钢铁能耗1
钢铁行业铁合金单位产品能源消耗限额标准

3、标准主要内容及分析
1. 能耗指标设定原则 2. 能耗统计范围及计算方法 3. 能耗限额指标取值
3.1 能耗指标设定原则
■ 指标项目
■ 限额值(淘汰落后)
■ 先进值(国际领先水平)
铁合金单位产品能耗的先进值依据目前国际或国内先进水平确定的。
3.2 能耗统计范围及计算方法
➢铁合金产品能耗统计范围
铁合金工序能耗应包括用于加热炉料、维持正常炉况耗用的冶炼 电力能源消耗,用于还原矿石所需的碳质还原剂(冶金焦丁或气煤半 焦焦粒)消耗,以及生产加工过程中的原料准备、供应、冶炼、合金 浇注、精整和物料与合金运输的动力耗能,扣除工序回收并外供的能 源后的实际消耗的各种能源总量。
综合能耗限额准入值(以电等价 值0.404kgce/kWh计),kgce/t
1910 4440
入炉矿品位
/
备 注
入炉矿品位每升高降低1%, 电耗限额值可降低升高值,
/
kWh/t
2600 710 1500 Mn34% 60
4200 990
3200 焦炭1320 kg/t
810
—
2260
1780
1220
本标准中对铁合金单位产品能耗限额值的取值大致是按照淘汰现有产 能约2400万吨(2007年前未含工业硅和电解锰的产能)、3500万吨 (2010年前的产能)中30% 35%左右的落后产能考虑的 。
■ 准入值(新建设备准入门槛)
铁合金单位产品能耗限额的准入值是根据较大容量(12.5MVA电炉) 装备规模、按照较好的水平来确定的。
钢铁烧结工序能耗计算公式
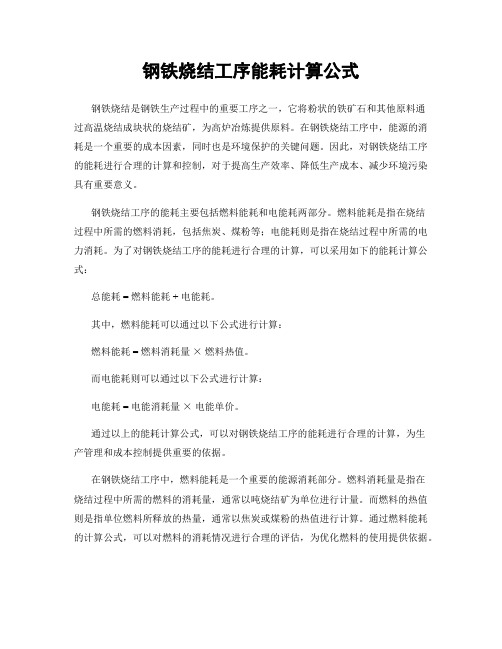
钢铁烧结工序能耗计算公式钢铁烧结是钢铁生产过程中的重要工序之一,它将粉状的铁矿石和其他原料通过高温烧结成块状的烧结矿,为高炉冶炼提供原料。
在钢铁烧结工序中,能源的消耗是一个重要的成本因素,同时也是环境保护的关键问题。
因此,对钢铁烧结工序的能耗进行合理的计算和控制,对于提高生产效率、降低生产成本、减少环境污染具有重要意义。
钢铁烧结工序的能耗主要包括燃料能耗和电能耗两部分。
燃料能耗是指在烧结过程中所需的燃料消耗,包括焦炭、煤粉等;电能耗则是指在烧结过程中所需的电力消耗。
为了对钢铁烧结工序的能耗进行合理的计算,可以采用如下的能耗计算公式:总能耗 = 燃料能耗 + 电能耗。
其中,燃料能耗可以通过以下公式进行计算:燃料能耗 = 燃料消耗量×燃料热值。
而电能耗则可以通过以下公式进行计算:电能耗 = 电能消耗量×电能单价。
通过以上的能耗计算公式,可以对钢铁烧结工序的能耗进行合理的计算,为生产管理和成本控制提供重要的依据。
在钢铁烧结工序中,燃料能耗是一个重要的能源消耗部分。
燃料消耗量是指在烧结过程中所需的燃料的消耗量,通常以吨烧结矿为单位进行计量。
而燃料的热值则是指单位燃料所释放的热量,通常以焦炭或煤粉的热值进行计算。
通过燃料能耗的计算公式,可以对燃料的消耗情况进行合理的评估,为优化燃料的使用提供依据。
另外,电能耗也是钢铁烧结工序中的重要能耗部分。
电能消耗量是指在烧结过程中所需的电能的消耗量,通常以千瓦时为单位进行计量。
而电能单价则是指单位电能的价格,通常以元/千瓦时为单位进行计算。
