基于软件的汽车等速万向节关键零件形面分析与逆向重构
等速万向节传动轴总成结构主参数的最优化设计

等速万向节传动轴总成结构主参数的最优化设计等速万向节传动轴总成结构主参数的最优化设计一、引言在汽车、机械设备等领域中,等速万向节传动轴总成是一种重要的传动装置,其性能对整个系统的稳定性和效率起着至关重要的作用。
对等速万向节传动轴总成的结构主参数进行最优化设计具有重要意义。
本文将对等速万向节传动轴总成的结构主参数进行深入探讨,并提出最优化设计的相关建议。
二、等速万向节传动轴总成的概述等速万向节传动轴总成是一种能够实现转动轴的等速传动和角偏差补偿的重要装置。
它通常由内套管、外套管、滚珠、保持架、密封圈等部件组成。
其中,内外套管的长度、直径,滚珠的数量和尺寸,保持架的结构等都是决定传动轴总成性能的关键参数。
三、等速万向节传动轴总成结构主参数的优化设计1. 内外套管长度和直径的优化内外套管的长度和直径直接影响着传动轴的承载能力和稳定性。
在进行最优化设计时,需要综合考虑传动轴总成的实际工作环境和使用要求,通过有限元分析等方法确定内外套管的最佳尺寸,以确保其在工作中具有良好的耐久性和稳定性。
2. 滚珠数量和尺寸的优化滚珠的数量和尺寸直接影响着传动轴的传动效率和扭矩传递能力。
在最优化设计中,需要通过仿真计算和试验验证等手段确定最佳的滚珠数量和尺寸,以实现传动轴在工作时的平稳传动和良好的功率输出。
3. 保持架结构的优化保持架作为传动轴总成中的重要部件,其结构设计对于传动轴的使用寿命和性能起着关键作用。
在最优化设计中,需要考虑保持架的材料、形状和加工工艺等因素,以确保其具有良好的刚性和耐磨性,同时尽量减小其重量和功耗。
四、个人观点和理解在进行等速万向节传动轴总成结构主参数的最优化设计时,我认为需要充分考虑传动轴总成的工作环境和使用要求,以及材料和加工工艺的实际条件。
通过综合运用计算机辅助设计、有限元分析、试验验证等方法,可以实现对传动轴总成结构主参数的科学、合理和有效的优化设计。
五、总结与回顾通过对等速万向节传动轴总成结构主参数的最优化设计进行深入探讨,我们可以得出以下结论:内外套管的长度和直径、滚珠数量和尺寸、保持架结构等参数的最优化设计,能够显著提高传动轴总成的稳定性、传动效率和使用寿命,从而为相关设备和系统的性能提升提供有力支持。
万向节参数化建模及运动特性的研究的开题报告

万向节参数化建模及运动特性的研究的开题报告1. 研究背景与意义随着现代汽车行业的发展,车辆的驱动系统也不断地进行升级和改进,其中万向节作为汽车驱动系统的重要组成部分之一,在传动系中起着至关重要的作用。
然而,传统的万向节参数化建模和运动特性研究方法在时间和精度上都存在一定的限制,为了更好地提高汽车传动系统的性能和效率,开展对万向节参数化建模及运动特性的研究显得尤为必要。
2. 研究内容和目标本研究将以传动系统中常用的万向节类型为研究对象,利用CAD软件实现其三维建模,探讨不同参数对万向节运动特性的影响,以找到最优方案,提高传动系统的性能。
研究具体包括以下几个方面:(1)对不同种类的万向节进行建模,并分析其结构和特点。
(2)通过建立系统动力学模型,探讨不同参数对万向节运动特性的影响,如角速度、角加速度、角位移等。
(3)利用有限元分析方法分析不同参数对万向节的应变、应力等情况,研究其应力分布情况。
(4)通过对比分析不同方案的性能和效率,找到最优化方案,提高传动系统的整体性能。
3. 研究方法和技术路线(1)CAD软件建模:利用CATIA等专业软件对万向节进行三维建模,建立几何体模型。
(2)动力学分析:建立动力学模型,分析不同参数对万向节运动特性的影响,如角速度、角加速度、角位移等。
(3)有限元分析:利用有限元分析方法,分析不同参数对万向节的应变、应力等情况,研究其应力分布情况。
(4)比较分析:通过对比分析不同方案的性能和效率,找到最优化方案,提高传动系统的整体性能。
4. 研究进度安排(1)前期调研和资料收集:2021年2月-2021年3月(2)CAD软件建模和参数化建模分析:2021年3月-2021年4月(3)动力学分析研究:2021年4月-2021年5月(4)有限元分析研究:2021年5月-2021年6月(5)方案比较和优化:2021年6月-2021年7月(6)论文写作和答辩准备:2021年7月-2021年9月5. 研究中的技术难点和创新点技术难点:建立动力学模型和有限元分析模型时,需要考虑万向节的复杂运动特性,将其转化为数学模型,并利用专业软件进行建立和优化。
