高强混凝土配合比设计方法及例题
高强混凝土配合比优化设计
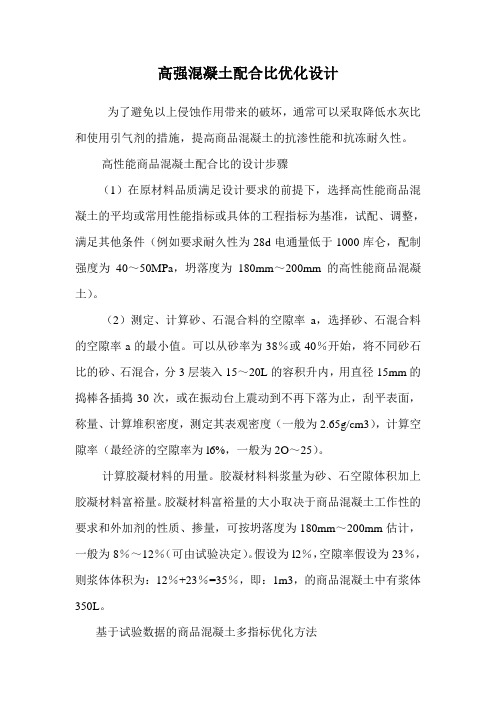
高强混凝土配合比优化设计为了避免以上侵蚀作用带来的破坏,通常可以采取降低水灰比和使用引气剂的措施,提高商品混凝土的抗渗性能和抗冻耐久性。
高性能商品混凝土配合比的设计步骤(1)在原材料品质满足设计要求的前提下,选择高性能商品混凝土的平均或常用性能指标或具体的工程指标为基准,试配、调整,满足其他条件(例如要求耐久性为28d电通量低于1000库仑,配制强度为40~50MPa,坍落度为180mm~200mm的高性能商品混凝土)。
(2)测定、计算砂、石混合料的空隙率a,选择砂、石混合料的空隙率a的最小值。
可以从砂率为38%或40%开始,将不同砂石比的砂、石混合,分3层装入15~20L的容积升内,用直径15mm 的捣棒各插捣30次,或在振动台上震动到不再下落为止,刮平表面,称量、计算堆积密度,测定其表观密度(一般为2.65g/cm3),计算空隙率(最经济的空隙率为l6%,一般为2O~25)。
计算胶凝材料的用量。
胶凝材料料浆量为砂、石空隙体积加上胶凝材料富裕量。
胶凝材料富裕量的大小取决于商品混凝土工作性的要求和外加剂的性质、掺量,可按坍落度为180mm~200mm估计,一般为8%~12%(可由试验决定)。
假设为l2%,空隙率假设为23%,则浆体体积为:12%+23%=35%,即:1m3,的商品混凝土中有浆体350L。
基于试验数据的商品混凝土多指标优化方法高强高性能商品混凝土的迅速发展,使得单目标优化已不能满足要求,更多的是趋向以多目标联合控制进行配比优化。
普通商品混凝土中的保罗米公式已不再适用,这时对于高强高性能商品混凝土来说,已没有明确的描述强度、工作性、耐久性等性能和配合比之间关系的公式。
为了得到优化目标函数,以试验数据为基础,利用统计软件,建立一个拟合精度较高的预测方程。
能够用于高强高性能商品混凝土配合比试验数据优化的方法有逐步回归、人工神经网络和主成分分析法三种。
结束语高强商品混凝土的应用越来越广泛,大家对高强配合比的认知也越来越清晰,合理搭配各种胶凝材料的比例关系,商品混凝土强度可以显著提高,不仅降低了成本,而且对于环保也具有非常明显的现实意义,相信随着高强商品混凝土技术的发展,我们配制出的高强商品混凝土经济效益更加显著。
高强混凝土的配制方法

高强混凝土的配制方法高强混凝土是一种优质的建筑材料,具有高强度、高耐久性、抗渗透性好等特点。
下面将详细介绍高强混凝土的配制方法。
一、原材料选择1.水泥选择标号为P.O42.5或P.O52.5的水泥,因为这种水泥强度高、硬化速度快、抗渗透性和耐久性好。
2.骨料骨料应选用强度高、形状良好、无泥土和其他杂质的鹅卵石或砾石。
推荐选用直径为5-20mm的中等粒度骨料。
3.细集料细集料应选用优质的河砂或人工制造的石粉,粒径为0.15-5mm。
细集料的质量对混凝土的强度、密实性、抗渗性和耐久性等有着重要的影响。
4.水水的质量对混凝土的强度、流动性和耐久性等有着重要的影响。
应选用清洁、无杂质的自来水或地下水。
二、配合比设计配合比设计是混凝土配制的重要环节,直接影响混凝土的强度、流动性和耐久性等。
配合比的设计应根据具体的工程要求和原材料的特性进行。
1.确定水灰比水灰比是指混凝土中水与水泥质量的比值,它直接影响混凝土的强度、流动性和耐久性等。
水灰比的确定应根据具体的工程要求和原材料的特性进行。
一般来说,水灰比应该控制在0.4-0.5之间。
2.确定骨料用量骨料用量的确定应根据混凝土的强度、流动性和耐久性等要求进行。
一般来说,骨料用量应占混凝土总质量的60-70%。
3.确定细集料用量细集料用量的确定应根据混凝土的强度、流动性和耐久性等要求进行。
一般来说,细集料用量应占混凝土总质量的30-40%。
三、混凝土配制混凝土的配制应按照配合比进行,每批混凝土的配制量应根据具体的工程要求和施工进度进行控制。
下面介绍具体的混凝土配制方法。
