粘度,色差影响因素及其控制方法
车身油漆色差的分析及控制方法

车身油漆色差的分析及控制方法现代工业的蓬勃发展,人们对车辆外观的性能指标要求越来越高,车辆油漆色差是越来越受到重视的细节问题,而且复杂难以控制。
本文主要分析了影响车辆油漆色差的因素以及车辆油漆色差的控制方法。
一、前言现代车体越来越重视细节的搭配与装饰,例如车体与窗框、车门、端墙的颜色无偏差,以及编好组的列车每节车厢之间的颜色无偏差,这就对如何有效控制油漆色差提出了更高的要求。
现在色差的测量一般都采用仪器测量与目测相结合的方法,即根据标准比色板,通过仪器测量和目测相结合,使车辆与彩色小部件的色差在允许的误差范围之内。
这就需要究其根本,不断地改进技术和方法,控制车辆油漆色差。
二、车辆油漆色差的影响因素1.不同油漆批次的色差影响:不同批次的油漆由于在调配及原料采购过程中存在差异,所以就导致油漆本身就存在色差,但只要在所允许的色差范围之内,就能通过现场施工参数的调整来做出改变。
但是油漆原漆的色差误差范围要比现场施工范围要小,这是因为现场施工条件要远比油漆实验室的条件差,为了降低现场施工的难度,必须对原漆的色差做出严格控制。
2.油漆遮盖能力的影响:研究表明只有当材料的涂抹厚度大于15μm时,才能达到遮盖的效果。
一般车辆底色漆膜的厚度只能达到(12~15)μm,并不能完全遮盖底材,这是造成车辆漆膜发花、色差差的主要原因。
经研究表明,只有当漆膜的厚度达到遮盖厚度时,色差才能稳定,不再有大的波动。
这种缺陷主要表现在返修和补修时,由于一些颜色较浅的遮盖能力较差,再次重涂时容易超出色差误差范围。
3.现场施工参数的影响:现场施工参数的调整对油漆色差有直接影响。
主要是影响到L值的变化。
出漆量增大时,L减小,雾化空气、成型空气和喷涂速度增大时,L值增大。
4.手工补漆的影响:车辆涂漆的流水线上一般都设有手工补漆区,来弥补涂漆流程中的一些油漆缺陷和划碰伤,手工喷涂技术的高低和喷涂工艺的先进与否在很大程度上的影响了车辆油漆色差的质量。
黏度测量结果的影响因素分析
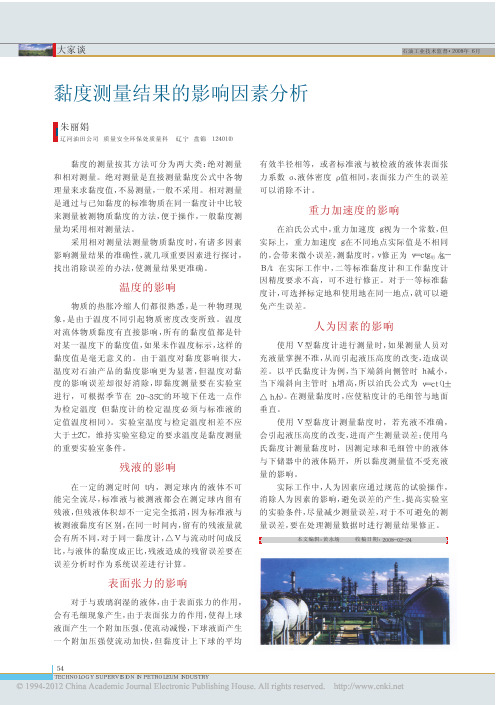
重力加速度的影响
在泊氏公式中, 重力加速度 g 视为一个常数, 但 实际上, 重力加速度 g 在不同地点实际值是不相同 的, 会带来微小误差, 测黏度时, v 修正为 v=ctg 用/gn- B/t。在实际工作中, 二等标准黏度计和工作黏度计 因精度要求不高, 可不进行修正。对于一等标准黏 度计, 可选择标定地和使用地在同一地点, 就可以避 免产生误差。
采用相对测量法测量物质黏度时, 有诸多因素 影响测量结果的准确性, 就几项重要因素进行探讨, 找出消除误差的办法, 使测量结果更准确。
温度的影响
物质的热胀冷缩人们都很熟悉, 是一种物理现 象, 是由于温度不同引起物质密度改变所致。温度 对流体物质黏度有直接影响, 所有的黏度值都是针 对某一温度下的黏度值, 如果未作温度标示, 这样的 黏度值是毫无意义的。由于温度对黏度影响很大, 温度对石油产品的黏度影响更为显著, 但温度对黏 度的影响误差却很好消除, 即黏度测量要在实验室 进行, 可根据季节在 20~35℃的环境下任选一点作 为检定温度( 但黏度计的检定温度必须与标准液的 定值温度相同) 。实验室温度与检定温度相差不应 大于±2℃, 维持实验室稳定的要求温度是黏度测量 的重要实验室条件。
残液的影响
在一定的测定时间 t 内, 测定球内的液体不可 能完全流尽, 标准液与被测液都会在测定球内留有 残液, 但残液体积却不一定完全抵消, 因为标准液与 被测液黏度有区别, 在同一时间内, 留有的残液量就 会有所不同, 对于同一黏度计, △V 与流动时间成反 比, 与液体的黏度成正比, 残液造成的残留误差要在 误差分析时作为系统误差进行计算。
