(完整版)我国钢铁工业能耗现状和节能潜力分析
钢厂能源总结报告范文(3篇)

第1篇一、前言随着全球能源需求的不断增长和环境保护意识的日益增强,钢铁行业的能源管理和优化成为企业可持续发展的关键。
本报告旨在总结我国某钢厂在能源管理、技术创新、节能减排等方面的成果和经验,为我国钢铁行业的能源革命提供参考。
二、能源消耗现状1. 能源结构我国某钢厂目前主要能源包括煤炭、电力、天然气等。
其中,煤炭占能源消耗的60%,电力占30%,天然气占10%。
能源结构较为单一,存在较大的优化空间。
2. 能源消耗总量根据统计数据,某钢厂年能源消耗量约为100万吨标准煤。
其中,炼铁、炼钢、轧钢等主要生产环节能源消耗量较大。
3. 能源利用效率某钢厂能源利用效率总体处于行业平均水平。
通过优化生产工艺、提高设备运行效率等措施,能源利用效率逐年提高。
三、能源管理措施1. 建立健全能源管理制度某钢厂制定了完善的能源管理制度,明确各级人员的能源管理职责,确保能源管理工作有序开展。
2. 开展能源审计定期对生产、生活、办公等领域的能源消耗进行审计,找出能源浪费环节,提出改进措施。
3. 推广节能技术(1)炼铁环节:采用高炉煤气余压发电(TRT)技术,提高能源利用率;推广富氧炼铁技术,降低焦炭消耗。
(2)炼钢环节:采用转炉炉顶煤气循环利用(OGC)技术,降低能源消耗;推广钢包烘烤技术,提高热能利用率。
(3)轧钢环节:采用余热回收技术,提高能源利用率。
4. 加强设备管理定期对设备进行维护保养,提高设备运行效率,降低能源消耗。
5. 开展节能培训提高员工节能意识,培养节能人才,为节能减排工作提供人才保障。
四、节能减排成果1. 能源消耗降低通过实施节能减排措施,某钢厂年能源消耗量较2010年降低20%。
2. 污染物排放减少二氧化硫、氮氧化物、烟粉尘等污染物排放量分别降低30%、50%和70%。
3. 经济效益提升节能减排措施的实施,使某钢厂每年节约成本约1亿元。
五、未来展望1. 优化能源结构加大新能源应用力度,逐步降低煤炭等传统能源消耗比例。
钢铁工业能源现状和管理

钢铁工业能源现状和管理1. 简介钢铁工业是现代工业领域中的重要组成部分,它对经济发展和社会进步具有重要意义。
然而,钢铁生产过程中对能源的需求量大、能耗高,给能源资源带来了巨大压力。
为了可持续发展和减少环境负荷,钢铁工业必须重视以及改善能源管理。
本文将从以下几个方面探讨钢铁工业能源现状和管理:能源消耗情况、环境影响、节能技术、管理措施和未来发展展望。
2. 能源消耗情况钢铁工业是能源密集型行业,对能源的需求非常大。
其主要能源消耗包括三个方面:原料预处理、高炉冶炼和炼钢。
其中,高炉冶炼占据了最大的能源消耗比重。
根据统计数据,我国钢铁工业每年消耗的能源约占全国工业总能源消耗量的15%左右。
3. 环境影响由于钢铁工业对能源的高度依赖和消耗,其对环境的影响也不可忽视。
钢铁生产过程中会产生大量的二氧化碳、氮氧化物等大气污染物,对大气质量造成了一定程度的破坏。
同时,钢铁工业在原料开采、废水排放以及废渣处理等环节也对水资源和土壤环境产生了一定程度的压力。
4. 节能技术为了减少能源消耗和降低环境负荷,钢铁工业需要采取一系列的节能技术。
以下是一些常用的节能技术:•高炉余热回收利用技术:通过回收和利用高炉煤气中的余热来提高能源利用效率。
•动态控制技术:通过实时监测和控制钢铁生产过程中的能耗和排放情况,使生产过程达到最佳能源利用效率。
•热再循环技术:将钢铁生产过程中产生的热能再循环利用,减少能源的浪费。
•新型燃料使用技术:采用新型的低碳燃料,如天然气、生物质能源等,来替代传统的煤炭、焦炭等高碳燃料,降低碳排放量。