基于Geomagic Studio的汽车连杆锻件逆向建模技术

个 N R S 体 都 可 以 用 数 学 表 达 式 U B物
一
特点 ,我们 可 以用 它做 出各种
外形放样 T艺 ,由C o s e ir 结 、给 出了关于B o n 、B z e 样条 的一套标准 复 杂 的 曲面造 型和 表现 特殊 的效 等大师于2世纪6 年代 奠定其理论 算法 ,17 年G r o  ̄ Ree f l 0 0 9 4 od n is n ed 果 ,如人的皮肤 ,面貌或流线型的
维普资讯
数 字 化 设 计
而易举地在参数连续性基础上解决
基 - o gc tdo  ̄Ge ma iS u i
了连接 问题 ,从而使 自由型 曲线曲
面形状 的描述问题得 到较好解决。
但 随着生产 的发展 ,B 样条方法 显 示 出明显不足 ,不能精确表示圆锥 截 线及 初 等解 析 曲面 ,这就 造成 了产 品几何 定义 的不 唯一 ,使得 曲线 曲面没 有统 一 的数学 描述 形 式 ,容易造成生产管理混 乱。为 了
的汽 车 连 杆 锻 件 逆 向
建模 技术
口 吉林大学超塑性与塑性研究所 赵 毅 王明辉
满足工业界进一步的要求 ,17 年 95
美 国S rc s 大学的V r p i]首 yaue e s r]e 次提 出有理 B 条方法 。后 来 由于 样 Pe l ilr ig ̄T l 等人 的功绩 ,终于使 e 非均匀有理B 样条 (U B ) N R S方法成为 现代 曲面造型 中最为广泛流行的技 术 。N R S U B 方法的提 出和广 泛流行
基于CATIA的汽车车身曲面逆向造型
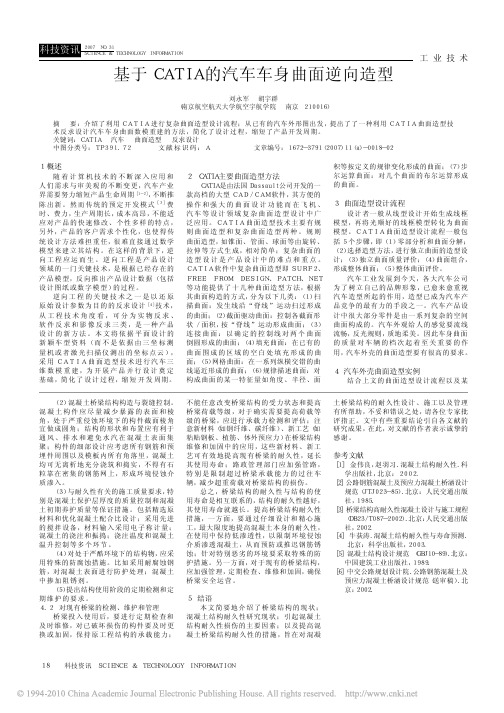
( 4 ) 对处于严酷环境下的结构物, 应采 用特殊的防腐蚀措施。比如采用耐腐蚀钢 筋, 对混凝土表面进行防护处理;混凝土 中掺加阻锈剂。
总之, 桥梁结构的耐久性与结构的使 用寿命是相互联系的, 结构的耐久性越好, 其使用寿命就越长。提高桥梁结构耐久性 措施, 一方面, 要通过仔细设计和精心施 工, 最大限度地提高混凝土本身的耐久性, 在使用中保持低渗透性, 以限制环境侵蚀 介质渗透混凝土, 从而预防或推迟钢筋锈 蚀;针对特别恶劣的环境要采取特殊的防 护措施。另一方面, 对于现有的桥梁结构, 应加强管理, 定期检查、维修和加固, 确保 桥梁安全运营。
对车身表面分块造型后, 将各部分装 配到一起, 然后先进行车身各部分曲线的 缝合, 再进行曲面的缝合。为了使曲面间 能做到二阶连续, 对一些区域要进行必要 的细化处理使之过渡自然、流畅、美观, 以 达到和谐的造型效果。最后创建的汽车造 型曲面如图 2 。 4.5 车身曲面品质评价
曲面质量对汽车的外覆盖件很重要, 表面上细微的缺陷都会在喷漆后引起光的
根据以上的曲面分块技术可以把一个复 杂汽车车身划分为几大曲面块:发动机罩、 前风窗、顶盖、后风窗、后备箱盖、左侧 玻璃窗、右侧玻璃窗、左侧边板、右侧边 板、和尾板。
科技资讯 2007 NO.31
SCIENCE & TECHNOLOGY INFORMATION
4.3 车身各独立曲面造型 曲面是在曲线的基础上生成的, 首先
42分解曲面分解曲面是依据现有参数化曲面理论和应用软件曲面造型方法结合产品的外形情况把复杂的轮廓不规则的三维曲面构成的汽车车身划分为多个比较简单容易处理的曲面块保证曲面质量要求进行拼接和缝合或用过渡面连结最终完成汽车车身设计实现车身的整体造型
复杂零件正逆向重构建模技术及应用研究

万方数据第3期张双侠等:复杂零件正逆向重构建模技术及应用研究231度,如果测量数据的可用性差,会为重构模型带来困难,更有可能导致最终的造型结果不合格。
因此,高效、高精度地实现样件表面的数据采集,是正逆向混合建模的基础和关键技术之一。
3.2曲面的测量规划为获得正确、完整的测量数据,测量前必须做好测量规划,做到“溅需要测的数据”,避免测量数据不能使用,为后续工作留下隐患。
在实际测量过程中,要对这些曲线、曲面进行高效率的测量与拟合,对曲线、曲面进行测量规划囡。