1.称量原材料将水泥、骨料、细集料和水按照配合比进行称量,确保每批混凝土的配合比稳定。
2.搅拌混凝土将原材料放入混凝土搅拌机中,进行充分的搅拌,直到混凝土达到均匀的状态。
3.浇注混凝土将混凝土从混凝土搅拌机中倒出,进行浇注。
浇注时应注意混凝土的流动性和均匀性,避免出现空鼓、夹杂等问题。
四、混凝土养护混凝土在刚浇注后需要进行养护,以确保混凝土的强度和耐久性。
混凝土配合比设计例题

(9)试验室配合比
水泥∶砂∶石=5.73∶8.99∶19.10=1∶1.57∶3.33 W/C=0.49 则调整后1m3 mC=5.73/(5.73+8.99+19.10+2.84)×2380=372kg mS=1.57×372=584kg mG=3.33×372=1239kg mW=0.49×372=182kg
fcu,o=fcu,k+1.645σ =20+8.2 =28.2(MPa) (2)确定水灰比(W/C)
①利用强度经验公式计算水灰比:
f cu ,v
C
0.48
fce
( W
0.33)
W 0.49 C
②复核耐久性 查表规定最大水灰比为0.65,
因此W/C=0.49满足耐久性要求。
4
(3)确定用水量(mW0) 此题要求施工坍落度为35~50mm,卵石最大粒
16
查表4—7(P52),最小水泥用量为260 kg,所 以应取mc0=368kg。 5.确定砂率 查表,βs=33%。
6.计算砂石用量 (1)质量法 假定混凝土表观密度mcp=2 400 kg/m3, mc0+ms0+mg0+mw0=mcp
17
混凝土计算配合比为: mc0:mw0:ms0:mgo=368:195:606:1 217 =1:O.53:1.65:3.31 (2)体积法
mco mGo mSo mWo 10 1000 c oG oS W
S 解得
mSo mSo mGo
mSO=599kg mGO=1273kg
6
②按质量法:强度等级C20的混凝土,取混 凝土拌合物计算表观密度m′CP=2400kg/m3,
mco mGo mSo mWo mC P
高强度混凝土配合比设计

目前国内一般把强度等级不低于C60的混凝土称为高强度混凝土。
它是用强度不低于42.5级的水泥和优质骨料掺配,并以较低的水灰比,通过充分振动密实作用制取而成的。
其优点是用于结构物后,在保证结构强度要求的前提下,可以显著减少截面尺寸,结构自重减轻,多用于高层建筑、大跨度桥梁等结构工程中。
已被列为建设事业“十一五”重点推广技术领域重点推广项目之一,下面对高强混凝土的原材料选择、配合比设计需注意的事项和要点分述如下:一、原材料由于混凝土是一种复杂的非匀质材料,原材料不同的混凝土其强度高低差异很大。
而对于高强度混凝土来说,影响强度的因素比普通混凝土更为复杂,主要体现在以下几个方面:1.水泥水泥是影响混凝土强度的主要因素。
配制高强度混凝土,应采用矿物组成合理、细度合格的高强度水泥,一般宜优先选取旋窑生产的强度等级不低于42.5的硅酸盐水泥或普通硅酸盐水泥。
之所以对细度特别要求是因为水泥磨的愈细,比表面积就愈大,水化反应愈充分,早期强度就愈高。
但要注意的是细度不宜过高,否则会造成水化热过大,导致混凝土内部产生裂缝,反而减低混凝土后期强度和耐久性。
2.粗集料粗集料在混凝土的结构中主要起骨架作用,骨料的性能对于高强度混凝土的抗压强度能起到决定性作用。
对于高强度混凝土,粗集料的抗压强度、表面特征、最大粒径、杂质含量等对其强度有着重要的影响。
(1)抗压强度为了制备高强度混凝土,要优先选取质地坚硬的碎石,以免粗集料发生破坏。
在试配混凝土之前,应合理确定粗集料的抗压强度,其强度可用压碎值或岩石立方体强度的来测定。
碎石的压碎指标值一般应小于12%。
抗压强度不应小于要求配制的混凝土抗压强度指标的1.5倍。
所以,在选料时最好是采用辉绿岩、花岗岩等强度较高的岩类作为集料。
(2)表面特征在混凝土初凝时,水泥砂浆与粗集料的粘结受集料表面特征的影响较大。
