3.3 晶粒大小的控制
控制晶粒大小的方法

控制晶粒大小的方法晶粒是材料中最小的可识别的晶体结构单元,晶粒的大小对材料的力学性能、导电性能、磁性能、耐腐蚀性能等具有重要影响。
因此,控制晶粒大小是材料制备中的一个重要方面。
下面将介绍几种常用的控制晶粒大小的方法:1. 热处理方法:热处理是一种常用的控制晶粒大小的方法。
通过控制材料的加热温度、保温时间以及冷却速率等参数,可以对晶粒的尺寸进行调控。
一般来说,高温下晶粒的生长速度较快,低温下晶粒的生长速度较慢。
因此,可以通过热处理的方式控制材料的晶粒尺寸。
2. 拉伸方法:在金属材料的加工过程中,可以通过拉伸的方法来控制晶粒的大小。
拉伸过程中,材料会受到拉伸应力,晶粒会在应力的作用下变形、分裂、再结晶。
通过控制拉伸应力的大小和作用时间,可以实现对晶粒的精确控制。
3. 添加外界元素:通过向材料中添加外界元素,可以有效控制晶粒的尺寸。
添加外界元素可以改变材料的晶界能、溶解度和晶核密度等特性,从而影响晶粒的生长行为。
常用的添加元素有Al、Mg、Cu等,这些元素可以形成固溶体、沉淀相或形成特殊的晶核,从而控制晶粒的尺寸。
4. 界面动力学方法:通过界面动力学方法可以控制晶界的迁移、再结晶和晶粒长大等过程,从而控制晶粒的尺寸。
界面动力学方法主要包括晶界迁移和晶粒长大机制的控制等。
晶界迁移是指晶界的运动和变形,晶粒长大机制是指晶粒体积的增大。
通过控制这两个过程,可以对晶粒的尺寸进行控制。
总结起来,控制晶粒大小的方法主要包括热处理方法、拉伸方法、添加外界元素和界面动力学方法等。
通过这些方法,可以在材料制备过程中精确控制晶粒的尺寸,从而调控材料的性能。
值得注意的是,不同材料的晶粒大小控制方法可能有所不同,需要根据具体材料的特点选择合适的方法。
此外,未来随着科学技术的不断发展,可能还会有更多新的方法出现来控制晶粒的尺寸。
晶粒细化的控制方法

通过采用工艺方法控制可使金属材料的晶粒细化、均匀,从而提高材料的强度、韧性和塑性,更好适应工程项目对材料的要求。
对于晶粒细化,目前的控制方法有:1、氧化物冶金技术基本原理是利用钢中形成较早、且分布均匀,氧化物作为钢中硫化物、氮化物和碳化物等析出物的非均质形核核心,并通过控制这些析出物的位置和分布,完成对晶粒成长的控制,然后利用钢中的复合夹杂物来诱导晶内针状铁素体形核来细化材料的组织。
该方法的关键是如何在钢中获得细小的夹杂物。
首先,必须提高钢液的纯净度,并且去除钢液中已生成的各种较大颗粒的非金属夹杂物;其次,为了确保获得细小的第二相粒子,以保证第二相粒子能够在固态下析出,应将各种夹杂物生成元素的浓度积控制在固相线的平衡浓度积以下。
获得第二相离子的方法有内部析出法和外部加入法。
前者利用钢中析出物作为非均质形核核心的原来来细化组织,后者通过在材质外部添加第二相粒子的方法对组织细化。
