没有理论模型情况下的工件表面检测
Deform试验
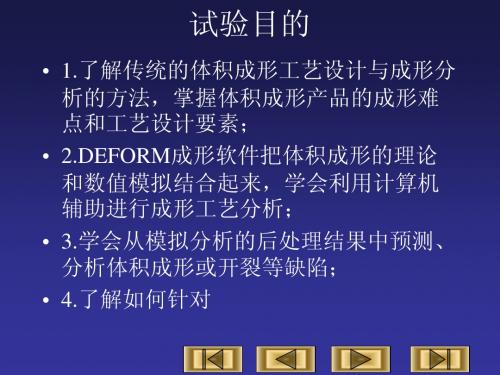
• 3.塑性变形中,金属与工模具的接触面不 断变化;因此,必须考虑非线性接触与 动态摩擦问题。 • 4.塑性理论中关于塑性应力应变关系与硬 化模型有多种理论,材料属性有的与时 间无关,有的则是随时间变化的粘塑性 问题;于是,采用不同的理论本构关系 不同,所得到的有限元计算公式也不一 样。
• 对于一些大变形弹塑性问题,一般包含 材料和几何两个方面的非线性,进行有 限元计算时必须同时考虑单元的形状和 位置的变化,即需采用有限变形理论。 而对于一些弹性变形很小可以忽略的情 况,则必须考虑塑性变形体积不变条件, 采用刚塑性理论。
?5对坯料进行网格划分有热传导情况模具也应划分网格?6为坯料定义材料有热交换的也需要对模具定义材料?7定义工具体的速度对轧制等给定坯料的初速度?8定义边界条件坯料性能体积补偿?9定义控制的单位和模拟类型以及步长和运算停止条件
试验目的
• 1.了解传统的体积成形工艺设计与成形分 析的方法,掌握体积成形产品的成形难 点和工艺设计要素; • 2.DEFORM成形软件把体积成形的理论 和数值模拟结合起来,学会利用计算机 辅助进行成形工艺分析; • 3.学会从模拟分析的后处理结果中预测、 分析体积成形或开裂等缺陷; • 4.了解如何针对
• 从数学角度理解,是将图7-1所示的求解 区域剖分成许多三角形子区域,子域内 的位移可以由相应各节点的待定位移合 理插值来表示。根据原问题的控制方程 (如最小势能原理)和约束条件,可以 求解出各节点的待定位移,进而求得其 他场量。推广到其他连续域问题,节点 未知量也可以是压力、温度、速度等物 理量。这就是有限元方法的数学解释。
刚(粘)塑性有限元的基本原理
• 在塑性加工的体积成形工艺中,变形体 产生了较大的塑性变形,而弹性变形相 对很小,可以忽略不计,此时可认为是 刚塑性问题,如锻造、挤压等;相应地 则可以用刚塑性有限元法分析。刚塑性 有限元法是在马尔可夫(Markov)变分 原理的基础上,引入体积不可压缩条件 后建立的。
数控加工学习总结

数控加工学习总结转眼间为期2周的数控加工与编程实训已经结束了,经过2周的实训让我学到了许多知识,回想实训这几天我确实有很大的收获。
在指导老师们耐心细致的指导下,圆满完成了实训任务,从总体上达到了实训预期的目标和要求。
这次实训给了我一次全面的、系统的实践锻炼机会,巩固了所学的理论知识,增强了我的数控操作能力,我进一步从实践中认识到数控的重要性。
实训中我学会了特种加工、华中数控车床、铣床的基本操作,但在实际动手加工的时候,很多问题都出现在我们的面前,使我们更加加深了各种知识的了解,在自己加工时,使我对对刀,参数的设置,编程的要求,工艺,还有在加工中的各种操做,以及刀补的建立,还有各种参数的修改,以及各种量具的使用有了更加深刻的了解。
通过这次实训我明白了在以后的工作中光有理论知识是不够的,还要把理论运用到实践中去才行。
实训就是把理论知识运用到实践操作中,及时对实践能力的培训,又是对理论知识的复习巩固和延伸。
在这2周的实训中,我学到的许多知识、技术及所获得的实践经验对我终身受益,我相信这些收获会在我以后的实际工作中将不断的得到验证,我会不断的理解和体会实训中所学到的知识,为实现自我的理想而努力奋斗!转眼间我期望已久的实训周已经过去,经过一周的实训让我学到了许多知识,回想实训这几天我确实有很大的收获。
