储罐底板漏磁检测综述.
储油罐底板无损检测技术
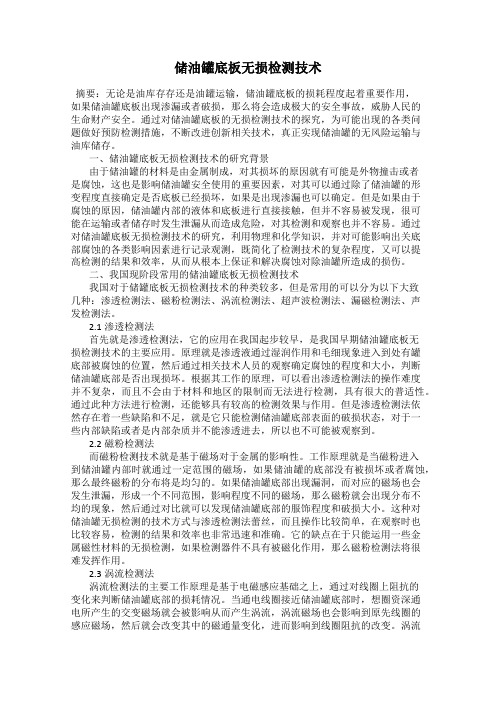
储油罐底板无损检测技术摘要:无论是油库存存还是油罐运输,储油罐底板的损耗程度起着重要作用,如果储油罐底板出现渗漏或者破损,那么将会造成极大的安全事故,威胁人民的生命财产安全。
通过对储油罐底板的无损检测技术的探究,为可能出现的各类问题做好预防检测措施,不断改进创新相关技术,真正实现储油罐的无风险运输与油库储存。
一、储油罐底板无损检测技术的研究背景由于储油罐的材料是由金属制成,对其损坏的原因就有可能是外物撞击或者是腐蚀,这也是影响储油罐安全使用的重要因素,对其可以通过除了储油罐的形变程度直接确定是否底板已经损坏,如果是出现渗漏也可以确定。
但是如果由于腐蚀的原因,储油罐内部的液体和底板进行直接接触,但并不容易被发现,很可能在运输或者储存时发生泄漏从而造成危险,对其检测和观察也并不容易。
通过对储油罐底板无损检测技术的研究,利用物理和化学知识,并对可能影响出关底部腐蚀的各类影响因素进行记录观测,既简化了检测技术的复杂程度,又可以提高检测的结果和效率,从而从根本上保证和解决腐蚀对除油罐所造成的损伤。
二、我国现阶段常用的储油罐底板无损检测技术我国对于储罐底板无损检测技术的种类较多,但是常用的可以分为以下大致几种:渗透检测法、磁粉检测法、涡流检测法、超声波检测法、漏磁检测法、声发检测法。
2.1渗透检测法首先就是渗透检测法,它的应用在我国起步较早,是我国早期储油罐底板无损检测技术的主要应用。
原理就是渗透液通过湿润作用和毛细现象进入到处有罐底部被腐蚀的位置,然后通过相关技术人员的观察确定腐蚀的程度和大小,判断储油罐底部是否出现损坏。
根据其工作的原理,可以看出渗透检测法的操作难度并不复杂,而且不会由于材料和地区的限制而无法进行检测,具有很大的普适性。
通过此种方法进行检测,还能够具有较高的检测效果与作用。
但是渗透检测法依然存在着一些缺陷和不足,就是它只能检测储油罐底部表面的破损状态,对于一些内部缺陷或者是内部杂质并不能渗透进去,所以也不可能被观察到。
储罐底板的漏磁检测信号处理中小波奇异性检测理论的应用
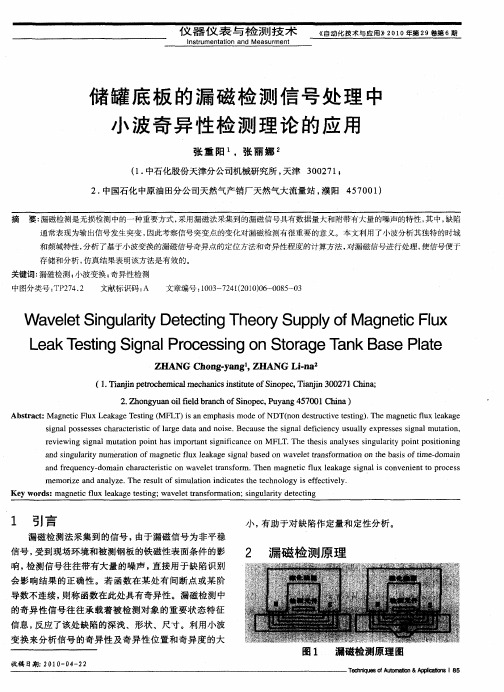
和频域特性 , 分析 了基于小波变换的漏磁信号奇异点的定位方法和奇异性程度 的计算方法 , 对漏磁 信号进 行处理 , 使信号便于 存储和分 析 , 仿真结果表明该方法是有效的 。
关键词 : 漏磁检测 ; 波变 换 ; 异性检测 小 奇
中图分类号 : 2 4 2 TP 7 .
