ZCS液体动压轴承实验指导书M
液体动压轴承试验
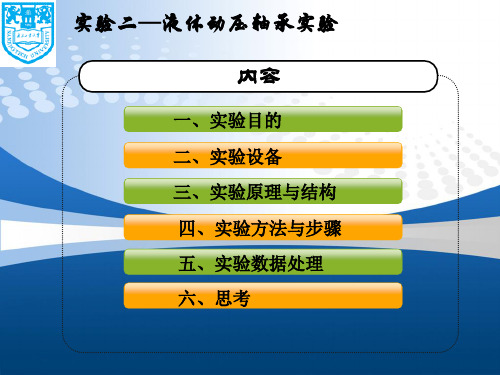
Page 6
实验二—液体动压轴承实验
四、实验方法与步骤
油膜压 力分布 测定
步骤分解
Page 7
轴承摩擦 特性曲线 的确定
PPT大宝库【】
实验二—液体动压轴承实验
(1) 油膜压力分布的测定
开启油泵,调节溢流阀,使加载油腔 压力在0.2Mpa以下
二、实验设备
•滑动轴承实验台
1-轴承箱 2-供油压力表 3、4-溢流 阀 5-加载油腔压力表 6-液压箱 7变速箱 8-调速电机控制器 9-底座 10-油泵 电机开关 11-总开关 12-调速电机
Page 3
PPT大宝库【】
实验二—液体动压轴承实验
三、实验原理与结构
1. 静压加载 当输送压力油到加载板的油腔时,轴承即获得载荷,轴 承载荷为:
正行程 反行程 正行程 反行程 正行程 反行程 正行程 反行程
0g
灵敏度
200g
400g
600g
800g
线性度
迟滞
重复性
精度
1000g
实验二—液体动压轴承实验
表3半桥邻臂实验记录
受力方式图
电桥接线图
半桥邻臂
计算公式与结论
Page 16
次 数
1 2 3 平均值 结果
加载(g) 电压(mv)
正行程 反行程 正行程 反行程 正行程 反行程 正行程 反行程
加载荷,调节溢流阀使得 p0=0.2Mpa,并计算此时载荷F,待 各压力表稳定后,记录压力表的数值
Page 9
实验二—液体动压轴承实验
(1) 油膜压力分布的测定
再将加载压力调至P0=0.4Mpa,计 算此时载荷F待压力表稳定后记录压
液体动压润滑向心滑动轴承实验

3’
4’
5’
2’
F
3
45
6’
6
2 1’
1
7 7’
端泄影响系数
Pm
2’ 1’
3’ 4’
5’ 6’ 7’
12 3
4 5 67
七、实验报告要求
数据记录
压力表号 p1
p2
p3
p4
p5
p6
p7
p8 (轴向)
压力
江苏大学工业中心
七、实验报告要求
绘制油膜的轴向和周向压力分布曲线
3’
µl
=
0.001 m mm
5’
江苏大学工业中心
四、实验设备
动力装置 油压测试装置
加载装置
1-直流电动机 2-三角带 3-传感器 4-螺旋加载杆 5-弹簧片 6-测力计(百分表) 7-压力表(径向7只,轴向一只) 8-主轴瓦 9-主轴 10-主轴箱
江苏大学工业中心
五、实验步骤
实验条件:W=70kgf,n=500r/min。 1、打开电源。 2、将转速调至500r/min左右。 3、加载,外载荷为70Kg.f。 4、等待油压表稳定后读出P1-P8的数据,记录在表格中。
稳定后再进行数据记录。
江苏大学工业中心
分组实验
2’
F
3
4 5
6’
µP
MPa
= 0.01
mm
4’
8’
8’
2
1’ 1 20o
6 7’ 7
30o
30o
0
0
B/4
d
B/2
B
n
周向压力分布曲线
轴向压力分布曲线
江苏大学工业中心
七、实验报告要求
液体动静压轴承系统 使用说明书
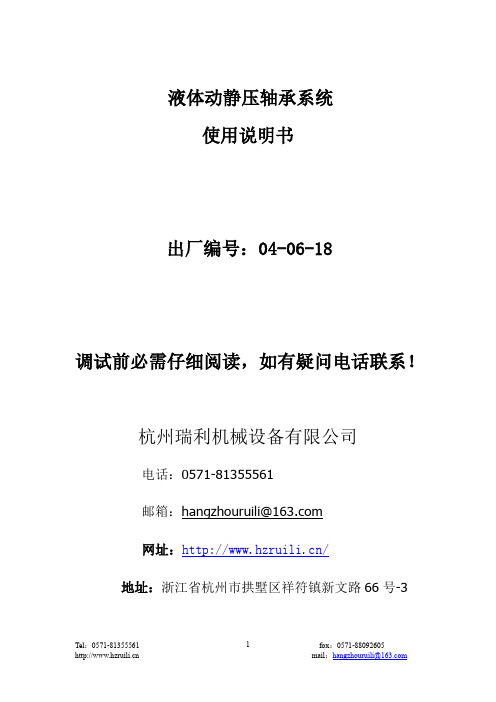
液体动静压轴承系统使用说明书出厂编号:04-06-18调试前必需仔细阅读,如有疑问电话联系!杭州瑞利机械设备有限公司电话:邮箱:网址:/地址:浙江省杭州市拱墅区祥符镇新文路66号-3动静压轴承主轴安装调试工艺规程装机调试必读动静压主轴安装调试工艺规程摘要:〈1〉开箱检查所有零部件,观察在运输过程中有无损伤。