一般应选取近似立方体形的碎石,其表面粗糙、多棱角,这样提高了混凝土的粘结性能,从而提高了混凝土的抗压强度,另外要严格控制针片状颗粒含量、含泥量。
高强混凝土配合比设计方法及例题
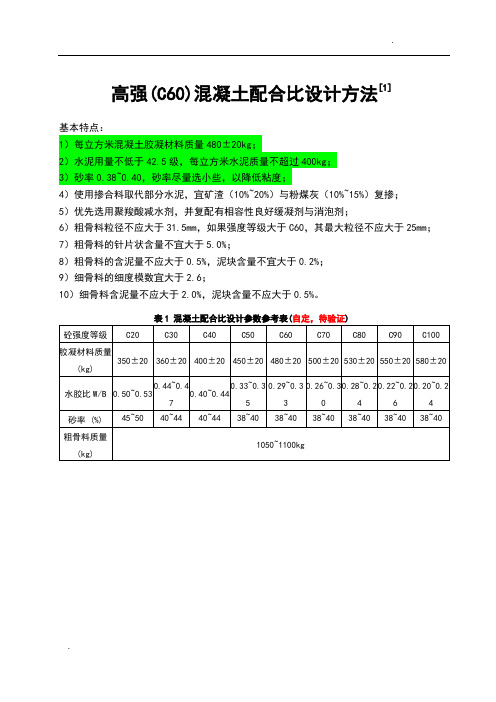
高强(C60)混凝土配合比设计方法[1]基本特点:1)每立方米混凝土胶凝材料质量480±20kg;2)水泥用量不低于42.5级,每立方米水泥质量不超过400kg;3)砂率0.38~0.40,砂率尽量选小些,以降低粘度;4)使用掺合料取代部分水泥,宜矿渣(10%~20%)与粉煤灰(10%~15%)复掺;5)优先选用聚羧酸减水剂,并复配有相容性良好缓凝剂与消泡剂;6)粗骨料粒径不应大于31.5mm,如果强度等级大于C60,其最大粒径不应大于25mm;7)粗骨料的针片状含量不宜大于5.0%;8)粗骨料的含泥量不应大于0.5%,泥块含量不宜大于0.2%;9)细骨料的细度模数宜大于2.6;10)细骨料含泥量不应大于2.0%,泥块含量不应大于0.5%。
3 基本规定3.0.1混凝土配合比设计应满足混凝土配制强度、拌合物性能、力学性能和耐久性能的设计要求。
混凝土拌合物性能、力学性能和耐久性能的试验方法应分别符合现行国家标准《普通混凝土拌合物性能试验方法标准》GB/T50080、《普通混凝土力学性能试验方法标准》GB/T50081和《普通混凝土长期性能和耐久性能试验方法标准》GB/T50082的规定。
3.0.2 混凝土配合比设计应采用工程实际使用的原材料,并应满足国家现行标准的有关要求;配合比设计应以干燥状态骨料为基准,细骨料含水率应小于0.5%,粗骨料含水率应小于0.2%。
3.0.3 混凝土的最大水胶比应符合《混凝土结构设计规范》GB50010的规定。
3.0.4 混凝土的最小胶凝材料用量应符合表3.0.4的规定,配制C15及其以下强度等级的混凝土,可不受表3.0.4的限制。
表3.0.4 混凝土的最小胶凝材料用量3.0.5矿物掺合料在混凝土中的掺量应通过试验确定。
钢筋混凝土中矿物掺合料最大掺量宜符合表3.0.5-1的规定;预应力钢筋混凝土中矿物掺合料最大掺量宜符合表 3.0.5-2的规定。
表3.0.5-1钢筋混凝土中矿物掺合料最大掺量注:①采用硅酸盐水泥和普通硅酸盐水泥之外的通用硅酸盐水泥时,混凝土中水泥混合材和矿物掺合料用量之和应不大于按普通硅酸盐水泥用量20%计算混合材和矿物掺合料用量之和;②对基础大体积混凝土,粉煤灰、粒化高炉矿渣粉和复合掺合料的最大掺量可增加5%;③复合掺合料中各组分的掺量不宜超过任一组分单掺时的最大掺量。
混凝土配合比设计例题

例 某工程现浇室内钢筋混凝土梁,混凝土设计强度等级为 用机械拌合和振捣,坍落度为30〜50mm 。
所用原材料如下:水泥:普通水泥 42.5MPa , 28天实测水泥强度为48MPa ; pc =3100kg/m 3;砂:中砂,级配 2区合格,匚=2650kg/m 3;石子:卵石 5 〜40mm ,為=2650kg/m 3;水:自来水(未掺外加剂),p w = 1000kg/m 3。
(采用体积法计算该混凝土的初步配合比。
) 解:(1)计算混凝土的施工配制强度f cu , o :根据题意可得:f cu , k = 30.0MPa ,查表3.21取尸5.0MPa ,则f cu , o = f cu , k + 1.645 a=30.0+1.645 X5.0 = 38.2MPa(2)确定混凝土水灰比 m w /m c ①按强度要求计算混凝土水灰比m w /m c根据题意可得: a = 0.48 , a = 0.33,则混凝土水灰比为:m .c fw — ____________ a ce ___________ m f ,. f 11"c 1cu,0 a b 1ce0.48X8.038.2 0.48 0.33 48.0②按耐久性要求复核由于是室内钢筋混凝土梁, 属于正常的居住或办公用房屋内, 查表3.22 知混凝土的最大水灰比值为 0.65,计算出的水灰比 0.50未超过规定的最 大水灰比值,因此 0.50能够满足混凝土耐久性要求。
