自动化集装箱卸载系统
装卸自动化系统及装、卸货自动化方法
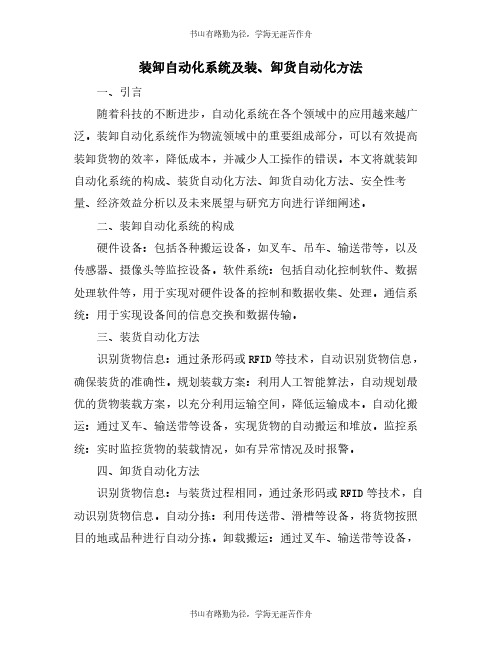
装卸自动化系统及装、卸货自动化方法一、引言随着科技的不断进步,自动化系统在各个领域中的应用越来越广泛。
装卸自动化系统作为物流领域中的重要组成部分,可以有效提高装卸货物的效率,降低成本,并减少人工操作的错误。
本文将就装卸自动化系统的构成、装货自动化方法、卸货自动化方法、安全性考量、经济效益分析以及未来展望与研究方向进行详细阐述。
二、装卸自动化系统的构成硬件设备:包括各种搬运设备,如叉车、吊车、输送带等,以及传感器、摄像头等监控设备。
软件系统:包括自动化控制软件、数据处理软件等,用于实现对硬件设备的控制和数据收集、处理。
通信系统:用于实现设备间的信息交换和数据传输。
三、装货自动化方法识别货物信息:通过条形码或RFID等技术,自动识别货物信息,确保装货的准确性。
规划装载方案:利用人工智能算法,自动规划最优的货物装载方案,以充分利用运输空间,降低运输成本。
自动化搬运:通过叉车、输送带等设备,实现货物的自动搬运和堆放。
监控系统:实时监控货物的装载情况,如有异常情况及时报警。
四、卸货自动化方法识别货物信息:与装货过程相同,通过条形码或RFID等技术,自动识别货物信息。
自动分拣:利用传送带、滑槽等设备,将货物按照目的地或品种进行自动分拣。
卸载搬运:通过叉车、输送带等设备,实现货物的自动卸载和搬运。
数据处理:对卸载过程中的数据进行收集和处理,以便进行后续的物流管理和优化。
五、安全性考量安全防护措施:确保所有设备符合安全标准,并配备必要的安全防护装置,如急停按钮、防护栏等。
监控系统:通过视频监控等手段,实时监测操作过程中的安全状况,及时发现并处理异常情况。
安全培训:对操作人员进行定期的安全培训,提高他们的安全意识和应对突发状况的能力。
应急预案:制定完备的应急预案,包括事故报告、处理和恢复等流程,确保在紧急情况下能迅速应对。
六、经济效益分析降低成本:自动化系统能够减少大量的人工操作,从而降低人力成本。
同时,能够提高装卸效率,缩短物流时间,降低库存成本。
装卸自动化系统及装、卸货自动化方法
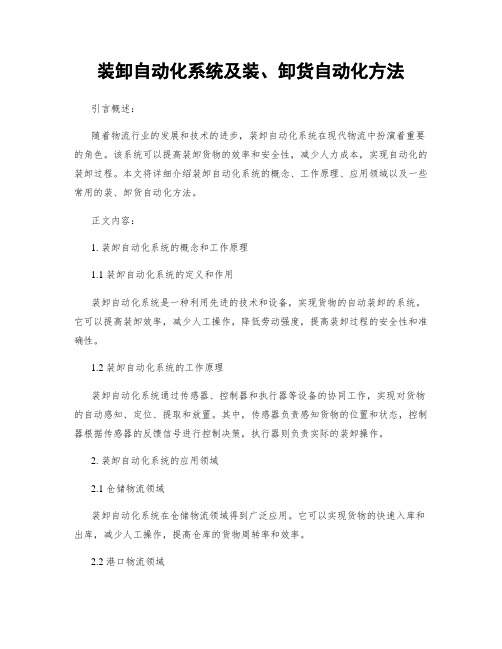
装卸自动化系统及装、卸货自动化方法引言概述:随着物流行业的发展和技术的进步,装卸自动化系统在现代物流中扮演着重要的角色。
该系统可以提高装卸货物的效率和安全性,减少人力成本,实现自动化的装卸过程。
本文将详细介绍装卸自动化系统的概念、工作原理、应用领域以及一些常用的装、卸货自动化方法。
正文内容:1. 装卸自动化系统的概念和工作原理1.1 装卸自动化系统的定义和作用装卸自动化系统是一种利用先进的技术和设备,实现货物的自动装卸的系统。
它可以提高装卸效率,减少人工操作,降低劳动强度,提高装卸过程的安全性和准确性。
1.2 装卸自动化系统的工作原理装卸自动化系统通过传感器、控制器和执行器等设备的协同工作,实现对货物的自动感知、定位、提取和放置。
其中,传感器负责感知货物的位置和状态,控制器根据传感器的反馈信号进行控制决策,执行器则负责实际的装卸操作。
2. 装卸自动化系统的应用领域2.1 仓储物流领域装卸自动化系统在仓储物流领域得到广泛应用。
它可以实现货物的快速入库和出库,减少人工操作,提高仓库的货物周转率和效率。
2.2 港口物流领域在港口物流领域,装卸自动化系统可以实现集装箱的自动装卸,提高港口的吞吐量和作业效率,减少装卸过程中的人为错误和事故风险。
