FMEA讲义
合集下载
FMEA讲义
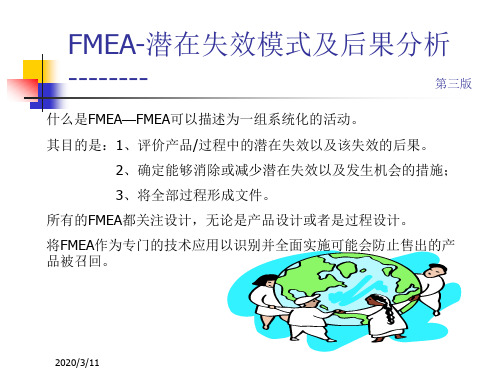
▪ 产品设计FMEA不能依靠过程检测作为控制程序 PFMEA应将作为DFMEA作为重要的输入,对
DFMEA中标明的特殊性也必须在PFMEA中作为重 点分析的内容。
2020/3/11
FMEA线路图
准备功能框图或过程流程图
确认现行控制
输入信息到FMEA表格
确认任务成功
用头脑风暴考虑所有 可能的问题和忧虑
2020/3/11
严 级 潜在
重 别 失效
度
起因/Leabharlann S机理有多糟 糕?
起因 是什 么?
频 现行控 度制 O
预探 防测
发生 的频 率如 何?
探R 测P 度N D
建议措 施
责任及 目标完 成日期
能做些什么? 设计更改 过程设计 特殊控制 标准、程序
或指南的更改
措施结果
采取 S O D R
的措
P
施
N
怎样能 得到预 防和探 测?
2020/3/11
思维方式的转变
采用像FMEA这样的工具,对于我们每一个人来说,有 利于提升我们工作质量,有利于全面发展,因为,对 于工程师来说,从单纯的技术的角度去分析问题,问 题的范围可能会局限于一个很窄的范围,而且很容易 犯经验主义,根据前期大量的实验和多年的经验,很容 易得出与事实真相完全背离的结果。如果我们的工程 师从质量的角度出发分析问题,借助诸如FMEA这样 的工具,将每一个潜在的失效因素细化,文件化。尤 其对于微电子这样的生产,细化每一项操作是非常重 要的。
确定失效模式和原因
是评定 FMEA
建立频度
完成FMEA分析
确认探测方法并 建立探测度
确认后果并 建立严重度
使用排列图;根据 需求选择需改进之处
DFMEA中标明的特殊性也必须在PFMEA中作为重 点分析的内容。
2020/3/11
FMEA线路图
准备功能框图或过程流程图
确认现行控制
输入信息到FMEA表格
确认任务成功
用头脑风暴考虑所有 可能的问题和忧虑
2020/3/11
严 级 潜在
重 别 失效
度
起因/Leabharlann S机理有多糟 糕?
起因 是什 么?
频 现行控 度制 O
预探 防测
发生 的频 率如 何?
探R 测P 度N D
建议措 施
责任及 目标完 成日期
能做些什么? 设计更改 过程设计 特殊控制 标准、程序
或指南的更改
措施结果
采取 S O D R
的措
P
施
N
怎样能 得到预 防和探 测?
