晶体硅太阳电池正面栅线电极的制作
晶体硅太阳电池制造技术
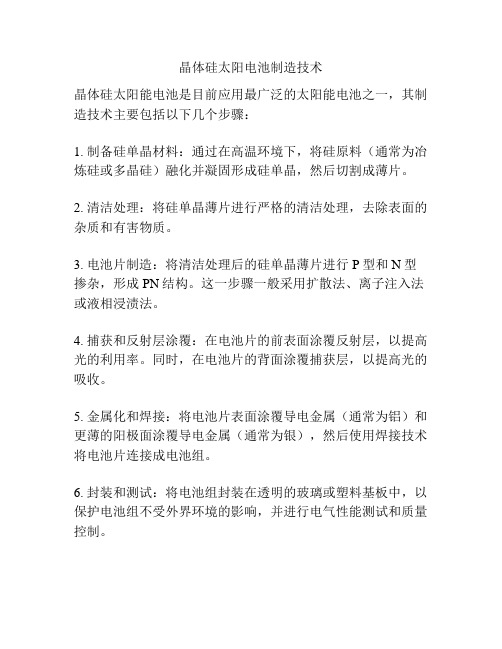
晶体硅太阳电池制造技术
晶体硅太阳能电池是目前应用最广泛的太阳能电池之一,其制造技术主要包括以下几个步骤:
1. 制备硅单晶材料:通过在高温环境下,将硅原料(通常为冶炼硅或多晶硅)融化并凝固形成硅单晶,然后切割成薄片。
2. 清洁处理:将硅单晶薄片进行严格的清洁处理,去除表面的杂质和有害物质。
3. 电池片制造:将清洁处理后的硅单晶薄片进行P型和N型掺杂,形成PN结构。
这一步骤一般采用扩散法、离子注入法或液相浸渍法。
4. 捕获和反射层涂覆:在电池片的前表面涂覆反射层,以提高光的利用率。
同时,在电池片的背面涂覆捕获层,以提高光的吸收。
5. 金属化和焊接:将电池片表面涂覆导电金属(通常为铝)和更薄的阳极面涂覆导电金属(通常为银),然后使用焊接技术将电池片连接成电池组。
6. 封装和测试:将电池组封装在透明的玻璃或塑料基板中,以保护电池组不受外界环境的影响,并进行电气性能测试和质量控制。
这些步骤是晶体硅太阳能电池制造的基本流程,具体制造技术还有其他细节和改进方法,以提高电池的效率和稳定性。
晶硅太阳能电池制造工艺-工艺流程以及工序简介
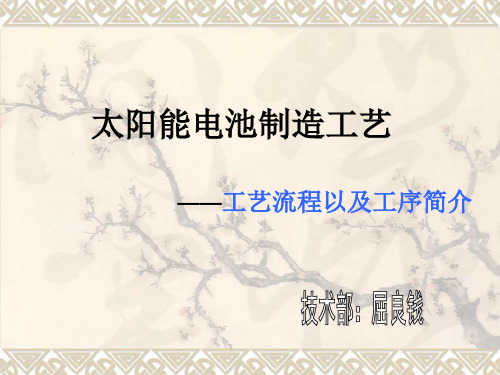
2)、工序简介
目前硅太阳能电池制造工序主要有:
制绒清洗工序 扩散工序 PECVD工序 丝网印刷工序 烧结工序 Laser刻蚀工序 测试分选工序
1. 制绒清洗工序
(a).单晶制绒---捷佳创
目的与作用:
(1)去除单晶硅片表面的机械损伤层和氧 化层。
(2)为了提高单晶硅太阳能电池的光电转 换效率,根据单晶硅的各向异性的特性, 利用碱(KOH)与醇(IPA)的混合溶液在单 晶硅表面形成类似“金字塔”状的绒面, 有效增强硅片对入射太阳光的吸收,从而 提高光生电流密度。
1)、硅太阳能电池的制造工艺流程:
清洗制绒
扩散
周边刻蚀
印刷电极PECVD去磷玻璃烧结分选测试
检验入库
1.原料硅片清洗制绒 12.测试分选
11.激光 10.烧 结 9.丝网印刷正电极 8.烘 干
2.高温扩散(液态扩散) 3.去磷硅玻璃(去PSG) 4.沉积减反射膜(PECVD)
5.丝网印刷背电极 6.烘 干
去除磷硅玻璃的目的、作用:
1. 磷硅玻璃的厚度在扩散中工艺难控制,且其工艺窗口太小,不稳 定。
2. 磷硅玻璃的折射率在1.5左右,比氮化硅折射率(2.07左右)小, 若磷硅玻璃较厚会降低减反射效果。
3. 磷硅玻璃中含有高浓度的磷杂质,会增加少子表面复合,使电池 效率下降。
2. 扩散(POCl3液态扩散)
(b). 多晶制绒---RENA InTex
3Si 2HNO3 18HF 3H2SiF6 0.45NO 1.35NO2 0.1N2O 4.25H2 2.75H2O