2、TMCP工艺TMCP工艺包括控制轧制工艺和轧制后的控制冷却工艺2个阶段,它主要是通过控制轧制温度和轧制后的冷却速度,以及冷却的开始温度和终止温度来控制高温奥氏体的组织形态和相变过程,目的是细化奥氏体晶粒组织,增加奥氏体的位错密度,提高铁素体的形核率来细化相变后的组织,从而达到细化组织和提高力学性能的目的。
3、HIP工艺与弛豫技术1)HIP工艺是在常规TMCP工艺的基础上发展起来的,它主要是增加钢中Nb的含量。
由于Nb除了具有阻止奥氏体再结晶和细化铁素体晶粒的作用以外,它还具有显著提高钢的再结晶和细化铁素体晶粒的作用以外,它还具有显著提高钢的再结晶终止温度和降低相变温度的作用,因此,通过HIP技术可以显著提高管线钢的终轧温度,然后配以较快的冷却速度,从而得到细小的针状铁素体组织,从而细化晶粒。
2)为了满足高级别材质高强度高韧性的同时并具有高塑性这一发展趋势,开发了弛豫技术。
这种技术的关键是将终轧后的钢板空冷一段时间,使钢板在入水前的温度降低到Ar3以下30-50℃,生成一定量的先共析铁素体,最后通过一定冷速的水冷,得到先共析铁素体和贝氏体/MA的双相组织,从而极大提高管线钢的强度、塑性及韧性。
控制晶粒度的方法

控制晶粒度的方法晶粒度是材料科学中一个重要的性质之一,它直接影响材料的力学性能、导电性能、磁性能等。
因此,控制晶粒度是材料研究中的一个重要课题。
本文将介绍几种常见的控制晶粒度的方法。
1. 热处理热处理是一种常见的控制晶粒度的方法。
通过控制材料的加热温度、保温时间等条件,可以使晶粒逐渐长大。
晶粒的长大过程遵循奥斯特沃德生长定律,即晶粒长大的速率与晶粒大小成反比。
因此,晶粒越大,其生长速率越慢。
通过热处理可以得到不同晶粒度的材料,从而实现对材料性能的调控。
2. 化学合成化学合成是一种常用的制备纳米材料的方法,同时也可以控制晶粒度。
在化学合成过程中,通过控制反应条件、添加剂等,可以控制晶粒的大小和组成。
例如,通过调节反应温度和反应时间,可以制备出晶粒大小均匀、尺寸可控的纳米材料。
3. 机械合金化机械合金化是一种通过高能球磨等方法制备纳米材料的技术。
在机械合金化过程中,材料经过高能球磨等机械力作用,使晶粒不断碾压、断裂、重组,从而实现晶粒的细化。
机械合金化技术可以制备出晶粒尺寸在几纳米至几十纳米之间的纳米材料。
4. 轧制轧制是一种通过机械力作用对材料进行加工的方法。
在轧制过程中,通过不断的轧制和拉伸,可以使材料中的晶粒逐渐细化。
此外,轧制还可以使晶粒形状变形,从而改变晶界的形态和数量,从而影响材料性能。
5. 离子注入离子注入是一种通过将离子注入到材料中来改变材料性质的方法。
在离子注入过程中,离子通过高能束流的作用,进入材料中与其原子发生相互作用,从而引起材料的结构和性质的变化。
离子注入可以实现对材料晶粒度的控制。
总之,控制晶粒度是材料研究中的一个重要课题。
通过热处理、化学合成、机械合金化、轧制、离子注入等方法,可以实现对晶粒的控制和调控,从而得到不同晶粒度的材料,满足不同应用的需求。
未来,随着科技的不断进步,控制晶粒度的技术将会越来越成熟,为材料科学的发展带来更多的可能性。
抑制晶粒长大的方法