2020/3/11
思维方式的转变
采用像FMEA这样的工具,对于我们每一个人来说,有 利于提升我们工作质量,有利于全面发展,因为,对 于工程师来说,从单纯的技术的角度去分析问题,问 题的范围可能会局限于一个很窄的范围,而且很容易 犯经验主义,根据前期大量的实验和多年的经验,很容 易得出与事实真相完全背离的结果。如果我们的工程 师从质量的角度出发分析问题,借助诸如FMEA这样 的工具,将每一个潜在的失效因素细化,文件化。尤 其对于微电子这样的生产,细化每一项操作是非常重 要的。
确定失效模式和原因
是评定 FMEA
建立频度
完成FMEA分析
确认探测方法并 建立探测度
确认后果并 建立严重度
使用排列图;根据 需求选择需改进之处
FMEA我的讲义

18
FMEA的实施 FMA:Failure Mode Analysis
FMA(失效模式分析) FMEA(潜在失效模式及后果分析)
失效已经产生
失效还未产生,可能发生,但不是一 定要发生
核心:纠正
核心:预防
诊断已知的失效
评估风险和潜在失效模式的影响
开始于产品设计和工艺开发活动之前
指引开发和生产
指引贯穿整个产品周期
• 4、1985年由国际电工委员会(IEC)出版的FMECA 国际标准(IEC812),即参考MIL-STD-1629A加以部分 修改而成。
13
FMEA 之適用範圍
• 1、ISO9004 8.5節FMEA作為設計審核的要項,另 FTA(失效樹分析)風險分析亦是。
• 2、CE標志,以FMEA作為安全分析方法。
E: Effect 後果
Effect談三種: 1.對本身的立即影響
2.對同一水平的影響, 也可能對下一工序的影響 3.對產品使用者的影響
6
FMEA定義
後果的通常表現形式:
人身安全 不舒服的氣味 不穩定 作業中斷 無法繫緊 無法安裝 損壞裝備
手感不良
作業過多
無法操作
操作不良
車控不良
顧客不滿意
滲漏
外觀不良
12
FMEA 之沿革
• 1、FMEA的前身為FMECA,是在1950由格魯曼飛機 提出,用在飛機主控系統的失效分析
• 2、波音與馬丁公司在1957年正式編訂FMECA的作业 程序,列在其工程手冊中
• 3、60年代初期,美太空总署将FMECA成功的应用于 太空计划。美军同时也开始应用FMECA技术,并于 1974年出版MIL-STD-1629 FMECA作业程序。
FMEA的实施 FMA:Failure Mode Analysis
FMA(失效模式分析) FMEA(潜在失效模式及后果分析)
失效已经产生
失效还未产生,可能发生,但不是一 定要发生
核心:纠正
核心:预防
诊断已知的失效
评估风险和潜在失效模式的影响
开始于产品设计和工艺开发活动之前
指引开发和生产
指引贯穿整个产品周期
• 4、1985年由国际电工委员会(IEC)出版的FMECA 国际标准(IEC812),即参考MIL-STD-1629A加以部分 修改而成。
13
FMEA 之適用範圍
• 1、ISO9004 8.5節FMEA作為設計審核的要項,另 FTA(失效樹分析)風險分析亦是。
• 2、CE標志,以FMEA作為安全分析方法。
E: Effect 後果
Effect談三種: 1.對本身的立即影響
2.對同一水平的影響, 也可能對下一工序的影響 3.對產品使用者的影響
6
FMEA定義
後果的通常表現形式:
人身安全 不舒服的氣味 不穩定 作業中斷 無法繫緊 無法安裝 損壞裝備
手感不良
作業過多
無法操作
操作不良
車控不良
顧客不滿意
滲漏
外觀不良
12
FMEA 之沿革
• 1、FMEA的前身為FMECA,是在1950由格魯曼飛機 提出,用在飛機主控系統的失效分析
• 2、波音與馬丁公司在1957年正式編訂FMECA的作业 程序,列在其工程手冊中
• 3、60年代初期,美太空总署将FMECA成功的应用于 太空计划。美军同时也开始应用FMECA技术,并于 1974年出版MIL-STD-1629 FMECA作业程序。
FMEA讲义
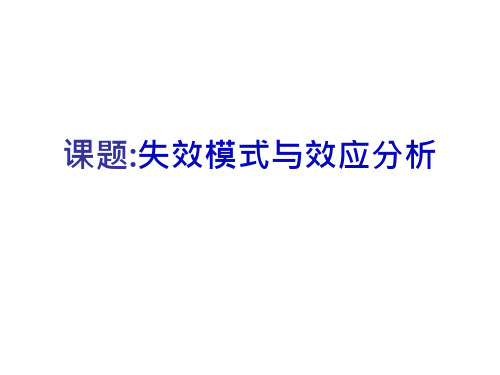
一.FMEA过程顺序
系统有那功能,特征,需要条件? 会有哪些错误?
频次
发生错误会有多惨?
那些错误是什么造成的?
严重度
发生之频率? 有哪些预防和检测? 检测方法能多好程度?
