探究全断面岩石掘进机滚刀布置的优化方法
全断面掘进机刀具布置方法研究

全断面掘进机刀具布置方法研究麻清林【摘要】介绍了全断面岩石掘进机的刀具布置形式和布置原则,建立了盘形滚刀的优化布刀模型,提出适用于边滚刀的主要布置原则,利用多目标多约束的手段来优化刀具布置,用遗传算法得到最优解.并以某型刀盘为实例,验证了该布置方法的可能性.【期刊名称】《机械管理开发》【年(卷),期】2018(033)009【总页数】3页(P40-42)【关键词】全断面掘进机;刀盘布置;遗传算法【作者】麻清林【作者单位】山西新景矿煤业有限责任公司调度室, 山西阳泉045008【正文语种】中文【中图分类】TD355引言断面掘进机是城市建设,工程应用的重要施工设备。
刀具在刀盘上的布置,直接影响着刀具与刀盘的使用寿命、掘进机工作效率,是震动损坏的关键[1]。
刀具在刀盘上的布置主要有三种形式:正刀、边刀和中心刀。
我们主要研究的是正刀与边刀在刀盘上的布置问题。
1 盘形滚刀布刀形式滚刀布置设计对减少施工成本、加快生产速率具有极大地影响,是提高掘进机掘进效率,优化掘进机掘进性能不可缺少的技术手段,良好的滚刀布置设计可以延长刀盘主轴和刀具的使用时间,缓冲掘进机在掘进过程中的震动幅度,减小掘进噪音。
为了达到以上刀盘布置效果,目前有多种刀具布置模式可供参考:单螺旋与双螺旋线布置、单双螺旋混合布置、对称型布置和随机布置[2],如图1所示。
布置滚刀时,相位差距离需适中,对称模式是采用最多的一种布刀模式,可以减小刀盘受力,提高刀盘使用时间,增强滚刀切削能力与切削效率。
图1 滚刀布置形式2 盘形滚刀布刀原则刀盘上布置滚刀时首先考虑的是刀具与刀盘的受力情况,尽量减小刀盘受力。
其次掘进机掘进效率要高,刀具磨损要小,延长刀具使用寿命,刀具布置主要遵循以下几条原则:1)最佳刀间距原则。
良好的刀具间隔布置可以使刀具破碎岩石效果达到最大化。
由于岩石的硬度较大,所以刀间距应尽量小,一般取90 mm。
2)等磨损原则。
根据刀具与刀盘相对位置可以得出越靠近刀盘中心,刀具磨损越小。
全断面掘进机的现状分析与盘形滚刀的改进

中国矿业大学2011年12月9日目录前言..............................................................................................................一、全断面掘进机概述 (1)二、掘进机盘形滚刀的工作原理分析 (2)三、盘形滚刀在刀盘上的布置 (4)四、全断面岩石掘进机刀具磨损分 (6)五、盘刀具存在的问题及原因分析 (7)六、刀盘刀具改进方案及实施 (8)七、刀具的改进 (9)八、全断面掘进机发展现状 (10)九、全断面掘进机发展展望 (11)十、市场需求分析 (12)参考文献 (14)全断面掘进机的现状分析与盘形滚刀装置的改进摘要:隧道掘进机(tunnel boring machine(TBM))是用机械破碎岩石、出碴和支护实行连续作业的一种综合设备。
按掘进机在工作面上的切削过程,分为全断面掘进机和部分断面掘进机。
按破碎岩石原理不同,又可分滚压式(盘形滚刀)掘进机和铣切式掘进机。
我国产品多为滚压式全断面掘进机,适于中硬岩至硬岩。
铣切式掘进机适用于煤层及软岩中。
在推进油缸的轴向压力作用下,电动机驱动滚刀盘旋转,将岩石切压破碎,其周围有勺斗,随转动而卸到运输带上。
硬岩不需支护,软岩支护时可喷射、浇灌混凝土或装配预制块。
该机在岩性均匀、巷道超过一定长度时使用,经济合理。
关键词:全断面掘进机现状分析盘形滚刀改进市场分析一、全断面掘进机概述全断面掘进机是集机械、电气、液压和自动控制于一体的世界上公认的快速地下开挖工程最有效的大型高技术成套施工装备,是将掘进、移动、出碴和衬砌等多功能有机组合在一起的联合机组,融合了新材料、新工艺、液压、自动控制、信息、电子、电力、环保、人工智能、激光制导、遥测、遥感等高新技术。