文献标识码 : A
仪 器 仪 表 与检 测 技 术
n tumen a i n an e s e t sr t to d M a ur n m
自 化 术 应 》0 年 9 第 期 动 技 与 用 21 第2卷 6 0
储 罐 底 板 的 漏 磁 检 测 信 号 处 理 中
小 波 奇 异 性检 测 理 论 的 应 用
sg a os e s sc a a t rsi f lr e d t n o s . c u e t e sg a e i i n y u u l xp e s s sg a t to , in l p s s e h r c e i t o g a a a d n i e Be a s h i n l fc e c s a l e r s e i n lmu a i n c a d y
1 引 言
漏磁 检 测法采 集到 的信号 , 由于 漏磁 信号 为非 平稳 信号 , 到现场环 境和被 测钢 板 的铁 磁性 表面条 件 的影 受 响 , 测信 号往往 带有 大量 的 噪声 , 接用 于缺 陷识 别 检 直 会 影响结 果 的正 确性 。若 函数在 某 处有 间断 点或 某 阶
张 重 阳 .张 丽 娜
(. 1 中石化股份天津分 公司机械研究所 , 天津 3 0 7 ; 0 2 l
2. 中国石化 中原油 田分公 司天然气产销厂 天然气大流量 站 , 阳 4 7 0 ) 濮 5 0 1
钢质储罐底板无损检测技术
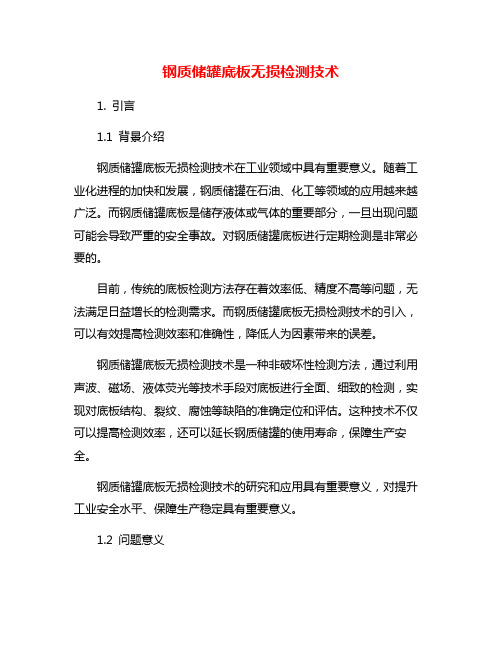
钢质储罐底板无损检测技术1. 引言1.1 背景介绍钢质储罐底板无损检测技术在工业领域中具有重要意义。
随着工业化进程的加快和发展,钢质储罐在石油、化工等领域的应用越来越广泛。
而钢质储罐底板是储存液体或气体的重要部分,一旦出现问题可能会导致严重的安全事故。
对钢质储罐底板进行定期检测是非常必要的。
目前,传统的底板检测方法存在着效率低、精度不高等问题,无法满足日益增长的检测需求。
而钢质储罐底板无损检测技术的引入,可以有效提高检测效率和准确性,降低人为因素带来的误差。
钢质储罐底板无损检测技术是一种非破坏性检测方法,通过利用声波、磁场、液体荧光等技术手段对底板进行全面、细致的检测,实现对底板结构、裂纹、腐蚀等缺陷的准确定位和评估。
这种技术不仅可以提高检测效率,还可以延长钢质储罐的使用寿命,保障生产安全。
钢质储罐底板无损检测技术的研究和应用具有重要意义,对提升工业安全水平、保障生产稳定具有重要意义。
1.2 问题意义钢质储罐底板无损检测技术对于保障储罐安全运行具有重要意义。
由于储罐长期承受介质的腐蚀和应力作用,底板可能存在各种缺陷和隐患,如裂纹、气泡、腐蚀等。
这些问题如果不及时发现和修复,可能会导致底板失效,引发泄漏事故,造成严重的环境污染和人身伤害。
开展钢质储罐底板无损检测具有重要的现实意义和实用价值。
钢质储罐底板无损检测技术可以帮助运营企业及时了解储罐底部情况,评估其安全性能,制定有效的检修计划,确保储罐的安全运行。
通过有效的无损检测技术,可以提高底板检测的准确性和效率,降低检测成本,减少人为因素对检测结果的影响,为储罐的安全管理提供有力支持。
钢质储罐底板无损检测技术的研究和应用具有重要的实践意义和理论价值。
通过深入研究和探讨该技术,可以不断提升其检测效率和准确性,为储罐行业的发展和安全提供更加可靠的保障。
【内容达到200字】1.3 研究目的研究目的是为了深入了解钢质储罐底板无损检测技术的应用和发展,探讨其在工程领域中的重要性和实用性。
