小直径铣刀铣削淬硬钢圆弧切削力研究
摆线走刀方式下高速铣削淬硬钢的切削力研究
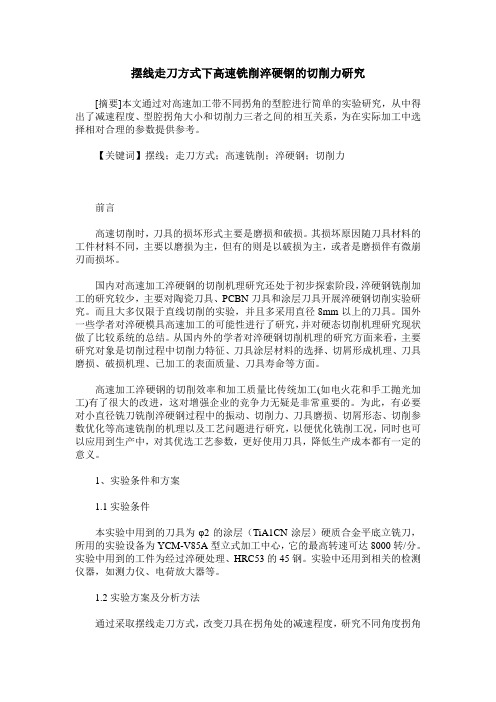
摆线走刀方式下高速铣削淬硬钢的切削力研究[摘要]本文通过对高速加工带不同拐角的型腔进行简单的实验研究,从中得出了减速程度、型腔拐角大小和切削力三者之间的相互关系,为在实际加工中选择相对合理的参数提供参考。
【关键词】摆线;走刀方式;高速铣削;淬硬钢;切削力前言高速切削时,刀具的损坏形式主要是磨损和破损。
其损坏原因随刀具材料的工件材料不同,主要以磨损为主,但有的则是以破损为主,或者是磨损伴有微崩刃而损坏。
国内对高速加工淬硬钢的切削机理研究还处于初步探索阶段,淬硬钢铣削加工的研究较少,主要对陶瓷刀具、PCBN刀具和涂层刀具开展淬硬钢切削实验研究。
而且大多仅限于直线切削的实验,并且多采用直径8mm以上的刀具。
国外一些学者对淬硬模具高速加工的可能性进行了研究,并对硬态切削机理研究现状做了比较系统的总结。
从国内外的学者对淬硬钢切削机理的研究方面来看,主要研究对象是切削过程中切削力特征、刀具涂层材料的选择、切屑形成机理、刀具磨损、破损机理、已加工的表面质量、刀具寿命等方面。
高速加工淬硬钢的切削效率和加工质量比传统加工(如电火花和手工抛光加工)有了很大的改进,这对增强企业的竞争力无疑是非常重要的。
为此,有必要对小直径铣刀铣削淬硬钢过程中的振动、切削力、刀具磨损、切屑形态、切削参数优化等高速铣削的机理以及工艺问题进行研究,以便优化铣削工况,同时也可以应用到生产中,对其优选工艺参数,更好使用刀具,降低生产成本都有一定的意义。
1、实验条件和方案1.1实验条件本实验中用到的刀具为φ2的涂层(TiA1CN涂层)硬质合金平底立铣刀,所用的实验设备为YCM-V85A型立式加工中心,它的最高转速可达8000转/分。
实验中用到的工件为经过淬硬处理、HRC53的45钢。
实验中还用到相关的检测仪器,如测力仪、电荷放大器等。
1.2实验方案及分析方法通过采取摆线走刀方式,改变刀具在拐角处的减速程度,研究不同角度拐角加工时的切削力和振动,进行拐角处的走刀方式和减速的参数优选,并得出刀具受力和振动随拐角角度的变化而变化的情况。
微径铣刀及微细铣削技术的研究

微径铣刀及微细铣削技术的研究1引言近年来,民用和国防等领域对各种微小型化产品的需求不断增加,对微小装置的功能、结构复杂程度、可靠性等要求也越来越高。
因此,研究开发经济上可行、能够加工三维几何形状和多样化材料、特征尺寸在微米级到毫米级的精密三维微小零件的微细加工技术具有重要意义。
目前,微细切削已成为克服MEMS技术局限性的重要技术,而微细铣削技术因具有高效率、高柔性、能加工复杂三维形状和多种材料的特点,已成为一个非常活跃的研究热点。
2微径铣刀及其制造技术(1)制造工艺及刀具性能磨削是一种传统的铣刀制造工艺,但对于直径仅为零点几毫米的微径铣刀,要在磨削力作用下,在不均质的刀具材料上磨削加工出锋利的切削刃口,是一件十分困难的事情,这也成为微径铣刀发展的一个技术瓶颈。
为此,从理论和实验的角度出发,可以选择一种不产生切削力的加工方法(如激光加工、聚焦离子束加工等)。
聚焦离子束加工方法从原理上比较适合用于制造微径铣刀。
Friedrich和Vasile等人采用聚焦离子束加工技术制作了微径铣刀,最小直径达到22mm。
利用微径铣刀和定制的高精度铣床,在聚甲基丙烯酸甲酯(PMMA)上加工出了89.5°直壁微槽结构,深度为62mm,槽间肋厚为8mm。