通过电能耗的计算公式,可以对电能的使用情况进行合理的评估,为降低电能消耗提供依据。
除了能耗的计算,钢铁烧结工序中还可以采取一系列的节能措施,进一步降低能耗。
例如,可以优化燃料的配比和燃烧条件,提高燃料的利用率;可以采用先进的烧结设备和技术,提高生产效率;可以采用余热回收技术,充分利用余热资源。
通过这些节能措施的实施,可以进一步降低钢铁烧结工序的能耗,减少生产成本,提高经济效益。
钢铁生产过程中的能源消耗如何降低

钢铁生产过程中的能源消耗如何降低钢铁行业作为国民经济的重要支柱产业,在为社会发展提供重要基础材料的同时,也面临着能源消耗巨大的挑战。
降低钢铁生产过程中的能源消耗,不仅对于企业降低成本、提高竞争力具有重要意义,也是实现可持续发展、应对全球能源危机和环境压力的必然要求。
在钢铁生产的各个环节中,都存在着不同程度的能源消耗。
首先是原料准备阶段,包括矿石开采、选矿和运输等。
矿石的开采需要消耗大量的电能和燃料,而选矿过程中的破碎、磨矿等作业也需要消耗不少能源。
在运输环节,长距离的运输会增加能源的消耗。
接下来是炼铁环节,这是钢铁生产中能源消耗最大的部分之一。
高炉炼铁需要消耗大量的焦炭作为还原剂和燃料,同时还需要消耗大量的热风来提供热量。
此外,高炉的鼓风系统、炉顶煤气余压回收装置等设备的运行也需要消耗电能。
炼钢环节同样消耗大量能源。
转炉炼钢需要消耗氧气、电能等,电炉炼钢则主要消耗电能。
在精炼过程中,如 LF 炉、RH 炉等设备的运行也需要消耗电能和热能。
轧钢环节的能源消耗主要来自加热炉,用于将钢坯加热到合适的轧制温度。
此外,轧机的运行也需要消耗电能。
为了降低钢铁生产过程中的能源消耗,可以从以下几个方面入手:一是采用先进的生产工艺和技术。
例如,推广使用高炉喷煤技术,可以减少焦炭的使用量,从而降低能源消耗。
在炼钢环节,采用转炉负能炼钢技术,通过回收转炉煤气和蒸汽等,实现能源的再利用。
另外,连铸连轧技术的应用,可以减少钢坯的加热次数,降低能源消耗。
二是优化设备运行和管理。
定期对设备进行维护和保养,确保设备处于良好的运行状态,减少设备故障和停机时间,提高设备的运行效率。
同时,采用先进的自动化控制系统,对生产过程进行精确控制,实现能源的合理分配和利用。
三是加强能源管理。
建立完善的能源管理体系,对能源的使用进行监测和分析,找出能源消耗的重点环节和部位,采取针对性的节能措施。
例如,通过安装能源计量仪表,对能源的消耗进行实时监测和统计,为能源管理提供数据支持。
钢铁行业单位产品能耗限额标准

钢铁行业单位产品能耗限额标准
钢铁行业的单位产品能耗限额标准因不同的产品种类和生产工艺而有所不同。
在中国,针对钢铁行业,国家制定了相应的能耗限额标准,其中包括了不同的产品种类的能耗限额标准。
以下是一些常见的钢铁产品能耗限额标准:
1. 转炉钢吨钢综合能耗:≤ /t;
2. 电炉钢吨钢综合能耗:≤ /t;
3. 轧钢综合能耗:≤ /t;
4. 高炉炼铁工序单位产品能耗:≤ 437kgce/t;
5. 转炉炼钢工序单位产品能耗:≤ 122kgce/t;
6. 电炉炼钢工序单位产品能耗:≤ 120kgce/t;
7. 烧结工序单位产品能耗:≤ /t;
8. 球团工序单位产品能耗:≤ /t。