〈2〉把磨头装上机床,注意在往机床上装的过程中,不要碰撞机床主轴。
〈3〉从泵站加油口处加入2#主轴油约110升到油标的四分之三,加油时一定要三层绸子布过滤。
注意:一定要2#主轴油,不能用别的代替。
〈4〉把泵站电机接入机床总开关,即机床总开关一开,泵站电机就工作。
检查泵站电机转向是否顺时针转动。
把高压进油软管插在加油口内,泵站工作15~20分钟,油路自循环,保证泵站出油清洁。
5〉把泵站上的压力继电器接在主轴电机的控制线路上,即泵站供油压力〉13kg时,主轴电机可以启动工作;泵站压力〈13kg时主轴电机不能启动。
这样做的目的是为了保护动静压主轴正常使用过程中不受损伤。
〈6〉把泵站上的高压进油软管接到主轴上的进油接头上。
注意:此步工序极为重要,一定要仔细认真,在接接头时千万别进入赃物。
因为这时如果进入赃物是不能出来的。
这样就影响了动静压主轴的正常工作,甚至抱轴!〈7〉把回油管两端分别接在主轴和泵站回油管嘴上。
〈8〉打开机床总开关,泵站工作,通过溢流阀调压,把泵站压力调整在 1.8MPa∽1.9MPa之间。
〈9〉观察主轴上的压力表,这时主轴处于静压状态。
静压应该是:1.7 MPa∽ 1.8 MPa之间。
用手轻轻转动主轴(有橡皮圈的除外),没有任何摩擦感觉,也有自转的可能。
〈10〉检查主轴电机转向是否和磨头一样,在不确定的情况下检查;如上有皮带采用点动,转向一定要正确。
〈11〉检查压力继电器的工作压力是否正常。
即把泵站压力调小到1.3MPa以下,启动主轴电机应不能启动。
把泵站压力调回1.8MPa∽1.9MPa时,磨头电机应能启动。
液体动压轴承实验2

液体动压轴承实验一、实验目的了解轴承油膜承载现象及其参数对轴承性能的影响,掌握油压及摩擦系数测试方法,加深对液体动压润滑原理的认识。
二、实验要求1、测定并绘出轴承油膜压力周向分布曲线及轴向分布曲线,并求出轴承的承载量。
2、计算实测端泄对轴承压力分布的影响系数k 值。
看其是否符合油膜压力沿抛物线分布规律。
3、测定轴承单位压力、滑动速度、润滑油粘度与摩擦系数之间的关系,绘制出轴承摩擦特性曲线。
三、试验台简介液体动压轴承试验台可用来进行油膜压力分布及轴承摩擦特性曲线的测定。
加载方法采用静压油垫。
调速方式采用 JZT 型调速电机,并配以变速箱,可实现 20~580r/min 无级变速,主轴转速可根据控制器表盘转速读数直接得出。
1、试验台主要技术参数(1)试验轴承参数轴颈直径d = 60mm。
轴颈有效长度l = 120mm直径间隙 0.07表面粗糙度1.6 ∇轴承材料ZQSn6-6-3(铸锡青铜)轴承自重G=80N(包括压力表及平衡锤等)(2)加载范围 3000N(3)加载油腔水平投影面积 188.5cm2(4)测力杆上测力点与轴承中心偏移距离 17mm(5)转速范围20~5800r/min(6)主电机功率0.375KW2、试验台总体布置图1 为试验台总体布置,图中 1 为试验轴承箱,由联轴器与变速箱 7 相联,6为液压箱,装于底座 9 内部,12 为调速电机,8 为调速电机控制器,5 为加载油腔压力表,2 为轴承供油压力表。
油泵电机开关为 10,主电机开关为 11,总开关位于试验台正面。
图 1 试验台总体布置图1-实验轴承箱 2-轴承供油压力表 3-减压阀 4-溢流阀 5-加载油腔压力表 6-液压箱7-变速箱8-调速电机控制器9-底座10-油泵电机开关11-主电机开关12-调速电机13-三角带传动装置3、试验轴承箱图 2 为试验轴承箱,图中 2 为主轴,由两只 P5 级滚动轴承支承。