实际工作中, 人为因素应通过规范的试验操作, 消除人为因素的影响, 避免误差的产生。提高实验室 的实验条件, 尽量减少测量误差, 对于不可避免的测 量误差, 要在处理测量数据时进行测量结果修正。
产品粘度之我见
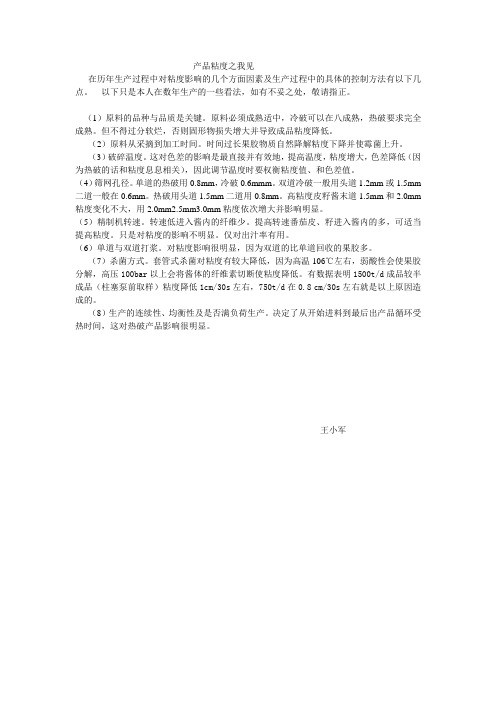
产品粘度之我见在历年生产过程中对粘度影响的几个方面因素及生产过程中的具体的控制方法有以下几点。
以下只是本人在数年生产的一些看法,如有不妥之处,敬请指正。
(1)原料的品种与品质是关键。
原料必须成熟适中,冷破可以在八成熟,热破要求完全成熟。
但不得过分软烂,否则固形物损失增大并导致成品粘度降低。
(2)原料从采摘到加工时间。
时间过长果胶物质自然降解粘度下降并使霉菌上升。
(3)破碎温度。
这对色差的影响是最直接并有效地,提高温度,粘度增大,色差降低(因为热破的话和粘度息息相关),因此调节温度时要权衡粘度值、和色差值。
(4)筛网孔径。
单道的热破用0.8mm,冷破0.6mmm。
双道冷破一般用头道1.2mm或1.5mm 二道一般在0.6mm。
热破用头道1.5mm二道用0.8mm。
高粘度皮籽酱末道1.5mm和2.0mm 粘度变化不大,用2.0mm2.5mm3.0mm粘度依次增大并影响明显。
(5)精制机转速。
转速低进入酱内的纤维少。
提高转速番茄皮、籽进入酱内的多,可适当提高粘度。
只是对粘度的影响不明显。
仅对出汁率有用。
(6)单道与双道打浆。
对粘度影响很明显,因为双道的比单道回收的果胶多。
(7)杀菌方式。
套管式杀菌对粘度有较大降低,因为高温106℃左右,弱酸性会使果胶分解,高压100bar以上会将酱体的纤维素切断使粘度降低。
有数据表明1500t/d成品较半成品(柱塞泵前取样)粘度降低1cm/30s左右,750t/d在0.8 cm/30s左右就是以上原因造成的。
(8)生产的连续性、均衡性及是否满负荷生产。
决定了从开始进料到最后出产品循环受热时间,这对热破产品影响很明显。
王小军。
化工产品粘度检验流程与质量控制
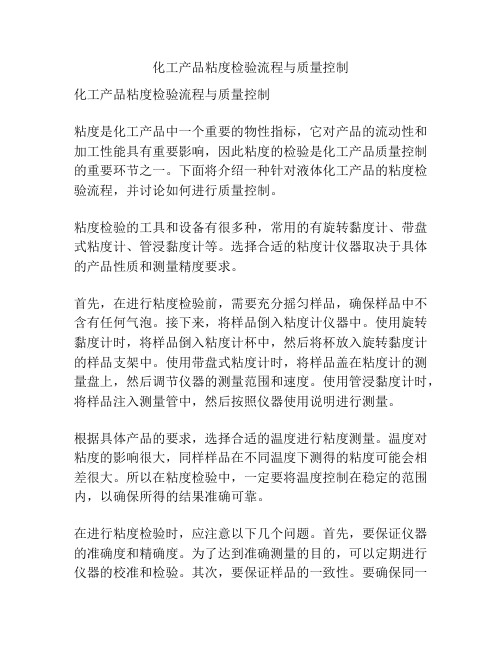
化工产品粘度检验流程与质量控制化工产品粘度检验流程与质量控制粘度是化工产品中一个重要的物性指标,它对产品的流动性和加工性能具有重要影响,因此粘度的检验是化工产品质量控制的重要环节之一。
下面将介绍一种针对液体化工产品的粘度检验流程,并讨论如何进行质量控制。
粘度检验的工具和设备有很多种,常用的有旋转黏度计、带盘式粘度计、管浸黏度计等。
选择合适的粘度计仪器取决于具体的产品性质和测量精度要求。
首先,在进行粘度检验前,需要充分摇匀样品,确保样品中不含有任何气泡。
接下来,将样品倒入粘度计仪器中。
使用旋转黏度计时,将样品倒入粘度计杯中,然后将杯放入旋转黏度计的样品支架中。
使用带盘式粘度计时,将样品盖在粘度计的测量盘上,然后调节仪器的测量范围和速度。
使用管浸黏度计时,将样品注入测量管中,然后按照仪器使用说明进行测量。
根据具体产品的要求,选择合适的温度进行粘度测量。
温度对粘度的影响很大,同样样品在不同温度下测得的粘度可能会相差很大。
所以在粘度检验中,一定要将温度控制在稳定的范围内,以确保所得的结果准确可靠。
在进行粘度检验时,应注意以下几个问题。
首先,要保证仪器的准确度和精确度。
为了达到准确测量的目的,可以定期进行仪器的校准和检验。
其次,要保证样品的一致性。
要确保同一产品的不同批次样品在相同的条件下测量,以保证结果的一致性和可比性。
最后,要保证操作的规范性。
粘度计仪器的使用和操作要遵循相关的标准和规范,保证测量结果的准确性和可重复性。
质量控制对于化工产品粘度的检验非常重要。
首先,要建立严格的质量控制标准和规范。
根据产品的要求和应用领域,制定合适的粘度上下限,对于不同产品可以制定不同的要求。
其次,要建立完善的样品管理和追溯体系。