石化系统常压储罐底板腐蚀失效与漏磁检测

石化系统常压储罐底板腐蚀失效与漏磁检测作者:李佳林来源:《中国石油和化工标准与质量》2013年第06期【摘要】常压储罐底板腐蚀失效是石化系统安全管理工作中不容忽视的安全隐患。
本文重点介绍了储罐底板漏磁检测技术的现场应用案例,通过案例分析总结了石化系统储罐底板腐蚀失效的原因,证实了漏磁检测技术的可靠性及优越性,说明了漏磁检测技术对石化系统常压储罐底板腐蚀检测工作的指导意义。
【关键词】储油罐底板腐蚀失效漏磁检测1 前言随着石油化工工业的迅速发展,各石油化工企业已建造了很多大型储油罐。
目前,仅克拉玛依石化公司就拥有各类储罐近600台,总罐容近150万m3,盛装介质包括原油、成品油、含油污水等化工原料,储罐的安全对炼油装置的长、稳、安、满、优生产起着巨大的保证作用,一旦发生腐蚀损坏,不但造成经济上的直接损失,而且会使油品泄漏,造成资源浪费、污染环境,更为严重的可酿成火灾、爆炸等危险,同时,腐蚀还会引起油品的胶质、酸碱度、盐分增加,影响油品的性能,降低石化企业的经济效益。
因此对在用常压储油罐的腐蚀情况进行可靠有效地定性、定量检测评估是保证石化工业安全运行的关键。
2 储罐底板腐蚀失效原因通过对克石化公司各类储罐腐蚀失效的统计分析表明,罐顶板气相部位腐蚀相对较轻;罐壁板腐蚀多为均匀点蚀,腐蚀主要发生在油水界面、油气界面处;相对而言,储罐底板最为严重,其腐蚀主要分为内壁腐蚀和外壁腐蚀。
内壁腐蚀主要形式为溃疡状的坑状腐蚀,腐蚀位置主要发生在焊接热影响区、凹陷及变形处,进料口及人孔处,外壁腐蚀主要形式为点状、针状或丝状腐蚀,主要发生在边缘板与环梁基础接触的一面以及底板隆起及踏空区域。
3 储罐底板漏磁检测现场实例(1)该罐底板的腐蚀失效主要发生在背部,主要原因是建造时基础表面没有清理干净,存在沉积物或地下水及其它污水渗透流到罐底而引起的,同时底板隆起变形也是造成背部腐蚀的重要因素之一;(2)该罐底板中幅板发生的腐蚀主要是坑状腐蚀、点腐蚀等局部腐蚀,焊缝处的残余应力对腐蚀的影响不大。
漏磁技术在常压储罐检测中的应用

漏磁技术在常压储罐检测中的应用摘要:文章叙述了常压储罐底板腐蚀测验中的应用特点;讲解了漏磁测验的原理与漏磁检测技术于钢制常压储罐底板测验之中的应用、特点及如何于常压储罐检测之中展开实施给出了精确的检测方法,研究了漏磁测验的主要影响因素,并且提交了仪器改良的建议。
关键词:常压储罐;漏磁技术;检测;影响大型常压储罐是石油石化行业常见的关键设备,一般用作存储石油产品或是危险性化学品。
目前国际上最大的常压储罐单体24万吨,我国现用的常压储罐单体最为大容积为15万吨。
因为相关标准与检验技术、检测设备等诸多的原因,使用储罐的检验率非常小,很多储罐交付运用之后没实行过精确的检验,以至于使用储罐因为生锈导致的破损、泄露等问题经常爆发,导致物料损失、环境污染等。
怎样采取有效措施,降低大型储罐的安全事故,变换目前预防性的周期检修模式是各储罐管理者面对的深远问题,因而科学简易的检验检测技术成为很多科研检测机构与储罐用户多年用以专注分析的方向,它结合了风险管理、一致性状况、检测检测以及应急救援措施等很多方面的内容,为管理者实时动态监管与决策提供平台。
漏磁侦测技术是目前尤为精确、快速的一种底板生锈腐蚀侦测的方法,于讲解其原理以及应用的基础之上,研究了其影响因素并且提交了相关改进建议。
一、漏磁检测原理介绍漏磁侦测是一种透过侦测电场的金属表面溢出的磁通量来辨别缺陷的技术。
