炼厂干气中乙烯回收和利用技术进展
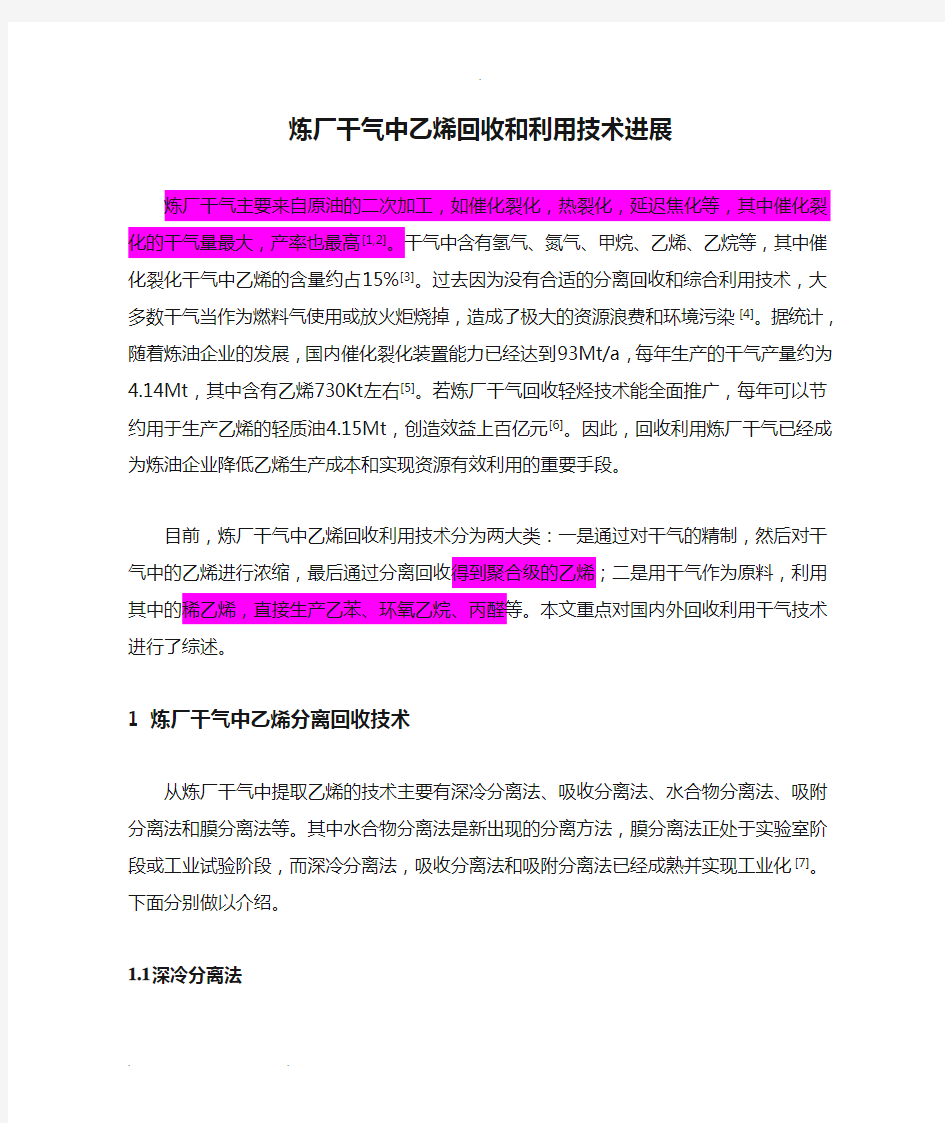
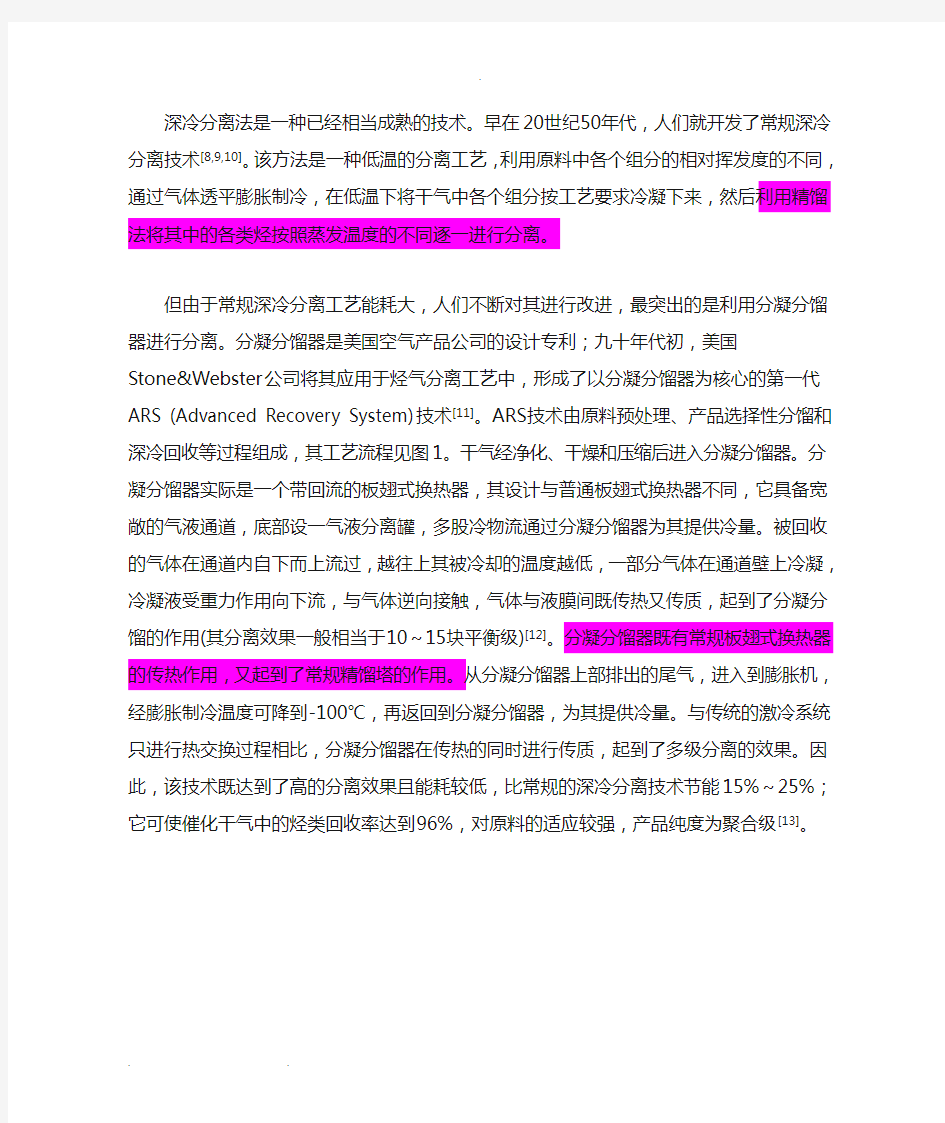
炼厂干气中乙烯回收和利用技术进展
炼厂干气主要来自原油的二次加工,如催化裂化,热裂化,延迟焦化等,其中催化裂化的干气量最大,产率也最高[1,2]。干气中含有氢气、氮气、甲烷、乙烯、乙烷等,其中催化裂化干气中乙烯的含量约占15%[3]。过去因为没有合适的分离回收和综合利用技术,大多数干气当作为燃料气使用或放火炬烧掉,造成了极大的资源浪费和环境污染[4]。据统计,随着炼油企业的发展,国内催化裂化装置能力已经达到93Mt/a,每年生产的干气产量约为4.14Mt,其中含有乙烯730Kt左右[5]。若炼厂干气回收轻烃技术能全面推广,每年可以节约用于生产乙烯的轻质油4.15Mt,创造效益上百亿元[6]。因此,回收利用炼厂干气已经成为炼油企业降低乙烯生产成本和实现资源有效利用的重要手段。
目前,炼厂干气中乙烯回收利用技术分为两大类:一是通过对干气的精制,然后对干气中的乙烯进行浓缩,最后通过分离回收得到聚合级的乙烯;二是用干气作为原料,利用其中的稀乙烯,直接生产乙苯、环氧乙烷、丙醛等。本文重点对国内外回收利用干气技术进行了综述。
1 炼厂干气中乙烯分离回收技术
从炼厂干气中提取乙烯的技术主要有深冷分离法、吸收分离法、水合物分离法、吸附分离法和膜分离法等。其中水合物分离法是新出现的分离方法,膜分离法正处于实验室阶段或工业试验阶段,而深冷分离法,吸收分离法和吸附分离法已经成熟并实现工业化[7]。下面分别做以介绍。
1.1深冷分离法
深冷分离法是一种已经相当成熟的技术。早在20世纪50年代,人们就开发了常规深冷分离技术[8,9,10]。该方法是一种低温的分离工艺,利用原料中各个组分的相对挥发度的不同,通过气体透平膨胀制冷,在低温下将干气中各个组分按工艺要求冷凝下来,然后利用精馏法将其中的各类烃按照蒸发温度的不同逐一进行分离。
但由于常规深冷分离工艺能耗大,人们不断对其进行改进,最突出的是利用分凝分馏器进行分离。分凝分馏器是美国空气产品公司的设计专利;九十年代初,美国Stone&Webster 公司将其应用于烃气分离工艺中,形成了以分凝分馏器为核心的第一代ARS (Advanced Recovery System)技术[11]。ARS技术由原料预处理、产品选择性分馏和深冷回收等过程组成,其工艺流程见图1。干气经净化、干燥和压缩后进入分凝分馏器。分凝分馏器实际是一个带回流的板翅式换热器,其设计与普通板翅式换热器不同,它具备宽敞的气液通道,底部设一气液分离罐,多股冷物流通过分凝分馏器为其提供冷量。被回收的气体在通道内自下而上流过,越往上其被冷却的温度越低,一部分气体在通道壁上冷凝,冷凝液受重力作用向下流,与气体逆向接触,气体与液膜间既传热又传质,起到了分凝分馏的作用(其分离效果一般相
当于10~15块平衡级)[12]。分凝分馏器既有常规板翅式换热器的传热作用,又起到了常规精馏塔的作用。从分凝分馏器上部排出的尾气,进入到膨胀机,经膨胀制冷温度可降到-100℃,再返回到分凝分馏器,为其提供冷量。与传统的激冷系统只进行热交换过程相比,分凝分馏器在传热的同时进行传质,起到了多级分离的效果。因此,该技术既达到了高的分离效果且能耗较低,比常规的深冷分离技术节能15%~25%;它可使催化干气中的烃类回收率达到96%,对原料的适应较强,产品纯度为聚合级[13]。
图 1 ARS工艺流程简图
1 净化干燥;
2 压缩;
3 分凝分溜器;
4 膨胀-压缩机;
5 尾气;
6 C2馏分;
7 C3馏分
Fig. 1 Process flow diagram of Advanced Recovery System
1 Purification and drying;
2 Compression;
3 Dephlegmator;
4 Expansion turbines- compressors;
5 Off gas;
6 C2 Fractions;
7 C3 Fractions
近年,Stone&Webster公司又提出以热集成精馏系统(Heat Integrated Rectifier System, 简称HRS)为核心设备的第二代ARS技术[14]。HRS既是对传统精馏的改进,也是对分凝分馏器的重大改进,它将常规板翅式换热器、分离罐和精馏塔进行了热集成,无回流泵。它与分凝分馏器相比,传热效率大幅度提高,约为分凝分馏器的10倍。达到相同的分离效果时,设备尺寸大幅减小,投资大幅降低。
深冷分离工艺是提纯裂解乙烯的传统工艺,技术成熟,回收率高,产品纯度高。但该工艺往往需要-100℃的低温下进行,装置能耗高且投资大。一般适合处理有大量干气的情况,特别是炼厂集中的地区及大型FCC装置比较多的地区。如美国Mobil公司,有550万吨/年的FCC干气,采用深冷分离法回收其中的乙烯收到了明显的经济效益[15]。但该技术对炼厂规模小,且又较分散的情况下,则不经济。
针对采用深冷分离法回收炼厂干气工艺存在的能耗高、设备规模大、投资大等问题,中石化北京化工研究院提出了利用混合气作制冷剂来分离催化干气中乙烯的方法。其工艺流程图见图2。炼厂干气经净化和干燥后,进入冷箱冷却,冷却后进入重烃分离罐,罐顶气体再次进入冷箱进一步冷却,罐底液体送入脱甲烷塔;重烃分离罐顶气体经过深冷、节流,进入闪蒸罐,罐顶气体经过膨胀,进入冷箱以回收冷量,然后自冷箱排出;罐底液体进入脱甲烷塔。进入脱甲烷塔的液体经精馏作用脱除甲烷、氢气和氮气等;脱甲烷塔顶得到的气体进入冷箱回收冷量,然后自冷箱排出,塔釜可以得到富含乙烯的物流。工艺利用由氢气、甲烷、乙烯和丁烷组成的混合气作制冷剂,通过三段压缩制冷,采用膨胀机和冷箱回收冷量。本工
艺的显著特点:用氢气、甲烷、乙烯和丁烷等组成的混合气作为制冷剂,来源容易,成本低廉;相对于复叠式制冷,本发明的混合制冷提高了冷量利用效率;干气进入冷箱冷却后进入重烃分离罐,罐底液相直接送入脱甲烷塔,降低了冷箱的负荷;采用膨胀机和冷箱有效地回收了冷量。
FCC Dry
Gas CH 4、H 2
图2
1.2 吸收分离法
吸收分离法是利用炼厂干气中各个组分在吸收剂溶解度的不同进行分离,它可以分为物理吸收法和化学吸收法。物理吸收主要包括油吸收法和Mehra 溶剂抽提工艺。化学吸收法包括水溶液和非水溶液体系。
1.2.1 油吸收法
油吸收法一般利用C 4、C 5和芳烃作为吸收剂,吸收干气中C 2+
,分离出甲烷、氢气、氮气等不凝气体,再用精馏法把吸收的各个组分逐一分离开来。通过对吸收液的解吸和初步分离
可得到含有乙烯84%以上的C 2组分,乙烯的回收率可达95%以上[13, 16]。工艺流程图见图2。该
方法具有规模小,适应性强,投资费用低等特点,适合中小规模炼厂干气中低浓度乙烯的回收。
9
图 2 中冷油吸收工艺流程图
1 炼厂干气;
2 净化及干燥;
3 压缩;
4 吸收塔
5 解吸塔
6 粗分塔;
7 富溶剂;
8 贫溶剂;
9 甲烷、
氢气、氮气等;10 粗乙烯;11 乙烷等组分
中国石化洛阳石化工程公司根据催化裂化干气特点,开发了中冷油吸收法分离干气中乙烯的工艺[17]。该工艺将干气加压到3.5MPa,在-40℃低温下用C5作为吸收剂吸收干气中的C2+,将干气中甲烷、氢气、氮气等分离出去;吸收乙烯的富溶剂进入解吸塔进行解吸,解吸塔顶解吸气经冷却冷凝后,液相回流,气相即为富乙烯气,送往乙烯装置的分离系统。该工艺采用了由螺杆压缩机、冷凝器、液氨储罐、节流阀、蒸发器组成密闭循环的制冷系统,并采用多级制冷方式来节能。
针对催化裂化干气制乙苯技术的发展和干气中丙烯对催化剂的影响,中国科学院大连化学物理研究所开发了一种从催化裂化干气中选择性吸收丙烯的方法[18]。该方法将无需净化和精制的催化裂化干气通过对丙烯有选择性吸收的吸收剂来除去丙烯。吸收剂包括苯、乙苯、二乙苯、三乙苯、多乙基苯、柴油、汽油等中一种或几种混合物。吸收剂对干气中丙烯的吸收条件:操作温度为-10℃~40℃,压力为0.1~3.5MPa,吸收剂/干气体积比(mL/L):3~25。张银龙等[19]通过苯、乙苯、柴油、反烃化料和乙苯/反烃化料等吸收剂对干气中丙烯吸收效果的对比,结果发现乙苯/反烃化料对丙烯的吸收效果最理想。吸收丙烯后的吸收剂可以在一定的条件下解吸,解吸后的吸收剂可以重复使用。利用吸收后的干气制乙苯可以明显地提高乙基化产物选择性。