抑制晶粒长大的方法晶粒长大是指晶体中晶粒尺寸的增大,通常是由于结晶过程中的温度变化或晶体生长速率不均匀等原因引起的。
晶粒长大会影响材料的性能和微观结构,因此在材料制备和加工过程中,抑制晶粒长大是一个重要的问题。
本文将介绍一些常见的抑制晶粒长大的方法。
1. 温度控制温度是影响晶粒长大的主要因素之一。
晶粒长大通常在高温下发生,因此通过控制温度可以有效抑制晶粒长大。
一种常用的方法是采用温度梯度结晶,即在结晶过程中设置温度梯度,使晶粒在温度梯度的作用下得以控制生长,从而抑制晶粒长大。
2. 添加抑制剂添加抑制剂是另一种常见的抑制晶粒长大的方法。
抑制剂可以通过与晶体表面发生化学反应,改变晶体表面能,从而减缓晶粒的生长速度。
例如,在金属材料的制备过程中,常用的抑制剂有钛、锆等元素,它们可以与晶体表面发生反应形成稳定的化合物,从而抑制晶粒长大。
3. 界面控制界面控制是一种有效的抑制晶粒长大的方法。
通过在晶体界面上引入各种界面结构、界面缺陷或界面能量,可以有效地阻止晶粒的生长。
例如,在陶瓷材料的制备过程中,可以通过控制添加剂的含量和选择合适的添加剂,来调控晶体的界面结构和能量,从而抑制晶粒长大。
4. 应力控制应力是影响晶粒长大的重要因素之一。
通过引入外部应力或内部应力,可以有效地抑制晶粒长大。
外部应力可以通过加工和热处理等手段施加在晶体上,从而改变晶粒的形态和尺寸,从而抑制晶粒长大。
内部应力可以通过合金元素的选择和添加来引入,从而改变晶粒的位错密度和分布,从而抑制晶粒长大。
5. 控制晶体形态晶体的形态对晶粒长大有很大的影响。
通过控制晶体的形态,可以有效地抑制晶粒长大。
例如,在陶瓷材料的制备过程中,可以通过控制原料的粒度和形状,以及控制结晶过程中的溶液浓度和pH值等因素,来控制晶体的形态,从而抑制晶粒长大。
抑制晶粒长大是材料制备和加工过程中一个重要的问题。
通过温度控制、添加抑制剂、界面控制、应力控制和控制晶体形态等方法,可以有效地抑制晶粒长大,从而改善材料的性能和微观结构。
晶粒尺寸的控制
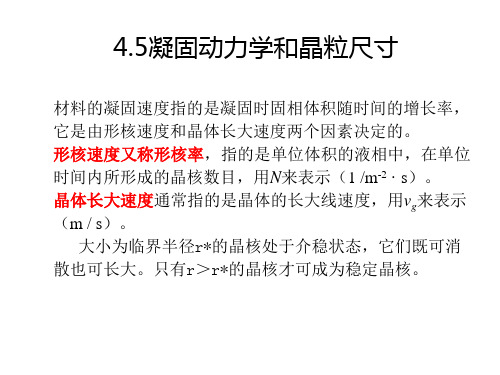
1、形核率
均匀形核 形核率N受两个矛盾的因素控制,一方面随过冷度增大, rc、ΔGc 减小,有利于形核;另一方面随过冷度增大, 原子从液相向晶胚扩散的速率降低,不利于形核。形核 率可用下式表示: Gc GA - RT RT N N1N2 KVe e
(式中 N 为总形核率, N1 为受形核功影响的形核率因子; N2 是受扩散影响的形核率因子。
v g v1Tk
• 其中v1为材料相关的比例常数, 单位是m / s ·K。凝固时晶体的 长大速度还受所释放潜热的传导 速度控制,对于具有粗糙界面的 晶体材料,其结晶潜热一般较小, 因此,连续生长时的长大速度较 高。
晶体的长大速率
• 对于二维形核生长方式而言,晶体 的生长是不连续的,相应的平均长 b 大速率可表示为, v g v 2 exp( ) • 其中v2和b均为常数。当 Tk 很小时, vg非常小,这是因为二维形核所需 形核功较大,且二维晶核需达到一 定临界尺寸后才能进一步扩展。 • 藉螺型位错生长方式的平均长大速 率可表示为,
