选矿实验流程
铜矿选矿工艺流程图

铜矿选矿工艺流程图铜矿选矿工艺流程图主要包括原矿破碎、磨矿、浮选、浓缩和提取等环节。
以下是一份典型的铜矿选矿工艺流程图,将详细介绍每个环节的工艺过程。
一、原矿破碎:首先,将铜矿矿石通过挖掘和运输设备送入破碎机进行粗碎。
粗碎后的矿石将通过给料机送入磨机进行进一步破碎。
二、磨矿:破碎后的矿石将进入磨机,通过旋转的磨轮对矿石进行细磨。
磨机采用湿式磨矿的方式,通过水的作用将矿石和砂石进行混合并形成矿浆。
磨机的工作参数包括磨机转速、磨球大小、磨机充填率等,这些参数将根据矿石性质的不同进行调整。
三、浮选:经过细磨的矿浆被送入浮选槽,浮选槽内设置有一系列浮选剂和气泡生成装置。
浮选剂的选择将根据矿石的性质进行调整,一般采用两种浮选剂来增加矿物与气泡的亲附程度。
气泡通过气泡生成装置进入浮选槽,与矿浆中的矿物粒子接触,使粒子表面产生浮力,然后使具有浮力的矿物颗粒浮起。
气泡通过浮选槽底部收集装置收集起来,清除其中的矿石杂质。
四、浓缩:浮选后的矿浆分为浮选泡沫液和浮选尾液。
浮选泡沫液中含有铜矿石,而浮选尾液中含有无价值的矿石杂质。
浮选泡沫液经过浓缩器的处理,将其水分蒸发掉,使其中的铜矿浓缩起来。
浓缩器采用真空蒸发的方式,通过调整压力和温度来控制蒸发过程。
五、提取:浓缩后的铜矿溶液被送入萃取槽中进行提取。
萃取槽内设置有一系列有机溶剂,这些溶剂与溶液中的铜矿发生化学反应,从而将铜离子转移至有机溶剂相。
然后,有机相和水相分离,有机相中的铜离子被还原为铜粉。
铜粉通过加热和过滤处理,使其得到纯净的铜。
以上就是一份典型的铜矿选矿工艺流程图及其详细的工艺过程介绍。
在实际的生产过程中,还会根据具体矿石的性质和要求进行一些细节上的调整和改进。
通过合理的工艺流程和技术手段,可以实现对铜矿的高效选矿,提高铜矿的浓度和纯度,为后续的冶炼和加工提供良好的原料。
铝土矿选矿工艺流程

铝土矿选矿工艺流程铝土矿的选矿主要涉及矿石的破碎、磨矿、分选、选后处理等过程。
接下来,我们详细了解每一个步骤。
一、破碎选矿的第一步是破碎。
铝土矿的硬度较高,需要使用颚式破碎机、圆锥破碎机等设备进行初步破碎。
破碎的目的在于将大块的矿石破碎成小块,以便于后续的磨矿过程。
二、磨矿经过破碎后,矿石被送入磨矿阶段。
磨矿的目的是使矿石中的矿物颗粒达到适合分选的粒度。
通常使用球磨机、棒磨机等设备进行磨矿,以将矿石磨成粉末状。
磨矿过程中需添加水和化学药剂,以促进磨矿效率并方便后续的分选。
三、分选在经过破碎和磨矿后,矿石进入分选阶段。
这一阶段的目标是利用矿物间的物理化学性质差异,将有价值的矿物与脉石矿物分离。
分选的方法包括重力分选、浮选、磁选等。
重力分选:对于比重差异较大的矿物,可以利用不同比重矿物在水中的沉降速度不同来进行分离。
这种方法主要用于铝土矿中的铁矿物的分离。
浮选:这是铝土矿选矿中常用的方法。
主要利用铝土矿与脉石矿物的表面物理化学性质差异,通过添加特定的浮选药剂,使铝土矿颗粒附着在气泡上并浮到水面,从而达到分离的目的。
磁选:对于具有磁性的矿物,可以利用磁场将其从非磁性矿物中分离出来。
这种方法在铝土矿选矿中不常用,但如果矿石中含有磁铁矿物,就需要采用磁选法进行分离。
四、选后处理经过分选后,有价值的矿物得到富集。
此时需要进行脱水、脱泥、浓缩等处理,以提高矿物的品位并方便后续的加工利用。
这一阶段还涉及尾矿的处理和堆放,需要合理规划以减少对环境的影响。
总结:铝土矿的选矿工艺流程包括破碎、磨矿、分选和选后处理等步骤。
每个步骤都至关重要,需精心操作以确保获得高质量的铝土矿产品。
选矿实验流程范文
