试压试漏方案1
工业管道压力试验及泄漏性试验方案含试压曲线及试验记录表式

工业管道压力试验及泄漏性试脸方案编制:×××审核:XXX批准:×××XX特种设备安装有限公司二。
二三年二月一日压力试验(含泄漏性试验)方案1目的通过对压力管道的压力试验,校核管道的强度和检查管道的密封性。
通过泄漏性试验是为了检查管道的致密性以验证管道设备、阀门、元件的严密性,特别是发现微消穿孔性缺陷,从而对压力管道的施工进行质量控制。
2编制依据(1)设计文件及图纸。
(2)GB50235-2010工业金属管道工程施工规范。
(3)GB/T20801-2023压力管道规范-工业管道。
3范围本施工方案适应于本次氨制冷压力管道安装工程(规格:Φ159×6,长度588米)。
4工作职责4.1本管道的压力试验和泄漏性试验的质量控制由检验责任人控制。
4.2试验方案由技术人员编制,检验责任人审核,质保师批准。
4.3项目施工队进行操作记录,质检员检查,检验责任人和甲方(业主)共同验证,压力试验现场应向监督检验人员约请现场确认压力试验过程及试验结果确认。
5试验准备5.1材料要求(1)系统压力试验和泄漏性试验所使用的施工材料,如无缝钢管、高压橡胶软管、阀门钢板等必须有质量证明书,其质量不得低于国家现行标准的规定,并应按照标准进行外观检验合格。
n1,其(2)试验用的压力表必须检定或校准合格,其精度等级不低于1.6,表盘直径不小于IOOm量程为0~4.0MPa,压力表不少于2块,应分别安装在试验管道(段)的两端,试验用的温度计读数分格不得大于1℃,并检定或校准合格,安装位置应避免阳光曝晒。
5.2主要机具(1)常用设备:氢弧焊机、电焊机、氮气瓶等。
(2)常用工具:角向磨光机、氧气乙烘焊割炬、液压扳手、无齿锯、扳手等常用具。
6.3试验条件(1)压力(泄漏性)试验方案已经过批准。
(2)已经过安全交底和技术交底。
4试验程序6压力(气压)试验6.1 压力试验值的确定根据设计文件的要求,结合施工验收标准GB50235-2010等相关标准。
打压试漏方案
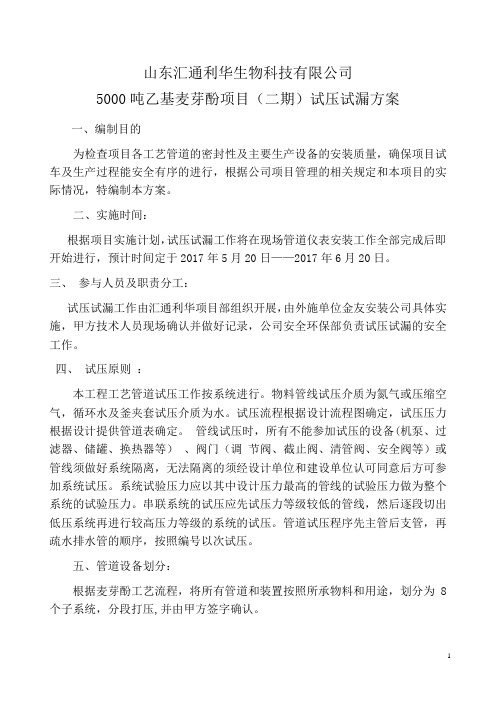
山东汇通利华生物科技有限公司5000吨乙基麦芽酚项目(二期)试压试漏方案一、编制目的为检查项目各工艺管道的密封性及主要生产设备的安装质量,确保项目试车及生产过程能安全有序的进行,根据公司项目管理的相关规定和本项目的实际情况,特编制本方案。
二、实施时间:根据项目实施计划,试压试漏工作将在现场管道仪表安装工作全部完成后即开始进行,预计时间定于2017年5月20日——2017年6月20日。
三、参与人员及职责分工:试压试漏工作由汇通利华项目部组织开展,由外施单位金友安装公司具体实施,甲方技术人员现场确认并做好记录,公司安全环保部负责试压试漏的安全工作。
四、试压原则:本工程工艺管道试压工作按系统进行。
物料管线试压介质为氮气或压缩空气,循环水及釜夹套试压介质为水。
试压流程根据设计流程图确定,试压压力根据设计提供管道表确定。
管线试压时,所有不能参加试压的设备(机泵、过滤器、储罐、换热器等)、阀门(调节阀、截止阀、清管阀、安全阀等)或管线须做好系统隔离,无法隔离的须经设计单位和建设单位认可同意后方可参加系统试压。