我们能做什么? -设计变更 -过程变更 -特殊控制 -改变标准程序或指南
难检度
一.风险优先数RPN
风险优先数(Risk Priority Number,RPN)
作为建立测试标准,质量管理程序(QCP),制程检验,标准操作 程序(SOP)及标准检验程序(SIP)等检验测试与管制规范的参 考。 7)可作为维护作业规划,维护保养手册编订以及备份料筹备等作 业的输入数据,也可据此制订避免导致失效的操作条件。
一.FMEA的功用
阶段
1.设计时间
2.开发阶段
功用
1.发掘所有可能的失效模式 2.依固有的技术进行设计变更 3.必要之处采用可靠性高的零组件
非常高 车辆/项目无法操作,丧失原来功能
等级 10
一.FMEA的目的
1)辅助设计与制造人员深入探讨产品各层级可能发生的失效模式, 发掘设计或制程上的弱点并改进或防范。
2)发掘可靠度关键件,列入作为设计验证及可靠度管制的重点。 3)研订失效准则,协助失效分析及改正作业,并可作为可靠度分
析的参考数据。 4)提供安全设计及可靠度评估的数据。 5)作为各研发阶段设计审查的输入数据。 6)设计初期即考虑制造组装的需求,并提供健全的失效信息基础,
一. 示例(4/5)
因素 温度太高 热电控制不当 应收帐款编号错误 打字错误 表面污染 高吊车使用时造成的 扔下电话 客户服务人数不足 釉层太薄 溶剂含量太高
一. 示例(5/5)
因素 脱胶 上胶不均匀且份量不足 鞋面破损 材质质量不良 鞋底断裂 鞋底材料配方不当 鞋面污点 模子与手套不洁所造成的 容易滑倒 鞋底材质不良,且设计不当
FMEA授课讲义6934

prepared by kingie, Not copy without permission.
设计FMEA 小组成员
❖ 在筹备样件期间开始 ❖ 设计工程师—通常的小组领导 ❖ 检验工程师 ❖ 可靠性工程师 ❖ 制造工程师 ❖ 最终服务工程师 ❖ 项目经理 ❖ 质量工程师 ❖ 顾客联系人 ❖ 其他,包括:销售、开发、过程、QA/QC等
permission.
FMEAs的关联
失效模式
后果
原因
SFMEA
问题的分支
问题
问题产生的原因
DFMEA 问题产生的原因来自 准确的后果定义 设计失效模式产
SFMEA
来自SFMEA
生的原因
PFMEA 问题产生的原因来自 和DFMEA相同 详细的过程失效
DFMEA
的后果
模式产生的原因
prepared by kingie, Not copy without permission.
FMEA 的益处
❖ 预防计划 ❖ 识别改变需求 ❖ 降低成本 ❖ 减少浪费 ❖ 降低保证成本 ❖ 降低无增值操作
prepared by kingie, Not copy without permission.
FMEA 的前提条件
❖ 选择适当的小组和有效的组织成员 ❖ 为每个产品/服务、过程/系统选择小组 ❖ 建立团队体系 ❖ 定义顾客和顾客需求/期望 ❖ 涉及/过程需求 ❖ 开发过程流程图**
❖在最初的DFMEA 中, 希望负责设计的工程师 能夠直接地、主动地联 系所有相关部门的代表。
❖ FMEA应成为促进不同部 门之间充份交換意見的 催化剂,从而提高整高 集体的工作水平。
prepared by kingie, Not copy without permission.
设计FMEA 小组成员
❖ 在筹备样件期间开始 ❖ 设计工程师—通常的小组领导 ❖ 检验工程师 ❖ 可靠性工程师 ❖ 制造工程师 ❖ 最终服务工程师 ❖ 项目经理 ❖ 质量工程师 ❖ 顾客联系人 ❖ 其他,包括:销售、开发、过程、QA/QC等
permission.
FMEAs的关联
失效模式
后果
原因
SFMEA
问题的分支
问题
问题产生的原因
DFMEA 问题产生的原因来自 准确的后果定义 设计失效模式产
SFMEA
来自SFMEA
生的原因
PFMEA 问题产生的原因来自 和DFMEA相同 详细的过程失效
DFMEA
的后果
模式产生的原因
prepared by kingie, Not copy without permission.
FMEA 的益处
❖ 预防计划 ❖ 识别改变需求 ❖ 降低成本 ❖ 减少浪费 ❖ 降低保证成本 ❖ 降低无增值操作
prepared by kingie, Not copy without permission.
FMEA 的前提条件
❖ 选择适当的小组和有效的组织成员 ❖ 为每个产品/服务、过程/系统选择小组 ❖ 建立团队体系 ❖ 定义顾客和顾客需求/期望 ❖ 涉及/过程需求 ❖ 开发过程流程图**
❖在最初的DFMEA 中, 希望负责设计的工程师 能夠直接地、主动地联 系所有相关部门的代表。
❖ FMEA应成为促进不同部 门之间充份交換意見的 催化剂,从而提高整高 集体的工作水平。
prepared by kingie, Not copy without permission.