Adams等人采用聚焦离子束加工技术制作了一些直径约为25μm的微径铣刀,其轮廓形状有两面体、四面体和六面体,切削刃分为2刃、4刃和6刃,刀具材料为高速钢和硬质合金。
用这些刀具分别对铝、黄铜、4340钢和PMMA四种工件材料进行了微细铣削加工。
但是,由于使用微径铣刀进行切削加工必须采用小进给量,且刀具磨损剧烈,加工毛刺较大,加工效果至今不能令人满意。
立铣刀的刀刃几何形状主要有直体、锥体三角形(D-type)、半圆形(D-type)和已商品化的螺旋刃立铣刀四种。
Fang等人通过实验和有限元分析,从刀具刚度和加工性能出发,对上述四种立铣刀进行了研究对比。
结果表明,锥体D-type立铣刀更适合微细切削加工,并用直径0.1mm的锥体立铣刀成功制作了特征尺寸小于50μm的生物医学零件和特征尺寸小于80μm的微型压花模具。
小直径铣刀铣削力与刀位路径曲率关系的研究

( 西大 学 机械 工程学 院 , 宁 50 0 ) 广 南 30 4
St d ea in h p b t e o l a h o u v t r n ln c t ir - n l u y on r lt s i e we n t o t fc r a u e a d mii g f e wi m c o e d mi o p l or h l
Ke r s M i r - n i ; r a u e Gr y f r c s ; o a h y wo d : c o e d m l Cu v t r ; a o e a t To l t l p
中图分 类号 : H1 文献 标识 码 : T 6 A
对于切削力与刀位路径 的关系 , 国内外学者研究甚少 。主要 实验从曲线外 部切入 , 进行侧铣 , 切人切 出采用 圆弧进刀退
1 铣削试验及灰色预测
1 切削试验条件 . 1
试验是在 Y M- 8 A型立式加工中心( C V5 最高转速 8 0 R M) 00 P 上, 采用硬质合金涂层( i1 平底立 铣刀 ( 2 TA N) = mm, 四刃 ) 加工
图 2铣削内抛物线刀位路径
F g2 To l Pah i l n r - u v i . o t n Mi i g Pa a c r e l
W ANG a - h n, n - i g S Ja qa g Xio c u HU Yig nn ,U i— in
( oeeo caiaE g er gG agi nvri , ann 30 4C ia C lg Mehncl ni ei , unx U iesyN nig50 0 ,hn ) l f n n t
通过小直径铣 刀侧铣抛物线轮廓实验来研究曲线曲率变化与铣 刀 , 可保证刀具的安全 。 铣削从远离曲线波谷点 的一侧进行 , 然后 削力之间的关 系 , 建立切削力 灰色模 型 , 并通过灰色预测方法对 经过波谷点再切出, 图 2 如 所示 。 小直径铣刀加工淬硬钢过程中变化趋势进行预测 , 研究刀位路 径 在不 同曲率半径下切削力规律 , 寻找减少小直径铣刀加工淬硬钢 时非正常破损的有效途径。
高硬度材料小直径螺纹铣削技术

京:机械工业出版社,2006. [2] 延波.加工中心的数控编程与操
作技术[M]. 北京:机械工业出 版社,2001. [3] 陆剑中,孙家宁.金属切削原理 与刀具[M].北京:机械工业出版 社,1985.