2.3 创造业领域在创造业领域,装卸自动化系统可以实现生产线的自动化装卸,提高生产效率和产品质量,减少人工操作对产品的影响。
3. 装货自动化方法3.1 机械臂装货机械臂装货是一种常见的装货自动化方法。
它通过机械臂的灵便运动和抓取功能,实现对货物的自动装载。
3.2 输送带装货输送带装货是一种简单高效的装货自动化方法。
通过设置输送带系统,将货物从一个位置运送到另一个位置,实现快速装货。
3.3 AGV装货AGV(自动引导车)是一种自动化运输设备,可以实现对货物的自动装载。
它通过激光导航和传感器感知,实现货物的自动定位和装载。
4. 卸货自动化方法4.1 机械臂卸货机械臂卸货是一种常见的卸货自动化方法。
集装箱焦炭运输智能化卸车系统

集装箱焦炭运输智能化卸车系统发布时间:2021-09-02T17:19:05.080Z 来源:《中国电气工程学报》2021年4期作者:朱海贵,凌云[导读] 本文以马钢炼焦总厂集装箱运输智能化环保改造工程为例朱海贵,凌云中冶华天南京工程技术有限公司,江苏南京,210019摘要:本文以马钢炼焦总厂集装箱运输智能化环保改造工程为例,探讨集装箱焦炭智能化卸车设备构成和自动化控制方面问题。
介绍火车皮改造方式,集装箱结构特点,智能化起重机构成和工作模式,卸车翻转平台构成,焦炭卸料和运输控制,绞车控制,除尘系统构成。
重点阐述智能化卸车控制系统组成和操作模式,自动卸车工艺流程。
关键词:集装箱;智能化起重机;卸车翻转平台;控制系统;操作模式;卸车流程中图分类号:TP273 文献标识码:BIntelligent Unloading System for Container Coke TransportationZHU Hai-gui,Ling yun(MCC Huatian Nanjing Engineering & Technology Corporation, Nanjing, Jiangsu, 210019, China) Abstract: Taking the intelligent environmental protection reconstruction project of container transportation in Masteel coking plant as an example, this paper discusses the composition and automatic control of container coke intelligent unloading equipment. This paper introduces the transformation mode of train wagon, the structural characteristics of container, the composition and working mode of intelligent crane, the composition of unloading turnover platform, coke unloading and transportation control, winch control and dust removal system. It focuses on the composition and operation mode of intelligent unloading control system and automatic unloading processKey words: Container; Intelligent crane; Unloading turnover platform; Control system; Operation mode; Unloading process引言马钢炼焦总厂为了响应国家环保要求,控制粉尘污染,解决炼焦总厂第二炼焦分厂干熄焦向第三炼铁总厂运输过程中的扬尘问题,对焦炭运输系统进行装备升级与环保改造。