六、FMEA讲义
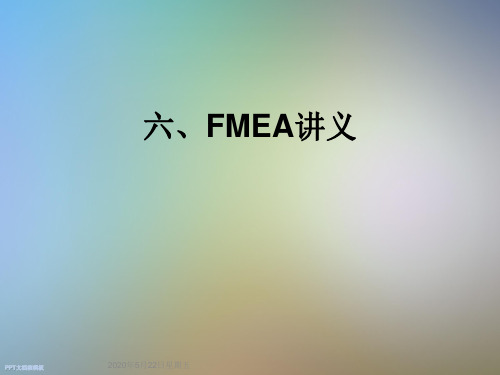
严重度评价表
• 失效模式的潜在要因(f):失效的潜在要因按照失效 怎么发生的迹象来定义,按照可纠正或可控制的情 形来描述.失效的潜在要因是设计或过程弱点的显 示,后果就是失效模式。失效模式可能是由一种或 一种以上的要因导致的。
• 发生率(O)(g): 发生率是失效特定要因发生的可能 性,发生可能性的排序值相对绝对值而言更有意义, 在1至10等级范围内评估失效潜在要因的发生可 能性。
• 严重度(s)(d): 严重度是与给定的失效模式最严重 后果相符的值。严重度是在单独FMEA范围内的 相关排序。
• 对等级9或10的不建议修改标准,等级为1的失效模 式不应再进一步分析。
• 分类(e):这栏可用于强调高优先权失效模式或可能 要求额外工程评估的要因,(为标识特殊特性)。
• FMEA中严重度等级识别为9或10的特殊特性,由 于这可能影响工程文件,应该通知负有设计责任的 工程师。
• 探测率(D) (i): 探测度是与探测控制栏列出 的最佳探测控制相符的级别.探测率是单独 FMEA范围内的相对排序,为了获得一个较 低的级别,一般来讲须改善计划的探测控制.
• 风险优先系数(RPN) (j): 帮助措施最优排序 的一种方法是使用风险优化系数。
• RPN=严重度(S) X 发生率(O) X 探测率 (D)
• FMEA帮助我们了解
• 哪里可能出错? • 造成的影响是什么? • 影响多严重? • 造成的原因是什么? • 发生概率多高? • 管制的方式是什么? • 管制多有效? • 整体风险多高? • 如何降低风险?
• 使用FEMA的好处
• 提高产品的质量、产品的可靠性和安全性。 • 帮助增加客户满意度。 • 减少产品开发时间和成本。 • 减少返工、维修和报废的数量。 • 记录并跟踪为减少风险而采取的行动。 • 优先考虑各缺点,关注改进努力。
FMEA讲义课件
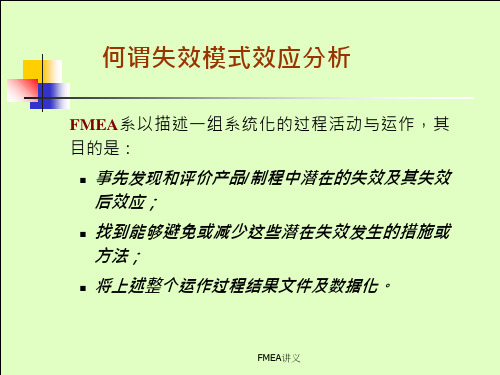
设计FMEA流程图
流 程
说 明
设计工程师应负责确认各项改正行动均经完成或均经通知负责人确实执行。
对RPN之项目应最优先采取必要措施,其目的在降低严重性、发生性及侦测性之分数。若不采有效之改正措施则制程FMEA之成效将受局限。
将风险领先指数做成柏拉图并决定建议之措施
将已采取之改正行动之内容及其完成日期填入记录,重新预估并记录改正后之严重性、发生性及侦测性之结果;计算新的RPN值。如果必要时,采取适当行动以降低RPN值。
9
很高
产品功能不能运作,丧失基本功能
8
高
产品功能能运作,但功能降低,顾客严重不满
7
中等
功能可运作,但舒适性及方便性降低,顾客使用时不满意
6
低
功能能运作,但舒适性及方便性降低,顾客使用时有些不满意
5
很低
如功能性、外观及结构等不合要求,大多数顾客注意到的了缺陷
4
微小
如功能性、外观等不合要求,一般顾客可注意到的缺陷
4
高
设计控制将会侦测出潜在原因/机制和随后的失效模式
3
非常高
设计控制有很高的机会侦测出潜在原因/机制和随后的失效模式
2
几乎肯定
设计控制几乎会侦测出潜在原因/机制和随后的失效模式
1
D-FMEA导入时机与展开
IN PUT
OUT PUT
产品主要功能
.
