高速铣削系统切削力动态分析
摆线走刀方式下高速铣削淬硬钢的切削力研究
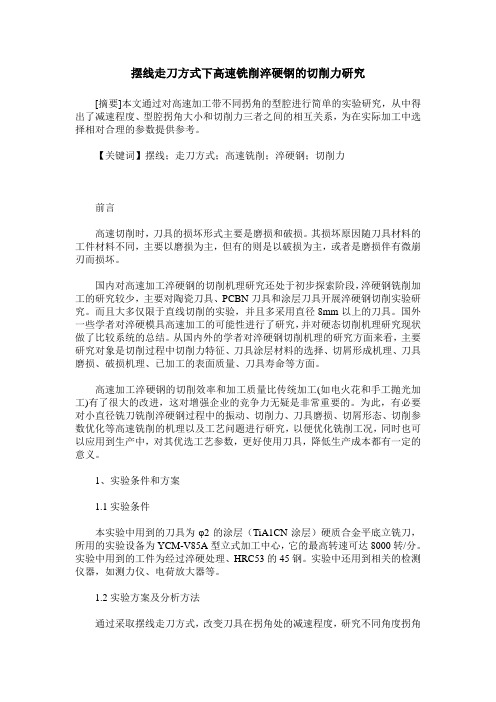
摆线走刀方式下高速铣削淬硬钢的切削力研究[摘要]本文通过对高速加工带不同拐角的型腔进行简单的实验研究,从中得出了减速程度、型腔拐角大小和切削力三者之间的相互关系,为在实际加工中选择相对合理的参数提供参考。
【关键词】摆线;走刀方式;高速铣削;淬硬钢;切削力前言高速切削时,刀具的损坏形式主要是磨损和破损。
其损坏原因随刀具材料的工件材料不同,主要以磨损为主,但有的则是以破损为主,或者是磨损伴有微崩刃而损坏。
国内对高速加工淬硬钢的切削机理研究还处于初步探索阶段,淬硬钢铣削加工的研究较少,主要对陶瓷刀具、PCBN刀具和涂层刀具开展淬硬钢切削实验研究。
而且大多仅限于直线切削的实验,并且多采用直径8mm以上的刀具。
国外一些学者对淬硬模具高速加工的可能性进行了研究,并对硬态切削机理研究现状做了比较系统的总结。
从国内外的学者对淬硬钢切削机理的研究方面来看,主要研究对象是切削过程中切削力特征、刀具涂层材料的选择、切屑形成机理、刀具磨损、破损机理、已加工的表面质量、刀具寿命等方面。
高速加工淬硬钢的切削效率和加工质量比传统加工(如电火花和手工抛光加工)有了很大的改进,这对增强企业的竞争力无疑是非常重要的。
为此,有必要对小直径铣刀铣削淬硬钢过程中的振动、切削力、刀具磨损、切屑形态、切削参数优化等高速铣削的机理以及工艺问题进行研究,以便优化铣削工况,同时也可以应用到生产中,对其优选工艺参数,更好使用刀具,降低生产成本都有一定的意义。
1、实验条件和方案1.1实验条件本实验中用到的刀具为φ2的涂层(TiA1CN涂层)硬质合金平底立铣刀,所用的实验设备为YCM-V85A型立式加工中心,它的最高转速可达8000转/分。
实验中用到的工件为经过淬硬处理、HRC53的45钢。
实验中还用到相关的检测仪器,如测力仪、电荷放大器等。
1.2实验方案及分析方法通过采取摆线走刀方式,改变刀具在拐角处的减速程度,研究不同角度拐角加工时的切削力和振动,进行拐角处的走刀方式和减速的参数优选,并得出刀具受力和振动随拐角角度的变化而变化的情况。
高速铣加工切削参数研究

; m 母 i 蕊 . 翟《 ! l
跑 ”原则。图 2为刀具厂商提供 的几种 材料 的高速切削 通用范围。
O
损的主要原 因。
( )扩散磨损 在高温作用下 ,刀具与工件接触面 3 间的分子活动能量 大 ,会 产生合 金元 素相互 扩散置 换 ,
■一 图
f=  ̄ fz
t {7 : / , 式中 n ——转数 (/ n ; rmi)
— —
I
—
f
线速度 ( / n ; m mi)
{
图 1
D ——刀具直径 ( m) m ; v f ——进 给速度 ( m mn ; m / i) 卜 进给量 ( n ) m Vr ;
线速度 和每齿 进 给量 的选 择 ,理论 上 与刀具 、 工件 、机床等多个环节有关 ,一般情 况下 ,刀具 厂商在
的切削速度 ,适 当的进给量 ,6 % ~8 % 的刀具大小 的 0 0
径向切深 、小 的轴 向切深 ,也就是通常所 说的 “ 少吃快
e, i\! 三 0 — 、 ;\! . ,、 -, /_ 、3 . , ,、 ; 三 ,. , 、0 0一 ,、 .三
5 机构传动效率的确定 .
