浅析如何提高转炉钢水纯净度(2月份)
提高转炉炉次数的方法

提高转炉炉次数的方法
提高转炉炉次数的方法主要有以下几个方面:
1.控制入炉原料的质量,如含硫量、含磷量和含碳量等,保证其符合工艺要求。
2.优化转炉冶炼工艺,如装入制度、供氧制度、炉渣控制制度等,以提高金属收得率和降低渣中带铁损失。
3.提高设备维护水平,如定期检查设备状态、及时更换易损件等,确保设备运行稳定可靠。
4.加强生产管理,如制定科学合理的生产计划、提高操作人员的技能水平等,以实现高效稳定的生产。
5.采用先进的监测技术,如炉气分析、副枪监测等,实时监控炉内反应情况并进行相应的调整。
6.探索新的工艺技术,如溅渣护炉、废钢预热等,以降低能源消耗和提高冶炼效率。
7.开发高炉龄转炉,延长转炉使用寿命,降低单位产量的设备折旧费用。
综上所述,提高转炉炉次数需要从多个方面入手,包括原料控制、工艺优化、设备维护、生产管理、监测技术、工艺技术和高炉龄转炉等方面。
转炉炼钢工艺分析

转炉炼钢工艺分析简介转炉炼钢是一种重要的钢铁生产工艺。
它采用转炉作为熔炼设备,通过氧化钢水的方式去除杂质,从而获得高纯度的钢水。
工艺流程转炉炼钢的工艺流程一般包括以下几个步骤:1.亚稳态钢水倒入转炉中,同时注入氧气;2.氧气与铁水反应生成氧化物,从而去除杂质;3.在适当的条件下加入渣剂,将浮渣与钢水分离;4.投入合适的合金和调节剂,调节钢水的成分和性质;5.倒出钢水至铸铁机或连铸机中,制成钢材。
工艺优势相对于其他炼钢工艺,转炉炼钢具有以下优势:1.钢水纯度高,化学成分稳定,可以得到各种不同技术要求的钢材;2.工艺流程简单,可自动化控制,生产效率高;3.单次生产能力大,适用于大批量生产。
工艺不足然而,转炉炼钢也存在一些问题,主要包括:1.熔炼过程中,由于氧化反应的过程比较复杂,会产生大量的烟尘和废气污染;2.熔炼后再行铸造需要添加铝、钛等金属,也会对环境造成一定的污染。
工艺改进针对转炉炼钢存在的问题,研究人员进行了多方面的工艺改进研究。
主要包括以下几个方面:1.减少污染:采用高热效应烟气脱硫技术和洗涤重金属离子等方法,减少烟尘、废水排放,改善环境;2.提高产能:对炉况和操作条件进行优化调整,提高单次生产能力;3.提高效益:加入合适的合金和调节剂,调节钢水的成分,生产高附加值、高品质的钢材。
市场应用目前,转炉炼钢工艺已经在全球范围内广泛应用。
根据统计数据,仅中国一国的转炉炼钢产量就占全球的60%以上。
随着技术的不断进步,转炉炼钢工艺在钢铁生产中的地位将更加重要。
结论综上所述,转炉炼钢是一种重要的钢铁生产工艺,具有钢水纯度高、生产效率高等诸多优点。
但其存在烟尘、废气污染等问题。
通过改善工艺和技术手段的引入,可以实现减少污染、提高产能和效益的目标。
这一工艺在全球范围内得到广泛应用,将在未来发展中继续发挥重要作用。
提高钢水质量的工艺优化实践
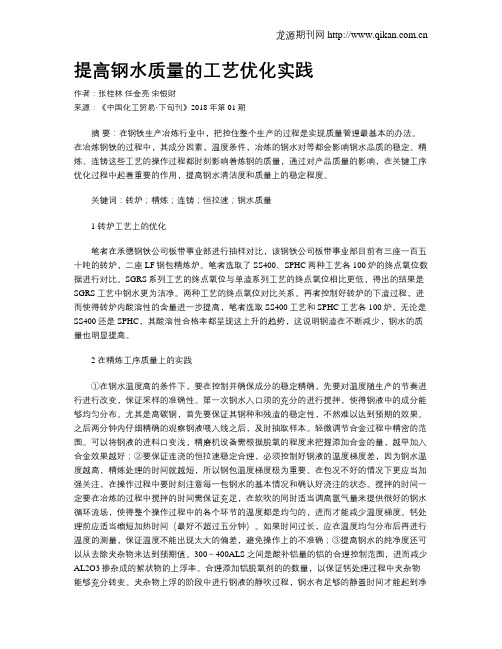
提高钢水质量的工艺优化实践作者:张桂林任金亮宋银财来源:《中国化工贸易·下旬刊》2018年第01期摘要:在钢铁生产冶炼行业中,把控住整个生产的过程是实现质量管理最基本的办法。
在冶炼钢铁的过程中,其成分因素,温度条件,冶炼的钢水对等都会影响钢水品质的稳定。
精炼、连铸这些工艺的操作过程都时刻影响着炼钢的质量,通过对产品质量的影响,在关键工序优化过程中起着重要的作用,提高钢水清洁度和质量上的稳定程度。