装卸自动化系统及装、卸货自动化方法

装卸自动化系统及装、卸货自动化方法标题:装卸自动化系统及装、卸货自动化方法引言概述:随着现代物流行业的快速发展,装卸作业的效率和精度要求也越来越高。
为了提高装卸作业的效率和准确性,自动化系统逐渐成为物流行业的主流选择。
本文将探讨装卸自动化系统及装、卸货自动化方法的相关内容。
一、装卸自动化系统1.1 自动化输送系统:自动化输送系统是装卸自动化系统的核心部份,通过输送带、升降机等设备将货物从一个地点转移到另一个地点,实现装卸作业的自动化。
1.2 自动化识别系统:自动化识别系统采用传感器、扫描仪等设备,对货物进行识别和定位,确保货物的准确装卸。
1.3 自动化控制系统:自动化控制系统通过PLC控制器、计算机等设备,实现对装卸作业的自动化控制和监控,提高作业效率和准确性。
二、装货自动化方法2.1 货物码垛系统:货物码垛系统采用机器人或者自动化设备,将货物按照预设的规则进行码垛,提高装货效率和准确性。
2.2 自动化包装系统:自动化包装系统采用自动包装机、封箱机等设备,对货物进行自动包装,减少人工介入,提高包装效率和质量。
2.3 自动化称重系统:自动化称重系统通过称重传感器和计算机系统,实现对货物分量的自动检测和记录,确保装货准确性。
三、卸货自动化方法3.1 自动化分拣系统:自动化分拣系统采用分拣机器人、传送带等设备,对货物进行自动分拣和分类,提高卸货效率和准确性。
3.2 自动化拆包系统:自动化拆包系统采用自动拆包机、分拣机等设备,对货物进行自动拆包和分类,减少人工介入,提高拆包效率和准确性。
3.3 自动化验货系统:自动化验货系统通过扫描仪、传感器等设备,对货物进行自动验货和记录,确保卸货准确性和完整性。
四、装卸自动化系统的优势4.1 提高作业效率:装卸自动化系统可以实现作业的自动化和高效化,大大提高了装卸作业的效率。
4.2 降低人工成本:自动化系统减少了人工介入,降低了人工成本,提高了企业的竞争力。
4.3 提高作业准确性:自动化系统可以减少人为错误,提高了装卸作业的准确性和稳定性。
自动化集装箱码头装卸工艺系统研究

自动化集装箱码头装卸工艺系统研究随着全球贸易的不断发展和集装箱运输的广泛应用,集装箱码头作为货物装卸的重要枢纽,扮演着至关重要的角色。
传统的人工装卸存在效率低下、劳动强度大、安全隐患多等问题,为了提高集装箱码头的装卸效率和安全性,自动化集装箱码头装卸工艺系统应运而生。
本文旨在对自动化集装箱码头装卸工艺系统进行研究,分析其工作原理、优势和发展趋势。
自动化集装箱码头装卸工艺系统是一种集成了自动化设备和智能控制技术的装卸系统。
其主要工作原理包括以下几个方面:1. 集装箱堆场管理:系统通过智能化堆场管理软件,对集装箱进行智能规划和管理,确保集装箱的合理堆放和高效利用。
2. 自动化堆垛机械装卸:采用自动化堆垛机械装卸设备,实现集装箱的自动装卸,避免了人工操作中的劳动强度大、效率低等问题。
3. 智能化运输系统:通过自动化输送设备和智能控制系统,实现集装箱的自动运输与转运,提高了装卸效率和安全性。
