ECRCVD设备镀膜工艺及膜系设计理论
cvd工艺技术

cvd工艺技术CVD(化学气相沉积)工艺技术是一种在半导体和材料科学领域中应用广泛的制备薄膜的技术。
CVD技术通过在气氛中加热化学物质,使其分解并产生反应,最终形成固体薄膜。
在以下的文章中,我将介绍一下CVD工艺技术的原理、应用以及它对于半导体和材料领域的重要性。
首先,我们来了解一下CVD工艺的原理。
CVD工艺是基于化学反应的原理。
在CVD过程中,化学物质被加热并分解为原子或分子,然后在衬底上重新组合形成固体薄膜。
这些化学物质通常是易挥发的有机化合物或无机化合物。
加热源可以是电阻加热、光照或者激光。
通过控制温度、压力和反应气氛的成分,可以调节薄膜的成分、晶格结构以及厚度。
其次,CVD工艺技术在半导体和材料科学领域中有着广泛的应用。
例如,CVD可以用于制备硅薄膜,用于太阳能电池、显示屏和集成电路的制造。
此外,CVD还可以用于制备金属薄膜,用于硬盘驱动器和光学薄膜。
此外,CVD还可以用于制备氮化硅等无机薄膜,用于涂层和保护层。
总的来说,CVD工艺技术提供了一种非常灵活和精确的薄膜制备方法,能够满足不同材料和器件的需求。
最后,CVD工艺技术在半导体和材料科学领域的重要性不可忽视。
制备高质量薄膜是半导体和材料领域中的一个关键步骤。
CVD工艺技术提供了一种控制制备过程的方法,可以实现高度纯净、高度均匀以及良好结晶的薄膜。
这对于提高材料的性能和器件的效率至关重要。
此外,CVD工艺技术还可以实现高度控制的厚度和界面,对于设计和制造复杂的器件非常重要。
总之,CVD工艺技术是一种在半导体和材料领域中应用广泛的制备薄膜的技术。
它基于化学反应的原理,通过控制温度、压力和反应气氛的成分,实现高质量的薄膜制备。
CVD工艺技术在半导体和材料科学领域有着广泛的应用,能够满足不同材料和器件的需求。
它对于提高材料的性能和器件的效率具有重要作用。
因此,CVD工艺技术在半导体和材料科学中扮演着不可忽视的角色。
cvd或pvd镀膜原理
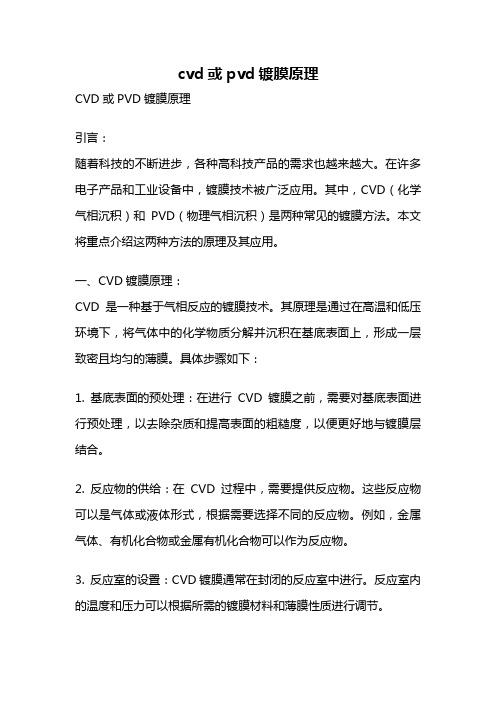
cvd或pvd镀膜原理CVD或PVD镀膜原理引言:随着科技的不断进步,各种高科技产品的需求也越来越大。
在许多电子产品和工业设备中,镀膜技术被广泛应用。
其中,CVD(化学气相沉积)和PVD(物理气相沉积)是两种常见的镀膜方法。
本文将重点介绍这两种方法的原理及其应用。
一、CVD镀膜原理:CVD是一种基于气相反应的镀膜技术。
其原理是通过在高温和低压环境下,将气体中的化学物质分解并沉积在基底表面上,形成一层致密且均匀的薄膜。
具体步骤如下:1. 基底表面的预处理:在进行CVD镀膜之前,需要对基底表面进行预处理,以去除杂质和提高表面的粗糙度,以便更好地与镀膜层结合。
2. 反应物的供给:在CVD过程中,需要提供反应物。
这些反应物可以是气体或液体形式,根据需要选择不同的反应物。
例如,金属气体、有机化合物或金属有机化合物可以作为反应物。
3. 反应室的设置:CVD镀膜通常在封闭的反应室中进行。
反应室内的温度和压力可以根据所需的镀膜材料和薄膜性质进行调节。
4. 反应过程:在反应室内,反应物会在高温下分解,并与基底表面上的活性位点发生反应,生成新的化合物。
这些化合物在基底表面沉积,逐渐形成一层均匀的薄膜。