关键词:转炉;精炼;连铸;恒拉速;钢水质量1 转炉工艺上的优化笔者在承德钢铁公司板带事业部进行抽样对比,该钢铁公司板带事业部目前有三座一百五十吨的转炉,二座LF钢包精炼炉。
笔者选取了SS400、SPHC两种工艺各100炉的终点氧位数据进行对比。
SGRS系列工艺的终点氧位与单渣系列工艺的终点氧位相比更低,得出的结果是SGRS工艺中钢水更为洁净。
两种工艺的终点氧位对比关系。
再者控制好转炉的下渣过程,进而使得转炉内酸溶性的含量进一步提高,笔者选取SS400工艺和SPHC工艺各100炉,无论是SS400还是SPHC,其酸溶性合格率都呈现这上升的趋势,这说明钢渣在不断减少,钢水的质量也明显提高。
2 在精炼工序质量上的实践①在钢水温度高的条件下,要在控制并确保成分的稳定精确,先要对温度随生产的节奏进行进行改变,保证采样的准确性。
第一次钢水入口须的充分的进行搅拌,使得钢液中的成分能够均匀分布。
尤其是高碳钢,首先要保证其钢种和残渣的稳定性,不然难以达到预期的效果。
之后两分钟内仔细精确的观察钢液喂入线之后,及时抽取样本。
轻微调节合金过程中精密的范围。
可以将钢液的进料口变浅,精磨机设备需根据脱氧的程度来把握添加合金的量,越早加入合金效果越好;②要保证连浇的恒拉速稳定合理,必须控制好钢液的温度梯度差,因为钢水温度越高,精炼处理的时间就越短,所以钢包温度梯度极为重要。
在包况不好的情况下更应当加强关注,在操作过程中要时刻注意每一包钢水的基本情况和确认好浇注的状态。
浅析转炉煤气回收的影响因素及提高措施
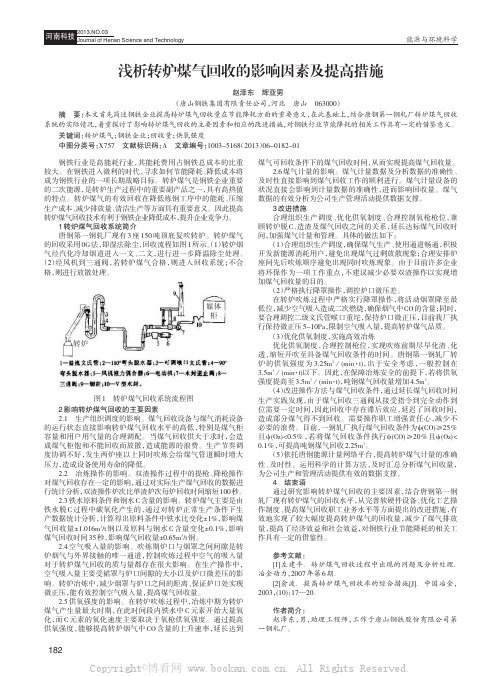
钢铁行业是高能耗行业,其能耗费用占钢铁总成本的比重较大。
在钢铁进入微利的时代,寻求如何节能降耗、降低成本将成为钢铁行业的一项长期战略目标。
转炉煤气是钢铁企业重要的二次能源,是转炉生产过程中的重要副产品之一,具有高热值的特点。
转炉煤气的有效回收在降低炼钢工序中的能耗、压缩生产成本、减少排放量、清洁生产等方面具有重要意义。
因此提高转炉煤气回收技术有利于钢铁企业降低成本,提升企业竞争力。
1转炉煤气回收系统简介唐钢第一钢轧厂现有3座150吨顶底复吹转炉。
转炉煤气的回收采用0G法,即湿法除尘,回收流程如图1所示。
(1)转炉烟气经汽化冷却烟道进入一文、二文,进行进一步降温除尘处理。
(2)经风机到三通阀,若转炉煤气合格,则进入回收系统;不合格,则进行放散处理。
2影响转炉煤气回收的主要因素2.1生产组织调度的影响。
煤气回收设备与煤气消耗设备的运行状态直接影响转炉煤气回收水平的高低,特别是煤气柜容量和用户用气量的合理调配。
当煤气回收供大于求时,会造成煤气柜饱和不能回收而放散,造成能源的浪费。
生产节奏调度协调不好,发生两炉座以上同时吹炼会给煤气管道瞬时增大压力,造成设备使用寿命的降低。
2.2冶炼操作的影响。
双渣操作过程中的提枪、降枪操作对煤气回收存在一定的影响,通过对实际生产煤气回收的数据进行统计分析,双渣操作炉次比单渣炉次每炉回收时间缩短100秒。
2.3铁水原料条件和钢水C含量的影响。
转炉煤气主要是由铁水脱C过程中碳氧化产生的,通过对转炉正常生产条件下生产数据统计分析,计算得出原料条件中铁水比变化±1%,影响煤气回收量±1.016m3/t钢以及原料与钢水C含量变化±0.1%,影响煤气回收时间35秒,影响煤气回收量±0.65m3/t钢。
2.4空气吸入量的影响。
吹炼期炉口与烟罩之间间隙是转炉烟气与外界接触的唯一通道,控制吹炼过程中空气的吸入量对于转炉煤气回收的质与量都存在很大影响。
