冰铜吹炼
冰铜吹炼

总反应:
2FeS(l)+3O2(g)+SiO2(s)=2FeO ∙SiO2(l)+2SO2(g)
△H=-1029.6 MJ/mol •产物白冰铜:成分接近Cu2S •强烈放热:105 MJ/kg O2
第二阶段 造铜期(Blister copper stage)
除去白冰铜中剩余的S: Cu2S
2Cu2S(l)+3O2=2Cu2O(l)+2SO2 △G0=-148.6 kJ/mol Cu2S(l)+2Cu2O(l)=6Cu(l)+SO2 △G0=-50.7 kJ/mol 总反应: Cu2S(l)+O2=2Cu(l)+SO2 △H=-217.4 MJ/mol
思考题
从热力学原理来说,区分熔炼与吹炼有无 必要? 吹炼的两个阶段中烟气成份的变化? 吹炼操作时过早或者过晚进入造铜期的危 害?(筛炉时熔剂的加入量不合适)
谢谢大家 欢迎提出宝贵意见!
二、冰铜吹炼的基本原理
•
吹炼步骤及主要化学反应
•
两个阶段划分的热力学原因(优先氧化)
冰铜中各成分在吹炼中的行为
PbS
Bi2S3
Bi2S3 在吹炼过程中大部分被氧化为Bi2O3 ,生 成的Bi2O3 与Bi2S3 反应生成金属铋。铋大部分进入 烟气中,少量留在冰铜中。
As与Sb
这 两 种 元 素 的 硫 化 物 大 部 分 氧 化 成 As2O3 和
Sb2O3,少量被氧化成As2O5 和Sb2O5进入炉渣。只有
•
教材:134页
3 冰铜中各组分在吹炼中的行为 FeS
1.
氧化后以铁橄榄石造渣为主要反应 有部分生成 Fe3O4. 无SiO2时, Fe3O4很难被FeS 还原,而SiO2存在时,很容易反应生成铁橄榄石 炉渣。
冰铜吹炼方案

冰铜吹炼方案冰铜是一种重要的金属材料,广泛应用于电子、航空航天、汽车等领域。
冰铜吹炼是指将含有氧化物杂质的铜化合物加热至高温,通过与氢气反应来除去杂质。
本文将介绍一种高效的冰铜吹炼方案,确保产品质量和生产效率。
一、原材料准备在进行冰铜吹炼之前,需要准备以下原材料:1. 含有氧化物杂质的铜化合物:通常使用氧化铜作为原料,确保其纯度和颗粒度符合要求。
2. 氢气:作为还原剂,用于去除氧化物杂质。
二、设备准备进行冰铜吹炼需要一套专用的设备,包括:1. 吹炼炉:具备高温和密封性能,可以承受冰铜吹炼过程中的高温和压力。
2. 氢气供应系统:确保氢气供应稳定,并具备调节氢气流量的功能。
3. 空气净化系统:用于除去氢气中的杂质,保证吹炼过程的纯净度。
4. 温度监测系统:实时监测吹炼炉内的温度,确保吹炼过程中温度控制在合适的范围内。
三、操作步骤1. 将含有氧化物杂质的铜化合物放入吹炼炉中,并密封好炉门。
2. 打开氢气供应系统,将氢气注入吹炼炉中。
3. 启动吹炼炉,将温度升至设定的吹炼温度。
在升温过程中,需要适当调节氢气流量,确保温度升高的同时,氧化物杂质得以还原。
4. 当吹炼温度达到设定值后,保持一定时间使得冰铜吹炼反应充分进行。
5. 关闭氢气供应系统,停止加热。
待吹炼炉冷却至安全温度后,打开炉门取出冰铜产品。