C30,施工采= 0.50(3)确定用水量m w0根据题意,集料为中砂,卵石,最大粒径为40mm ,查表3.24取m wo=160kg o(4) 计算水泥用量 m co ①计算:m c0= mw0= 160= 320kg m w / m c0.50②复核耐久性由于是室内钢筋混凝土梁, 属于正常的居住或办公用房屋内, 查表3.22 知每立方米混凝土的水泥用量为 260kg ,计算出的水泥用量 320kg 不低于 最小水泥用量,因此混凝土耐久性合格。
高强混凝土配合比确定方法
高强混凝土配合比确定方法论述了高强砼配合比确定方法仍采用普通砼配合比确定方法的不足,并论述了采用“正交——综合评定法”是解决问题的有效方法。
随着材料的开发及应用,砼组成材料由普通砼的水泥、砂、石、水四种发展为5~7种组成材料,使影响砼强度及工作性等的因素变得更复杂,这就为砼配合比的确定提出了新的要求。
砼配合比的确定,关键是要保证砼满足施工、强度、耐久性、经济性四方面要求。
在现行配合比设计规程JGJ/T55—96中,高强砼配合比确定方法基本上还采用普通砼的确定方法,但在实践中,该方法已显不足。
1 现行的高强砼配合比确定方法高强砼配合比的确定现在基本是应用普通砼的确定方法。
该方法是利用鲍罗公式及表格按强度及耐久性要求确定水灰比;按;按经验确定外加剂粘聚性要求确定砂率Sp;按流动性要求确定单位用水量WO掺量及掺合料用量;按以上确定参数计算初步配合比;然后进行试拌,按工作性及外加剂等作适当调节;最后利用~f的线性关系进行强度调节好坏,对Sp、WO确定配合比,这方法以其简单易行一直被人们所应用。
2 在普通砼及高强砼中,用料及配合比关键参数对性能的影响的差别。
2.1 水灰比1)在原材料一定的条件下,在普通砼中,对强度起决定性作用。
因此,在确定时,除考虑耐久性外。
主要由强度确定:而在高强砼中,除外,骨料含量、砂率、单位用水量等对强度也影响较为显著。
2)在普通砼中,灰水比与砼强度f的关系为线性关系,在进行砼试配时,正是利用了此关系进行强度调整;而在高强砼中,当较小时,~f的线性关系反常。
2.2 磅率Sp的影响在普通砼中,Sp对强度影响很少,对粘聚性影响十分显著。
随着Sp增大,粘聚性变好。
因此,在确定砼配合比时,没有考虑对强度的影响,只是按施工操作要求的粘聚性确定Sp。
在高强砼中,Sp对砼强度影响较大,试验表明,Sp减少,强度增加,Sp每减少1%,强度约增加1%;而Sp对粘聚性影响较小,原因是高强砼的较小,水泥用量大,且掺入大量的掺合料,本身粘聚性很好。
混凝土配合比例题
某工程现浇室内钢筋混凝土梁,混凝土设计强度等级为 C30,施工采用机械拌合和振捣,坍落度为30〜50mm 。
所用原材料如下:水泥:普通水泥 42.5MPa , 28天实测水泥强度为 48MPa ; p= 3100kg/m 3;砂:中砂,级配 2区合 格,==2650kg/m 3;石子:卵石 5〜40mm , -g = 2650kg/m 3;水:自来水(未掺外加剂),p = 1000kg/m 3。
1•采用体积法计算该混凝土的初步配合比。
解:(1)计算混凝土的施工配制强度f eu , 0:根据题意可得:f eu , k = 30.0MPa ,查表3.24取 尸5.0MPa ,贝Uf eu , 0 = f eu , k + 1.645(T=30.0+1.645 >5.0 = 38.2MPa(2)确定混凝土水灰比 m^/m c①按强度要求计算混凝土水灰比m w / m e根据题意可得:f ee = 1.13 >42.5MPa , a= 0.48 , a= 0.33,则混凝土水灰比为:mw— a ' f eem e f cu ,0 • : af ee0.48X48.0 38.2 0.48 0.33 48.0②按耐久性要求复核由于是室内钢筋混凝土梁,属于正常的居住或办公用房屋内,查表 0.65,计算出的水灰比 0.50未超过规定的最大水灰比值,因此0.50能够满足混凝土耐久性要求。