4.5凝固动力学和晶粒尺寸
材料的凝固速度指的是凝固时固相体积随时间的增长率, 它是由形核速度和晶体长大速度两个因素决定的。 形核速度又称形核率,指的是单位体积的液相中,在单位 时间内所形成的晶核数目,用N来表示(1 /m-2 ·s)。 晶体长大速度通常指的是晶体的长大线速度,用vg来表示 (m / s)。 大小为临界半径r*的晶核处于介稳状态,它们既可消 散也可长大。只有r>r*的晶核才可成为稳定晶核。
凝固后晶粒尺寸的控制
• (3)采用振动或搅拌等物理方法 • 在熔液凝固时施加振动或搅拌作用能得到细小的 晶粒. • 机械振动、电磁搅拌、超声波振动等。 • 晶粒的细化作用主要是通过两个方面来实现的 • 由于能量的输入使液相的形核率提高 • 振动或搅拌使生长的晶冷却速度来实现,即通过 改变铸造条件如降低浇注温度、提高铸型的吸热能力 和导热性能等来实现。但利用提高冷却速度增大过冷 度来细化晶粒往往只适用于小件和薄件,对大件就难 以办到。
三种控制晶粒大小的方法
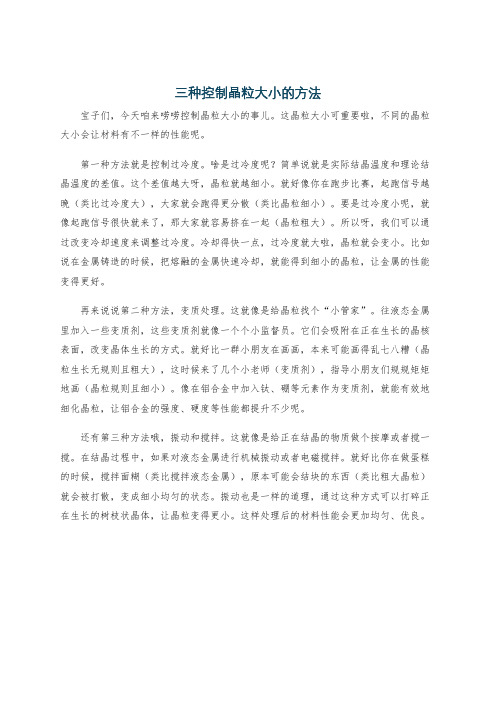
三种控制晶粒大小的方法宝子们,今天咱来唠唠控制晶粒大小的事儿。
这晶粒大小可重要啦,不同的晶粒大小会让材料有不一样的性能呢。
第一种方法就是控制过冷度。
啥是过冷度呢?简单说就是实际结晶温度和理论结晶温度的差值。
这个差值越大呀,晶粒就越细小。
就好像你在跑步比赛,起跑信号越晚(类比过冷度大),大家就会跑得更分散(类比晶粒细小)。
要是过冷度小呢,就像起跑信号很快就来了,那大家就容易挤在一起(晶粒粗大)。
所以呀,我们可以通过改变冷却速度来调整过冷度。
冷却得快一点,过冷度就大啦,晶粒就会变小。
比如说在金属铸造的时候,把熔融的金属快速冷却,就能得到细小的晶粒,让金属的性能变得更好。
再来说说第二种方法,变质处理。
这就像是给晶粒找个“小管家”。
往液态金属里加入一些变质剂,这些变质剂就像一个个小监督员。
它们会吸附在正在生长的晶核表面,改变晶体生长的方式。
就好比一群小朋友在画画,本来可能画得乱七八糟(晶粒生长无规则且粗大),这时候来了几个小老师(变质剂),指导小朋友们规规矩矩地画(晶粒规则且细小)。
像在铝合金中加入钛、硼等元素作为变质剂,就能有效地细化晶粒,让铝合金的强度、硬度等性能都提升不少呢。
还有第三种方法哦,振动和搅拌。
这就像是给正在结晶的物质做个按摩或者搅一搅。
在结晶过程中,如果对液态金属进行机械振动或者电磁搅拌。
就好比你在做蛋糕的时候,搅拌面糊(类比搅拌液态金属),原本可能会结块的东西(类比粗大晶粒)就会被打散,变成细小均匀的状态。
振动也是一样的道理,通过这种方式可以打碎正在生长的树枝状晶体,让晶粒变得更小。
这样处理后的材料性能会更加均匀、优良。
961材料科学基础答案