需要注意的是,这些标准是针对不同的钢铁产品种类和生产工艺而制定的,而且随着技术的不断进步和环保要求的提高,这些标准也在不断更新和调整。
因此,在实际生产中,钢铁企业需要按照最新的标准进行节能降耗,以实现可持续发展。
钢铁能耗分析

kg 标煤/t 60.38 63.83 63.47 59.75 kg 标煤/t 395.47 453.91 443.11 488.16 kg 标煤/t 6.81 13.03 5.29 20.85 kg 标煤/t 186.96
kWh/t 36.21 12.45 33.20 22.10
——绝大部分企业仍然存在较大的差距。
国内企业比较:
——铁工序是钢铁生产能耗最大的工序,2003 年较 2002 年全国总体呈现略微上升趋势; 各企业差距较大,宝钢 2003 年炼铁工序能耗 395kgce/ t,全国平均为 465kgce/t,相差 70kgce/t;
——钢工序能耗在吨钢综合能耗中不可忽视,国内 2003 年平均水平为 23.56kgce/t, 宝钢、武钢连续两年实现转炉负能炼钢,优于国内平均水平约 25kgce/t;
宝钢 EMS 使分布于宝钢全厂范围的全部变电所(室)、排水泵站和给排水设施、煤气加压 站、煤气混合站及能源分配设施等通过计算机网络联结在一起,实现能源系统的分散控制、 集中管理、优化分配。
(1)可以减少能源中心定员,节约成本,提高工作效率。
(2)调度管理人员可以更全面地了解能源系统,提高能源管理水平.
1995 年 2002 年 13.27 12.41 79.2 81.1
国际先进 7(美国) 84-85
180.69 149.38
128.03
53.00 1.36
56.60 1.491
58.67(日本)
日历作业率/% 结
工序能耗/(标煤)/kg·t-1
入炉矿品位/%
高
利用系数/t·m-3.d-1
热风温度/℃
0.755
0.08
钢铁行业主要生产工序能耗指标标杆值

附件1 钢铁行业主要生产工序能耗指标标杆值
表1-1 粗钢综合性指标标杆值
表1-2 焦化工序标杆值
表1-3 烧结工序标杆值
表1-4 球团工序标杆值
表1-5 炼铁工序标杆值
表1-6 转炉炼钢工序标杆值
表1-7 电炉炼钢工序标杆值
表1-8 轧钢工序标杆值
注[1]:国家标准指《焦炭单位产品能源消耗限额》(GB21342-2008)
注[2]:国家标准指《粗钢生产主要工序单位产品能源消耗限额》(GB21256-2007)、《清洁生产标准钢铁行业(烧结)》(HJ/T426-2008)、《清洁生产标准钢铁行业(高炉炼铁)》(HJ/T427-2008)、《清洁生产标准钢铁行业(炼钢)》(HJ/T428-2008)、国标《钢铁企业节能设计规范》(2010年送审稿)。
工信部钢铁能耗标准
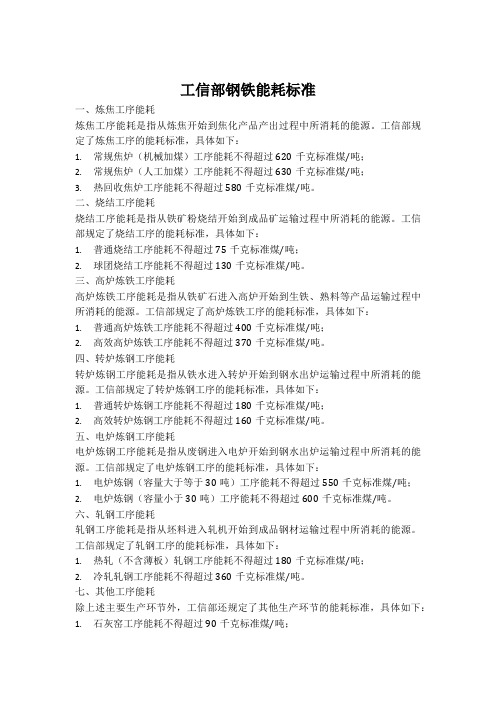
工信部钢铁能耗标准一、炼焦工序能耗炼焦工序能耗是指从炼焦开始到焦化产品产出过程中所消耗的能源。
工信部规定了炼焦工序的能耗标准,具体如下:1.常规焦炉(机械加煤)工序能耗不得超过620千克标准煤/吨;2.常规焦炉(人工加煤)工序能耗不得超过630千克标准煤/吨;3.热回收焦炉工序能耗不得超过580千克标准煤/吨。
二、烧结工序能耗烧结工序能耗是指从铁矿粉烧结开始到成品矿运输过程中所消耗的能源。