6 为试验轴承,空套在主轴上,轴承内径d = 60mm,有效长度l= 120mm,在中间横断面,即有效长度 1/2 处的断面上沿周向开有七个测压孔,在 120º范围内均匀分布,距中间断面 1/4 处,即距周向测压孔15mm 处在铅直方向还开有另一个测压孔(即轴向测压孔),图中 1 表示七只压力表分别与七个周向测压孔相联,8 为一只与轴向测压孔相联的压力表,3 为加载盖板,固定在箱体上,加载油腔在水平面上的投影面积为188.5cm2.轴承外圆左侧装有测杆4、环5装在测杆端部,其与轴承中心距离为 78 mm。
动压滑动轴承实验指导书

动压滑动轴承实验指导书一、实验学时本实验2学时。
二、实验目的1. 观察油膜的形成与破裂现象、分析影响动压滑动轴承油膜承载能力的主要因素;2. 测量轴承周向及轴向的油膜压力、绘制其油膜压力分布曲线;3. 测定轴承的摩擦力、绘制轴承特性(λ−f )曲线;4. 掌握动压滑动轴承试验机的工作原理及其参数测试方法。
(1) 油膜压力(周向和轴向)的测量; (2) 转速的测量;(3) 摩擦力及摩擦系数的测量;三、实验机的构造及参数测试原理直流电机 2-V 形带 3-箱体 4-压力传感器 5-轴瓦 6-轴7-加载螺杆8-测力杆 9-测力传感器 10-载荷传感器 11-操作面板 图1 1.传动装置直流电机1通过V 带2驱动轴6旋转。
轴6由两个滚动轴承支承在箱体3上,其转速由面板11上的电位器进行无级调速。
本实验机的转速范围3~375转/分,转速由数码管显示。
2.加载方式由加载螺杆7和载荷传感器10组成加载装置,转动螺杆7可改变外加载荷的大小。
载荷传感器的信号经放大和A/D 转换后由数码管显示其载荷数值。
加载范围0~80㎏,不允许超过100㎏。
3. 油膜压力的测量在轴瓦5中间截面120°的承载区内(见图2左图)钻有七个均布的小孔,分别与七只压力传感器4接通,用来测量径向油膜压力。
距正中小孔的B/4轴承有效长度处,另钻一个小孔连接第八只压力传感器,用来测量轴向压力。
图2压力传感器的信号经放大、A/D 转换分别由数码管显示轴承径向油膜压力和周向油膜压力。
4. 摩擦系数的测量在轴瓦外圆的后端装有测力杆8(见图1),测力杆紧靠测力传感器9,轴旋转后,轴承间的摩擦力矩应由力臂作用于测力传感器所产生的摆动力矩相平衡。
即302F 2M L Fc D L Fc L F D F C M ⋅=⋅=⋅=⋅故 摩擦系数(3)式中:F — 轴承外载荷 (N) F=外加载荷 + 轴承自重=750 N 30FL Fc F f ⋅==F M L -力臂长度 (mm ) F M — 轴承的摩擦力 (N) F C — 测力传感器读数四、实验数据处理及绘制有关曲线为消除载荷对机械系统变形引起测量的误差,通常在载荷不变的情况下,分级改变转速,测量各级转速下有关参数,然后进行计算处理和绘制有关曲线。
实验7 液体动压滑动轴承油膜压力与摩擦仿真及测试分析

思考题
1. 动压滑动轴承的油膜压力大小与实验 中那些因素有关? 2. 加载载荷对最小油膜厚度有何影响? 3. f—μ 曲线中A点及μ 0点的意义。 第一次μ 0=?第二次μ 0= ?。 改变加载载荷和电机转速对μ 0的影响? 4. 润滑油温度如有变化将会对动压滑动 轴承的油膜压力的变化产生什么影响?