一块表面平坦而且内里材质皆匀、铁磁性工件遭磁场磁化之后,工件之内会存在磁场,磁力线垂直在工件表面穿越工件;当工件有着生锈或是机械损伤等缺陷时,因为工件材料和缺陷部位的导磁率有所不同,穿越工件的磁力线会发生变化:大部分磁力线会绕过缺陷,余下部分磁力线会穿越缺陷,历经空气或是其他介质绕过缺陷再次转入工件。
溢出工件的部分便是所说的漏磁场,其大小和缺失的深度、形状,呈一定的线性关系,透过磁感应传感器取得漏磁场信号,使用计算机展开分析处理,透过和标准试板比对,便可更进一步认识缺陷的相应特征例如大小、深度等。
漏磁检测技术在带涂层常压罐底板检测中的应用
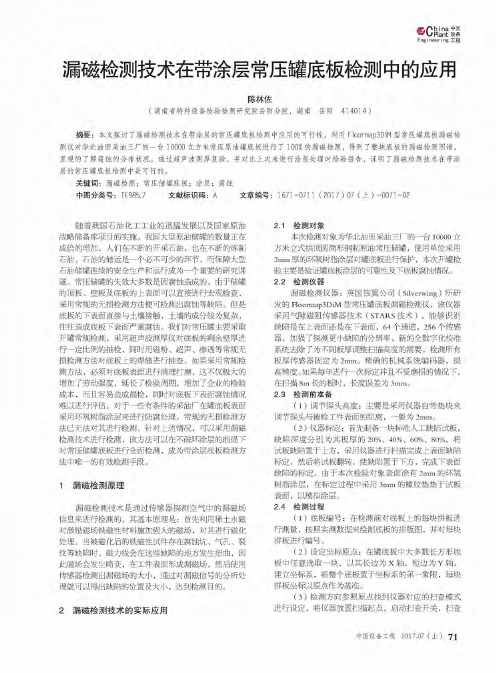
漏磁检测技术在带涂层常压罐底板检测中的应用陈林佐(湖南省特种设备检验检测研究院岳阳分院,湖南岳阳414014)摘要:本文探讨了漏磁检测技术在带涂层的常压罐底板检测中应用的可行性,利用Floormap3Di M 型常压罐底板漏磁检测仪对华北油田采油三厂的一台10000立方米常压原油罐底板进行了 100%的漏磁检测,得到了整块底板的漏磁检测图谱, 直观的了解腐蚀的分布状况。
通过超声波测厚复验,并对比上次未进行涂层处理时检验报告,证明了漏磁检测技术在带涂 层的常压罐底板检测中是可行的。
关键词:漏磁检测;常压储罐底板;涂层;腐蚀中图分类号:TE985.7文献标识码:A文章编号:1671-0711 ( 2017 ) 07 (上)-0071-02®C hl Ln n t a 中备Engineering 工程随着我国石油化工工业的迅猛发展以及国家原油 战略储备库项目的实施,我国大型原油储罐的数量正在 成倍的增加,人们在不断的开采石油,也在不断的炼制 石油。
石油的储运是一个必不可少的环节,而保障大型 石油储罐连续的安全生产和运行成为一个重要的研究课 题。
常压储罐的失效大多数是因腐蚀造成的,由于储罐 的顶板、壁板及底板的上表面可以直接进行宏观检查, 采用常规的无损检测方法便可检测出腐蚀等缺陷。
但是 底板的下表面直接与土壤接触,土壤的成分较为复杂, 往往造成底板下表面严重腐蚀。
我们对常压罐主要采取 开罐常规检测,采用超声波测厚仪对底板的剩余壁厚进 行一定比例的抽检,同时用磁粉、超声、渗透等常规无 损检测方法对底板上的焊缝进行抽查。
如果采用常规检 测方法,必须对底板表面进行清理打磨,这不仅极大的 增加了劳动强度,延长了检验周期,增加了企业的检验 成本,而且容易造成漏检,同时对底板下表面腐蚀情况 难以进行评估。
对于一些有条件的采油厂在罐底板表面 采用环氧树脂涂层来进行防腐处理,常规的无损检测方 法已无法对其进行检测。
钢质储罐底板无损检测技术

钢质储罐底板无损检测技术钢质储罐底板是储罐的基础和承载结构,其安全性和完整性对于储罐的正常运行至关重要。
随着储罐的使用年限的增长,底板的老化、腐蚀和损坏等问题也逐渐显现出来。
定期对储罐底板进行无损检测显得尤为重要。
钢质储罐底板无损检测技术是一种在不损伤储罐底板的情况下,通过对储罐底板进行各种检测手段来评估其完整性和安全性的技术。
无损检测技术能够检测到底板的各种缺陷和损伤,如裂纹、腐蚀、磨损等,帮助运营人员及时了解储罐的健康状况,确定是否需要采取维修措施,并及时进行维修和更换。
1. 超声波检测:超声波检测是利用超声波在材料中的传播特性来检测底板的缺陷和损伤的一种方法。
通过探头将超声波传入底板,根据不同的传播速度和反射情况,可以判断出底板是否存在问题。
