±300h-1反应温度:230±1℃、250±1℃气体组成:CO 12×10-2~15×10-2,CO2 3×10-2~8×10-2惰性气体 7×10-2~10×10-2,其余为H2。
催化剂活性为:230℃时,催化剂的时空收率≥1.50Kg/L∙h;250℃时,催化剂的时空收率≥2.0Kg/L∙h。
4.催化剂的使用寿命在正常条件下运转寿命为3年以上。
二.催化剂的使用条件XNC-98系列催化剂在下列条件范围内使用反应压力: 3.0~15.0MPa反应温度:还原好的催化剂在190℃就具有较好的活性,一般使用温度是200~300℃。
制甲醇合成操作问答 使用
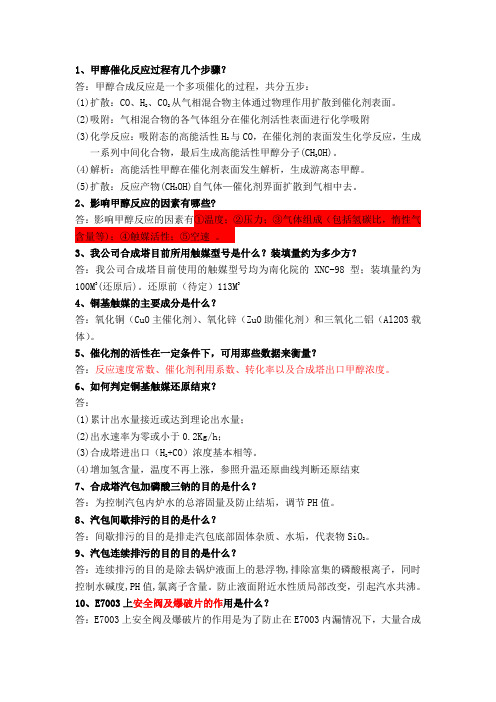
1、甲醇催化反应过程有几个步骤?答:甲醇合成反应是一个多项催化的过程,共分五步:(1)扩散:CO、H2、CO2从气相混合物主体通过物理作用扩散到催化剂表面。
(2)吸附:气相混合物的各气体组分在催化剂活性表面进行化学吸附(3)化学反应:吸附态的高能活性H2与CO,在催化剂的表面发生化学反应,生成一系列中间化合物,最后生成高能活性甲醇分子(CH3OH)。
(4)解析:高能活性甲醇在催化剂表面发生解析,生成游离态甲醇。
(5)扩散:反应产物(CH3OH)自气体—催化剂界面扩散到气相中去。
2、影响甲醇反应的因素有哪些?答:影响甲醇反应的因素有①温度;②压力;③气体组成(包括氢碳比,惰性气含量等);④触媒活性;⑤空速。
3、我公司合成塔目前所用触媒型号是什么?装填量约为多少方?答:我公司合成塔目前使用的触媒型号均为南化院的XNC-98型;装填量约为100M3(还原后)。
还原前(待定)113M34、铜基触媒的主要成分是什么?答:氧化铜(CuO主催化剂)、氧化锌(ZuO助催化剂)和三氧化二铝(Al2O3载体)。
5、催化剂的活性在一定条件下,可用那些数据来衡量?答:反应速度常数、催化剂利用系数、转化率以及合成塔出口甲醇浓度。
6、如何判定铜基触媒还原结束?答:(1)累计出水量接近或达到理论出水量;(2)出水速率为零或小于0.2Kg/h;(3)合成塔进出口(H2+CO)浓度基本相等。
(4)增加氢含量,温度不再上涨,参照升温还原曲线判断还原结束7、合成塔汽包加磷酸三钠的目的是什么?答:为控制汽包内炉水的总溶固量及防止结垢,调节PH值。
8、汽包间歇排污的目的是什么?答:间歇排污的目的是排走汽包底部固体杂质、水垢,代表物SiO2。
9、汽包连续排污的目的目的是什么?答:连续排污的目的是除去锅炉液面上的悬浮物,排除富集的磷酸根离子,同时控制水碱度,PH值,氯离子含量。
防止液面附近水性质局部改变,引起汽水共沸。
10、E7003上安全阀及爆破片的作用是什么?答:E7003上安全阀及爆破片的作用是为了防止在E7003内漏情况下,大量合成气泄漏到循环水系统后造成循环水系统设备、管道超压或爆炸事故的发生或排放到回水系统威胁循环水系统安全。
甲醇合成催化剂反应机理及应用1