5. 薄膜性质的调节:通过调节反应室内的温度、压力和反应物的浓度,可以控制薄膜的成分、结构和性质。
这些参数的调节可以实现对薄膜的硬度、抗腐蚀性、电学性能等特性的控制。
6. 后处理:在CVD过程结束后,需要对镀膜进行后处理,以去除残余的反应物和提高薄膜的质量。
这可以通过热处理、溶剂洗涤或化学处理等方法来实现。
二、PVD镀膜原理:PVD是一种基于物理过程的镀膜技术。
其原理是通过蒸发或溅射源,将固体材料转化为气体或离子态,并沉积在基底表面上,形成一层致密且均匀的薄膜。
具体步骤如下:1. 蒸发源或溅射源的选择:PVD镀膜过程需要使用蒸发源或溅射源来提供镀膜材料。
蒸发源可以是电子束蒸发源或电阻加热蒸发源,而溅射源可以是直流或射频溅射源。
ECR_PECVD制备Si_3N_4薄膜沉积工艺的研究

ECR 2PECV D 制备Si 3N 4薄膜沉积工艺的研究Ξ陈俊芳 吴先球 王德秋(华南师范大学物理系,广州 510631)丁振峰 任兆杏(中国科学院等离子体物理研究所,合肥 230031)(1998年8月25日收到)Ξ国家自然科学基金(批准号:69493501)及广东省自然科学基金(批准号:970317)资助的课题. 由偏心静电单探针诊断了电子回旋共振等离子体增强化学汽相沉积(ECR 2PECVD )反应室内等离子体密度的空间分布规律.结果表明在轴向位置Z =50cm 处,直径<12cm 范围内等离子体密度分布非常均匀.分析了等离子体密度径向均匀性对沉积速率均匀性和薄膜厚度均匀性的影响.讨论了沉积制备一定薄膜厚度的Si 3N 4薄膜的工艺重复性.研究了各种沉积工艺参数与Si 3N 4薄膜沉积速率的相互关系.得到了ECR 2PECVD 技术在沉积薄膜时的工艺参数条件.PACC :6855;8115H ;52701 引言目前,低温等离子体技术在材料科学、半导体微电子学和光电子学等领域的研究和加工中起重要作用[1—4].微波电子回旋共振等离子体增强化学汽相沉积(ECR 2PECVD )技术是低温等离子体加工方法中重要技术之一,它是在化学汽相沉积(CVD )的基础上发展起来的新技术.由于等离子体是不等温系统,其中“电子气”具有比中性粒子和正离子大得多的平均能量,电子温度为1—10eV ,约为气体分子的10—100倍,即反应气体接近环境温度,而电子的能量足以使气体分子的化学键断裂,并导致化学活性高的粒子(离子、活化分子等基团)的产生,亦即反应气体的化学键在低温下即可被分解,从而实现高温材料的低温合成[5,6].Si 3N 4薄膜材料是一种人工合成的精细陶瓷功能材料,它具有优良的抗冲击能力、耐高温、抗腐蚀、强度高等特点,在汽车工业、加工工业、微电子工业和光电子工业等方面已得到了广泛的应用[7—9].传统制备Si 3N 4薄膜方法的沉积温度高,对设备的耐温性能和加热方法有特殊的要求,限制了它的应用,ECR 2PECVD 能在较低沉积温度下制备优质均匀的Si 3N 4薄膜.Si 3N 4薄膜的性能取决于薄膜的形成过程,而薄膜的形成受到诸多因素的第48卷第7期1999年7月100023290/1999/48(07)/1309206物 理 学 报ACTA PHYSICA SIN ICA Vol.48,No.7,J uly ,1999ν1999Chin.Phys.S oc.影响[10].如基片沉积温度、基片在反应室内的位置、基片表面性质、反应室内等离子体密度、气体流量等.