改善钢水洁净度,提高轧材内在质量

cleanliness,thusimpmvesthe舛删∞d up in Aught,1996 T‰t幽nd。盯is印曲。d for the production。f IF steal,pend咖pirdine,automobile beam
WLSl0,hotsehdd gastankHF295,whichgreatlyimproves steal
3.1.2控制钢水增碳技术
控制真空精炼后钢水增碳技术主要措施是:采
改善钢水洁净度,提高轧材内在质量
31
用无碳或低碳大包、中包耐火材料和覆盖剂以及超 低碳结晶器保护渣来控制真空精炼后钢水增碳。
通过以上技术,我厂对[c]的控制水平大大提 高,以IF钢为例,2001年生产的汽车板用IF钢的 [C]可控制在(10~35)×10 4%,平均为24.7× 10。%。历年来IF钢的[C]含量的降低见图3。
闻寄霎笔军三篓智‘鬟銮::翌望詈璺婪誓冀篓望
国家重点工程项目,是继宝钢投产之后我国建设的 又一个具有国际先进承乎蛹大型转炉垒连镑钢厂。 全部工程分力鞭期建设:第一期海转炉二吹~期一 台板坯连铸,设诗能力为年产180万t连铸坯;第二 期为转炉二吹一阍时新增一台板鳋连铸梳,设计能
力为年产250万t连铸坯。合嗣予1992年2胄丧 西斑牙骂德量签订,当年t l旁生效。武钢三炼钢经 过45个月的建设(眈台掏规定提前三个片)。于
aimed at producing high'tech and high vahe-added pr。du∞,developed successfully the tec}mdk画荡of d既矿decarbollizillg,
Nitrogen contr01.totaloxygen control,deep-desulphurizing and Calcium trtmtrnent,to improvepteel cleanliness since st&Tt—
浅谈纯净钢生产技术
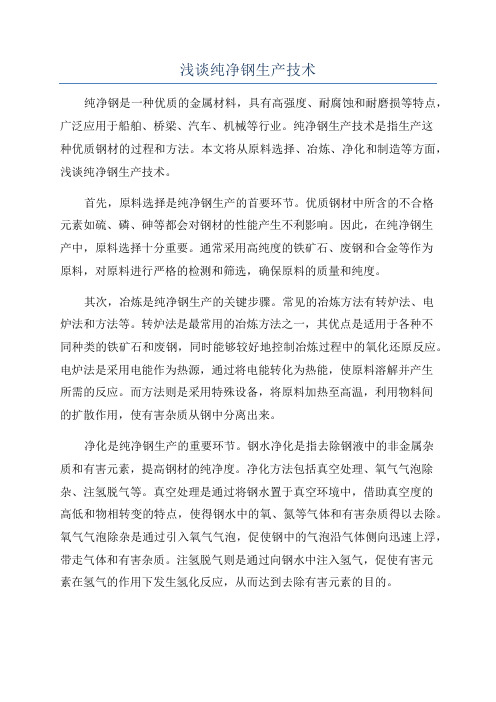
浅谈纯净钢生产技术纯净钢是一种优质的金属材料,具有高强度、耐腐蚀和耐磨损等特点,广泛应用于船舶、桥梁、汽车、机械等行业。
纯净钢生产技术是指生产这种优质钢材的过程和方法。
本文将从原料选择、冶炼、净化和制造等方面,浅谈纯净钢生产技术。
首先,原料选择是纯净钢生产的首要环节。
优质钢材中所含的不合格元素如硫、磷、砷等都会对钢材的性能产生不利影响。
因此,在纯净钢生产中,原料选择十分重要。
通常采用高纯度的铁矿石、废钢和合金等作为原料,对原料进行严格的检测和筛选,确保原料的质量和纯度。
其次,冶炼是纯净钢生产的关键步骤。
常见的冶炼方法有转炉法、电炉法和方法等。
转炉法是最常用的冶炼方法之一,其优点是适用于各种不同种类的铁矿石和废钢,同时能够较好地控制冶炼过程中的氧化还原反应。
电炉法是采用电能作为热源,通过将电能转化为热能,使原料溶解并产生所需的反应。
而方法则是采用特殊设备,将原料加热至高温,利用物料间的扩散作用,使有害杂质从钢中分离出来。
净化是纯净钢生产的重要环节。
钢水净化是指去除钢液中的非金属杂质和有害元素,提高钢材的纯净度。
净化方法包括真空处理、氧气气泡除杂、注氢脱气等。
真空处理是通过将钢水置于真空环境中,借助真空度的高低和物相转变的特点,使得钢水中的氧、氮等气体和有害杂质得以去除。