5. 管理措施除了采用节能技术外,钢铁工业还需要建立完善的能源管理体系,强化能源管理措施。
以下是一些常见的管理措施:•能源审计:定期对钢铁生产过程中的能源消耗情况进行审计和评估,发现问题并提出改进措施。
•员工培训:加强对员工的节能意识培养和能源管理知识培训,提高员工的能源利用效率。
•制定能源消耗指标:设定合理的能源消耗目标,对能源利用情况进行定量评价,并对能源消耗指标进行动态调整。
钢铁能耗分析

kg 标煤/t 60.38 63.83 63.47 59.75 kg 标煤/t 395.47 453.91 443.11 488.16 kg 标煤/t 6.81 13.03 5.29 20.85 kg 标煤/t 186.96
kWh/t 36.21 12.45 33.20 22.10
——绝大部分企业仍然存在较大的差距。
国内企业比较:
——铁工序是钢铁生产能耗最大的工序,2003 年较 2002 年全国总体呈现略微上升趋势; 各企业差距较大,宝钢 2003 年炼铁工序能耗 395kgce/ t,全国平均为 465kgce/t,相差 70kgce/t;
——钢工序能耗在吨钢综合能耗中不可忽视,国内 2003 年平均水平为 23.56kgce/t, 宝钢、武钢连续两年实现转炉负能炼钢,优于国内平均水平约 25kgce/t;
宝钢 EMS 使分布于宝钢全厂范围的全部变电所(室)、排水泵站和给排水设施、煤气加压 站、煤气混合站及能源分配设施等通过计算机网络联结在一起,实现能源系统的分散控制、 集中管理、优化分配。
(1)可以减少能源中心定员,节约成本,提高工作效率。
(2)调度管理人员可以更全面地了解能源系统,提高能源管理水平.
1995 年 2002 年 13.27 12.41 79.2 81.1
国际先进 7(美国) 84-85
180.69 149.38
128.03
53.00 1.36
56.60 1.491
58.67(日本)
日历作业率/% 结
工序能耗/(标煤)/kg·t-1
入炉矿品位/%
高
利用系数/t·m-3.d-1
热风温度/℃
0.755
0.08
浅析钢铁企业的能耗现状及节能对策
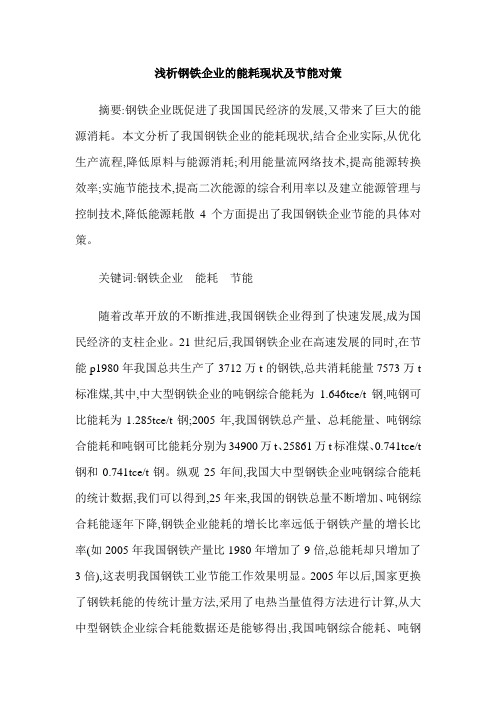
浅析钢铁企业的能耗现状及节能对策摘要:钢铁企业既促进了我国国民经济的发展,又带来了巨大的能源消耗。
本文分析了我国钢铁企业的能耗现状,结合企业实际,从优化生产流程,降低原料与能源消耗;利用能量流网络技术,提高能源转换效率;实施节能技术,提高二次能源的综合利用率以及建立能源管理与控制技术,降低能源耗散4个方面提出了我国钢铁企业节能的具体对策。
关键词:钢铁企业能耗节能随着改革开放的不断推进,我国钢铁企业得到了快速发展,成为国民经济的支柱企业。
21世纪后,我国钢铁企业在高速发展的同时,在节能p1980年我国总共生产了3712万t的钢铁,总共消耗能量7573万t 标准煤,其中,中大型钢铁企业的吨钢综合能耗为1.646tce/t钢,吨钢可比能耗为1.285tce/t钢;2005年,我国钢铁总产量、总耗能量、吨钢综合能耗和吨钢可比能耗分别为34900万t、25861万t标准煤、0.741tce/t 钢和0.741tce/t钢。
纵观25年间,我国大中型钢铁企业吨钢综合能耗的统计数据,我们可以得到,25年来,我国的钢铁总量不断增加、吨钢综合耗能逐年下降,钢铁企业能耗的增长比率远低于钢铁产量的增长比率(如2005年我国钢铁产量比1980年增加了9倍,总能耗却只增加了3倍),这表明我国钢铁工业节能工作效果明显。