2. 磁粉检测:磁粉检测是通过在底板表面涂覆磁粉,利用其自身磁性特性来检测出底板表面的裂纹和缺陷。
当磁粉与底板表面的磁场发生作用时,会产生磁粉堆聚在缺陷区域,从而可以观察到缺陷情况。
3. 射线检测:射线检测是利用X射线或γ射线通过底板材料来检测底板内部的缺陷和损伤。
将射线投射到底板上,通过观察射线在底板中的衰减情况,可以确定底板是否存在问题。
4. 磁带检测:磁带检测是利用感应电流产生的磁场来检测底板的缺陷和损伤的方法。
感应电流在底板中传播时,会受到缺陷和损伤的影响,通过测量磁场的变化,可以判断底板的健康状况。
这些无损检测技术在实际应用中经过了长期的改进和发展,已经成为储罐底板检测的常用手段。
它们具有操作简便、检测灵敏度高、范围广等优点,能够有效地发现底板的缺陷和损伤,并及时采取措施修复和更换。
钢质储罐底板无损检测技术是确保储罐安全和设施可靠运行的关键技术之一。
通过定期的无损检测,可以及时发现底板的问题,减少事故的发生,保障装置的正常运行。
储罐运营管理人员应高度重视储罐底板的无损检测工作,并合理安排检测周期,确保检测工作的有效性和及时性。
在检测过程中要严格遵守相关的安全操作规程,确保检测人员的安全。
钢制储罐罐底板的检测及修复

钢制储罐罐底板的检测及修复作者:李文正来源:《赢未来》2017年第13期摘要:本文首先介绍了钢制储罐罐底的腐蚀机制,然后介绍了几种常用的罐底板检测技术,并对检测技术的特点进行了比较,最后结合工程实际,介绍了几种常用的罐底板的修复方法。
关键词:钢制储罐;罐底板;检测;修复中图分类号:TE988 文献标识码:A 文章编号:2095-3178(2018)06-0310-01钢制储罐在化工领域有着普遍的应用,而储罐罐底板的腐蚀是钢制储罐的主要失效形式,储罐一旦泄露,极易引起火灾及爆炸事故。
但罐底板的检测难度较大,腐蚀泄露后的修复方法不当,仍然会在短时间内引起储罐的再次泄露,由此可见,对于罐底板腐蚀泄露的检测及腐蚀后的修复显得尤为重要。
一、腐蚀原因分析腐蚀分为杂散电流腐蚀和电化学腐蚀。
1、杂散电流腐蚀杂散电流是沿规定路径之外的途径流动的电流,它在土壤中流动,经过土壤到达预期目的以外的结构。
该电流从底板的某一部位进入底板,沿底板流动一段距离后,又从底板流入土壤,在电流流出部位,底板发生腐蚀。
2、电化学腐蚀两种不同组分的金属在电解质中连接时会产生电化学腐蚀。
电流从最活跃的金属(阳极)流动至最不活跃的金属(阴极),并加速攻击阳极金属。
二、罐底板检测技术1、漏磁检测1)漏磁检测简介:漏磁检测是建立在铁磁性材料高磁导率特性的基础上,通过测量外加磁场作用下构件表面漏磁场大小来确定缺陷信息的一种无损检测方法。
漏磁罐底扫描能覆盖罐底除焊缝连接处以及其他阻碍物以外的绝大部分区域。
2)漏磁检测与超声检测法的配合:一般情况下,超声检测方法用于证实工作,后续的超声检测对于有效的电磁罐底扫描检测至关重要,宜实施更为具体的定量超声波厚度扫描检测或者腐蚀扫描检测。
2、取样检测法以前进行取样的目的是为了要确定是否存在土壤侧腐蚀。
与目前的其他方法相比,取样法已经不能可靠地确定局部土壤侧点蚀的位置了。
但是可以取下代表性截面或者样品核实漏磁检测或者超声测试结果。
- 1、下载文档前请自行甄别文档内容的完整性,平台不提供额外的编辑、内容补充、找答案等附加服务。
- 2、"仅部分预览"的文档,不可在线预览部分如存在完整性等问题,可反馈申请退款(可完整预览的文档不适用该条件!)。
- 3、如文档侵犯您的权益,请联系客服反馈,我们会尽快为您处理(人工客服工作时间:9:00-18:30)。
