烧结
一、烧结基本原理解析

一、烧结(1)、烧结基本原理烧结是粉末冶金生产过程中最基本的工序之一。
烧结对最终产品的性能起着决定性作用,因为由烧结造成的废品是无法通过以后的工序挽救的;相反,烧结前的工序中的某些缺陷,在一定的范围内可以通过烧结工艺的调整,例如适当改变温度,调节升降温时间与速度等而加以纠正。
烧结是粉末或粉末压坯,加热到低于其中基本成分的熔点温度,然后以一定的方法和速度冷却到室温的过程。
烧结的结果是粉末颗粒之间发生粘结,烧结体的强度增加。
在烧结过程中发生一系列物理和化学的变化,把粉末颗粒的聚集体变成为晶粒的聚结体,从而获得具有所需物理,机械性能的制品或材料。
烧结时,除了粉末颗粒联结外,还可能发生致密化,合金化,热处理,联接等作用。
人们一般还把金属粉末烧结过程分类为:1、单相粉末(纯金属、古熔体或金属化合物)烧结;2、多相粉末(金属—金属或金属—非金属)固相烧结;3、多相粉末液相烧结;4、熔浸。
通常在目前PORITE微小轴承所接触的和需要了解的为前三类烧结。
通常在烧结过程中粉末颗粒常发生有以下几个阶段的变化:1、颗粒间开始联结;2、颗粒间粘结颈长大;3、孔隙通道的封闭;4、孔隙球化;5、孔隙收缩;6、孔隙粗化。
上述烧结过程中的种种变化都与物质的运动和迁移密切相关。
理论上机理为:1、蒸发凝聚;2、体积扩散;3、表面扩散;4、晶间扩散;5、粘性流动;6、塑性流动。
(2)、烧结工艺2-1、烧结的过程粉末冶金的烧结过程大致可以分成四个温度阶段:1、低温预烧阶段,在此阶段主要发生金属的回复及吸附气体和水分的挥发,压坯内成形剂的分解和排除等。
在PORITE微小铜、铁系轴承中,用R、B、O(Rapid Burning Off)来代替低温预烧阶段,且铜、铁系产品经过R、B、O 后会氧化,但在本体中可以被还原,同时还可以促进烧结。
2、中温升温烧结阶段,在此阶段开始出现再结晶,首先在颗粒内,变形的晶粒得以恢复,改组为新晶粒,同时颗粒表面氧化物被完全还原,颗粒界面形成烧结颈。
第五章 烧结-1

2. 中温阶段(300~950℃)
• 任务:脱水、分解、氧化、晶型转变
• 结构水排除(高岭土) Al2O3 . 2SiO2 . 2H2O
Al2O3 . 2SiO2+2H2O
• 碳酸盐分解
✓由原料中带入
✓分解反应
500~850℃
MgCO3
MgO+CO2
CaCO3 850~1050℃CaO+CO2
MgCO3 . CaCO3 730~950℃ CaO+MgO+2CO2
研究表明,较小的颗粒尺寸分布范围是获取高烧结密度的必要条件。
二、影响陶瓷材料烧结的工艺参数
(1)烧成温度对产品性能的影响
烧成温度是指陶瓷坯体烧成时获得最优性质时的相应温度,即操作 时的止火温度。
烧成温度的高低直接影响晶粒尺寸和数量。对固相扩散或液相重结 晶来说,提高烧成温度是有益的。然而过高的烧成温度对特瓷来说,会因总 体晶粒过大或少数晶粒猛增,破坏组织结构的均匀性,因而产品的机电性能 变差。
颗粒间由点接触转变为面接触,孔隙缩小,连通孔 隙变得封闭,并孤立分布。 ③ 小颗粒间率先出现晶界,晶界移动,晶粒长大。