1.为什么室温下金属晶粒越细强度,硬度越高,塑性韧性也越好?答:金属晶粒越细,晶界面积越大,位错障碍越多,需要协调的具有不同位向的晶粒越多,金属塑性变形的抗力越高,从而导致金属强度和硬度越高。
金属的晶粒越细,单位体积内晶粒数目越多,同时参与变形的晶粒数目也越多,变形越均匀,推迟了裂纹的形成和扩展,使得在断裂前发生较大的塑性变形。
在强度和塑性同时增加的情况下,金属在断裂前消耗的功增大,因而其韧性也比较好。
因此,金属的晶粒越细,其塑性和韧性也越好。
2.冷塑性变形金属产生加工硬化的原因?随变形量增加,空密度增加。
④由于晶粒由有利位向而发生几何硬化,因此使变形抗力增加。
随变形量增加,亚结构细化,亚晶界对位错运动有阻碍作用。
答:①晶体内部存在位错源,变形时发生了位错增值,随变形量增加,位错密度增加。
由于位错之间的交互作用,使变形抗力增加。
3.某厂用冷拉钢丝绳吊运出炉热处理工件去淬火,钢丝绳的承载能力远超过工件的质量,但在工件的运送过程中钢丝绳发生断裂,试分析其原因?答:冷拉钢丝绳是利用热加工硬化效应提高其强度的,在这种状态下的钢丝中晶体缺陷密度增大,强度增加,处于加工硬化状态。
在淬火的温度下保温,钢丝将发生回复、再结晶和晶粒长大过程,组织和结构恢复软化状态。
在这一系列变化中,冷拉钢丝的加工硬化效果将消失,强度下降,在再次起吊时,钢丝将被拉长,发生塑性变形,横截面积减小,强度将比保温前低,所以发生断裂。
4细化晶粒方法1.在浇注过程中:1)增大过冷度;2)加入变质剂;3)进行搅拌和振动等。
2. 在热轧或锻造过程中:1)控制变形度;2)控制热轧或锻造温度。
3. 在热处理过程中:控制加热和冷却工艺参数利用相变重结晶来细化晶粒。
4. 对冷变形后退火态使用的合金:1)控制变形度;2)控制再结晶退火温度和时间5、试说明滑移,攀移及交滑移的条件,过程和结果,并阐述如何确定位错滑移运动的方向。
解答:滑移:切应力作用、切应力大于临界分切应力;台阶攀移:纯刃位错、正应力、热激活原子扩散;多余半原子面的扩大与缩小交滑移:纯螺位错、相交位错线的多个滑移面;位错增殖位错滑移运动的方向,外力方向与b一致时从已滑移区→未滑移区。
冷变形度与再结晶退火后晶粒大小的关系_概述说明

冷变形度与再结晶退火后晶粒大小的关系概述说明1. 引言1.1 概述本文旨在研究冷变形度与再结晶退火后晶粒大小之间的关系。
冷变形度是指金属材料在室温下受到外力作用导致其形状和尺寸发生改变的程度。
而晶粒大小则是指金属材料中晶界之间的距离以及各个晶粒的尺寸。
通过对冷变形度与晶粒大小之间的相关性进行研究,我们可以深入理解冷加工过程对材料微观结构的影响机制。
同时,了解再结晶退火对晶粒大小的影响机理和规律也具有重要意义。
这些研究结果有助于提高材料制备、工艺参数选择以及材料性能优化等方面的实践应用。