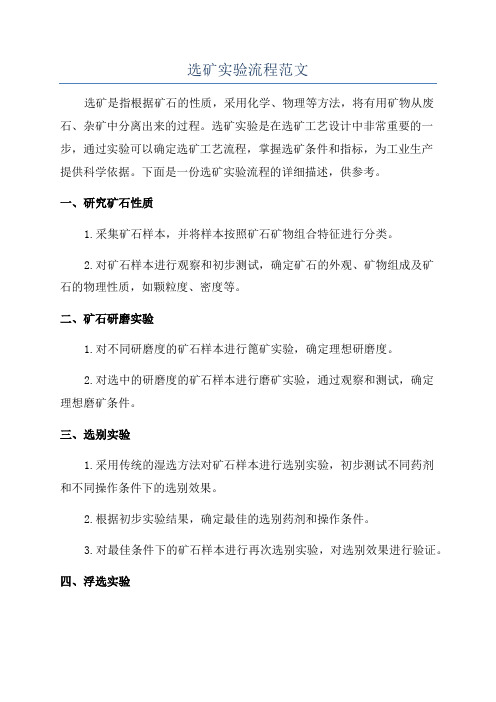
选矿实验流程范文选矿是指根据矿石的性质,采用化学、物理等方法,将有用矿物从废石、杂矿中分离出来的过程。
选矿实验是在选矿工艺设计中非常重要的一步,通过实验可以确定选矿工艺流程,掌握选矿条件和指标,为工业生产提供科学依据。
下面是一份选矿实验流程的详细描述,供参考。
一、研究矿石性质1.采集矿石样本,并将样本按照矿石矿物组合特征进行分类。
2.对矿石样本进行观察和初步测试,确定矿石的外观、矿物组成及矿石的物理性质,如颗粒度、密度等。
二、矿石研磨实验1.对不同研磨度的矿石样本进行篦矿实验,确定理想研磨度。
2.对选中的研磨度的矿石样本进行磨矿实验,通过观察和测试,确定理想磨矿条件。
三、选别实验1.采用传统的湿选方法对矿石样本进行选别实验,初步测试不同药剂和不同操作条件下的选别效果。
2.根据初步实验结果,确定最佳的选别药剂和操作条件。
3.对最佳条件下的矿石样本进行再次选别实验,对选别效果进行验证。
四、浮选实验1.采用不同的浮选药剂、浮选剂用量和浮选条件,对矿石样本进行浮选实验。
2.根据浮选结果,确定最佳浮选药剂、最佳浮选剂用量和浮选条件。
五、干法选别实验1.对矿石样本进行干法选别实验,通过物理方法将杂质和有用矿物分离。
2.根据实验结果,确定干法选别的最佳操作条件。
六、矿石尾矿处理实验1.对选别和浮选过程中产生的尾矿进行处理实验,通过不同处理方法,减少废石、杂质的含量。
2.根据实验结果,确定尾矿处理方法和最佳处理条件。
七、选矿工艺流程确定1.根据前面各项实验的结果,结合矿石性质和选矿指标要求,确定最佳的选矿工艺流程。
2.在确定工艺流程的基础上,进一步调整和优化工艺参数,确保工艺的稳定性和经济性。
3.根据实验结果,制定选矿生产工艺流程和操作规程,为工业生产提供指导。
八、选矿过程及产品分析1.在工业生产过程中,对选前、选中、选后的矿石和尾矿进行实时在线监测和分析。
2.根据分析结果,及时调整工艺参数和工艺流程,保证产品质量和选别效果的稳定性。
锑矿选矿工艺流程
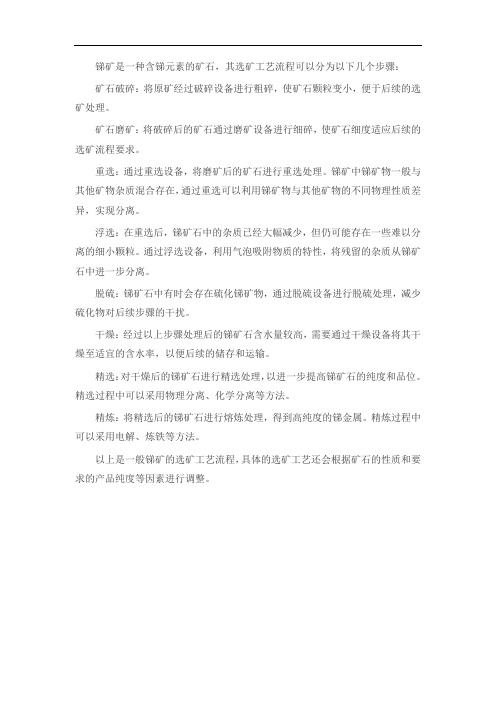
锑矿是一种含锑元素的矿石,其选矿工艺流程可以分为以下几个步骤:
矿石破碎:将原矿经过破碎设备进行粗碎,使矿石颗粒变小,便于后续的选矿处理。
矿石磨矿:将破碎后的矿石通过磨矿设备进行细碎,使矿石细度适应后续的选矿流程要求。
重选:通过重选设备,将磨矿后的矿石进行重选处理。
锑矿中锑矿物一般与其他矿物杂质混合存在,通过重选可以利用锑矿物与其他矿物的不同物理性质差异,实现分离。
浮选:在重选后,锑矿石中的杂质已经大幅减少,但仍可能存在一些难以分离的细小颗粒。
通过浮选设备,利用气泡吸附物质的特性,将残留的杂质从锑矿石中进一步分离。
脱硫:锑矿石中有时会存在硫化锑矿物,通过脱硫设备进行脱硫处理,减少硫化物对后续步骤的干扰。
干燥:经过以上步骤处理后的锑矿石含水量较高,需要通过干燥设备将其干燥至适宜的含水率,以便后续的储存和运输。
精选:对干燥后的锑矿石进行精选处理,以进一步提高锑矿石的纯度和品位。
精选过程中可以采用物理分离、化学分离等方法。
精炼:将精选后的锑矿石进行熔炼处理,得到高纯度的锑金属。
精炼过程中可以采用电解、炼铁等方法。
以上是一般锑矿的选矿工艺流程,具体的选矿工艺还会根据矿石的性质和要求的产品纯度等因素进行调整。
各种选矿法的流程及原理

各种选矿法的流程及原理1. 重力选矿法流程:- 初步矿石破碎:将原矿石破碎成块矿或颗粒状矿石。
- 洗选:利用洗选设备将矿石中的杂质和次要矿物分离出来。
- 重力选矿:利用重力差异,将矿石中的有用矿石分选出来。