2)烧结后期阶段 ① 孔隙的消除:晶界上的物质不断扩散到孔隙处, 使孔隙逐渐消除。 ② 晶粒长大:晶界移动,晶粒长大。
➢ 烧结的分类:
烧结
固相烧结(只有固相传质) 液相烧结(出现液相) 气相烧结(蒸汽压较高)
颗粒形状和液相体积含量对颗粒之间作用力的影响 只有在大量液相存在的情况下,才能使这些具有一定棱角形状 的陶瓷粉体之间形成较高的结合强度。
(4)颗粒尺寸分布对烧结的影响
颗粒尺寸分布对最终烧结样品密度的影响可以通过分析有关的动力学 过程来研究,即分析由不同尺寸分布的坯体内部,在烧结过程中“拉出气孔” (pore drag)和晶粒生长驱动力之间力的平衡作用。
烧结的基本过程

《烧结的基本过程》同学们,今天咱们来了解一下烧结的基本过程。
你们可能会问,什么是烧结呀?其实,烧结就是把一些粉末状的东西变成一个坚固的整体。
那它是怎么做到的呢?简单说,就是先把粉末堆在一起,然后加热。
就好像我们做饼干,把面粉等材料混合好,再放进烤箱里烤。
比如说,制造砖头的时候,就会用到烧结。
把泥土弄成粉末,然后放进一个特别的炉子里加热,出来就是坚硬的砖头啦。
有个小工厂,专门生产零件,他们就用烧结的方法。
把一些金属粉末加热后,就变成了结实好用的零件。
同学们,现在是不是对烧结有点概念啦?《烧结的基本过程》同学们呀,咱们来聊聊烧结的基本过程。
烧结这个词,听起来有点陌生,其实很有趣。
想象一下,有一堆小小的粉末,它们分散着,没什么力气。
但是经过烧结,它们就能团结在一起,变得很强壮。
比如制作陶瓷,把陶土粉末弄好,经过高温烧结,就成了漂亮的陶瓷碗、陶瓷杯。
我听说过一个故事,有个小朋友好奇地看着爸爸工作,爸爸就是在做烧结,把一些材料变成有用的东西。
小朋友觉得太神奇啦!同学们,烧结是不是很有意思呢?《烧结的基本过程》同学们,今天咱们说一说烧结的基本过程。
你们知道吗?烧结能让一些小小的粉末变得很厉害。
一开始,粉末们松松散散的。
然后给它们加热,它们就开始发生变化啦。
就像一群小伙伴,本来各自玩耍,后来一起努力,变成了一个强大的团队。
比如说,制造铁锅的时候,也是用烧结。
把铁的粉末加热,就有了我们家里用的铁锅。
有一次,我去工厂参观,看到了烧结的过程,那场面可壮观啦!同学们,烧结是不是很神奇呀?。
烧结工艺知识点总结大全

烧结工艺知识点总结大全一、烧结原理1. 烧结是指将粉末材料在一定温度下加热,使其颗粒间发生结合,形成致密的块状产品。
烧结的基本原理是固相扩散,即热力学上的固相之间的扩散过程。
2. 烧结过程中主要有三种力学过程,分别为颗粒间的原子扩散、颗粒间的表面扩散和颗粒间的体扩散。
这三种扩散方式相互作用,共同促进颗粒间发生结合。
3. 烧结过程中温度、时间和压力是影响烧结效果的重要因素。
通过控制这些参数,可以使烧结过程更加均匀和有效。
二、烧结设备1. 烧结设备主要包括热处理炉、烧结炉、烧结机等。
不同的烧结设备适用于不同的烧结材料和工艺要求。
2. 烧结设备的主要部件包括燃烧室、加热炉、炉膛、热风循环系统、控制系统等。