氧气气泡除杂是通过引入氧气气泡,促使钢中的气泡沿气体侧向迅速上浮,带走气体和有害杂质。
注氢脱气则是通过向钢水中注入氢气,促使有害元素在氢气的作用下发生氢化反应,从而达到去除有害元素的目的。
最后,制造是纯净钢生产的最后一步。
制造过程中,主要包括热处理、轧制和加工。
热处理是将钢材加热至一定温度,然后通过快速冷却的方法,使钢材获得理想的力学性能。
轧制是将钢坯通过轧机进行塑性变形,使得钢材在尺寸和形状上得到满足需求的改变。
加工是将轧制后的钢材进行切割、焊接、打孔等工艺,制成最终的产品。
综上所述,纯净钢生产技术是一个复杂而严谨的过程。
原料选择、冶炼、净化和制造都是非常重要的环节,需要严格按照标准进行操作。
3号转炉炉修期间钢水洁净度分析
\ /
\
\
|
. ・
图 1 两种铁 水条件 下钢 包渣 中( e FO)+( O) 量 对 比情 况 Mn 含
《捌如1壬举 I 车 《删缸1壬 | 举 I
4 中包钢 水 0与 N含量对 比
N含量情况 , 炉修期 问不 添加梅精 矿时生产 A钢种 时[ ] [ ] 0 和 N 的控制水平均稍有欠缺 , 见图 23 、。
的梅 精 矿 , 3号转 炉 炉 修 期 问烧 结 生 产 则停 加 在
梅精矿 , 铁水中 P含量减少 ,i s 含量也有所 降低 ,
具体 铁水 成分 见 表 1 。
表 1 添 加 与不添 加梅精 矿 的 铁水 成分 比较
元 素 不 添 加 梅 精 矿 C 42 .6 S i 0 3 .2 Mn P
和 s 含量 相差 较多 , i 两种铁 水 条件 下 转 炉 吹氧 时 间相差 不多 , 这是 不 添 加梅 精 矿 条 件下 渣 的氧 化
不添加 梅精 矿 的铁 水来 冶炼 的钢 水 洁净度进 行 了分 析 , 为今后 梅钢 的炼钢 生产提 供 了借 鉴 。 关 键词 : 山铁 精矿 ; 梅 炼钢 ; 洁净度
An l ss o o t n S e lC e n i e sd rn . n e t r M a n e a c a y i n M l t e l a l s u i g No 3 Co v r e i t n n e e n
为: 铁水 预脱 硫一 炉冶炼 一 钢包 吹氩一 连 铸 。 转 +
1 入炉 铁水 情 况 2 1 年 度 梅 钢烧 结 生 产 一般 配 加2) 00 ( %左 右
2 转炉 生产 情况 冶 炼时入 炉铁 水 为 10t不 添加 梅 精矿 与采 5 ,
210转炉厂生产SPHE钢头坯纯净度的研究
(p pm)
碳 达到要 求后 , 加铝 脱氧并 合金 化 , 后加 人 然
金 属锰 和 钛 铁 。 R 纯 处 理 时 间 控 制 在 3 H 5 分 钟 以 内 。 出站 后 进 入 连 铸 工 艺 。 表 1为 R 出站时 S H H P E钢 水 的成分 。
表1 R H出站 时 S H P E钢水 的成分 ( ) %
C s i № P S Al t T i bb N i ≤ .  ̄ .1 01 n2 0( m 005 . 2 5≤n0 002 1 .】 n锄 . . n0 5≤ 0∞0 勋 n∞D一≤ 0 n05
包 裹在 外 。
表 5 SH P E钢 头 坯 在 宽 度 14处 不 同 /
浇 铸 长 度 大 样 分 析 结 果
距部 头
一
r m /0 g < 0t 0 Gt > 0 tn a g g 1k 5 t 5 1 p 10t m  ̄1 t O m Om 0 ̄ p e 2 .1 13 1 0
6 .