工信部规定了烧结工序的能耗标准,具体如下:1.普通烧结工序能耗不得超过75千克标准煤/吨;2.球团烧结工序能耗不得超过130千克标准煤/吨。
三、高炉炼铁工序能耗高炉炼铁工序能耗是指从铁矿石进入高炉开始到生铁、熟料等产品运输过程中所消耗的能源。
工信部规定了高炉炼铁工序的能耗标准,具体如下:1.普通高炉炼铁工序能耗不得超过400千克标准煤/吨;2.高效高炉炼铁工序能耗不得超过370千克标准煤/吨。
四、转炉炼钢工序能耗转炉炼钢工序能耗是指从铁水进入转炉开始到钢水出炉运输过程中所消耗的能源。
工信部规定了转炉炼钢工序的能耗标准,具体如下:1.普通转炉炼钢工序能耗不得超过180千克标准煤/吨;2.高效转炉炼钢工序能耗不得超过160千克标准煤/吨。
五、电炉炼钢工序能耗电炉炼钢工序能耗是指从废钢进入电炉开始到钢水出炉运输过程中所消耗的能源。
工信部规定了电炉炼钢工序的能耗标准,具体如下:1.电炉炼钢(容量大于等于30吨)工序能耗不得超过550千克标准煤/吨;2.电炉炼钢(容量小于30吨)工序能耗不得超过600千克标准煤/吨。
六、轧钢工序能耗轧钢工序能耗是指从坯料进入轧机开始到成品钢材运输过程中所消耗的能源。
工信部规定了轧钢工序的能耗标准,具体如下:1.热轧(不含薄板)轧钢工序能耗不得超过180千克标准煤/吨;2.冷轧轧钢工序能耗不得超过360千克标准煤/吨。
七、其他工序能耗除上述主要生产环节外,工信部还规定了其他生产环节的能耗标准,具体如下:1.石灰窑工序能耗不得超过90千克标准煤/吨;2.耐火材料及制品生产工序能耗不得超过450千克标准煤/吨;3.铁合金生产(包括硅系、锰系等)工序能耗不得超过580千克标准煤/吨。
钢铁能耗限额标准

钢铁能耗限额标准钢铁能耗限额标准是指国家针对钢铁行业制定的能源消耗限制标准,旨在促进钢铁行业的节能减排和可持续发展。
该标准是中国政府在推进绿色发展、加强环境保护的背景下,为了实现能源消耗总量控制和结构调整而制定的重要政策措施。
钢铁行业是我国重要的基础产业之一,但同时也是能源消耗最大的行业之一。
据统计,我国钢铁行业的能源消耗占全国能源消耗总量的15%左右,排放的二氧化碳占全国总量的20%以上。
因此,制定钢铁能耗限额标准,对于实现我国能源消耗总量控制和结构调整具有重要意义。
钢铁能耗限额标准的制定,主要是通过对钢铁企业的能源消耗进行限制,促进企业采用更加节能环保的生产方式和技术,从而实现能源消耗的降低和环境污染的减少。
具体来说,钢铁能耗限额标准主要包括以下几个方面:1. 能源消耗限额。
根据钢铁企业的生产规模、产品品种和技术水平等因素,制定相应的能源消耗限额标准,要求企业在生产过程中严格控制能源消耗,降低能源消耗强度。
2. 能源结构调整。
钢铁企业要根据能源消耗限额标准,逐步调整能源结构,采用更加清洁、高效的能源,如天然气、风能、太阳能等,减少对煤炭等传统能源的依赖。
3. 技术创新。
钢铁企业要加强技术创新,推广先进的节能环保技术,提高生产效率和产品质量,降低能源消耗和环境污染。
4. 管理措施。
钢铁企业要建立健全的能源管理体系,加强能源消耗监测和统计,制定能源消耗计划和节能措施,加强能源消耗的监督和管理。