中石化北京化工研究院从20世纪70年代开始了中冷油吸收工艺的研究,当时开发的中冷油吸收技术主要用于管式裂解炉裂解气的分离。最近又开发了用于催化干气回收乙烯的浅冷油吸收工艺[3,20]。催化干气经过一段压缩后,脱除酸性气体、NO x和氧气等;再经过二段压缩机,干气的压力提高到2.0~2.6MPa,然后进入干燥器;将干燥后的干气逐步冷却至-20℃~-10℃,送入吸收塔。该工艺采用包含正戊烷、异戊烯、正戊烯和2-戊烯等碳五馏分作为吸收剂,吸收干气中的C2+。富溶剂靠压差进入解吸塔,塔顶得到回收的C2馏分;塔釜采出贫吸收剂,经过逐级冷却,返回吸收塔循环使用。吸收塔中未被吸收的甲烷、氢气、氮气等不凝气体,进入膨胀机和冷箱组成的系统,利用自身的压力膨胀制冷,再在闪蒸罐中闪蒸,从闪蒸罐底部回收其中未被吸收的C2馏分和夹带的吸收剂,不含C2馏分的尾气进入瓦斯管网系统。该工艺的特点是:采用浅冷油吸收流程脱除甲烷、氢等,吸收温度在-15℃左右,可以用氨制冷,操作简单,投资少,能耗低;采用膨胀机和冷箱回收冷量,乙烯回收率提高,可达95%,同时减少了吸收剂的循环量和损失量。
1.2.2 溶剂抽提工艺
溶剂抽提工艺又称作Mehra工艺,它是由美国休斯顿AET公司开发的从炼厂干气中回收乙烯的一种方法[21,22]。Mehra工艺流程图如图3所示。干气经压缩,净化和干燥后,流到抽提-汽提塔下部,由贫溶剂抽提气体中的C2+,然后将富溶剂送入分馏塔就可以得到乙烯等烃类产品。贫溶剂由分馏塔底流出,通过抽提-汽提塔上部和闪蒸罐,可以分别得到90%的氢气和甲烷燃料气,氢气可在变压吸附装置中进一步净化达到99%的纯度。Mehra工艺采用的溶剂一般为聚烷撑二醇二烷基醚、N-甲基吡咯烷酮、二甲基甲酚胺、碳酸丙烯酯、环丁砜和乙二醇三乙酸酯等的特殊混合物。该工艺的操作温度为-37℃,压力为1.7Mpa。
图3 Mehra工艺流程图
1 抽提-汽提塔(下部);2抽提-汽提塔(上部);3 闪蒸罐;4 分馏塔;
Fig 3 Process flow diagram of Mehra
1 Extraction-Stripping column(bottom);
2 Extraction-Stripping column(top);
3 Flash Tank;
4 Fractionator
1.2.3 化学吸收法
化学吸收法是利用吸收剂中过渡金属与烯烃形成Π-络合物,使烯烃和其他组分分离。通常采用与烯烃形成络合物可逆性较好,成本相对较低的Cu(I)和Ag(I)。化学吸收法包括水溶液和非水溶液体系。
水溶液体系包括Cu(I)和Ag(I)两种体系。AgNO3、AgBF4和CuNO3等均可用作烯烃的分离。Douglas等[23]开发了一种以AgNO3水溶液为吸收剂的工艺,操作压力为1.65MPa,吸收温度为30~40℃,解吸温度约为50℃。文献[23]还报道I.C.I公司开发了以CuNO3/ 乙醇胺为吸收剂的工艺,操作压力为1.2MPa,吸收温度为30℃,脱附温度为60℃,产品纯度为86.6%,回收率也较高。
非水溶液体系主要是Cu(I)体系。Cu(I)与有机溶剂有弱络合作用,在有机溶剂中比在水溶液中稳定,不易歧化。研究比较多的络合剂有CuCF3(CO)2、CuNO3、Cu2SO4、CuBF4、CuAlCl4、CuAlCH3Cl3、CuAlC2H5Cl3、CuAlCNCl3和卤化胺等,溶剂一般用芳香溶剂[24]。美国Tenneco化学公司开发了一种称为ESEP的双金属盐络合吸收工艺[25, 26]。该工艺采用一种双金属盐类(CuAlCl4)溶于甲苯而形成的Π-络合物作为吸收剂,吸收剂对氢和饱和烃不反应,对CO和不饱和烃具有反应活性,可从气体混合物中选择性的吸收乙烯组分。在吸收乙烯过程中,吸收剂的甲苯被取代,乙烯与络合剂之间形成一个较弱的键,经加热后即可从络合剂中分离出乙烯。副产物CO可进一步精制成CO成品或者用作炼油厂燃料。该工艺在乙烯含量为12%(体积)时,乙烯的回收率可达96%,纯度为99.5%。在炼厂规模不大,产气量较小的情况下,采用该工艺具有一定的优越性。但工艺对原料中水和硫化合物含量要求严格控制,两者质量分数均要求小于10-6。因此该工艺的预处理工程较复杂,性能较好的络合吸收剂的制备工艺也比较困难,所以该工艺的发展受到了限制[27, 28]。
1.3水合物分离法
利用水合物法实现低沸点混合气体分离是一种新的分离技术[29]。气体水合物(简称水合物)是气体小分子(如N2、CO2、CH4、C2H6、C3H8等)在一定的温度和压力下和水生成的一种固体结晶物质[30]。当气体的混合物和水反应生成水合物后,残余气相的组成和进料的组成以及固体水合物相中气相的组成是不一样的。水合物分离气体混合物正是基于平衡时气固两相的组成差异来实现的[31]。
中国科学院广州能源研究所开发了一种从催化裂化干气中分离回收乙烯的方法[32]。该方法的特点是使催化裂化干气与水进行水合反应,生成含有乙烯组分的水合物。在减压和加热状态下,水合物释放出乙烯而达到分离的目的。吸收的压力为2~6MPa,温度为-20~15℃,乙烯产品的浓度为56-81%。他们还提出利用磁化可以加速水合物的生长[33]。对于低沸点气体混合物的分离,与传统的方法相比,水合物分离可以节约大量的能量,是一具有广泛开发前景的分离方法。但是目前水合法的分离技术远不成熟,未达到工业应用阶段。
1.4 吸附分离法
吸附分离法是借助气体混合物中某些组分在固体吸附剂上的优先吸附来实现分离的方法。根据吸附剂再生方法的不同可以分为变压吸附法(PSA)、变温吸附法(TSA)等[34]。在PSA 中吸附剂的再生靠降低压力来完成,而在TSA中吸附剂的再生主要靠加热来完成。PSA由于具有适用气源范围广,产品纯度高,环境污染小,操作简单等特点,目前对其研究较为活跃。TSA工艺由于循环时间长,处理气量小,仅用于纯化过程。有时两者可以结合使用。在分离烯烃-烷烃的吸附工艺中,使用吸附剂通常有沸石、活性碳和金属络合物等。
UOP公司采用沸石型分子筛进行了PSA方法回收催化裂化干气中乙烯的研究[35]。他们在C2分馏塔后配备了一套PSA系统,气体经过压缩、脱水、分馏后,进入C2分馏塔,顶部得到95%以上的乙烯,底部是含少量乙烯的乙烷,再将其送入PSA系统进行乙烯的回收,回收得到的乙烯混到裂化气中再次循环分离。
BOC公司[36]公开了以A型沸石(Na的质量分数60%~75%,K的质量分数25%~40%)为吸附剂,在操作压力0.05~5MPa,操作温度50~200℃的条件下,分离回收乙烯的工艺。专利[37, 38]提出了一种用PSA工艺回收乙烯氧化后混合气体中乙烯的技术,通过PSA工艺可以出去混合气体中的甲烷和氢气,所得乙烯返回到脱甲烷塔中,大大提高了脱甲烷塔的温度,从而降低了能耗。Raymond等[39]人利用吸附法从含低浓度乙烯的混合气体中回收乙烯。首先采用4A沸石为吸附剂从混合物中除去CO2,再用13X沸石为吸附剂从剩余的气体中选择性吸附乙烯,最后在低压下脱附,达到回收乙烯的目的。
中国四川天一科技股份有限公司开发了一种催化干气变压吸附回收乙烯的工艺。该工艺利用吸附剂对气体中不同组分的吸附能力、吸附容量和吸附速度随压力的变化而产生的差异,在吸附床中加压吸收催化干气的C2+组分,排除不易吸收的H2、CH4、N2等组分;在吸附床减压时再排除吸附的组分,从而达到分离得到目的。工艺采用多塔床循环操作,以实现工艺过程的连续性。中国石化燕山石化公司采用该工艺于2004年建成30000 Nm3/h的干气提浓装置,2005年8月开车成功,目前已经实现连续稳定生产[40]。
1.5 膜分离法
气体膜分离法是以膜两侧的气体分压差为推动力,利用不同气体在膜中渗透速率的差异,使其在膜两侧富集以实现分离的过程。1979年美国Monanto公司研制出硅橡胶-聚砜非对称复合中空纤维膜分离装置,并成功应用于合成氨弛放气中氢气的回收,它标志着气体膜分离走向了工业应用阶段[41]。
膜分离技术已经得到广泛应用,但在烯烃分离方面还处于研究阶段。近年被用于烯烃-
烷烃分离的聚合物材料主要分为两类:一类是基于烯烃、烷烃分子的尺寸和形状存在差异而导致其在膜材料中溶解扩散速率的较大差别进行分离的聚合物膜 [42];另一类膜是利用膜中金属载体与烯烃的选择性可逆络合,从而实现烯烃-烷烃分离的聚合膜,膜中金属离子有Na+、Ag+和Cu+等[43]。