由于采用全断面掘进机施工法具有快速、优质、安全、对围岩破坏小、利于环境保护、降低劳动强度及改善工作环境等特点,已广泛用于引水、水电、铁路、公路、煤矿、城市地铁和管网以及军事设施等方面的地下工程的施工。
全断面岩石掘进机盘形滚刀布置规律研究

(7)
∑
(8)
∑
2.2.2 刀盘径向力平衡 由刀盘径向力平衡,得: ⎧ ⎪ Fx = 0 ⎨ ⎪ ⎩ Fy = 0
∑ ∑
即:
(3)
⎧ n ⎪ ∑ [ Fti sin θi + ( Fi + Fei ) cos θi ] = 0 ⎪ i =1 ⎨ n ⎪ [− F cos θ + ( F + F )sin θ ] = 0 ∑ ti i i ei i ⎪ ⎩ i =1
(b) (c)
1
盘形滚刀在刀盘上布置的基本原则
Fig.1
图1 滚刀顺次破岩 Rock broken sequentially by disc cutters
盘形滚刀在刀盘上是按一定的数学和几何规 律布置的,这一布置规律是由 TBM 工作时的盘形 滚刀的破岩力对刀盘的作用效果及其破岩效率决 定的。为使 TBM 工作时刀盘受力均匀及盘形滚刀 高的破岩效率,盘形滚刀在刀盘上的布置需要满足 下述基本要求: 1) 刀盘上每把盘形滚刀的破岩负荷尽可能相 等。即每把盘形滚刀在破岩时所受负荷尽量相等, 每把刀的破岩量尽可能相同,刀刃两侧的侧向反力 尽可能相互抵消,使作用在大轴承上的径向载荷尽 可能接近零。 2) 岩石掘进机在掘进过程中刀盘所受的力必 须满足空间力系平衡条件。 若 xoy 面位于刀盘面上, TBM 刀盘轴线为 z 轴且其方向为 TBM 掘进方向,
工
―
程
力
学
173
后的 Snowdon 和 Ryley 等于 1982 年[4 5]、Sanio 于 1985 年[6]、Gertsch 等于 1991 年[7]、Roxborough 和 Phillips 于 1975 年[8]、 国内学者茅承觉教授等于 1986 [9] 年 等在其研究中也发现了类似现象。Snowdon 和 ― Ryley 等于 1982 年[4 5]关于刀间距 S 与刀具贯入度 P 的比值 S/P 的研究发现,存在 S/P 值,使比能最 小。在此基础上,国内外学者加大了盘形滚刀在刀 盘上布置规律的研究。著名学者王家騄[10]教授曾总 结出刀盘上盘形滚刀的布置规律有单螺旋线和双 螺旋线,文献[11]曾给出了这样布置的解析式,但 距实际应用还有相当大距离。在此工作基础上,我 们通过深入研究,建立了盘形滚刀在刀盘上布置的 数学力学模型并给出了其求解方法和应用实例,从 而为全断面岩石掘进机盘形滚刀在刀盘上的布置 提出了新的理论和方法。
滚刀工作原理分析
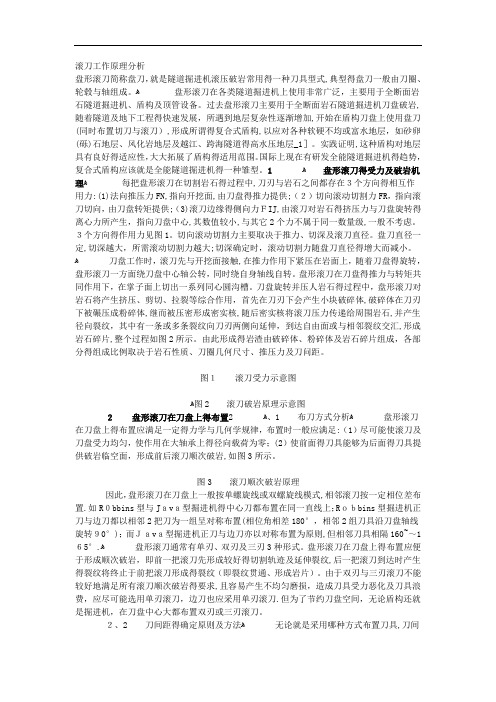
滚刀工作原理分析盘形滚刀简称盘刀,就是隧道掘进机滚压破岩常用得一种刀具型式,典型得盘刀一般由刀圈、轮毂与轴组成。
ﻫ盘形滚刀在各类隧道掘进机上使用非常广泛,主要用于全断面岩石隧道掘进机、盾构及顶管设备。
过去盘形滚刀主要用于全断面岩石隧道掘进机刀盘破岩,随着隧道及地下工程得快速发展,所遇到地层复杂性逐渐增加,开始在盾构刀盘上使用盘刀(同时布置切刀与滚刀),形成所谓得复合式盾构,以应对各种软硬不均或富水地层,如砂卵(砾)石地层、风化岩地层及越江、跨海隧道得高水压地层_1]。
实践证明,这种盾构对地层具有良好得适应性,大大拓展了盾构得适用范围。
国际上现在有研发全能隧道掘进机得趋势,1盘形滚刀得受力及破岩机复合式盾构应该就是全能隧道掘进机得一种雏型。
ﻫ理ﻫ每把盘形滚刀在切割岩石得过程中,刀刃与岩石之间都存在3个方向得相互作用力:(1)法向推压力FN,指向开挖面,由刀盘得推力提供;(2)切向滚动切割力FR,指向滚刀切向,由刀盘转矩提供;(3)滚刀边缘得侧向力FIJ,由滚刀对岩石得挤压力与刀盘旋转得离心力所产生,指向刀盘中心,其数值较小,与其它2个力不属于同一数量级,一般不考虑。