总之,钢铁能耗限额标准的制定,是我国推进绿色发展、加强环境保护的重要举措,对于实现能源消耗总量控制和结构调整具有重要意义。
钢铁企业要积极响应国家政策,加强节能减排,推广清洁能源,加强技术创新,实现可持续发展。
同时,政府也应加强监管和执法力度,确保钢铁企业严格遵守能耗限额标准,促进钢铁行业的绿色发展。
- 1、下载文档前请自行甄别文档内容的完整性,平台不提供额外的编辑、内容补充、找答案等附加服务。
- 2、"仅部分预览"的文档,不可在线预览部分如存在完整性等问题,可反馈申请退款(可完整预览的文档不适用该条件!)。
- 3、如文档侵犯您的权益,请联系客服反馈,我们会尽快为您处理(人工客服工作时间:9:00-18:30)。
环境因素推进了钢铁工业的发展据世界银行中国环境报告,中国GDP总量占世界经济总量4%,但消耗的钢材却占世界消耗总量的
21%,煤炭的31%,铝的25%,水泥的40%
这些产品高消耗的直接结果就是高污染,我们可以看到,钢材、煤炭、铝、水泥,这都是高能耗、高污染的产业,造成了严重的水资源和空气的污染。
因此,控制高耗能产业的发展成为必然的选择。
2005年以后,我国钢铁产能持续高速增长,但增长方式仍然没有摆脱传统的粗放增长方式,低水平重复建设现象十分严重。
2003年国家对钢铁行业果断采取宏观调控政策,对抑制投资过热、低水平重复建设起到了明显效果,2006年在全社会固定资产投资比上年增长24%①的情况下,钢铁行业投资额
2247亿,比上年下降2.5%,宏观调控的效果初步显现。
环境优化增长是经济发展的大趋势
中央提出节能减排,把能耗和主要污染物排放总量作为两大约束性指标,作为不可逾越的‘红线’,寓意是十分深刻的。
因为这两大指标在很大程度上反映了经济增长方式和产业结构的状况,反映了
经济运行的质量,直接关系到经济社会长远发展。
因此,越是固定资产投资增幅过大,越是经济增长速度加快,越要坚决落实目标不动摇。
确定每年削减2%的污染物排放总量,就是要‘积小胜为大胜’,每年对照指标,衡量进展情况,分析主客观原因,找出存在差距,及时制定措施,通过持续施加压力,调动各方面的力量,既要依靠污染治理措施,又要依靠经济结构优化升级,不断加大削减力度,努力实现削减目标。
这是在当前形势下?D?D环境优化增长,
促进经济增长方式转变的重要内容。
当前我国钢铁工业发展中节能减排情况
2.1钢铁产能仍保持较快增长
2006年,全国粗钢产量4.2266亿吨①,比上年增长19.7%,相当于世界排名第二、第三、第四、第五的日本、美国、俄罗斯、韩国钢产量之合。
截至2006年已连续11年位居世界钢产量第一,占世界粗钢产量的比重由2000年的15.26%上升到2006年的34.1%,占全世界钢产量的三分之一。
2.2钢铁工业整体能源消耗进一步增长
2006年纳入统计的大中型钢铁企业总能耗19779.05万吨标煤,比上年同期增加1540.55万吨标
煤耗,增长8.45%。
2006年吨钢综合能耗645.12千克标煤/吨,同比下降7.06%;吨钢可比能耗623.04千克标煤/吨,同比下降6.19%;吨钢消耗新水6.56吨/吨,同比下降14.9%。
由于钢铁总产量大幅增长,虽吨钢可比能耗下降,但总能耗上升,所以,污染物排放量总体上升,
加大了减排的压力。