在师傅的耐心指导和鼓励下,圆满完成了实训任务,从总体上达到了实训预期的目标和要求。
这次实训给了我一次全面的、系统的实践锻炼机会,巩固了所学的理论知识,增强了我的数控操作能力,我进一步从实践中认识到数控的重要性。
这次实训我学会了华中数控车床、铣床、数控加工中心的基本操作,但在实际加工中又反应了许多学习上的不足。
通过这次实训我明白了在以后的工作中光有理论知识是不够的,还要把理论运用到实践中去才行。
实训就是把理论知识运用到实践操作中,及时对实践能力的培训,又是对理论知识的复习巩固和延伸。
再通过于师傅的交谈中,了解了当即时代数控加工在工厂中的重要性,特别是未来工业。
计量检定人员资格考试题库及答案

计量检定人员资格考试题库及答案1.量具的分辨力是什么?答:指引起相应示值产生可觉察到变化的被测量的最小变化。
2.当室内外温差较大时,室外的精密零件转运到室内检测时,需要与量具同时恒温后再检测吗?答:是,原因是减少温差造成的误差。
3.扭矩扳子的校验步骤:答:1.检查扭矩扳子的外观,;2.放置扭矩扳子到检测仪上,检测仪清零;3.校准前,先把扭矩扳子预扭几次;4.校准时,转动手轮时施加的力要均匀,严禁用猛力快速转动手轮进行校准;5.记录三次校准值,判定是否合格。
4.使用带表量规测量工件时,注意工件被测表面的(清洁)状况。
工件放入测量位置之前,应保证其表面没有残留的(切削冷却液)及(切削残屑),没有尖锐的(飞边或毛刺),以免损坏量具或引起测量的不准确。
5.测量系统是指?答:对测量数据有关的人、量具、零件、方法、环境、标准的集合.6.通用卡尺零位检查的步骤:答:答对1条得10分1.使用前用纱布将测量面擦拭干净;2.游标卡尺零位检查-合拢量爪后,检查主尺刻线零位与游标零位刻线是否对齐。
3.数显卡尺检查零位--打开ON按键,合拢量爪后,如果不在零位,按清零键(ZERO)清零。
4.数显深度尺零位检查-打开ON按键,将测量基面立放在平台上,移动尺框,使用测尺端面与测量基面平齐,如果不在零位,按清零键(ZERO)清零。
5.深度尺零位检查-将测量基面立放在平台上,移动尺框,使用测尺端面与测量基面平齐,检查主尺零位刻线与游标零位刻线是否对齐。
7.当再现性(AV)变差值大于重复性(EV)时出现了哪些问题答:答对1条得10分1.作业员对量具的操作方法及数据读取方式应加强教育,作业标准应再明确订定或修订。
2.可能需要某些夹具协助操作员,使其更具一致性的使用量具。
3.量具与夹具校验频率于入厂及送修纠正后须再做测量系统分析,并作记录。
8.再现性变差大是因为什么造成的?答:变差由测量者的技巧造成。
9.游标卡尺/数显卡尺-测量时,用力适当。
故障诊断技术综述
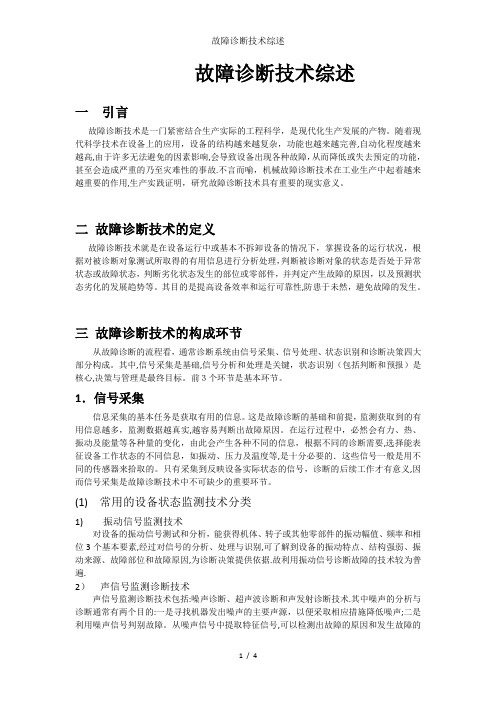
故障诊断技术综述一引言故障诊断技术是一门紧密结合生产实际的工程科学,是现代化生产发展的产物。
随着现代科学技术在设备上的应用,设备的结构越来越复杂,功能也越来越完善,自动化程度越来越高,由于许多无法避免的因素影响,会导致设备出现各种故障,从而降低或失去预定的功能,甚至会造成严重的乃至灾难性的事故.不言而喻,机械故障诊断技术在工业生产中起着越来越重要的作用,生产实践证明,研究故障诊断技术具有重要的现实意义。
二故障诊断技术的定义故障诊断技术就是在设备运行中或基本不拆卸设备的情况下,掌握设备的运行状况,根据对被诊断对象测试所取得的有用信息进行分析处理,判断被诊断对象的状态是否处于异常状态或故障状态,判断劣化状态发生的部位或零部件,并判定产生故障的原因,以及预测状态劣化的发展趋势等。