日本山口大学和宇都工业公司将3,7-二氨基-2,8(6)-二甲基硫芴砜涂布在不对称聚酰亚胺中空纤维素膜上,制备了一种碳化膜[44]。当原料中丙烷和丙烯的体积分数各为50%时,在温度100℃、0.1MPa条件下,丙烯的渗透率为8.71×10-2kmol/(m2.s.kPa),丙烯-丙烷的分离因子可达22。
Leblanc等[45]通过离子交换法把Ag+浸入聚合物基体,发明了一种含银的磺化聚苯撑氧化物膜。用这种膜分离乙烯-乙烷混合物时,膜对乙烯的分离因子可达288。Boom等[46]发现加入硅铝铁盐、Na型和Ag型的沸石粉末的聚合物膜,对烯烃具有很高的渗透性和选择性。他们用乙烯和乙烷的实验证实了这一点,并认为高渗透性的原因是膜对烯烃的溶解吸收性更好;高选择性的原因是烷烃要环绕沸石颗粒走更长的通道。
膜分离技术具有工艺简单,能耗低,操作弹性大等特点。但膜受原料杂质的影响很大,需对原料进行特殊处理,设备投资很高,离工业化的要求较大,还需要进一步研究和开发。
1.6 联合工艺
在目前技术不太很成熟的情况下,采用联合工艺,发挥工艺各自的优点,将会改善分离效果和经济性。如膜分离与PSA联用、PSA与蒸馏的联用、中冷油吸收与PSA的联用等。Bessarabov等[47]对一种平片膜和流动吸收剂相结合的工艺进行了研究。结果发现在298~318K,常压的条件下,乙烯/乙烷分离系数可达560。蒋国梁等[48]采用膜分离和深冷分离联合工艺用于催化裂化氢烃的分离:先用膜分离法分离干气中的氢,随后贫氢干气用深冷法分离,从而提高了脱甲烷塔顶气的露点,降低了脱甲烷塔的能耗,所得的富氢也可直接作为加氢原料气。
2 炼厂干气的直接加工技术
2.1 炼厂干气制乙苯技术
利用炼厂干气中稀乙烯直接与苯烃化制取乙苯,是开发利用干气中乙烯资源的有效途径。国外早在20世纪50年代就开始了研究和探索,主要的工艺有Alkar工艺和Mobil-Badger 工艺等。 Alkar工艺由美国UOP公司开发,所用催化剂为BF3改性的γ-Al2O3强酸性催化剂[49]。此法催化剂活性高,选择性好,对乙烯浓度范围要求较宽。缺点是催化剂制备条件苛刻,费用较高,并且容易中毒失活。所以,在用炼厂干气作为原料时,干气中的H2S、CO2、O2及H2O需严格脱除,均需达到<1ppm,才能使过程正常操作。Mobil-badger工艺是Mobil石油公司和Badger工程公司在1976年共同开发,并与1977年实现工业化[50]。它采用ZSM-5沸石作为催化剂,用稀乙烯为原料,乙苯的收率接近100%。该工艺反应温度为430℃左右,压力1.4~2.2MPa,可以用乙烯体积分数为10%~100%的混合气体为原料。但用炼厂干气为原料时,混合气体必须脱除H2S、CO2和H2O等有害杂质,才可以使催化剂保持长时间的操作稳定性。
我国的干气制乙苯技术虽然起步较晚,但经过20多年的发展和创新,已经处于国际领先地位。从1986年开始,中科院大连化物所和抚顺石化公司石油二厂等单位联合攻关,先后开发了干气制乙苯第一代至第五代系列成套技术[51]。第一代、第二代和第三代干气制乙苯已先后应用于抚顺石油二厂、大庆林源炼油厂、大连石化公司和锦西石化等。第四代技术也完成中试试验并通过中科院的鉴定。第五代技术目前也正进行中试放大试验和8万吨/年工
艺包的编制。我国干气制乙苯技术的一个显著特点是炼厂干气不需要特殊精制就可以直接作为反应气,与苯烃化制得乙苯,节约了干气精制部分的投资和降低了能耗。据Nexant ChemSystems咨询公司分析,以炼厂干气中稀乙烯为原料生产乙苯/苯乙烯,净成本比纯乙烯降低了13%~15%[52]。
2.2 炼厂干气制环氧乙烷
以干气为原料生产环氧乙烷的工艺,目前普遍采用的是氯醇法工艺路线。该工艺包括两个反应,第一步是乙烯和次氯酸水溶液反应,在20℃~50℃及0.2MPa~0.3MPa条件下,生成氯乙醇;第二步是氯乙醇和10%~20%的碱(Ca(OH)2)反应,在100℃的条件下,生成环氧乙烷。抚顺石油二厂有一套用FCC干气以氯醇法生产环氧乙烷,进而生产乙二醇,乙醇胺等产品的工业装置,但装置存在氯气、碱等消耗指标高,经济效益不太显著的问题[53]。
2.3 炼厂干气制丙醛
目前世界上普遍应用的丙醛制备方法是将乙烯、一氧化碳和氢气的混合气在羰基钴体系或者铑膦络合物催化器体系上合成丙醛。而催化干气中含有较多的乙烯和氢气,所以在干气中加入一定量的一氧化碳,通过羰基合成丙醛,是合理利用干气的方法。四川大学开发出以FCC干气提浓的40%~80%的乙烯为原料,利用水溶性的铑膦催化剂催化稀乙烯生产技术,目前已在新疆新峰股份有限公司建成700t/a的丙醛中试装置。结果表明,水溶性的铑膦催化剂连续运转2000多小时,仍保持高活性和高选择性,产品质量达到了进口标准[54, 55, 56]。总的来说,炼厂干气中乙烯经低压羰基合成制丙醛的技术是可行的,它既能充分利用廉价的干气,又可以填补我国丙醛的市场缺口,该技术具有广阔的应用前景。
2.4 其它利用途径
中科院大连化物所与抚顺石油二厂共同研究了在LaZSM-5催化剂上,催化裂化干气
中的乙烯与甲苯制取对甲基乙苯的反应,结果表明,催化干气无需精制可作为合成对甲基乙苯的原料,乙烯的转化率达82%,对甲基乙苯的选择性为90%[57, 58]。此外,炼厂干气还可以作为制二氯乙烷[59],氯乙烯[60],燃料乙醇[61]等的原料。
3结语
干气回收利用乙烯在国外早已实施,并取得了明显的效益。但是,国内干气回收利用乙烯的工作刚刚开始,这主要是国内炼油及石化企业的结构特点和布局决定的。随着石油资源的日益紧张和催化裂化装置规模的扩大,从炼厂干气中回收乙烯可获的效益越来越显著。要解决好国内干气回收利用乙烯的问题,当务之急是根据国内企业的特点,开发出合适的技术。当今回收干气的技术很多,各具特色,各有利弊。深冷分离工艺投资大,生产成本高,适合炼厂集中的地区;油吸收和吸附工艺投资费用低,适用中小规模的炼厂,具有良好的应用前景;其他的分离方法原料必须经过严格的预处理,在经济上限制了其实用性。干气还可以直接生产出高附加值的乙苯、丙醛和环氧乙烷等。总之,炼厂干气的回收利用涉及企业诸多问题,在实际的操作中,炼油企业必须对干气的回收利用方案进行经济技术评估,根据自身特点,采用合适的技术,以得到最佳的经济效益和环境效益。同时,对炼化一体化的企业,要充分考虑炼油和化工的资源,利用好干气中乙烯等资源,充分发挥炼化一体化优势,提高企业的市场竞争力。
聚乙烯醇新型工艺技术的研究进展
聚乙烯醇新型工艺技术的研究进展 摘要: 综述了聚乙烯醇的发展历程和国内外的研究现状。介绍了聚乙烯醇的生产原料、合成高聚合度聚乙烯醇的聚合方法和引发方式,以及合成低聚合度聚乙烯醇方法的研究进展。同时从醇解过程着手简述了聚乙烯醇解工艺和醇解设备的研究和应用状况,并对中国聚乙烯醇行业的 发展提出建设性的意见。 关键词:聚乙烯醇; 新型工艺技术;研究 聚乙烯醇( PV A) 是1924 年德国的化学家赫尔曼和汉奈将NaOH 加入聚醋酸乙烯酯( PV Ac)中首次完成实验室合成的,1926 年实现工业化生产之后在全球范围内推广。PV A 可以根据不同的合成方法制备出性能各异的高分子聚合物,性能介于塑料和橡胶之间。其粘结性、耐油性、胶体 保护性、阻隔性、可降解性等特殊优异的性能大幅拓宽了它的应用领域。PV A 的研究及生产随着应用领域的不断扩大而不断深入。20 世纪80 年代中后期,国内逐步开始PV A 多用途的研究。PV A 新产品的研究与开发已成为国内外研究的热点课题. 1 目前国内外聚乙烯醇的工艺技术及产品 中国从1963 年首次引进PV A 生产工艺以来,迄今已有13 家生产企业,产量跃居全球第一。目前已有的生产工艺有乙烯法和乙炔法,分别以乙烯和乙炔为原料制备PV Ac 。再经过醇解得到PV A。根据用碱量的不同分为高碱醇解和低碱醇解两种。国内目前PV A 的聚合度主要为中等聚合度, 醇解度的范围主要有78 %、88 %、98 %和完全醇解的98 %~100 %。大宗产品PV A1799 , 主要用于纱浆料和纺织助剂。PV A2099 在盐水的催化作用下与甲醛缩合而产生具有耐水性的聚乙烯醇缩甲醛高分子化合物,广泛应用于建筑物和内外墙壁涂料。