1.3储罐底板漏磁检测方法、应用及其发展趋势 磁现象是认识较早的物理现象之一,我国春秋战国时期就使用司南作为磁测量仪器,东汉时期就有磁化技术的研究。北宋沈括所著《梦溪笔谈》对磁化技术有详细的介绍。国外对漏磁检测技术的研究很早, 采用磁粉探伤检测技术的设想,最早由美国人霍克于1922年提出,因为当时没有磁化技术的限制和合格的磁粉,这一伟大设想没有实现.1933 年Zuschlug [ 5]首先提出应用磁敏传感器测量漏磁场的思想, 但并没受到重视。1947 年Hast ing s 设计了第一套完整的漏磁检测系统, 漏磁检测才开始受到普遍的承认,1950年西德Forster 研制出产品化的漏磁探伤装置。用于焊缝及其管、棒体的探伤,磁化方式采用剩磁法。1965 年, 美国TubecopeVetco 国际公司采用漏磁检测装置Linalo g 首次进行了管内检测, 开发了Wellcheck 井口探测系统, 能可靠地探测到管材内外径上的腐蚀坑、横向伤痕和其它类型的缺陷。漏磁的检测结果具有良好的定量性、客观性和可记录性, 不仅适用于钢棒和钢管的成品检验, 而且对于粗糙表面的钢坯等中间产品的探伤也适用, 但是一般情况下漏磁探伤只适用于形状比较规则的工件。1973 年, 英国天然气公司采用漏磁法对其所管辖的一条直径为600 mm 的天然气管道的管壁腐蚀减薄状况进行了在役检测, 首次引入了定量分析方法。ICO 公司的EMI 漏磁探伤系统通过漏磁探伤部分来检测管体的横向和纵向缺陷, 壁厚测量结合超声技术进行, 提供完整的现场探伤。;1976年,加拿大诺兰达矿业有限公司Krank KitZinger等人[25l首次采用霍尔元件作为磁敏元件外加永磁体构成的轴向磁扼对钢管施加轴向磁化的漏磁检测设备. 英国Silver Wing 公司已经推出了多种储罐和管道漏磁检测系统,例如FLOORMAP2000储罐底板检验系统, 通过便携式计算机将所有检测到的数据以图形方式直观地显示出来, 它能检测下底板的深为40% 罐板厚的人工缺陷( 圆锥形孔洞或弧坑 , 也可发现6mm 厚的平板上大约深为20%罐板厚的腐蚀。
对于缺陷漏磁场的计算始于1966 年, Shcherbinin和Zat sepin 两人采用磁偶极子模型计算表面开口的无限长裂纹, 前苏联也于同年发表了第一篇定量分
析缺陷漏磁场的论文, 提出用磁偶极子、无限长磁偶极线和无限长磁偶带来模拟工件表面的点状缺陷、浅裂纹和深裂缝。之后, 苏、美、德、日、英等国相继对这一领域开展研究, 形成了两大学派, 主要为研究磁偶极子法和有限元法。Shcherbinnin和Poshag in 用磁偶极子模型计算了有限长表面开口裂纹的磁场
分布。1975 年, Hw ang 和Lo rd 采用有限元方法对漏磁场进行分析, 首次把材料内部场强和磁导率与漏磁场幅值联系起来。Atherton[ 6] [ 7]把管壁坑状缺陷漏磁场的计算和实验测量结果联系起来, 得到了较为一致的结论。Edw ards 和Palaer[ 5]推出了有限长开口裂纹的三维表达式, 从中得出当材料的相对磁
导率远大于缺陷深宽比时, 漏磁场强度与缺陷深度呈近似线性关系的结论。 另外,2009年,美国莱斯大学( ReeuniversitySushantM.Dutta和 FathiH.Ghorbel等人[95一96]自建磁偶极子模型模拟分析缺陷的3一D漏磁场分布;