甲醇合成催化剂的反应机理及应用新疆广汇新能源有限公司新疆哈密839000 杨林君摘要:本文介绍了甲醇合成反应的机理,合成催化剂的制备;对XNC-98催化剂的使用情况做了介绍。
关键词:甲醇合成催化剂甲醇是重要的有机化工原料,碳一化学的母体,广泛用于生产塑料、纤维、橡胶、染料、香料、医药和农药等,还是重要的有机溶剂。
甲醇在发达国家其产量仅次于乙烯、丙烯和苯,居第四位。
甲醇用作汽车发动机燃料,所谓甲醇汽油,今后随着石油不断开采资源日渐减少,直至枯竭,特别在我国少油多煤的资源下,甲醇用作汽车燃料将达亿吨/年以上,跃升化工产品的首位。
研究开发应用推广近代甲醇合成工艺与合成塔技术和建设大型化生产装置,成为我国甲醇工业大发展的必由之路[1]。
随着甲醇工业的发展,以低压法铜基催化剂为代表的甲醇合成技术得到了很大的发展。
国内近年来在合成催化剂的反应机理、性能及应用等方面研究不断深入,开发出具有世界先进水平的合成催化剂。
一甲醇合成反应的机理甲醇合成反应机理与活性中心的研究一直是甲醇合成反应过程的研究重点,其对高效催化剂的开发、实验现象本质特征的解释和反应结果的预测都具有重要意义。
一个合理的甲醇合成反应历程能够为反应条件的优化以及催化剂制备过程等催化体系的改进提供理论依据,为工业化生产提供理论支撑。
按合成甲醇直接碳源的不同,将机理划分为以下3种:CO与CO2共同作为直接碳源机理、CO作为直接碳源机理以及CO2作为直接碳源机理[2]。
1.1 CO直接作为碳源机理长期已来,在铜基催化剂上加氢合成甲醇的碳源问题都是研究者争论的焦点问题。
Herman 等研究了CO/H2体系在Cu/ZnO/Al2O3催化剂上的反应,认为反应的活性中心是Cu+,H2的解离吸附发生在ZnO上,并提出以下反应机理:CO+*(Cu2O)→CO*(Cu2O)H2+2*(ZnO)→2H*(ZnO)CO*(Cu2O)+H*(ZnO)→HCO*(Cu2O)+*(ZnO)H*(ZnO)+HCO*(Cu2O)→CH2O*(Cu2O)+*(ZnO)2H*(ZnO)+CH2O*(Cu2O)→CH3OH*(Cu2O)+2*(ZnO)CH3OH*(Cu2O)→CH3OH+*(Cu2O)式中:*指催化剂的活性吸附位。
甲醇合成催化剂技术的发展与展望

甲醇合成催化剂技术的发展与展望摘要:目前,甲醇在工业生产中变得越来越为重要,需求量也越来越大。
因此,对于甲醇的合成也就成为了一项课题。
现如今,国内外都积极开展利用甲醇合成过程中所需催化剂的研究,本文也将针对此项技术的发展进行一等的探讨,并对以后甲醇合成催化剂的前景进行了分析,找到催化剂技术发展的最佳途径。
关键词:甲醇催化剂发展展望一、甲醇合成催化剂简介甲醇目前是一种常用的有机化工产品,其用途广泛,也可用作有机化工的原料。
在生产和生活中常常可以看到甲醇的踪影。
譬如农业制药、医学药剂、香料等,直至目前三大合成材料的生成,都需要有甲醇的参与。
随着科学技术的进步,甲醇又有了新的使用方向,对于生物学来说,甲醇可以用来合成人工蛋白;在化学方面,甲醇可以用来做能源,取代汽油。