实验7 液体动压滑动轴承油膜压 力与摩擦仿真及测试分析
7.1 实验目的
通过在 HSB 型试验台上,对液体动压 轴承进行径向和轴向油膜压力分布及大小的 测量和仿真,对摩擦特性曲线进行测定及仿 真,了解影响液体动压滑动轴承油膜建立及 影响油膜大小各项因素之间的关系。
7.2 实验原理
利用轴承与轴颈配合面之间形成的楔形间
轴颈与轴承中心的连线上,我们把外载荷作 用线与轴颈和轴承中心连线所形成的夹角称 为偏位角。(见下页 )
液体动压润滑油膜形成过程及油膜压力分布
动压油膜形成
由于实验台的外载荷是加在轴瓦上,故 动压油膜形成如上图示。
7.4 动压油膜建立的判断
液体动压润滑是否建立,可通过在HS-B试验 台上做摩擦特征曲线,简称f–u 曲线来判断。
F P dB
F d B S
— 外载荷(N) — 轴颈直径(mm) — 轴承有效工作长度(mm) = d × B —有效工作面积(mm)
7.5 油膜压力测量、分析
1. 动压润滑压力油膜
径 向 压 力 油 膜 示 意 平 均 压 力 示 意 图
轴向压力油膜示意图
径向滑动轴承油 膜压力分布曲线
2.油膜压力分析
固体摩擦区 液体摩擦区
摩擦特征曲线图
7.4 动压油膜建立的判断
固体摩擦区 液体摩擦区
摩擦特征曲线图中: f — 轴颈与轴承之间的摩擦系数 0 — 轴承特性系数 A — 临界点(非液体润滑向液体润滑转变) — 临界特性系数
ZCS-Ⅰ液体动压轴承实验指导书MX

液体动压轴承实验一、实验目的该实验台用于机械设计中液体动压滑动轴承实验。
主要利用它来观察滑动轴承的结构、测量其径向油膜压力分布、测定其摩擦特征曲线。
1、观察滑动轴承的动压油膜形成过程与现象。
2、通过实验,绘出滑动轴承的特性曲线。
3、了解摩擦系数、转速等数据的测量方法。
4、通过实验数据处理,绘制出滑动轴承径向油膜压力分布曲线与承载量曲线。
二、实验系统组成(一)实验系统组成图1 滑动轴承实验系统框图轴承实验系统框图如图1所示,它由以下设备组成:1、ZCS—I液体动压轴承实验台——轴承实验台的机械结构2、油压表——共7个,用于测量轴瓦上径向油膜压力分布值3、工作载荷传感器——为应变力传感器、测量外加载荷值4、摩擦力矩传感器——为应变力传感器、测量在油膜粘力作用下轴与轴瓦间产生的磨擦力矩5、转速传感器——为霍尔磁电式传感器、测量主轴转速6、XC—I液体动压轴承实验仪——以单片微机为主体、完成对工作载荷传感器,磨擦力矩传感器及转速传感器信号采集,处理并将处理结果由LED数码管显示出来。
(二)轴承实验台结构特点实验台结构如图2所示该试验台主轴7由两高精度的单列向心球轴承支承。
直流电机1通过三角带2传动主轴7 ,主轴顺时针转动.主轴上装有精密加工的轴瓦5由装在底座上的无级调速器12实现主轴的无级变速,轴的转速由装在实验台上的霍尔转速传感器测出并显示。
主轴瓦5外圆被加载装置(末画)压住,旋转加载杆即可方便地对轴瓦加载,加载力大小由工作载荷传感器6测出,由测试仪面板上显示。
主轴瓦上还装有测力杆L,在主轴回转过程中,主轴与主轴瓦之间的磨擦力矩由磨擦力矩传感器测出,并在测试仪面板上显示,由此算出磨擦系数。
主轴瓦前端装有7只测径向压力的油压表4,油的进口在轴瓦的1/2处。
由油压表可读出轴与轴瓦之间径向平面内相应点的油膜压力,由此可绘制出径向油膜压力分布曲线。