(3) 确定用水量m w0根据题意,集料为中砂,卵石,最大粒径为 40mm ,查表3.26取m w0 = 160kg 。
(4) 计算水泥用量m e 。
①计算: m e0= m w0=迪=320kgm w / m e 0.50②复核耐久性由于是室内钢筋混凝土梁,属于正常的居住或办公用房屋内,查表 量为260kg ,计算出的水泥用量 320kg 不低于最小水泥用量,因此混凝土耐久性合格。
(5 )确定砂率仪根据题意,混凝土采用中砂、卵石(最大粒径 40mm )、水灰比0.50,查表3.28可得侮=28%〜33 %,取仪=30%。
配合比计算例题及详解
配合比计算例题及详解一、在混凝土配合比设计中,已知水泥用量为300kg/m³,水灰比为0.5,则每立方米混凝土中水的用量为多少kg?A. 100B. 150C. 200D. 250(答案)B二、某砂浆配合比中,砂的用量为1.2m³,水泥用量为250kg,若水泥与砂的重量比为1:4,则每立方米砂浆中砂的实际重量是多少kg?A. 800B. 1000C. 1200D. 1600(答案)B(注:此处考虑了砂的容重,假设为1600kg/m³,则1.2m³砂重1920kg,但按比例算应为1000kg水泥对应4000kg砂,取较小值即B选项)三、在沥青混合料配合比设计中,若已知沥青用量为5.5%,矿料总质量为1900kg/m³,则每立方米混合料中沥青的质量是多少kg?A. 95B. 104.5C. 110D. 115(答案)B四、某混凝土配合比设计中,水灰比为0.45,水泥用量为350kg/m³,若要保持水灰比不变,将水泥用量增加至400kg/m³,则每立方米混凝土中应增加多少kg水?A. 10B. 15C. 20D. 22.5(答案)D五、在砂浆配合比中,若已知砂的用量为1.5m³,水泥与砂的体积比为1:6,且水泥的密度为3.1g/cm³,则每立方米砂浆中水泥的质量是多少kg?A. 258.3B. 516.6C. 775D. 1033(答案)A(注:此处需将体积比转换为质量比,考虑砂的容重后计算)六、某混凝土配合比中,已知水的用量为180kg/m³,水灰比为0.6,若要将水灰比调整至0.55,且保持水泥用量不变,则每立方米混凝土中应减少多少kg水?A. 10B. 16.36C. 20D. 27.27(答案)B七、在沥青混合料配合比设计中,若沥青用量为4.8%,混合料总质量为2400kg/m³,则每立方米混合料中矿料的质量是多少kg?A. 2208B. 2256C. 2304D. 2352(答案)C八、某混凝土配合比中,水泥用量为320kg/m³,砂率为35%,若砂的密度为1.6g/cm³,石子的密度为2.7g/cm³,且假设混凝土容重为2400kg/m³,则每立方米混凝土中石子的体积是多少m³?A. 0.8B. 0.85C. 0.9D. 0.95 (答案)C (注:需先计算出砂和石子的总质量,再根据砂率分配,最后转换为体积)。
(精选)混凝土配合比设计例题
例 某工程现浇室内钢筋混凝土梁,混凝土设计强度等级为C30,施工采用机械拌合和振捣,坍落度为30~50mm 。
所用原材料如下:水泥:普通水泥42.5MPa ,28天实测水泥强度为48MPa ; ρc =3100kg/m 3;砂:中砂,级配2区合格,s ρ'=2650kg/m 3;石子:卵石5~40mm ,gρ'=2650kg/m 3;水:自来水(未掺外加剂),ρw =1000kg/m 3。
(采用体积法计算该混凝土的初步配合比。
