无主栅太阳电池多线串接技术研究
【CN110112229A】一种无细栅的太阳能电池【专利】

(19)中华人民共和国国家知识产权局(12)发明专利申请(10)申请公布号 (43)申请公布日 (21)申请号 201910358920.3(22)申请日 2019.04.29(71)申请人 国家电投集团西安太阳能电力有限公司地址 710099 陕西省西安市航天基地东长安街589号申请人 国家电投集团西安太阳能电力有限公司西宁分公司 青海黄河上游水电开发有限责任公司 国家电投集团黄河上游水电开发有限责任公司(72)发明人 席珍珍 (74)专利代理机构 上海精晟知识产权代理有限公司 31253代理人 冯子玲(51)Int.Cl.H01L 31/0216(2014.01)H01L 31/0224(2006.01)H01L 31/04(2014.01) (54)发明名称一种无细栅的太阳能电池(57)摘要本发明的目的在于公开一种无细栅的太阳能电池,它包括硅基衬底、扩散层、减反射层、正电极及负电极,在所述扩散层与所述减反射层之间设置有石墨烯透明导电层;与现有技术相比,采用石墨烯透明导电薄膜层代替丝网印刷细栅线来收集面电流,避免了细栅对电池遮挡,有效减小面阻和遮挡效应,提高电池光电转换效率,减少了印刷工序和浆料的使用量,大幅度降低生产成本,且制作的无细栅的太阳能电池外观美观简洁,增大客户受众面,不仅可用于低成本的大批量生产,而且与新兴技术相兼容,有着巨大的发展潜力,实现本发明的目的。
权利要求书1页 说明书4页 附图2页CN 110112229 A 2019.08.09C N 110112229A权 利 要 求 书1/1页CN 110112229 A1.一种无细栅的太阳能电池,其特征在于,它包括硅基衬底、扩散层、减反射层、正电极及负电极,在所述扩散层与所述减反射层之间设置有石墨烯透明导电层。
2.如权利要求1所述的无细栅的太阳能电池,其特征在于,所述石墨烯透明导电层的厚度为10-100nm。
3.如权利要求1所述的无细栅的太阳能电池,其特征在于,所述石墨烯透明导电层的透光率大于90%。
一种以触盘代替主栅线的太阳电池正面电极栅线结构[发明专利]
![一种以触盘代替主栅线的太阳电池正面电极栅线结构[发明专利]](https://img.taocdn.com/s3/m/08e285222cc58bd63086bd76.png)
专利名称:一种以触盘代替主栅线的太阳电池正面电极栅线结构
专利类型:发明专利
发明人:岳之浩,周潘兵,黄海宾,周浪
申请号:CN201410421063.4
申请日:20140826
公开号:CN104218104A
公开日:
20141217
专利内容由知识产权出版社提供
摘要:本发明涉及硅太阳电池技术领域,特别涉及一种以触盘代替主栅线的太阳电池正面电极栅线结构,包括多条水平细栅线,所述水平细栅线均各自平行等距排布,每条水平细栅线上均等距分布着若干个触盘式电极,由于每条水平细栅线上都有多个触盘式电极,因此细栅线所收集的电流可以很好地被与串联焊带连接的触盘式电极导出,由于该发明省去了主栅线,因此可以显著节省导电银浆,从而降低太阳电池的制造成本。
申请人:南昌大学
地址:330000 江西省南昌市红谷滩新区学府大道999号
国籍:CN
代理机构:南昌洪达专利事务所
代理人:刘凌峰
更多信息请下载全文后查看。
太阳电池无主栅互联封装技术研究进展