发生性系指预测该不良模式发生之频
度,不
良之
预防必须加以考虑
.
侦
测性系对该零件或装配件送交生产前,其可
能
存在之设计弱点是否能经设计
验证而查出之能
力
.
设计工程师应负责确认各项改正行动均经完成
FMEA讲义

续保持最新版),应该总是反映最新设计水准,及最新
的相关措施,包括生产后发生的设计更改和措施。
王昌兴
3、测量不精确; 4、热处理不当——时间、温度有误; 5、不充分的通风; 6、不足/无润滑; 7、零件漏装或错装。
王昌兴
明确描述起因/机理
应明确记录具体的错误或误操作情况(例如:操作者 未装密封圈),而不应用一些含糊不清的词语(如,操 作者错误、机器工作不正常)。
王昌兴
发生性
发生性是指具体的失效起因/机理发生的频率。 用来估计发生性的可能。就这种等级而言,只有导致 失效模式的发生性应该加以考虑。
王昌兴
探测度
是对现行控制方法下将检测出一个潜在失效起因/机 理的可能性的评价指标,或找出后续工序发生的失效模 式的可能性的评价指标。
王昌兴
风险优先序数(RPN)
RPN=(S)X(O)X(D)
如果风险优先序数很高,小组必须采取纠正措施,努 力减少该值。在一般实践中,不管RPN的结果如何,当
严重度(S)高时,就应予特别注意。
适当地加以应用,FMEA是一贯相互作用的过程,永无止
境。
王昌兴
种类、定义:
DFMEA:Design FMEA(设计 FMEA)
PFMEA:Process FMEA(过程FMEA) SFMEA: System FMEA(系统FMEA)
过程FMEA中“顾客”的定义,一般指“最终使用者”, 但也 可以是后续的或下游制造或装配工序,以及服务工作。
不起作用 工作不正常 外观不良
费力 异味 工作减弱
间歇性工作 车辆控制减弱 牵引阻力
王昌兴
如果顾客是下一个工程或后续的场所,失效的后果应
用过程/工序性能来描述。如: 不能扣紧 不衔接 不能转向 不符合 不能上升 损坏设备 不能钻孔 不匹配 伤害操作员
FMEA讲义(mqe)
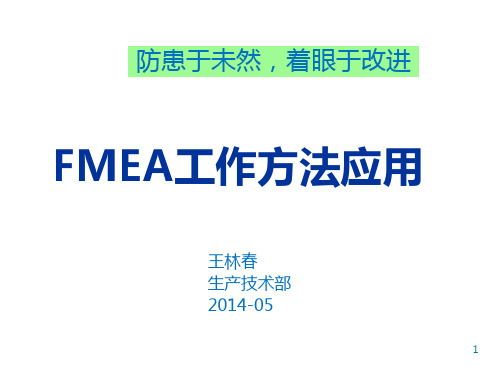
顾客不满或一部分小于100产品可能需要报废不需分检或者车项目需在返修部门返修少于05小时车辆项目可运行但舒适性便利性项目性能水平有所下降或100的产品可能需要返工或者车辆项目在线返修不需送往返修部门处理很低配合和外观尖响和卡嗒响项目不舒服多数75以上顾客能发觉缺陷或产品可能需要分检无需报废但部分产品小于100轻微配合和外观尖响和卡嗒响项目不舒服50的顾客能发觉缺陷或部分小于100产品可能需要返工无需报废在生产线上其它工位返工
• FMEA从局部失效入手,分析其对上一级系统、
相关部分、下游程序以及总体系统的后果。分析 路径“由下至上”。 • FTA一般由系统的失效模式入手、分析造成该失 效产生的原因。分析路径“由上至下”。
7
第 1 章 概论
新的 更改的 设计 评价 方框图
设计 FMEA
DFMEA
产品 过程 特性 过程流 程图 过程 FMEA
过程
PFMEA
1.2 FMEA种别
• •
8
SFMEA– 系统FMEA; DFMEA– 设计FMEA;PFMEA– 过程FMEA AFMEA—应用FMEA;SFMEA—服务FMEA;PFMEA—采购FMEA
第 1 章 概论
1. 3 FMEA主要用途
设计用 设计分析及改 善 设计品质/可靠 度 制程分析及改 善 提升制程能力 1设计改进; 2保养、维修、稽 核 制度及清单 3 sop sop制程管制 重点 系统及方法
5
第 1 章 概论
1. 1 什么是FMEA?