图2 实验台结构示意图1、直流电机2、三角带3、磨擦力矩传感器4、油压表5、轴瓦6、工作载荷传感器7、主轴9、油槽10、底座12、调速旋钮(三)液体动压轴承实验仪1 2 3 4图3 轴承实验仪正面图1、转速显示2、工作载荷显示3、摩擦力矩显示4、摩擦力矩清零5、电源开关图 4 轴承实验仪背面图1、电源座2、摩擦力矩传感器输入接口3、工作载荷传感器输入接口4、转速传感器输入接口5、工作载荷传感器清零按钮如图所示,实验仪操作部分主要集中在仪器正面的面板上,在实验仪的后面板上设有磨擦力矩输入接口,载荷力输入接口,转速传感器输入接口等。
液体动压径向滑动轴承实验指导书

液体动压径向滑动轴承实验指导书一、实验内容与目的:1.观察径向滑动轴承的摩擦现象,加深对概念的理解; 2.测绘径向滑动轴承的摩擦特性曲线,掌握测绘方法;3.测绘径向滑动轴承油膜压力曲线,求油膜承载能力。
了解复杂问题的简化处理方法。
二、实验设备的结构与工作原理:本实验有二类(二种型号)设备,它们的结构示意图如图1和图2所示:它们包括以下向个部份:可以证明,抛物面与轴直径截面所围体积与以m P 值为高的长方体的体积之比32=KdB m 。
如果我们测量是精确的;那么我们计算结果摩擦状态指示装置的原理是用一个与轴和轴瓦相连的直流电路上的灯泡来指示的。
当轴当轴在很低的转速下转动时,轴将润滑油带入轴和轴瓦之间收敛性间隙内,但由于此时的油膜厚度很薄,轴与轴瓦之间部分微观不平的凸峰处仍在接触,当轴的转速达到一定值时,轴与轴瓦之间形成的压力油膜厚度完全分开两表面之间微观不平的凸峰,油膜守全将轴与轴瓦隔开,灯泡就不亮了。
这个指示装置还有一个作用就是当指示灯亮时不能加载,以免出现油温过高烧瓦等现三、实验方法与步骤:一)操作前检查:1.调速旋钮是否逆时针旋到底;2.将百分表调零;3.察看油标,检查润滑油油位是否到位;4.使加载系统处于未加载状态;二)实验操作(在做完以上准备工作后):1.观察润滑现象:接通电源,将调速旋钮右旋将使在一定转速(300转/分左右)下旋转,再回调至200转/分左右,然后再慢慢的调到转速为零。
注意观察各种摩擦状态。
2.摩擦系数测量:①接通电源,旋转调速旋钮使轴在一定转速(300转/分)下旋转。
②用加、减载荷方法记录在不同载荷情况下百分表读数;然后再在一固定载荷(HS-A型加到40kg;HZ型加三块砝码)下,用加、减转速方法记录百分表读数。
这样就得到摩擦系数各点值。
3.油膜承载压力测量:①调节调速旋钮,将轴转速达到各试验机的最高转速(500转/分以内);②加载使轴承受一定载荷(HS-A型100kg;HZ型六块砝码),待压力表值稳定后记录各块压力表的值。
- 1、下载文档前请自行甄别文档内容的完整性,平台不提供额外的编辑、内容补充、找答案等附加服务。
- 2、"仅部分预览"的文档,不可在线预览部分如存在完整性等问题,可反馈申请退款(可完整预览的文档不适用该条件!)。
- 3、如文档侵犯您的权益,请联系客服反馈,我们会尽快为您处理(人工客服工作时间:9:00-18:30)。
液体动压轴承实验一、实验目的该实验台用于机械设计中液体动压滑动轴承实验。
主要利用它来观察滑动轴承的结构、测量其径向油膜压力分布、测定其摩擦特征曲线。
1、观察滑动轴承的动压油膜形成过程与现象。
2、通过实验,绘出滑动轴承的特性曲线。
3、了解摩擦系数、转速等数据的测量方法。
4、通过实验数据处理,绘制出滑动轴承径向油膜压力分布曲线与承载量曲线。