2005年以后,国家更换了钢铁耗能的传统计量方法,采用了电热当量值得方法进行计算,从大中型钢铁企业综合耗能数据还是能够得出,我国吨钢综合能耗、吨钢可比能耗也是逐年下降(2008年受金融危机影响例外),2005年我国吨钢综合能耗、吨钢可比能耗分别为695kgce/t钢、714kgce/t钢,2010年这两项数据为604kgce/t钢和581kgce/t钢。
总之,我国将进30年钢铁发展历程表明我国钢铁企业节能工作取得了伟大的成就[2]。
1.2 我国钢铁企业能耗存在的问题虽然我国钢铁企业能耗逐年下降,但是从2005年起,吨钢能耗的降幅不断减少,继续节能的难度在不断增加,存在着一些突出问题:第一,我国钢铁企业能耗总体水平与发达国家先进水平相比,还存有一定差距。
中国钢铁工业节能减排效果分析与前景

问题的提 出
钢铁工 业是 国民经济 的重要 产业 ,也是 国家 推进 节能 减排工 作 的重点产 业 。钢铁 工业 能源 消耗 约 占全 国 总能耗 的 1% ,二氧化 碳排 放量 约 占全 国排 放量 的 1% ,废 水 排放 约 占工 业 废水 排 放 总量 的 5 2
1 . 5 ,粉 尘排 放约 占工业 粉尘 排放 总量 的 1. 5 ,烟尘 排放 约 占全 国烟尘 排 放 总量 的 8 3 ,二 56% 56 % .% 氧化 硫排 放 约 占全 国 工 业 二 氧 化 硫 排 放 总 量 的 7 4 ,废 气 排 放 量 约 占全 国 工 业 废 气 排 放 量 的 .%
能源利用 效率和技 术水平 等依 然低 于 国外先进 水平 。随着废钢 以及 电炉炼 钢 比重 的不 断提 高, “ 二五” 十
时期钢铁 工业的节能减 排效果将有所提升 。为了进一步加 快 中国钢铁工 业节能减 排,笔者从 需要发展完 善 的废钢收集系统、提高 电炉炼钢 比例 、淘汰落后产能、 引进与开发关键技 术等方面提 出政策措施 。 [ 关键词 ]钢铁工业;节 能减排 ; 状;前景 现 [ 中图分类号] F6 [ 02 文献标识码 ]A [ 文章编号] 17 8 9 (02)0 -0 1—1 6 4— 28 2 1 50 8 1
二 “ 一五” 期 间中 国钢铁工业发展的基 本情况 十
( )产量 情况 分析 一
“ 十一 五 ” 期 间 ,中国钢铁 产量增 长迅 速 ,据 中国钢铁 工业 协会 统计 ,20 2 1 05— 00年 ,中国粗 钢 产 量从 35 吨增长 到 62 .3亿 .7亿 吨 ,20 2 1 同 比增 长 1.7 、1.2 、23% 、1.6 和 06— 0 0年 9 8% 68 % .0 34 % 1.6 ,年均增 长 1.0 。 同时 ,中 国 粗 钢 产 量 全 球 占 比 由 20 03 % 24 % 05年 的 3. % 提 高 到 2 1 09 00年 的
钢铁企业工序能耗和节能潜力

钢铁企业工序能耗和节能潜力近年来,我国重点钢铁企业的钢、铁产量增长在16%以上,而总能耗的增长低于产量增长约5个百分点。
这说明,我国重点钢铁企业在节约能源方面做出很大成绩。
一、重点钢铁企业工序能耗情况1.近3年我国重点钢铁企业各工序能耗变化情况见表1。
从中可看出,各工序能耗中球团、转炉炼钢和焦化工序能耗呈上升态势,而烧结、电炉、轧钢工序均呈下降态势。
2.2004年各工序能耗与1999年国际先进水平相比,烧结工序差距最小,为7.49kgce/t;差距最大的是转炉炼钢工序,差值为35.45kgce/t,其次为炼铁工序,差值为28.27kgce/t。
2000年国外主要产钢国家(英、日、法、德)平均吨钢可比能耗为642kgce。
2004年我国重点钢铁企业平均吨钢可比能耗为705kgce/t,与国外主要产钢国家相比高出9.81%。
二、2004年重点钢铁企业各工序能耗分析表3列出我国重点钢铁企业各工序能耗数值、各工序能耗占钢铁工业总能耗的比例、企业先进与落后值。