4. 数据集成与监控:系统通过大数据分析和智能监测技术,对装卸过程进行实时监控和数据分析,为系统优化和决策提供数据支持。
自动化集装箱码头装卸工艺系统相比传统的人工装卸具有明显的优势,主要体现在以下几个方面:1. 提高装卸效率:自动化集装箱码头装卸工艺系统利用智能化设备和控制技术,能够大幅提高集装箱的装卸效率,减少人工操作繁琐,降低装卸时间成本。
2. 降低劳动强度:自动化集装箱码头装卸工艺系统采用自动化装卸设备,能够减少人工劳动,降低了劳动强度,保障工人身体健康。
3. 提升安全性:系统采用智能监控技术,可以对装卸过程进行实时监测和控制,减少了人为操作的安全隐患,提升了装卸作业的安全性。
4. 降低成本:自动化集装箱码头装卸工艺系统可以有效降低人工成本和装卸时间成本,提升了码头的运营效益,降低了企业的运营成本。
5. 环保节能:自动化集装箱码头装卸工艺系统采用节能环保的设备和技术,降低了装卸过程中的能源消耗和环境污染。
当前,随着智能化技术的不断发展和集装箱运输的日益增长,自动化集装箱码头装卸工艺系统应用前景广阔,未来的发展趋势主要体现在以下几个方面:1. 智能化升级:未来自动化集装箱码头装卸工艺系统将更加智能化,通过人工智能和大数据技术,实现装卸作业的智能规划、自主控制和智能决策。
装卸自动化系统及装、卸货自动化方法

装卸自动化系统及装、卸货自动化方法标题:装卸自动化系统及装、卸货自动化方法引言概述:随着现代物流行业的快速发展,装卸作业的效率和精度要求越来越高。
为了提高装卸作业的效率和减少人力成本,装卸自动化系统应运而生。
本文将介绍装卸自动化系统的概念以及装、卸货自动化方法。
一、装卸自动化系统的概念1.1 自动化系统的定义自动化系统是指利用计算机、机械、电子等技术,通过一定的程序控制和调度,实现装卸作业的自动化进行。
1.2 系统组成装卸自动化系统通常由物料搬运设备、传感器、控制系统和执行机构等组成,通过这些部件的协同工作,实现装卸作业的自动化。
1.3 优势自动化系统可以提高装卸作业的效率和准确度,减少人为失误和劳动强度,同时还可以降低人力成本和提升企业竞争力。
二、装货自动化方法2.1 自动装卸机器人自动装卸机器人是一种可以代替人工进行装卸作业的智能机器人,它可以根据预设的程序和指令,自主完成装货作业。
2.2 自动输送线自动输送线是一种通过传送带或输送机等设备,将货物从一个地点运送到另一个地点的自动化系统,可以实现装货作业的自动化。
2.3 AGV(自动引导车)AGV是一种能够自主导航和运输货物的无人驾驶车辆,可以根据预设的路线和任务,自动进行装货作业。
三、卸货自动化方法3.1 自动卸货机器人自动卸货机器人可以根据预设的程序和指令,自主完成卸货作业,减少人为失误和提高卸货效率。
3.2 自动分拣系统自动分拣系统是一种能够根据货物的特征和目的地,自动将货物分类和分拣的系统,可以实现卸货作业的自动化。
3.3 AGV(自动引导车)AGV不仅可以用于装货作业,还可以用于卸货作业,通过自主导航和运输货物的功能,实现卸货作业的自动化。
四、装卸自动化系统的应用领域4.1 仓储物流装卸自动化系统在仓储物流领域得到广泛应用,可以提高仓库的货物周转率和准确度,降低仓储成本。
4.2 生产制造在生产制造领域,装卸自动化系统可以提高生产线的效率和稳定性,减少人为失误和提高产品质量。
装卸自动化系统及装、卸货自动化方法

装卸自动化系统及装、卸货自动化方法引言概述:随着物流行业的快速发展,装卸作业的效率和精度要求越来越高。
装卸自动化系统及装、卸货自动化方法成为了解决这一问题的重要途径。