1.2 文章结构本文将按照以下结构展开:引言部分将介绍文章的背景和目标;接着在第二部分,我们将详细探讨冷变形度的定义及其影响因素,以及冷变形度与晶粒大小之间的相关性研究;第三部分将介绍实验方法和结果分析,包括实验设计、样品制备、冷变形度测量方法和数据收集,以及再结晶退火实验及晶粒大小测量方法;在第四部分,我们将对结果进行分析与讨论,并进一步探讨影响冷变形度和再结晶退火后晶粒大小的其他因素;最后一部分是文章的结论与展望,总结主要研究结果,并提出未来进一步研究的方向。
1.3 目的本文的目的旨在通过实验和理论分析,探索冷变形度与再结晶退火后晶粒大小之间的关系。
具体而言,我们将回答以下几个问题:1) 冷变形度如何定义?有哪些主要影响因素?2) 冷变形度与晶粒大小之间是否存在相关性?如果存在,其相关性如何?3) 再结晶退火对晶粒大小的影响机理是什么?4) 除了冷变形度和再结晶退火外,还有哪些因素可能会影响到材料的晶粒大小?通过解答这些问题,我们希望能够深入了解冷加工过程对材料微观结构的影响规律,并且为进一步优化金属材料制备和处理工艺提供科学依据和理论支持。
2. 冷变形度与再结晶退火后晶粒大小的关系2.1 冷变形度的定义和影响因素冷变形度是指在室温下,材料在受到外力作用下所发生的塑性变形程度。
冷变形度一般通过冷加工量来表示,可以使用应变量、应力量或者压缩率等不同参数进行描述。
- 1、下载文档前请自行甄别文档内容的完整性,平台不提供额外的编辑、内容补充、找答案等附加服务。
- 2、"仅部分预览"的文档,不可在线预览部分如存在完整性等问题,可反馈申请退款(可完整预览的文档不适用该条件!)。
- 3、如文档侵犯您的权益,请联系客服反馈,我们会尽快为您处理(人工客服工作时间:9:00-18:30)。
“晶粒大小的控制”部分结束! 请转入:
“金属的同素异构转变” 金属的同素异构转变”
Байду номын сангаас
3.3 晶粒大小的控制 一、晶粒度及其对金属性能的影响 1.晶粒度 . ① 晶粒度表示晶粒大小,由平面截面单位面积内所包含晶粒 个数来表示; ② 晶粒度级别越高,晶粒越细; ③ 也可用晶粒平均直径来表示晶粒的大小。 ④ YB27-64中对结构钢规定了八级晶粒度标准。 ⑤ 其它金属也有各自的晶粒度标准。
三、晶粒度的控制 可用以下方法予以控制: 1.控制过冷度 . 铸造浇铸时降低浇铸温度,用金属型、石墨型代替砂型等 增加T。 2.变质处理 . 在金属浇铸前向液态金属内加变质剂(形核剂)促进大量 非自发形核,细化晶粒。 3.振动、搅拌 .振动、 对即将凝固的金属进行振动或搅拌,一方面输入能量促使 形核,另一方面使成长中的枝晶破碎,使晶核数目增加,细化 晶粒。
2.晶粒度对金属性能的影响 . 晶粒度对力学性能的影响如图所示。 分析: 分析: ① 晶粒越细,常温强度越高,塑性 韧性有所改善。 ② 并非任何情况下都希望得到细晶 粒,例如硅钢片、高温加热电阻 材料等。
二、影响晶粒度的因素 1.形核率N: .形核率 : 指单位时间单位体积内形成晶核的数目。 2.长大速度 : .长大速度G: 指单位时间内生长的长度。 3.N、G与T的关系 . 、 与 的关系 分析: 分析 晶粒大小取决于N和G;其 比值N/G越大,晶粒越小。