总之,对甲醇性能的探索与使用正在不断进行中,其越来越突出的优点也在不断被发掘。
甲醇催化剂也在日益凸显着其重要的作用,它在一定程度上衡量了甲醇工业技术水平的。
由于对甲醇需求量的不断上升,对于甲醇合成催化剂的开发也是迫在眉睫的。
无论是我国还是国外,对于甲醇合成催化剂的研发都在不断的进行着,并要求其有更高的效率,在尽可能短的时间内生产更多数量的甲醇,并尽可能使得质量提高。
在生产过程中还需要节约投入的能源,降低生产成本,促进经济效益最大化,使得甲醇工业能够有利发展。
二、国内外甲醇合成催化剂技术的发展状况无论国内还是国外,催化剂的发展都经历了从锌铬催化剂、铜基催化剂、非铜基催化剂到液相催化剂的阶段,在摸索过程中也经历了坎坷,但是最终仍然取得了不错的成果。
就锌铬催化剂而言,这类催化剂是由德国的公司首先研发的,这种催化剂活性较低,操作压力也较小,对于此类催化剂还有一定的毒性,杂质含量也较多,所以这种催化剂已经退出了历史舞台,被工厂所淘汰。
铜基催化剂是由英国与德国公司先后进行研发的,这种催化剂的温度较高,但是操作压力也同样很小,可以说是低压催化剂,相对于锌铬催化剂来说,合成的温度较低,降低了供热的资源,并且对甲醇的生成也起到了促进作用,不仅活性好,选择性也十分高。
催化剂甲醇合成
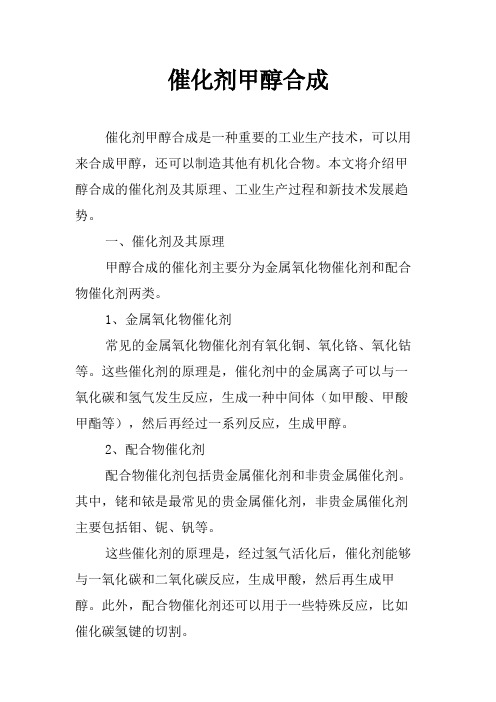
催化剂甲醇合成催化剂甲醇合成是一种重要的工业生产技术,可以用来合成甲醇,还可以制造其他有机化合物。
本文将介绍甲醇合成的催化剂及其原理、工业生产过程和新技术发展趋势。
一、催化剂及其原理甲醇合成的催化剂主要分为金属氧化物催化剂和配合物催化剂两类。
1、金属氧化物催化剂常见的金属氧化物催化剂有氧化铜、氧化铬、氧化钴等。
这些催化剂的原理是,催化剂中的金属离子可以与一氧化碳和氢气发生反应,生成一种中间体(如甲酸、甲酸甲酯等),然后再经过一系列反应,生成甲醇。
2、配合物催化剂配合物催化剂包括贵金属催化剂和非贵金属催化剂。
其中,铑和铱是最常见的贵金属催化剂,非贵金属催化剂主要包括钼、铌、钒等。
这些催化剂的原理是,经过氢气活化后,催化剂能够与一氧化碳和二氧化碳反应,生成甲酸,然后再生成甲醇。
此外,配合物催化剂还可以用于一些特殊反应,比如催化碳氢键的切割。
二、工业生产过程甲醇的工业生产过程主要有两种方法:一是合成气法,即将氢气和一氧化碳反应生成甲醇;二是天然气法,即从天然气中提取甲烷,然后通过一系列化学反应生成甲醇。
合成气法合成气法是目前最常用的甲醇生产方法。
生产过程主要包括合成气的制备、催化剂的选择和反应的控制。
1、合成气制备合成气制备方法包括煤气、重油和天然气重整、重油催化裂解和煤气化等。
其中,天然气煤气化是最常用的方法。
通过高温高压反应,将天然气转化成含有一氧化碳和氢气的合成气。
2、催化剂选择甲醇合成的催化剂主要是氧化物和配合物催化剂。
目前工业生产中,氧化铜和氧化锌是最常用的催化剂,伴有一些助剂。
3、反应控制甲醇合成的反应控制十分关键。
在反应过程中,必须控制反应温度、压力和催化剂用量等参数,才能获得高质量的甲醇。