在曲面测量阶段:尽量一次扫描完整张曲面;应避免边界线跨越特征线;测量区域内特征线的走向应尽可能一致;为保证数据的完整性,测量区域应该有一定的重叠;表面孔域补凸后再进行测量;测量曲面复杂三维边界时,测量方向与测点曲面法矢保持—致当测量方向与边界点曲面法矢方向一致时,这时测量误差最小。
为了能使曲面上每点都能测量到,测量头的半径应小于曲面中凹区域的最小曲率半径;各个曲面—般是由多个面片组合而成,各面片之间通过过渡面片或圆角相互连接。
从原型的数字化开始,就应根据零件的造型方案来合理地划分面片,充分利用原型提供的几何信息,以确保数据的准确性和针对性。
3.3数据处理在进行重构之前,需要对测量数据进行预处理工作,目的是获得完整、正确的测量数据以方便后续的造型工作。
(1)排除异常数据,对测量点云进行滤波,去除飞点;(2)数据插补:由于实物拓扑结构以及测量仪器的限制,一种情况是在实物数字化时会存在一些探头无法测量的区域,另一种情况则是实物零件中经常存在经裁剪或“布尔减”运算等生成的外形特征,使曲面出现缺口,这样在造型时就会出现数据“空白”现象,使逆向建模变得困难。
通过数据插补的方法来补齐“空白”处的数据,最大限度获得实物剪裁前的信息;(3)数据平滑,目的是消除测量数据的噪声,以得到精确的数据和好的特征提取效果;(4)数据精简:自动测量所得到的数据点云十分密集,数据存在大量冗余,无法直接用于曲面构造。
等速万向节传动轴总成结构主参数的最优化设计

等速万向节传动轴总成结构主参数的最优化设计(原创实用版)目录1.等速万向节传动的概述2.等速万向节传动轴总成结构主参数的最优化设计2.1 传动轴总成结构的主要参数2.2 优化设计方法2.3 最优化设计的验证正文一、等速万向节传动的概述等速万向节传动是一种在传动过程中,使得输出轴和输入轴的角速度始终相等的传动方式。
这种传动方式广泛应用于汽车驱动轴、船舶推进器等领域。
等速万向节传动能够保证传动过程中的平稳性和可靠性,从而提高整个传动系统的工作效率和性能。
二、等速万向节传动轴总成结构主参数的最优化设计2.1 传动轴总成结构的主要参数在等速万向节传动轴总成结构中,主要的参数包括:万向节的类型、尺寸和材料;传动轴的直径、长度和材料;轴承的类型、尺寸和材料;以及密封件的类型和材料等。
这些参数对等速万向节传动的性能和可靠性有着重要的影响。
2.2 优化设计方法为了提高等速万向节传动轴总成结构的性能和可靠性,需要对其主要参数进行最优化设计。
最优化设计方法可以分为两类:一类是基于数学模型的优化设计,另一类是基于实验数据的优化设计。
基于数学模型的优化设计,主要是通过建立等速万向节传动轴总成结构的数学模型,然后运用数学方法和数值计算方法进行优化求解。
这种方法的优点是计算精度高,缺点是需要建立准确的数学模型,并对模型的参数进行精确的数值计算。
基于实验数据的优化设计,主要是通过进行大量的实验测试,然后运用统计方法和数据挖掘方法进行优化求解。
这种方法的优点是实验数据准确,缺点是实验过程耗费时间和资源。
2.3 最优化设计的验证最优化设计完成后,需要对其进行验证。
验证的主要方法有:模拟仿真验证、实验验证和实际应用验证。
模拟仿真验证主要是通过数学模型进行仿真实验,验证最优化设计的正确性和有效性;实验验证主要是通过实验设备进行实验测试,验证最优化设计的正确性和有效性;实际应用验证主要是通过实际应用,验证最优化设计的正确性和有效性。
基于FARO测量系统的汽车零部件逆向设计

作 者简 介: 崔秀梅(9 1 )女 ( 18一 , 满族 )辽宁人 , , 硕士 , 主要从 事逆向工程 、A C E\ A C D\ A C M技术研究
对 复 杂 曲面 进 行 逆 向设 计 , 曲 面精 度 可 达 ± 0 其 2 m, 测 量 速 度 是 接 触 式 三 坐 标 测 量 机 的 5 , 且 倍
较好地解决 了含光滑 曲面的汽车零件快速 、 高精度 逆向设计 的问题 .
关 键 词 : 向设 计 ; 据 采 集 ; 逆 数 曲面 重 构 ;A O测 量 系 统 FR
ec l nl x el ty. e Ke r s:r v re d sg ; d t c iiin;s ra e r c n tu t n;F y wo d e es e i n aa a q st u o u fc e o src i o ARO es rn y tm m a ui g s se