二、实验系统组成(一)实验系统组成图1 滑动轴承实验系统框图轴承实验系统框图如图1所示,它由以下设备组成:1、ZCS—I液体动压轴承实验台——轴承实验台的机械结构2、油压表——共7个,用于测量轴瓦上径向油膜压力分布值3、工作载荷传感器——为应变力传感器、测量外加载荷值4、摩擦力矩传感器——为应变力传感器、测量在油膜粘力作用下轴与轴瓦间产生的磨擦力矩5、转速传感器——为霍尔磁电式传感器、测量主轴转速6、XC—I液体动压轴承实验仪——以单片微机为主体、完成对工作载荷传感器,磨擦力矩传感器及转速传感器信号采集,处理并将处理结果由LED数码管显示出来。
(二)轴承实验台结构特点实验台结构如图2所示该试验台主轴7由两高精度的单列向心球轴承支承。
直流电机1通过三角带2传动主轴7 ,主轴顺时针转动.主轴上装有精密加工的轴瓦5由装在底座上的无级调速器12实现主轴的无级变速,轴的转速由装在实验台上的霍尔转速传感器测出并显示。
主轴瓦5外圆被加载装置(末画)压住,旋转加载杆即可方便地对轴瓦加载,加载力大小由工作载荷传感器6测出,由测试仪面板上显示。
主轴瓦上还装有测力杆L,在主轴回转过程中,主轴与主轴瓦之间的磨擦力矩由磨擦力矩传感器测出,并在测试仪面板上显示,由此算出磨擦系数。
主轴瓦前端装有7只测径向压力的油压表4,油的进口在轴瓦的1/2处。
由油压表可读出轴与轴瓦之间径向平面内相应点的油膜压力,由此可绘制出径向油膜压力分布曲线。
1 2 345图2 实验台结构示意图1、直流电机2、三角带3、磨擦力矩传感器4、油压表5、轴 瓦6、工作载荷传感器7、主 轴 9、油 槽 10、底 座 12、调速旋钮(三)液体动压轴承实验仪图3 轴承实验仪正面图XC-I 液体动压轴承实验仪摩擦力矩(Nm )转速(r/m ) 工作载荷(N ) 清零电源1、转速显示2、工作载荷显示3、摩擦力矩显示4、摩擦力矩清零5、电源开关图 4 轴承实验仪背面图1、电源座2、摩擦力矩传感器输入接口3、工作载荷传感器输入接口4、转速传感器输入接口5、工作载荷传感器清零按钮如图所示,实验仪操作部分主要集中在仪器正面的面板上,在实验仪的后面板上设有磨擦力矩输入接口,载荷力输入接口,转速传感器输入接口等。
实验仪箱体内附设有单片机,承担检测,数据处理,信息记忆,自动数字显示等功能。
三、实验原理及测试内容1、实验原理滑动轴承形成动压润滑油膜的过程如图5(a)所示。
当轴静止时,轴承孔与轴颈直接接触,如图5(a)所示。
径向间隙△使轴颈与轴承的配合面之间形成楔形间隙,其间充满润滑油。
由于润滑油具有粘性而附着于零件表面的特性,因而当轴颈回转时,依靠附着在轴颈上的油层带动润滑油挤入楔形间隙。
因为通过楔形间隙的润滑油质量不变(流体连续运动原理),而楔形中的间隙截面逐渐变小,润滑油分子间相互挤压,从而油层中必然产生流体动压力,它力图挤开配合面,达到支承外载荷的目的。
当各种参数协调时,液体动压力能保证轴的中心与轴瓦中心有一偏心距e。
最小油膜厚度n存在于轴颈m i n与轴承孔的中心连线上。
液体动压力的分布如图5(c)所示。
图5 液体动压润滑膜形成的过程液体动压润滑能否建立,通常用f-λ曲线来判别。
图6中f为轴颈与轴承之间的摩擦系数,λ为轴承特性系数,它与轴的转速n ,润滑油动力粘度η、润滑油压强p之间的关系为:λ为=ηn/p式中,n为轴颈转速;η为润滑油动力粘度;p为单位面积载荷。