四、质量控制为确保冰铜吹炼方案的质量稳定,需要进行以下检测和控制:1. 产品纯度检测:使用化学分析方法,检测冰铜中的杂质含量是否符合要求。
2. 产品颗粒度检测:使用粒度分析仪,测量冰铜颗粒的大小分布,确保产品的均匀性。
3. 温度控制:通过温度监测系统实时监控吹炼炉内的温度,确保吹炼过程中温度控制在合适的范围内。
五、优化改进为进一步提高冰铜吹炼方案的效率和质量,可以考虑以下优化改进措施:1. 设备改良:更新吹炼炉和氢气供应系统,提高温度控制和氢气供应的稳定性。
2. 工艺调整:优化吹炼温度、时间和氢气流量的配比,通过实验确定最佳参数组合。
冰铜(铜锍)PS转炉熔炼法的工艺过程以及其他吹炼工艺
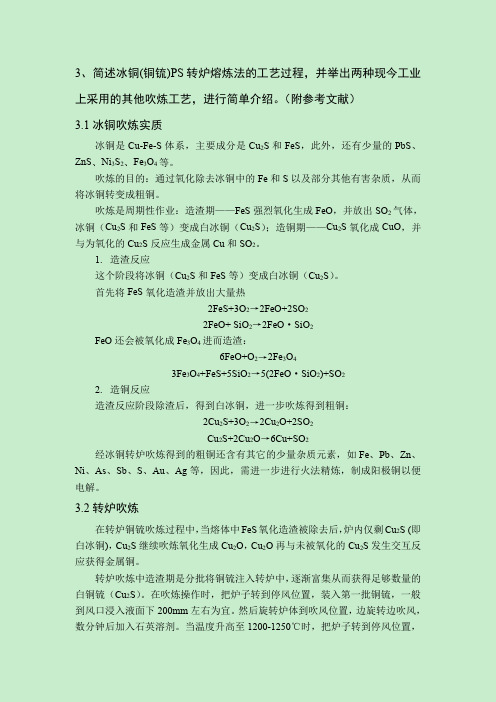
3、简述冰铜(铜锍)PS转炉熔炼法的工艺过程,并举出两种现今工业上采用的其他吹炼工艺,进行简单介绍。
(附参考文献)3.1冰铜吹炼实质冰铜是Cu-Fe-S体系,主要成分是Cu2S和FeS,此外,还有少量的PbS、ZnS、Ni3S2、Fe3O4等。
吹炼的目的:通过氧化除去冰铜中的Fe和S以及部分其他有害杂质,从而将冰铜转变成粗铜。
吹炼是周期性作业:造渣期——FeS强烈氧化生成FeO,并放出SO2气体,冰铜(Cu2S和FeS等)变成白冰铜(Cu2S);造铜期——Cu2S氧化成CuO,并与为氧化的Cu2S反应生成金属Cu和SO2。
1.造渣反应这个阶段将冰铜(Cu2S和FeS等)变成白冰铜(Cu2S)。
首先将FeS氧化造渣并放出大量热2FeS+3O2→2FeO+2SO22FeO+SiO2→2FeO·SiO2FeO还会被氧化成Fe3O4进而造渣:6FeO+O2→2Fe3O43Fe3O4+FeS+5SiO2→5(2FeO·SiO2)+SO22.造铜反应造渣反应阶段除渣后,得到白冰铜,进一步吹炼得到粗铜:2Cu2S+3O2→2Cu2O+2SO2Cu2S+2Cu2O→6Cu+SO2经冰铜转炉吹炼得到的粗铜还含有其它的少量杂质元素,如Fe、Pb、Zn、Ni、As、Sb、S、Au、Ag等,因此,需进一步进行火法精炼,制成阳极铜以便电解。
3.2转炉吹炼在转炉铜锍吹炼过程中,当熔体中FeS氧化造渣被除去后,炉内仅剩Cu2S(即白冰铜),Cu2S继续吹炼氧化生成Cu2O,Cu2O再与未被氧化的Cu2S发生交互反应获得金属铜。
转炉吹炼中造渣期是分批将铜锍注入转炉中,逐渐富集从而获得足够数量的白铜锍(Cu2S)。
在吹炼操作时,把炉子转到停风位置,装入第一批铜锍,一般到风口浸入液面下200mm左右为宜。
然后旋转炉体到吹风位置,边旋转边吹风,数分钟后加入石英溶剂。
当温度升高至1200-1250℃时,把炉子转到停风位置,加入冷料,随后继续吹炼。
采用顶吹吹炼相关工艺及生产操作技术性问题
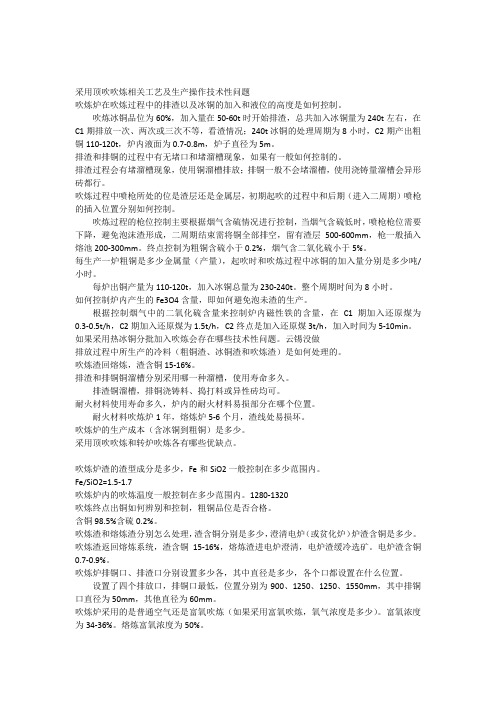
采用顶吹吹炼相关工艺及生产操作技术性问题吹炼炉在吹炼过程中的排渣以及冰铜的加入和液位的高度是如何控制。
吹炼冰铜品位为60%,加入量在50-60t时开始排渣,总共加入冰铜量为240t左右,在C1期排放一次、两次或三次不等,看渣情况;240t冰铜的处理周期为8小时,C2期产出粗铜110-120t,炉内液面为0.7-0.8m,炉子直径为5m。