Absr c :Th t o fd t c uiiin,te tc n lg fd t ip s n u fc e o sr cin d rn ta t emeh d o aaa q st o h e h oo o aad s o a a d s ra e rc n tu t u ig y l o
h r c s fs oh s ra e d gt ai r e e rh d.T e k y tc n lg fs o t u fc e e s e t ep o e so mo t u fc ii z t n ae r s ac e i o h e e h oo o mo h s r e rv red — y a sg sa ay e in i l z d.Usn RAO a u i g s se t e e e d sg mo t u fc n ig F me s rn y tm o rv r e i a s o h s ra e, te r s l h w h t s n h eu t s o ta s i i n in ro e ls a we t ir n ,a d t e s a nig s e d i f e t s q ik r ta h t dme so a err a e s tn t ny m co s n h c n n p e s i i c e n t e s l s r h v me u h
万向节
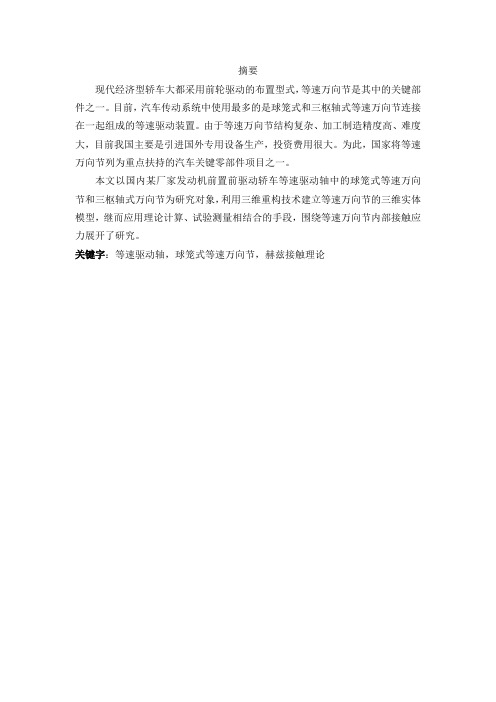
摘要现代经济型轿车大都采用前轮驱动的布置型式,等速万向节是其中的关键部件之一。
目前,汽车传动系统中使用最多的是球笼式和三枢轴式等速万向节连接在一起组成的等速驱动装置。
由于等速万向节结构复杂、加工制造精度高、难度大,目前我国主要是引进国外专用设备生产,投资费用很大。
为此,国家将等速万向节列为重点扶持的汽车关键零部件项目之一。
本文以国内某厂家发动机前置前驱动轿车等速驱动轴中的球笼式等速万向节和三枢轴式万向节为研究对象,利用三维重构技术建立等速万向节的三维实体模型,继而应用理论计算、试验测量相结合的手段,围绕等速万向节内部接触应力展开了研究。
关键字:等速驱动轴,球笼式等速万向节,赫兹接触理论ABSTRACTThe modern economical car adopts the pattern of assigning of front-wheel drive mostly,and the constant velocity universal joint is one of the key components among them.At present the constant velocity driving device which is composed of ball basket constant velocity universal joint together with constant velocity universal joint with pivot is used by automobile transmission system mostly.Because the structure of constant velocity universal joint is very complicated,process the precision of making is high,and difficulty of making is large.Our country introduces foreign special-purpose device mainly at present,it is very expensive to make the investment.For this reason,our country have regard constant velocity universal joint as one of the key part project to support especially.The ball-cage type and the three pivot shaft type constant velocity joints of theconstant velocity drive shaft on the F-F type