这些部件共同作用,实现对粉末材料的加热和烧结作用。
3. 热处理炉是常见的烧结设备之一,主要通过电阻加热、气体燃烧等方式对粉末材料进行加热处理,适用于各种金属和非金属材料的烧结工艺。
三、烧结工艺控制1. 烧结工艺控制是烧结过程中的关键环节,可以通过控制温度、时间、压力等参数,实现对烧结过程的精确控制。
2. 烧结工艺控制的主要方法包括PID控制、自适应控制、模糊控制等。
这些控制方法通过对烧结过程中的各个参数进行实时监测和调整,以实现对烧结过程的精确控制。
3. 在实际生产中,烧结工艺控制可以通过计算机控制系统实现自动化,提高生产效率和产品质量。
四、烧结材料选型1. 烧结工艺适用于各种粉末材料,包括金属粉末、陶瓷粉末、粉末冶金材料等。
根据不同的材料性质和要求,选择合适的烧结工艺和设备。
2. 烧结材料的选型考虑因素包括原料种类、粒度、成分、形状等。
根据不同的要求,选择合适的烧结材料,可以有效提高产品质量和生产效率。
3. 在烧结材料选型过程中,也需要考虑成本、资源利用率和环境保护等方面的因素,以实现经济、环保和可持续发展。
五、烧结工艺的应用1. 烧结工艺广泛应用于金属、陶瓷、粉末冶金、电子材料等行业。
在金属制品生产中,烧结工艺可以用于制造各种粉末冶金制品、焊接材料、钎焊材料等。
材料科学基础 第十四章烧结

清洁的Si3N4粉末γSV为1.8J/m2,但它极易在空 气中被氧污染而使γSV降低,同时由于共价键材料原 子之间强烈的方向性而使γGB增高。固体表面一般不 等于表面张力,但当界面上原子排列是无序的,或 在高温下烧结时,这两者仍可当作数值相同来对待 。
2、压力差:颗粒弯曲的表面上存在压力差。 粉末体紧密堆积后,颗粒间仍有很多细小气孔 通过,在这些弯曲的表面上由于张力的作用而造成 的压力差为: △P=2γ/r 式中:γ为粉末体表面张力;r为粉末球型半径。
(2)温度继续升高,传质过程开始进行,颗粒间 接触状态由点接触逐渐扩大为面接触,接触面积 增加,固-气表面积相应减少。 (3)随着温度不断升高,传质过程继续进行,颗 粒界面不断发育长大,气孔相应地缩小和变形 ,而形成孤立的闭气孔。同时,颗粒界面开始移 动,粒子长大,气孔迁移到颗粒界面上消失,致 密度提高。 根据上面讨论,烧结过程可以分为三个阶段 :烧结初期、中期和后期。
第二节 烧结过程及机理
烧结过程
烧结推动力
烧结机理
一、烧结过程
首先从烧结体的宏观性质随温度的变化上 来认识烧结过程。
(一)烧结温度对烧结体性质的影响 图1是新鲜的电解铜粉(用氢还原的),经高 压成型后,在氢气气氛中于不同温度下烧结2 小时然后测其宏观性质:密度、比电导、抗拉 强度,并对温度作图,以考察温度对烧结进程 的影响。
比电导(Ω-1· cm-3)
密度(g/cm2)
温度(°C)
图1 烧结温度对烧结体性质的影响 l一比电导 2一拉力 3一密度