通过对样品进行记录和编号,可以随时查找和追溯,以确保产品质量。
同时,要加强对生产过程中关键参数的控制。
比如,加工温度、搅拌速度等对产品粘度有直接影响的参数,应加以监控和控制。
此外,还要进行定期的检验和抽样检测,对产品进行全面的检测和评估。
色差控制
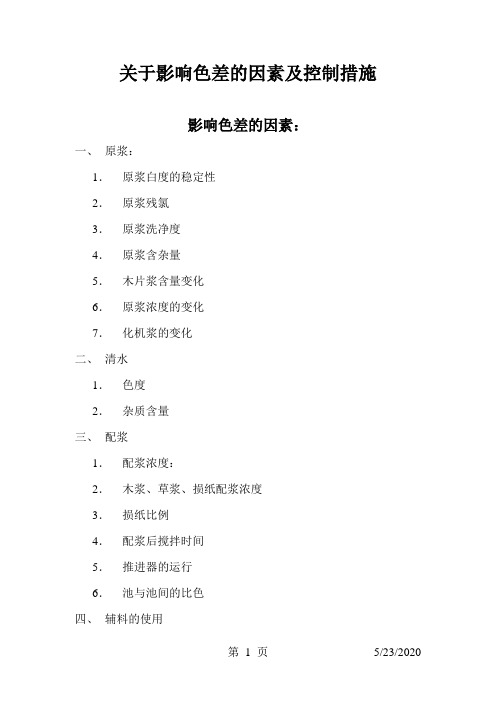
关于影响色差的因素及控制措施影响色差的因素:一、原浆:1.原浆白度的稳定性2.原浆残氯3.原浆洗净度4.原浆含杂量5.木片浆含量变化6.原浆浓度的变化7.化机浆的变化二、清水1.色度2.杂质含量三、配浆1.配浆浓度:2.木浆、草浆、损纸配浆浓度3.损纸比例4.配浆后搅拌时间5.推进器的运行6.池与池间的比色四、辅料的使用1.阳离子淀粉的使用2.填料的使用,灰份的控制3.原淀粉,填料的白度4.助剂的使用五、纸机工艺:1.网部真空度2.气压,水份六、损纸处理:控制措施一1.原浆白度必须必须稳定,每池浆与上一池浆之间不能超过05%,纸车化验员要加强对原浆浆白度的检测。
3.原浆白度要求无残氯,纸车兑浆工每池浆都要闻浆的气味,用碘化钾试纸检测残氯4.原浆洗度,要求中化定期检测原浆钙离子含量5.纸车化验员每池浆要观察原浆的颜色,并留浆样观察观察方法:①几池浆放在一起比颜色。
②抄片测L、a、b 值。
③取盆水连续抄3-5池张纸样,第一张纸样与最后一张纸样白度不超过1%。
否则视为原浆杂质含量过大。
6.木片混和均匀性:要求木片在草浆中混和均匀,判断办法:抄片测L、a、b值。
7.原浆浓度,原浆浓度必须稳定,浓度差不能超过0.5%。
8.制浆贮浆池、打浆段贮浆池均需保证一定浆位。
9.每倒塌过一次草浆,兑料工都需留样并观察浆池子与之间的原浆颜色是否一致,用鼻子闻原浆是否有气味,若有可用碘化钾试纸检测。
若观察色相不同,可抄样测L、a、b值,同时检测浆中的含杂量。
检测方法:取一分水,在水中抄3-5张纸样,检测第一张纸样与最后一张样的白度差,从而判断原浆的含杂量。
二10.清水色度的检测:要求化验员每班取3-5次水样,目测对比所取水样与标准水样色度的差别。
若有差别则采取以下判别方法:①取原浆分别用蒸馏水和清水抄片测纸样白度,若用清水所抄纸样的白度与蒸馏水所抄纸样的白度相差超过2度(也可根据本厂实际制定标准),则视所用水有问题。
②引起清水不合格原因可能有两方面:一是清水色度不合格,二是清水浊度不合格。
喷漆工艺中常见的质量问题及分析处理方法
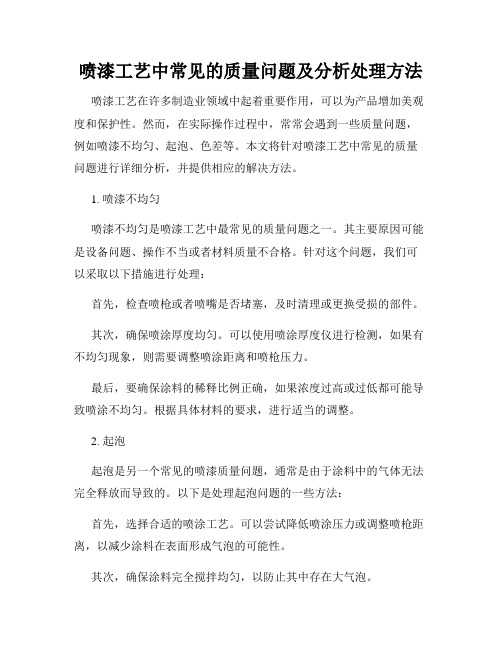
喷漆工艺中常见的质量问题及分析处理方法喷漆工艺在许多制造业领域中起着重要作用,可以为产品增加美观度和保护性。
然而,在实际操作过程中,常常会遇到一些质量问题,例如喷漆不均匀、起泡、色差等。
本文将针对喷漆工艺中常见的质量问题进行详细分析,并提供相应的解决方法。
1. 喷漆不均匀喷漆不均匀是喷漆工艺中最常见的质量问题之一。
其主要原因可能是设备问题、操作不当或者材料质量不合格。
针对这个问题,我们可以采取以下措施进行处理:首先,检查喷枪或者喷嘴是否堵塞,及时清理或更换受损的部件。
其次,确保喷涂厚度均匀。
可以使用喷涂厚度仪进行检测,如果有不均匀现象,则需要调整喷涂距离和喷枪压力。
最后,要确保涂料的稀释比例正确,如果浓度过高或过低都可能导致喷涂不均匀。
根据具体材料的要求,进行适当的调整。
2. 起泡起泡是另一个常见的喷漆质量问题,通常是由于涂料中的气体无法完全释放而导致的。
以下是处理起泡问题的一些方法:首先,选择合适的喷涂工艺。
可以尝试降低喷涂压力或调整喷枪距离,以减少涂料在表面形成气泡的可能性。
其次,确保涂料完全搅拌均匀,以防止其中存在大气泡。
另外,要保证基材的表面干燥、清洁和光滑,以便涂料能够更好地附着并排出潜在的气泡。
3. 色差色差是指涂装表面出现的不一致的颜色。