太阳电池无主栅互联封装技术研究进展
雷楠;左燕;郭永刚;王锐;孙蛟;杨紫琪;雷鸣宇
【期刊名称】《电源技术》
【年(卷),期】2024(48)4
【摘要】采用无主栅技术降低银浆成本是降低太阳电池组件成本的一个重要方向。
主要阐述了无主栅电池组件技术的优势和发展历程,总结对比了覆膜互联、点胶互联、焊接点胶互联几种不同的无主栅电池互联封装工艺,论述了无主栅互联封装技
术引入的低温焊丝、聚合物膜新材料、无主栅电池组件的热循环可靠性及不同互联方案对无主栅电池金属化图形的要求,最后对无主栅技术面临的挑战及优化方向进
行了展望。
【总页数】10页(P612-621)
【作者】雷楠;左燕;郭永刚;王锐;孙蛟;杨紫琪;雷鸣宇
【作者单位】青海黄河上游水电开发有限责任公司西宁太阳能电力分公司;青海黄
河上游水电开发有限责任公司西安太阳能电力分公司;青海黄河上游水电开发有限
责任公司太阳能电池及组件研发实验室
【正文语种】中文
【中图分类】TM914
【相关文献】
1.太阳电池封装技术的现状与发展建议
2.非晶硅太阳电池封装材料层压技术EVA 和DNP应用与分析
3.无主棚太阳电池多线串接技术研究
4.无主栅太阳电池栅线的设计优化
5.空间太阳电池柔性封装材料与技术研究进展
因版权原因,仅展示原文概要,查看原文内容请购买。
光伏无主栅焊接

光伏无主栅焊接
光伏无主栅焊接是一种先进的太阳能电池片制造技术,它通过激光或超快激光在电池片表面形成无主栅线,以提高电池片的光电转换效率和降低生产成本。
这种技术具有以下特点:
1. 高效率:无主栅焊接技术可以提高电池片的光电转换效率,因为它可以减少电池片表面的遮光面积,增加电池片的有效受光面积,从而提高电池片的输出功率。
2. 降低成本:传统的太阳能电池片制造过程中需要使用大量的银浆作为导电材料,而无主栅焊接技术可以减少银浆的使用量,降低生产成本。
3. 提高可靠性:无主栅焊接技术可以提高电池片的可靠性,因为它可以减少电池片表面的温度分布不均匀,降低热应力,从而提高电池片的稳定性和寿命。
4. 环保:无主栅焊接技术可以减少银浆的使用量,从而减少对环境的污染。
5. 适应性强:无主栅焊接技术可以应用于不同类型的太阳能电池片,如单晶硅、多晶硅、薄膜等,具有较强的适应性。
总之,光伏无主栅焊接技术是一种具有广泛应用前景的太阳能电池片制造技术,它将有助于提高太阳能电池的性能,降低生产成本,推动太阳能产业的发展。
无主栅技术在光伏电池封装中的应用研究

无主栅技术在光伏电池封装中的应用研究1. 应用背景随着环境保护意识的增强,可再生能源的利用成为了人们关注的焦点。
太阳能作为最常见的可再生能源之一,有着广阔的应用前景。
而光伏电池作为太阳能的核心转换器件,其封装技术对于光伏发电系统的性能和寿命有着重要的影响。
传统的光伏电池封装技术中,主栅极通过铝丝与光伏电池片连接,但这种封装方式存在电阻大、光伏电池效率低、易产生热点等问题,限制了光伏电池的发展。
无主栅技术(back contact)是一种新型的光伏电池封装技术,在封装过程中,不需要使用传统的主栅极,而是直接在电池片背面制作电极,通过背面封装来提高光伏电池的性能。
这种技术的应用研究正是为了解决传统封装技术的问题,提高光伏电池的效率和可靠性。
2. 应用过程无主栅技术在光伏电池封装中的应用过程主要包括以下几个步骤:步骤1:电池片制备首先需要制备光伏电池片。
光伏电池片的材料通常是硅,可以是单晶硅、多晶硅或非晶硅。