因此,要提高沉积薄膜的质量和性能,必须了解工艺过程和反应室参量对薄膜性质的影响,确定最佳工艺过程.本文主要研究了反应室内等离子体空间分布的均匀性对ECR 2PECVD 制备Si 3N 4薄膜厚度均匀性的影响,分析了沉积工艺(工作压力、气体配比、基片沉积温度、微波功率)与Si 3N 4薄膜沉积速率的关系,并讨论了制备Si3N 4薄膜的工艺重复性.2 实验装置与等离子体参数空间分布图1为制备Si 3N 4薄膜的ECR 2PECVD 装置图.主要由真空系统、配气系统、微波系统、励磁系统、反应室和基片加热系统以及静电单探针系统组成.真空系统由涡轮分子泵图1 ECR 2PECVD 装置原理图 1为微波源,2为真空系统,3为励磁系统,4为配气系统,5为反应室,6为基片加热系统,7为静电单探针图2 等离子体密度的空间分布和机械泵组成;配气系统由SiH 4,N 2气源和双路流量计组成;微波系统由600W 功率可调的微波源和微波输入匹配耦合器组成;励磁系统由励磁线圈和113×75—115×75A 直流电源组成;反应室由<12cm ×10cm的共振区和<1415cm ×70cm 反应区的不锈钢圆筒两部分组成;基片放置在轴向可移动、温度可调节的基片架上.图2给出当运行气压为8×10-3Pa ,微波功率为240W 时,由偏心静电单探针诊断获得的等离子体反应室内等离子体密度的空间分布.从图2可见,在反应室轴向位置Z =70cm 的共振区附近,径向R =0cm 的中心位置等离子体密度为812×1010cm -3.从微波窗口向抽气口方向过渡时,等离子体密度减小;在轴向位置Z =50cm 处,径向0131物 理 学 报48卷R =0—6cm 范围内等离子体密度很均匀,平均约为1179×1010cm -3.这说明在轴向位置Z =50cm 处的等离子体密度在直径<12cm 范围内分布均匀,有利于制备厚度均匀的薄膜.3 Si 3N 4薄膜样品的制备基片采用(111)单晶硅片、溴化钾(K Br )片和载波片.将基片作常规清洗后烘干装入沉积室进行薄膜沉积.在本底真空好于2×10-3Pa 时,将SiH 4和N 2作为反应气体,经双路流量计送入等离子体反应室内.在ECR 等离子体的激活下,进行化学反应,反应方式为3SiH 4+2N 2+e 等离子体Si 3N 4↓+6H 2↑+e.(1)在基片上沉积出Si 3N 4薄膜.4 实验结果与讨论411 Si 3N 4薄膜的沉积速率与工作气压的关系实验使用80%N 2稀释的SiH 4气体为反应气体(即SiH 4∶N 2配比为1∶4),反应气体经流量计送入反应室,调节气体流量可在不同工作气压下沉积Si 3N 4薄膜.图3给出沉积图3 Si 3N 4薄膜的沉积速率与工作气压的关系速率与工作气压的关系曲线.从图3可见,当工作气压上升时,沉积速率逐渐增高,当工作气压从6×10-2Pa 升至9×10-2Pa 时,沉积速率从15nm/min 增至28nm/min ,增高较快,当工作气压为8×10-2Pa 时,沉积速率为26nm/min 左右,当工作气压从9×10-2Pa 增至3×10-1Pa 时,沉积速率从28nm/min 增至32nm/min ,增高较慢.这是因为工作气压从低气压处开始上升时,反应室内参与反应的气体增加,使到达基片表面的反应产物增多,同时气压适当提高,反应室内的等离子体密度增大,反应气体中活性粒子增多,从而得到高的沉积速率.