这可能是由于涂料本身的质量问题、施工环境的差异或操作人员的不当处理导致的。
下面是解决色差问题的几种方法:首先,确保使用的涂料来源可靠,并符合预期颜色的要求。
其次,要控制好施工环境的温度和湿度。
过高或过低的温度都会影响涂料的干燥速度和颜色表现。
另外,操作人员应该严格按照涂料生产厂家提供的使用说明进行操作,以确保正确的涂装过程。
4. 涂料流挂涂料流挂是指喷涂后在表面上形成垂直流痕或滴状流动的现象。
这可能是由于喷涂过度或者涂料粘度过高导致的。
下面是处理涂料流挂问题的一些建议:首先,调整喷涂时间和压力,确保每一次喷涂的涂料量适中。
其次,可以尝试使用低粘度的涂料,以减少涂料在表面上流动的可能性。
关于水性油墨粘度控制指标的几个影响因素
关于水性油墨粘度控制指标的几个影响因素粘度是油墨内聚力的大小,也是水墨应用中最主要的控制指标。
水墨的粘度过低,会造成色浅、网点扩大量大、高光点变形、传墨不均匀等弊端;水墨粘度过高,会影响网纹辊的传墨性能,墨色不匀,颜色有时反而印不深,同时容易造成脏版、糊版、起泡、不干等弊病。
粘度是油墨内聚力的大小,也是水墨应用中最主要的控制指标。
水墨的粘度过低,会造成色浅、网点扩大量大、高光点变形、传墨不均匀等弊端;水墨粘度过高,会影响网纹辊的传墨性能,墨色不匀,颜色有时反而印不深,同时容易造成脏版、糊版、起泡、不干等弊病。
1、温度对水墨粘度的影响车间温度对印刷质量的影响,相对湿度在60%~85%较好。
在冬、夏季温差大时,粘度的表现最为敏感。
温度高时,水分蒸发快,干燥快,在操作时,就要注意延长干燥时间或提高机器速度;温度低时,水分蒸发慢,水墨干燥也慢,在操作时,可提高水墨干燥速度或加开烘干装置。
冬季使用时,因水墨在0℃以下容易结冰,如果水墨结冰后,可放置在温度高的房间内,让其自然溶解,搅拌均匀后,可继续使用。
在实际生产中,当使用带有刮墨刀的印刷机时,温度过低时油墨的传墨量不如温度稍高时稳定。
油墨温度升高会使粘度下降,其结果是使印品密度降低,墨层变薄。
要保持印刷质量的一致性,就必须保持油墨粘度一致。
印刷者必须高度重视油墨温度所带来的影响,在印刷前应把的用油墨的温度稳定在印刷车间的温度。
这一措施非常重要,否则印刷过程中的油墨密度将会有较明显的变化。
2、触变性对水墨粘度的影响触变性是指油墨在外力搅拌作用下流动性增大,停止搅动后流动性逐渐减小,恢复原状的性能。
水墨放置时间久了以后,有些稳定性差的油墨容易沉淀、分层。
还有的出现假稠现象。
这时,可充分搅拌,经过一定时间的搅拌后,以上问题自然消失。
在使用新鲜水墨时,一定要提前搅拌均匀后,再作稀释调整。
或预计到一定量的墨上机后,粘度下降程度,因机中含水和墨的触变性可以改善墨的流动性。
影响番茄酱粘度、色差因素的分析与控制
是 冷 破 和 热 破 酱 的 粘 度 产 生 机 理 及 粘 度 差 别 的 原 因 。粘 性 果 胶物质在这种弱酸性受热环境中可继续降解而失去粘性。
绍色差控制方法。
( 4) 有无破碎保鲜真空装置。理论上 讲 破 碎 后 脱 气 可 防
( 1) 原料成熟度。冷破色差很容易达标( 2.1 以上) ,而热破
止各种褐变以提高色差。另外, 粘度、色差还有重要的一点是
必须选用完全成熟的原料并且是自然成熟的才能达到 2.0 以
稳定性, 除以上因素外还有原料品种不一, 成熟度不均匀, 热
( 1) 高粘度原酱做番茄沙司可节省原酱。因此, 与低粘度 相 比 可 降 低 成 本 。即 相 同 量 高 粘 度 原 酱 较 低 粘 度 原 酱 可 做 更 多的直接食用产品。
( 2) 消费者对直接食用的番茄制品 的 鲜 红 程 度 有 要 求 高 , 而 原 酱 的 色 差( a/b 值) 直 接 决 定 了 成 品 的 外 观 好 坏 。 因 此, 客户希望原酱色差( a/b 值) 越大越好。下面我就对这一问 题详述:
( 5) 精制机转速。转速低, 进入酱内的 纤 维 少 , 提 高 转 速 番茄皮、籽进入酱内的多, 这样可适当提高粘度 , 对 粘 度 影 响 不很明显, 仅对出汁率有用。
( 6) 单道、双道打浆。对粘度影响很明 显 , 这 是 因 为 双 道 打浆果胶回收率高缘故。
车身油漆色差的影响因素及控制方法
车身油漆色差的影响因素及控制方法摘要:从色漆材料、喷涂工艺、喷涂设备及供漆系统状态等方面探讨了色差的影响因素,提出了相应的控制方法。
1 前言车身油漆色差是每个涂装生产部门都会遇到的一个非常复杂且难以控制的问题,随着保险杠、门把手、后视镜及加油小门等彩色塑料件的大量采用,要求车身与塑料件的颜色无偏差,这就对车身油漆色差的控制提出了更高的要求。
目前轿车厂流行的方法是采用仪器测量与目测相结合的方式来控制色差,一般提供一块标准颜色样板,要求车身及塑料配件的颜色与该标准样板相比无论是目测,还是仪器测量都应接近。
车身油漆色差的影响因素众多,它与色漆材料、喷涂工艺、喷涂设备、供漆系统状态等因素密切相关。
本文就车身油漆色差的控制谈一点看法。
2.色差的概念及测量2.1 色差为了定量地表示颜色,目前通常采用CIE 表色系统,它采用分光光度法对颜色进行分析,精度高。
Lab 色空间是目前最流行的用于测量物体颜色的色空间(如图1所示)。
在该色空间中,L *为明度,+L *为白色方向,-L *为黑色方向。
a *,b *为色度坐标,其中+a *为红色方向,-a *为绿色方向,+b *为黄色方向,-b *为蓝色方向,中心为无色。
L *、a *、b *可由三刺激值X 、Y 、Z 计算而得。
图1 L *a *b *色空间LCH 色空间与Lab 色空间的色度图相同,但该色空间为柱面坐标而不是直角坐标。
L *表示明度,与Lab 色空间的L *值相同,H 表示色相,C 表示饱和度。
CIELAB 色空间中的两个色度值(L *样品,a *样品,b *样品)和(L *标准,a *标准,b *标准)之间的色差△E ab *由下式决定:△E ab * = [(△L *)2+(△a *)2+(△b *)2]1/2绿 -a*其中:△L*= L*样品- L*标准(明度差异),△a*= a*样品- a*标准(红/绿差异),△b*= b*样品- b*标准(黄/蓝差异)如△L*为正值,说明样品颜色偏浅;△L*为负值,样品偏深。
乳胶漆质量控制
乳胶漆质量控制一、引言乳胶漆是一种常见的涂料,广泛应用于室内和室外装饰。
为了确保乳胶漆的质量,需要进行严格的质量控制。
本文将详细介绍乳胶漆质量控制的标准格式,包括乳胶漆的外观、粘度、干燥时间、附着力等多个方面。
二、外观质量控制1. 乳胶漆的颜色应与样品一致,不应浮现色差。
2. 乳胶漆的表面应平整,不应有明显的颗粒或者凹凸不平。
3. 乳胶漆的涂层应均匀,不应有滴落、流淌或者起皮现象。
4. 乳胶漆的涂层应具有良好的光泽,不应有明显的暗淡或者反光不均匀现象。
三、粘度质量控制1. 乳胶漆的粘度应符合标准要求,普通应在20-50KU之间。
2. 采用粘度计进行测量时,应按照标准操作程序进行,确保结果的准确性。
3. 若乳胶漆的粘度超过标准范围,可能会导致涂层施工难点或者涂膜质量不稳定,应及时调整粘度。
四、干燥时间质量控制1. 乳胶漆的干燥时间应符合标准要求,普通应在2-4小时之间。
2. 干燥时间的测定可以采用触摸干燥法或者仪器测定法,测定时应按照标准操作程序进行。
3. 若乳胶漆的干燥时间过长,可能会延长施工周期或者影响涂膜的质量,应及时调整干燥时间。
五、附着力质量控制1. 乳胶漆的涂层应具有良好的附着力,不应浮现剥离或者起皮现象。
2. 附着力的测定可以采用划格法或者剥离法,测定时应按照标准操作程序进行。
3. 若乳胶漆的附着力不符合标准要求,可能会导致涂层易剥离或者起皮,应及时调整涂料配方或者施工工艺。