Frd;Nmm2。
Fr是轴承承受的径向载荷;d是轴承即式中,p= l1的孔径,本实验中,d= 70mm;l是轴承有效工作长度,对本实验轴1=125mm。
承,取l1如图6,当轴颈开始转动时,速度极低,这时轴颈和轴承主要是金属相接触,产生的摩擦为金属间的直接摩擦,摩擦阻力最大。
随着转速的增大,轴颈表面的圆周速度增大,带入油楔内的油量也逐渐加多,则金属接触面被润滑油分隔开的面积也逐渐加大,因而摩擦阻力也就逐渐减小。
当速度增加到一定大小之后,已能带入足够把金属接触面分开的油量,油层内的压力已建立到能支承轴颈上外载荷程度,轴承就开始按照液体摩擦状态工作。
此时,由于轴承内的摩擦阻力仅为液体的内阻力,故摩擦系数达到最小值,如图6摩擦特性曲线上A点。
当轴颈转速进一步加大时,轴颈表面的速度亦进一步增大,使油层间的相对速度增大,故液体的内摩擦也就增大,轴承的摩擦系数也随之上升。
图6 摩擦特性曲线(Stribeck曲线)特性曲线上的A点是轴承由混合润滑向流体润滑转变的临界点。
此点的摩擦系数最小,此点相对应的轴承特性系数称为临界特性系数,以λ。
表示。
A点之右,即λ>λ。
区域为流体润滑状态;A 点之左,即λ<λ。
区域称为边界润滑状态。
根据不同条件所测得的f和λ之值,我们就可以作出f-λ曲线,用以判别轴承的润滑状态,能否实现在流体润滑状态下工作。
2、油膜压力测试实验(1)理论计算压力图7为轴承工作时轴颈的位置。
根据流体动力润滑的雷诺方程,从油膜起始角 1 到任意角的压力为:P=6η(1-1)式中:P ——任意位置的压力单位:Paη——油膜粘度ω——主轴转速单位:rad/s——相对间隙=其中D为轴承孔直径,d为轴径直径——油压任意角单位:度0——最大压力处极角单位:度1——油膜起始角单位:度——偏心率= =其中e为偏心距在雷诺公式中,油膜起始角1、最大压力处极角0由实验台实验测试得到。
另一变化参数:偏心率的变化情况,它由查表得到。
具体方法如下:对有限宽轴承,油膜的总承载能力为:F= (1-2)式中:F——承载能力,即外加载荷单位:NB——轴承宽度单位:mmCp——承载量系数,见表1图7 径向滑动轴承的油压分布由公式(1-2)可推出:Cp= (1-3)由公式(1-3)计算得承载量系数Cp后再查表可得到在不同转速、不同外加载荷下的偏心率情况。
注:若所查的参数系数超出了表中所列的,可用插入值法进行推算。
(2)实际测量压力如前图2所示,启动电机,控制主轴转速,并施加一定工作载荷,运转一定时间后轴承中形成压力油膜。
图中代号F1,F2,F3,F4,F5,F6,F7七个油压表,用于测量并显示轴瓦表面每隔22度角处的七点油膜压力值。
根据测出的各实际压力值,按一定比例绘制出油压分布曲线作出油膜实际压力分布曲线与理论分布曲线,比较两者间的差异。
3、摩擦特性实验(1)理论摩擦系数理论摩擦系数公式:f = +0.55(1-4)式中:f ——摩擦系数p ——轴承平均压力,p= 单位: Paε——随轴承宽径比而变化的系数,对于B/d<1的轴承,ε=(d/B)1.5;当B/d≥1时,ε=1;——相对间隙=由公式(1-4)可知理论摩擦系数 f的大小与油膜粘度η、转速ω和平均压力p(也即外加载荷F)有关。
在使用同一种润滑油的前提下,粘度η的变化与油膜温度有关,由于不是在长时间工作的情况下,油膜温度变化不大,因此图8 轴径圆周表面摩擦力分析在本实验系统中暂时不考虑粘度因素。