格率为零。而且在丝锥断裂后还 需进行电火花清除断裂丝锥,电 火花加工不当还会对螺纹的底孔 侧壁、口部及螺纹造成不同程度 的损伤,严重时甚至出现报废, 不仅严重制约了生产进度,而且 提高了加工成本。因此,探索高 速、高效的高硬材料螺纹加工方 法才能保证产品质量,提高生产 效率,并降低加工成本。
2.螺纹铣削工艺分析 通过查阅资料,决定试验用 螺纹铣削的方法来加工该零件高 硬材料螺纹。 铣削的特征是:①铣刀各刀齿 周期性地参与间断切削。②每个刀 齿在切削过程中的切削厚度是变化 的。③每齿进给量 fz(mm/z),表 示铣刀每转过一个刀齿的时间内工 件的相对位移量。 螺纹铣削原理:螺纹铣削时 圆周运动产生螺纹直径,同时垂 直方向的移动,产生螺距。螺纹 铣削是利用数控机床三轴联动功 能,实现螺旋插补铣削,铣削是 使用旋转的多刃刀具切削工件, 是高效率的加工方法。工作时刀 具旋转(作主运动),工件移动
表 2 不同硬度材料铣削螺纹时的切削速度
工件材料 非合金钢 低合金钢 高合金钢
布氏硬度HBW 120~220 170~400 200~400
切削速度vc/(m/min) 90~140 50~130 50~100
4.结语 通过对高硬度材料螺纹铣削 技术的改进,圆满解决了生产加 工瓶颈,不仅保证了加工质量, 而且提高了加工效率,同时还降 低了生产成本。
图2
纹孔的多次铣削加工,实现螺纹
3.工艺改进后的效果
的少进给、高速度加工。 加工程序为:
小直径平底铣刀铣削淬硬钢拐角动力特性研究

层 材料 的选 择 、 屑 形破 已加 工 的
表面质量 、刀具 寿命 等方面对淬硬 钢切削 机理进行研究 , 钟 平、 孙方宏㈣ 究表明 , 研 在高速铣 削的情况 下 , 平均铣 削力 的
幅 度减 少 。 削 力 减小 的本 质 与 铣 削 过 程 中金 属 材 料 的 变 形 、 铣 切 屑 与刀 具 、 具 与 已加 工表 面 间 的摩 擦 密 切相 关 。 曾 宝平 P 刀 - }
图 1 实 验 系 统 示 意 图
图1 为实验 系统示意 图 ,实验 系统 的主要设备及仪器是
2 实 验结果 分 析
21 铣 削 速 度 对 铣 削 力 的 影 响 . 平 底 铣 刀 铣 削 拐 角 时 改 变 铣 削速 度 的 实 验 参 数 见 表 1 , 图 2~ 4是 外 拐 角 铣 削 力 与 铣 削速 度 的关 系 曲线 , 5 7 图 ~ 是
铣 削量 的走刀策 略。国内外对小直径铣 刀加工 拐角的研究还 非 常有 限, 需要进一步研究。 本文 主要通过采用小直径 (5 mm)i1  ̄2 TAN涂层硬质 合金
平底立铣刀进行 干式铣削 , 件是 4 工 5钢 淬 硬 H C 3, 角 包 R5 拐 括 内 、 拐 角 , 数 分 别 是 10 、0 、0 。 验 采 用单 因素 外 度 2。 9。 6。 实
据高速铣削的不 同进刀方式 ,解决 了型腔 和外轮廓铣削刀轨
进 刀方 式 的选 取 。安 鲁 陵 、 来水 等 用 将 拐 角 区域 加 工 分 周 采 为 多个 循 环 进 行 渐 进铣 削 的策 略 , 减 小 径 向切 深 。 可 同时 , 一 每
微细铣削机床研制及硬脆性材料切削实验研究

关键词:微细加工;桌面铣床;开放式数控;硬脆性材料
I
万方数据
山东理工大学硕士学位论文
ABSTRACT
ABSTRACT
Micromilling is an ultra-precision machining technique which is capable of realizing the fabrication of three-dimensional and complicated geometrical features. The CNC micromilling machine tool with excellent motion performances is the prerequisite for micromilling techniques. In order to conduct micromilling studies, the design and development of a CNC micromilling machine tool is introduced in the study firstly. Experimental evaluations are conducted for the developed desktop micromilling machine tool. Furthermore, the micromilling process has been conducted for the typical hard and brittle material. Considering the fact that features to be created in