原理:根据矿石中有用矿石和废石的密度差异,通过不同的重力分选设备,例如离心机、重力选矿机等,将有用矿石予以分离。
2. 磁选法流程:- 磁力选矿:利用磁性差异将矿石中的有用矿物和废石分离出来。
原理:根据矿石中有用矿物和废石对磁场的不同反应,通过磁选设备,例如磁选机等,利用磁性差异将有用矿物与废石分离。
3. 浮选法流程:- 破碎与磨矿:将原矿石破碎、磨细。
- 药剂处理:加入药剂,处理矿浆,使有用矿物与泡沫一起浮起。
- 浮选分离:通过浮选设备,例如浮选机等,利用泡沫的浮力将有用矿物与废石分离。
原理:通过加入特定的药剂,使有用矿物与气泡结合形成泡沫,利用泡沫的浮力将其分离。
4. 电选法流程:- 尾矿处理:将矿石经过前期破碎、磨细处理,得到尾矿。
- 前选处理:将尾矿经过前选设备,例如电选机等,利用较低电位的特殊电解质和电极将有用矿物分离出来。
- 精选处理:将前选步骤中分离得到的矿物经过精选设备进行进一步处理。
原理:根据矿物在特定电场中的电性差异,通过电解质和电极的运用,将有用矿物与废石分离。
5. 流体力学选矿法流程:- 矿石破碎:将原矿石破碎成适当粒度。
- 砂浆制备:将矿石与水或其他流体制成砂浆。
- 分选:通过分选设备,例如旋流器、水力分选器等,根据矿石颗粒的大小与密度差异,将其分离。
原理:利用流体力学原理,根据矿石颗粒的大小与密度差异,通过流体中的运动分离有用矿物与废石。
铅锌矿选矿工艺流程
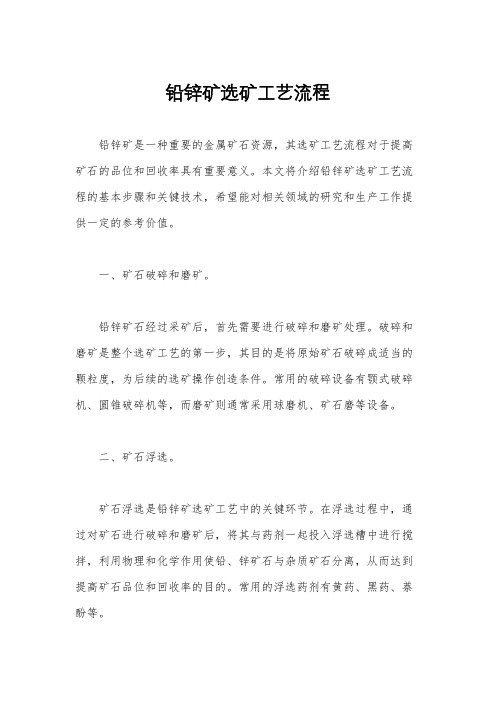
铅锌矿选矿工艺流程铅锌矿是一种重要的金属矿石资源,其选矿工艺流程对于提高矿石的品位和回收率具有重要意义。
本文将介绍铅锌矿选矿工艺流程的基本步骤和关键技术,希望能对相关领域的研究和生产工作提供一定的参考价值。
一、矿石破碎和磨矿。
铅锌矿石经过采矿后,首先需要进行破碎和磨矿处理。
破碎和磨矿是整个选矿工艺的第一步,其目的是将原始矿石破碎成适当的颗粒度,为后续的选矿操作创造条件。
常用的破碎设备有颚式破碎机、圆锥破碎机等,而磨矿则通常采用球磨机、矿石磨等设备。
二、矿石浮选。
矿石浮选是铅锌矿选矿工艺中的关键环节。
在浮选过程中,通过对矿石进行破碎和磨矿后,将其与药剂一起投入浮选槽中进行搅拌,利用物理和化学作用使铅、锌矿石与杂质矿石分离,从而达到提高矿石品位和回收率的目的。
常用的浮选药剂有黄药、黑药、萘酚等。
三、矿石脱泥。
在浮选后,矿石中会残留一定的泥土和杂质,需要进行脱泥处理。
脱泥操作可以采用浮选机、脱泥机等设备,通过对矿石进行洗涤、筛分等操作,去除矿石表面的泥土和杂质,提高矿石的纯度。
四、矿石浸出。
矿石浸出是指将经过浮选和脱泥处理后的矿石进行浸出操作,以进一步提取铅、锌等有用金属。
浸出过程中,通常采用化学浸出法或氰化浸出法,将金属离子从矿石中溶解出来,形成金属盐溶液,再通过电解、水解等方法得到金属。
五、金属精炼。
最后,经过浸出得到的金属盐溶液需要进行精炼,以得到纯净的金属产品。
金属精炼通常包括电解精炼、火法精炼等方法,通过对金属盐溶液进行电解、熔炼等操作,将金属离子还原成纯净的金属,从而得到成品。
总结。
铅锌矿选矿工艺流程是一个复杂的系统工程,涉及到矿石的处理、浮选、脱泥、浸出、精炼等多个环节。
不同的矿石性质和工艺条件将影响选矿工艺流程的具体操作方法,因此在实际生产中需要根据具体情况进行调整和优化。
希望本文所介绍的内容能够为相关领域的研究和生产工作提供一定的帮助,推动铅锌矿选矿工艺的发展和进步。
选矿实验流程
3.选矿方法和流程试验研究
1选矿方法的研究;由于选矿技术的发展,处理一种矿石,可以用多种选矿方法,因此在试验中应根据矿石性质、用户对产品质量的要求和建设条件等因素,有选择地进行选矿方法多方案对比试验,并选定合理的选矿方法;