本文将介绍装卸自动化系统的概念、原理及应用,以及装、卸货自动化方法的具体实施。
一、装卸自动化系统1.1 自动化系统概念:装卸自动化系统是指利用自动控制技术和设备,实现装卸作业的自动化操作,提高作业效率和准确性。
1.2 自动化系统原理:装卸自动化系统通过传感器、执行器、控制器等设备,实现对货物的自动抓取、搬运、堆放等操作,完成整个装卸过程。
1.3 自动化系统应用:装卸自动化系统广泛应用于仓储、物流、生产等领域,可以有效提高作业效率,减少人力成本,降低错误率。
二、装货自动化方法2.1 AGV装货:AGV(自动引导车)是一种能够自主行驶的无人驾驶车辆,可以实现货物的自动搬运和装卸操作。
2.2 机器人装货:机器人装货系统利用机器人手臂和视觉系统,可以实现对货物的自动识别、抓取和放置,提高装货效率和准确性。
2.3 输送线装货:通过设置输送线路,可以实现货物的自动输送和装载,减少人工搬运,提高装货速度和效率。
三、卸货自动化方法3.1 AGV卸货:类似于装货过程,AGV也可以用于货物的自动卸货操作,通过自动导航和搬运,实现货物的快速卸载。
3.2 机器人卸货:机器人卸货系统可以根据货物的特征和位置,自动识别、抓取和放置货物,实现卸货过程的自动化操作。
3.3 输送线卸货:利用输送线和机械装置,可以实现货物的自动卸载和分拣,减少人工干预,提高卸货效率。
四、装卸自动化系统优势4.1 提高作业效率:自动化系统可以实现连续、高效的装卸作业,减少作业时间,提高作业效率。
4.2 降低错误率:自动化系统减少了人为操作的干扰和误差,提高了作业的准确性和稳定性。
4.3 减少人力成本:自动化系统可以减少人力投入,降低作业成本,提高企业的竞争力。
五、未来发展趋势5.1 智能化发展:未来装卸自动化系统将更加智能化,集成人工智能、大数据等技术,实现更高效、更灵活的装卸作业。
仓储行业中的货物装载与卸载技术创新

仓储行业中的货物装载与卸载技术创新近年来,随着全球化进程的加速推进和电子商务行业的迅猛发展,仓储行业面临着日益巨大的货物处理压力。
为了提高工作效率、降低成本、缩短作业周期,并确保货物的安全和完好,仓储行业在货物装载与卸载技术方面不断进行创新。
本文将从自动化装载系统、智能卸载设备以及物流管理系统三个方面来分析仓储行业中的货物装载与卸载技术创新。
1. 自动化装载系统随着物流发展的迅猛,仓储行业对于装载效率的需求越来越高。
传统的人工装载方式已经无法满足高效装载的需求,因此自动化装载系统成为了仓储行业的重要创新方向。
自动化装载系统通过引入自动化机械设备和智能化控制系统,实现了货物装载过程的自动化和智能化。
这不仅提高了装载效率,还大大降低了人力成本。
同时,自动化装载系统还能减少因人为操作带来的误差和损坏,提高货物装载的准确性和安全性。
2. 智能卸载设备货物卸载是仓储行业中同样重要的工作环节。
为了提高卸载效率和减少安全事故的发生,智能卸载设备的应用变得日益普遍。
例如,自动堆垛机、卸货机器人等设备的应用,使得卸载过程更加高效、精确和安全。
自动堆垛机可以按照预先设置的程序和规则完成货物的分拣、堆放和卸载工作,大大缩短了卸载时间。
而卸货机器人则通过激光测距、视觉识别等技术,能够准确识别货物位置和形状,实现自主卸货,提高了卸载效率和准确性。
3. 物流管理系统随着仓储行业规模的不断扩大,传统的人工管理方式已经无法满足对物流信息化管理的需求。
物流管理系统的引入,使得货物装载与卸载工作有了更高效、更精确的管理方式。
物流管理系统通过实时监控货物的装载与卸载过程,可以准确掌握每个环节的时间、成本和效率等关键指标,从而优化作业流程,提高装载与卸载效率。