但当工作气压进一步上升到较高值时,等离子体密度增加不大,在一定的工作气压下反而会减小[11,12],使反应气体活性变弱,导致在高气压范围沉积速率增高较少.412 Si 3N 4薄膜的沉积速率与进气配比的关系利用双路流量计将80%N 2稀释的SiH 4同N 2以不同配比的SiH 4∶N 2气体送入反应室内.分别调节SiH 4和N 2的流量,得到SiH 4∶N 2的进气配比为1/4,1/6,1/8,1/10,1/12.在沉积过程中保持工作气压为8×10-2Pa ,在不同进气配比条件下沉积Si 3N 4薄膜.图4给出沉积速率与进气配比的关系.从图4可见,随进气配比的变小,沉积速率逐渐11317期陈俊芳等:ECR 2PECVD 制备Si 3N 4薄膜沉积工艺的研究降低.在高进气配比1/4处沉积速率为26nm/min 左右,在1/6处沉积速率为24nm/min 左右,在1/8处沉积速率为22nm/min 左右.进气配比从1/4降到1/8范围内,沉积速率图4 Si 3N 4薄膜的沉积速率与进气配比的关系降低较慢.在1/8到1/12低进气配比范围内,沉积速率降低加快.在进气配比为1/10处沉积速率为18nm/min 左右,在进气配比为1/12处沉积速率为125nm/min 左右.这是因为在一定的工作气压下,SiH 4∶N 2进气配比降低时,反应室内SiH 4含量减少,使Si 3N 4的生成产物降低所造成。
MWECR CVD

( 北京工业 大学新型功 能材料教育 部重点实验 室 , 京 102 ) 北 0 02
摘要: 应用 微波 电子 回旋共振 化学气 相沉 积( c v ) m R c o 方法 , 在较 高速度 下沉积 了 ns: —i H薄 膜 , F R红外 谱 用 f l 仪研 究 了 n s: -iH薄膜 的结 构特性 随 H / i4沉积 温度 和沉积 速率变化关 系 , 对 20 c 1 2S 、 H 并 00 mI附近 的特征 吸收峰用 高 斯 函数 进行 了拟合分析 , 获得 了沉积 高质量 n S: —iH薄膜 的最佳工艺 条件 。 关键词 : MWE R C D; —iH薄膜B 分析 ; C V a S: m 高斯 函数 拟合
维普资讯
第 3 1卷 第 3 期
2 0 年 6月 02
人
工 晶 体 学报 源自Vo . No. 1 31 3
J UR L OF Y THE I C YS A S O NA S N TC R T L
Jn 2 0 u e.0 2
MWE R C D 法 高 速 沉 积 .iH C V S: 薄 膜 的 红 外 光 谱 研 究
中图分类号 :4 4 O8 文献标 识码 : A 文 章编号 :0095 2 ))30 2—4 10 -8X((2 0—3 1 I 0
S ud n I I S e t a o W ECR t y o i R p c r fM 1’ CVD . i H S:
Fi s wih g De o ii n t l t a m h p sto Ra e m
c e i l a rd ps i ( hm c p e io M C V a vo o tn R C D)ss m. yt 陬 e
镀膜技术CVD

概 念:气态反应物在一定条件下,通过化学反应,将反应形成的固相产物沉积于基片表面,
形成固态薄膜的方法。
基本特征:由反应气体通过化学反应沉积实现薄膜制备!