3磨蚀指数试验;磨矿介质及磨矿机衬板的消耗是选矿厂一项主要消耗指标,因此应测定其耗量指标;
4自磨介质性能试验;拟采用自磨工艺时,应先进行自磨介质试验,依此决定是否需要进行自磨或半自磨的半工亚试验或工业试验;
5在研究碎磨工艺流程时,应根据矿石含泥率和矿泥性质及其对破碎、磨矿、选别、脱水作业的影响程度,考虑是否有必要和有可能进行洗矿,如有必要洗矿,则需进行相应的洗矿和洗矿溢流处理的试验;
5在开路流程试验的基础上,进行闭路流程试验;应注意稳定相应的工艺和控制条件最好采用微型连续试验装置进行试验,试验指标应具有重现性、稳定性、流程的数量质量指标应平衡;
4推荐选矿工艺流程;对选矿方法、工艺流程和选别条件应进行多方案试验,并在重点的对 I 一 2 个方案作对比试验的基础上推荐出选矿工艺流程;推荐的工艺流程应包括合理的磨矿细度、各作业或产品的浓度、品位、部分回收率、总回收率及产出率、工艺条件、新水及回水补加量等内容;
2选别条件试验:
1浮选:应进行磨矿细度、矿浆浓度、矿浆温度、矿浆酸碱度pH、药剂制度、搅拌与浮选时间等试验;有些情况下,还应做回水利用、水质、脱药、脱泥、风压及风量等试验;2磁选:一般应进行磁感应强度、物料入选粒度、处理能力、物料分级与不分级对比试验等;此外,对干式弱磁选还应进行矿石水分对选别指标的影响试验,矿石经洗矿与不经洗矿对选别指标的影响试验;对湿式强磁选应进行矿浆浓度、冲洗水压和水量、告形介质板间隙或
选矿实验方案
选矿实验方案选矿实验是矿石开发过程中的重要环节之一,其目的是通过实验研究找到最佳的选矿工艺流程,提高选矿回收率和矿石品位。
本文将详细介绍选矿实验方案的制定步骤及具体内容。
一、确定实验目的和任务选矿实验的首要任务是确定矿石的物理和化学性质,了解矿石中存在的各种有用和有害成分以及其赋存状态。
同时,还需确定实验的具体目的,如提高矿石品位、降低有害成分含量等。
基于这些目标,选择合适的实验方法和指标。
二、实验方案的制定选矿实验方案的制定包括实验设计、实验流程、实验材料和仪器设备等方面。
1. 实验设计实验设计是选矿实验的核心内容之一。
在实验设计过程中,需要考虑实验的可行性、科学性和可重复性。
常用的实验设计方法有正交试验、单因素试验和多因素试验等。
2. 实验流程实验流程主要包括试样的制备、实验操作过程和实验数据的处理与分析。
在试样制备过程中,需要注意样品的选取、粉碎、混合等工艺参数。
实验操作过程必须准确操作每个环节,确保实验结果的可靠性和准确性。
实验数据的处理与分析是为了从实验结果中找到关键指标和规律,评估不同工艺条件下的选矿效果。
3. 实验材料和仪器设备选矿实验中所需的材料包括原矿样品、试剂和标准物质等。
仪器设备的选择要根据实验需要和实验条件来确定,如磁选机、浮选机、鉴定仪器等。
三、实验方案的实施和结果分析在实施实验过程中,需要严格按照实验方案进行各项操作,并及时记录实验数据。
根据实验结果,进行系统的数据分析,探索选矿过程中存在的问题和潜在的解决方案。
四、实验结论和建议基于实验结果的分析,将得出选矿实验的结论和相应的建议。
结论应准确反映实验数据,建议要具有可操作性和可实施性,帮助实现选矿工艺的优化和矿石回收率的提高。
通过制定合理的选矿实验方案,并严格按照方案进行实施和分析,可以为矿石选矿工艺的优化提供科学依据。
实验方案制定时要充分考虑实际情况,并根据实验目的和任务确定合适的方案内容,以确保实验结果的有效性和可靠性。
选矿工艺流程
选矿工艺流程选矿工艺流程是矿石开采和提取有用矿物的关键步骤,通过一系列物理和化学方法,将原料中的有用矿物分离出来,从而实现资源的有效利用。