排渣和排铜的过程中有无堵口和堵溜槽现象,如果有一般如何控制的。
排渣过程会有堵溜槽现象,使用铜溜槽排放;排铜一般不会堵溜槽,使用浇铸量溜槽会异形砖都行。
吹炼过程中喷枪所处的位是渣层还是金属层,初期起吹的过程中和后期(进入二周期)喷枪的插入位置分别如何控制。
吹炼过程的枪位控制主要根据烟气含硫情况进行控制,当烟气含硫低时,喷枪枪位需要下降,避免泡沫渣形成,二周期结束需将铜全部排空,留有渣层500-600mm,枪一般插入熔池200-300mm。
终点控制为粗铜含硫小于0.2%,烟气含二氧化硫小于5%。
每生产一炉粗铜是多少金属量(产量),起吹时和吹炼过程中冰铜的加入量分别是多少吨/小时。
每炉出铜产量为110-120t,加入冰铜总量为230-240t。
整个周期时间为8小时。
如何控制炉内产生的Fe3O4含量,即如何避免泡未渣的生产。
根据控制烟气中的二氧化硫含量来控制炉内磁性铁的含量,在C1期加入还原煤为0.3-0.5t/h,C2期加入还原煤为1.5t/h,C2终点是加入还原煤3t/h,加入时间为5-10min。
如果采用热冰铜分批加入吹炼会存在哪些技术性问题。
云锡没做排放过程中所生产的冷料(粗铜渣、冰铜渣和吹炼渣)是如何处理的。
吹炼渣回熔炼,渣含铜15-16%。
排渣和排铜铜溜槽分别采用哪一种溜槽,使用寿命多久。
排渣铜溜槽,排铜浇铸料、捣打料或异性砖均可。
耐火材料使用寿命多久,炉内的耐火材料易损部分在哪个位置。
耐火材料吹炼炉1年,熔炼炉5-6个月,渣线处易损坏。
吹炼炉的生产成本(含冰铜到粗铜)是多少。
冰铜冶炼
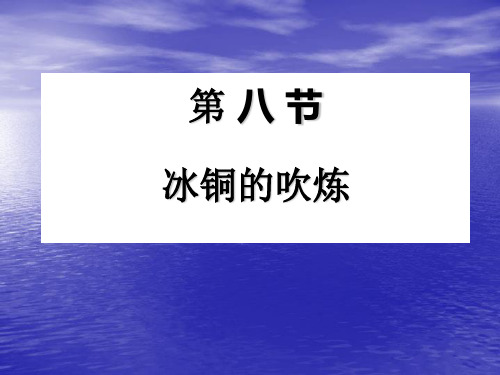
可以用Cu-Cu2S-Cu2O体系状态图8.4说明。
15
L1: 溶解有少量 Cu2S的铜相 L2: 溶解有少量 铜的Cu2S相,
图8.4 Cu-Cu2S-Cu2O 系状态图
16
Cu2S
Cu2S + Cu
Cu + Cu2S
过吹
Cu含 Cu2O
Cu
Cu2S+Cu
Cu+ Cu2S
17
4、Fe3O4 的生成与破坏
第八节 冰铜的吹炼
一、概述
硫化铜精矿经过造锍熔炼产出了铜锍。 铜锍是金属硫化物的共熔体。主要成分除了Cu、 Fe、S外,还含有少量Ni,Co,Pb,Zn,Sb,Bi, Au,Ag,Se等及微量SiO2,此外还含有2% ~4%的 氧,铜锍中的Cu,Pb,Zn,Ni等重有色金属一般 是以硫化物的形态存在,铁的物相主要是FeS,也 有少量以FeO、Fe3O4形态存在。 吹炼目的:除去铜锍中的铁和硫以及其它杂质, 获得粗铜。 铜锍是贵金属的良好捕集剂。 在吹炼过程中,金、银及铂族元素等贵金属几 乎全部富集于粗铜中。
23
1)Ni3S2在吹炼过程中的变化
Ni3S2是高温下稳定的镍的硫化物。当熔体 中有FeS存在时,NiO能被FeS 硫化成Ni3S2:
3NiO(s) + 3FeS(l) + O2 = Ni3S2 (l) +3FeO(l) +SO2