设备的基本构成:
气体输运
气相反应 去除副产品 (薄膜沉积)
Chemical vapor deposition, CVD
一、反应过程【以TiCl4(g)+CH4(g)TiC(s)+4HCl(g)为例说明】
■ 各种气体反应物流动进入扩散层;
■ 第①步(甲烷分解):CH4 C + H2 ■ 第②步(Ti的还原):H2+TiCl4 Ti + HCl ■ 第③步(游离Ti、C原子化合形成TiC):Ti + C TiC
二、CVD形成薄膜的一般过程:
单晶 (外延)
板状 单晶
针状 单晶
树枝晶
柱状晶
T
微晶
非晶
粉末 (均相形核)
T
Chemical vapor deposition, CVD
CVD沉积装置
一、概述:
反应气体和载气的供给和计量装置
1)基本系统构成:加热和冷却系统
反应气体的排出装置或真空系统
2)最关键的物理量:沉气积相温反度应物的过饱和度
( E h hc / )
② 基片温度 只影响扩散传输、不影响化学反应
主要优点:
① 沉积温度低、无需高能粒子轰击,可获得 结合好、高质量、无损伤的薄膜;
② 沉积速率快; ③ 可生长亚稳相和形成突变结(abrupt junction)。
主要应用场合:
低温沉积各种高质量金属、介电、半导体薄膜。
cvd涂层工艺技术

cvd涂层工艺技术CVD (化学气相沉积) 涂层工艺技术是一种通过在材料表面使用化学反应沉积薄膜的技术。
CVD涂层工艺技术具有许多优点,如提高材料的硬度、耐腐蚀性和抗磨损能力。
本文将介绍CVD涂层工艺技术的基本原理和步骤,以及其应用领域。
CVD涂层工艺技术的基本原理是利用化学反应在材料表面形成固态产物。
这种技术涉及将涂层物质的预体,通常是气体或液体,通过化学反应转化为固态产物。
整个过程在高温和高压条件下进行。
CVD涂层可以在几微米到几百微米的范围内形成,具有很高的成膜速率和均匀性。
CVD涂层工艺技术的步骤包括基体的预处理、涂层物质的供应和反应、以及产物的固化和后处理。
首先,基体需要进行表面清洁和活化处理,以确保涂层的附着力和均匀性。
接下来,涂层物质被输送到基体表面。
这可以通过气体、液体或固体源来实现。
涂层物质和基体表面之间发生化学反应,形成固态产物。
这个过程需要在适当的温度和压力下进行,并可能需要辅助材料,如催化剂和反应助剂。
最后,产物被固化,并进行后处理,以调整涂层的性能和外观特性。
CVD涂层工艺技术有广泛的应用领域。
例如,它可以在刀具上形成陶瓷涂层,提高其硬度和耐磨损性能。
这使刀具更加耐用,减少了更换刀片的频率,并提高了切削效率。
此外,CVD涂层可以在电子元器件上形成保护层,提高其耐腐蚀性和可靠性。
在汽车行业中,CVD涂层可以在发动机部件上形成陶瓷涂层,以提高其耐高温和耐磨损性能。
此外,CVD涂层还可以用于太阳能电池、光学器件和生物医学材料等领域。
总之,CVD涂层工艺技术是一种通过化学反应在材料表面形成固态产物的技术。
它具有很高的成膜速率和均匀性,可以提高材料的硬度、耐腐蚀性和抗磨损能力。
CVD涂层工艺技术在刀具、电子元器件、汽车部件等领域有广泛的应用。
通过不断改进和创新,CVD涂层工艺技术将在未来的材料科学中扮演重要角色。
CVD的原理与工艺

CVD的原理与工艺CVD(化学气相沉积)是一种常用的薄膜制备技术,通过在高温条件下将气体衍生物在固体表面沉积形成薄膜。