天然气法天然气法是一种新兴的甲醇生产方法。
与合成气法相比,天然气法具有取之不尽、用之不竭的优势,并且生产过程更加环保。
1、天然气的处理天然气中的甲烷需要经过催化裂解,生成含有一氧化碳和氢气的合成气。
2、合成气的制备和处理生产过程与合成气法一致。
一甲醇装置合成催化剂(NC307)使用小结已有

甲醇装置NC307合成催化剂使用技术王会强武汉理工大学摘要:本文讲述了NC-307甲醇合成催化剂在大庆油田甲醇厂一甲醇装置的实际应用情况;阐述了NC307合成催化剂所具有的特点,总结了NC307在生产操作及管理中的使用经验,具有一定的指导意义。
主题词:甲醇装置合成反应 NC307催化剂保护周期一、合成塔简介大庆油田化工有限公司甲醇分公司一甲醇装置合成塔,采用鲁奇固定管板列管式甲醇合成反应器,年设计生产能力精醇10万吨,日产精醇333吨,日粗醇400吨。
合成塔规格:二、合成触媒装填及升温还原情况1、目前一甲醇装置使用合成的触媒型号为NC307 ,触媒生产厂家:南化院;2、NC307规格:规格:∮5.0×(4.~5)mm外观:两端为球面的黑色圆柱体堆密度:1.40-1.6kg/l比表面:90-110m2/g耐热后甲醇时空产率:≥1.0g/mL催化剂.小时3、装填时间:2007年4月12日,装填重量:34.8吨(23.2立方)。
4、触媒升温还原情况:07年4月13日完成触媒的装填工作,从4月14日22:00开始进行触媒的升温还原,18日19:30升温还原结束,还原时间累计117.5小时。
在整个还原过程中物理出水量为1.1328吨,化学出水量 3.802 吨,还原结束经72小时低负荷运转后转入正常生产,初始使用温度为控制合成塔出口温度232±1℃运行。
三、运行情况:本炉触媒自07年4月18日——09年3月25日共计运行16570小时,累计生产精醇21.26万吨,日产精醇最高产量412吨/日,目前合成塔进口温度217.63℃,出口温度249℃,预计触媒还有5个的使用时间。
1、合成塔触媒提温情况:2、触媒不同时期的相关操作数据:合成触媒初期:239-240℃工况四、NC-307催化剂的特点:在NC-307催化剂使用过程中,我们总结出该催化剂具有以下特点:一是易还原,整个还原过程易于控制。
关于甲醇合成过程中催化剂的研究
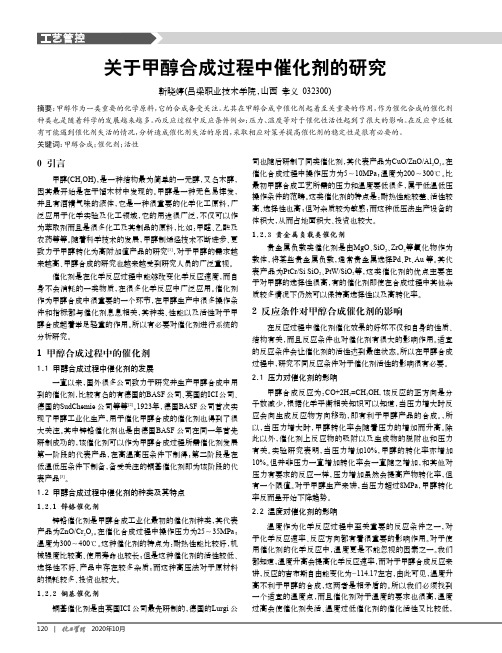
司也随后研制了同类催化剂,其代表产品为CuO/ZnO/Al 2O 3。
在催化合成过程中操作压力为5~10MPa ;温度为200~300℃。
比最初甲醇合成工艺所需的压力和温度要低很多,属于低温低压操作条件的范畴。
这类催化剂的特点是:耐热性能较差、活性较高、选择性也高;但对杂质较为敏感;而这种低压法生产设备的体积大,从而占地面积大、投资也较大。
1.2.3 贵金属负载类催化剂贵金属负载类催化剂是由MgO 、SiO 2、ZrO 2等氧化物作为载体,将某些贵金属负载,通常贵金属选择Pd 、Pt 、Au 等。