( 收稿 1 :2 10 0 ) 3期 0 0 7 1
( 一2) , H 11 = .7 ,叼 = 55 ,满足 了 1 i ] H 2= /3 006 9 m 4.%
参磊 工冷 工 加
WWW. e a| m t wor i k ng1 950 co . r n
21年 2期 0 第 0 0
性 ,此处我们仅计算刀架松开 、锁紧时机构的效率 。 综合上述 因素 ,取 吼 =09 ( 为转 化机构 的效率 ) . ,
金属切削中的刀具动态负荷分析与振动控制

金属切削中的刀具动态负荷分析与振动控制随着制造业的发展和技术的进步,金属切削已成为现代加工工艺中不可或缺的环节。
金属材料的切削加工过程中,刀具承受着巨大的动态负荷,而这些负荷会导致刀具的振动,进而影响加工的精度和表面质量。
因此,对金属切削中刀具的动态负荷进行分析和振动控制具有重要意义。
刀具动态负荷分析主要通过建立数学模型来描述切削过程中的力学性能。
一般来说,刀具动态负荷分析需要考虑以下几个方面的因素:首先是切削力的分析。
切削力是指在切削过程中刀具受到的力的大小和方向。
切削力主要由切削阻力和切削热导致的材料变形引起的应力引起。
通过分析切削力的分布和变化规律,可以评估刀具的负荷程度,从而为刀具的设计和选择提供科学依据。
其次是动态特性的分析。
刀具的动态特性是指刀具在受力作用下振动的频率和振幅。
刀具的振动对加工过程和加工结果具有重要影响,因此需要进行动态特性的分析。
常用的分析方法包括有限元分析和模态分析等。
通过这些分析方法,可以得到刀具的振动模态及其频率等关键参数,为后续的振动控制提供依据。
最后是振动控制的方法。
根据刀具的动态特性分析结果,可以采取一系列的振动控制措施来减小刀具的振动。
常见的振动控制方法包括动平衡、刚性支撑和减振器等。
动平衡是指通过增加或减少刀具上的质量分布,使刀具的振动幅值减小。
刚性支撑是指在切削过程中给予刀具充分的支撑,使其振动减小。
减振器是一种通过阻尼材料或装置来减小振动幅值的方法。
通过采取这些振动控制方法,可以有效地降低刀具的振动,提高加工质量和效率。
在金属切削中的刀具动态负荷分析与振动控制中,还需要考虑到刀具和材料之间的磨损和热变形等因素。
刀具的磨损会导致切削力的变化,进而影响刀具的动态负荷和振动。
而材料的热变形会引起刀具的振动,甚至导致刀具的断裂。
因此,在分析和控制刀具的动态负荷时,还需要考虑到这些因素的影响,并采取相应的措施进行修正和优化。
总之,金属切削中的刀具动态负荷分析与振动控制是一项重要的技术研究领域。
高速切削刀具系统动平衡技术研究

高速切削刀具系统动平衡技术研究摘要:介绍高速切削刀具系统动平衡技术的发展现状,并在此基础上提出相关问题进行讨论。
一、概述在高速旋转下,刀具系统(刀具-夹头-刀柄)的一点点不平衡都会产生较大的离心力,引起机床和刀具的振动,产生不均匀的切削力,不仅影响被加工工件的加工精度和表面质量,又会影响机床主轴轴承和刀具的不规则磨损,迅速降低其使用寿命。
高速旋转刀具的不平衡对加工表面粗糙度Ra的影响可用下面的实例说明。
实验目的:通过切削实验,比较用两种不平衡量的刀具系统进行切削,径向切深,对铣削加工表面粗糙度Ra的影响。
实验条件:试件材料为铝合金。
加工机Array床为瑞士米克郎公司产HSM600铣削中心,刀具选用Ø10mm超细晶粒硬质合金整体立铣刀,4齿,30°螺旋角,刀尖圆弧半径1mm ,两刀具系统不平衡量分别为u1=100g·mm、u2=2.5g·mm。
加工参数为主轴转速15,000r/min ,进给速度5.3m/min 。