其目的是提高设备效率和运行可靠性,防患于未然,避免故障的发生。
三故障诊断技术的构成环节从故障诊断的流程看,通常诊断系统由信号采集、信号处理、状态识别和诊断决策四大部分构成。
其中,信号采集是基础,信号分析和处理是关键,状态识别(包括判断和预报)是核心,决策与管理是最终目标。
前3个环节是基本环节。
1.信号采集信息采集的基本任务是获取有用的信息。
这是故障诊断的基础和前提,监测获取到的有用信息越多,监测数据越真实,越容易判断出故障原因。
在运行过程中,必然会有力、热、振动及能量等各种量的变化,由此会产生各种不同的信息,根据不同的诊断需要,选择能表征设备工作状态的不同信息,如振动、压力及温度等,是十分必要的.这些信号一般是用不同的传感器来拾取的。
只有采集到反映设备实际状态的信号,诊断的后续工作才有意义,因而信号采集是故障诊断技术中不可缺少的重要环节。
(1)常用的设备状态监测技术分类1)振动信号监测技术对设备的振动信号测试和分析,能获得机体、转子或其他零部件的振动幅值、频率和相位3个基本要素,经过对信号的分析、处理与识别,可了解到设备的振动特点、结构强弱、振动来源、故障部位和故障原因,为诊断决策提供依据.故利用振动信号诊断故障的技术较为普遍.2)声信号监测诊断技术声信号监测诊断技术包括:噪声诊断、超声波诊断和声发射诊断技术.其中噪声的分析与诊断通常有两个目的:一是寻找机器发出噪声的主要声源,以便采取相应措施降低噪声;二是利用噪声信号判别故障。
表面缺陷检测训练 python

表面缺陷检测训练 python表面缺陷检测是指利用计算机视觉技术对产品表面进行缺陷检测的过程。
在Python中进行表面缺陷检测的训练可以通过以下步骤来实现:1. 数据收集,首先需要收集包含有缺陷和正常产品的图像数据集。
这些图像可以是通过摄像头拍摄的实时图像,也可以是通过其他渠道获取的图像数据集。
2. 数据预处理,对于收集到的图像数据,需要进行预处理操作,包括但不限于图像去噪、尺寸标准化、灰度化或彩色转换等操作,以便于后续的特征提取和模型训练。
3. 特征提取,利用Python中的图像处理库(如OpenCV)对图像进行特征提取,提取图像的纹理、形状、颜色等特征,以便于后续的模型训练。
4. 模型选择,选择合适的机器学习或深度学习模型来进行表面缺陷检测的训练。
常用的机器学习模型包括支持向量机(SVM)、随机森林(Random Forest)等,深度学习模型可以选择使用卷积神经网络(CNN)等。
5. 模型训练,利用Python中的机器学习库(如scikit-learn、TensorFlow、Keras等)对选定的模型进行训练,使用预处理后的图像数据集进行训练。
6. 模型评估,训练完成后,需要对模型进行评估,可以使用交叉验证、混淆矩阵等方法对模型进行性能评估,确保模型的准确性和泛化能力。
7. 模型部署,最后,将训练好的模型部署到实际的表面缺陷检测系统中,可以使用Python的相关库来实现模型的部署和集成。
需要注意的是,在进行表面缺陷检测训练的过程中,需要考虑数据的质量、模型的选择和调参、评估指标的选择等问题,以确保训练得到的模型能够准确地检测表面缺陷。
同时,还需要关注模型的实时性和稳定性,以适应实际生产环境中表面缺陷检测的需求。
三坐标测量机测量原理

三坐标测量机测量原理三坐标测量机测量原理三坐标测量机是测量和获得尺寸数据的最有效的方法之一,因为它可以代替多种外表测量工具及昂贵的组合量规,并把复杂的测量任务所需时间从小时减到分钟。