系统试验压力应以其中设计压力最高的管线的试验压力做为整个系统的试验压力。
串联系统的试压应先试压力等级较低的管线,然后逐段切出低压系统再进行较高压力等级的系统的试压。
管道试压程序先主管后支管,再疏水排水管的顺序,按照编号以次试压。
五、管道设备划分:根据麦芽酚工艺流程,将所有管道和装置按照所承物料和用途,划分为8个子系统,分段打压,并由甲方签字确认。
5.1罐区外管廊系统:包括管廊主管道(原料、蒸汽、污水、循环水及其他公用工程管道),车间内支管,调节阀组,进釜分管。
5.2格氏系统:包括格氏工段所属的反应釜、受槽、冷凝器、相互连接管道、调节阀组、气液分离器,接收罐(包括计量罐),打料泵、塔类等。
5.3氯化系统:包括氯化工段所属的反应釜、受槽、冷凝器、相互连接管道、调节阀组、气液分离器,接收罐(包括计量罐),打料泵、塔类等。
炼铁高炉打压试漏方案
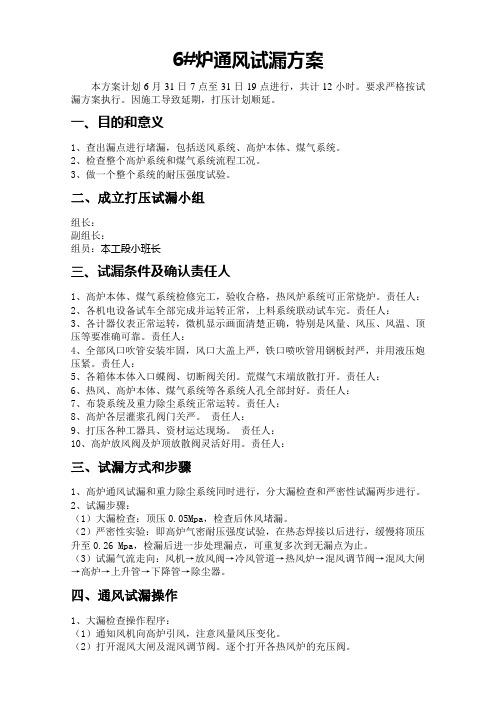
6#炉通风试漏方案本方案计划6月31日7点至31日19点进行,共计12小时。
要求严格按试漏方案执行。
因施工导致延期,打压计划顺延。
一、目的和意义1、查出漏点进行堵漏,包括送风系统、高炉本体、煤气系统。
2、检查整个高炉系统和煤气系统流程工况。
3、做一个整个系统的耐压强度试验。
二、成立打压试漏小组组长:副组长:组员:本工段小班长三、试漏条件及确认责任人1、高炉本体、煤气系统检修完工,验收合格,热风炉系统可正常烧炉。
责任人:2、各机电设备试车全部完成并运转正常,上料系统联动试车完。
责任人:3、各计器仪表正常运转,微机显示画面清楚正确,特别是风量、风压、风温、顶压等要准确可靠。
责任人:4、全部风口吹管安装牢固,风口大盖上严,铁口喷吹管用钢板封严,并用液压炮压紧。
责任人:5、各箱体本体入口蝶阀、切断阀关闭。
荒煤气末端放散打开。
责任人:6、热风、高炉本体、煤气系统等各系统人孔全部封好。
责任人:7、布袋系统及重力除尘系统正常运转。
责任人:8、高炉各层灌浆孔阀门关严。
责任人:9、打压各种工器具、资材运达现场。
责任人:10、高炉放风阀及炉顶放散阀灵活好用。
责任人:三、试漏方式和步骤1、高炉通风试漏和重力除尘系统同时进行,分大漏检查和严密性试漏两步进行。
2、试漏步骤:(1)大漏检查:顶压0.05Mpa,检查后休风堵漏。
(2)严密性实验:即高炉气密耐压强度试验,在热态焊接以后进行,缓慢将顶压升至0.26 Mpa,检漏后进一步处理漏点,可重复多次到无漏点为止。
(3)试漏气流走向:风机→放风阀→冷风管道→热风炉→混风调节阀→混风大闸→高炉→上升管→下降管→除尘器。
四、通风试漏操作1、大漏检查操作程序:(1)通知风机向高炉引风,注意风量风压变化。
(2)打开混风大闸及混风调节阀。
逐个打开各热风炉的充压阀。
(3)缓慢关放风阀加风,将顶压加到0.05Mpa为止。
(4)风压、顶压稳定后,通知检漏人员开始检漏,用目视、手感、刷肥皂水等方法检漏。
管道试压专项方案

管道试压专项方案管道试压是指在管道系统安装完毕并且通过水、气、氮或其他介质进行密封后,检测管道系统的密封性能,以确保其安全运行。