同时,物流管理系统还可以集成各个环节的信息,实现多方协同,加强对物流过程的监控和控制,提高整体运作效能。
综上所述,仓储行业中的货物装载与卸载技术创新对于提高工作效率、降低成本、确保货物安全至关重要。
- 1、下载文档前请自行甄别文档内容的完整性,平台不提供额外的编辑、内容补充、找答案等附加服务。
- 2、"仅部分预览"的文档,不可在线预览部分如存在完整性等问题,可反馈申请退款(可完整预览的文档不适用该条件!)。
- 3、如文档侵犯您的权益,请联系客服反馈,我们会尽快为您处理(人工客服工作时间:9:00-18:30)。
摘要:根据实际集装箱卸载的要求,构建轨道式自动化集装箱卸载系统。在此基 础上,采用 PC、西门子 S7-300 系列的 PLC、变频器、三相电机,通过以太网构 建 SCADA 系统。PLC 接收来自 PC 的起始位置、目标位置、搬运信号,实时控制 横、纵轴二维运动,并由 PC 实时跟踪、记录集装箱的运动轨迹。整个系统能够 实现平滑起停、自动安全卸载、智能故障诊断等功能。 引言 在当今低碳经济时代,全新的自动化集装箱装卸模式代表了装载机械的先进 发展方向,在港口、码头建立效率高、投资经济的自动化装载系统成为世界各国 在 21 世纪的一个研究热点。 上世纪 90 年代在荷兰鹿特丹港、 德国汉堡港相继建 成了自动化码头系统, 实现了集装箱的自动化装卸。但是现存的自动化码头的水 平运输均采用内燃机驱动的自动导航汽车,投资巨大,不易于推广。为了解决港 口自动化码头的现场问题, 行业内提出采用低架桥电驱动运输系统取代内燃机驱 动的自动导航汽车方案,降低了成本。 基于此方案和实际集装箱卸载要求,本文构建了轨道式港口集装箱码头物理 模型,并以此为研究平台,设计自动化集装箱卸载系统。该系统主要包括 4 部分 组成:PLC 控制变频器调速模块、位移检测模块、PC 与 PLC 通讯模块、上位机 PC 的组态设计模块。 1. 系统的总体设计 系统结构框图如图 1 所示:
现场有一个卡车停靠站和一个 10×10×4 的集装箱堆放站,当卡车停放 到位后,由 PC 机指定需要搬运的集装箱的起始位置、目标位置,当 PLC 接收 到搬运指令时,则智能自动的搬运集装箱。在搬运过程中,PLC 将运行指令 和转速给定输入到变频器,采用变频器矢量控制技术调节电动机的转速,从 而调节吊车的速度。同时,利用编码电缆位移传感器实时检测吊车的位置信 息, 根据反馈得到的位置信息给出期望转速, 控制电机的正、 反转以及起停。 PLC 及时将位置信息上传至 PC,以方便操作人员监控,如果出现紧急事件, 能够及时报警并作出相应的保护动作。 2. PC 与 PLC 的通讯 控制器 PLC 安放在低架桥轨道上的平板小车上,PC 由操作人员控制,考 虑到通讯的稳定性,可采用无线路由器实现计算机与 PLC 的以太网通讯。PC 可以随意移动, 在 WebAccess 的开发环境下, 实现 PC 与多台 PLC 的通讯模块 无线通讯。 系统中使用 S7-300 系列的 PLC:CPU314 的主核,CP343 通讯模块。 在 WebAccess 中新建子网如图 2 所示:设置各自 PLC 的地址,用不同的 IP 地址区分不同的 PLC,并设置“PG/PC 接口”为“TCP/IP->无线网络” 。
图 6 精密地址工作原理
精密地址实质上就是对绝对地址再进行细分,如图 6 所示,V1 =
V0
W 2
∗X−