目的与作用:
(1)去除单晶硅片表面的机械损 伤层和氧化层。
(2)有效增加硅片对入射太阳光 的吸收,从而提高光生电流密度,提高 单晶硅太阳能电池的光电转换效率。
单晶硅太阳能电池详细工艺
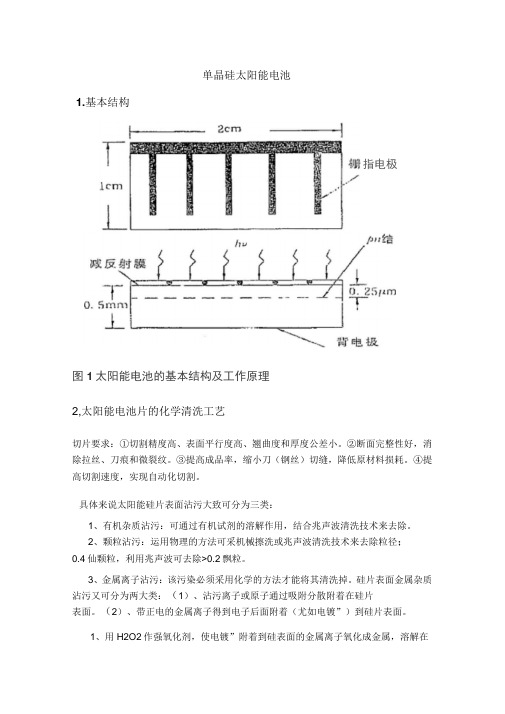
单晶硅太阳能电池1.基本结构指电极图1太阳能电池的基本结构及工作原理2,太阳能电池片的化学清洗工艺切片要求:①切割精度高、表面平行度高、翘曲度和厚度公差小。
②断面完整性好,消除拉丝、刀痕和微裂纹。
③提高成品率,缩小刀(钢丝)切缝,降低原材料损耗。
④提高切割速度,实现自动化切割。
具体来说太阳能硅片表面沾污大致可分为三类:1、有机杂质沾污:可通过有机试剂的溶解作用,结合兆声波清洗技术来去除。
2、颗粒沾污:运用物理的方法可采机械擦洗或兆声波清洗技术来去除粒径;0.4仙颗粒,利用兆声波可去除>0.2飘粒。
3、金属离子沾污:该污染必须采用化学的方法才能将其清洗掉。
硅片表面金属杂质沾污又可分为两大类:(1)、沾污离子或原子通过吸附分散附着在硅片表面。
(2)、带正电的金属离子得到电子后面附着(尤如电镀”)到硅片表面。
1、用H2O2作强氧化剂,使电镀”附着到硅表面的金属离子氧化成金属,溶解在清洗液中或吸附在硅片表面。
2、用无害的小直径强正离子(如H+),一般用HCL作为H+的来源,替代吸附在硅片表面的金属离子,使其溶解于清洗液中,从而清除金属离子。
3、用大量去离子水进行超声波清洗,以排除溶液中的金属离子。
由于SC-1是H2O2和NH40H的碱性溶液,通过H2O2的强氧化和NH4OH的溶解作用,使有机物沾污变成水溶性化合物,随去离子水的冲洗而被排除;同时溶液具有强氧化性和络合性,能氧化Cr、Cu、Zn、Ag、Ni、Co、Ca、Fe、Mg等,使其变成高价离子,然后进一步与碱作用,生成可溶性络合物而随去离子水的冲洗而被去除。
因此用SC-1液清洗抛光片既能去除有机沾污,亦能去除某些金属沾污。
在使用SC-1液时结合使用兆声波来清洗可获得更好的清洗效果。
另外SC-2是H2O2和HCL的酸性溶液,具有极强的氧化性和络合性,能与氧化以前的金属作用生成盐随去离子水冲洗而被去除。
被氧化的金属离子与CL-作用生成的可溶性络合物亦随去离子水冲洗而被去除。
晶硅太阳能电池制造工艺-工艺流程以及工序简介
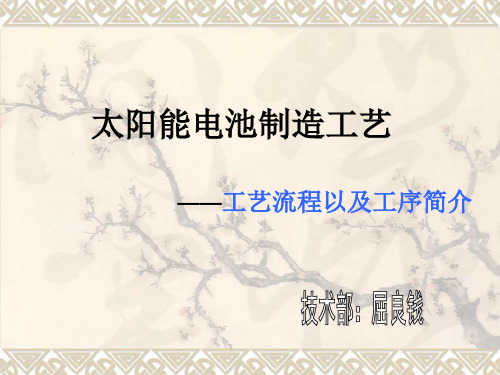
1)、硅太阳能电池的制造工艺流程:
清洗制绒
扩散
周边刻蚀
印刷电极
PECVD
去磷硅玻璃
烧结
分选测试
检验入库
1.原料硅片清洗制绒 12.测试分选
11.激光 10.烧 结 9.丝网印刷正电极 8.烘 干
2.高温扩散(液态扩散) 3.去磷硅玻璃(去PSG) 4.沉积减反射膜(PECVD)