下面就以铁矿石选矿为例,阐述其基本流程。
首先,铁矿石开采需要进行爆破,将矿石从地下岩层中分离出来。
然后,矿石会通过输送设备送往破碎机进行粗碎,将大块矿石破碎成较小的颗粒。
接下来,矿石会通过振动筛等设备进行筛分,将破碎后的矿石颗粒按照大小进行分级。
其中,过筛的矿石颗粒会被分到不同的料仓中,以便后续处理。
然后,矿石会进一步通过磁选机进行磁选,将其中的含铁矿物分离出来。
磁选机通过电磁力将带磁性的矿石颗粒吸附在磁性辊上,而不带磁性的矿石颗粒则会被排除。
接下来,矿石会经过震荡筛进行再次筛分,将经过磁选的矿石分离开来。
其中,带有磁性的矿石颗粒会被排除,而不带磁性的矿石颗粒则会继续进行处理。
随后,铁矿石会进行磨矿处理,将颗粒磨碎成更加细小的粉末。
磨矿过程通常采用湿式磨矿方法,即在磨矿设备中加入水来进行磨碎和分类。
磨矿后的铁矿石粉末会通过造粒机进行浓缩,将粉末压制成颗粒状的矿石矿粉。
然后,矿粉会通过湿式选粉机进行浮选,将其中的铁矿石矿粉与杂质进行分离。
最后,经过浮选的铁矿石会通过干燥机和热风炉进行烘干,将其中的水分蒸发掉,使铁矿石达到所需的干燥度。
然后,干燥后的铁矿石会通过烧结机进行烧结,使粉末颗粒互相结合,形成烧结矿。
综上所述,铁矿石选矿工艺流程主要包括爆破、粗碎、筛分、磁选、磨矿、浓缩、浮选、烘干和烧结等步骤。
通过这些步骤,铁矿石中的含铁矿物可以得到分离和浓缩,从而实现矿石的提取和资源的有效利用。
当然,不同的矿石类型和矿石性质,在选矿工艺流程中可能会有些许差异。
铜选矿工艺流程
铜选矿工艺流程铜是一种重要的金属资源,广泛应用于建筑、电子、通信和工业制造等领域。
铜矿是铜的主要矿石,其含铜量较高,但通常还伴随着其他杂质和矿物。
为了从铜矿中提取出高纯度的铜,需要经过一系列的选矿工艺流程。
本文将介绍铜选矿工艺流程的主要步骤和关键技术。
1. 破碎和磨矿。
铜矿首先需要经过破碎和磨矿的处理,将矿石从原始的大块状破碎成较小的颗粒。
通常采用颚式破碎机、圆锥破碎机和砂磨机等设备进行破碎和磨矿操作。
破碎和磨矿的目的是将矿石颗粒大小降低,以便后续的选矿操作。
2. 浮选。
浮选是铜选矿中最常用的工艺流程之一。
在浮选过程中,通过向矿浆中添加各种药剂,使铜矿和其他杂质矿物发生不同程度的浮选,从而实现铜矿和杂质的分离。
浮选药剂通常包括捕收剂、起泡剂和调整剂等。
浮选过程中,通过气泡的作用,使铜矿颗粒附着在气泡上浮到矿浆表面,而杂质矿物则沉入矿浆底部。
3. 磁选。
磁选是另一种常用的铜选矿工艺流程。
通过磁选设备,如磁选机和高梯度磁选机,可以将含铜矿物和磁性杂质矿物进行有效分离。
磁选过程中,通过磁场的作用,使含铜矿物和磁性杂质矿物产生不同的磁性响应,从而实现它们的分离。
4. 重选。
重选是利用矿石颗粒在重介质中的沉降速度不同而进行的选矿操作。
在重选过程中,通过向矿浆中加入重介质,如重液或重浆,使含铜矿石和杂质矿石产生不同的沉降速度,从而实现它们的分离。
重选工艺通常用于处理颗粒粒度较细的铜矿。
5. 焙烧和冶炼。
经过浮选、磁选和重选等工艺之后,得到的铜精矿需要进行焙烧和冶炼,以提取出纯度较高的铜金属。
在焙烧过程中,铜精矿被加热至一定温度,使其中的硫化物和其他杂质燃尽或氧化。
随后,经过冶炼,将焙烧后的铜精矿转化为铜金属。
以上就是铜选矿工艺流程的主要步骤和关键技术。
通过破碎和磨矿、浮选、磁选、重选、焙烧和冶炼等工艺操作,可以从铜矿中提取出高纯度的铜金属,满足工业生产和市场需求。
铜选矿工艺流程的不断改进和创新,对于提高铜资源的利用率和保护环境具有重要意义。