国外利用不同聚合度和醇解度具有不同的性能的特点,已生产出各种高低聚合度和醇解度的聚乙烯醇产品,高聚合度有的高达2 500~4 500 ,甚至到10 000 ;低聚合度产品的聚合度低于100 、醇解度小于50 %的聚乙烯醇产品也已问世。目前,国外已能生产出不同聚合度、醇解度的聚乙烯醇产品品种在50 种以上。特别是日本可乐丽公司生产的KH220 和LL207 ,作为PVC 聚合的悬浮剂,基本上垄断了中国的市场。中国还在加大对PV A 多品种、多用途的开发,缩短与发达国家的差距。 2 PV A 新型工艺技术的研究概况 当前PV A 新型工艺技术开发的热点主要是两个极端产品, 主要从生产的原料, 高聚合度PV A 和低聚合度PV A 的合成方法,以及在醇解过程中醇解工艺和醇解设备方面进行研究。下面分别从几个方面简述聚乙烯醇新型工艺技术的研究概况。 2. 1 生产原料 中国的13 家企业都是以天然气和电石为原料生产PV A ,技术相当成熟。最近美国哈尔康研究所开发了以甲醇和合成气制取醋酸乙烯工艺。由于中国石油、天然气资源并不丰富,要实现乙炔路线向乙烯、天然气路线的转换成本很高,而煤炭资源相对丰富,由煤生产甲醇和合成气制取醋酸乙烯是美国哈尔康研究和发展公司开发的新技术,据报道此工艺路线生产成本将比乙烯法或天然 气乙炔法低21 %。而在乙烯气相法工艺中,采用Leap 流化床工艺建厂或改扩建,在一定的生产规模下,投资费用降低30 %。利用丰富的煤炭资源,实现PV A 大规模工业化生产一定会有广阔的市场前景。目前, Halcon 公司正在开发以醋酸甲酯为原料的合成气路线,其主要的步骤是醋酸甲酯
Agilent6820分析炼厂干气全组成操作要点
1、仪器型号:6820 仪器编号: 2、操作条件(见详细操作要点) 2.1 面板: H2:0.4MPa(上表) 流量:35ml/min N2:0.24MPa(下表)流量:20ml/min 空气:>0.35MPa 2.2 柱温:50±1℃;检测器:双TCD;温度:250℃;极性:前正后负;载气:H2(前检测器)、 N2(后检测器)。 3、简单操作步骤 3.1打开色谱仪电源开关,等待仪器自检完毕后液晶显示屏显示“开机正常”。 3.2 在仪器面板上按键“柱箱”“开”,即打开柱箱温度;接着按键“前检测器”“开”, “后检测器”,即打开检测器温度,仪器便开始升温。 3.3等待检测器的温度达到150℃以上时,打开热丝温度。按键“前检测器”,通过上下按钮键 将光标移到“热丝”处,接着按“开”;同样的操作方法打开后检测器的热丝温度。 3.4双击电脑桌面上的图标“Cerity QA-QC”,进入色谱工作站软件。 3.5注册样品:进样前需要先注册样品,单击“样品”“编辑”,输入样品名称,如“循环 氢”,在方法的下拉列表中选择分析方法,干气的方法选择“炼厂气”,重整气的方法选择“重整气(样品)”,然后在操作员列表中选择分析人员姓名。最后点击“注册样品”,等待色谱面板上的“预运行”灯亮后即可进样。 3.6接入球胆,按球胆至少1分钟,夹好球胆后(非负压进样),按色谱仪“开始”键。 3.7运行灯灭后,处理色谱峰图,计算结果。 3.8结果处理:点击“重新处理”,选中需要处理的样品,打开“调用新的分析方法”,单击“用 新设定重新处理”,再点击“结果”或者“报告”,确认是否有峰没有被识别,如果有峰没有被识别或者识别错误,单击“校准”“识别”,然后修改正确的校正时间。最后点击绿色箭头“重新处理”,在报告中查看结果。 注:如果积分中需要用到手动积分,需要先按手动积分按钮,如“划基线”等,然后再手动积分事件中选中“使用手动事件”,然后点击绿色箭头“重新处理”,而不需要保存。 3.9数据传输:打开色谱工作站电脑的D盘下的“files”,将传输到里面的文本文件重命名为 LIMS中的样品号。 3.10选择下一个样品处理,电脑会提示是否需要保存所做的修改,选择“否”。切记! 4、安全注意事项 4.1 进样口高温,小心烫伤。 4.2 本仪器使用氢气,分析前请试漏。
催化裂化干气中乙烯回收利用的新途径
加工工艺 石油炼制与化工 PETROLEUMPROCESSINGANDPETROCHEMICALS 2014年12月 第45卷第12期 收稿日期:2014﹣05﹣27;修改稿收到日期:2014﹣07﹣18。 作者简介:姚日远,硕士,高级工程师,从事石油化工生产及技 术管理工作。获中国石化科技进步三等奖1项,江苏省科技 成果1项,扬州市科技进步三等奖1项,国内外发表论文10余 篇,江苏省“333”科技带头人。 通讯联系人:姚日远,E﹣mail:yaory.jsyt@sinopec.com。 催化裂化干气中乙烯回收利用的新途径 姚日远 (扬州石化有限责任公司,江苏扬州225000) 摘要:介绍了一种催化裂化干气中乙烯回收利用的新途径。该技术在扬州石化有限责任公司工业应用 后,取得了较好的经济效益。实际运行数据表明,干气中乙烯的转化率达到95.41%以上,目的产品汽油的硫质量分数仅为6 g∕g、研究法辛烷值高达114,是较好的汽油调合组分。该技术的不足之处是汽油选择性偏低,仅为37.64%。此外,针对目前装置运行状况,提出了改进催化剂性能等建议。 关键词:催化裂化干气乙烯芳烃 干气是炼油厂的副产品,主要包括催化裂化干气、焦化干气、重整干气、加氢裂化干气以及常减压蒸馏装置的不凝气等。其中,催化裂化干气产量大,乙烯和轻烃的含量高,极具利用价值。我国炼油企业的干气绝大部分来源于催化裂化气体,全国已建成投产的催化裂化装置年加工量超过150Mt[1],按干气产率(w)4%~6%计,干气年产量超过6.0Mt,其中乙烯产量0.6~1.0Mt,这些乙烯是化工厂的宝贵原料。目前干气的利用途径大多为提取氢气[2]、制乙苯[3]、深冷分离回收乙烯[4]等。但对于小型炼油厂,制乙苯以及深冷分离等均不经济。所以,通常都送入瓦斯管网作燃料气用,有些甚至放入火炬烧掉,浪费资源。随着石油资源日益枯竭,其价格不断上涨,开源节流变得十分重要,若将干气中的轻烃加以合理利用,将产生巨大的经济效益。 为了在投资不高、流程简单、操作费用较低的情况下,将干气中的乙烯等烯烃资源转化为高附加值的石化产品,扬州石化有限责任公司(以下简称扬州石化)采用专有技术将干气中的乙烯和少量的丙烯、丁烯通过低聚、环化等反应转化成以芳烃为主的轻质燃料油。该装置投资920余万元,于2012年4月2日建成并一次开车成功,设计处理量20kt∕a,目前装置运行平稳。 1工艺简介 1·1原理 装置使用的催化剂是改性分子筛催化剂,该催化剂是金属改性的酸性催化剂。原料干气中的C2,C3,C4等烯烃分子,在酸性催化剂表面的酸中心上依照正碳离子机理进行齐聚、叠合、环化、异构化、芳构化等一系列化学反应,生成富含芳烃等的汽油组分,以及少量燃料油组分,完成乙烯等低碳烯烃的回收利用。该催化剂具有可重复再生、抗水、抗硫等优点。 1·2工艺流程 干气回收利用工艺原则流程示意如图1所示。原料干气进入缓冲罐,与反应后的贫气一起进入吸附器,吸附其中的碱性组分,然后一部分经二级换热进入加热炉,升温到200℃以上从反应器顶部进入,另一部分未经加热的干气从反应器中部注入,通过分段床层进行反应。反应产物经过 与 图1干气回收利用工艺原则流程示意 1—缓冲罐;2—吸附器;3—加热炉;4,5—反应器;6—柴油塔; 7—油水分离器;8—捕油器;9—压缩机;10—缓冲罐
干气制乙烯说明书
中石化齐鲁分公司 催化干气回收乙烯项目 方案设计 山东三维石化工程股份有限公司 二○○九年三月 1 项目名称、建设地点、承办单位及项目负责人 1.1 项目名称:齐鲁石化公司催化干气回收乙烯项目 1.2 建设地点:齐鲁石化公司胜利炼油厂内 1.3 承办单位:齐鲁石化公司 1.4 承办单位负责人:孙振光 2 项目提出的必要性与建设的有利条件 2.1 乙烯生产的原料费用约占成本的 70%,乙烯裂解的主要原料石脑油的价格一直居高不下,因此采用廉价的代替原料可有效的降低乙烯生产成本。利用炼油厂副产的催化干气经过油吸收工艺生产乙烯、丙烯是油化一体化、高效利用炼厂资源的重要途径。 2.2 该项目将干气中附加值较高的成品――乙烯提浓后送往烯烃厂裂解车间,目前齐鲁石化分公司乙烯裂解原料尚不能自给需要外购,每年公司需花费大量运费,该装置建成投产后每年将提供约5.23万吨乙烯裂解气,将节省大量裂解原料和运费,可创造可观的经济效益。 2.3 催化干气回收乙烯装置的原料是胜利炼油厂的两套催化装置的脱后干气,经过乙烯提浓后,作为半成品送至齐鲁石化烯烃厂裂解车间进入后续工序处理。两套催化装置脱后干气流量~1 3.5/h,乙烯含量19.69%(wt),干气流量稳定,由两套催化管输供应十分便利。催化干气回收乙烯装置采用由中国石油化工股份有限公司北京化工研究院 (以下简称 BRICI)和齐鲁分公司共同开发的油吸收工艺,该技术成熟、可靠。 催化干气回收乙烯装置拟建于北区第二常减压装置北侧,与拟建的S-zorb装置组成联合装置,该区域总图布置合理、运输便利,而且装置公用工程可就近依托胜利炼油厂相应设施;催化干气回收乙烯装置的建设、投产,取得好的经济效益是完