其代表产品为PtCr/Si SiO 2、PtW/SiO 2等,这类催化剂的优点主要在于对甲醇的选择性很高,有的催化剂即使在合成过程中其他杂质较多情况下仍然可以保持高选择性以及高转化率。
2 反应条件对甲醇合成催化剂的影响在反应过程中催化剂催化效果的好坏不仅和自身的性质、结构有关,而且反应条件也对催化剂有很大的影响作用。
适宜的反应条件会让催化剂的活性达到最佳状态。
所以在甲醇合成过程中,研究不同反应条件对于催化剂活性的影响很有必要。
2.1 压力对催化剂的影响甲醇合成反应为:CO+2H 2=CH 3OH,该反应的正方向是分子数减少,根据化学平衡相关知识可以知道,当压力增大时反应会向生成反应物方向移动,即有利于甲醇产品的合成。
,所以,当压力增大时,甲醇转化率会随着压力的增加而升高。
除此以外,催化剂上反应物的吸附以及生成物的脱附也和压力有关。
实验研究表明,当压力增加10%,甲醇的转化率亦增加10%。
但并非压力一直增加转化率会一直随之增加,和其他对压力有要求的反应一样,压力增加虽然会提高产物转化率,但有一个限值。
对于甲醇生产来讲,当压力超过8MPa ,甲醇转化率反而呈开始下降趋势。
2.2 温度对催化剂的影响温度作为化学反应过程中至关重要的反应条件之一,对于化学反应速率、反应方向都有着很重要的影响作用。
对于使用催化剂的化学反应中,温度更是不能忽视的因素之一。
- 1、下载文档前请自行甄别文档内容的完整性,平台不提供额外的编辑、内容补充、找答案等附加服务。
- 2、"仅部分预览"的文档,不可在线预览部分如存在完整性等问题,可反馈申请退款(可完整预览的文档不适用该条件!)。
- 3、如文档侵犯您的权益,请联系客服反馈,我们会尽快为您处理(人工客服工作时间:9:00-18:30)。
甲醇合成催化剂知识d i4 X+ }1 z! j0 v1 铜基催化剂的催化原理 + W7 b1 C1 Y9 W4 M1 h)o9 F0 t8 j* c: D q, |6 O 目前,低压甲醇合成铜基催化剂主要组分是 CuO、ZnO和Al2O3,三组分在催化剂中的比例随着生产厂家的不同而不同。
一般来说, CuO的质量分数在40% ~80%, ZnO的质量分数在10% ~30%, Al2O3的质量分数在5% ~10%。
铜基催化剂在合成甲醇时, CuO、ZnO、Al2O3三组分的作用各不相同。
CO和H2在催化剂上的吸附性质与催化剂的活性有非常密切的关系。
在铜基催化剂表面对CO的吸附速率很高,而H2的吸附则比CO 慢得多。
ZnO是很好的氢化剂,可使H2被吸附和活化, 但对CO几乎没有化学吸附,因此可提高铜基催化剂的转化率。
纯铜对甲醇合成是没有活性的,H2和CO合成甲醇的反应是在一系列活性中心上进行的,而这种活性中心存在于被还原的Cu-CuO界面上。
在催化剂中加入少量 Al2O3的首要功能就是阻止一部分氧化铜还原。
当催化剂被还原后,开始进行反应时,合成气中的H2 和CO都是还原剂,有使氧化铜进一步还原的趋势。
这种过度的还原,使得活性中心存在的界面越来越小,催化剂活性也越来越低。