FMEA 与8D(Failure Mode Analysis) 分析 的区别:
• FMEA是一种事前行为; • 8D是一种事后行为;
• 8D报告是进行FMEA的重要的资料。
• FMEA从局部失效入手,分析其对上一级系统、
相关部分、下游程序以及总体系统的后果。分析 路径“由下至上”。 • FTA一般由系统的失效模式入手、分析造成该失 效产生的原因。分析路径“由上至下”。
7
第 1 章 概论
新的 更改的 设计 评价 方框图
设计 FMEA
DFMEA
产品 过程 特性 过程流 程图 过程 FMEA
过程
PFMEA
1.2 FMEA种别
• •
8
SFMEA– 系统FMEA; DFMEA– 设计FMEA;PFMEA– 过程FMEA AFMEA—应用FMEA;SFMEA—服务FMEA;PFMEA—采购FMEA
第 1 章 概论
1. 3 FMEA主要用途
设计用 设计分析及改 善 设计品质/可靠 度 制程分析及改 善 提升制程能力 1设计改进; 2保养、维修、稽 核 制度及清单 3 sop sop制程管制 重点 系统及方法
5
第 1 章 概论
1. 1 什么是FMEA?
FMEA 与8D(Failure Mode Analysis) 分析 的区别:
• FMEA是一种事前行为; • 8D是一种事后行为;
• 8D报告是进行FMEA的重要的资料。
- 1、下载文档前请自行甄别文档内容的完整性,平台不提供额外的编辑、内容补充、找答案等附加服务。
- 2、"仅部分预览"的文档,不可在线预览部分如存在完整性等问题,可反馈申请退款(可完整预览的文档不适用该条件!)。
- 3、如文档侵犯您的权益,请联系客服反馈,我们会尽快为您处理(人工客服工作时间:9:00-18:30)。
思维方式的转变
采用像FMEA这样的工具,对于我们每一个人来说,有 利于提升我们工作质量,有利于全面发展,因为,对 于工程师来说,从单纯的技术的角度去分析问题,问 题的范围可能会局限于一个很窄的范围,而且很容易 犯经验主义,根据前期大量的实验和多年的经验,很容 易得出与事实真相完全背离的结果。如果我们的工程 师从质量的角度出发分析问题,借助诸如FMEA这样 的工具,将每一个潜在的失效因素细化,文件化。尤 其对于微电子这样的生产,细化每一项操作是非常重 要的。
2020/7/8
全面质量管理的工具和对我们的要求
主要的TQM的工具有: SPC(统计过程控制) CP(控制计划) FMEA(失效模式及后果分析) PPAP(生产件批准程序) APQP(质量先期策划) MSA(测量系统分析) 除了以上必要的工具,DOE(实验设计)、MPCPS(
设备和工艺能力分析)、OEE(全面设备效率)等也 是作为一个管理者或技术人员在平时的工作中必须的 。
地利用时间。
2020/7/8
过程FMEA评价依据
1过程改进---FMEA推动过程改进作为主要目标。重点在于防错方法。 2高风险失效模式---FMEA对小组识别的所有高风险失效模式都引起重视,并有可
实施的措施计划。对所有其他失效模式也都加以考虑。 控制计划---试生产和生产控制计划对来自FMEA的失效模式均加以考虑。 综合—FMEA与过程流程图和过程控制计划相结合并且一致。如果有设计FMEA作
2020/7/8
FMEA定义
英文:Failure Mode and Effects Analysis.