据统计,2005年我国大中型钢铁企业吨钢可比能耗比发达国家高出9.85%,全行业能耗平均水平
与国外先进水平差距估计在15%左右。
2.3钢铁工业整体污染物排放总量加大
据统计,钢铁行业排放废水量约占全国总排废水量的8%,SO2排放量约占7%,烟尘量约占8%、
粉尘约占15%,固废产生量约占13%。
2006年我国钢铁行业的铁、钢和钢材的产量都超过了4亿吨,但是按照“钢铁产业发展政策”的
要求,到2005年底,钢铁行业的落后产能炼铁
9880万吨,占总生产能力的24.2%;炼钢5500万吨,占总生产能力的13.29%;轧钢7900万吨,占总生产能力的18.81%。
因此,淘汰落后产能,仍是钢铁工业整体发展的关键。
环境优化钢铁工业增长的途径分析
3.1严格控制钢铁工业新增产能
一些大型钢铁企业节能减排成效很大,但整体污染物排放量加大,因此,加快淘汰落后生产能力,提高钢铁工业发展的质量是钢铁工业发展的必然选择。
国家发改委在通知中要求,加快兼并重组,产业集中度有所提高,形成2-3个3000万吨级、若干个千万吨级的具有国际竞争力的大型钢铁企业集团,国内排名前10位的钢铁企业集团钢产量占全国的比例达到50%以上。
这是从发展的源头,优化钢铁工业的增长。
3.2依靠科技进步提高企业发展的内力
我国环境污染的形势严峻,节能减排的压力非常大,完成节能减排指标已经成为当地政府第一把手的主要责任。
因此,只有提高企业发展的内力才是最佳选择。
2006年底对大中型钢铁企业进行统计,高炉安装炉顶压差发电装置(TRT)的座数,仅占总数的31%;安装高炉煤气回收装置的高炉,占总数的77%;安装转炉煤气回收装置的转炉,占总数的64%;安装转炉
余热蒸汽回收装置的转炉,占总数的68%。
节能技术应用方面还有较大空间和潜力。
如:烧结矿余热回收、高风温热风炉、高炉余压发电
(TRT)、高炉喷煤、干熄焦(CDQ)、转炉负能炼钢、转炉烟道汽化冷却、轧钢蓄热式加热炉等,进一步
提高高炉煤气、转炉煤气等二次能源回收利用率。
应加大节能减排资金的投入,进一步提高节能减排先进工艺技术的普及面,提高回收利用的有效
率。
3.3推行清洁生产标准,强化经济政策,强制规范企业的环境行为
为贯彻《中华人民共和国环境保护法》和《中华人民共和国清洁生产促进法》,保护环境,保障人体健康,促进清洁生产,国家环境保护总局决定制定《清洁生产标准
钢铁行业(炼钢)》等七项国家环境保护行业标准。
目前,标准编制单位已编制完成标准的征求
意见稿。
清洁生产标准的编制和发布,是引导和推动企业清洁生产的需要;是环保工作加快推进历史性转变,提高环境准入门槛,推动实现环境优化经济增长的重要手段;是完善国家环境标准体系,加强污染全过程控制的需要。
清洁生产标准将作为强制性清洁生产审核的依据,环境影响评价的依据和环境友好企业
评估的依据。
加大运用经济政策推动淘汰落后产能。
对落后产能实施更严格的差别电价与差别水价,压缩落后产品利润空间,促其尽快退出市场。
为了解决企业的外部不经济性问题,正在制定经济赔偿政策。
3.4淘汰落后产能,提高钢铁工业发展的质量
国家公布的《产业结构调整指导目录》中,800立方米及以下的小高炉要淘汰,产能达9980万吨;
20吨及以下的小转炉和小电炉要淘汰,产能达5500万吨。