- 1、下载文档前请自行甄别文档内容的完整性,平台不提供额外的编辑、内容补充、找答案等附加服务。
- 2、"仅部分预览"的文档,不可在线预览部分如存在完整性等问题,可反馈申请退款(可完整预览的文档不适用该条件!)。
- 3、如文档侵犯您的权益,请联系客服反馈,我们会尽快为您处理(人工客服工作时间:9:00-18:30)。
选矿试验的要求选矿试验资料是选矿工艺设计的主要依据。
选矿试验成果不仅对选矿设计的工艺流程、设备选型、产品方案、技术经济指标等的合理确定有着直接影响,而且也是选矿厂投产后能否顺利达到设计指标和获得经济效益的基础。
因此,为设计提供依据的选矿试验,必须由专门的试验研究单位承担。
选矿试验报告应按有关规定审查批准后才能作为设计依据。
在选矿试验进行之前,选矿工艺设计者应对矿床资源特征、矿石类型和品级、矿石特征和工艺性质、以及可选性试验等资料充分了解,结合开采方案,向试验单位提出试验要求,在“要求”中,一般不必详述试验单位通常都应做到的内容,而应着重提出需要试验单位解决的特殊内容和主要问题。
一、选矿试验类型的划分选矿试验按研究的目的可分为可选性试验、工艺流程试验和选矿单项技术试验三种,按试验规模可分为试验室试验、半工业试验和工业试验三种。
为便于明确选矿试验要求和叙述的方便,概括上述两种分类,将选矿试验类型划分为可选性试验、试验室小型流程试验、试验室扩大连续试验、半工业试验、工业试验和选矿单项技术试验六种。
(1)可选性试验。
一般由地质勘探部门完成。
在地质普查、初勘和详勘阶段,应循序渐进地提高和加深可选性试验研究深度。
可选性试验着重研究和探索各种类型和品级矿石的性质与可选性差别,基本选矿方法与可能达到的选矿指标,有害杂质剔除的难易,伴生成分综合回收的可能性等。
试验研究的内容和深度应能判定被勘探的矿床矿石的利用在技术上是否可行、经济上是否合理,能为制订工业指标和矿床评价提供依据。
可选性试验是在试验室装置或小型试验设备上进行的,一般只作矿床评价用。
(2)试验室小型流程试验。
试验室小型流程试验是在矿床地质勘探完成之后,可行性研究或初步设计之前进行。
它着重对矿石矿物特征和选矿工艺特性、选矿方法、工艺流程结构、选矿指标、工艺条件及产品(包括某些中间产品)等进行试验研究和分析,并应进行两个以上方案的试验对比。
试验研究的内容和深度。
一般应能满足设计工作中初步制订工艺流程和产品方案、选择主要工艺设备及进行设计方案比较的要求。
由于试验室小型流程试验规模小、试料少、灵活性大、入力物力花费较少,因此允许在较大范围内进行广泛的探索,又因它的试料容易混匀,分批操作条件易于控制,因此是各项试验的最基本试验。
但是,它是在试验室小型非连续(或局部连续)试验设备上进行的,其模拟程度和试验结果的可靠性虽优于可选性试验,但不及试验室扩大连续试验。
(3)试验室扩大连续试验。
试验室扩大连续试验是在小型流程试验完成之后,根据小型流程试验确定的流程,用试验室设备模拟工业生产过程的磨矿、选别乃至脱水作业的连续试验。
它着重考察流程动态平衡条件下(包括中矿返回)的选矿指标和工艺条件。
各试验研究单位连续试验设备的能力很不一致,一般为 40 一 200kg/h。
试验室扩大连续试验比小型流程试验的模拟性较好,可靠性较小型流程试验高些。
(4)半工业试验。
半工业试验是在专门建立的半工业试验厂或车间进行的,试验可以是全流程的连续,也可以是局部作业的连续或单机的半工业试验。
试验的目的主要是验证试验室试验的工艺流程方案,并取得近似于生产的技术经济指标,为选矿厂设计提供可靠的依据或为进一步做工业试验打下基础。
半工业试验所用的设备为小型工业设备,试验厂的规模尚无明确的规定,一般为 1~5t/h。