结果与讨论: 随烧结温度的升高,比电导和抗拉强度增加。 曲线表明,在颗粒空隙被填充之前(即气孔率 显著下降以前),颗粒接触处就已产生某种键 合,使得电子可以沿着键合的地方传递,故比 电导和抗拉强度增大。 温度继续升高,物质开始向空隙传递,密度 增大。当密度达到理论密度的90~95%后,其 增加速度显著减小,且常规条件下很难达到完 全致密。说明坯体中的空隙(气孔)完全排除是 很难的。
烧结与还原过程

定义
还原是一种化学反应过程,通过加入 还原剂或采用其他手段,将金属氧化 物或盐类中的氧去除,从而得到金属 或其化合物。
目的
还原过程主要用于制备金属、合金或 某些化合物,以及从金属氧化物中提 取金属。
还原的化学反应
01
金属氧化物与碳反应
在高温下,金属氧化物与碳发生还原反应,生成金属和二氧化碳。例如
:$2CuO + Crightarrow 2Cu + CO_{2}$。
精确控制烧结与还原过程 中的温度,确保温度波动 在允许范围内。
压力控制
合理调节压力,以实现烧 结与还原过程的稳定进行 。
时间控制
根据工艺要求,严格控制 烧结与还原过程的时间。
产品质量的检测与控制
外观检测
对产品外观进行检测,确 保产品表面无明显缺陷。
尺寸检测
测量产品的各项尺寸参数 ,确保符合设计要求。
还原工艺参数
温度
压力
还原反应需要在一定温度下进行,温度的 高低直接影响反应速率和产物的纯度。
在某些还原反应中,压力对反应速率和产 物有一定影响。
时间
还原剂与原料配比
反应时间也是影响还原过程的重要因素, 时间过短可能导致反应不完全,时间过长 则可能导致副反应发生。
还原剂与原料的配比对反应速率和产物质 量有重要影响,需根据具体反应条件进行 选择和调整。
目的
烧结的目的是通过致密化过程,提高物料的强度、硬度、耐磨性等机械性能, 以及改变物料的导电、导热等物理性能。
烧结的物理化学变化
物理变化
在烧结过程中,物料会发生颗粒间的 接触、粘结、融合等现象,导致物料 的致密化。同时,物料的体积会收缩 ,密度会增加。
化学变化
烧结理论及工艺要求

烧结理论及工艺要求
一、烧结理论
烧结,它是一种特殊的金属加工方法,是将金属粉末或粒子因加热及
压实而聚结成固态或凝固态的工艺。
烧结过程一般分为三个阶段,疏松期、烧结期和结晶期。
烧结期包括加热期、热压期和持热期。
1、疏松期:粉末在温度小于熔点时,它的聚结能力较低,它的表面
比较滑,一般称为粉末状态,它既可以形成颗粒和宏观结构。
2、烧结期:当温度上升到金属熔点以上时,粉末微粒之间的聚结能
力增强,它的表面光滑,此时粉末形成了小的颗粒,并可以粘合在一起,
形成较大的烧结体。
3、结晶期:当温度上升到金属晶体化温度时,粉末发生晶体结构,
进一步烧结,形成金属晶体。
二、烧结工艺要求
1、烧结温度:烧结温度是控制烧结成果的重要参数,一般来说,烧
结温度应高于金属的熔点,低于其晶体化温度。
2、压力:压力也是影响烧结成果的重要参数。
如果压力太低,烧结
质量就会受到影响,这时就需要使用较高的压力,以保证烧结质量。
3、时间:在烧结过程中,烧结时间也是一个重要的参数,如果烧结
时间不足,就可能导致金属的结晶不匀,从而影响烧结的成果。
烧结过程的三个阶段