3 0 以后 , .m 边缘 显微 夹 杂物数 量 维持 在 5 7 .0 个 ・ m。以下 ; 坯 宽度 I4处 显 微 夹 杂物 m 头 / 数量波 动下降 , 在浇铸 长 度 大于 3 5 14处 . m,/
显微夹 杂物数量稳定 在 7~ 8个 ・nl r ~。 n
在 不 同浇铸 阶段 显微 夹 杂 物 种类 基 本 一 致 , 其 中大 部 分 为 不规 则 形 状 的 A: ,还 有 部 1O ,
制缺 陷 , 头坯通 常被 改判或 直接判 废 , 影响 了
涟钢 的生 产效 益 和 产 能 的发 挥 , 而所 产 生 的 废钢 量也是 巨大 的 , 导致 了极 大 的能源 和原 材料 的浪 费 。因 此 , 过 研 究 连 铸过 程 中 头 通
- 1、下载文档前请自行甄别文档内容的完整性,平台不提供额外的编辑、内容补充、找答案等附加服务。
- 2、"仅部分预览"的文档,不可在线预览部分如存在完整性等问题,可反馈申请退款(可完整预览的文档不适用该条件!)。
- 3、如文档侵犯您的权益,请联系客服反馈,我们会尽快为您处理(人工客服工作时间:9:00-18:30)。
浅析如何提高转炉钢水纯净度
炼钢过程枪位的控制
(2月份小结)
前言
1、氧枪
氧枪由喷头(枪头)、枪身(枪体)和枪尾组成。转炉吹炼时,喷头必须保证氧气流股对熔
池具有一定的冲击力和冲击面,使熔池中的各种反应快速而顺利的进行。
2、枪位对炼钢的重要性
在转炉炼钢整个炉役中,随着炼钢炉次的增加,炉衬由于受到侵蚀不断变薄,炉容不断增大。
因此,要求当班生产前需对熔钢液面进行测定,根据装入制度(定深装入或定量装入)及测定
结果确定氧枪高度,而在两次测定期间,液面高度保持不变。
氧枪系统
我厂氧枪采用五孔拉瓦尔型枪头,马赫数为2.0,氧枪实际最大氧气流量位500m3/min,设
计工作氧压0.8~0.9MPa,氧气扩张角度为13.45°,喉口直径38.4mm。枪体采用高压循环
水冷却,设计流量为200~240m³/h,
枪位控制
目前,转炉炼钢氧枪枪位一般是根据吹炼状况分段设定的,在本文中,根据转炉炼钢的不同
阶段采用不同的控制策略。在吹炼初期和中期,由于分批加入造渣材料和助熔剂,因此采用
模糊控制调节枪位。而在吹炼末期,则采用较低的固定枪位进行吹炼,以利于石灰进一步渣
化,使脱碳反应按扩散进行,渣钢反应趋于平衡,炉内钢水成分和温度得以均匀。
因本厂采用留渣操作模式,在整个冶炼过程,氧枪采用低—高—低模式冶炼。
在开吹点火阶段采用氧枪相对高度1.5m点火;
点火成功后枪位设置在1.6m,直至第一批辅料的加入;
加入第一批辅料后枪位设置在1.5m,渣子起来后,压枪至1.4m,氧流量设置为25000m3/h;
在冶炼中前期适当的提高枪位至1.55m,根据炉内碳氧反应情况适当调整枪位;
冶炼中期,在保证不喷溅的前提下,适当提高枪位防止炉渣的“返干”;
后期,枪位压低至1.4m,增大氧流量,进行拉碳升温。
小结
在转炉炼钢过程中,氧枪是必不可少的设备,氧枪的枪位直接关系到脱碳、升温及冶炼过程
的平稳进行,适应了炉衬变薄及炼钢原料化学成分波动带来的不利影响,减少喷溅的发生,
使氧枪枪位在整个冶炼期间始终处于最优位置。