(5)工业试验。
工业试验是在专门建立的工业试验厂或利用生产选矿厂的一个系列甚至全厂进行的局部或全流程的试验,由于其设备、流程、技术条件与生产或今后的设计基本相同,故技术经济指标和技术参数比半工业试验更为可靠。
(6)选矿单项技术试验。
选矿单项技术试验包括单项新技术试验和单项常规技术试验,其中单项新技术试验包括新设备、新工艺、新药剂、新材质试验等。
凡采用尚无使用经验的新技术,必须坚持“一切通过试验”的原则,取得技术鉴定资料后,并由设计单位认定是可靠的,方能在设计中采用。
二、选矿试验规模选矿设计对选矿工艺流程试验规模的要求见表 1,对选矿单项技术试验规模的要求见表 2。
表 2选矿设计对选矿单项技术试验规模的要求三、选矿试验内容试验室小型流程试验是选矿工艺流程试验的基本试验,如果该试验尚不能满足设计工作的要求,则视需要进行试验室扩大连续试验、半工业试验或工业试验。
后者都是在前者试验内容的基础上,根据试验的目的和要求提出的验证、补充或增加的试验。
单项选矿技术试验也应先从试验室小型试验开始,逐步扩大试验的规模,各段试验的内容应根据试验目的确定。
在作为设计依据的各类选矿试验进行之前,设计单位向试验单位提出的“试验要求”中,对各类选矿试验内容要求提纲大致如下:(一)试验室小型流程试验1.原矿石性质研究(1)光谱分析。
查明各种元素的大约含量及有无稀散元素和其他可供综合回收的元素。
(2)多元素分析或全分析。
查明矿石中主要组分、伴生有益和有害组分的含量。
必要时还要进行矿浆性质的化学分析,测定可溶性盐类等。
(3)试金分析。
查明金、银和其他贵金属的种类及其含量(含有金、银等贵金属时才进行)。
(4)显微镜鉴定。
查明矿石类型、矿物组成及含量、矿石的结构构造、矿物粒度及嵌布特征和共生关系等。
进行选矿目的矿物挑纯分析。
(5)物相分析。
对矿石主要有用组分及伴生有益及有害组分的赋存状态,即对它们的不同矿物产出形式进行测定。
例如,铜矿石需测定自然铜、原生硫化物、次生硫化物、氧化物及铜的盐类等的相对含量;铁矿石需测定磁铁矿、赤铁矿、菱铁矿、镜铁矿、褐铁矿、黄铁矿、磁黄铁矿、钛铁矿和硅酸铁等的相对含量。
(6)粒度分析。
通过筛析和水析,测定矿石粒度特性和原生矿泥的各粒级含量、金属分布率。
必要时用不同密度的重液,测定各粒级按不同密度部分的产率及金属分布率,为重液分离提供依据。
(7)重波分离。
在钨、锡、铅、锌、铁等矿石和稀有金属矿石中,如有可能使大部分脉石不经细磨即可分离出来时,应进行重液分离试验,为进行重介质预选试验提供依据。
(8)矿石物理机械性质测定。
对矿石的密度、松散密度、安息角、内摩擦角、摩擦系数、硬度、粘度、水分、比磁化系数、导电性、含泥率等进行测定。
(9)其他必要的分析研究内容。
2.碎磨工艺(含洗矿和预选)流程试验研究试验室一般应进行如下的试验和测定工作:(1)功指数测定。
如按邦德公式进行破碎和磨矿设备计算时,应进行破碎和磨矿功指数的测定。
测定的功指数有以下几种:粗、中、细破碎功指数;自磨功指数;棒磨功指数;球磨功指数;以及粗精矿或中矿再磨功指数等。
(2)可磨度测定。
如用容积法计算磨矿设备时,应测定各段磨矿的矿石可磨度。
在进行矿石可磨度试验时,须采取用作对比试验的标准矿样,有色金属矿山选矿厂设计多以杨家杖子钼矿的矿石为标准矿样,化工矿山硫铁矿选矿厂设计以向山硫铁矿矿石为标准矿样,沉积变质磷灰岩以锦屏磷矿矿石为标准矿样,沉积磷块岩和硅钙质型磷矿石当采用多段磨矿时以王集第三层矿矿石为标准矿样,黑色金属矿山选矿厂设计一般以类似磨矿工艺生产选矿厂的原矿作为标准矿样。