car of a certain domestic factory wereregarded as research objects.The 3D models of the constant velocity joints werebuilt by using 3D re-created technology,then the finite element models of theconstant velocity joints were built by using ANSYS software,then the authorcarries out the study on the inner contact stress of the constant velocity joints bymeans of the connection of the finite element analysis,theoretic calculation and thetest. Keywords:The Constant V elocity Drive-shaft;The Ball-cage Type Constant V elocity Joint;Hertz Contact Theory第1章绪论1.1 万向节的应用在机械领域里,有一个很重要的基础件,称为万向节。
- 1、下载文档前请自行甄别文档内容的完整性,平台不提供额外的编辑、内容补充、找答案等附加服务。
- 2、"仅部分预览"的文档,不可在线预览部分如存在完整性等问题,可反馈申请退款(可完整预览的文档不适用该条件!)。
- 3、如文档侵犯您的权益,请联系客服反馈,我们会尽快为您处理(人工客服工作时间:9:00-18:30)。
・设计・计算・研究・
表1三枢轴轴段截面的形状尺寸mm参数Ⅱ161以620363长轴17.90317.9217.89517.9】17.91517.905测件1短轴17.87217.88717.86817.8917.90417.856拟合平均偏差0.026~0.042O.018~0.02l0.02~0.026长轴17.83l17.82617.84617.823】7.84817.823测件2短轴17.7817.80417.78617.78717.77217.775拟合平均偏差O.019~0.0240.014~0.024O.020~0.028
尺寸,详见表3;应用CArI'IA工具求得不同位置的沟道之间夹角,详见表4。
表2三枢轴的轴段中心线间夹角(。
)参数A日C
测件1119.990120.008119.999
测件2120.04l119.852120.132
根据上述求得的三枢轴和三柱槽壳的关键尺寸数据,应用CATIAV5软件QSR的BasicSurfaceRecognition和PowerFit、GSD的Loft和Fill、PartDesign的CloseSu血ce等功能,对各零件进行逆向重构,分别得到三枢轴和三柱槽壳的准确数学模型,从而可以应用于后续的进一步模拟计算和优化设计。
图5是三枢轴的测量点云和数学模型,图6是三柱槽壳的测量点云和数学模型,图7是三枢轴式等速万向节关键零件的数学模型。
表3三柱槽壳沟道截面的形状尺寸mm参数尺1尺2R3
位置Zl,Xl,Xl,测件l半径16.25416.19116.25516.24816-26516.172拟合平均偏差0.029~0.030.024~0.026O.02~0.026位置石J,石,,X、测件2半径15.98515.90l16.00315.91716.02715.94拟合平均偏差0.007~O.0310.01~0.0220.015~O.026
图4三柱槽壳的结构形状
图6三柱槽壳的测量点云和数学模型表4三柱槽壳内腔沟道形面中心线间夹角(o)
参数EFG
X,rX王,Z,,
测件1
120.10119.86119.83120.13120.06119.99
XyXyXy
测件2
119.93119.73120.10119.77119.96120.48
图5三枢轴的测量点云和数学模型
图7三枢轴式汽车等速刀向节关键零件的数学模型
4结束语
根据应用本模型所做的接触应力分析、疲劳分析及试验结果,找到了影响万向节使用寿命的主要因素,采取相应改进措施后使产品寿命大大延长。
事实证明,采用此方法求得的三枢轴式等速万向节的。