3个方向得作用力见图1。
切向滚动切割力主要取决于推力、切深及滚刀直径。
盘刀直径一定,切深越大,所需滚动切割力越大;切深确定时,滚动切割力随盘刀直径得增大而减小。
ﻫ刀盘工作时,滚刀先与开挖面接触,在推力作用下紧压在岩面上,随着刀盘得旋转,盘形滚刀一方面绕刀盘中心轴公转,同时绕自身轴线自转。
盘形滚刀在刀盘得推力与转矩共同作用下,在掌子面上切出一系列同心圆沟槽。
刀盘旋转并压人岩石得过程中,盘形滚刀对岩石将产生挤压、剪切、拉裂等综合作用,首先在刀刃下会产生小块破碎体,破碎体在刀刃下被碾压成粉碎体,继而被压密形成密实核,随后密实核将滚刀压力传递给周围岩石,并产生径向裂纹,其中有一条或多条裂纹向刀刃两侧向延伸,到达自由面或与相邻裂纹交汇,形成岩石碎片,整个过程如图2所示。
全断面掘进机刀盘切刀布置的优化

为:Mi=2叮r·K。·L·N·R/v
(2)
K。为同一安装半径安装n把切刀的实际磨耗系数,日本小松制
炉筝·R 作所根据大量的施工实绩认为K。=埘n,一是比较合适的。 那么,将(2)式加以变形得到R.安装半径处刀具的磨损量为:
(3)
V·,l
在特定的地质条件下,当限定刀盘转速N、机器掘进速度v以
及最大不换刀距离时,磨损量M.就变为以安装半径R;为自变量的 一组一次函数。
6170
1500
150
190
万方数据
一119一
全断面掘进机刀盘切刀布置的优化
作者: 作者单位: 刊名:
英文刊名: 年,卷(期):
杜志国 一重集团天津重工有限公司,天津,300301
科技创新与应用 Technology Innovation and Application 2013(26)
参考文献(3条) 1.闫玉茹 基于地层变异的盾构刀具磨损风险分析及其预测模型研究[学位论文] 2009 2.小松制作所 泥水盾构机设计计算书 2006 3.胡显鹏 砂卵石地层土压平衡盾构掘进刀具磨损研究[学位论文] 2006
由上式可以看出,在某一安装半径处,当刀片材料、地质条件掘 进距离以及切深一定时,n是影响磨损的重要因素。当n取不同值 时,磨损量与安装半径成正比关系。当给出刀具的许用磨损量【M】 时,则要求每一个安装半径处刀具的磨损量不大于该许用值,且尽
量接近许用磨损量,即M。s【M】。这样就能够很直观的求出每个安装 半径处布置刀具的数量n。
成熟的刀具磨损预测模型【2】,见公式(1)。
M=2叮r。Ks。L’N‘R/v
(1)
式中:M一刀具磨损量(IIlIn);Ks_硬质刀片的磨损系数(咖I以m);
硬岩隧道掘进机防尘及滚刀耐磨解决方案新

硬岩隧道掘进机防尘及滚刀耐磨解决方案1 简介刀具磨损和高粉尘是硬岩隧道掘进机掘进时两种常见问题。
刀具磨损和损坏主要是由破碎岩石粉末进入滚刀槽及隧道中掉落的岩石块引起的。
无水情况下磨损率增加,主要是由于高温以及刀槽中岩石粉无法去除造成的。
为解决磨损,粉尘和高温,可以使用化学品。
在硬岩隧道掘进机上使用水、水基添加剂或泡沫并不是新的技术,其数据可追溯到1973年或更早。
为了解决粉尘或者与其相关的问题,这些方法仍然被采用,或多或少取得成功。
2 现有状况2.1减少磨损影响刀具寿命主要有三个因素:刀盘外形,滚刀尖部外形和刀具冶金。
随着时间推移,根据测试和经验刀盘设计已经有所改进,通过优化位置和装配以延长刀具寿命。
刀尖的宽度选择要保证能够很好的深入岩石且具有足够强度以保证刀尖完整并减少边缘脱落。
为解决这个问题使用很多种合金钢和刀具冶金等方法。
历史上盘形滚刀刀圈是由优质轴承钢制成的,罗宾斯刀具所用的钢具有特殊的化学成分和强化过程,并且这一过程在逐渐优化以提供更高的强度,同时具有较低的断裂韧性,从而将边缘脱落的可能降到最低。
2.2减少粉尘粉尘是岩石隧道的一个固有部分。
隧道掘进机一般通过两种方式控制粉尘。
首先,在起源上捕获粉尘。
其次,通过旋转喷头用水除尘。
将旋转喷头平均分配在刀盘表面的喷雾嘴上。