它在半导体、光电子、材料科学等领域有着广泛的应用。
本文将介绍CVD的基本原理和常见的工艺流程。
CVD的基本原理是利用气体在固体表面发生化学反应产生固体沉积。
其过程可以简单概括为三个步骤:传输扩散、化学反应和沉积。
首先,在高温下,气体分子从气相传输到固相表面,这个过程称为传输扩散。
然后,在固体表面发生化学反应,气体分子与表面原子或分子发生物理或化学相互作用。
最后,与固体表面反应的产物发生聚集并沉积到固相表面上,形成薄膜。
CVD工艺可以分为四个主要组成部分:反应室、基底、前驱物和载气。
反应室是进行反应的容器,通常由高温和高真空环境下的材料制成。
基底是待沉积薄膜的衬底,可以是玻璃、硅等多种材料。
前驱物是产生沉积薄膜的化学物质,通常是气态或液态的。
载气是用来稀释前驱物的气体,使其在反应室中更均匀地传输。
CVD的工艺流程是在反应室中将前驱物供应和载气送入,通过传输扩散和化学反应后,形成薄膜并覆盖在基底上。
根据前驱物供应的方式和反应室的特点,CVD可以分为几个常见的工艺类型。
最常见的是热CVD,也称为低压CVD(LPCVD)。
在低压下,前驱物和气体通过加热传输到反应室中,沉积在基底上。
这种方法适用于高温下的材料制备,例如多晶硅、氮化硅等。
另一种常见的是PECVD(等离子体增晶体化学气相沉积)。
在PECVD 中,通过产生等离子体来激活前驱物的化学反应。
在等离子体的作用下,前驱物转化为离子和活性物种,进一步在基底上反应形成薄膜。
这种方法适用于制备非晶硅、氮化硅等。
还有一种CVD工艺称为MOCVD(金属有机化学气相沉积)。
在MOCVD 中,金属有机化合物作为前驱物供应,经氢气或氨气稀释。
通过热解和化学反应,金属有机前驱物转化为金属原子和活性物种,在基底上形成薄膜。
这种方法适用于制备复杂的金属氧化物、尖晶石等。
ECRCVD设备镀膜工艺及膜系设计理论解析

2.2 光在两种均匀介质界面的传播的基本概念和公式: 入射面:入射光线与入射点处界面法线所构成的平面 入射角:入射光线与入射点处界面法线所构成的夹角
折射定律: n0 sinθ0= n1 sinθ1
0
R
n0
n1
1 T
S光、P光:偏振光在入射界面按振动分量分解成S光、P 光。S光的振动方向垂直与入射面,P光的振动方向平行 与入射面,界面对S光和P光有不同的反射率。
路程。
T 2d2p
等离子体:气体放电过程中分子、离子、电子混合存在,形 成相对稳定的状态,称为等离子体。
气体辉光放电:气体直流放电特性,特点是辉光放电时放电 管管压降、电流稳定,气体呈现辉光。
化学气相沉积:在等离子状态下,一些离子在真空室中发生 化学反应,形成固体沉积下来,称为化学气相沉积。
2 膜系设计基本理论
1.2 英文翻译 :
Electron Ceclotron Resonance Chemical Vapor Deposition 电子回旋共振化学气相沉积
1.3 设备基本原理:微波激励、磁场限制气体辉光放电产生 等离子体,在淀积室中反应并沉积形成介质膜。微波激 励气体辉光放电,磁场可以增加离子行程,增加等离子 体密度,并在一定程度上限制离子。离子在淀积室中反 应,沉积在衬底上形成薄膜。
*
R s, p
0 0
Y Y
0 0
Y Y
η0是入射介质
2.4 单层膜正入射的反射率极值(菲涅尔振幅系数公式)
正入射:入射角为0,即θ0 =0。
n1
0 1 2 0 Rs Rp