电池片的制备工艺包括原料选取、切割、清洗、扩散、薄膜镀膜等步骤。
制备好的电池片需要具备一定的厚度和电学性能。
步骤2:背面电极制作在电池片背面制作电极是无主栅技术的核心步骤。
常用的背面电极制作方法有屏印法和激光刻蚀法。
•屏印法:利用屏印机在电池片背面涂覆电极浆料,然后通过烧结和退火等工艺,制作出电极。
这种方法简单、成本低,但电极的厚度不易控制。
•激光刻蚀法:利用激光蚀刻技术,直接在电池片背面刻蚀出电极。
这种方法可以实现较薄的电极,提高光伏电池的效率,但设备和工艺复杂。
步骤3:封装过程背面电极制作完成后,需要进行电池片的封装。
封装过程包括电池片的边框加固、玻璃固定、焊接连接等步骤。
在封装过程中,需要保证电池片与封装材料的良好结合,同时确保背面电极的外观和电性能。
步骤4:后续工艺完成封装后,还需要进行一系列的后续工艺。
这包括电池片的测试、清洗、质量检验等环节,以确保光伏电池的性能和质量达到要求。
同时,还需要进行光伏电池组件的制备,将多个光伏电池片组装成更大的光伏电池组件。
从多主栅到无主栅,晶硅电池正面电极设计如何“维新”
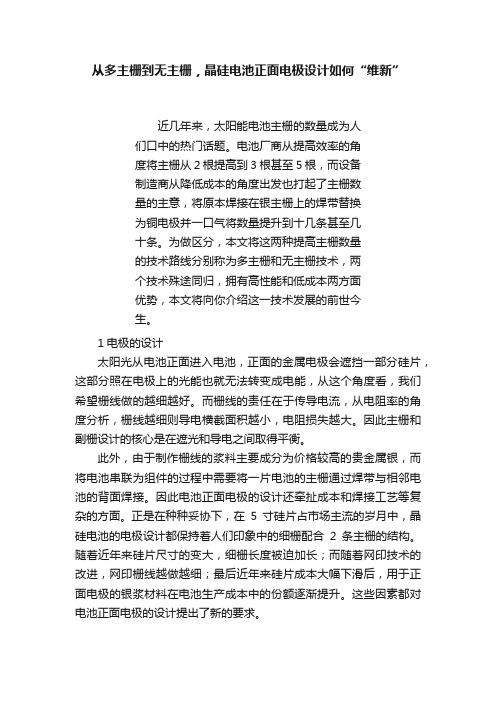
从多主栅到无主栅,晶硅电池正面电极设计如何“维新”近几年来,太阳能电池主栅的数量成为人们口中的热门话题。
电池厂商从提高效率的角度将主栅从2根提高到3根甚至5根,而设备制造商从降低成本的角度出发也打起了主栅数量的主意,将原本焊接在银主栅上的焊带替换为铜电极并一口气将数量提升到十几条甚至几十条。
为做区分,本文将这两种提高主栅数量的技术路线分别称为多主栅和无主栅技术,两个技术殊途同归,拥有高性能和低成本两方面优势,本文将向你介绍这一技术发展的前世今生。
1电极的设计太阳光从电池正面进入电池,正面的金属电极会遮挡一部分硅片,这部分照在电极上的光能也就无法转变成电能,从这个角度看,我们希望栅线做的越细越好。
而栅线的责任在于传导电流,从电阻率的角度分析,栅线越细则导电横截面积越小,电阻损失越大。
因此主栅和副栅设计的核心是在遮光和导电之间取得平衡。
此外,由于制作栅线的浆料主要成分为价格较高的贵金属银,而将电池串联为组件的过程中需要将一片电池的主栅通过焊带与相邻电池的背面焊接。
因此电池正面电极的设计还牵扯成本和焊接工艺等复杂的方面。
正是在种种妥协下,在5寸硅片占市场主流的岁月中,晶硅电池的电极设计都保持着人们印象中的细栅配合2条主栅的结构。
随着近年来硅片尺寸的变大,细栅长度被迫加长;而随着网印技术的改进,网印栅线越做越细;最后近年来硅片成本大幅下滑后,用于正面电极的银浆材料在电池生产成本中的份额逐渐提升。
这些因素都对电池正面电极的设计提出了新的要求。
2电池厂商的“维新”在上述背景下,电池厂商选择了一条“维新”式的技术升级之路解决正面电极设计的新问题。
日本的京瓷成了其中第一个吃螃蟹的制造商。
虽然京瓷2013年在全球组件供应商排行中仅排名第九,太阳能也不是京瓷的目前的主营业务,但其实京瓷早在1975就开始进入太阳能产业,并在1998年成为当时全球产量最多的太阳能制造商。
进入20世纪初,京瓷的研发人员遇到了这样一个问题,为了进一步提高太阳能电池的效率,他们尝试采用更细的主栅和细栅增加电池的有效受光面积,但由于之前介绍过的原理,随着电极变细串联电阻提高,电池的填充因子也因此降低。
晶硅电池从多主栅到无主栅的发展历程!