5.丝网印刷背电极 6.烘 干
磷扩散层
其主要是利用硅半导体p-n结的 光生伏打效应。即当太阳光照 射p-n结时,便产生了电子-空 穴对,并在内建电场的作用下, 电子驱向n型区,空穴驱向p型 区,从而使n区有过剩的电子, p区有过剩的空穴,于是在p-n 结的附近形成了与内建电场方 向相反的光生电场。在n区与p 区间产生了电动势。当接通外 电路时便有了电流输出。
扩散的目的:制造太阳能电池的PN结。
PN结是太阳能电池的“心脏” 。 制造PN结,实质上就是想办法使受主杂质在半导体晶体内的一个
区域中占优势(P型),而使施主杂质在半导体内的另外一个区域 中占优势(N型),这样就在一块完整的半导体晶体中实现了P型 和N型半导体的接触。
5POCl 3 600 C以上 3PCl 5 P2O5
7.丝网印刷背电场
2)、工序简介
目前硅太阳能电池制造工序主要有:
制绒清洗工序 扩散工序 PECVD工序 丝网印刷工序 烧结工序 Laser刻蚀工序 测试分选工序
1. 制绒清洗工序
(a).单晶制绒---捷佳创
目的与作用:
(1)去除单晶硅片表面的机械损伤层和氧 化层。
(2)为了提高单晶硅太阳能电池的光电转 换效率,根据单晶硅的各向异性的特性, 利用碱(KOH)与醇(IPA)的混合溶液在单 晶硅表面形成类似“金字塔”状的绒面, 有效增强硅片对入射太阳光的吸收,从而 提高光生电流密度。
- 1、下载文档前请自行甄别文档内容的完整性,平台不提供额外的编辑、内容补充、找答案等附加服务。
- 2、"仅部分预览"的文档,不可在线预览部分如存在完整性等问题,可反馈申请退款(可完整预览的文档不适用该条件!)。
- 3、如文档侵犯您的权益,请联系客服反馈,我们会尽快为您处理(人工客服工作时间:9:00-18:30)。
晶体硅太阳电池正面栅线电极的制作
——超细栅线技术
关于晶体硅太阳能电池的正面电极外观图形,不同的生产厂家会有所不同,并且每一家也在不断的优化种,但改变的方向均为将栅线制作的越来越细、越来越高、数目越来越多。
从2006年之前的120um到2010年的80um甚至有的厂家达到了60um。
随着副栅线宽度变的越来越窄,对于传统的丝网印刷和浆料来说制作难度也变的越来越大,暴露的问题包括断栅增多、结点、栅线边缘不平整等等,从而会导致电性能的不稳定及损失。
而作为细栅线制作的潜在技术,Ink Jet Printing(IJP)和Aerosol Jet Printing(AJP)技术开始逐渐应用到太阳电池制作,下面将对这几种印刷方式进行简单的介绍和比较。
1、Ink Jet Printing、Aerosol Jet Printing技术的工业应用和基本原理
1.1 IJP技术的工业应用和基本原理
IJP技术已经被广泛应用在显示器件、生物科学等领域,如图1所示;其在生产、科研领域的应用也越来越广泛,如图2所示,主要的设备厂家包括Dimatix,OTB等。