从合成的整个过程来看,随着还原表面向催化剂的内层深入,未还原的核心越来越小,作为被还原的Cu-CuO界面的核心表面积也越来越小,催化剂的活性降低,合成反应速率随之降低。
研究认为,Al2O3在催化剂中作为结构助剂起阻碍铜颗粒烧结的作用, CuO/ZnO/Al2O3催化剂的活性远高于双功能催化剂CuO/ZnO的活性。
q7 h- G8 n9 ]$ B5 m- Q: ?& ]/ D2 铜基催化剂助剂6 j8 } x5 L! ?0 V1 l1 K4 H$ Q! m% g\5 K8 e) C+ g5 A)E! ~ 铜基催化剂助剂的研究是甲醇合成催化剂研究的一个重要课题。
铜基催化剂耐热强度较低,使用时间过长或操作温度过高都会造成铜的晶体长大使催化剂失去活性。
其热稳定性差,很容易发生硫、氯中毒,使用寿命短等缺点,一般通过加入其他助剂得以改善,由此形成具有工业价值的新一代铜基催化剂。
$ P3 d }9 z x* |/ t2 bf, Z6 f)K& R2 y( U q: b1 B)t3 @ 锌就是铜基催化剂的最好助剂,很少量的锌就能使铜基催化剂的活性提高。
加入Al2O3,可以使催化剂铜晶体尺寸减小,活性提高。
若在CuO ZnO/Al2O3催化剂中再加入Cr,则会表现出良好的助催化作用。
在催化剂组成中增添硼、铬、锰、钒及稀土元素等,对合成甲醇具有显著的促进作用。
据报道,在铜基催化剂的基础上添加钒、锆等,可以提高合成甲醇的催化活性及催化剂的耐热性能。
、 k* {7 a% M V3 铜基催化剂的失活 % v+ F, O2 ~ R8 Q8 催化剂的烧结和热失活是指由高温引起的催化剂结构和性能的变化。
高温除了引起催化剂的烧结外,还会引起催化剂化学组成和相组成的变化5 a8 _5 K4 r#[2 S- M)o, |" o; J5 K$ R, h( T% v+ h l 虽然CuO/ZnO/Al2O3铜基甲醇合成催化剂活性好、选择性高,但由于甲醇合成反应的放热量大容易造成铜基催化剂失活,使催化剂的使用寿命缩短,因此如何提高铜基催化剂的热稳定性、延长其使用寿命成为人关注的问题。
2 p+ W/ L& \, c& C: i! h/ Y- g, f F, T0 ?* t v3、2 中毒失活 :[! f2 f- h" i# s1 b H$ M9 N+ H)p1 t9 s1 u 由于某些有害杂质的影响而使催化剂活性下降称为催化剂中毒,这些物质称为毒物。
毒物一般来自进料中的杂质。
J9 ~9 e 通过研究铜基催化剂的失活原因及再生方法, 发现失活催化剂中有硫、镍和积炭存在,表面出现铜粒长大现象,且毒物完全破坏了催化剂原有的表面结构。
在目前的工艺中,导致甲醇合成催化剂中毒失活的因素主要集中在以下几个方面: 硫及硫的化合物;2)氯及氯的化合物;3)羰基金属等金属毒物;4)氨;5)油污。
其中,硫是最常见的毒物,也是引起催化剂活性衰退的主要因素,它决定了铜基催化剂的活性和使用寿命。
3、3 羰基金属对甲醇催化剂的毒害研究进展工业上使用的许多催化剂对羰基化合物分敏感,百万分之几的羰基化合物就可导致催化剂中毒而失活。