)解:(1)计算混凝土的施工配制强度f cu ,0:根据题意可得:f cu ,k =30.0MPa ,查表3.21取σ=5.0MPa ,则f cu ,0 = f cu ,k + 1.645σ=30.0+1.645×5.0=38.2MPa(2)确定混凝土水灰比cw /m m①按强度要求计算混凝土水灰比c w /m m根据题意可得:αa =0.48,αb =0.33,则混凝土水灰比为:ceb a 0cu cea c w f f f m m ⋅⋅+⋅ααα,= 50.00.4833.048.02.380.4848.0==⨯⨯+⨯②按耐久性要求复核由于是室内钢筋混凝土梁,属于正常的居住或办公用房屋内,查表3.22知混凝土的最大水灰比值为0.65,计算出的水灰比0.50未超过规定的最大水灰比值,因此0.50能够满足混凝土耐久性要求。
(3)确定用水量m w0根据题意,集料为中砂,卵石,最大粒径为40mm ,查表3.24取m w0=160kg 。
(4)计算水泥用量m c0 ①计算:kg 32050.0160/c w w0c0===m m m m ②复核耐久性由于是室内钢筋混凝土梁,属于正常的居住或办公用房屋内,查表3.22知每立方米混凝土的水泥用量为260kg ,计算出的水泥用量320kg 不低于最小水泥用量,因此混凝土耐久性合格。
(5)确定砂率βs根据题意,混凝土采用中砂、卵石(最大粒径40mm )、水灰比0.50,查表3.25可得βs =28%~33%,取βs =30%。
- 1、下载文档前请自行甄别文档内容的完整性,平台不提供额外的编辑、内容补充、找答案等附加服务。
- 2、"仅部分预览"的文档,不可在线预览部分如存在完整性等问题,可反馈申请退款(可完整预览的文档不适用该条件!)。
- 3、如文档侵犯您的权益,请联系客服反馈,我们会尽快为您处理(人工客服工作时间:9:00-18:30)。
高强(C60)混凝土配合比设计方法[1]基本特点:1)每立方米混凝土胶凝材料质量480±20kg;2)水泥用量不低于42.5级,每立方米水泥质量不超过400kg;3)砂率0.38~0.40,砂率尽量选小些,以降低粘度;4)使用掺合料取代部分水泥,宜矿渣(10%~20%)与粉煤灰(10%~15%)复掺;5)优先选用聚羧酸减水剂,并复配有相容性良好缓凝剂与消泡剂;6)粗骨料粒径不应大于31.5mm,如果强度等级大于C60,其最大粒径不应大于25mm;7)粗骨料的针片状含量不宜大于5.0%;8)粗骨料的含泥量不应大于0.5%,泥块含量不宜大于0.2%;9)细骨料的细度模数宜大于2.6;10)细骨料含泥量不应大于2.0%,泥块含量不应大于0.5%。
3 基本规定3.0.1混凝土配合比设计应满足混凝土配制强度、拌合物性能、力学性能和耐久性能的设计要求。
混凝土拌合物性能、力学性能和耐久性能的试验方法应分别符合现行国家标准《普通混凝土拌合物性能试验方法标准》GB/T50080、《普通混凝土力学性能试验方法标准》GB/T50081和《普通混凝土长期性能和耐久性能试验方法标准》GB/T50082的规定。
3.0.2 混凝土配合比设计应采用工程实际使用的原材料,并应满足国家现行标准的有关要求;配合比设计应以干燥状态骨料为基准,细骨料含水率应小于0.5%,粗骨料含水率应小于0.2%。
3.0.3 混凝土的最大水胶比应符合《混凝土结构设计规范》GB50010的规定。
3.0.4 混凝土的最小胶凝材料用量应符合表3.0.4的规定,配制C15及其以下强度等级的混凝土,可不受表3.0.4的限制。
表3.0.4 混凝土的最小胶凝材料用量3.0.5矿物掺合料在混凝土中的掺量应通过试验确定。
钢筋混凝土中矿物掺合料最大掺量宜符合表3.0.5-1的规定;预应力钢筋混凝土中矿物掺合料最大掺量宜符合表3.0.5-2的规定。
表3.0.5-1钢筋混凝土中矿物掺合料最大掺量注:①采用硅酸盐水泥和普通硅酸盐水泥之外的通用硅酸盐水泥时,混凝土中水泥混合材和矿物掺合料用量之和应不大于按普通硅酸盐水泥用量20%计算混合材和矿物掺合料用量之和;②对基础大体积混凝土,粉煤灰、粒化高炉矿渣粉和复合掺合料的最大掺量可增加5%;③复合掺合料中各组分的掺量不宜超过任一组分单掺时的最大掺量。
表3.0.5-2 预应力钢筋混凝土中矿物掺合料最大掺量②在复合掺合料中,各组分的掺量不宜超过单掺时的最大掺量。