我国从90 年代初对漏磁检测技术进行了研究, 在国内理论研究方面, 仲维畅[ 10] 用磁偶极子模型研究了有限长、无限长磁偶极子的漏磁场分布, 阐述了缺陷处漏磁场的特点。于2002 年研制出管道和钢板腐蚀漏磁检测仪[ 8] , 其总体技术水平落后于欧美等发达国家。近年来, 在无损检测工作者的努力合作下, 目前已有许多的高校和研究单位取得了丰硕的成果, 逐步缩小了与国际水平的
差距。国内研究漏磁检测技术的高校主要有清华大学、华中科技大学、天津大学、上海交通大学、沈阳工业大学等。其中华中科技大学的杨叔子、康宜华、武新军等, 在储罐底板漏磁检测研究和管道漏磁无损检测传感器的研制、对钢丝绳无损检测仪器中的一些算法进行探讨, 从一些信号的处理中提取了缺陷特征, 利用AN SYS 软件分析了传感器励磁装置的参数对钢板局部磁化的影响, 设计了相应的漏磁检测传感器等[ 9]; 我国华中科技大学陈厚桂[97]在其博士论文中进行了钢丝绳漏磁检测及评估数学建模描述。清华大学的黄松龄、李路明等研究了管道和铁铸件的漏磁探伤方法[ 10] , 采用有限元分析法研究永磁体几何参数对管道磁化效果的影响[ 11] , 分析漏磁探伤中各种量之间的数值关系, 如表面裂纹宽度对漏磁场Y 分量影响的问题; 交直流磁化问题[ 12] ; 沈阳工业大学的杨理践等, 研究了基于单片机控制系统的管道漏磁在线检测系统[ 13] , 分析了小波包在管道漏磁信号分析中的应用[ 14] , 通过时域分析理论对管道漏磁信号进行处理; 合肥工业大学的何辅云对漏磁探伤采用多路缺陷信号的滑环传送方法[ 15] 并研制了在役管线漏磁无损检测设备; 上海交通大学的阙沛文、金建华等对海底管道缺陷漏磁检测进行研究, 通过小波分析对漏磁检测信号进行去噪实验, 同时将巨磁阻传感器应用于漏磁检测系统[ 16] , 研制了适用于输油、输气管道专用漏磁检测传感器[ 17] ; 中原油田钻井机械仪器研究所开发出了抽油杆井口漏磁无损检测装置; 军械工程学院研制的智能漏磁裂纹检测仪, 能对钢质构件的表面和内部的裂纹进行定量检测[ 18] ; 中国科学院金属研究所的蔡桂喜对磁粉和漏磁探伤对裂伤缺陷检出能力进行了研究, 用环电流模型计算了各种矩形槽形状人工及自然缺陷产生的漏磁场, 提出磁粉和漏磁两种方法不适合开裂缝隙很窄的疲劳裂纹的检测的结论[ 19] 。爱德森公司采用多信息融合技术研制成集涡流、漏磁、磁记忆、低频电磁场于一体的便携式检测仪器, 该仪器能同时获取多种检测信号, 适用于流动现场的检测。各无损检测公司还不断与各大研究所、高效联手,致力于将储罐漏磁检测的理论研究及其应用推向更高水平
[ 6 ] D. L. Atherto n, Finit e element calculatio ns and computer measur ements of mag net ic flux lea kag e patter ns fo r pits. 30 ( 2 , p159, British Jo urnal of NDT , 1988
[ 7] D. L. Atherto n, Mag netic inspect ion is key to ensuring safe pipelines, 87( 8 , Oil and Ga s Jour nals [95]Sushant .M.Dutta, Fathi.H.Ghothel, RoderieK.Stanley.Dipole modeling of Magnetic flux Ieakage[J].IEEE Trans.Magn.,2009,45(4:1959一1965.