只有在FeS浓度降低到很小时,Ni3S2才按下式 被氧化:
Ni3S2+3.5O2=3NiO+2SO2 +1186kJ
2PbO + SiO2 = 2PbO· 2 SiO
由于PbS沸点较低(1280℃),在吹炼温度下, 有相当数量的PbS直接从熔体中挥发出来进入炉气 中。
冰铜吹炼过程周期性依据

温度/℃
1273 1373
1473 1573
[Cu2S]/[FeS] 2.5×104 1.62×104 1.1×104 7.8×103
在1200~1300 ℃吹炼温度下:只有当[Cu2S]为[FeS]的 11000~7800倍时,二者才同时氧化;实践中冰铜含 Fe低于1%时Cu2S才育(店铺)
2.5冰铜吹炼-2.5.2~吹炼过程周期性依据
(2) Cu2S氧化与粗铜的形成 ED段:到达E点后,如果继续鼓风向D点吹炼,粗铜中溶 氧量升高,会产生过吹,金属铜氧化-相内变化,到D点时 开始有Cu2O新相生成-质变 生产上一般含硫0.05%时停止吹炼,含Cu 98.5~99%; 过吹可用热冰铜还原。 。
fes1054378548tj表明有fes存在时cuo不可能稳定存在必然转化成cuo的相互反应才能进行这就是冰铜吹炼产出粗铜分造渣期和造铜期两个阶段的热力学依据过程周期性或间断吹炼25252吹炼过程周期性依据s氧化与粗铜的形成含124cu25252吹炼过程周期性依据有缘学习更多谓ygd3076或关注桃报
2.5冰铜吹炼-2.5.2~吹炼过程周期性依据
(1) FeS的优先氧化 造 锍 反 应 : FeS(l)+Cu2O(l)=Cu2S(l)+FeO(l) ; ΔG0= 105437-85.48T (J) 表明有FeS存在时,Cu2O不可能稳定存在,必然被硫化 成Cu2S。 只有当FeS完全氧化除去后,Cu2S和Cu2O的相互反 应才能进行,这就是冰铜吹炼产出粗铜分两个阶段的热 力学依据-过程周期性
冶金学—重金属冶金
2.5冰铜吹炼-2.5.2~吹炼过程周期性依据
(1) FeS的优先氧化 初始阶段FeS优先氧化,而FeS和Cu2S的同时氧化应
冰铜熔炼的基本原理

冰铜熔炼的基本原理冰铜熔炼是在高温和氧化气氛条件下将硫化铜精矿熔化生成MeS共融体的方法,又称造锍熔炼。
冰铜熔炼将精矿中的铜富集于冰铜中,而大部分铁的氧化物与加入的熔剂造渣。
冰铜和炉渣由于性质差别极大而分离。
根据炉料受热方式、热源、炉料所处状态、气氛氧化程度,冰铜熔炼有鼓风炉熔炼、反射炉熔炼、电炉熔炼、闪速炉熔炼、白银炉熔炼及一步炼铜等。
尽管设备不同,冶炼过程的实质是相同的,都属于氧化熔炼。
精矿首先熔炼获得冰铜,然后将冰铜吹炼成粗铜,要获得纯度较高的精铜,将粗铜进行精炼,即火法精炼和电解精炼,这些过程都包括了氧化过程。
熔炼的基本原理:冰铜熔炼所用炉料主要是硫化铜精矿和含铜的返料,出含有Cu、Fe、S等元素外,还含有一定量的脉石。
如用一般冶炼方法如反射处理,S/Cu比值较高的精矿,得到的冰铜品位低。
此时,要先进行氧化焙烧,脱去部分S然后熔炼,才能获得要求品位的冰铜。
如采用闪速炉或一步炼铜法测不受S/Cu比限制。