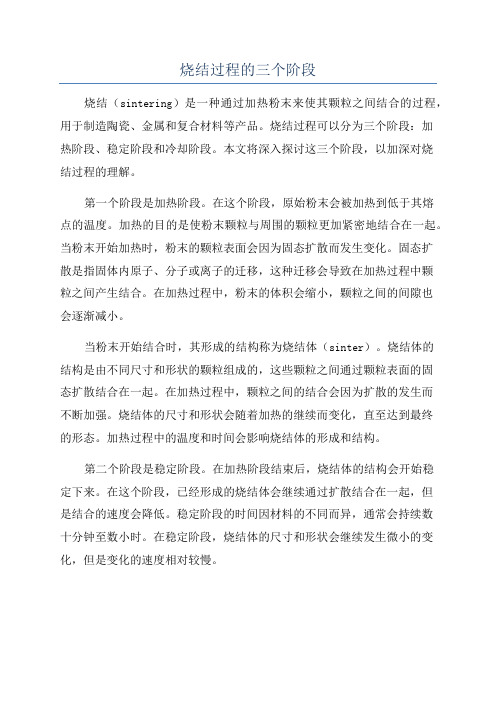
烧结过程的三个阶段烧结(sintering)是一种通过加热粉末来使其颗粒之间结合的过程,用于制造陶瓷、金属和复合材料等产品。
烧结过程可以分为三个阶段:加热阶段、稳定阶段和冷却阶段。
本文将深入探讨这三个阶段,以加深对烧结过程的理解。
第一个阶段是加热阶段。
在这个阶段,原始粉末会被加热到低于其熔点的温度。
加热的目的是使粉末颗粒与周围的颗粒更加紧密地结合在一起。
当粉末开始加热时,粉末的颗粒表面会因为固态扩散而发生变化。
固态扩散是指固体内原子、分子或离子的迁移,这种迁移会导致在加热过程中颗粒之间产生结合。
在加热过程中,粉末的体积会缩小,颗粒之间的间隙也会逐渐减小。
当粉末开始结合时,其形成的结构称为烧结体(sinter)。
烧结体的结构是由不同尺寸和形状的颗粒组成的,这些颗粒之间通过颗粒表面的固态扩散结合在一起。
在加热过程中,颗粒之间的结合会因为扩散的发生而不断加强。
烧结体的尺寸和形状会随着加热的继续而变化,直至达到最终的形态。
加热过程中的温度和时间会影响烧结体的形成和结构。
第二个阶段是稳定阶段。
在加热阶段结束后,烧结体的结构会开始稳定下来。
在这个阶段,已经形成的烧结体会继续通过扩散结合在一起,但是结合的速度会降低。
稳定阶段的时间因材料的不同而异,通常会持续数十分钟至数小时。
在稳定阶段,烧结体的尺寸和形状会继续发生微小的变化,但是变化的速度相对较慢。
稳定阶段的主要目的是确保烧结体的稳定性和一致性。
稳定阶段的结束标志是燃料在烧结体中完全燃尽。
当燃料燃尽时,烧结体的温度会开始降低,以进入第三个阶段。
第三个阶段是冷却阶段。
在冷却阶段,加热源会被移除,并且烧结体会开始冷却。
烧结体的冷却速度会影响其最终的性能和结构。
如果冷却速度过快,可能会导致烧结体的内部产生应力,从而引起开裂或变形。
因此,冷却过程需要在控制的条件下进行,以确保烧结体的质量。
综上所述,烧结过程的三个阶段是加热阶段、稳定阶段和冷却阶段。
加热阶段是使粉末颗粒结合的起始阶段,通过固态扩散来形成烧结体。
- 1、下载文档前请自行甄别文档内容的完整性,平台不提供额外的编辑、内容补充、找答案等附加服务。
- 2、"仅部分预览"的文档,不可在线预览部分如存在完整性等问题,可反馈申请退款(可完整预览的文档不适用该条件!)。
- 3、如文档侵犯您的权益,请联系客服反馈,我们会尽快为您处理(人工客服工作时间:9:00-18:30)。
sintering
1
一、基本概念
• (一)烧结的定义极其目的 • 1定义:在一定的温度下,通过烧结体内原 子的扩散使粉末颗粒之间由机械啮合转变 成原子之间的晶界结合。
烧结
颗粒界面
晶界面 烧结结合状态转变示意图
2
2.目的
• 使压坯成为冶金意义上的材料,赋予粉末 冶金零件所需要的机械性能和物理性能。
• 烧结颈的形成和长大,是通过原子由颗粒 表面和内部向烧结颈迁移而进行的。这种 迁移方式称为体积扩散。这种扩散的结果 是,在烧结颈形成和长大的同时,两颗粒 之间中心距离随之而缩短 .