三坐标测量机的功能是快速准确地评价尺寸数据,为操作者提供关于生产过程状况的有用信息,这与所有的手动测量设备有很大的区别。
将被测物体置于三坐标测量空间,可获得被测物体上各测点的坐标位置,根据这些点的空间坐标值,经计算求出被测物体的几何尺寸,形状和位置。
三坐标测量机的组成:1,主机机械系统(X、Y、Z三轴或其它);2,测头系统;3,电气控制硬件系统;4,数据处理软件系统(测量软件);三坐标测量机在现代设计制造流程中的应用逆向工程定义:将实物转变为C AD模型相关的数字化技术,几何模型重建技术和产品制造技术的总称。
广义逆向工程:包括几何逆向,工艺逆向,材料逆向,管理逆向等诸多方面的系统工程。
正向工程:产品设计-->制造-->检验(三坐标测量机)逆向工程:早期:美工设计-->手工模型(1:1)-->3轴靠模铣床当今:工件(模型)-->3维测量(三坐标测量机)-->设计à制造逆向工程设备:1,测量机:获得产品三维数字化数据(点云/特征);2,曲面/实体反求软件:对测量数据进行处理,实现曲面重构,甚至实体重构;3, CAD/CAE/CAM软件;4,数控机床;逆向工程中的技术难点:1,获得产品的数字化点云(测量扫描系统);2,将点云数据构建成曲面及边界,甚至是实体(逆向工程软件);3,与CAD/CAE/CAM系统的集成;(通用CAD/CAM/CAE软件)4,为快速准确地完成以上工作,需要经验丰富的专业工程师(人员);三坐标测量机测量原理三坐标测量机是测量和获得尺寸数据的最有效的方法之一,因为它可以代替多种外表测量工具及昂贵的组合量规,并把复杂的测量任务所需时间从小时减到分钟。
三坐标测量机的功能是快速准确地评价尺寸数据,为操作者提供关于生产过程状况的有用信息,这与所有的手动测量设备有很大的区别。
表面粗糙度的检测方法
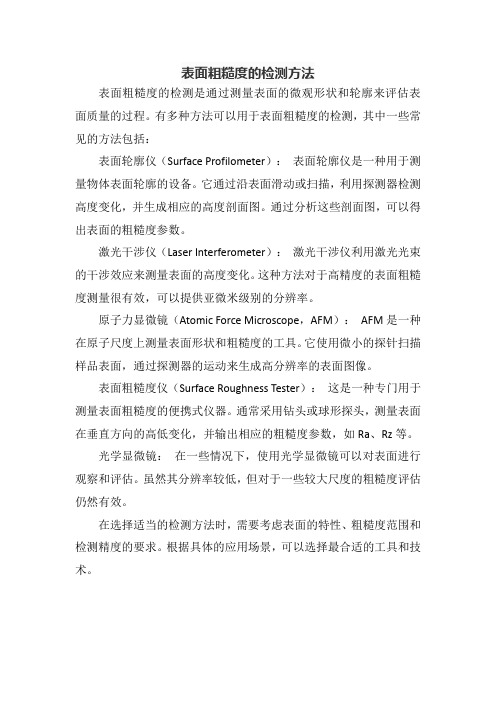
表面粗糙度的检测方法
表面粗糙度的检测是通过测量表面的微观形状和轮廓来评估表面质量的过程。
有多种方法可以用于表面粗糙度的检测,其中一些常见的方法包括:
表面轮廓仪(Surface Profilometer):表面轮廓仪是一种用于测量物体表面轮廓的设备。
它通过沿表面滑动或扫描,利用探测器检测高度变化,并生成相应的高度剖面图。
通过分析这些剖面图,可以得出表面的粗糙度参数。
激光干涉仪(Laser Interferometer):激光干涉仪利用激光光束的干涉效应来测量表面的高度变化。
这种方法对于高精度的表面粗糙度测量很有效,可以提供亚微米级别的分辨率。
原子力显微镜(Atomic Force Microscope,AFM):AFM是一种在原子尺度上测量表面形状和粗糙度的工具。
它使用微小的探针扫描样品表面,通过探测器的运动来生成高分辨率的表面图像。
表面粗糙度仪(Surface Roughness Tester):这是一种专门用于测量表面粗糙度的便携式仪器。
通常采用钻头或球形探头,测量表面在垂直方向的高低变化,并输出相应的粗糙度参数,如Ra、Rz等。
光学显微镜:在一些情况下,使用光学显微镜可以对表面进行观察和评估。
虽然其分辨率较低,但对于一些较大尺度的粗糙度评估仍然有效。
在选择适当的检测方法时,需要考虑表面的特性、粗糙度范围和检测精度的要求。
根据具体的应用场景,可以选择最合适的工具和技术。
先进制造工艺--高速切削技术
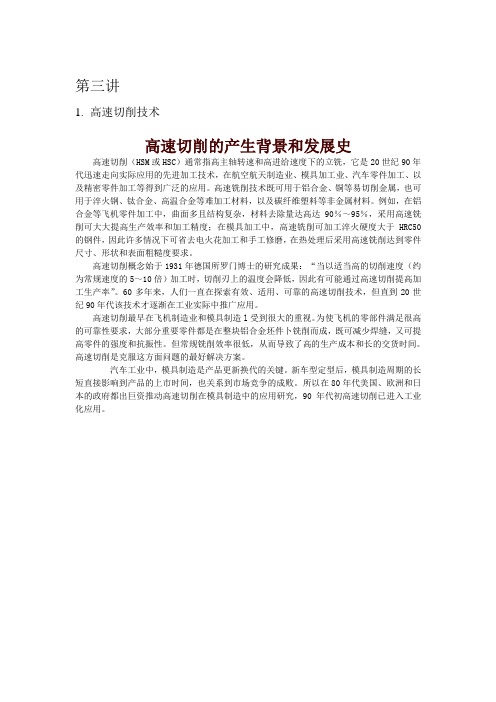