3.0.6 混凝土拌合物中水溶性氯离子最大含量应符合表3.0.6的要求。
混凝土拌合物中水溶性氯离子含量应按照现行行业标准《水运工程混凝土试验规程》JTJ 270中混凝土拌合物中氯离子含量的快速测定方法进行测定。
表3.0.6 混凝土拌合物中水溶性氯离子最大含量3.0.7 长期处于潮湿或水位变动的寒冷和严寒环境、以及盐冻环境的混凝土应掺用引气剂。
引气剂掺量应根据混凝土含气量要求经试验确定;掺用引气剂的混凝土最小含气量应符合表3.0.7的规定,最大不宜超过7.0%。
表 3.0.7 掺用引气剂的混凝土最小含气量注:含气量为气体占混凝土体积的百分比。
3.0.8 对于有预防混凝土碱骨料反应设计要求的工程,混凝土中最大碱含量不应大于3.0kg/m3,并宜掺用适量粉煤灰等矿物掺合料;对于矿物掺合料碱含量,粉煤灰碱含量可取实测值的1/6,粒化高炉矿渣粉碱含量可取实测值的1/2。
3.0.8混凝土耐久性设计[2]限制每立方米混凝土中胶凝材料的最低和最高用量,尽可能减水硅酸酸盐水泥用量。
除此之外,还应保证混凝土施工质量。
即要混凝土搅拌搅拌均匀、浇捣密实、加强养护,避免产生次生裂缝。
[2]注:氯化物环境(Ⅲ和Ⅳ)对混凝土材料也有一定腐蚀作用,但主要是引起钢筋的严重锈蚀。
反复冻融(Ⅱ)和其它化学介质对混凝土的冻蚀和腐蚀,也会间接促进钢筋锈蚀,有的并能直接引起钢筋锈蚀,但主要是对混凝土的损伤和破坏。
标准[3]对混凝土的最低强度等级、最大水胶比和每立方米混凝土胶凝材料最小用量作了如下规定:[3]-3注:1、对于氯盐环境(Ⅲ-D和Ⅳ-D),这一混凝土最大水胶比0.45宜降为0.40。
2、引气混凝土的最低强度等级与最大水胶比可按降低一个环境等级采用。
3、表中胶凝材料最小用量与骨料最大粒径约为20mm的混凝土相对应,当最大粒径较小或较大时需适当增减胶凝材料用量。
4、对于冻融和化学腐蚀环境下的薄壁构件,其水胶比宜适当低于表中对应的数值。
4 混凝土配制强度的确定4.0.1 混凝土配制强度应按下列规定确定:1.当混凝土的设计强度等级小于C60时,配制强度应按下式计算:cu,0cu,k 1.645f f σ≥+(4.0.1-1)式中,f cu,o —混凝土配制强度,MPa ;f cu,k —混凝土立方体抗压强度标准值,这里取设计混凝土强度等级值,MPa ; σ—混凝土强度标准差,MPa 。
2.当设计强度等级大于或等于C60时,配制强度应按下式计算:cu,0cu,k 1.15f f ≥(4.0.1-2)4.0.2 混凝土强度标准差应按照下列规定确定:1.当具有近1个月~3个月的同一品种、同一强度等级混凝土的强度资料时,其混凝土强度标准差σ应按下式计算:σ=(4.0.2)式中,f cu ,i —第i 组的试件强度,MPa ;m fcu —n 组试件的强度平均值,MPa ; n —试件组数,n 值应大于或者等于30。
对于强度等级不大于C30的混凝土:当σ计算值不小于3.0MPa 时,应按照计算结果取值;当σ计算值小于3.0MPa 时,σ应取3.0MPa 。
对于强度等级大于C30且不大于C60的混凝土:当σ计算值不小于4.0MPa 时,应按照计算结果取值;当σ计算值小于4.0MPa 时,σ应取4.0MPa 。
2.当没有近期的同一品种、同一强度等级混凝土强度资料时,其强度标准差σ可按表4.0.2取值。
表4.0.2 标准差σ值 (MPa)5 混凝土配合比计算5.1 水胶比5.1.1 混凝土强度等级小于C60等级时,混凝土水胶比宜按下式计算:a bcu,0a b b/f W B f f ααα⋅=+⋅⋅(5.1.1)式中:W /B -混凝土水胶比;αa 、αb —回归系数,按规程5.1.2条的规定取值;f b —胶凝材料(水泥与矿物掺合料按使用比例混合)28d 胶砂强度(MPa ),可实测,试验方法应按现行国家标准《水泥胶砂强度检验方法(ISO 法)》GB/T 17671执行;也可按本规程5.1.3条确定。