10
a
a
ρ x x
ρ
收缩型模型
不收缩型模型
x 2a
2
x 4a
11
2
(三)烧结热力学问题
• 1烧结驱动力
X3/a = 3Mγ (M/2πRT)1/2 pa/d2RT· t
19
• 4.体积扩散 • x5/a=(20Dvγ Ω/kT)t
烧结颈表明 (空位源) 晶界 (空位阱)
颗粒表面 (空位阱) 体积扩散, 晶界扩散,
晶粒内和位错攀 移 (空位源或阱) 表面扩散
20
• 4.表面扩散 • x7/a3 = (56Dsγ δ 4/kT) · t • 5. 晶界扩散 • X6/a2 = (12 γ δ 4Db/kT) · t • 6.塑性流动 x2/a = K﹒ζy/η﹒ t
T再 0.25 0.35T熔
27
• 粒间聚集再结晶
a
b
c
聚集再结晶示意图 a 晶界形成,b 晶界迁移,c 晶粒长大
28
• (2)孔隙的变化 • 孔隙的球化发生在烧结后期。即当孔隙被 隔离,成为孤立的孔隙以后进行的。
a 孔隙的空位扩散球化
b 小孔隙向大孔扩散
孔隙的球化和长大示意图
29
5.影响烧结过程的因素
• 系统自由能降低使烧结的驱动力: • Z H TS 如烧结前后物质状态不变,
Z H U
高能状态(压坯)U压
U U 烧 U 压
U
低能状态(烧结体)U烧
能量状态变化示意图
12
• U 值来自以下几个方面: • (1)粉末颗粒的表面能 • 粉末压坯具有很大的表面能。这种表面能随粉末 颗粒的细化而增加,例如粒度为1um的金粉,其 表面能为37卡/克分子,而粒度为0.1um,其表面 能可达370卡/克分子。 • (2)粉末颗粒内的畸变能和内能 • 粉末压坯内具有很大的内能,并随粉末粒径的细 化和畸变量的增加而增加
24 22 20 18 16 14 12 10 8 6 4 2 0 200 400 600 800 1000 1200 1400 烧结温度,K
导电率,Sm/mm
24将烧结划分为三个阶段: • 1) 低温预烧阶段 这一阶段的温度α≤0.25,还没有达到最 低烧结温度,在这一阶段主要发生金属的回复、吸附气体 和水分的挥发、成型剂的分解和排除。 • 2)中温烧结阶段 这一阶段的温度α≤0.4~0.55,已经超 过了起始烧结温度,颗粒之间开始烧结,形成烧结颈,同 时还发生颗粒表面氧化物的还原和粉末颗粒内的再结晶。 • 3) 高温烧结阶段 这一阶段的温度为α≤0.5~0.85。在这一 阶段将发生烧结颈的长大、晶界迁移、颗粒合并、烧结体 收缩、孔隙封闭和球化等过程。
30
(二)、多元系固相烧结
• 这是指两种以上单一粉末的混合粉末或混合粉末
压坯的烧结.多元系固相烧结比单元系烧结要复杂。 根据合金化反应,这类烧结又可分为:无限互溶 系固相烧结,有限互溶系固相烧结和互不相溶系 固相烧结
A a B A b B A B c A d B
31
1.无限互溶系烧结
• 无限互溶系烧结,即在合金相图中是无限 可以互溶的体系烧结,如Fe-Ni、Cu-Ni 系的烧结。无限互溶的意思是任一比例的 两种或两种以上的粉末,在烧结中可以溶 合在一起。这类烧结在烧结后将产生单一 的相组织。如任一比例的铁粉和镍粉烧结, 将会有: • Fe + Ni Fe(Ni) • 烧结后纯铁和纯镍完全消失,而得到的是 Fe(Ni)固溶体相组织 .
32
• 这类体系的烧结,除了单元系所要求的密 度、孔隙度外,还有合金均匀化的要求, 即AB两个元素完全合金化 . • 合金均匀化程度,可采用均匀化程度因素 mt 表示: F
m
F-均匀化因素,mt-在时间t内,通过界面的物质迁移差, m∞-时间无限长,所通过界面的迁移差。由此可见,当F= 1时,则可达到完全均匀化程度
0 cv exp( S f / k ) exp( E f / k T ) 0 cv cv exp( / k T ) 0 cv cv exp( / k T )
1, exp( / k T ) 1 / k T 0 cv cv (1 / k T ) 0 cv cv (1 / k T ) 0 0 0 cv cv cv cv / k T cv / k T 0 cv / cv / k T 2
25
3.烧结时间
• 烧结时间是指高温烧结阶段的保温时间。 显然烧结时间愈长,烧结愈充分。