第三讲1.高速切削技术高速切削的产生背景和发展史高速切削(HSM或HSC)通常指高主轴转速和高进给速度下的立铣,它是20世纪90年代迅速走向实际应用的先进加工技术,在航空航天制造业、模具加工业、汽车零件加工、以及精密零件加工等得到广泛的应用。
高速铣削技术既可用于铝合金、铜等易切削金属,也可用于淬火钢、钛合金、高温合金等难加工材料,以及碳纤维塑料等非金属材料。
例如,在铝合金等飞机零件加工中,曲面多且结构复杂,材料去除量达高达90%~95%,采用高速铣削可大大提高生产效率和加工精度;在模具加工中,高速铣削可加工淬火硬度大于HRC50的钢件,因此许多情况下可省去电火花加工和手工修磨,在热处理后采用高速铣削达到零件尺寸、形状和表面粗糙度要求。
高速切削概念始于1931年德国所罗门博士的研究成果:“当以适当高的切削速度(约为常规速度的5~10倍)加工时,切削刃上的温度会降低,因此有可能通过高速切削提高加工生产率”。
60多年来,人们一直在探索有效、适用、可靠的高速切削技术,但直到20世纪90年代该技术才逐渐在工业实际中推广应用。
高速切削最早在飞机制造业和模具制造l受到很大的重视。
为使飞机的零部件满足很高的可靠性要求,大部分重要零件都是在整块铝合金坯件卜铣削而成,既可减少焊缝,又可提高零件的强度和抗振性。
但常规铣削效率很低,从而导致了高的生产成本和长的交货时间。
高速切削是克服这方面问题的最好解决方案。
汽车工业中,模具制造是产品更新换代的关键。
新车型定型后,模具制造周期的长短直接影响到产品的上市时间,也关系到市场竞争的成败。
所以在80年代美国、欧洲和日本的政府都出巨资推动高速切削在模具制造中的应用研究,90年代初高速切削已进入工业化应用。
图16 高速切削在生产应用中的发展历程图17 采用高速切削后产品质量提高的历程a一硬质合金切钢 b一硬质合金切铸铁c—CBN切铸铁图16是德国宝马公司(BMW)采用高速切削的历程。
- 1、下载文档前请自行甄别文档内容的完整性,平台不提供额外的编辑、内容补充、找答案等附加服务。
- 2、"仅部分预览"的文档,不可在线预览部分如存在完整性等问题,可反馈申请退款(可完整预览的文档不适用该条件!)。
- 3、如文档侵犯您的权益,请联系客服反馈,我们会尽快为您处理(人工客服工作时间:9:00-18:30)。
0 引 言
在 水轮 机制 造 业 中 , 型工 件 的 数 字化 检 测 大
且 目前使用 的水 轮机 叶片测 量装 置测 量不 确定 度 超过 1m 无法 满足 厂家要 对 叶片 的高 精度 检 测 m,
要求( 现在 国 内设 计 的抽 水 蓄能 机组 叶片 制 造公 差 只 有 51m 。 因 此 , 计 出 一 种 能 够 代 替 - m) 设 C D模 型 的测量 和计算 方法 就显 得极 为有 必要 。 A
t h c e it n d r g ma ua trn n p lig hste i it d c so e c vtt n is e — oc e k d vai u n n fcu iga d a pyn .T i h s nr u e n a i i np c o i s o ‘ — ao
是在 工件 表面 上按 网格 状 采集 一 些 坐 标 点 云 , 在
分析 软件 中把 点云与 C D模ห้องสมุดไป่ตู้型最佳 拟合 , 后计 A 然
算点 到型 面的偏 差 。然而 我 国现阶段 有很 多非 自
主生 产研 发 的 设 备 在 装 机 后 进 行 问 题 排 检 的时 候, 由于没有 理论 模型 而很难 找 出问题 的所在 , 现 以真机 叶 片为例 进行 说 明。某 电厂发 电机组 运行