硫含量大,自热能力好。
炉料中的化合物有如下几种:1、硫化物熔炼生成精矿以CuS、FeS2、FeS为主;焙砂以Cu2S、FeS为主,还有少量ZnS、NiS、PbS等。
2、氧化物Fe2O3、Fe3O4、Cu2O、CuO、ZnO、MeO。
如炉料为焙砂氧化物较多,生生精矿中氧化物较少。
3、脉石CaCO3、MgCO3、SiO2、Al2O3等。
其中硫化物和氧化物数量占80%以上。
熔炼过程实质上是铁和铜的化合物及脉石在高温和氧化气氛条件下进行的一系列化学反应,并生成MeS相和MeO相,即冰铜和炉渣,二者因性质和密度的不同而分离。
熔炼炉料还包括加入的熔剂如石英、石灰石等,与精矿中部分铁盒脉石形成炉渣。
一、熔炼过程的化学反应1、热分解反应(1)、高价硫化物的热分解FeS2= FeS + 1/2 S2反应573K开始,833K激烈进行。
2CuFe S2= Cu2S + 2FeS +1/2 S2反应823K开始分解。
对冰铜吹炼及粗铜精炼各阶段终点判断的探讨

对冰铜吹炼及粗铜精炼各阶段终点判断的探讨葫芦岛有色金属集团公司杨文栋苏凤来摘要:本文介绍了在转炉冰铜吹炼及粗铜阳极炉精炼过程中,每个阶段终点判断方法。
关键词:冰铜吹炼;粗铜精炼;终点判断0前言在火法炼铜过程中,无论是转炉冰铜吹炼,还是粗铜阳极精炼,对每个阶段终点判断至关重要。
终点判断准确与否,直接关系到金属直收率、企业的安全生产及企业的经济效益。
本人结合多年生产实际,归纳总结了关于转炉冰铜吹炼和粗铜阳极炉精炼的终点判断方法,仅供大家参考。
1、冰铜转炉吹炼简述火法冶炼中,冰铜转炉吹炼分为两个周期:造渣期和造铜期。
在讨论造渣期和造铜期终点判断的同时,本文将筛炉期也单列出来一起讨论。
2、冰铜转炉吹炼终点判断方法2.1 造渣期终点判断方法造渣操作是转炉吹炼操作的关键。
在造渣反应过程中,造渣期终点判断不准,会造成渣子过吹、欠吹或喷炉事故的发生。
除影响金属直收率外,还会造成人身伤害及设备事故发生。
因此,造渣期终点判断尤为重要。
具体方法如下:2.1.1 化学成份分析法取白铍和转炉渣样化验,当白铍含铜为75+5%,渣含铜小于3%,渣含硅在19~24%时,证明造渣期终点到。
2.1.2 烟气及火焰判断法观察炉口,烟气飘浮边沿下降,气流活跃,四周似翻腾状溢出烟罩外,同时为焰由橙色变成黄绿色,再变为灰色,火焰强劲有力,亮度增加,当火焰转变为黄白色时,证明造渣期终点到。
2.1.3 喷溅物判断法炉口喷溅物较始吹时变得细小、密集、频繁并呈絮状、飘浮无力、发亮;喷溅物冷却凝固样呈空心粒状,证明造渣期终点到。
2.1.4 图示法在配备有温度指示表和二氧化硫浓度指示表的情况下,当出现温度指示值上下移动频繁,在1100~1300。
C范围内温度曲线图呈锯齿状;二氧化硫浓度指示值由低逐渐升高,当稳定在一、二个格内上下移动曲线图时,证明造渣期终点到。
2.1.5 炉后钎样判断法炉后钎样粘结物的颜色由灰白色转为青灰色,再转为油黑色,有光泽,结构松脆,能自动断裂脱离,证明造渣期终点到。
- 1、下载文档前请自行甄别文档内容的完整性,平台不提供额外的编辑、内容补充、找答案等附加服务。