表1 重点钢铁企业工序能耗单位:kgce/t1.炼铁系统(炼、球、焦、铁)的工序能耗占钢铁工业总能耗的69.41%,是钢铁工业的能耗大户。
由于能耗高,生产过程中所排放的C02、S02、NOx等物质也必然多,因此,炼铁系统是一个重要污染源。
从节能和环保的角度出发,炼铁系统应当完成钢铁工业的节能降耗、减少外排有害气体的重任。
2.动力系统是仅次于炼铁系统的第二个能耗大户。
从表3可看出,动力系统能耗占钢铁工业总能耗的15%,仅次于炼铁工序能耗。
分解动力系统能耗构成是:高炉鼓风和压缩空气用能约55~60kgce/t,制氧约30~40kgce/t,蒸汽和煤气管网运行约25~28kgce/t,发电和输电约30~37kgce/t。
所以各钢铁企业应当重视动力系统的节能工作。
三、钢铁工业节能潜力据统计分析,国内外钢铁企业生产过程中可回收利用的余压、余热、余能的总量,一般占本企业总能量的15%左右。
中国钢铁行业现状及发展趋势
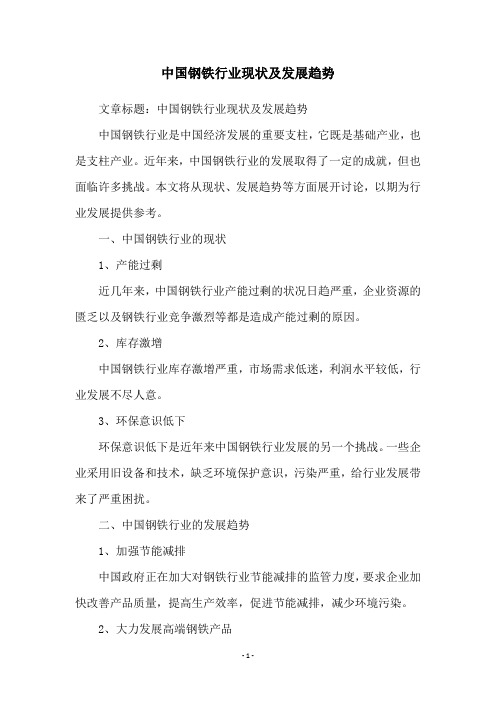
中国钢铁行业现状及发展趋势
文章标题:中国钢铁行业现状及发展趋势
中国钢铁行业是中国经济发展的重要支柱,它既是基础产业,也是支柱产业。
近年来,中国钢铁行业的发展取得了一定的成就,但也面临许多挑战。
本文将从现状、发展趋势等方面展开讨论,以期为行业发展提供参考。
一、中国钢铁行业的现状
1、产能过剩
近几年来,中国钢铁行业产能过剩的状况日趋严重,企业资源的匮乏以及钢铁行业竞争激烈等都是造成产能过剩的原因。
2、库存激增
中国钢铁行业库存激增严重,市场需求低迷,利润水平较低,行业发展不尽人意。
3、环保意识低下
环保意识低下是近年来中国钢铁行业发展的另一个挑战。
一些企业采用旧设备和技术,缺乏环境保护意识,污染严重,给行业发展带来了严重困扰。
二、中国钢铁行业的发展趋势
1、加强节能减排
中国政府正在加大对钢铁行业节能减排的监管力度,要求企业加快改善产品质量,提高生产效率,促进节能减排,减少环境污染。
2、大力发展高端钢铁产品
另外,中国钢铁行业的发展不仅仅是节能减排,还应大力发展高端钢铁产品,提高钢铁产品质量,提高技术水平,进行技术改造,开发新产品,拓宽钢材销售渠道,促进行业持续有序发展。
三、总结
中国钢铁行业已成为中国经济发展的支柱,但也面临着许多挑战。
未来,钢铁行业必须加大节能减排的力度,提高产品质量,大力发展高端钢铁产品,拓宽钢材销售渠道,同时积极稳妥应对挑战,以实现行业有序发展。
2023年我国钢铁行业能源消耗评述

2023年我国钢铁行业能源消耗评述重点统计企业吨钢综合能耗551.36kgce∕t目录1 .前言 (1)2 .能源消耗情况 (1)2.1.基本情况 (1)2.2.各工序能耗现状 (2)2.2.1.烧结工序 (2)2.2. 2.焦化工序 (3)2.2. 3.球团工序 (3)2.2. 4.炼铁工序 (4)3.结构节能情况 (4)1 .前言2023年我国钢铁行业处于需求减弱、价格下跌、成本上涨、利润下滑的态势;受行业限产、环保要求高等因素的影响,粗钢、生铁、钢材、铁矿石和铁合金的产量均出现下降,详见表1。
说明:因国家统计局对国产铁犷石统计范围的变化,使我国铁矿石产量数据偏低,约少3亿吨左右,实际产量在12亿吨以上。
2023年中钢协会员单位拥有废钢资源9579万吨,炼钢消耗废钢9435万吨,比上年减少1631万吨,其中转炉消耗废钢7628万吨,比上年减少1272万吨,废钢消耗量的减少不利于钢铁工业能耗降低。
2 .能源消耗情况2.1. 基本情况2023年中钢协能耗统计的会员单位有99家,其对应的钢产量为61404.07万吨,总能耗为34582.83万吨标准煤;与上年相比,重点统计企业的钢产量下降2.70%,总能耗降低2.49%。