1 = μ ∗ X − 1,当X < ������时,V0/V1 与 X 成线性关系。由于 G0、L0 的交叉间距 相同且错开μ, 故在绝对精度间距的每个位置总有一个 V0/V1 比值, 且这个比 值不受环境噪音和接收信号电平波动的影响。这样,就可以根据 V0/V1 的比 值确定吊车的精确位置。 根据工程经验, 细分数取 20, 如果μ = 100mm,则精密地址精度=5mm。 3.2 吊车位置检测设计 自行式轨道小车控制重心在车上,因此采用车上检测方式。小车要求定 位精确,误差在 5cm 之内,仅用绝对地址不能满足要求,必须增加一对地址 线采用精密地址检测方法。如图 7 所示,采用格雷母线车上检测方式的小车 位置检测系统,测量小车在轨道上的精确位置,即吊车所处的纵向位置,用 同样的方法可以检测出吊车的横向位置。
监控计算机 工业以太网
横向(X轴) 编码电缆位移 Profibus-DP 传感器
T-link
PLC(X) S7-300 控制横向运动
T-link
PLC(Y) S7-300 控制纵向运动
Profibus-DP
纵向(Y轴) 编码电缆位移 传感器
变频器
制动器
变频器
制动器
三相电机
三相电机
图 1 系统结构框图
3.1 格雷母线位置检测工作原理 如图 5 所示,以 4 个地址的检测系统为例来描述绝对地址检测方式:
图 5 格雷母线绝对地址工作原理
固定站的地址编码发射器以同频率分时方式分别将信号送给格雷母线标 准线,交叉线 1、交叉线 2,并通过电磁耦合方式将信号传送到移动站的天线 箱。移动站的地址编码接收器按顺序接收信号后,将两对交叉线的信号分别 与标准线信号比较,如果交叉线的信号相位与平行线的相位相同,那么定义 地址为“0” ,如果相位相反,定义地址为“1” 。因此地址 1 为“00” ,地址 2 为“01” ,地址 3 为“10” ,地址 4 为“11” 。实际上,用 n 对地址线可以检测 到2n 个地址。 理论上,只要将格雷母线最小步长 W 取得足够小,格雷母线定位精度就 可以做得很高,但是在工程上由于格雷母线芯线、天线箱尺寸误差、机车摆 动,磁场分布不均匀性,以及外界干扰等因素,格雷母线最小步长 W 取值收 到一定限制。W 取得太小,点磁感应面积变小,地址检测的信噪比低,造成 地址不稳定。根据工程经验,W=200mm 比较好。 绝对定位精度μ = W 2,格雷母线长度L = 2n × μ,如果格雷母线地址为 10 对,当 W=200mm 时,L=102.4m,实际运用时,根据轨道长度来适当调节 W。 如果只适用绝对地址,则精度最好为 100mm,并不能精确定位,无法确 保吊车的准确停止。因此,必须在绝对地址的基础上,对大地址进行细分能 进一步获得高精密地址。精密地址检测方法是在格雷母线中增加一对地址线 L0,L0 交叉间隔跟 G0 一样,只是错开半个步长。
数据类型的位置检测值和一个 WORD 类型的格雷母线工作状态值。程序将收 到的位置检测值进行格式和类型的转换并统一到自动化港式轨道坐标系下: 将格雷母线工作状态字根据其位定义进行解析,得到格雷母线故障及位置刷 新等信息。在格雷母线处于正常工作状态下,将处理过的位置值传递给 TPOSTN 变量,TPOSTN 变量即为吊车所处的当前位置。 4. 电机转速给定设计 当 PLC 接收到起始位置、目标位置、搬运信号之后,就平滑启动快速进 入匀速运动阶段,但是当吊车接近目标位置时,必须合理稳定的降速,使得 吊车平稳的停靠在目标位置。 4.1 减速过程的给定速度 由于实际小车在运行时可能出现振动、打滑、啃轨等情况,减速度跟给 定完全一致, 因此不能保证转速给定为 0 时, 小车到达目标位置。 