- 2、"仅部分预览"的文档,不可在线预览部分如存在完整性等问题,可反馈申请退款(可完整预览的文档不适用该条件!)。
- 3、如文档侵犯您的权益,请联系客服反馈,我们会尽快为您处理(人工客服工作时间:9:00-18:30)。
Ni3S2
造渣期:主要以Ni3S2存在; 造铜期:自身的交互反应不能完成,会与 Cu或Cu2O反应生成少量Ni。
CoS
CoS是在冰铜FeS含量非常低时才被氧化。当冰铜 中含铁量低于10%时,CoS开始强烈氧化造渣。也就 是说造渣期末期开始才开始氧化。因此工业上把转炉 渣作为提钴的原料(0.4-0.5%)。
ZnS
造渣期:ZnS被O2或FeO氧化成ZnO,然后与SiO2造 渣。这一部分的锌占冰铜锌总量的70~80%。 15~20%的Zn按下列反应生成锌蒸气进入炉气。 2ZnO + ZnS = 3Zn(g) + SO2(g) ZnS + 2Cu = Cu2S + Zn(g)
造渣期:部分氧化生成的PbO容易与SiO2造渣。部分 PbS被炉气带走,有一部分PbS与PbO反应生成金属 铅。生成的Pb一部分进入烟气中,大部分留在Cu2S 中,到造铜期才被氧化。
PbS
Bi2S3
Bi2S3 在吹炼过程中大部分被氧化为Bi2O3 ,生 成的Bi2O3 与Bi2S3 反应生成金属铋。铋大部分进入 烟气中,少量留在冰铜中。
As与Sb
这 两 种 元 素 的 硫 化 物 大 部 分 氧 化 成 As2O3 和
Sb2O3,少量被氧化成As2O5 和Sb2O5进入炉渣。只有
魏寿昆:《冶金过程热力学》,上海科学技术出版社,1980年
冰铜吹炼分两个阶段的热力学依据
FeS(l) + Cu2O(l) = Cu2S(l) + FeO(l)
ΔG0= -105437-85.48T (J/mol)
实际体系的真实溶液中
[Cu2 S ] 3416 lg 1.72 [ FeS ] T
思考题
从热力学原理来说,区分熔炼与吹炼有无 必要? 吹炼的两个阶段中烟气成份的变化? 吹炼操作时过早或者过晚进入造铜期的危 害?(筛炉时熔剂的加入量不合适)
谢谢大家 欢迎提出宝贵意见!
二、冰铜吹炼的基本原理
•
吹炼步骤及主要化学反应
•
两个阶段划分的热力学原因(优先氧化)
冰铜中各成分在吹炼中的行为
Copper sulfide ore - Concentrate 0.2-1% 10-30% Matte - Blister copper – Cathode copper 30-70% 98.5-99.5% 99.5-99.98%
冰铜的主要成分:Cu2S-FeS,少量其它金属硫化物(如
Ni3S2、Co3S2、PbS、ZnS等)、贵金属(Au、Ag)、铂族金属、 微量的Se、Te、As、Sb、Bi等元素。
•
教材:134页
3 冰铜中各组分在吹炼中的行为 FeS
1.
氧化后以铁橄榄石造渣为主要反应 有部分生成 Fe3O4. 无SiO2时, Fe3O4很难被FeS 还原,而SiO2存在时,很容易反应生成铁橄榄石 炉渣。
2
如何控制Fe3O4的生成与析出?如何利用Fe3O4高熔点性质?