2023年重点统计企业的吨钢综合能耗为55136kgce∕t,比上年升高127kgce∕t;吨钢可比能耗485.77kgce∕t,比上年升高0.38%。
2023年其他钢铁企业的铁、钢产量比上年分别下降2.22%、5.03%,下降幅度均高于重点统计企业变化幅度,使我国钢铁产业集中度进一步升高,有利于行业结构优化、能耗降低、冶金设备大型化等发展。
2.2.各工序能耗现状表2是2023年中钢协会员单位能耗情况对比。
从表2可以看出,与上年相比,2023年中钢协会员单位的烧结、球团、焦化、高炉、转炉和钢加工工序的能耗均出现下降。
部分钢铁企业的部分指标已达到或接近国际先进水平。
特别是吨钢耗新水指标创出历史最好水平(达到2.44m3∕t),有54家企业吨钢耗新水指标出现下降,有35家企业吨钢耗新水指标低于2.0m3∕t0表2中的数据表明,各企业之间节能工作发展不平衡,生产条件和结构也不一样,企业之间的各工序能耗最高值与先进值差距较大,说明我国钢铁企业之间技术水平和装备水平差距较大,企业节能工作还有较大潜力。
- 1、下载文档前请自行甄别文档内容的完整性,平台不提供额外的编辑、内容补充、找答案等附加服务。
- 2、"仅部分预览"的文档,不可在线预览部分如存在完整性等问题,可反馈申请退款(可完整预览的文档不适用该条件!)。
- 3、如文档侵犯您的权益,请联系客服反馈,我们会尽快为您处理(人工客服工作时间:9:00-18:30)。
我国钢铁工业能耗现状和节能潜力分析2010-12-17 特约专家王维兴特约专家王维兴近年来我国钢铁工业节能减排工作取得了显著的成绩。
2009年全国重点钢铁企业钢产量为4.659亿吨,2005年为2.9939亿吨,2009年钢产量比2005年增长68.96%;2009年全国重点钢铁企业能源消耗总量为23832万吨标准煤,2005年为19427万吨,2009年能源消耗比2005年增长22.67%。
这表明,全国重点钢铁企业能源消耗总量增幅要比钢产量增幅低46.29%。
这说明,钢铁工业节能工作取得了显著的成绩。
2009年全国重点钢铁企业吨钢综合能耗由2005年的694KGCE/T,降到2009年的619.43 KGCE/T,,下降10.74%,相应各工序能耗均有不同程度的下降。
全国重点钢铁企业各主要生产工序能耗情况见表1。
表1 重点钢铁企业各主要生产工序能耗情况单位:KGCE/T我国于2005年将电力折标准煤系数由0.404KGCE/KWH,调整为0.1229 KGCE/KWH,使我国钢铁工业能耗指标与国外企业出现不可比,也使企业内部历史数据存在不可比性。
为便于比较,2005年的数据已按0.1229 KGCE/KWH折标准煤系数进行调整。
从2006年起转炉工序能耗中不再计算炉外精炼部分的能耗。
所以,2007年与2006年转炉工序能耗数值下来较多。
从表1可看出,近五年我国重点钢铁企业各主要生产工序能耗均得到不同程度的下降。
降幅最大的工序是电炉工序,主要是因我国电炉生产中使用热铁水的比例不断增加,由2005年的311KG/T增加到2009年的484KG/T,使电炉工序能耗下降133.76KGCE/T。
从表1还可看出,进入2010年我国重点钢铁企业能耗得到进一步普遍下降,说明钢铁企业加大了节能工作力度,不断取得新进展,为我国节能减排做出新贡献。