天然气制合成气的新技术
天然气制合成气的新技术 摘要:伴随煤炭石油等能源的日益枯竭,天然气等新型能源进入到人们的视野当中,如何更有效的利用天然气成为关键。本文简单介绍了国内外天然气的化工利用情况,并介绍了天然气为原料制成的合成物,最后分析了天然气制合成气的新技术。 关键词:天然气催化工艺 天然气作为一种新兴重要能源,一般情况下不能直接利用,在合成燃料前会先合成气,而在整个天然气转化为使用能源的过程当中,合成气的步骤耗费相当大的成本,能够占到全程的百分之六十左右,因此天然气制合成气工艺的改善是一个巨大挑战。近年来国外发展了自然重整,非催化部分氧化和联合重整等制合成气新工艺。 一、国内外天然气的化工利用 上世纪初西方国家首次铺设了天然气管道为化工使用,自此天然气成功加入了世界能源的行列,各个国家开始了天然气的开发使用,并在相当长时间段内有着飞速发展,从1940年发展速度的开始提升至1960年达到鼎盛,天然气利用技术趋于成熟,转化成各类能源物,一定程度上促进了各国的发展。至70年代,由于石油化工廉价化,天然气研发的脚步减慢,但仍有着较为稳定的发展速度。目前,石油供给短缺,价格不断上升,世界石油局势紧张,而天然气作为一种新兴能源,处于开发的初级阶段,且储量巨大,国际能源机构认为,天然气产量增加,并且今后将会作为主要能源之一。 作为21世纪新兴能源,天然气合成燃料的工艺备受关注,不断得到改善,被应用到工业化工中去。企业中的天然气转化工艺,可分为以下两种方法: 1.直接转化法 在制作乙烯过程中,当利用甲烷作氧化剂时,可以选择氧化制甲醇和甲醛。 2.间接转化法 天然气制燃料常用的就是间接转化法,利用转化器将天然气进行转化,合成的合成气,应用于工业化工上,将之彻底转变成燃料、化肥等。 二、以天然气为原料的化工合成物 1.合成氨 氨肥是化肥工业中的主导产品,世界各国对化工氨需求量大,氨的产量直接
中国现有乙烯装置及其技术水平.doc
1.中国现有乙烯装置多少套? 2012年,我国乙烯工业产能快速增长,装置大型化、炼化一体化程度进一步提升,但开工率有所下降,进口量有所增加,总体走势呈以下三个特点:一是增速加快,乙烯总产能突破1700万吨/年。建设大型化装置、发展规模经济,是国内外乙烯工业实现低成本发展战略的有效途径。统计数据显示,100万吨/年乙烯与50万吨/年乙烯装置相比较,吨成本可降低25%. 截至2012年底,我国乙烯新增产能140万吨,总产能达1709.5万吨,比上年增长8.9%.一批新建和改扩建乙烯项目快速推进,其中大庆石化120万吨/年乙烯改扩建工程和抚顺石化80万吨/年乙烯装置,均实现一次开车成功,四川、武汉等地的煤制烯烃,以及浙江宁禾、陕西延长榆林等多个煤制烯烃项目在稳步推进中。 2012年,我国共有24家乙烯生产企业、有32套乙烯装置(其中石脑油基制乙烯装置28套),装置平均规模约52.4万吨/年,而2005年装置的平均规模仅为39.5万吨/年。若不计算煤制烯烃和甲醇制烯烃装置,蒸汽裂解装置共有29套,蒸汽裂解装置平均规模近60万吨/年,高于世界52万吨/年的平均规模。我国产能在80万吨/年以上的装置数量也有大幅增长。截至2012
年,共有10套80万吨以上的蒸汽裂解装置,合计产能达988万吨/年,占总产能的58.9%。单套最大规模为上海赛科119万吨/年的乙烯装置。乙烯生产企业平均规模74.1万吨/年,比2011年的68万吨/年增加了6.1万吨/年;乙烯装置平均规模57万吨/年,比2011年的56.1万吨/年上升了0.9万吨/年,高于世界52万吨/年的平均规模。 若不计算煤制烯烃和甲醇制烯烃装置,我国石脑油裂解乙烯装置的平均规模为59.2万吨/年,单套规模达80万吨/年以上的装置有8套,合计产能774万吨/年,占总产能的45%;单套规模60万吨/年以下的装置降至12套,产能合计263.5万吨/年,占总产能的16%. 据美国《油气杂志》最新统计数据显示,当前全球十大乙烯生产商排名情况如下: 排名第一的是埃克森美孚公司,共有19套装置,总产能1251.5万吨/年; 排名第二的是陶氏化学,共有18套装置,产能1214.48万吨/年; 排名第三的是沙伯公司,共有13套装置,产能1084.22万吨/年; 排名第四的是壳牌化学,共有13套装置,产能935.84万吨/年;
炼厂干气制氢工艺流程介绍
干气制氢工艺流程 (一)造气单元 1、进料系统 来自装置外的焦化干气进入原料气缓冲罐,经原料气压缩机压缩至3.2MPa(G)后进入原料气脱硫部分。 2、脱硫部分 进入脱硫部分的原料气经原料气-中变气换热器或开工加热炉(开工时用)升温到230℃左右进入加氢反应器,在其中原料中的不饱和烃通过加氢转化为饱和烃类,床层温度升至380℃左右,此外通过加氢反应,原料中的有机硫转化为无机硫,然后进入氧化锌脱硫反应器脱除硫化氢和氯化氢。经过精制后的气体总硫含量小于0.5PPm,氯化氢含量小于1 PPm,进入转化部分。 3、转化部分 精制后的原料气按水碳比3.5与自产的3.5MPa水蒸汽混合,再经转化炉对流段予热至500℃,进入转化炉辐射段。在催化剂的作用下,发生复杂的水蒸汽转化反应。整个反应过程是吸热的,所需热量由分布在转化炉顶部的气体燃料烧嘴提供,出转化炉840℃高温转化气经转化气蒸汽发生器换热后,温度降至360℃,进入中温变换部分。 4、变换部分 来自转化气蒸汽发生器约360℃的转化气进入中温变换反应器,在催化剂的作用下发生变换反应,将变换气中CO含量降至3%左右。中变气经原料气-中变气换热器、中变气蒸汽发生器、中变气-脱氧水换热器、中变气-除盐水换热器进行热交换回收大部分余热后,再经中变气空冷器冷却至40℃,并经分水后进入中变气PSA单元。 5、热回收及产汽系统 来自装置外的脱盐水与来自酸性水气提塔的净化水混合并经中变气-除盐水换热器预热后进入除氧器。除氧水经锅炉给水泵升压后,再经中变气-脱氧水换热器预热后进入中压汽包。
锅炉水通过自然循环的方式分别经过转化炉对流段的产汽段及转化气蒸汽发生器产生中压蒸汽。所产生的中压蒸汽在转化炉对流段蒸汽过热段过热至440℃离开汽包。一部分蒸汽作为工艺蒸汽使用;另一部分进入全厂中压蒸汽管网。 (二)中变气PSA单元 来自造气单元压力约2.1MPa(G)、温度40℃中变气进入界区后,自塔底进入吸附塔中正处于吸附工况的塔(始终同时有两台),在其中多种吸附剂的依次选择吸附下,一次性除去氢以外的几乎所有杂质,获得纯度大于99.9 的产品氢气,经压力调节系统稳压后送出装置。 当吸附剂吸附饱和后,通过程控阀门切换至其它塔吸附,吸附饱和的塔则转入再生过程。在再生过程中,吸附塔首先经过连续四次均压降压过程尽量回收塔内死空间氢气,然后通过顺放步序将剩余的大部分氢气放入顺放气罐(用作以后冲洗步序的冲洗气源),再通过逆放和冲洗两个步序使被吸附杂质解吸出来。逆放解吸气进入解吸气缓冲罐,冲洗解吸气进入解吸气缓冲罐,然后经调节阀调节混合后稳定地送往造气单元的转化炉作为燃料气。
(精选文档)干气制乙烯说明书
中石化齐鲁分公司催化干气回收乙烯项目 方案设计 山东三维石化工程股份有限公司 二○○九年三月