图1. Ink Jet Printing技术的应用
图2. Ink Jet Printing技术主要应用领域
IJP印刷的基本原理是将过滤后的墨水利用压电陶瓷的压电效应,使小墨水滴透过喷嘴喷射到器件表面,如图3所示。
图3. Ink Jet Printing的印刷头的原理示意图
1.2 Aerosol Jet Printing的工业应用和基本原理
AJP广泛应用在集成电路和生命科学领域,如图4所示,主要的设备厂家如与Manz合作的Optomec等,其工作原理如图5所示,气流从入口将墨滴带到大腔室,其中大的墨滴在重力的作用下会被筛选掉重新回到原来的溶液,小墨滴在气流的吹动下进入喷嘴,在喷嘴处有两路气流夹着小液滴吹到器件表面形成图形,图形的宽度会大大小于喷嘴的宽度。
图4. Aerosol Jet Printing的工业应用
图5 Aerosol Jet Printing的工作原理
2. Ink Jet Printing、Aerosol Jet Printing技术在太阳电池电极制作中的应用
IJP和AJP应用到电极制作中的步骤如图6所示,由于所采用的墨水的价格相对昂贵,一般仅用其来做种子层如步骤2所示,通过IJP或AJP技术在氮化硅表面形成栅线较细的电极图形,经过烧结后该层与PN结形成良好的欧姆接触,然后通过电镀的
方式增加电极的导电性,从而可以得到栅线宽度在40um左右的电极,如图7所示。
图6. IJP和AJP工艺中电极制作流程
电镀前
电镀后
图7 IJP、AJP工艺电镀前后的栅线形貌(以AJP为例)
表1 AJP工艺应用在普通P型结构上的电性能
在2008年AJP工艺应用在普通P型结构上已到达18.3%的效率,如表1所示。
ISE研究机构在23-24届欧洲光伏会议上发表了利用AJP结合电镀工艺获得20.3%效率的电池(如下表)。
此外,据报告国内有公司开始使用类似该细栅线工艺实现了更高效率电池的制作,具体信息不在此纰漏。
3. Ink Jet Printing和Aerosol Jet Printing技术的比较
目前,认为对于实现细栅线电极来说AJP的技术要好于IJP,主要体现在前者制作的电极更细更均匀,原因包括:a. AJP是连续出料方式,而IJP是间歇出料方式;b. AJP喷嘴的出料方向性强,而IJP的墨滴在滴落时方向具有随机性;c. AJP的墨水浓度更高,高宽比更大,如图8所示;d.AJP的线宽可以做到5-40 um,而IJP是远达不到的。
图8. IJP与AJP比较
另外,AJP的精度更高,可达1um,更有利于与SE工艺相匹配制作高效电池。
AJP目前的开发方向包括:墨水的开发和工艺参数的优化,其中墨水的开发主要是提高种子层与PN结的接触性能以及减小墨水的颗粒度、增加种子层的均匀性,现在正在开发亚微米级的墨水以及与电镀工艺匹配性更好的墨水。