管道试压专项方案是管道试压工作的详细操作指导,包括试压计划、安全措施、试压工艺等内容。
以下是一份关于管道试压专项方案的参考:一、试压计划1.试压目的:(1)检测管道系统是否存在漏气、漏水等问题,确保系统的密封性能;(2)验证管道系统的耐压能力,确保系统能够承受正常工作压力;(3)排除施工过程中可能引入的杂质,确保管道系统的清洁度。
2.试压对象:(1)管道系统的全部或部分,包括主干管道、支线管道、设备和配件等;(2)试压的范围、区段和试验压力根据实际情况进行确定。
3.试压压力:(1)试压压力应根据设计要求确定,一般为1.25倍或1.5倍的设计工作压力;(2)试压时应逐渐增加压力,每次增加0.1倍试验压力,每次保持不少于10分钟;(3)保持试压压力持续时间应根据试验要求进行确定。
4.试压介质:(1)水:适用于一般管道系统;(2)气体:适用于防结露、防冻等特殊要求的管道系统;(3)氮气:适用于高纯度气体管道系统。
二、安全措施1.试压前的准备工作:(1)确保试压设备的可靠性和准确性,校准试压仪表,并确保试压仪表与试压介质相容;(2)检查管道系统的密封性能,确认未存在明显漏水、漏气的情况;(3)清理管道系统,将可能引起堵塞和损坏的杂质、油污等清理干净;(4)确保试压区域的安全,设置安全警示标志,并保证无人员进入试压区域。
2.试压期间的安全措施:(1)试压过程应有专人负责,负责监测试压压力和试压时间;(2)应定期检查试压设备,确保设备正常工作;(3)在试压期间应保持管道系统的稳定,防止因管道晃动、温度变化等引起试压失败;(4)试压仪表应放置在安全区域内,保证工作人员的安全。
三、试压工艺1.试压步骤:(1)确定试压范围和试验压力;(2)准备试验介质,清理管道系统;(3)设置试压设备,校准试压仪表;(4)逐渐增加试压压力,每次保持不少于10分钟;(5)保持试压压力一段时间,观察有无压力下降;(6)释放试压介质,恢复管道系统原状。
开车前设备试压试漏记录

4、整个作业过程由车间负责人负责,岗位操作工实施,机修、安全人员现场监护。
时间
系统
试压试漏介质、方法、流程全过程及存在问题处理
操作人复核人验ຫໍສະໝຸດ 结论:车间负责人: 验收人:
年 月 日
开车前设备试压试漏记录
试压试漏工段
五车间 工段
试压试漏设备
2,6-MEA、酰氯、二甲苯、浓硫酸、盐酸计量罐、酰化釜、产气釜、冷凝器、缓冲罐及管道
试压试漏人员
试压试漏时间
试压试漏方案(试压试漏系统、使用介质、流程顺序及具体要求):
1、试压试漏前对设备进行外观检查,有无明显缺陷。
2、使用介质:水、冷冻盐水。流程顺序:①2,6-MEA、酰氯、二甲苯计量罐→酰化釜。②浓硫酸、盐酸计量罐→缓冲罐→产气釜。 冷凝器。 各夹套加热、冷却系统
给水管道试压专项方案

给水管道试压专项方案水管道试压是为了验证水管道系统的密封性和承受压力的能力而进行的一项测试。
下面是一份水管道试压专项方案,包括试压前准备、试压操作、试压结果验证等步骤。
一、试压前准备1.确定试压的区段:根据工程设计和施工图纸,确定需要进行试压的水管道区段。
2.准备试压试验设备:包括试压泵、压力表、连接管件等。
确保设备的完好,并进行必要的检测和校准。