micromilling are usually small-sized, the CNC micromilling machine tool is designed as a desktop one. The miniaturized desktop machine tool not only saves space and energy, but also has the ability to improve the accuracy theoretically. Open architecture CNC system is applied to the developed machine tool. The controller uses the UMAC motion card from Delta Tau which has integrated I/O and power supply. It also has high-speed USB, Ethernet, Macro communication system to communicate with IPC to satisfy the performance expansions. Direct drive linear motors are used to avoid the transmission errors brought by conventional ball screws. Linear encoders with the graduation of 5nm are used for feedback to construct the closed-loop control. After the construction of the desktop micromilling machine tool, PID debugging, calibration and compensation by laser interferometer are conducted to realize the sub-micron positioning accuracy. Based on the minimum chip thickness theory in micromachining, experimental studies are conducted on the typical ductile material copper. The effect of the feed and axial depth of cut on surface roughness has been studied. The developed machine tool also has been verified by the experiments. The physical properties of single-crystalline silicon have been analyzed to select the micromilling cutter and cutting fluid. Experimental studies have been conducted on the developed machine tool. The federate and the cutting fluid supply method have been selected as the experimental factors. Based on the federate identified in previous studies, the two-factor and whole-level experiments have been conducted. The surface roughness has been analyzed by white-light interferometer. Variance analysis has been used to study the effects of the experimental factors on the surface roughness and the sequence of importance has been identified. It shows that the larger the federate, the worse the surface roughness is. The cutting fluid is very important in micromilling of single-crystalline silicon. The cutting fluid has more effects on the surface roughness than that