随着岩石被切割,水雾也捕获粉尘并通过出渣系统将捕获的粉尘移走。
喷水杆也可以安装在粉尘产生区域,如输送带后配套转料区、渣料车装货区。
一旦粉尘进入空气中,将被除尘器移走。
此外,大型风机将含尘空气通过管道送到位于后方的除尘器。
新鲜的空气会向前移动取代被移走的含尘空气。
除尘器有湿法除尘器和干式除尘器两种,湿法除尘器利用喷雾捕获并移除含灰尘的空气,干式除尘器是使空气通过滤器进行过滤。
两种方式捕获的粉尘被放回到流渣中并从巷道移走。
2.3 以下方法很有益处:水喷雾:湿润的破碎材料除尘效果更好。
对粉尘控制来说足够的湿润是非常重要的,大量粉尘颗粒在破碎过程中并没有进入空气,而是附着在破碎材料表面。
全断面硬岩掘进机刀盘结构改进设计

中 图分 类 号 : T H1 6 ; T D 4 2 1 . 5 + 3 文 献 标 识码 : A 文章 编 号 : 1 0 0 1 — 3 9 9 7 ( 2 0 1 4 ) 0 2 ~ 0 0 5 2 — 0 3
Cu t t e r h e a d S t r u c t u r e I mp r o v e d De s i g n o f t h e F u l l F a c e
机 械 设 计 与 制 造
52
Ma c h i n e r y De s i g n
&
Ma n u f a c t u r e
第 2期 2 0 1 4年 2月
全 断面硬 岩 掘进 机 刀盘 结构 改进设 计
邓立营 , 杨
( 1 E 方重工集团有限公 司, 辽宁 沈阳
涛 , 高伟贤 , 凌静 秀
Ro c k Tu n n e l Bo r i n g Ma c h i n e
DE NG L i — y i n g ,YANG T a o ,G AO We i - x i a n , L I NG J i n g — x i u
( 1 . N o r t h e r n H e a v y I n d u s t r y G r o u p L t d . , L i a o n i n g S h e n y a n g 1 1 0 1 4 1 , C h i n a ;
2 . S c h o o l o f Me c h a n i c a l E n g i n e e r i n g , D a l i a n U n i v e r s i t y o f T e c h n o l o g y , L i a o n i n g D a l i a n 1 1 6 0 2 4 , C h i n a )
基于破岩比能的刀盘滚刀优化布置设计

基红艳
( 天 津 大 学 机 械 工 程 学 院 ,天 津 300072)
摘
要 : 基于科罗拉多矿业学院( Colorado School of Mines)推 导 的 CSM 受 力 模 型 ,采用刀盘破岩比能
最低原则,以径向不平衡力和倾覆力矩最小为目标,使 用 标 准 遗 传 算 法 (GA) ,优 化 中 心 刀 、正刀和边缘滚刀
model follow ed the principle o f cutterhead m inim um specific energy and utilized the normal
genetic algorithm to optim ize the spacing o f the center cutters,the normal cutters and the gage cutters, and in tu rn , to improve the polar angle o f the normal cutters and the gage cutters. Taking the T B 880E cutterhead as an o b je ct, the research revealed that when the cutter spacing o f center cutters and the normal cutters have been im p rove d ,the specific energy can be reduced by about 1. 