六、其他质量控制要点1. 乳胶漆的密度应符合标准要求,普通应在1.3-1.5g/cm³之间。
2. 乳胶漆的PH值应符合标准要求,普通应在7-9之间。
3. 乳胶漆的固含量应符合标准要求,普通应在30-50%之间。
4. 乳胶漆的稀释比例应符合标准要求,普通应在1:1-1:3之间。
七、结论乳胶漆质量控制是确保乳胶漆质量稳定的重要手段。
通过对乳胶漆的外观、粘度、干燥时间、附着力等方面进行严格控制,可以保证乳胶漆的质量符合标准要求。
- 1、下载文档前请自行甄别文档内容的完整性,平台不提供额外的编辑、内容补充、找答案等附加服务。
- 2、"仅部分预览"的文档,不可在线预览部分如存在完整性等问题,可反馈申请退款(可完整预览的文档不适用该条件!)。
- 3、如文档侵犯您的权益,请联系客服反馈,我们会尽快为您处理(人工客服工作时间:9:00-18:30)。
粘度、色差影响因素及控制方法番茄酱质量有霉菌、浓度、粘度、色差(色值)、番茄红素、PH值、黑斑、总酸、析水度(仅对热破),感观事项指标。
其中感观、霉菌及浓度直接决定产品是否合格。
而粘度、色差(色差值)、析水度则反映产品的优劣,这对热破产品尤为明显。
众多客户往往对粘度及色差更重视,愿意购买高粘度并且深红色而不是泛黄的热破酱。
这有以下两点原因:1、使用高粘度原酱做番茄沙司可节省原酱,因此可降低成本,其他许多产品也类似。
即相同量高粘度原酱较低粘酱可做更多的直接食用的产品,因此客户希望原酱越粘越好2、消费者对直接食用的番茄制品的鲜红程度有较高要求。
而原酱的色差(色值)直接决定了成品外观的好坏。
因此客户希望原酱色差(色值)越高越好。
新疆气候干燥少雨,日照长阳光充足,并且昼夜温差大。
这一独特的气候和环境使新疆番茄原料的固形物含量高,番茄红素含量高,亩产高,并且不易腐烂,适宜运输,加工期长,同时霉菌指标低。
这一大优势就使新疆番茄酱在国际市场上有很强的竞争力。
(当然价格优势也同等重要)。
要使质量优势充分发挥,还需加强生产过程控制才能达到高粘度色差。
下面我们就对这一问题详述。
首先我们必须对粘度、色差有关知识有个大体了解。
粘度指数样品酱稀释至一定程度(常规12.5%皮籽酱12%浓度),20℃30秒钟酱体流过的长度。
其单位是cm/12.5%、30秒。
它定量的反映了酱的粘性。
测量仪器是确定的粘度仪。
所以应该这样理解:粘度越大,值越小:值越大,酱就不粘。
粘度与粘度值相反。
色差即a/b值,红比黄。
确切的说是酱体中番茄红素与番茄素含量的比值,它反映的是酱体红的程度,同时反映原料的成熟度。
它没有单位。
色差越大酱体越红,外观也越好。
其次,我们还要对番茄粘度产生机理、番茄物料在加工过程中发生的生化反应及色差降低原因有个大体的了解。
酱体之所以有粘性是因为存在果胶物质包括原果胶、果胶及果胶酸三种状态。
原果胶不溶于水,它与纤维素结合存在于细胞壁中,有粘性。
果胶可溶于水,它存在于细中,有粘性。
果胶酸可溶于水,存在于细胞中,无粘性。
未成熟的果实细胞间含有大量原果胶,因而组织坚硬。
随着成熟的进程,原果胶在果胶酶的作用下水解与纤维素分离成为果胶,并渗入细胞液内,果实变软有弹性,此时果实成熟。
果胶在果胶酶的作用下水解成果胶酸,果实变成软塌状态,粘性逐渐降低。
原果胶酶及果胶对完整的得番茄作用很慢,但对于破碎受伤的番茄作用迅速。
这两种酶对热很敏感,77℃其活性完全钝化,为使产品达到一定粘度就要通过物料预热钝化酶的活性,保存有粘性的果胶物质,因此冷破酱预热(60℃-72℃)只是部分钝化其活性,而且要通过预热的作用,使果胶同纤维素分离,得到更多粘性果胶物质,这就是冷破和热破的粘度产生机理及粘度差别的原因。
粘性果胶物质在这种弱酸新受热环境中可继续降解而失去粘性。
番茄红素是一种热敏性物质,长时间受热对其损失很大,会使色差降低。