of the federate. Brittle-ductile transmissions (ductile-mode micromachining) can be realized in a certain micromilling conditions. The experimental study found the basis for further studies on micromilling of hard and brittle materials. Keywords: Microcutting; Desktop milling machine tools; Open CNC; Hard and brittle materials
基于UG的小直径立铣刀应力场有限元分析

基于UG的小直径立铣刀应力场有限元分析作者:刘鹏王好臣引言在模具制造业,用高速铣削加工替代电加工已成为一种发展趋势。
模具型腔精加工的典型工艺为:毛坯粗加工→半精加工→热处理→精加工(高速或超高速铣削)。
在精加工工序中,常使用小直径立铣刀在高转速下进行清角和微细结构加工(小直径刀具在低转速下加工易发生崩刃或断裂)。
由于小直径立铣刀受力时容易变形,导致加工精度缺失,因此对小直径立铣刀铣削力应力场进行有限元分析很有必要。
2 瞬时动态铣削力基本模型圆周铣削加工的几何关系如图1所示。
在此不考虑铣刀的渐进磨损过程。
瞬时动态铣削力可分解为瞬时圆周铣削力dFri。
i(切向力)和瞬时垂直切削力dFri(径向力),可表示为式中,KS为切向铣削力系数;t I (ψ I ) 为瞬时切削厚度(它是时间的函数);R为刀具半径;β为刀具螺旋角;c为切削力切向与径向的比例系数;ψi为第i个刀齿上一个切削点的齿位角,其计算公式为:ψi=ψ+θ+(i一1)2π/m,(1≤i≤m,o≤ψ《Ψ,其中:ψ为螺旋滞后角,θ为刀具在dt时间转过的角度,m为刀具齿数,Ψ为刀具切入角,当轴向切削深度为ba时,有:图1 圆周铣削加工的几何关系瞬时切屑厚度及刀具有效前角对动态铣削力的的影响可表示为:周铣加工有不同的加工方式(见图2)。
顺铣和逆铣加工时,每个切削刃的总切削力为式中,Ψe和Ψs为切削刃的起始滞后角和终止滞后角,可按以下两种方法计算:将m个切削刃的切削力累积后,可得整个刀具所受的总切削力为:图2 圆周铣削加工的不同方式3 立铣刀铣削力试验在铣削力试验中,采用Kistler(9257B)三向动态测力仪、电荷放大器(5017B)和A/D转换卡测量在高速切削时不同切削条件(切削速度、切削深度和进给量)下的切削力,铣削力测试系统的工作原理见图3。
该试验获得的切削力还可在应力场有限元分析时用于确定受力边界条件。
图3 铣削力测试系统原理图4 立铣刀的实体建模根据铣刀制造原理,选择以去除材料的方式来建立铣刀模型。
小直径立铣刀后刀面磨损带的研究

小直径立铣刀后刀面磨损带的研究刀具的磨损不仅影响机床的切削状态,而且与工件加工质量密切相关,因此刀具状态的实时监测是保证加工质量的一项重要措施,而刀具磨损程度的评价指标是刀具状态监测的基础。
本文通过分析立铣刀后刀面磨损带的磨损规律及特点,研究了后刀面和副后刀面磨损带宽度VB和磨损带面积AVB在铣刀渐进磨损过程中的变化特点,提出了衡量刀具磨损程度的两个评价指标。
1 铣刀磨损量的评价指标刀具后刀面的磨损对加工精度和切削力的影响较前刀面更为显著。
由于后刀面磨损量比较容易测量,因此在刀具管理和金属切削研究中,多按后刀面磨损带中间部分平均磨损量允许达到的最大值(通常以VB表示)来制定磨钝标准。
刀具的磨损不仅影响机床的切削状态,而且与工件加工质量密切相关,因此刀具状态的实时监测是保证加工质量的一项重要措施,而刀具磨损程度的评价指标是刀具状态监测的基础。
本文通过分析立铣刀后刀面磨损带的磨损规律及特点,研究了后刀面和副后刀面磨损带宽度VB和磨损带面积AVB在铣刀渐进磨损过程中的变化特点,提出了衡量刀具磨损程度的两个评价指标。
1 铣刀磨损量的评价指标刀具后刀面的磨损对加工精度和切削力的影响较前刀面更为显著。
由于后刀面磨损量比较容易测量,因此在刀具管理和金属切削研究中,多按后刀面磨损带中间部分平均磨损量允许达到的最大值(通常以VB表示)来制定磨钝标准。
ISO制定了外圆车刀使用寿命实验中的刀具磨钝标准,但该标准只适用于切削实验。
在实际加工过程中,存在许多影响刀具磨损的不可预见和难以控制的因素。
虽然可将铣刀的每一刀齿看成一把车刀,但铣刀的磨损比车刀的磨损更为复杂,在不同的切削条件下将产生不同的磨损方式。
因此,ISO制定的刀具磨钝标准很难在实际生产中推广应用。
实验研究结果表明,影响刀具后刀面磨损带的因素很多,如加工条件、工件材料、刀具安装、机床性能、刀具几何角度等,仅以刀具后刀面磨损带中间部分磨损量作为评价指标很难真实、准确和完整地评价刀具磨损状态。
- 1、下载文档前请自行甄别文档内容的完整性,平台不提供额外的编辑、内容补充、找答案等附加服务。