实验结果分析:用两种不平衡量刀具进行切削,试件加工表面粗糙度Ra与径向切深a p的关系如图1所示。
从实验结果看,试件加工表面粗糙度Ra随径向切削深度a p的增大而增大,而且两种不图1 试件加工表面粗糙度Ra与a p关系平衡量刀具对其加工表面粗糙度的影响有较大差距。
因此,研究高速旋转刀具的动平衡技术是推广应用高速切削加工技术的重要内容。
目前,许多国家已对高速切削刀具的动平衡问题进行了广泛研究,如动平衡标准,动平衡方法、动平衡质量等级界定、动平衡仪器等。
二、刀具系统动平衡技术的发展现状1. 平衡标准旋转体的不平衡量,是指其质量重心偏离旋转中心的量。
不平衡量U在数值上等于旋转体质量M(g) 乘以偏心距e(mm),也等于等效不平衡质量m(g)乘以其回转半径r(mm),即:U=Me=mr(g·mm)不平衡量U可在动平衡机上测得。
就旋转刀具和刀柄来说,目前由于国内、外尚无统一的刀具平衡标准,世界各国和机床厂家采用的标准也不一样,往往借用旋转体平衡的国际标准ISO1940-1。
高速铣削加工实验报告

高速铣削加工实验报告一、实验目的本实验旨在探究高速铣削加工的原理和方法,验证其在工业生产中的应用价值。
二、实验原理高速铣削加工是指在高速转动的铣刀刀具下,通过削减工件的材料,使其形成需要的形状和表面质量。
该加工方法具有高效、高精度、高表面质量的特点。
三、实验步骤1. 准备实验所需设备:数控铣床、高速铣刀、工件材料、润滑剂等。
2. 将工件夹在数控铣床上,并调整好加工参数。
3. 启动数控铣床,通过程序控制铣刀的运动程式。
4. 对工件进行高速铣削加工,观察并记录加工过程中的各项数据。
5. 完成加工后,对加工件进行检查,评估其表面质量和尺寸精度。
四、实验结果与数据分析经过高速铣削加工后,我们得到了一批加工件。
通过检查和测量,我们得到了以下数据:1. 加工件的尺寸精度均匀在±0.02mm范围内,达到了我们的要求。
2. 加工表面的光洁度较高,无明显划痕和毛刺。
3. 加工过程中的切削力较小,表明高速铣削加工确实能够提高加工效率。
根据上述结果,我们可以得出以下结论:高速铣削加工在工业生产中具有重要的应用价值。
它能够快速、准确地加工各种形状的工件,并且保证工件的尺寸精度和表面质量。
此外,高速铣削加工还能够降低切削力,延长刀具的使用寿命,提高生产效率和经济效益。
五、实验总结通过本次实验,我们进一步了解了高速铣削加工的原理和方法,并验证了其在工业生产中的应用价值。
高速铣削加工不仅能够提高加工效率和精度,还能够改善加工表面的质量。
在以后的工作中,我们将进一步研究并优化高速铣削加工的工艺参数,提高其应用效果。
六、参考文献1. 《数控铣床操作与编程》,xxx,xxx出版社,2010年。
2. 《机械加工技术》,xxx,xxx出版社,2015年。
(注:以上文献仅作参考,具体引用请根据实际情况进行。
)以上是本次高速铣削加工实验的报告,感谢您的阅读。
高速主轴-夹具-刀具系统动态特性分析

高速铣 削加 工广 泛 应用 于汽 车 和航 空 工业 的机 械 零 部件 的加 工 中 , 然而 , 铣 削过 程 中颤 振 的发 生成
态特 性 的影 响 , 导致 该 方法 不仅 费 时 费力 , 而且 还没 法 考 虑主 轴 转 速 对 刀 具 端 点频 响 函 数 的影 响 , 因 而
为 影响工件 加工 表 面 质 量 和 加工效率 的 主 要 因 素u J 。如 何避 免 颤振 , 一 直 以来 都 是一个 重要 的研 究 内容 。为了通过对铣削稳定性 的预测来确定合适