Cu2S
造渣期: 由于FeS的存在,Cu2S基本不氧化 造铜期: 氧化生成Cu2O后,Cu2O与Cu2S反应生成 金属铜
总反应:
2FeS(l)+3O2(g)+SiO2(s)=2FeO ∙SiO2(l)+2SO2(g)
△H=-1029.6 MJ/mol •产物白冰铜:成分接近Cu2S •强烈放热:105 MJ/kg O2
第二阶段 造铜期(Blister copper stage)
除去白冰铜中剩余的S: Cu2S
2Cu2S(l)+3O2=2Cu2O(l)+2SO2 △G0=-148.6 kJ/mol Cu2S(l)+2Cu2O(l)=6Cu(l)+SO2 △G0=-50.7 kJ/mol 总反应: Cu2S(l)+O2=2Cu(l)+SO2 △H=-217.4 MJ/mol
吹炼任务:利用空气中的氧,将液态冰铜中的铁和硫 几乎全部氧化除去,同时除去部分杂质,以得到粗铜
原料 液态冰铜; 空气(O2); 熔剂(SiO2) 产物 粗铜、炉渣、烟气、烟尘
PS 卧 式 转 炉
操作:冰铜吹炼为周期性作业
吹炼步骤
第一阶段:造渣期
加冰铜、熔剂-鼓风-排渣+加冰铜、熔剂-鼓风-排渣……=>白冰铜 加入熔剂,鼓风;排出炉渣,产出SO2烟气 产物:白冰铜(White metal/matte)Cu2S
三、冰铜吹炼的生产实践
P-S转炉 生产操作
主要工艺参数
Fe3O4既可以由FeS被氧化所生成,也可以由FeO被氧化所生成;Fe3O4生 成后只有在SiO2存在时才可能被FeS还原; 3Fe3O4(s)+FeS(l)+5SiO2(s)=5(2FeO∙SiO2) (l)+SO2 (固-液-固反应)
魏寿昆.冶金过程热力学.上海科学技术出版社,1980
只有当FeS完全氧化除去后,Cu2S和Cu2O的相互反 应才能进行。也就是说造渣没有完成前,不可能造铜。
2 吹炼步骤及其主要化学反应
第一阶段:造渣期(White metal stage)
除去熔锍中的全部铁和与之结合的硫:Cu2S-FeS 2FeS(l)+3O2(g)=2FeO(l)+2SO2(g) △G0=-225.9 kJ/mol 2FeO(l)+SiO2(s)=2FeO∙SiO2(l) △G0=-135.6 kJ/mol
筛炉:最后一次加入熔剂、鼓风,排渣
第二阶段:造铜期
只鼓风,产出SO2烟气;不加熔剂,也无炉渣 产物:粗铜(Blister copper)Cu
二、冰铜吹炼的基本原理
•
两个阶段划分的热力学原因(优先氧化)
•
吹炼各步骤主要化学反应
冰铜中各的热力学依据
冰铜吹炼氧化反应的分类
1、熔融硫化物氧化 MS+0.5O2=MO+SO2 2、金属硫化物与其它金属氧化物的反应 FeS+MO=MeS+FeO 3、同一金属硫化物与氧化物的交互反应 MS+2MO=3M+SO2
不同金属硫化物的优先氧化
转炉正常操作温度:1150-1300℃
1765K
•
FeS最容易被氧化
•
FeS+MeO->MeS+FeO最容易进行
•放热反应,6MJ/kg O2
Converting process: Autogenous
a->b:含硫不足的白冰铜 (S>19.4%) b->c:液相分层:白冰铜和 粗铜 c->d:单一的金属粗铜相 (S<1.0%)
终点:含S可达0.003%
白冰铜 粗铜
造铜期熔体成分和物相 的变化
小结
1、冰铜吹炼的任务及两个阶段 2、冰铜吹炼过程中的优先氧化(吹炼分为两 阶段进行的热力学依据) 3、两个阶段的主要化学反应
冰铜吹炼基本原理
冶金与生态工程学院 有色系
曹战民
冰铜吹炼(Converting of Matte)
一、任务 二、基本原理 FeS优先氧化(重点) 吹炼步骤及其主要化学反应 冰铜中各成分在吹炼中的行为 三、生产实践 P-S转炉 生产操作 主要工艺参数
一、冰铜吹炼的任务
火法炼铜的基本过程铜的富集过程
少量铜的砷化物和锑化物留在粗铜中。
贵金属
在吹炼过程中,冰铜中的Au、Ag以金属形 态留在粗铜中。 电解精炼时,贵金属富集于阳极泥。
三、冰铜吹炼的生产实践
P-S转炉
生产操作
主要工艺参数
冰铜吹炼 Converting of Matte
一、冰铜吹炼的任务
二、冰铜吹炼的基本原理
优先氧化 吹炼步骤及其主要化学反应 吹炼过程中冰铜成分的变化
为什么不能在P-S转炉中直接吹炼获得粗镍?
P-S转炉:鼓风时是转炉静止;一般鼓入空气;操作温度为1150-1300℃
NiO熔点为1984℃,以固态存在
Ni3S2(l)与Ni(l)完全互溶, 固相NiO容易漂浮在液 相表面,生成Ni(l)交互反应动力学上难以进行
生成Ni(l)的交互反应能进行的温度高达17001800℃