1 项目名称、建设地点、承办单位及项目负责人 1.1 项目名称:齐鲁石化公司催化干气回收乙烯项目 1.2 建设地点:齐鲁石化公司胜利炼油厂内 1.3 承办单位:齐鲁石化公司 1.4 承办单位负责人:孙振光 2 项目提出的必要性与建设的有利条件 2.1 乙烯生产的原料费用约占成本的 70%,乙烯裂解的主要原料石脑油的价格一直居高不下,因此采用廉价的代替原料可有效的降低乙烯生产成本。利用炼油厂副产的催化干气经过油吸收工艺生产乙烯、丙烯是油化一体化、高效利用炼厂资源的重要途径。 2.2 该项目将干气中附加值较高的成品――乙烯提浓后送往烯烃厂裂解车间,目前齐鲁石化分公司乙烯裂解原料尚不能自给需要外购,每年公司需花费大量运费,该装置建成投产后每年将提供约5.23万吨乙烯裂解气,将节省大量裂解原料和运费,可创造可观的经济效益。 2.3 催化干气回收乙烯装置的原料是胜利炼油厂的两套催化装置的脱后干气,经过乙烯提浓后,作为半成品送至齐鲁石化烯烃厂裂解车间进入后续工序处理。两套催化装置脱后干气流量~1 3.5/h,乙烯含量19.69%(wt),干气流量稳定,由两套催化管输供应十分便利。催化干气回收乙烯装置采用由中国石油化工股份有限公司北京化工研究院 (以下简称 BRICI)和齐鲁分公司共同开发的油吸收工艺,该技术成熟、可靠。 催化干气回收乙烯装置拟建于北区第二常减压装置北侧,与拟建的S-zorb装置组成联合装置,该区域总图布置合理、运输便利,而且装置公用工程可就近依托胜利炼油厂相应设施;催化干气回收乙烯装置的建设、投产,取得好的经济效益是完全可能的。 3 项目建设的主要内容 3.1 该项目主要包括一套催化干气回收乙烯装置;装置公用工程依托于胜利炼油厂相应设施。 3.2 本装置控制室与S-zorb装置共用,装置配电部分由第二常减压装置配电室内
天然气制备合成气
天然气制备合成气 天然气作为一种清洁、环境友好的能源,越来越受到广泛的重视。天然气作为一种清洁、环境友好的能源,越来越受到广泛的重视。制合成气是间接利用天然气的重要步骤,也是天然气制氢的基础,充分了解天然气制合成气 的工艺与催化剂对于我们进一步研究天然气的利用将有很大帮助。天然气中甲烷含量一般大于90%,其余为小量的乙烷、丙烷等气态烷烃,有些还含有少量氮和硫化物。其他含甲烷等气态烃的气体,如炼厂气、焦炉气、油田气和煤层气等均可用来制造合成气。 目前工业上有天然气制合成气的技术主要有蒸汽转化法和部分氧化法。本文主要对蒸汽转化法进行具体的描述,并具体介绍此工艺的发展趋势。 蒸气转化法 蒸气转化法是目前天然气制备合成气的主要途径。蒸汽转化法是在催化剂存在及高温条件下,使甲烷等烃类与水蒸气反应,生成CO H 、2等混合气,其主反应为: 2243H CO O H CH +=+,mol /206298KJ H =?Θ 该反应是强吸热的,需要外界供热。因为天然气中甲烷含量在90%以上,而甲烷在烷烃中热力学最稳定,其他烃类较易反应,因此在讨论天然气转化过程时,只需考虑甲烷与水蒸气的反应。 甲烷水蒸气转化反应和化学平衡 甲烷水蒸气转化过程的主要反应有: 2243H CO O H CH +?+,mol /206298KJ H =?Θ 222442H CO O H CH +?+,mol /165298KJ H =?Θ 222H CO O H CO +?+,mol /9.74298KJ H =?Θ 可能发生的副反应主要是析碳反应,它们是: 242H C CH +?,mol /9.74298KJ H =?Θ 22CO C CO +?,mol /5.172-298KJ H =?Θ O H C H CO 22+?+,mol /4.131-298KJ H =?Θ
高密度聚乙烯生产工艺开发进展
高密度聚乙烯生产工艺开发进展 概述世界聚乙烯工业生产和消费现状,了解高密度聚乙烯(HDPE)生产工艺的最新进展,提出本地该行业发展建议。 标签:聚乙烯;生产工艺;现状 高密度聚乙烯(HDPE)是一种不透明白色腊状材料,密度比水小,柔软而且有韧性,被广泛应用于制备诸如片材挤塑、薄膜挤出、管材或型材挤塑,吹塑、注塑和滚塑等。 在聚乙烯生产工艺技术领域,一直是多种工艺并存,各展其长。目前并存的液相法工艺有Nova公司的中压法工艺、Dow化学公司的低压冷却法工艺和DSM 公司的低压绝热工艺。应用最为广泛的浆液法工艺是科诺科菲利浦斯、索尔维公司的环管工艺和赫斯特、日产化学、三井化学的搅拌釜工艺。气相法工艺主要有Univation公司的Unipol工艺、BP公司的Innovene工艺和Basell公司的Spherilene 工艺。近年来,气相法由于流程较短、投资较低等特点发展较快,目前的生产能力约占世界聚乙烯总生产能力的34%,新建的LLDPE装置近70%采用气相法技术。近年来,在各工艺技术并存的同时,新技术不断涌现。其中冷凝及超冷凝技术、不造粒技术、共聚技术、双峰技术、超临界烯烃聚合技术以及反应器新配置等新技术的开发,极大地促进了世界聚乙烯工业的发展。 1 冷凝及超冷凝技术 冷凝及超冷凝技术是UCC、Exxon化学和BP公司开发的,是指在一般的气相法PE流化床反应器工艺的基础上,使反应的聚合热由循环气体的温升和冷凝液体的蒸发潜热共同带出反应器,从而提高反应器的时空产率和循环气撤热的一种技术。冷凝操作可以根据生产需要随时在线进行切换,使装置可以在投资不需要增加太大的情况下大幅度提高装置的生产能力,装置操作的弹性大,使得该技术具有无可比拟的优越性。通过采用该技术不仅将单线最大生产能力从22.5wt/y 提高到45wt/y年以上,而且进一步降低了单位产品的投资和操作费用,操作稳定性也得到了进一步提高。国外已有大量采用冷凝和超冷凝技术对气相法PE装置扩能的实绩,最高扩能达到原有能力的2.5倍以上。我国扬子石化公司、天津石化公司、广州石化公司以及吉林石化公司、中原石化有限责任公司、新疆独山子石化公司等的聚乙烯装置采用该技术也取得扩能成功。 2 不造粒技术 随着催化剂技术的进步,现在已出现了直接由聚合釜中制得无需进一步造粒的球形PE树脂的技术。直接生产不需造粒树脂,不但能省去大量耗能的挤出造粒等步骤,而且从反应器中得到的低结晶产品不发生形态变化,这样有利于缩短加工周期、节省加工能量。Montell公司的Spherilene工艺采用负载于MgCl2上的钛系催化剂,由反应器直接生产出密度为0.890-0.970g/cm3的PE球形颗粒,
炼厂干气中乙烯回收和利用技术进展
炼厂干气中乙烯回收和利用技术进展 炼厂干气主要来自原油的二次加工,如催化裂化,热裂化,延迟焦化等,其中催化裂化的干气量最大,产率也最高[1,2]。干气中含有氢气、氮气、甲烷、乙烯、乙烷等,其中催化裂化干气中乙烯的含量约占15%[3]。过去因为没有合适的分离回收和综合利用技术,大多数干气当作为燃料气使用或放火炬烧掉,造成了极大的资源浪费和环境污染[4]。据统计,随着炼油企业的发展,国内催化裂化装置能力已经达到93Mt/a,每年生产的干气产量约为4.14Mt,其中含有乙烯730Kt左右[5]。若炼厂干气回收轻烃技术能全面推广,每年可以节约用于生产乙烯的轻质油4.15Mt,创造效益上百亿元[6]。因此,回收利用炼厂干气已经成为炼油企业降低乙烯生产成本和实现资源有效利用的重要手段。 目前,炼厂干气中乙烯回收利用技术分为两大类:一是通过对干气的精制,然后对干气中的乙烯进行浓缩,最后通过分离回收得到聚合级的乙烯;二是用干气作为原料,利用其中的稀乙烯,直接生产乙苯、环氧乙烷、丙醛等。本文重点对国内外回收利用干气技术进行了综述。 1 炼厂干气中乙烯分离回收技术 从炼厂干气中提取乙烯的技术主要有深冷分离法、吸收分离法、水合物分离法、吸附分离法和膜分离法等。其中水合物分离法是新出现的分离方法,膜分离法正处于实验室阶段或工业试验阶段,而深冷分离法,吸收分离法和吸附分离法已经成熟并实现工业化[7]。下面分别做以介绍。 1.1深冷分离法 深冷分离法是一种已经相当成熟的技术。早在20世纪50年代,人们就开发了常规深冷分离技术[8,9,10]。该方法是一种低温的分离工艺,利用原料中各个组分的相对挥发度的不同,通过气体透平膨胀制冷,在低温下将干气中各个组分按工艺要求冷凝下来,然后利用精馏法将其中的各类烃按照蒸发温度的不同逐一进行分离。 但由于常规深冷分离工艺能耗大,人们不断对其进行改进,最突出的是利用分凝分馏器进行分离。分凝分馏器是美国空气产品公司的设计专利;九十年代初,美国Stone&Webster 公司将其应用于烃气分离工艺中,形成了以分凝分馏器为核心的第一代ARS (Advanced Recovery System)技术[11]。ARS技术由原料预处理、产品选择性分馏和深冷回收等过程组成,其工艺流程见图1。干气经净化、干燥和压缩后进入分凝分馏器。分凝分馏器实际是一个带回流的板翅式换热器,其设计与普通板翅式换热器不同,它具备宽敞的气液通道,底部设一气液分离罐,多股冷物流通过分凝分馏器为其提供冷量。被回收的气体在通道内自下而上流过,越往上其被冷却的温度越低,一部分气体在通道壁上冷凝,冷凝液受重力作用向下流,与气体逆向接触,气体与液膜间既传热又传质,起到了分凝分馏的作用(其分离效果一般相