烧 结 密 度 1 2 3
烧结时间 (曲线1和3压坯密度相同,但1的烧结温度高于3;曲线2的压坯 密度高于3,但烧结温度相同)
26
4.烧结零件显微组织变化
• 单元系没有相成分和相组织的变化,所以 烧结中只发生颗粒的烧结、颗粒界面的消 失、晶界的迁移和晶粒长大以及孔隙形状 和孔隙连通状态的变化。 • (1)再结晶与晶粒长大 • 晶内再结晶 最低的结晶温度为:
2
F s in
2
) 2 ( x )
2 ( x ) 1 1 ( ) x 2 x 2 x
15
(2)空位浓度差
cv exp( S f / k ) exp( E 'f / kT)
E 'f E f cv exp( S f / k ) exp{( E f ) / kT} exp( S f / k ) exp( E f / kT) exp( / kT)
36
A A A B B A A B B A A B B B
A
B 4
1
2
3
互不相溶系的4种烧结状况 性能与成分的关系 1)收缩率
2 Ac A 2 B cB 2 AB c AB
c A cB 1
37
• η A、η B-分别为相同条件下单独烧结是的收缩率, 分别为cA、cB的平方; • η AB -为A-B接触时的收缩率 • cA、cB –A、B的体积浓度 • 如果:
• 单元系的烧结性能主要由密度、强度、延性、和导电性来 衡量。影响这些性能的因素可以归纳为如下几个方面: • (1)材料的性质,如材料的表面能、扩散系数、粘性系 数、临界剪切应力、蒸气压和蒸发速率,这些因素都会影 响到烧结驱动力和烧结颈长大速度。 • (2)粉末性质 粉末颗粒大小、表面活性(表面活性与表 面是否存在氧化膜以及表面的结构完善程度有关,表层氧 化膜、表面晶体存在大量位错、空位则活性很高),晶格 活性(晶格缺陷和晶格畸变),外来物质(杂质、氧化物、 吸附气体和烧结气氛)。
21
三、固相烧结
• (一)、单元系烧结 • 1.定义:单元系烧结是指单一成分的粉末或者单 一成分粉末压坯的烧结。所谓单一成分有如下几 种情况: • 纯金属粉末,如纯铁、纯铜、纯钼粉, • (2)合金粉末,如不锈钢粉、青铜粉、黄铜 粉, • (3)化合物粉末,如WC、MoSi、Al2O3。 • 单元系烧结的特点是在烧结中只发生颗粒之间的 冶金结合,没有化学成分和相组织的变化,这类 烧结通常是在其熔点的2/3~4/5温度下烧结。
7
• 2.烧结颈的长大 • 烧结颈由点向面发展即发生了烧结颈的长 大,烧结颈的长大使两个颗粒合并成一个 颗粒,颗粒界面成为晶界面。继续进行烧 结,晶界迁移,在原先颗粒接触面的晶界 消失,合并为一个晶粒,烧结即告结束.
8
• 3.孔隙球化阶段
隔离的孔隙在最小表面能的驱动下将会自发地发 生球化
9
(二)烧结是如何进行的
35
3.互不相溶系烧结
• 互不相溶系,即在合金相图中相互之间无溶解度 的体系. • 如W-Cu、Cu-C、Ag-CdO等 • 这类烧结如同单元系烧结,只发生颗粒之间的烧 结,烧结前后的相组织不发生变化 • 依据热力学,A、B组元之间的烧结有如下几种情 况: • 1)γAB<γA+γ B • 2)γAB>γA+γ B • 3)γAB>γA-γ B • 4)γAB<γA-γ B
22
2.烧结温度
• ( 1)起始烧结温度 • 起始烧结温度是指颗粒之间形成冶金结合 的最低温度。起始烧结温度通常以烧结绝 对温度与材料熔点的绝对温度之比α表示。 通过测定一些金属的α分别为:Au为0.3, Cu为0.35,Ni为0.4,Fe为0.4,Mn为0.45, W为0.4。
23
起始烧结温度的测定 导电率随烧结温度的变化
1 2 不发生物质迁移 发生物质迁移,并且 原子移动较长距离 粘结 表明扩散 晶格扩散(空位) 晶格扩散(间隙) 晶界扩散 蒸发凝聚 塑性流动 晶界滑移 回复或再结晶
18
3
发生物质流动,但原 子移动较小距离
• 2.粘性流动
ζ
X a
ρ
x2/a = K﹒γ /η ﹒ t
3. 蒸发凝聚
m = △p(M/2πRT)1/2 m—凝聚物质量 M—烧结物质的原子量
AB
1 ( A B ) 2
总体积收缩服从线形关系
38
• 如果
AB
1 ( A B ) 2
ηAB
是凹向上抛物线关系,如果