在采用渣油、煤、焦炭为原料制合成气过程中,常因含羰基铁、羰基镍导致后续工序,如甲醇合成、丁辛醇合成、氨合成等生产过程中的催化剂产生不可逆中毒,不仅缩短了催化剂的使用寿命,而且还引起一些副反应,在很大程度上影响了装置的长周期运行。
众所周知,催化剂的表面性质不是均一的,其表面不具有同一的催化活性与吸附特性,而是由一系列活性中心形成。
活性中心不是杂乱地散布在催化剂表面,而是具有一定的规律与催化剂相适应。
这些活性中心一旦遭到破坏,催化剂便丧失活性或引起其他副反应。
催化剂的中毒,普遍认为是催化剂毒素在催化剂表面生成薄膜使表面丧失活性。
但在很多情况下,使催化剂中毒的毒素剂量非常少,它们甚至不可能生成一个单分子层,而这种毒素被牢固地吸附在活性中心上,使催化剂丧失活性或引起其他副反应。
Fe(CO)5和Ni(CO)4在低于反应器温度下生成,又在反应器温度下分解而沉积在催化剂表面。
这一分解反应很可能是由催化剂自身所催化,逐步被催化剂表面所吸附,堵塞催化剂的表面和孔隙,使催化剂活性下降。
由于反应生成热不能及时带走,又使催化剂床层温度升高,从而影响了催化剂的工业使用寿命。
羰基铁、羰基镍对甲醇催化剂活性的影响,证明催化剂的活性衰退正比于催化剂上毒物的沉积量。
同时,由于铁和镍是费托反应的活性组分,羰基铁、镍的存在,还可引起许多副反应,如生产烃类和石蜡烃等反应,给分离工序增加了困难。
RK-05低压甲醇催化剂使用说明书一、用途及特点RK-05甲醇催化剂适用于以煤造气、焦炉气、天然气、乙炔尾气、石油(重油、渣油、轻油等)为原料的低压甲醇生产。
具有低温活性好、转化率高、稳定性好、选择性高、耐毒能力强、寿命长等特点。
二、催化剂组成和物理性质1.催化剂组成主要由铜、锌、铝的氧化物所组成其中氧化铜:52~58% 氧化锌:22~27% 氧化铝:6~9%2.催化剂物理性质外观:有黑色金属光泽的圆柱体外形尺寸:Ф5(4、5~5、5)㎜或Ф64㎜(可根据用户要求提供其它尺寸的片剂)堆密度:1、250、05 kg/L 径向抗压碎强度: ≥250 N/cm 比表面积:100 m2/g~110 m2/g 还原后体积收缩率:≤6、0%三、合成甲醇基本反应合成甲醇的基本反应为:CO +2H2 = CH3OH +90、7 KJ CO2 +3H2 = CH3OH + H20 +49、5 KJ合成甲醇反应过程中,通常伴随有副反应发生,副产物主要有醛、酮、醚、烯烃、烷烃(石蜡)、杂醇、高聚物等,副产物含量主要取决于催化剂杂质含量、选择性、使用周期、以及工艺操作条件等。
四、催化剂使用特性及要求1、催化剂使用前须先经过还原活化后才具有活性,合适的还原活化过程是获得高活性催化剂的关键。
2、还原活化后的催化剂暴露在空气中会迅速燃烧,因此在使用中或停车检修时应防止空气渗入,卸触媒前要经过钝化、降温。
3、合成气中的硫、氯、铁或镍的羰基物、不饱和烃、油类等都能使催化剂中毒,导致催化剂丧失活性、缩短寿命、降低选择性。
因此,要求合成新鲜气中杂质应按要求脱除后才能进入甲醇合成系统。