鉴于生产矿山开采的矿石性质常有变化,故在采取标准矿样的同时,应测定该矿山选矿厂处理这种矿石当时的磨矿机处理量、技术条件和有关的技术参数。
(3)磨蚀指数试验。
磨矿介质及磨矿机衬板的消耗是选矿厂一项主要消耗指标,因此应测定其耗量指标。
(4)自磨介质性能试验。
拟采用自磨工艺时,应先进行自磨介质试验,依此决定是否需要进行自磨或半自磨的半工亚试验或工业试验。
(5)在研究碎磨工艺流程时,应根据矿石含泥率和矿泥性质及其对破碎、磨矿、选别、脱水作业的影响程度,考虑是否有必要和有可能进行洗矿,如有必要洗矿,则需进行相应的洗矿和洗矿溢流处理的试验。
(6)矿石预选的试验研究。
应根据开采矿石时的废石混入率或磨选作业对原矿品位富集的需要,考虑有无可能在原矿石入磨前进行矿石预选。
如有可能,需进行矿石预选试验,并在磨选工艺流程试验方案中包括有预选矿石的磨选流程试验。
(7)磨矿方法和磨矿流程的试验研究。
常用的磨矿方法,按磨矿介质不同可划分为球磨、棒磨、自磨、半自磨、砾磨等。
应根据矿石性质和特征、上述有关试验测定资料、生产和试验类似经验及其他因素,分析研究各种磨矿方法的可能性和进行扩大试验的必要性,并选择和推荐 1 一 2 个为主的单一或联合的磨矿方法。
在此基础上进行一段磨矿或多段磨矿、多段连续磨矿或阶段磨矿(含粗磨抛尾、中矿和粗精矿再磨等试验)等磨矿流程和磨矿细度的多方案对比试验。
(8)磨矿产物分析。
应对各段磨矿给料和产物(含中矿、粗精矿等)进行筛析和单体解离度的测定。
3.选矿方法和流程试验研究(1)选矿方法的研究。
由于选矿技术的发展,处理一种矿石,可以用多种选矿方法,因此在试验中应根据矿石性质、用户对产品质量的要求和建设条件等因素,有选择地进行选矿方法多方案对比试验,并选定合理的选矿方法。
(2)选别条件试验:1)浮选:应进行磨矿细度、矿浆浓度、矿浆温度、矿浆酸碱度(pH)、药剂制度、搅拌与浮选时间等试验。
有些情况下,还应做回水利用、水质、脱药、脱泥、风压及风量等试验。
2)磁选:一般应进行磁感应强度、物料入选粒度、处理能力、物料分级与不分级对比试验等。
此外,对干式弱磁选还应进行矿石水分对选别指标的影响试验,矿石经洗矿与不经洗矿对选别指标的影响试验;对湿式强磁选应进行矿浆浓度、冲洗水压和水量、告形介质板间隙(或球介质直径、介质充填率)、转速等试验,以及强磁性矿物的聚积和影响试验。
3)焙烧磁选:应进行焙烧气氛、焙烧温度、焙烧时间、燃料种类、用量、挥发成分、物料粒度等条件试验及有关技术参数测定。
4)重选:应进行给矿量、给矿粒度及范围、矿浆浓度(固液比)、冲洗水压和水量、给排料方式和截取位置等试验。
此外,还应根据使用的重选设备的不同,进行相应的工艺参数试验。
5)重介质选矿:应进行给矿量、给矿粒度及范围,重介质悬浮液的密度,加重剂的原料、密度、粒度、加入量、回收措施及消耗量的试验。
此外,还应根据使用的重介质设备的不同,进行相应的工艺参数试验。
6)电选:除应进行选别段数、作业电压、极距及电极位置、转鼓速度、给矿量、粒度、温度、温度等项试验外,还应进行转鼓速度与电压、粒度的关系的试验,给料分级与不分级的对比试验,分矿板位置调整对比试验等。
7)光拣选:先进行洗矿分级,然后在料层为单层矿粒的情况下进行给矿粒度与处理量关系的对比试验。
8)选矿药剂、燃料、介质等主要原材料选用对比试验:应结合不同选矿方法和设备的试验,对其所采用的主要药剂、燃料、介质的种类、性能、规格、耗量、选矿效果等进行比较试验,选择选矿指标好、价格便宜、来源充足、环境污染小或容易治理的品种。
(3)选别流程结构试验研究:1)确定选别段数。
2)探讨精选和扫选作业的合理次数,尽量提高精矿品位和回收率,降低产品杂质含量,富集伴生有益组分或可综合回收组分。