另外酶促褐变,非酶褐变,焦糖化褐变,vc褐变都会随受热时间加长而加深,使酱体发暗变黑,并使色差降低,这就是色差降低机理。
明白了粘度及色差降低机理,要分析影响因素及生产过程中具体控制方法就比较容易了。
先介绍粘度控制方法。
一、原料的品质。
这是关键因素。
原料必须成熟适中,冷破要求八成熟到全熟,已使色差值合格。
但不得过分软烂,否则固形物损失就会增大并且产品粘度降低二、原料从采摘到加工时间。
时间过长果胶物质自然降解产品粘度降低,霉菌也会上升。
三、破碎温度。
这对粘度影响是直接并最有效的。
提高温度,粘度将增大(粘度值下降)同时色差降低,因此调节温度时要权衡粘度值、色差值同时合格并稳定。
四、筛网孔径(末道筛网)。
单道打浆时,常规冷破用0.6mm,常规热破用0.8mm双道打浆时,冷破用 1.2mm/0.6mm或 1.5mm/0.6mm筛网,热破用1.5mm/0.8mm筛网。
高粘度皮籽酱,末道用1.5mm、2.0mm或2.5mm粘度相差不得大,用2.5mm、4.0mm、6.0mm粘度依次增大并影响程度明显。
五、精制机、打浆机转速。
对粘度影响不很明显。
六、单道双道打浆机。
对粘度影响很明显。
新线60℃与老线68℃可生产出粘度相同的冷破。
这就是因为双道打浆果胶回收率高缘故。
七、生产的连续性、均衡性及是否满负荷生产。
这一点决定了从开始到最后出产品循环受热时间,这对热破产品影响很明显。
八、套管式杀菌且对粘度有较大降低。
因为高温度(106℃左右)会使酱体中的纤维素切断变短而降低粘性。
九、原料成熟度。
冷破色差很容易达标(2.1以上),而热破必须选用完全成熟的原料并且是自然成熟的才能达到2.0以上的色差,另外还要加强对青黄果地挑选。
一、破碎温度。
粘度达标前提下,必须尽量让色差值提高。
因为客户很重视酱的外观色泽及色差值,又是超过其他指标(如霉菌)。
因为破碎温度对粘度和色差的影响是相反的,所以必须在二者之间寻求一最佳温度设定值。
二、生产的连续性、均衡性及是否有长时间循环不过料现象。
这种情况对色差影响很大,压量生产或设备故障物料长时间循环,必须尽量防止。
三、有无破碎保险真空装置。
理论上讲破碎后脱气可防止各种褐变可以提高色差。
另外,粘度、色差还有一重要的一点事稳定性问题,除以上因素外还有原料品种不一,成熟度不均匀,热破温度波动等因素影响,同时要加强操作,严禁频繁调动热破温度设定值。
只有这样才能产出国际一流热破酱(粘度3-5,色差2.1以上)。
破碎温度统计破碎温度:用0.6mm筛网、750-1000rpm精制机转速,破碎温度65-72℃,设定68℃。
原料过孰70℃,原料过青72℃,粘度8.5左右;新线冷破:用1.2mm/0.6mm或1.5mm/0.6mm筛网、1000/950rpm精制机转速,破碎温度60℃-64℃,设定60℃。
原料过孰62℃,原料过青64℃,粘度8.5左右;原料过熟(果胶物质中,非粘性的果胶酸比重增大),粘度下降,只有通过降低果胶酶活性,保留更多果胶。
同时物料中果胶与纤维素分离更完全,汁中果胶及纤维素增多,从而保证粘度,这就是原料过熟时升温控制粘度的机理。
原料过青,较硬不易打烂取汁,汁中所得粘性果胶较小,果胶物质多以原果胶状态与纤维来结合存在于皮渣中。
因此原料较青,粘度低,只有通过升温进一步软化物料,促使原果胶与纤维素分离从而得到更多的果胶物质,保证粘度。
这就是原料过青升温控制粘度的机理。
但此时会遇到这种现象:粘度保证了,控制住了粘度降低的趋势,但化验室测浓度时,遇到了问题:纱布过滤取汁测浓度困难,并且看起来像温破,但粘度值却合适。
这是因为酱体中原果胶比重增大,其持水性较果胶强,因此测浓度时挤汁困难,此时可以通过降低温度加以解决,但要保证粘度值符合标准。
用0.8mm筛网、900-1050rpm精制机转速,破碎温度84℃-94℃,设定88℃-90℃,使用完全成熟甚至过熟的原料,粘度4.5左右;热破:用1.5mm/0.8mm筛网、1000/950rpm精制机转速,破碎温度90℃-94℃,设定92℃。