s p
n1
d1
n2
反射率极值:正入射情况下,在薄膜的光学厚度 n1d1为 λ/4的整数倍时,反射率R取极值。 (菲涅尔振幅系数公式)
- 1、下载文档前请自行甄别文档内容的完整性,平台不提供额外的编辑、内容补充、找答案等附加服务。
- 2、"仅部分预览"的文档,不可在线预览部分如存在完整性等问题,可反馈申请退款(可完整预览的文档不适用该条件!)。
- 3、如文档侵犯您的权益,请联系客服反馈,我们会尽快为您处理(人工客服工作时间:9:00-18:30)。
路程。
T 2d2p
等离子体:气体放电过程中分子、离子、电子混合存在,形 成相对稳定的状态,称为等离子体。
气体辉光放电:气体直流放电特性,特点是辉光放电时放电 管管压降、电流稳定,气体呈现辉光。
化学气相沉积:在等离子状态下,一些离子在真空室中发生 化学反应,形成固体沉积下来,称为化学气相沉积。
d1
n2
d2
n 2N1
正入射下:
Rs
Rp
n0
n
0
nk1
nk1
n1 n2
n1 n2
2N
2N
2
3 650nm LD中应用到的典型λ/4膜系
3.1 重点概念 增透膜:设计膜系的反射率低于不镀膜时的反射率,称为增透膜或减反膜。 高反膜:设计膜系的反射率高于不镀膜时的反射率,称为高反膜。
1
k 1
组合导纳: Y C
B
0 n0
n1
nk n k1
k1
反射率:
*
R s, p
0 0
Y Y
0 0
Y Y
η0是入射介质
2.4 单层膜正入射的反射率极值(菲涅尔振幅系数公式)
正入射:入射角为0,即θ0 =0。
R=
3.52 3.52
1.5 8 2.3 1.5 8
2
96%
2.3
3.3.2 R=85% 膜系结构: GaAs|(Si02|SiNx)3|Air
3.52
1.5
6
2
R=
2.3
SiNx Si4 H N2- SiNx H2
4.3 折射率和膜厚控制
折射率控制:改变工艺参数,如微波功率、反应气体流 量等
膜厚控制: 控制工艺条件和工艺时间
0 n1
n1
d1
1
n2
2
0 n0 n1
N nk n k1
k1
n0
n1
d1
n2
d2
n1 n2 n1 n2 n 2N1
n1
0 1 2 0 Rs Rp
s p
n1
d1
n2
反射率极值:正入射情况下,在薄膜的光学厚度 n1d1为 λ/4的整数倍时,反射率R取极值。 (菲涅尔振幅系数公式)
i
2
is ip ni
Rs
Rp
n0
ห้องสมุดไป่ตู้
n12 n2
n0
n12 n0n2
2
2 膜系设计基本理论
2.1 光在自由空间传播的基本概念和公式:
横波:波的振动方向与传播方向垂直。
光的偏振: 光的振动方向与传播方向的不对称性叫光的 偏振。
光的正弦波表示: 2
E ACos(t nd )
0
自由空间的光程: Δ= nd
光的干涉:两束 相干光在迭加区域内,某些区域光强减 小,某些区域光强增大的现象。本质上是波的迭加。单 色光在空间某点能否形成干涉要看能否形成固定相位差。
n1
n1
n2
d1 d2 d1 d2
d1
2.3 光在分层均匀介质薄膜的传播的基本概念和公式:
(建立光在薄膜中传播的麦克斯韦方程组,根据边界条件求解,得到干 涉矩阵)
折射定律: n0Sin0 n1Sin1 ... nk1Sink1
光在薄膜中传播的光程差:
1 2n1d1Cos1
薄膜的光学厚度:
1 2
3.52
1.