近几年来,太阳能电池主栅的数量成为人们口中的热门话题。
电池厂商从提高效率的角度将主栅从2根提高到3跟甚至5跟,而设备制造商从降低成本的角度出发也打起了主栅数量的主意,将原本焊接在银主栅上的焊带替换为铜电极并一口气将数量提升到十几条甚至几十条。
为做区分,本文将这两种提高主栅数量的技术路线分别称为多主栅和无主栅技术,两个技术殊途同归,拥有高性能和低成本两方面优势,本文将向你介绍这一技术发展的前世今生。
1 .电极的设计太阳光从电池正面进入电池,正面的金属电极会遮挡一部分硅片,这部分照在电极上的光能也就无法转变成电能,从这个角度看,我们希望栅线做的越细越好。
而栅线的责任在于传导电流,从电阻率的角度分析,栅线越细则导电横截面积越小,电阻损失越大。
因此主栅和副栅设计的核心是在遮光和导电之间取得平衡。
此外,由于制作栅线的浆料主要成分为价格较高的贵金属银,而将电池串联为组件的过程中需要将一片电池的主栅通过焊带与相邻电池的背面焊接。
因此电池正面电极的设计还牵扯成本和焊接工艺等复杂的方面。
正是在种种妥协下,在5寸硅片占市场主流的岁月中,晶硅电池的电极设计都保持着人们印象中的细栅配合2条主栅的结构。
随着近年来硅片尺寸的变大,细栅长度被迫加长;而随着网印技术的改进,网印栅线越做越细;最后近年来硅片成本大幅下滑后,用于正面电极的银浆材料在电池生产成本中的份额逐渐提升。
这些因素都对电池正面电极的设计提出了新的要求。
2. 电池的“维新”在上述背景下,电池厂商选择了一条“维新”式的技术升级之路解决正面电极设计的新问题。
日本的京瓷成了其中第一个吃螃蟹的制造商。
虽然京瓷2013年在全球组件供应商排行中仅排名第九,太阳能也不是京瓷的目前的主营业务,但其实京瓷早在1975就开始进入太阳能产业,并在1998年成为当时全球产量最多的太阳能制造商。
进入20世纪初,京瓷的研发人员遇到了这样一个问题,为了进一步提高太阳能电池的效率,他们尝试采用更细的主栅和细栅增加电池的有效受光面积,但由于之前介绍过的原理,随着电极变细串联电阻提高,电池的填充因子也因此降低。
太阳能发电中的光伏电池组串优化设计研究

太阳能发电中的光伏电池组串优化设计研究随着环保意识的不断提高,太阳能发电成为了广泛关注的话题。
而光伏电池组串作为太阳能发电的核心部件之一,其优化设计也成为了发电效率提升的重要手段。
一、光伏电池组串的意义光伏电池组串是太阳能发电中的重要部件,其主要功能是将太阳能转换为直流电能。
在太阳能光照下,光伏电池会产生电流,并经过组串连接后输出电压和电流。
而组串中电池的数量、排列方式、连接方式等都对发电效率产生着重要影响。
二、组串优化设计的研究方法为了提高光伏电池组串的发电效率,需要进行优化设计。
其研究方法可以从以下几个方面着手:1. 组串电池的选择。
不同的电池具有不同的特性和性能,选择合适的电池对组串的发电效率至关重要。
在挑选电池时需要考虑多个方面因素,如电池材质、工作温度、光谱响应等。
2. 电池的布局方式。
电池的布局方式包括电池的数量、排列方式等。
在电池数量越多、面积越大的情况下,组串的发电效率会越高。
而电池的排列方式也会影响发电效率,如竖向排列和横向排列等。
3. 电池的连接方式。
电池之间的连接方式有串联和并联两种,其中串联可以增加组串的输出电压,而并联则可以增加组串的输出电流。
因此,在选择电池的连接方式时也需要考虑发电需求和电池的特性。
三、光伏电池组串优化设计案例下面以某光伏电站为例,探讨光伏电池组串优化设计的实际应用。
该光伏电站的组串采用了72个多晶硅电池片,通过串联的方式输出电压为36V,输出电流为10A。
这种组串方式的优点是输出电压高,用于支持长距离传输,且能满足大部分应用需求。
但是在日照条件不理想的情况下,该组串的发电效率会受到影响,因此需要进行优化设计。
通过增加电池片的数量,并采用横向排列的方式来增加面积,可以增加组串的输出功率,并大大提高发电效率。
同时,在太阳能资源充足的情况下,采取串联方式可以增加输出电压,满足高压电力系统的需求。
此外,还可以通过安装铝制框架来固定和保护电池,这样不仅可以延长其使用寿命,还可以保证组串的稳定性和安全性。
- 1、下载文档前请自行甄别文档内容的完整性,平台不提供额外的编辑、内容补充、找答案等附加服务。
- 2、"仅部分预览"的文档,不可在线预览部分如存在完整性等问题,可反馈申请退款(可完整预览的文档不适用该条件!)。
- 3、如文档侵犯您的权益,请联系客服反馈,我们会尽快为您处理(人工客服工作时间:9:00-18:30)。