3.清洁管道:清理管道内的沉淀物、杂物和积水等,确保管道内部的清洁。
4.检查管道连接件:检查管道连接件的安装是否牢固,无漏水和松动现象。
5.安全措施:制定完善的安全措施,并提供必要的个人防护装备。
二、试压操作1.连接试压设备:将试压泵与要试压的水管道区段连接起来。
确保连接件紧固可靠,无漏水现象。
2.设定试压压力:根据设计要求和施工标准,设定试压压力。
通常情况下,试压压力应为最大使用压力的1.5倍。
3.试压过程控制:按照试压压力逐步增加的原则,控制试压泵的水流量和压力。
在每次增压之后,保持试压压力稳定一段时间,并观察管道是否有漏水、渗水和松动等现象。
4.试压时间:根据施工规范和试压要求,确定试压时间。
通常情况下,试压时间为30分钟至1小时。
5.试压结束:试压时间结束后,观察管道是否有明显的漏水、渗水和变形等现象。
确认试压结果后,停止试压泵的工作,释放管道内的压力。
三、试压结果验证1.检查漏水点:对试压过程中出现的漏水点进行记录,并进行修复。
确保所有的漏水点完全消除。
2.校验压力:使用压力表对管道系统进行压力校验,验证管道是否能够保持稳定的工作压力。
3.提交试压报告:整理试压数据和试压过程中的记录,并编制试压报告。
报告中应包括试压结果、漏水点修复情况、压力校验结果等信息。
4.完工验收:提交试压报告后,由相关部门进行水管道系统的完工验收。
确认系统能够正常工作,并符合设计要求。
以上是一份水管道试压专项方案的基本步骤和要点,具体操作应根据工程实际情况和相关标准进行调整和完善。
vcm试压试漏方案

vcm试压试漏方案vc转化试压、试漏方案一.注意事项1.对被试压的设备、管道要反复检查流程是否正确,特别是生产系统与其它系统是否采取可靠隔离措施。
2.带压设备、管道升压、降压都应缓慢进行。
3.在检查受压设备管道时,法兰、法兰盖的侧面和对面都不能站人。
4.登高检查时,应系好安全带,防止高空坠落。
试压过程中发现泄漏,不得带压补焊或修理。
二.1.自HCl总管到预热器进口阀充气源,压力至45—50Kpa。
2.自C2H2总管到混合器乙炔总阀前充气源,压力至55—60Kpa。
3.自预热器到合成气出口管充气源,压力至35—40Kpa。
4.合成气冷却器到碱洗塔充气源,压力至20—25Kpa。
(每段充气时,逐步提升压力,不能超压,防止损坏设备,用肥皂水试漏,每段保压至少30min,压力不降为合格。
)三.触媒抽空自转化器抽空阀到废气缓冲罐充气源,压力至0.2—0.3Mpa,保压30min—1h,压力不降为合格。
四.盐酸脱析1. 打开脱吸塔去浓酸预热器、稀酸冷却器物料阀。
2. 开启酸泵,向脱析塔打酸,直至回流稀盐酸槽,观察是否有漏点。
五.热水系统1. 转化器热水自循环,自热水加水阀处接气源,压力至0.2—0.3Mpa,保压30min—1h,不下降为合格。
2. 向热水罐加水,启泵打循环,加水循环憋压0.25Mpa,观察转化器、预热器是否有渗漏。
压缩精馏试压、试漏方案一.试压前的准备及注意事项1.施工单位试压前进行自检工作,自检合格报监理申请三查四定。
自检内容包括:填报资料、螺栓、垫片、紧固件、盲板、支吊架、基础、管道、焊缝、仪表是否合格。