1.我国重点钢铁企业能耗情况1.1我国钢铁企业的能源利用水平发展不平衡,一批企业能耗指标达国际先进水平,但也有落后产能存在, 能耗指标落后.目前,我国钢铁工业是处于不同层次、多种结构、各种生产技术经济指标共同发展阶中国有800多家钢铁企业, 重点钢铁企业有105家,钢产量占全国的82.06%.近年来,非重点铁企业的发展速度高于重点钢铁企业.使我国钢铁产业集中度不断下降. 重点钢铁企业的能耗水平基本上可以代表我国钢铁企业的能源利用基本情况.重点钢铁企业之中有三分之一的钢铁企业的技术装备水平达到国际水平,宝钢,首钢,鞍钢,武钢,天管等企业的部分技术装备已达到国际先进水平,他们的相关工序能耗也已达到或接近国际先进水平.但是,我国仍有一批应淘汰的落后技术装备在生产. 钢铁企业之间能耗水平有较大的差距,详见表2.表2 2010年前4个月重点钢铁企业各主要生产工序能耗情况单位:KGCE/T1. 2.我国重点钢铁企业能耗水平与国际先进水平相比,差距在10%~15%我国钢铁企业之间技术装备水平,产品结构,生产条件,生产规模,企业现代管理水平,以及装备容量等方面均存在较大的差距.所以,钢铁企业之间能耗水平差距也较大.这也说明我国钢铁企业节能工作尚有一定的潜力.总体评价,我国重点钢铁企业能耗水平与国际先进水平相比,差距在10%~15%..存在差距的主要原因有:中国铁钢比高(2009年中国铁钢比为0.94,比国外高约0.51,是我国吨钢综合能耗高的主要原因),冶金装备平均容量偏小(使吨钢综合能耗高出约50~80KGCE/T),生产工艺流程不尽科学,炼铁原燃料质量较差(特别是焦炭质量),造成高炉燃料比高(包括热风温度比国外低100~150℃),产品结构不合理,企业现代化管理水平低等.1.3. 近年重点钢铁企业节能工作取得显著成绩近年重点钢铁企业节能工作取得显著成绩,主要表现是:⑴重点钢铁企业吨钢综合能耗,各工序能耗历年均在不断下降,创出历史最好水平,详见表1;一批企业的相关工序能耗达到或接近国际先进水平, 2010年前5个月重点钢铁企业之中,炼铁工序能耗有20个企业能耗低于400KGCE/T,先进值的企业有:新余358.64 KGCE/T,太钢368.64 KGCE/T,宣钢363.32 KGCE/T,国丰375.94 KGCE/T,湘钢383.99 KGCE/T,冷水江385.37 KGCE/T,石钢385.65 KGCE/T,唐钢387.14 KGCE/T等。
转炉工序由22个企业实现了负能炼钢,先进值的企业有:太钢-12.96KGCE/T,天钢-12.41 KGCE/T,沙钢-11.55 KGCE/T,青钢-12.75 KGCE/T,重钢-10.05 KGCE/T等。
烧结工序由13个企业能耗低于50.00 KGCE/T,先进值的企业有:新余43.51 KGCE/T,太钢42.06 KGCE/T,宣钢42.33 KGCE/T,三明46.08 KGCE/T,青钢46.08 KGCE/T,等。
⑵2009年重点钢铁企业高炉技术经济指标创出历史最好水平.如入炉焦比为371KG/T,喷煤比为147 KG/T,热风温度为1158℃等.为炼铁工序能耗的降低创造出有利条件.⑶2010年前5个月重点钢铁企业转炉煤气回收量为79M3/T,比上年提高4 M3/T,太钢达128 M3/T,促进了重点钢铁企业转炉工序能耗创出历史最好水平.。
⑷重点钢铁企业二次能源回收利用取得新进展:高炉煤气压差发电装置(TRT)已得到普及, 全国有600多台。
京唐公司曹妃甸5500M3高炉煤气采用干法除尘,TRT吨铁发电量达48。
8KWH,是技术创新取得的新成就,达到国际领先水平。
投产和在建的干法熄焦装置(CDQ)有近100套,处理焦炭能力约1亿吨/年。
已开发出高压高温的CDQ。
马钢,济钢,宝钢等企业已建成几十套烧结余热回收装置,提高了二次能源回收利用水平。
首钢,宝钢,鞍钢,包钢等十几个企业建设了CCPP煤气发电设备,有效地提高企业能源利用效率。