An a l y s i s o f Dy n a mi c Ch a r a c t e r i s i t c s o f
Hi g h S p e e d S p i n d l e — Ho l d e r - T o o l S y s t e m
C HAI Y i n - g a n g,M E N G De - h a o,LONG Xi n - h u a,M E N G Gu a n g
摘 要: 基 于导纳耦 合分析法 , 建立 高速轴一夹 具一 刀具 系统模型 , 得 到不 同转速下 刀具端 点处的频响函数 , 并采
用半离 散分析法 , 对变 刚度 铣削加工 过程 的稳 定性进行分 析, 研 究主轴转速对 铣削稳 定性的影 响。结果表 明, 考虑轴 承变剐度 的影响 , 在 高速 情况下铣削加工稳定 曲线 向低转速 方向偏 移, 且临界铣 削深度 明显 降低 。 关键 词: 振动 与波 ;高速主轴 ;导纳耦合 分析 法; 半 离散分析法; 稳 定性图 中图分类号: T H1 1 3 文献标识码 : A DO I 编码 : 1 0 . 3 9 6 9 / j . i s s n . 1 0 0 6 . 1 3 3 5 . 2 0 1 3 。 0 6 . 0 0 6
铝合金高速铣削中切削温度动态变化规律的试验研究
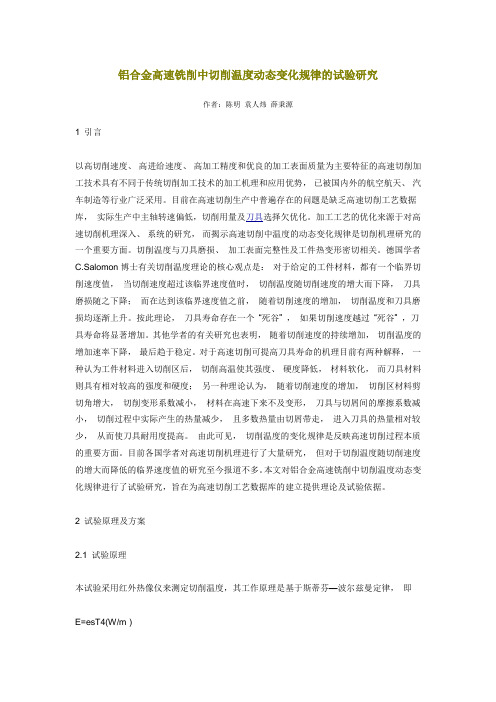
铝合金高速铣削中切削温度动态变化规律的试验研究作者:陈明袁人炜薛秉源1 引言以高切削速度、高进给速度、高加工精度和优良的加工表面质量为主要特征的高速切削加工技术具有不同于传统切削加工技术的加工机理和应用优势,已被国内外的航空航天、汽车制造等行业广泛采用。
目前在高速切削生产中普遍存在的问题是缺乏高速切削工艺数据库,实际生产中主轴转速偏低,切削用量及刀具选择欠优化。
加工工艺的优化来源于对高速切削机理深入、系统的研究,而揭示高速切削中温度的动态变化规律是切削机理研究的一个重要方面。
切削温度与刀具磨损、加工表面完整性及工件热变形密切相关。
德国学者C.Salomon博士有关切削温度理论的核心观点是:对于给定的工件材料,都有一个临界切削速度值,当切削速度超过该临界速度值时,切削温度随切削速度的增大而下降,刀具磨损随之下降;而在达到该临界速度值之前,随着切削速度的增加,切削温度和刀具磨损均逐渐上升。
按此理论,刀具寿命存在一个“死谷” ,如果切削速度越过“死谷” ,刀具寿命将显著增加。
其他学者的有关研究也表明,随着切削速度的持续增加,切削温度的增加速率下降,最后趋于稳定。
对于高速切削可提高刀具寿命的机理目前有两种解释,一种认为工件材料进入切削区后,切削高温使其强度、硬度降低,材料软化,而刀具材料则具有相对较高的强度和硬度;另一种理论认为,随着切削速度的增加,切削区材料剪切角增大,切削变形系数减小,材料在高速下来不及变形,刀具与切屑间的摩擦系数减小,切削过程中实际产生的热量减少,且多数热量由切屑带走,进入刀具的热量相对较少,从而使刀具耐用度提高。
由此可见,切削温度的变化规律是反映高速切削过程本质的重要方面。
目前各国学者对高速切削机理进行了大量研究,但对于切削温度随切削速度的增大而降低的临界速度值的研究至今报道不多。
本文对铝合金高速铣削中切削温度动态变化规律进行了试验研究,旨在为高速切削工艺数据库的建立提供理论及试验依据。
高速铣削加工技术