2.管线检查包括仪表、阀门、垫片、螺母、焊口、管支架、管托、弹簧、支吊架等检查。
每根试压管道需进行三次检查,检查顺序:先总管,后支管。
并用三种颜色标识检查结果,白色为合格,红色不合格,黄色为整改后合格。
3.检查流程是否有误,管件的材质、压力等级、阀门的方向是否有误。
4.焊缝及其他检查部位不得涂漆或加绝热层,不锈钢管焊缝必须酸洗完毕。
容器中间槽试漏方案
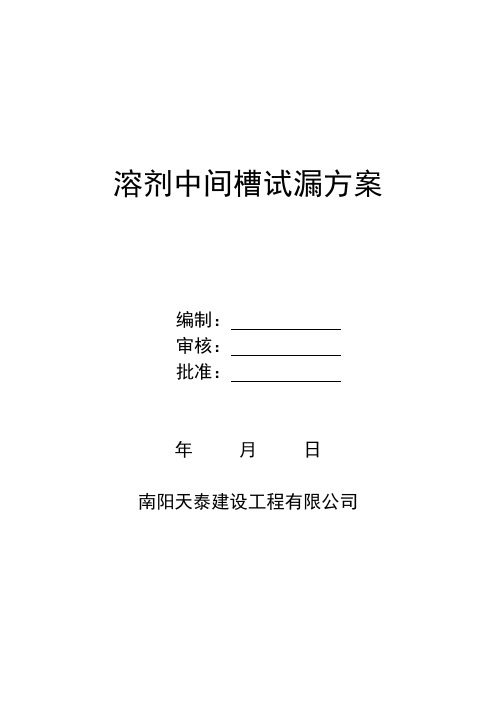
溶剂中间槽试漏方案编制:审核:批准:年月日南阳天泰建设工程有限公司一、试压试漏的目的:为查明设备的强度和严密度保障设备的安全运行。
二、试压试漏方案的编制依据及标准本次试验方案及检验标准依据,《钢制焊接常压容器》NB/OT47003.1-2009的标准编制执行三、试压试漏的准备工作①容器按照施工图纸要求,已完成全部施工,符合设计要求和标准的有关规定②焊接工作已全部完工,并检验合格③与容器相关联的设备、仪表、安全阀等已隔离拆除。
并检确认。
④所有的人孔、管线、阀门已全部关闭或隔离并检查确认。
⑤试验用的管道、阀门、水箱等,已安装完毕,并检查确认,附合试验要求。
⑥以清洁水作试验介质,要求高点放空,低点放水。
检查放空阀、放水阀设置是否符合要求。
⑦试压试漏现场环境打扫干净。
⑧参加人员经过技术培训并合格。
⑨试验前与甲方代表对将试验容器进行全面检查,合格后进行试验。
四、试压试漏的质量标准1.注水试验,容器应无明显外形变化2.注水试验后容器应无泄漏3.容器注水完成后,保持24小时无泄漏。
五、实验方法与步骤1.将外部供水管连接至容器进水口2.打开容器上部高点放空阀3.待放空阀出水后,先关闭进水阀,然后关闭放空阀。
4.在进水过程中,随时观察容器外观变化,及有无泄漏,如有任何一种情况发生,应立即停止进水,终止试验。
并及时上报。
5.进水完成后,应保持24小时无泄漏、无沉降、外观无明显变化,经检验确认是否合格。
5.试验完成后,打开上端高点放空阀,然后缓慢打开低点放水阀门排水。
6.待容器内清洁水排放完毕后,拆除试验装置,恢复容器与生产装置的连接,连接应符合生产单位要求。
7.经检查试验,容器符合《钢制焊接常压容器》要求、施工图纸及甲方要求后签订设备接收单,完成容器制作,试压试漏工作。
- 1、下载文档前请自行甄别文档内容的完整性,平台不提供额外的编辑、内容补充、找答案等附加服务。
- 2、"仅部分预览"的文档,不可在线预览部分如存在完整性等问题,可反馈申请退款(可完整预览的文档不适用该条件!)。
- 3、如文档侵犯您的权益,请联系客服反馈,我们会尽快为您处理(人工客服工作时间:9:00-18:30)。
神华蒙西变压吸附氢提纯装置
设备及管道
试漏、试压方案
天一科技股份有限公司变压吸附气体分离工程研究所
中国.成都
2012.06
装置内设备、管道试压、试漏
一、目的
试压、试漏是一项重要工作,必须严格认真完成。
易燃、易爆、有毒介质的泄露将危害工厂的安全生产和人员的生命安全。
二、试压、试漏前应具备的条件
1、试验范围内管道安装工程除涂漆、保温保冷外,已按设计图纸全部完成,安装质量符合有关规定。
2、焊缝和其它待试验部分尚未涂漆和保温保冷。