- 2、"仅部分预览"的文档,不可在线预览部分如存在完整性等问题,可反馈申请退款(可完整预览的文档不适用该条件!)。
- 3、如文档侵犯您的权益,请联系客服反馈,我们会尽快为您处理(人工客服工作时间:9:00-18:30)。
( 12)
v f 2 = 1 . 471 15 v f 1
( 13)
为了保证直线加工和圆弧加工的材料切除率 相等 , 在改变径向切深时 , 圆弧和直线的进给速度 对应的参数值如表 3 所示。
表3 图4 直线刀位路径切削过程的切削力 切除率相等时径 向切深对切削影响的实验参数表
0. 02, 0. 03, 0. 04, 0. 05, 0. 06, 0. 07, 0. 08 200 250 300 350 400 450 500 v f1 ( mm/ min) v f2 ( mm/ min) R ( mm ) R d1 ( mm )
294. 2 367. 8 441. 3 514. 9 588. 5 662. 0 735. 5 3
图 6 是直线和圆弧的材料切除率相等时, x 方向与 y 方向的切削合力 F xy 随着径向切深变化 的曲 线 图 ( A d = 0. 15m m , L = 19m m , v c = 40m/ min, v f = 300mm/ min, R = 3m m ) , 从图 6
( 8)
由式( 6 ) 和式( 7) 得
Fx = Fy =
2 F2 r + F t sin ( +
) )
( 3)
F + F cos ( +
2 x 2 y 2 r 2 t
2 r
2 t
由式 ( 3) 可知
F + F = F + F ( 4)
为了保证直线加工和圆弧加工的材料切除率 相等, 即 V 1 = V 2 , 在改变切削速度时圆弧和直线 1605
[ 3- 5] [ 2]
实验在 YCM - V85A 型立式加工中心( 最高 转速为 8000r/ m in) 上进行 , 加工材料为 45 钢 ( 淬 火硬度为 H RC52) 。刀具 为硬质合金 T iAlN 涂 层平底四 刃立铣刀 ( 直径为 2mm ) , 刀具 悬伸量 L = 19mm 。数据由 YDX- III9702 型压电式铣削 测力仪( 大连理工大学生产, 分辨率为 0 01N) 、 重 庆大 学 的 QL V 型 系 列 虚拟 测 试 仪 器 和 KIS T L ER 声发射测试仪 器 ( 包括传 感器、 信 号耦合 器、 24V 直流电源) 记录。实验系统及坐标如图 1 所示 , 其中 z 轴方向为刀具的轴向方向。
中国机械工程第 20 卷第 13 期 2009 年 7 月上半月
轨迹长度不同。 设在时间 t 内 , 走直线路径时刀具 中心经过的长度为 l2 , 走圆弧时经过的圆心角为 , 刀路轨迹长度为 l 1 , 则有
l1 = V1 = ( R + R d1 - r )
2 2
( 9) ( 10) ( 11)
0
引言
切削力是切削过程中的重要物理参数, 是金
1
1. 1
圆弧路径与直线路径的铣削实验
实验条件与实验系统
属切削过程中必不可少的重要因素 [ 1] 。小直径铣 刀是硬铣方式加工复杂型面淬硬模具必不可少的 刀具之一 , 但其切入过程的崩刃、 断刀现象非常严 重 ; 小直径铣刀加工淬硬钢的切削用量现在没 有切削用 量手册 可查 , 仍依 靠经验 或实验 来选 取
2 r
令 sin =
Fr , cos = F + F2 t
2 r
等, 故在相同时间内刀具中心经过的轨迹长度相 等, 圆弧路径和直线路径切除材料的体积分别为
V1 = V2 = A d1 [ ( R + R d1 ) 2 - R 2 ] / 2 A d2 R d2 ( R + R d1 - r ) ( 6) ( 7)
刀具直径 d = 2m m ; 刀具齿数 N = 4; 刀具悬伸量 L = 19m m 注 : 机床主轴转速为 1592 ~ 6366r/ min。
和
2
2
) , x 方向的力与径向力的夹角分别为
1
2
实验数据分析
图 3 为圆弧刀位路径切削过程采集的切削力
和
。
信号波形图( 部分) , 图 4 为直线刀位路径切削过 程采集的切削力信号波形图 ( 部分) 。 切削力数值 为负表示切削力与测力仪测量的正方向相反。
测力仪测得的圆弧刀位路径力 F x 、 F y 与刀具 所受切向力 F t 和径向力 F r 之间的关系为
F x = F r cos + F t sin F y = F r sin - F t cos - 90 90
2. 1
切削速度对切削力的影响
假设在时间 t 内 , 圆弧路径刚好为一个半圆, 其轨迹长度为 ( R + R d1 - r ) , 因为进给速度相 Ft , 则有 F + F2 t
表1 圆弧路径的因素水平表