模具高速铣削加工技术一、前言在现代模具生产中,随着对塑件的美观度及功能要求得越来越高,塑件内部结构设计得越来越复杂,模具的外形设计也日趋复杂,自由曲面所占比例不断增加,相应的模具结构也设计得越来越复杂。
这些都对模具加工技术提出了更高要求,不仅应保证高的制造精度和表面质量,而且要追求加工表面的美观。
随着对高速加工技术研究的不断深入,尤其在加工机床、数控系统、刀具系统、CAD/CAM软件等相关技术不断发展的推动下,高速加工技术已越来越多地应用于模具型腔的加工与制造中。
数控高速切削加工作为模具制造中最为重要的一项先进制造技术,是集高效、优质、低耗于一身的先进制造技术。
相对于传统的切削加工,其切削速度、进给速度有了很大的提高,而且切削机理也不相同。
高速切削使切削加工发生了本质性的飞跃,其单位功率的金属切除率提高了30%~40%,切削力降低了30%,刀具的切削寿命提高了70%,留于工件的切削热大幅度降低,低阶切削振动几乎消失。
随着切削速度的提高,单位时间毛坯材料的去除率增加了,切削时间减少了,加工效率提高了,从而缩短了产品的制造周期,提高了产品的市场竞争力。
同时,高速加工的小量快进使切削力减少了,切屑的高速排出减少了工件的切削力和热应力变形,提高了刚性差和薄壁零件切削加工的可能性。
由于切削力的降低,转速的提高使切削系统的工作频率远离机床的低阶固有频率,而工件的表面粗糙度对低阶频率最为敏感,由此降低了表面粗糙度。
在模具的高淬硬钢件(HRC45~HRC65)的加工过程中,采用高速切削可以取代电加工和磨削抛光的工序,从而避免了电极的制造和费时的电加工,大幅度减少了钳工的打磨与抛光量。
对于一些市场上越来越需要的薄壁模具工件,高速铣削也可顺利完成,而且在高速铣削CNC加工中心上,模具一次装夹可完成多工步加工。
高速加工技术对模具加工工艺产生了巨大影响,改变了传统模具加工采用的“退火→铣削加工→热处理→磨削”或“电火花加工→手工打磨、抛光”等复杂冗长的工艺流程,甚至可用高速切削加工替代原来的全部工序。
- 1、下载文档前请自行甄别文档内容的完整性,平台不提供额外的编辑、内容补充、找答案等附加服务。
- 2、"仅部分预览"的文档,不可在线预览部分如存在完整性等问题,可反馈申请退款(可完整预览的文档不适用该条件!)。
- 3、如文档侵犯您的权益,请联系客服反馈,我们会尽快为您处理(人工客服工作时间:9:00-18:30)。
Absr c Du i g c ti g t e sr t r la d p o e s d na c r n rnsc ly c u e Th t a t: rn u tn h tucu a n r c s y misa e i ti i al o pld. e vb ai n f t e mil g s se patc lry i i h s e d i r to s o h li y t m ri u a l n h g - p e miln t ro ae he fr e n li g dee ir t t o c sg l a u e y t e f r e s n o a S inas me s r d b h oc e s r s y a KI TLER y a mee . n t i a e ,h y d n mo t r I h s p p r t e d — n mi so h li g s se i n l s d.T i r to ft e wo k i c r a u e a c ft e miln y t m s a ay e he vb ains o h r p e e wee me s r d