2008年2010年2013年2015年2017年
图1 太阳电池主栅数量发展历程
收稿日期:2017-11-30
通信作者:张治(1978—),男,博士、高级工程师,主要从事太阳电池、光伏组件的研发、生产工艺设计和优化及产品电性能检测方法的研究。
yangzhenying@
电池而言,若使镀层铜丝的最大遮光宽度小于等于三主栅太阳电池的主栅总宽度(4.5 mm),当覆盖在无主栅太阳电池表面的铜丝直径为0.2 mm 根数应≤22根;当铜丝直径为0.25 mm 时,根
数应≤18根;当铜丝直径为0.3 mm 时,根数应
15根。
因此,综合考虑太阳电池主栅的总宽度、间距、功率损耗和印刷工艺的可实现性后,决定采用电池正面只印刷宽度为40 µm 、数量为90间距为1.724 mm 的副栅及覆有18根直径为的镀层铜丝的设计作为无主栅太阳电池的设
计,如图3所示。
图2 太阳电池主栅数量、宽度与总功率损失关系图1.1电池正面的遮光方面
无主栅太阳电池的电极图形若采用表1所示方案时,其正面的理论遮光率为4.573%;而在副栅的数量、宽度、间距相同的情况下,三主栅太阳电池的正面理论遮光率为5.137%。
覆有根直径为0.2 mm 铜丝的无主栅太阳电池的理论
遮光率比三主栅太阳电池的减少了10.98%。
1.2银浆耗量方面
根据无主栅太阳电池及三主栅太阳电池样片
a.正面效果图
b.背面效果图
图3 156 mm ×156 mm 单晶硅无主栅太阳电池效果图
总功率损失主栅宽度0.60.40.1
0.50.20.3
015372648910121511141316主栅数量/根
合
金
涂
层
a. 截面图
b. 局部放大图
图4 低熔点合金镀层铜丝截面图及其局部放大图
a. 未添加稀土元素
b. 添加稀土元素
图5 添加稀土元素前后的Sn-Pb-Bi合金的抗氧化性对比引起的电池碎裂,为该合金能够应用在太阳电池串接工艺中提供了有利条件。
选取光伏行业内应用广泛的4种有机薄膜,分别为EVA、PES、TPU、TPO,进行透光率测试、交联性测试和粘接强度测试,测试结果如表2所示。
由表2可知,TPO薄膜是比较理想的可用于无主栅焊带制作的有机薄膜。
将低熔点合金镀层铜丝与TPO有机薄膜复合,可得到熔化温度低于145 ℃的无主栅焊带,如图6所示。
无主栅太阳电池与无主栅焊带之间的匹配性验证
与常规太阳电池封装工艺相比,无主栅太阳电池是使用新型串焊机在100 ℃左右的条件下,将镀层铜丝与有机薄膜经过机械复合后的铜丝复合膜铺设在两片电池的正、背面,实现相邻电池的串接;串接后的电池串经过排布、叠层后,在一定的层压温度和压力下将镀锡铜丝和电池细栅
图6 无主栅焊带样品图
优化后的无主栅太阳电池正面效果图
实验使用正面只印刷细栅、背面只有铝背场、
0.2 mm的Sn-Pb-Bi合金铜丝封装的单片无主栅太阳电池片,印刷方案如图
图像相对较暗,如图8a所示;然后在保持镀层成分和铜丝直径不变的情况下,对无主栅太
a.优化前
b.优化后
图8 单片无主栅太阳电池片EL图
使用优化后的无主栅太阳电池印刷方案,采用直径为0.2 mm与0.3 mm的镀层铜丝进行单片电池片封装,对比发现,后者的EL图像更亮。
因此,经过多次对比实验发现,采用优化后的电池印刷方案和使用直径为0.3 mm的15根镀
图9 第1片无主栅太阳电池预压后效果图
2)将第1片无主栅太阳电池背面朝上放置在载物台上,铺好铜丝与薄膜复合膜,进行第
预压,操作过程同步骤1),只是此次铺设的铜丝与薄膜复合膜长度是步骤1)中复合膜长度的倍,如图10所示。
图10 第1片无主栅太阳电池第2次预压后效果图
a.第1片
b. 第2片
图11 第1片、第2片无主栅太阳电池预压后效果图
a. 第1片
b. 第2片图12 2片无主栅太阳电池层压后EL图像
3)再将第2片无主栅太阳电池的正面朝上放置在载物台上,与第1片电池预压后剩下的另一半复合膜铺设在第2片电池正面,进行第3次预压;预压前将2片电池的间距调整到2~3 mm 范围内,固定好薄膜位置。
4)将预压好的第1片、第2片电池整体反过来,再将正常大小的铜丝与薄膜复合膜铺设在第片电池背面,进行第4次预压。
经过4次预压后,片无主栅太阳电池串接完成,形成具有正负极的电池串,如图11所示。
由图12可知,观察2片无主栅太阳电池经焊接、层压后的EL图像发现,电池中间较亮,四周微暗,说明电池边缘与铜丝的接触不够紧密,串联电阻仍然较大。
在后续的实验过程中对预压设备的下探加热板进行了调整,使得加热板表面平整,与电池表面的温度分布均匀,最终达到了预设的效果。
5 无主栅光伏组件与三主栅光伏组件性能。