水平 0. 15 10, 15, 20, 25, 30, 35, 40 200, 250, 300, 350, 400, 450, 500 0. 02, 0. 03, 0. 04, 0. 05, 0. 06, 0. 07, 0. 08 2. 0, 2. 5, 3. 0, 3. 5, 4. 0, 4. 5, 5. 0 因素 轴向切深 A d1 ( m m ) 切削速度 v c ( m/ min ) 进给速度 v f ( mm/ min) 径向切深 R d1 ( m m ) 曲面半径 R( mm )
。如何合理选择小直径铣刀进行特殊路径
[ 6]
的铣削成为精密加工 的重点和 难点
[ 7]
。全燕鸣
等 通过刀位路径的切削实验, 研究了小直径铣 刀铣削淬硬钢时切入、 切出、 拐角及直线铣削的切 削力、 振动的动态特征, 但没有研究曲线刀位路径 在铣削过程中的动态特性。目前, 从本研究领域 来看 , 曲线路径的研究较少, 而模具型腔大多是曲 面, 因此通过对小直径铣刀铣削圆弧路径与直线 路径的对比实验, 进一步研究曲线刀位路径下的 铣削特性是有必要的。基于单因素法 , 在圆弧路 径和直线路径的材料切除率相等的条件下 , 分析 切削力信号, 以寻找加工参数对切削力信号的规 律, 在切削加工前实现对参数的优选。
( A d = 0. 15mm , L = 19mm , v c = 40m/ min, v f = 300mm/ min, R d = 0 . 04mm )
的径向切深对应的参数值如表 2 所示。
表2 切除率相等时切削 速度对切削影响的实验参数表
v c ( m/ min ) R d1 ( m m ) R d2 ( m m ) R( m m ) 10, 15, 20, 25, 30, 35, 40 0. 04 0. 059 3
A d1 [ ( R + R d1 ) - R ] / 2 V 2 = A d2 R d2 l 2
令 V1 = V2 , 则
l1 2( R + R d - r ) = l2 2R + R d
f1 1 R d + 2R v f1 , 即 显然 v = l , 故 v f2 = v f2 l2 2( R + R d - r )
收稿日期 : 2008 12 30
图1
铣削实验原理图
1. 2
实验方法和实验方案
基金项目 : 国家自然科学基金资助项目 ( 50665001) ; 广西科学基 金资助项目 ( 0575013)
实验在保证圆弧路径和直线路径的材料切除 率相等的情况下进行 , 采用单因素法分别对进给
1604
小直径铣刀铣削淬硬钢圆弧切削力研究
中国机械工程第 20 卷第 13 期 2009 年 7 月上半月
小直径铣刀铣削淬硬钢圆弧切削力研究
王小纯 胡映宁 曹景源 龙卫仁 苏家强
广西大学, 南宁, 530004
摘要 : 在高速加工中心上 , 用直径 2m m 的小直径铣刀, 采用单因素法 , 在相同材料切除率的情况下 对 45 淬硬钢( 硬度为 H RC52) 进行了圆弧路径和直线路径的高速铣削对比实验 。通过对切削力信号的 分析研究 , 找出了铣削参数对铣削力的影响规律, 获得了等切除率条件下直线路径切削力均大于圆弧路 径切削力的结论 , 建立了该实验条件下的切削力经验公式。 关键词: 高速铣削; 小直径铣刀 ; 淬硬钢; 材料切除率 中图分类号 : T G506. 1 文章编号: 1004 132X( 2009) 13 1604 04
王小纯
胡映宁
曹景源等
速度、 径向切深等因素进行实验。因为切削过程 中, 圆弧路径切削力的大小和方向是不断变化的, 所以本实验比较的是 x 方向与 y 方向的合力 F xy 。 实验中, 圆弧路径和直线路径的轴向切深始终相 等, 即 A d1 = A d2 。 图 2 是圆弧路径和直线路径的切削加工示意 图, 图中, r 为刀具半径, R 为工件圆弧半径 , R d1 为 圆弧路径径向切深, R d2 为直线路径径向切深 , A d1 为圆弧路径轴向切深 , A d2 为直线路径轴向切深。 图 2 中的坐标系为工件坐标系 , 取切削位置的任 意两个不同坐标点 ( x 1 , y 1 ) 和( x 2 , y 2 ) , 其对应的 径向力分别为 F r1 和 F r2 、 切向力分别为 F t1 和 F t2 ; 在( x 1 , y 1 ) 和( x 2 , y 2 ) 两位置点, 测力仪所测的力 分别用 F x 1 、 Fx 2 、 F y1 、 F y 2 表示。 刀具接触角是铣刀 刀齿从切入到切出之间切削接触弧对应的中心角 (
( a) 圆弧铣削 图2
( b) 直线铣削
圆弧和 直线的切削示意图
1
显然 , 在同一切削 过程的两个位 置, 接触角 = 2 , 所以这两个位置点的刀具所受的径向力
F r1 = F r2 Ft1 = Ft2
是相等的 , 切3 圆弧刀位路径切削过程的切削力 ( A d = 0. 15mm, L = 19mm , v c = 40m/ min, v f = 300mm/ min, R d = 0 . 04mm ) ( 2)