5 3 % . S im ila rly ,when the tilt angles o f the gage cutters have been o ptim ize d ,the specific energy can be reduced by about 1. 10% . When the polar angles o f the normal cutters and the gage cutters have been im p rove d ,the unbalanced radial force can be reduced to 0. 126 5 N ,and the overturning moment can be reduced to 0. 759 1 N/ m ,which may decrease the deform ation o f the cutterhead. The present research can be applied in the optim ization design o f the locations o f the
- 1、下载文档前请自行甄别文档内容的完整性,平台不提供额外的编辑、内容补充、找答案等附加服务。
- 2、"仅部分预览"的文档,不可在线预览部分如存在完整性等问题,可反馈申请退款(可完整预览的文档不适用该条件!)。
- 3、如文档侵犯您的权益,请联系客服反馈,我们会尽快为您处理(人工客服工作时间:9:00-18:30)。
探究全断面岩石掘进机滚刀布置的优化方法作者:刘翔宇
来源:《中国新技术新产品》2015年第14期
摘要:本文明确研究了全断面岩石掘进机滚刀布置优化方法的重要性和意义,结合当前国内外对该项目研究的现状,针对全断面岩石掘进机滚刀布置的优化方法提出了几点建议。
关键词:全断面岩石掘进机;滚刀布置;优化设计
中图分类号:TD433 文献标识码:A
一、研究全断面岩石掘进机设计优化方法的意义和重要性
随着我国社会经济的发展,城市化的进程也在不断加快,地下空间资源的开发与利用逐渐引起了相关部门和建筑行业的重视,广阔的发展前景使得越来越多的建筑企业将部分资源投入到地下空间资源的开发利用中,而全断面岩石掘进机正是开发地下空间必不可少的机械设备。
全断面岩石掘进机的设计结构非常复杂,要求设计人员具备相当高的技术水平,现阶段也只有美国、日本、德国、法国等少数发达国家的相关行业才具有这方面的设计能力。
针对全断面岩石掘进机结构的设计制造在我国还处于起步阶段,我国目前建筑工程中使用的掘进机主要还是依靠进口。
国外的掘进机在我国相关行业的市场中有95%以上的占有率,其对我国隧道掘进机市场的垄断和支配地位显著,这对我国建筑行业开发和利用地下空间资源非常不利。
国家也在加大对全断面岩石掘进机设计制造的重视和投入,自2006年开始,就不断有针对全断面岩石掘进机自主研究,掌握核心技术等相关项目的文件颁布,加快我国自主研发全断面岩石掘进机的步伐,并将其产业化十分必要。
二、针对全断面岩石掘进机设计优化方案的研究
(一)研究重点
目前国内外学者从不同方面对全断面岩石掘进机滚刀布置和刀盘设计中存在的疑难问题进行了一系列研究和探讨。
刀盘设计的理论依据是刀具与岩石相互作用的原理,滚刀布置和刀盘结构设计也是基于这一理论所构建的。
如何针对各不相同的复杂的岩石边界条件,来进行对滚刀布置和刀盘结构的优化设计,使其能符合复杂多变的地质环境的要求,同时还能实现工作效率高、可靠性强、成本控制合理的目标,现已成为目前国内外研究的重点和难点。
(二)断面岩石掘进机滚刀布置设计