国内外天然气制合成气的技术研究进展
国内外天然气制合成气技术进展 徐俊忠 (西南石油大学化学化学化工学院,四川成都610500) 摘要:本文综述了国内外天然气制合成气技术的研究进展,主要介绍了甲烷部分氧化技术(包括固定床工艺、流化床工艺和陶瓷膜工艺),甲烷临氧化制备合成气技术(包括甲烷临氧CO 2重整制合成气、甲烷临氧自热三重整制合成气和甲烷临氧水蒸气重整制合成气),水蒸气转化制备合成气,CO 2转化法制合成气,自热式转化法制合成气,以及新出现的激光促进表面反应技术和等离子体技术。 关键词:天然气,制备,合成气,技术进展 T hermal cracking gas of h ydrocarbon separation method were reviewed Xu Junzhong (College of Chemistry and Chemical Engineering,Southwest Petroleum University,Chengdu 610500) Abstract:In the paper,the progress on preparation of synthetic gas from natural gas using different processes were described.methane partial oxidation process was introduced(Including fixed-bed process,fluidized-bed process and ceramic membrane process),the preparation of methane oxidation syngas technology(autothermal CO 2reforming(ATR-CO 2),triple-reforming of methane and autothermal H 2O reforming (ATR-H 2O)),water vapor into syngas preparation,CO 2into syngas preparation,self-heating transformation ssyngas preparation,the recent discovery of laser surface reaction to promote technology and plasma technology. Key words :Natural gas,preparation,synthetic gas,technology progress 1引言 根据17届世界石油会议提供的调查数据,全球现已探明的天然气储量为3141071.1m ×,按油当量计这与全球探明的石油储量十分接近。但因石油的储采比天然气的储采比高,预计石油资源40年后就会枯竭,天然气资源可维持约60年。我国在2005年探明的天然气储量约为312103m ×,我国天然气的人均占有量仅为全球的十分之一。对我国来讲,如何好喝的利用这些珍贵的天然气资源具有十分重要的意义。[1]
乙烯装置技术水平分析及节能措施
乙烯装置技术水平分析及节能措施 近年来,随着新的乙烯装置建设及老装置的扩能改造,新技术、新工艺及相关系统的设计优化的应用,我国乙烯装置能耗显著下降,随着国家“节能、降耗、减排”的要求提高,作为石油工企业耗能大户的乙烯装置将面临更大的节能降耗压力。乙烯企业应严格控制工艺参数、工况条件,保证装置平稳运行、延长运行周期;通过用能数据、产品收率的对比分析以及对工艺单元的模拟计算,提出具体节能增效的措施。乙烯企业应减少非计划停工事故发生,并结合装置特点逐步降低负荷、逐台有序停炉,尽可能回收物料,实现乙烯装置的无排放开停工。 标签:乙烯装置;综合能耗;节能措施 1乙烯装置节能增效措施的研究 1.1裂解炉系统优化 原料的裂解性能在很大程度上决定了乙烯生产的能耗水平,但乙烯装置原料的优化和其上游炼厂的配制有很大关系。大炼油小乙烯的配制,乙烯装置的原料就有很大的灵活性,相反小炼油或自身没有炼厂的乙烯装置其对原料就没有多少选择的余地。我国优化裂解原料的重要措施就是实行“煉油化工一体化”,采用“宜烯则烯,宜芳则芳”的原则,它有利于炼厂和乙烯装置之间的原料互供和优化。 1.2装置精细化管理和无排放开停工 创建节约型企业是企业增强核心竞争力的根本要求,石油化工企业通过精细化管理来实现节能增效具有重要的现实意义。乙烯生产具备流程长、设备多、工艺机理复杂等特点,装置工艺指标约有上百个关键指标,因此在乙烯实际生产过程中,实施精细化管理、不断提升管理水平显得尤为重要。乙烯企业应严格控制工艺参数、工况条件,例如裂解炉单元应加强烟道气氧含量、炉出口温度、炉管出口温度偏差、排烟温度及燃烧状况等工艺指标的管理,保证装置平稳运行、延长运行周期,为装置节能增效打下坚实基础。 例如独山子乙烯装置通过进细化管理和操作,裂解炉出口温度偏差保持在±2℃之间,双烯收率平均提高0.59%,经济效益显著。同时应对重点耗能单元制订能耗消减措施,对易波动的工艺指标实行跟踪监控;通过用能数据的对比分析以及产品收率的对比评估,以及应用如Aspon等化工辅助模拟软件对工艺单元进行模拟计算,提出具体节能增效的措施。乙烯装置开停工是一个物耗、能耗较大的操作,传统开工方式一般沿流程从前到后,将不合格物料放火炬,对经济效益和周边环境产生很大的影响;停工操作程序是将裂解炉整体退料、压缩机组整体停车,时间短且操作快,但大量物料留在系统管线中造成浪费又增加了火炬排放。尤其是对目前新设计装置能力较大,如采用传统的开停工方式物料损失量更大,其弊端表现的更为明显,因此减少非计划停工事故发生,实现乙烯装置的无排放开停工可降低加工损失率、降低成本、提高综合效益。
炼厂干气利用的现状
炼厂干气利用的现状 发布时间(2007-5-30 10:00:27)炼厂干气利用的现状 炼厂干气主要来自于原油的二次加工,如催化裂化、热裂化、延迟焦化等,其中催化裂化的干气量最大,产率最高。目前,我国有催化裂化装置100多套。干气产量212万t/a,到本世纪末,干气产量将达到452万t/a~634万t/a。干气中含有氢气、甲烷、乙烷、乙烯等组份,其中乙烯含量占质量的12%。国内炼厂催化裂化干气基本用作工业燃料气、民用燃料气,其余的则放火炬烧掉,造成严重的资源浪费。随着我国炼油工业原油深度加工的迅速发展,副产的催化裂化干气也在大量增加。炼厂干气是石油化工的一种重要资源,如何充分利用这部分宝贵的化工原料,开发新的综合利用工艺,提高炼油厂的综合效益,已引起人们的普遍关注。另外由于环境保护的要求,绝大多数的炼油厂已有简单的脱硫处理装置,每克干气中硫含量一般在200μg以下,这为干气的进一步加工利用创造了有利的条件。 2. 国内外催化裂化干气回收利用技术 80年代,国外炼厂部分或全部采用炼厂气为原料的乙烯生产能力约为330万t/a,占世界乙烯总能力的6.4%。但只有三个厂是完全以炼厂气为原料生产乙烯的,即阿尔科化学公司的威明厂(4.5万t/a)、考尔斯登公司的格罗伟斯厂(0.9万t/a)、联合碳化物公司的托兰斯厂(7.5万t/a),其余大部分是用炼厂气作为乙烯的一种补充原料。 2.1干气中乙烯回收技术 国外十分重视回收炼厂干气中乙烯的技术开发,除深冷分离法外,近十年来又研制成功双金属盐络合吸收法、溶剂抽提法、膨胀机法、吸附法等项技术。国内从气体中提浓乙烯的方法有四种,其中深冷分离法和中冷油吸收法在工业中常被采用,络合吸收法和吸附法尚处在实验阶段。国内目前炼厂干气中较成熟的乙烯提浓技术有中冷油吸收和深冷分离工艺,但尚无工业化装置。 2.1.1 深冷分离工艺 早在20世纪50年代,人们就开发出了深冷分离工艺。这是一种低温分离工艺,利用原料中各组分相对挥发度的差异,通过气体透平膨胀制冷,在低温下将干气中各组分按工艺要求冷凝下来,然后用精馏法将其中的各类烃依其蒸发温度的不同逐一加以分离。