4.催化剂使用条件:正常使用温度:190℃~300℃ 最佳使用温度:205℃~280℃工作压力:3~15MPa 操作空速:4000 h-1~20000h-15.原料气杂质含量要求:总硫≤0、1ppm 氯≤0、01ppm 氨≤10pm 氧≤0、2% 无重金属不饱和烃、油污等:微量五、正常操作及使用条件1、使用温度范围(1)RK-05甲醇催化剂使用温度是185℃~280℃,最佳使用温度是205℃~280℃。
在满足设计产量的前提下,尽量维持催化剂床层在较低温度下操作,有利于延长催化剂的使用寿命。
(2)高温、高压会加速副反应的进行,降低甲醇的质量,主要的副产物有醇、醚、酯和高碳烷烃等有机物。
(3)操作温度大幅度地波动会造成床层局部过热,高温操作会加速催化剂晶粒增长、比表面积减少,从而加速催化剂的“老化”。
(4)超温会给甲醇催化剂造成严重的危害,增加催化剂床层阻力,副产物增多,影响催化剂使用寿命。
2、操作压力RK-05型催化剂可用于3MPa~15MPa操作。
甲醇合成是一个体积缩小的反应,加压对甲醇合成反应有利,提高压力,时空产率显著增大。
3、操作空速一般使用空速4000 h-1~20000h-1。
提高空速,可增加甲醇时空产率,减少副产物的生成。
4、原料气中有害杂质对催化剂的影响:4、1 硫的影响:合成气中H2S、CS2、COS等硫化物很容易与催化剂中ZnO、Cu 作用,从而使催化剂失活。
ZnO + H2S = ZnS + H2O2Cu + H2S = Cu2S + H24、2 油的影响:新鲜气和循环气经过压缩机和循环机时,会带部分机油进入合成塔,使催化剂被污染,机油在催化剂上沉积将堵塞催化剂孔隙和阻碍气体接触催化剂表面,同时油中还可能含有硫等其它杂质,会使催化剂中毒,因此气体进入合成塔前必须进行有效的油水分离。
4、3 烯、炔烃类及氯化物也会造成对催化剂严重的危害,尤其是氯化物危害性比硫化物还要严重,要严格控制。
4、4 氨的影响:原料气中含氨对催化剂的活性、寿命及其产品质量有一定影响,如:甲醇中的鱼腥味,就是合成甲醇时生产了二甲胺、三甲胺等副反应产物所致,同时氨与触媒中的铜会发生络合反应,络合物溶于水后呈蓝色,因此原料气中氨含量长时间超标会使触媒中活性成分逐渐减少,影响触媒活性和使用寿命。
六、停车1.催化剂的钝化需要更换催化剂时,在卸出催化剂之前,必须对催化剂进行钝化,防止催化剂与大气接触时剧烈氧化。
卸出催化剂前按正常停车程序将系统降至常压,温度降至≤60℃,继续开循环压缩机,用N2气置换系统合格后,维持系统~0、5MPa压力下,慢慢导入空气,按下表程序进行钝化。
在钝化过程中应严防温升过快,若温升过快,必须降低或切断导入的空气量。
催化剂钝化程序表(供参考)反应器出口温度,℃≤100反应器进口氧含量,10-2≤0、51251021(全部空气)需要时间*,h3771053*注:根据不同情况钝化时间可作适当调整。
2、卸催化剂催化剂钝化完毕,打开反应器底部卸料口,放出催化剂。
顶部人孔保持密封,防止反应器大量吸入空气。