FMEA是在产品设计阶段和过程设计阶段,对构成产品
的子系统、零件,对构成过程的各个工序逐一进行分 析,找出所有潜在的失效模式,并分析其可能的后果 ,从而预先采取必要的措施,以提高产品的质量和可 靠性的一种系统化的活动,并将全部过程形成文件。 它是工程师分析和解决问题的一种思维过程,一种表 格化的系统方法。尽可能的减少在生产线上潜在的、 影响产品的因素。
影响。 小组----整个分析过程,小组成员应接受培训,应有一名促进者。 文件-FMEA文件根据要求完全填写好,包括“取措施”以及RPN 时间的使用—FMEA小组所用的时间,以“尽可能早”为目标,有效、高效地利用时
间,带来增值结果。这还要假设建议措施都按要求进行了识别,且措施也得到了 实施。
2020/7/8
另一个小组FMEA的评分结果进行比较是不合适宜的 采取有效的预防/纠正并对这些措施加以跟踪,措施应传递到受影
响的部门。才能发挥FMEA的作用。 FMEA是动态文件。
2020/7/8
评价设计FMEA的依据
1设计改进---FMEA推动设计改进作为主要目标。 2高风险失效模式---FMEA对小组识别的所有高风险失效模式都引起重视
2020/7/8
严 级 潜在
重 别 失效
度
起因/
S
机理
有多糟 糕?
起因 是什 么?
频 现行控 度制 O
预探 防测
发生 的频 率如 何?
探R 测P 度N D
建议措 施
责任及 目标完 成日期
能做些什么? 设计更改 过程设计 特殊控制 标准、程序
或指南的更改
措施结果
采取 S O D R
的措
P
施
N
怎样能 得到预 防和探 测?
效模式的输入。 特殊或关健特性---FMEA将识别的关键特性,输入到关键特性选择过程以
被选择确定。 时间性---FMEA在“机会之窗”关闭之前完成。 小组----整个分析过程,小组成员应接受培训,应有一名促进者。 文件-FMEA文件根据要求完全填写好,包括“采取措施”以及RPN 时间的使用—FMEA小组所用的时间,以“尽可能早”为目标,有效、高效
2020/7/8
思考二:
FMEA的编制责任通常都指派到某个人,但是FMEA的输入应是小 组的努力。小组应有知识丰富的人员组成(如:设计、分析/试验 、制造、装配、服务、回收、质量及可靠性等方面有丰富经验的 工程师)。
FMEA有责任单位的工程师开始启动。 即使产品/过程看起来完全相同,将一个小组FMEA的评分结果同
情形2:对现有设计或过程的修改(假设对现有设计或过程已有 FMEA)。FMEA的范围应集中于对设计或过程的修改、由于修改 可能产生的相互影响以及现场的历史情况。
情形3:将现有的设计或过程用于新的环境、场所或应用(假设 对现有设计或过程已有FMEA)。FMEA的范围是新环境或场所对 现有设计或过程的影响。
该方 法在 探测 时有 多好 ?
思考一:
FMEA过程顺序图描述了进行FMEA的顺序,这并不是简单的填写 以下表格,而是要理解FMEA的过程,以便消除风险并策划适宜的 控制方法以确保顾客满意。
在进行FMEA时有三种基本的情形,每一种都有其不同的范围或关 注焦点:
情形1:新设计、新技术或新过程。FMEA的范围是全部设计、技 术或过程。
,并有可实施的措施计划。对所有其他失效模式也都加以考虑。 A/S/V或DVP&R计划---分析/开发/确认(A/D/V)和/或设计验证计划和报
告( DVP&R )对来自FMEA的失效模式均加以考虑。 接口—FMEA的范围包括流程图及分析中综合和衔接各失效模式。 吸取的教训---FMEA将所有吸取过的重大“教训”(召回产品)作为识别失
FMEA讲义
2020年7月8日星期三
前言
FMEA的实施: 最重要的因素之一是时间性(即“事件发
生前”的措施,而不是“事件出现后”的演 练。
2020/7/8
潜在失效模式及后果分析 顺序
子系 统
潜在失 效模式
潜在失效后 果
功能 要求
功能、特 性或要求 是什么?
后果是 什么?
会有什么问题? 无功能 部分功能/功能 过强/功能降级 功能间歇 非预期功能
为分析的一部分可以提供,那么过程FMEA也要考虑设计FMEA 吸取的教训---FMEA将所有吸取过的重大“教训”(召回产品)作为识别失效模式的
输入。 特殊或关健特性---FMEA将识别的关键特性,输入到关键特性选择过程以被选择确
定。 时间性---FMEA在“机会之窗”关闭之前完成。可以最高效地对产品或过程设计施加