5.1.2 回归系数(αa 、αb )宜按下列规定确定:1.根据工程所使用的原材料,通过试验建立的水胶比与混凝土强度关系式来确定; 2.当不具备上述试验统计资料时,可按表5.1.2采用。
表 5.1.1 回归系数(α5.1.3 当胶凝材料28d 胶砂抗压强度值(f b )无实测值时,可按下式计算:b f s ce f f γγ=⋅⋅(5.1. 2)式中:γf 、γs —粉煤灰影响系数和粒化高炉矿渣粉影响系数,可按表5.1.2选用;f ce —水泥28d 胶砂抗压强度,MPa ,可实测,也可按本规程第5.1.4条规定。
表5.1.2 粉煤灰影响系数γ注:1 采用Ⅰ级、Ⅱ级粉煤灰宜取上限值;2 采用S75级粒化高炉矿渣粉宜取下限值,采用S95级粒化高炉矿渣粉宜取上限值,采用S105级粒化高炉矿渣粉可取上限值加0.05。
3 当超出表中的掺量时,粉煤灰和粒化高炉矿渣粉影响系数应经试验确定。
5.1.4 当水泥28d 胶砂抗压强度(f ce )无实测值时,可按下式计算:ce c ce,g f f γ=⋅(5.1.3)式中:γc —水泥强度等级值的富余系数,可按这际统计资料确定;当缺乏实际统计资料时,也可按表5.1.3选用。
f ce,g —水泥强度等级,MPa 。
表5.1.3 水泥强度等级值的富余系数 (γ5.2 用水量和外加剂用量5.2.1 每立方米干硬性或塑性混凝土的用水量(m wo )应符合下列规定:1.混凝土水胶比在0.40~0.80范围时,可按表5.2.1-1和表5.2.1-2选取; 2.混凝土水胶比小于0.40时,可通过试验确定。
表 5.2.1-1 干硬性混凝土的用水量(kg/m 3)表 5.2.1-2 塑性混凝土的用水量(kg/m 3)注:① 本表用水量系采用中砂时的取值。
采用细砂时,每立方米混凝土用水量可增加5~10kg ;采用粗砂时,可减少5~10kg 。
②以本规程表5.2.1-2中90mm 坍落度的用水量为基础,按每增大20mm 坍落度相应增加5kg/m 3用水量来计算,当坍落度增大到180mm 以上时,随坍落度相应增加的用水量可减少。
③基于保证剩余强度和混凝土耐久性考虑,单方用水量需小于200kg ,采用低水胶比、大掺和料的方式设计混凝土配合比。
5.2.2 掺外加剂时,每立方米流动性或大流动性混凝土的用水量(m wo )可按下式计算:'w00(1)w m m β=⋅-(5.2.2)式中:m w0—计算配合比每立方米混凝土的用水量,kg ;'0w m—未掺加外加剂时推定的满足实际坍落度要求的每立方米混凝土用水量(kg/m 3),以本规程表5.2.1-2中90mm 坍落度的用水量为基础,按每增大20mm 坍落度相应增加5kg/m 3用水量来计算,当坍落度增大到180mm 以上时,随坍落度相应增加的用水量可减少。
β—外加剂的减水率,%,应经混凝土试验确定。
5.2.3 每立方米混凝土中外加剂用量应按下式计算:a0b0a m m β=⋅(5.2.3)式中:m a0—计算配合比每立方米混凝土中外加剂用量,kg ;m b0—计算配合比每立方米混凝土中胶凝材料用量,kg ; βa —外加剂掺量,%,应经混凝土试验确定。
5.3 胶凝材料、矿物掺合料和水泥用量5.3.1 每立方米混凝土的胶凝材料用量(m bo )应按下式计算:0b0/w m m W B =(5.3.1)式中:m b0—计算配合比每立方米混凝土中胶凝材料用量,kg ; m w0—计算配合比每立方米混凝土用水量,kg ; W/B —混凝土水胶比。
5.3.2 每立方米混凝土的矿物掺合料用量(m f0)计算应按下式计算:f0b0f m m β=(5.3.2)式中:m f0—计算配合比每立方米混凝土中矿物掺合料用量,kg ;βf —矿物掺合料掺量,%,可结合本规程3.0.5条和第5.1.1条的规定确定。
计算水胶比过程中确定的矿物掺合料掺量(%)。
5.3.3 每立方米混凝土的水泥用量(m co )应按下式计算:c0b0f0m m m =-(5.3.3)式中:m c0—计算配合比每立方米混凝土中水泥用量,kg 。