[96] SushantM.Dutta ,Fathi H.Ghorbel,and Roderic K.Stanley,Simulation And analysisof3一 D magnetic flux leakage[J].IEEE Trans onMAGN.,2009, 45(4:1966一
1972.
[ 10] 仲维畅. 磁偶极子与磁粉探伤磁粉探伤原理之一[ J] . 无损检测, 1990, 12( 3 : 66- 70 [ 8] 沈功田. 中国无损检测进展. NDT 无损检测, 中国. 世界, 2005, ( 2 [ 9] 刘志平, 康宜华, 武新军, 等. 储罐底板漏磁检测传感器设计. 无损检测, 2004, 26( 12 : 612~615
[97]陈厚桂.钢丝绳磁性无损检测技术的评估方法及标准研究[DI.华中科技大学图书馆,2006.
[ 10] 李路明, 黄松龄, 李振星, 等. 铸铁件的漏磁检测方法.清华大学学报, 2002, 42( 4 : 474~476
[ 11] 黄松龄. 管道磁化的有限元优化设计. 清华大学学报,2000, 40( 2 : 67~69 [ 12] 李路明, 黄松龄, 施克仁. 漏磁检测的交直流磁化问题. 清华大学学报, 2002, 42( 2 : 154~156
[ 13] 杨理践, 马凤铭, 高松巍. 管道漏磁在线检测系统的研究. 仪器仪表 学报, 2004, ( 8 [ 14] 杨理践, 李松松, 王玉梅, 等. 小波包在管道漏磁信号分析中的应用. 仪器仪表学报, 2002, ( 6
[ 15] 何辅云. 漏磁探伤中多路缺陷信号的滑环传送方法.合肥工业大学学报( 自然科学版 , 1998( 6 : 128~132
[ 16] 周林, 阙沛文. 海底输油管道缺陷漏磁检测信号采集与处理系统的设计. 计算机测量与控制, 2004, 12( 2 :120~121
[ 17] 陈亮, 阙沛文, 黄作英, 等. 一种新型磁阻式传感器在漏磁检测中的 应用. 传感器技术, 2004, 23( 10 [ 18] 徐章遂, 靳英卫, 张政保, 等. 基于磁检测的螺栓孔裂纹定量检测方法. 无损检测, 2001, ( 6 : 237~239 [ 19] 蔡桂喜. 磁粉和漏磁探伤对裂纹状缺陷检出能力的研究. 2004 年全国电磁( 涡流 检测技术研讨会论文集.鞍山: 爱德森( 厦门 电子有限公司NDT 事业部,2004, 40~48
[ 20] 任吉林, 林俊明, 高春法. 电磁检测. 北京: 机械工业出版社, 2000 [ 21] 美国无损检测学会. 美国电磁无损检测手册电磁卷.1986, 922~966 [ 22] 金建华, 阙沛文, 杨叔子. 油管腐蚀缺陷的在线检测技术. 计算机测
量与控制, 2002, 10( 11 : 716~718 [ 23] 金涛, 阙沛文. 小波分析对漏磁检测噪声消除实验的分析. 传感技术 学报, 2003, 16( 3 : 260~262 [ 24] 李路明, 黄松龄, 杨海青, 等. 抽油管壁磨损量检测方法. 清华大学 学报, 2002, 42( 4 : 509~511 1.3.2 国内发展概况 国内开展储罐检测的时间较晚,检测技术和设备也比较落后。目前国内常用的 检测技术包括超声法、磁粉法和真空检漏法等。以超声法为例,一个直径 30m 的原