使用完全成熟甚至过熟的原料,粘度5.0左右,色差2.2-2.1较老线低。
做热破必须用完全成熟甚至过熟原料,这样才能保证粘度、色差同时合格,并且此时可防止做冷破霉菌超标。
今年新线停机前几天,冷破霉菌超标严重(70%),改为热破后,由于原料过青,粘度、色差均不合格,因此热破只能在原料过熟时生产。
霉菌高8%并非冷破浓度高的缘故,而是由于以下原因:霉菌致死温度(湿热条件)为77℃,低于此温度它将繁殖(条件合适时半小时就繁殖一倍)。
而冷破温度一般不能直接将其直接杀死。
因此冷破物料中的霉菌在三效(48℃)、二效(60℃左右),甚至一效(<77℃)均在繁殖,只是速度较正常时慢,但一直在增值。
而热破不同,热破温度直接将霉菌杀死,在后面管路中不会繁殖,因此这就造成相同的原料同时加工CB较HB霉菌平均值要高8%。
30%-32%HB皮籽酱。
用2.0/1.5筛网,1000/950rpm,热破温度96℃,5.0左右粘度(120%Brix 测),色差很低(小于2.0)。
筛网孔径增大,汁中果胶物质,纤维素等粘性物质增多,酱粘度增大,但用1.5mm、2.0mm (末道),并且较低热破温度生产高粘度、高色差热破皮籽酱,但要看客户要求。
新、老线生产热破适合性比较老线自95年以来生产冷破,不但达产能力高而且质量好。
热破也同样能生产粘度3-5.0,色差大于2.1的国际一流热破酱,并且柱塞泵负荷也够,压力也不太高(1#120-140bar,2#110-130bar),蒸发效率也可以。
新线99生产期生产过两次热破,但质量不理想,主要表现在:粘度低、色差低。
破碎温度设定92℃,粘度只能达到4.6-5.0,但色差较低<2.0,在这一点上远不如老线。
做皮籽酱时,破碎温度96℃,2.0/1.5,1000/950rpm,粘度仅5.0(12.0%Bx测,若用常规测为4.6),色差1.9左右。
这当然有原料成熟度不够的原因,但有一点可以肯定,由于新线工艺管路较长,原料从进选台到灌装出成品需4h,物料循环受热时间过长导致粘度降损较大。
老线工艺管线短仅用2h出成品粘度降损较小,因此新线生产国际一流热破酱较老线困难的多,因此从设备到产品的合适性比较,老线生产热破合适新线生产冷破合适,从而发挥各自优点长处,做到最佳组合,要使新线生产优质热破,可以从以下两方面解决:1使用完全成熟的原料2破碎系统增加真空脱气装置:套管式杀菌与蒸汽直接注入式杀菌对粘度影响程度比较目前。
番茄酱生产设备杀菌器杀菌方式有两种。
一是套管式杀菌它是最常见的杀菌方式。
包括罗西.卡泰利,小罗西、曼再尼、扎可米、芬扣、阿尔泰克几个公司的杀菌器都采用套管式热交换杀菌原理。
其原理是通过导流器作用来回旋转翻滚的酱体与外来夹套理的过热水进行交换达到杀菌的目的。
此过程酱体在杀菌段、保温段整个受热时间约5-7分钟,然后在冷却段冷却约10min,其特点是温度高(106℃),压力大(HB130bar左右CB90bar左右),受热时间长。
另一种是蒸汽直接注入酱体式杀菌方式,目前知道的有FMC杀菌器,其原理是120℃-140℃蒸汽在几秒钟内使酱体温度迅速升至杀菌温度(160℃),酱体在杀菌器内翻转混和彻底杀透。
然后无菌保温、闪蒸冷却。
其特点是升温快,受热时间段,压力小5bar。
后者由于其先进的原理及升温快、受热时间短,压力小的特点,它对酱体质量影响很小,粘度降损及色差降低较前者小的多。
有统计数据,老线成品粘度与半成品粘度相差0.8,新线1.0.这说明常规杀菌方式明显降低粘度。
粘度到一点数值,再上升将不容易。
另外柱塞泵负荷及压力也使粘度受限。
经验表明:老线最粘热破3.0新线只有4.0,色差还受影响。
原因有两点:1高温、酸性条件下粘性果胶物质水解,粘度降低;2高压且来回翻转使纤维素剪断变短,使酱体粘度降低。