3、试验用压力表已经校验,其精度不得低于1.5级,表的满刻度值应为被测最大压力的1.5~2.0倍,压力表不得少于2块。
4、各压力等级的设备和管道连接完毕:压缩空气(必须是无油干燥的压缩空气或氮气)试压,至设计压力2.6MPa的1.15倍,工艺水和冷却水管道等地下管道液压试验0.9MPa;蒸汽管道1.8倍。
5、待测管道与无关系统已用盲板或采用其它隔开。
6、待测管道上的安全阀、仪表元件等已经拆下或加以隔离。
三、试压、试漏前应准备的工具
准备好试压、试漏所用的无油干燥压缩空气或氮气,以及准备肥皂水、刷子、洗耳球等气密检查工具。
四、试压、试漏的方法
由于装置采用气动程控阀,为了保护程控阀内部件,不建议用水压进行试压,根据GB/T 19773-2005:
气压试验前应先预试验0.2MPa检查合格。
试验时应缓慢升压,升压速度0.2MPa/分,将压力升至试验压力的1/3时,用肥皂水涂抹检查所有的管道连接处、设备密封口、管道焊缝及螺纹接头处。
当压力达50%试验压力时,停下检查无异状或泄漏。
然后按每10%试验压力稳压3分钟,直至试验压力。
稳压10分钟后,将压力降至设计压力保压30分钟,检查无泄露和变形。
即试验合格。
然后将气压试验的所有设备和管道在最高工作压力下进行保压(24h),要求每小时的平均泄漏率≤0.5%。
当装置内所有密封点都严密无泄漏时气密试验完成,关闭所有的程控阀,擦去检查处的溶液和溶液污垢,并用干净的压缩空气将设备、
管道吹干,以免造成吸附剂受潮,设备、管道生锈。
试压检查时,还应有进行如下操作和注意事项:
1、开关前、后压力相等的手动截止阀2~3次,重复检查阀门的阀杆和填料压盖处。
2、开关所有调节阀3~4次,重复检查调节阀的阀杆和填料压盖处。
3、开关前、后压力相等的程控阀5~6次,重复检查阀门的阀杆和填料压盖处,同时检查整个行程所用的时间(应当在规定值范围内)和程控阀的动作是否与时序一致。
4、装置试压、试漏过程中记录好所有气体泄露处。
5、在压力小于等于0.25MPa设备和管路上,发现少量气体泄露允许小心的带压处理,较大的泄露量必须泄压处理。
6、在压力大于等于0.25MPa设备和管路上,发现气体泄露必须泄压处理。
7、程控阀的密封件发现泄露应当小心处理,过分拧紧不仅会损坏密封填料,而且还会影响阀门的正常开关。
8除了脱硫器与解吸气缓冲罐、相连的管线外,其它管线可以按照吸附压力的1.15倍进行试压,此时,低压部分与高压部分的阀门要关闭,以此分界。
待吸附塔压力降至相应罐压力时,再对其试压。
五、安全措施
1、试压、吹扫前,应设置安全警戒区,并有专人看护。
操作人员应进行安全和技术交底。
2、试压、吹扫前有关部门联合检查,确认符合试压条件的工程状况和外部环境后,方可进行试压、吹扫。
3、在试压前及试压过程中,应详细检查被试设备、管道的盲板、法兰盖、压力表的加设情况及试压中的变形等,确实具备升压条件时,方可升高压力。
4、夜间施工时应具备足够的照明。
5、带压设备、管道严禁受到强烈冲撞或气体冲击,升压和降压应缓慢进行。
6、在试验过程中,如发现有泄漏现象时,不得带压紧固螺栓、补焊或修理。
7、在检查受压设备和管道时,法兰、盲板的对面和侧面不得站人。