5
6
87.5%
2.3
3.3.3 R=30% 膜系结构: GaAs|Si02|Si02|Air
R=
3.52 3.52
1.52 1.5
1.52
2
31.1%
1.5
3.3.2 R=5%
n1d1
薄膜的相位厚度:
1
2
n1d1Cos1
0 n0
n1
d1
1
艾塔参量 S光 is niCosi , P光 ip ni / Cosi
干涉矩阵(特征矩阵):
B
C
k i1
Cos i ji Sin i
jSini /i Cos i
1.2 英文翻译 :
Electron Ceclotron Resonance Chemical Vapor Deposition 电子回旋共振化学气相沉积
1.3 设备基本原理:微波激励、磁场限制气体辉光放电产生 等离子体,在淀积室中反应并沉积形成介质膜。微波激 励气体辉光放电,磁场可以增加离子行程,增加等离子 体密度,并在一定程度上限制离子。离子在淀积室中反 应,沉积在衬底上形成薄膜。
膜系结构: GaAs|Si02|Air
R=
3.52
1.5
2
2
1
3.52
1.5 1
2
4.8%
3.3.4 R=0%
膜系结构: GaAs|SiNx|Si02|Air
R=
3.52
n1
2
2
1.4
1.4 设备示意图(未反映水电气系统)。
机械泵
工作气
主阀
真空计3
气 控
扩散泵
箱 手动阀
增压泵
手动阀 冷阱
硅烷 其它混合气
波导
磁场 微波源
衬底 观察窗
淀积室
机械控制 真空计4
分子泵
机械泵
仪表
主机 预真空室 机械手 装料门 侧阀
1.5 设备结构图(未反映水电气系统)。
1.6 重点概念
分子的平均自由程:分子在连续两次碰撞之间所走过的平均
ECRCVD设备镀膜工艺 及膜系设计理论讲座
制作:李雪冬
1. ECRCVD设备的基本原理 2. 膜系设计基本理论
3. 650nm LD中应用到的典型λ/4膜系 4. 设计好的膜系在ECRCV设备上如何实
现
1 ECRCVD设备的基本原理
1.1 工艺目的:在半导体激光器的前后腔面镀光学介质膜用 以形成谐振腔。
3.52
n1
2
0%
1.4
n1= 1.4 3.52 2.6
4 设计好的膜系在ECRCV设备上如何实现
4.1 工艺基本过程:
放入工艺气体
微波启动,计时
计时结束,微波停止
4.2 反应方程式:
SiO2 Si4 H O2- SiO2 H2
2.2 光在两种均匀介质界面的传播的基本概念和公式: 入射面:入射光线与入射点处界面法线所构成的平面 入射角:入射光线与入射点处界面法线所构成的夹角
折射定律: n0 sinθ0= n1 sinθ1
0
R
n0
n1
1 T
S光、P光:偏振光在入射界面按振动分量分解成S光、P 光。S光的振动方向垂直与入射面,P光的振动方向平行 与入射面,界面对S光和P光有不同的反射率。
无影响膜层:在正入射下,薄膜的光学厚度 n1d1为 λ/2的 整数倍时,特征矩阵为单位矩阵,对膜系没有影响。
2.5 周期性λ/4膜系的基本概念和公式
周期性λ/4膜系:膜系结构周期性重复,各层膜的光学厚 度均为λ/4,又称规则膜系。
图例
n0
n1
d1
n2
d2
N
n1
d1
n2
d2
n1
3.2 基本膜系设计参数选取
波长λ=650nm
因为激光器内发散角小于10°,可近似为正入射。
入射介质近似为GaAs,出射介质为空气 。
n0=3.52
nk+1=n2N+1=1
膜层介质为Si02、SiNx 。
n1=1.46~1.52
n2=1.8~2.8
3.3 典型规则膜系:
3.3.1 R=95% 膜系结构: GaAs|(Si02|SiNx)4|Air