(2)测量摩擦系数如图 2 所示,在轴瓦中心引出一测力杆压在力传感器2,用以测量轴承工作时的摩擦力矩,进而换算得摩擦系数值。
对它们分析如图8:∑F* r = N*L (1)∑F=f*F (2)式中:∑F ——圆周上各切点摩擦力之和∑F=F1+F2+F3+F4+…r ——圆周半径N ——压力传感器测得的力L ——力臂F ——外加载荷力f ——摩擦系数所以实测摩擦系数公式:f= (1-5)4、轴承实验中其他重要参数在轴承实验实验中还有一些比较重要的参数概念,以下分别作一一介绍。
(1) 轴承的平均压力p (单位:MPa)p=≤ [p] (1-6)式中:F ——外加载荷,NB ——轴承宽度,mmd ——轴径直径,mm[p]——轴瓦材料许用压力,MPa ,其值可查(2) 轴承pv值(单位:MPa*m/s)轴承的发热量与其单位面积上的摩擦功耗fpv成正比(f是摩擦系数),限制pv值就是限制轴承的温升。
P v==≤ [pv] (1-7)式中:v ——轴颈圆周速度,m/s[pv]——轴承材料pv许用值,MPa*m/s,其值可查⑶最小油膜厚度hmin = r*(1-8)式中各参数说明见前。
四、实验操作步骤1、系统联接及接通电源轴承实验台在接通电源前,应先将电机调速旋扭逆时针转至“0速”位置。
将磨擦力矩传感器信号输出线,转速传感器信号输出线分别接入实验器对应接口。
松开实验台上的螺旋加载杆,打开实验台及实验仪的电源开关接通电源。
2、载荷及磨擦力矩调零保持电机不转,松开实验台上螺旋加载杆,在载荷传感器不受力的状态下按一下实验仪后板上的“复位”按钮5。
此时单片机系统采样载荷传感器,并将此值作为“零点”保存,实验台面板上工作载荷显示为“0”。
按一下实验仪面板上的“清零”键,可完成对磨擦力矩清零,此时实验仪面板上磨擦力矩显示窗口显示为“0”。
3、记录各压力表压力值(1)在松开螺旋加载杆的状态下,启动电机并慢慢将主轴转速调整到300转/分左右。
(2)慢慢转动螺旋加载杆,同时观察实验仪面板上的工作载荷显示窗口,一般应加至1800N左右。
(3)待各压力表的压力值稳定后,由左至右依次记录各压力表的压力值。
4、摩擦系数f测量当实验台运行平稳,待各压力表的压力值稳定后,从实验仪面板磨擦力矩显示窗口中读取磨擦力矩值,按前述摩擦特性实验原理,计算得到摩擦系数f。
5、关机待实验数据记录完毕后,先松开螺旋加载杆,并旋动调整电位器使电机转速为零,关闭实验台及实验仪电源。
6、绘制径向油膜压力分布曲线与承载曲线根据测出的各压力值按一定比例绘制出油压分布曲线与承载曲线,如图七的上图所示。
此图的具体画法是:沿着圆周表面从左到右画出角度分别为30、50、70、90、110、130、150 等分别得出油孔点1、2、3、4、5、6、7的位置。
通过这些点与圆心O连线,在各连线的延长线上将压力表(比例:0.1MP=5mm)测出的压力值画出压力线1—1’,2—2’,3—3’,……,7—7’。
将1’,2’,3’,……,7’各点连成光滑曲线,此曲线就是所测轴承的一个径向截面的油膜径向压力分布曲线。
为了确定轴承的承载量,用Pi sinφi(I=1、2、…、7)求得向量1—1’,2—2’,3—3’,……,7—7’在载荷方向(即y轴的投影值。
角度φi与sinφi的数值见下表)然后将Pi sinφi这些平行于y轴的向量移到直径0—8上。