⑸2010年前5个月重点钢铁企业高炉煤气放散率为5.02%,焦炉煤气放散率为1.43%,创出历史最好水平,促进了企业二次能源回收利用水平的提高.⑹我国开发成功高炉和转炉煤气干法除尘技术,并得到大力推广,已在首钢京唐钢铁公司曹妃甸5500M3高炉采用,有较好的节能和节水的效益. 2. 钢铁企业节能潜力分析2.1.钢铁工业节能工作重点在炼铁系统据统计, 炼铁系统(包括烧结,球团,焦化,高炉四个工序)能耗占钢铁联合企业总能耗70%,生产成本占55%~60%,污染物排放占约70%.所以说, 炼铁系统要承担钢铁联合企业的节能减排,降低生产成本,实现生产过程的环境友好的任务.钢铁联合企业各生产工序能耗占企业总能耗的比例见表3.表3 各工序能耗占联合企业总能耗比例首钢京唐钢铁公司曹妃甸5500M3高炉采用一系列先进的节能技术设备(实现上百项技术创新和专利)大大促进了全公司节能减排进步.该高炉2010年3月多项技术经济指标达到国际领先水平,详见表4.表4 曹妃甸5500 M3高炉指标2009年全国重点钢铁企业炼铁工序能耗为410.65KGCE/T,比上年下降5%,创出历史最好水平..主要原因是与上年度相比,高炉燃料比下降12KG/T,焦比下降22KG/,风温提高25℃.有14个企业高炉燃料比下降大于近几年,武钢按技术措施和管理措施并重的原则,在产量和产值快速增长的同时,通过采用各种先进的生产和节能工艺技术装备,使单位产品综合能耗连年下降,2010年前5个月达632.03KGCE/T,企业经济效益不断提高.太钢近年来积极采用各项先进的节能技术设备,建设4700M3高炉,7.63米焦炉,660M2烧结机等.二次能源回收设备,如CDQ,TRT,烧结余热回收,CCPP煤气发电,煤脱湿技术,蓄热式燃烧技术,高炉富氧大喷煤技术,热风炉高风温等.近年来,太钢炼铁,炼钢等工序能耗均居国内先进水平, 2010年前5个月炼铁工序能耗为368.64 KGCE/T,转炉工序能耗为-12.96 KGCE/.2.2.钢铁工业节能思路第一,实现减量化用能,体现出节能工作要从源头抓起.钢铁企业减量化用能工作重点是,降低能源亏损(由7%降到5%以下),降低炼铁燃料比(由550KG/T降到500KG/T以下).表5数据说明,2009年全国重点钢铁企业炼铁工序为实现钢铁工业减量化用能作出了贡献. 表6为降低炼铁燃料比的技术措施.表6 降低炼铁燃料比(煤比+焦比+小块焦比)的技术措施第二,实现提高能源利用效率.主要是体现在要充分合理科学利用好企业产生的副产煤气..钢铁企业生产用煤的能量有34%会转换为副产煤气(高炉,转炉,焦炉煤气).这体现出钢铁工业有能源转换功能.用好煤气就是提高能源利用效率.首先要不放散或少放散副产煤气(2010年前5个月重点钢铁企业高炉煤气放散率降为5.02%,焦炉煤气放散率为 1.43%,为历史最好成绩水平),然后是把煤气充分地在本企业内得到利用,企业内部取消一切燃油和烧煤的炉窑,把富余的焦炉煤气喷入高炉,降低炼铁燃料比,而不是用于发电.. 企业内的副产煤气,内部实再用不完,才去用于发电.煤气用于发电的能源利用效率在30%~45%,能源利用效率低,对企业经济性是不合适的.煤气发电投资高,运行费高,电上网对企业对经济是不利的.第三.提高二次能源回收利用水平. 二次能源是指企业生产过程中产生的余压,余热,余能.扣除副产煤气, 二次能源回量占企业总用能的15%..对二次能源进行回收利用主要是依靠添加节能设备,如TRT,CDQ,烧结余热回收,焦炉煤气上升管热量回收,炉渣显热回收等.2.3.钢铁企业节能技术第一. 管理节能钢铁企业实现现代化管理后,可以实现降低企业总能够的5%.具体内容有:企业能源有专人和部门管理.专职人员有较高的业务素质和管理水平;.