该工艺是美国Mobil公司和AirProducts公司共同开发的,并已在1987年投入工业化生产。采用该工艺,乙烯收率可达90%~98%,乙烷收率99%,重烃收率100%,投资可降低25%以上。 近年来出现的深冷分凝器工艺(cryogenicdephlegmatorprocess)适于回收炼厂干气中的烯烃。采用这种将热传导与蒸馏结合起来的高效分离技术,提高了深冷分离的效果,可使FCC(fluidcatalyticcracking)干气中的烃类回收率达到96%~98%,比常规的深冷分离技术节能15%~25%,经济效益显著。利用深冷分离法分离干气,原料中低沸点组分的浓度直接影响产品的纯度,但对回收率影响不大。 ARS技术是美国石伟工程公司(SWTC)开发的先进的回收技术,主要用于从FCCT和DCC 干气中提纯乙烯,还可用于分离含有乙烯、丙烯和丁烯的气体,所得乙烯、丙烯均可达到聚合级。它主要是应用膨胀制冷过程,产生足够冷量,在特殊结构的局部冷凝分馏器中进行冷量的间接传递,以形成局部冷凝,以及在分馏器的底部特殊通道中送进工艺蒸气与冷液逆向流动,以形成烯烃分离条件。其流程特点是:(1)以最小的消耗,得到最大量的烯烃;(2)操作灵活,对进料要求不太严格;(3)分离较重馏份更有其独特之处。该工艺
天然气制备合成气
天然气制备合成气 天然气作为一种清洁、环境友好的能源,越来越受到广泛的重视。天然气作为一种清洁、环境友好的能源,越来越受到广泛的重视。制合成气是间接利用天然气的重要步骤,也是天然气制氢的基础,充分了解天然气制合成气的工艺与催化剂对于我们进一步研究天然气的利用将有很大帮助。天然气中甲烷含量一般大于90%,其余为小量的乙烷、丙烷等气态烷烃,有些还含有少量氮和硫化物。其他含甲烷等气态烃的气体,如炼厂气、焦炉气、油田气和煤层气等均可用来制造合成气。 目前工业上有天然气制合成气的技术主要有蒸汽转化法和部分氧化法。本文主要对蒸汽转化法进行具体的描述,并具体介绍此工艺的发展趋势。 蒸气转化法 蒸气转化法是目前天然气制备合成气的主要途径。蒸汽转化法是在催化剂存在及高温条件下,使甲烷等烃类与水蒸气反应,生成 H2、CO等混合气,其主反应为: CH4 + 出0 =C0+3战,人H% =206KJ/mol 该反应是强吸热的,需要外界供热。因为天然气中甲烷含量在 90%以上,而甲烷在烷烃中热力学最稳定,其他烃类较易反应,因此在讨论天然气转化过程时,只需考虑甲烷与水蒸气的反应。 甲烷水蒸气转化反应和化学平衡 甲烷水蒸气转化过程的主要反应有: CH4 +日2。= CO+3H2,A^29^206KJ/mol CH4+2H2O= CO2+4H2,AH % =165KJ/mol CO + H 2O u CO2+ H2,△H % = 74.9KJ / mol 可能发生的副反应主要是析碳反应,它们是: CH4=C+2H2,也Hd98 =74.9KJ/mol 2CO U C+CO2,心Hd98 =-172.5KJ/mol CO + H2U C + H2O,心H 色98 =-131.4KJ /mol
国内外乙烯生产技术进展与评述
生产情况 1.1 世界 截至2007年1月1日,世界乙烯的总生产能力约为11757.52万t/a,开工率约为91%。预计到2010年末,世界乙,烯产能将上升到1.56亿t/a,开工率将下降到86%,生产能力的增长主要来自中东及亚太地区。 2006年世界十大乙烯生产商的产能情况见表1,世界十大乙烯生产厂见表2。 表1 世界十大乙烯生产商
注:截至2007年1月1日。 表2 世界十大乙烯生产厂
注:截至2007年1月1日。 全球乙烯发展的重心将由墨西哥湾转移到亚洲和中东,尤其是具有廉价原料优势的中东。尽管目前美国、欧洲和日本占世界乙烯总产能的60%,但在2010年前这些地方将不会有新建乙烯装置投产,而某些装置可能将永久性关闭,剩下的装置将集中力量进行脱瓶颈改造。到2012年,中东地区的乙烯生产能力将和北美持平,我国大陆、新加坡、印度及中国台湾将有多套乙烯装置投产。 表3为世界主要地区乙烯产能分布及增长情况。 表3 世界各地区乙烯生产能力
1.2 国内 随着中海油壳牌乙烯项目的建成投产,2006年我国乙烯的生产厂家达到19家,装置达到23套。截至2006年底,我国乙烯产能已经达到984.5万t/a,比2005年增长25%;2006年乙烯产量达922.6,较2005年的754.1万t增加22.3%。其中,中国石油生产乙烯206.8万t,同比增长9.6%;中国石化共生产乙烯633.1万t,同比增长15.19%;中海油生产乙烯64.6万t。装置的开工率约为97%,
大大高于世界平均水平。我国乙烯产能的增加主要来自于中海油壳牌乙烯项目投产、中国石化茂名乙烯扩能以及兰州乙烯扩能。 2006年,中国石油吉林石化、兰州石化的两套70万t/a乙烯装置扩能顺利完成;中海油壳牌项目建成投产;中国石化与国外公司合资的上海赛科石化增产乙烯33.6万t,南京扬巴乙烯增产30.6万t。 表4为2006年我国乙烯装置生产能力,表5为各公司2006年比2005年乙烯产量增长情况。 表4 2006年我国主要乙烯装置生产能力
炼厂干气作为制氢原料的技术探讨与工业应用
炼厂干气作为制氢原料的技术探讨 与工业应用 彭成华(北京海顺德钛催化剂有限公司北京100176) 摘要:对炼厂干气作为制氢装置原料的可行性进行了分析,针对焦化干气和催化干气作为制氢原料中存在有机硫和烯烃等问题提出了不同加氢处理工艺以及与此相配套的低温性能良好的加氢催化剂。工业运转数据表明,北京海顺德钛催化剂有限公司研发的新一代加氢催化剂T205A-1/T205,具有初活性温度低、烯烃饱和性能好、抗结炭性能好等优点,可以很好的处理焦化干气和/或催化干气,使之满足水蒸气转化催化剂对原料的要求。 关键词:制氢原料炼厂干气加氢精制工业应用 1.前言 随着世界石油资源重质化、劣质化趋势的加剧以及各项环保法规的日益严格,加氢技术在原油二次加工过程中的应用日益广泛,相应的氢气需求也迅速增加。而在加氢装置的加工成本中,氢气成本约占50%,因此降低加氢成本,提供更多廉价的氢气已经成为发展加氢技术,提高炼油企业综合经济效益的关键。 目前,蒸汽转化制氢工艺由于其技术可靠、流程简单、投资低廉、操作简便,而在制氢装置中占主导地位。对此工艺来讲,原料消耗在制氢成本中占有很大比例,因此如何选用合适的原料以降低氢气生产成本,成了制氢装置首要考虑的问题。 本文探讨了炼油企业中常常作为燃料用的低廉的炼厂干气作为制氢原料的可行性,并列举了相应的工业运转实例。 2.炼厂干气作为制氢原料的技术探讨 2.1炼厂干气性质比较与分析 炼厂干气是指原油加工过程中副产的各种尾气,包括催化裂化干气、焦化干气、催化重整气、热裂解气、高压加氢裂化尾气等。各种炼厂干气的组成变化较大,表1列出了炼厂干气的典型性质。 从表1数据可以看出,加氢裂化干气、加氢精制干气和重整干气基本不含有机硫和烯烃,经过湿法脱硫后硫化氢的含量一般也小于20μg·g-1,是制氢的良好原料。焦化干气和催化裂化干气中烯烃和有机硫的含量较高,必须经过加氢处理,降低烯烃和硫含量,才能作为制氢装置的原料。 焦化气体是原油经减压蒸馏后的渣油经常压高温热裂化、聚合、焦化反应的气体产物,所以烯烃和有机硫的含量较高。以往,焦化装置排出的富气经压缩机升压后用柴油吸收,回收其中C5以上的轻汽油组分,未被冷凝吸收下来的组分称为焦化干气。焦化干气中含有一定的烯烃,必须经过加氢处理,使烯烃含量降到1v%以下才能满足转化催化剂的要求;其次焦化干气中有机硫含量较高,硫的形态比较复杂,因此必须采取能彻底脱除有机硫的脱硫技术,以满足转化催化剂对总硫含量小于0.5μg·g-1的要求。 催化裂化干气是炼厂的主要副产气体,由于催化裂化是在催化剂作用下的裂解反应,与焦化干气相比,它的烯烃含量更高(一般在10~15v%),还会含有一些氧气,这些都是作为制氢原料所不希望存在的。如果原料气中的氧含量较高,会对加氢催化剂带来不利影响,也大量消耗其中的氢气,通常要控制原料气中O2≯2v%。 焦化干气和催化干气作为廉价的制氢原料,已越来越受到重视,国内制氢装置利用炼厂焦化干气和/或催化干气做制氢原料,已成功推出了全焦化和/或催化干气制氢工艺。 由此可见,炼厂干气包括焦化干气、催化裂化干气、加氢干气和重整干气等气源,将逐渐成为制氢装置的主要原料来源之一。 表1 炼厂干气的典型性质