目前,不符合产业政策的落后炼铁能力约1亿吨,落后炼钢能力约5500万吨,这些设备容量小、效率低、污染重,单位能耗大,对于实现“十一五”可持续发展目标十分重要。
各地应加大执法力度,对不符合国家产业政策、未经环保审批的落后钢铁企业协同有关部门依法
关停。
3.5积极开展规划环评,使钢铁工业有序发展
2006年,中国粗钢产量4.2亿吨,位居全球第一。
但不符合产业政策的落后炼铁能力约占总产能
的24.2%,落后炼钢能力占总产能的
13.3%。
如果把这些落后产能淘汰掉,一年可以节能5000多万吨标准煤,1亿吨水。
我国75家重点钢铁企业中,有26家建在直辖市和省会城市,34家建在百万人口以上大城市,由于城市对环保要求越来越高,钢铁行业与城市发展的矛盾也越来越大。
这是典型的布局与结构问题。
因此,开展规划环评是
钢铁工业发展的必然选择。
通过规划环评促进钢铁行业健康有序发展,通过规划环评优化发展和布局。
钢铁生产重点省份,均已编制“十一五”钢铁工业发展规划。
应在此基础上,尽快开展规划环评,从环境容量、资源承载力、节能减排、淘汰落后产能等角度优化发展规模、调整发展思路,使之符合可持续发展的要求,实现绿色制
造。
建议钢产量大省和环境问题突出的地区,如河北、辽宁、山东、江苏、上海等省市,优先开展钢铁工业可持续发展规划环评。
上述区域内钢铁项目必须在钢铁工业规划环评通过后受理和审批。
科学发展观与生态文明为钢铁工业的发展导航
十七大明确提出,在优化结构、提高效益、降低消耗、保护环境的基础上,实现人均国内生产总值到二0二0年比二000年翻两番的目标。
并着重指出:“经济增长的资源环境代价过大”,为此提出“发展是第一要义”与“生态文明”的概念,这是我国多年来在经济发展中处理经济发展与环境保护问题的重要经验,是实施可持续发展战略的总结,也是人类对人与自然关系所取得的最重要认识成果的继承和发展。
这充分体现了“发展是第一要义”与“生态文明”对中华民族生存发展的重要意义。
我们的责任是把“发展是第一要义”与“生态文明”的理念变为行动物质决定精神,存在决定意识。
在一定的经济基础之上,必然要有一定的上层建筑包括意识形态与之相适应。
一个社会的存在和发展,既需要以生产力的发展为基础,所以说“发展是第一要义”。
同时也离不开精神、文明的发展,生态文明,是人类社会发展进步的一个重要内容,也是社会发展在精神领域的一个重要标志。
我们要遵循经济基础决定上层建筑的要求,在发展的前提下,建立起可持续发展的生态文明,为科学发展观是用来指导发展的,离开了发展,科学发展观就成了无源之水、无本之木。
发展是一个永无止境的历史过程,指导发展的观念也必须与时俱进。
生态文明主要指人们在改造客观物质世界的同时,不断克服改造过程中的负面效应,积极改善和优化人与自然、人与人的关系,建设有序的生态运行机制和良好的生态环境。
在生产方式上,转变高生产、高消费、高污染的工业化生产方式,以生态技术为基础实现社会物质生产的生态化,使生态产业在产业结构中居于主导地位,成为经济增长的主要源泉。
发展观的改变,生态文明的建立是一个长期的过程,改变发展的模式,生态文明的建立需要一定的时间,我国市场化进程还需要深化,涉及到机制与体制问题只能逐步克服,因此,在钢铁工业发展过程
中,环境优化钢铁工业增长的因素会长期存在。