企业能源仪器仪表配备率.完好率,周检率要达标;企业能源统计规范,及时,科学,执行国家和行业各能源介质折标煤系数规定;企业实行能源定额制管理制度.;编制钢铁企业能源发展规划(要与企业发展规划相衔接);建立企业能源管理中心等.宝钢建立企业能源管理中心,实现降低企业总能耗5%;马钢建立企业能源管理中心,能耗降低7%.第二. 结构节能钢铁企业通过调整产品结构,优化用能结构,优化炼铁炉料结构,提高钢锭热送热装比,优化钢铁生产流程,实现生产过程的连续化,紧凑化,高效化等措施均会有结构节能的效果.• 高炉炼铁多喷煤,代替焦炭,可以实现炼铁系统节能(焦化工序能耗为112 KGCE/T,喷煤工序能耗为20~35KGCE/T,.一顿煤粉代替一顿焦炭, 炼铁系统降低能耗约90 KGCE/T).体现出用能结构的节能效果.• 高炉炼铁炉料结构优化的方向是提高球团矿配比(烧结工序能耗为56 KGCE/T, 球团工序能耗为30 KGCE/T, 一顿球团代替一顿烧结, 炼铁系统降低能耗约26KGCE/T)• 钢锭热送热装比冷装节能65%,钢锭直接轧制可节能70%~80%.• 高技术含量,高附加值的钢材使用寿命高,使用量少,有显著的节能效果.宝钢立足于生产高技术含量,高附加值钢铁精品,形成普碳钢,不锈钢,特钢三大产品系列.产品实物质量与国际同类产品相当.• 钢铁生产实现连续化,紧凑化,高效化生产,生产过程中所有中间产品不落地,铁水给炼钢实现一罐到底,不设混铁炉,提高铁水温度,减少铁损,即节能,又提高生产效率.首钢京唐钢铁公司曹妃甸实现了连续化,紧凑化,高效化生产,生产过程中所有中间产品不落地.鞍钢鲅鱼圈也实现了连续化,紧凑化,高效化生产.他们的能耗均达到国际先进水平.•.我国短期内废钢资源的短缺不会得到缓解,铁钢比也不会大幅度下降.我国电费也比国外高.所以,近期短流程工艺在我国不会有大的发展.我们承认短流程生产工艺有较高的节能减排效果.但是要审时度事.第三. 技术节能钢铁工业各工序均有数百项的节能技术.钢铁企业要根据本企业的具体情况进行选择.要找出主要矛盾,要评价出节能工作的经济性,实用性,技术的成熟性和可靠性等.目前,我国炼铁指标中与国际先进水平相比差距最大的地方是热风温度偏低.约差100~150℃.炼铁工作者和领导要在提高我国热风温度上下工夫,要重视高风温对降低炼铁燃料比有大的作用.目前,我国钢铁企业各工序中能耗水平与国际先进水平相比差距最大的工序是转炉工序.主要是我国转炉煤气和蒸汽回收量偏少. 国际先进水平转炉煤气回收量100M3/T以上, 蒸汽回收量在50KG/T以上,实现转炉冶炼能耗为负值.我国有一批小转炉, 转炉煤气和蒸汽回收量偏少,甚至没有回收装置.目前,我国钢铁企业对焦炉上升管荒煤气显热(有1000℃左右显热) 尚没有进行回收利用.这部分的二次能源量几乎与干熄焦相当.我们应当加紧开发其技术,尽快组织回收利用这部分显热,对降低钢铁企业能耗有重大意义.我国电炉炼钢使用热铁水比例较高,对节能是不利的. 电炉炼钢使用热铁水比例在25%~35%还合理.高达80%就不合理了. 转炉炼钢可以使用15%的废钢,可以实现负能炼钢,再用电炉炼钢是不符合钢铁工业节能政策.国内外炼铁届公认,融熔还原的能耗在理论和生产实践证明,均要比高炉炼铁的能耗高.这说明,融熔还原技术还需要进一步的完善和提高.国外直接还原大多数是在特殊条件下实现的. 我国尚不具备这些特殊条件(高质量铁矿石和天然气富裕等),所以我国非高炉炼铁发展缓慢,进一步发展也要慎重..目前, 非高炉炼铁的能耗,一般是要高于高炉炼铁.所以,我们要及时跟踪国内外非高炉炼铁技术进展,进行必要的研究和开发.但不要再上新的,融熔还原设施. 避免出现非高炉炼铁能耗高,生产成本高的被动局面.。