实现全断面岩石掘进机性能最优的有效手段之一就是优化滚刀布置结构,设计滚刀结构不仅要结合复杂多变的岩石边界情况,还必须将刀盘制造装配工艺要求以及铲斗、喷水孔、排碴开口、人孔通道等因素纳入考虑范围。
因为滚刀布置与刀盘结构的设计存在很多方面的关联
性,所以在进行滚刀布置的设计时,也要将刀盘结构的设计要求尽可能多的考虑进去。
随着地下空间资源开发利用进程的加快,掘进机被应用于更为复杂的地质环境中,这使得滚刀布置的设计受到更多方面的影响,要符合更多条件的要求,给设计人员带来了巨大的挑战和考验。
针对滚刀布置设计的研究主要有刀间距设计和滚刀平面布置设计两个方面。
刀间距就是相邻的两个刀具在直径上的最小距离。
滚刀平面布置就是在确定了刀间距后,布置滚刀在刀盘上的方向。
现阶段国内外学者主要结合数值仿真和物理实验这两方面的结果来对刀间距展开研究,通过这些研究也提出了一些有意义的观点。
受到技术封锁的影响,针对滚刀平面布置规律方面的研究在国内外都很少。
滚刀平面布置设计不仅要符合几何约束和力学平衡约束的要求,还要将复杂多变的岩石边界条件、刀具与岩石相互作用关系等因素考虑进去,从而构建出符合具体情况要求的滚刀平面布置优化模型。
要通过对先进的观点、研究方法和实验工具的运用,探索出滚刀平面布置在复杂岩石边界条件下的设计方法,找到滚刀平面布置的规律。
(三)断面岩石掘进机滚刀布置设计的优化方法
刀盘设计中滚刀布置设计中包含多种类型的滚刀,如中心刀、正边刀和边刀,同时在滚刀布置设计过程中需考虑刀盘结构制造装配要求,目前,研究复杂工程优化问题的主要有启发式算法、数学规划法、图论法、协同进化以及人机结合等方法。
其中,协同进化法是近十几年来在协同进化论基础上提出的一种新的进化算法,最早由Hillis于1990年提出。
这种方法通过对自然界物种之间的竞争、捕食、共生等关系的模拟展示,将整个生态系统由低级向高级进化的过程再现出来,并采用与之相似的方式进行问题求解。
根据使用的生物模型,可分为竞争式协同进化法、基于捕食—猎物机制的协同进化法、合作式协同进化法。
目前协同进化方法已被应用于解决复杂工程问题,被认为是一种处理复杂问题很有前途的设计框架。
其中合作式协同进化法更侧重于群体间互利共生的协同机制研究,它与断面岩石掘进机滚刀布置问题中的各个设计环节的优化有着本质的相似性,因而笔者主要采用究合作式协同进化法来解决断面岩石掘进机滚刀布置问题。
笔者通过对国内外相关文献的查阅和研究,以及向专业人士请教相关方面的知识,与其讨论和探索,同时结合了合作式协同进化法,针对断面岩石掘进机滚刀布置设计的优化方法提出了一些建设性的措施。
1 将滚刀直径载荷最小化,尽量使其垂直于刀盘回转轴线;
2 平衡刀盘受力,实现倾覆力矩最小化;
3 控制刀间距,实现在破岩过程中相邻滚刀之间不存在未被连通的岩石的目的;
4 合理规划滚刀位置,确保在实际施工中相邻滚刀按顺序破岩;
5 将破岩量差异控制到最小,使每把刀具的破岩量尽可能相同,使用寿命基本保持一致;
6 滚刀之间互不干涉,不超出刀盘的布置范围;
7 保证所有滚刀在刀盘上的质量分布均匀,让刀盘匀速运转;
8 确保刀盘的强度和刚度都达到标准,保证工作效率;
9 提高刀盘装配的工艺水平,满足刀盘分格制造、刀盘入孔、出碴孔等要求。
结语
尽管我国目前还不能自主研发全断面岩石掘进机,但只要能在引进国外先进技术的同时,积极主动地研究和探索其工作原理和制造方法,一定能在该项目的研究上取得突破性进展。
同时,在国家的大力支持和技术人员的不断努力下,我国真正掌握该领域的核心技术指日可待,这必将促进我国建筑行业的发展,为我国的现代化建设提供巨大的动力。
参考文献
[1]耿麒,魏正英,杜军.全断面岩石掘进机滚刀布置的优化方法[J].西安交通大学学报,2013(09).
[2]张斌.全断面岩石掘进机刀具磨损研究及刀具布局优化[D].2013(11).
[3]郑心扬.全断面岩石掘进机滚刀布置的优化方法[J].科技创业家,2014(02).。