( 尔滨电机 厂有限责任公 司 , 尔滨 104 ) 哈 哈 50 0
摘
要: 大型工件 的数字化 检测一直是生产 和应用过程 当中作为偏差检查 的主要且较为精密 的手段之一 。本
文介绍 了一种在没有理论模型的情况下应用激光跟踪仪进行 装机叶片 的汽 蚀检测 。这一方 法也可推广 到类 似情况下 的大型工件的数字化检测 当中。 关键词 : 激光跟踪 仪 ; 测量点 ; 型线偏差
( abnEetcl oo o ,t , ri 50 0 C i ) H ri l r a M t C . Ld Ha n1 0 4 , hn ci r b a
Ab t a t Di i ldee to fl re wo k i c s awa s b e n ft i n e ie meh d s r c : g t t cin o a g r p e e ha l y e n o e o he man a d pr cs t o s a
to ih u e a e r c e o n tle ld swih u h o ei a d 1 in whc s sls rta k rfri sald b a e t o tte r t lmo e .An h smeh d c n as c d ti t o a lo be e tn d t i i ld tc in o a g r p e e i i l rst to . x e de o d gt e e to flr e wo k ic n smi i ins a a ua Ke r s:a e rc e ;me s rn on ;ln a e it n y wo d ls r ta k r a u g p it i e rd va i i o ‘
时震动 超标 , 检修 时 发 现 转 轮 的其 中两个 叶片 在
正 面 出水边 区域 有 汽 蚀 现象 , 型 线 样 板 检查 也 用 发 现这 两 片 叶 片 出水 边 型 线 与 其 他 叶 片 差 异 较 大, 由于 样板 检 查 的 限制 , 只能 检查 很 小 的 区域 ,
收 稿 日期 :0 2—0 21 3—1 8
作者简介 : 丽娜( 95一) 女, 谢 18 , 助理工程师, 主要从事精 密测量等工作 。
中 图分 类 号 : G 1 T 15 文 献标 识 码 : B
S r a e Ex m i e wi u e r tc lM o e u f c a n t ho t Th o e i a d l
X/ i a, i n S i ig, u Y h e L n T a h yn S a
l 测 量 设备 原 理
本 文 中应用 的检测 设备 是美 国 A I 司生产 P公
的激 光跟踪 仪 , 这是 一 种 高 精 度 的便 携 坐 标 测 量 设 备 , 设备 是球 坐标 系 的坐标测 量 系统 , 该 由两个 测 角单 元和 一个测 距单 元组 成 , 角采 用 圆光栅 , 测 而i距 则采 用激 光 干 涉 仪 , 用球 形 反 射 镜 接 触 贝 0 利 被 测 物体并 反射 激 光 开 展测 量 , 一 种 接 触 式测 是
第 4期
21 0 2年 7月
锅
炉
制
造
No 4 .
BOI ER MANUFACTURI L NG
J 12 2 u . 01
文章 编 号 :N 3—14 (0 2 0 0 6 0 C2 29 2 1 )4— o 0— 2
没有 理 论 模 型 情 况 下 的 工件 表 面 检 测
谢 丽娜 , 田世 颖 , 艳 苏