文 章 编 号 :6 3— 0 2 2 1 )2— 0 2— 4 17 0 6 (0 1 0 0 2 0
高速 铣削 系统 切削力动态分析
李世 春 , 彭 程
( 长江 师范 学院 机械工程学 院 , 重庆 4 8 0 ) 0 0 3
摘
要: 工件 的切 削加 工与过 程 动 态力 学之 间存在 着必然 的 内在 联 系. 由于铣 削 系统
第2 5卷第 2期
2 1 年 6月 01
南 华大学学报 ( 自然科 学 版 ) Junl f nvri f ot C i ( cec n ehooy ora o iesyo uy hn SineadT cnlg) U t S a
Vo. No 2 125 .
J n 2 1 u.01
关 键词 : 削 ; 铣 高速 ; 削力 ; 切 测量 中 图分 类 号 :H1 T 6 文 献标 识码 : A
Dy m iso il g S se nd Fo c e s r me t n Hi h-p e i i na c fM l n y t m a r e M a u e n si g s e d M l n i lg
相 对 稳定 的切 削力 对 于降 低刀 具 的磨损 及 提 高加 工零 件 表 面质 量 非 常 重 要 , 得 瞬 时切 削 力 获
收 稿 日期 :0 1 ) 一1 2 1 一( l 1
数据 有利 于对 机 床 主轴 、 件 系统 和 铣 削 加 工 过 工
me t lr s t r v ha n h g p e li g o t e h ir to s a ii g fo t e a n a e ulsp o e t ti ih s e d miln fse lt e vb ai n , rsn r m her l— tv l to g i a t c i o main me h nim , n e o a c fe t c n o e in r d i ie y sr n mp c , h p f r to c a s a d r s n n e efc s, a n tb g o e n
LI Sh ・ hu PENG e g ic n, Ch n
( co l f c a i l n ier g Y n t om l nvri , hn qn 0 0 3 C ia Sh o o h nc g ei , a g eN r a U iesy C o gig4 8 0 , hn ) Me aE n n z t
t e a l ss o he c tn o c n r c s . h nay i ft ut g fr e a d p o e s i
k y wo ds: i i g; g p e ; ut n o c me s r m e t e r m l n hih s e ds c t g fr e; a u e n s l i
中的振 动 , 别 高速 铣 削加 工 过 程 中的振 动 , 运 用 K S L R 测 力 计 系统 测 量切 削 特 在 IT E
力时 , 常会 出现信 号 失真 现 象. 通 文章 进 行 了铣 削 系统 的 动 力 学 分析 , 量 了切 削过 测
程 中工件 的振 动 , 估算 了工件 的惯 性 力 、 力 计 等 效质 量 和 测 定 的 力 学数据 增量 . 测 试 验 结果 表 明 , 高速铣 削硬 钢 构件 时的振 动 , 由较 强 的冲 击 、 屑 形 成机 理 以及 共振 是 切 所产 生 , 些 因素 在分 析切 削力和切 削过程 时 不容 忽视 . 这