实际情况, 可能出现小车没有到达目标位置但转速给定为 0;或是小车到达目标位置时, 转速给定还不为 0,要通过制定强行制动,由于小车惯性大,需要的制动力 大, 一方面造成制动器磨损, 缩短其使用寿命, 另一方面可能造成车轮抱死, 小车在轨道上滑移。所以,必须在小车接近目标位置之前的一段距离,将小 车的速度减到较小值,当小车到达目标位置时,立即使用制动,这样制动器 磨损小,且能够平稳停车。 小车越接近目标位置速度应该越小,按照这个理念,设计的转速给定方 法如下:先确定一个减速距离 S,系统实时检测小车当前位置 TPOSTN,并不 断计算当前位置与目标位置(STOPPOS)的差 eS,当位置差大于减速距离 S 时,小车转速给定保持初始给定;当位置差小于减速距离 S 时,小车需要开 始减速,位置差越小,转速给定越小;当差等于 0 时,转速给定也为 0, 可用 公式 1 表示,减速过程的转速给定如图 8 所示。
图 7 格雷母线车上检测方式
假设轨道总长度为 125m,若 W=100mm,则 L=102.4m,不满足实际轨道 的长度,所以适当增加 W 的值,W=2n −1 =
L 125000 29
=244.1mm,取 W=250mm,使
用 20 细分技术,则精密精度=6.25mm,基本上满足控制精度的要求。 控制系统采用 Profibus-DP 总线通过主从方式,实时地向格雷母线地址编 码器发送请求查询命令, 地址编码器收到请求命令后向 PLC 发送一个 DWORD
TMSREF0 TMSREF = TMSREF0 × eS S eS = TPOSTN − STOPPOS
(1)
图 8 减速过程的 9 小车速度控制结构图
小车运行前,根据控制中心(PC)发来的目标位置和减速距离,确定减 速位置,同时根据编码电缆位移传感器输入的小车当前位置确定运行距离, 并结合 PC 发来的参考速度, 确定小车的当前转速和运行方向。 当小车位置与 目标位置差小于 30mm 时,小车运行命令取消,当无运行命令且转速小于某 个值时,发送制动信号。即只要小车实际转速在目标前后 30mm 范围内减到 50 以下,变频器反馈制度信号,小车实现精确停车。 4.2 变频器控制电机转速 小车运动控制系统中,PLC 综合各种信息做出控制决策,即给出小车运 行命令和转速给定,而变频器的作用就是实现交流电机能够按照 PLC 给定的 转速运转。为实现集装箱的自动化卸载,小车必须能够准确定位,因此控制 系统必须能够精确控制小车的运行速度,对于过度过程的动态响应和转速精 度有很高的要求。因此,选择高性能的矢量控制变频器来实现电机转速的控 制。 4.3 变频器的通讯
图 3 监控节点的设置图
WebAccess 的监控界面如图 4 所示:
图 4 系统监控画面图
当点击搬运按键后,横向位置 x0、x1 被发送到控制横向运动的 PLC 中, 纵向位置 y0、y1 被发送到纵向运动的 PLC 中;由各自方向的 PLC 根据反馈得 到吊车位置,发送运行命令和速度给定信号至变频器;变频器接收到运行指 令和转速给定,根据电动机的转速反馈采用矢量控制驱动电动机;PLC 将吊 车的当前位置反馈给 PC,实时跟踪。 3. 位置检测设计 编码电缆(格雷母线)技术比较适合于自动式轨道小车的位置检测,格 雷母线位置检测有两种检测地址,即绝对地址和精密地址。
PLC 与变频器通过 T-Link 总线连接,采用主从方式进行通信,通讯格式 如图 10 所示。
图 10 变频器的 T-Link 通讯格式