高速切削加工中切削力的应用研究
切削速度和切削力的关系

切削速度和切削力的关系
切削速度和切削力是切削加工中相互关联的两个重要参数。
一般来说,它们的关系可以归纳为以下几点:
1.切削速度对切削力影响较大。
当切削速度增加时,调整好其他相关参数的情况下,切削力通常也会随之增大。
这是因为高速切削会导致刀具与工件之间的反作用力增大,从而引起切削力的增加。
但是,随着切削速度的继续增加,切削力的增加幅度会逐渐减小,甚至趋于稳定。
2.切削力对切削速度影响较小。
当切削力增加时,切削速度并不会受到太大的影响。
这是因为在一定范围内,切削力的增加主要受到切削深度、进给量、材料等因素的影响,与切削速度关系相对较小。
3.刀具的选择也会影响切削力和切削速度的关系。
在不同的加工情况下,需要选择适合的刀具来适应切削速度和切削力的变化。
例如,对于高速切削应用,需要选择高速钢、硬质合金等材质较好的刀具,以确保刀具的刚度和硬度,在切削过程中能够稳定运转,降低切削力的损耗。
高速切削时切削参数对切削力的影响

高速铣削试验证明,在切削速度较低的情况下,切削力随转速的增加而升高,但达到某一临界速度值后,随着转速继续增大,切向切削分力反而下降,但最大切削功率和主轴功率利用率增大。不同刀具材料与工件材料的匹配在不同切削条件下有不同的临界切削速度。涂层刀具、LT55陶瓷刀具铣削调质45钢时的切向分力Fy,先随切削速度的增加而增加,达到临界速度后,切削速度提高,Fy下降较快,临界速度约为800m/min。其刀具参数及切削条件如下表[D高速铣削中]。
1.1.3
仅当切深增加一倍时,Y向、XY平面切削力峰值、切向力峰值、最大切削功率减和主轴功率利用率都增加基本增加一倍,切削力和切深呈线形关系。各切削分力随着切削深度的加大而成正比增加。[高速铣削时切削力研究]
1.1.4
仅当切宽减小一半时,切削力、最大切削功率、主轴功率利用率没有减小一半,Y向、XY平面切削力峰值几乎没有变化,切向力峰值、最大切削功率和主轴功率利用率也减小很少,切削力和切宽不呈线性关系。[高速铣削时切削力研究]
1.1.2
图4是切削分力随进给量的变化曲线(仿真条件:切削速度v=1000m/min,切削深度ap=0.2mm)。用硬质合金刀具高速加工45#调质钢时,各切削分力Fx、Fy、Fz都随着进给量的提高而增加,增加的趋势近似为线性。各切削分力曲线的增大速率,按由大到小的顺序排列,依次为Fy、FFz增大约42%,Fx增大仅为10%[D高速加工时]。
进给量
用硬质合金刀具高速加工45#调质钢时,各切削分力Fx、Fy、Fz都随着进给量的提高而增加,增加的趋势近似为线性。各切削分力曲线的增大速率,按由大到小的顺序排列,依次为Fy、Fz和Fx。
切削深度
当切深增加一倍时,Y向、XY平面切削力峰值、切向力峰值、最大切削功率减和主轴功率利用率都增加基本增加一倍,切削力和切深呈线形关系。各切削分力随着切削深度的加大而成正比增加。
切削力在金属切削加工中的作用与控制

切削力在金属切削加工中的作用与控制切削力是指在金属切削加工过程中作用在切削刀具上的力量,它对于金属切削加工的效果和工件质量起着至关重要的作用。
了解切削力的作用和控制,对于提高金属切削加工效率、延长切削刀具寿命和改善工件表面质量具有重要意义。
首先,切削力的作用在于将切削刀具施加在工件表面上,引起剪切和剥离,从而实现对工件的切削。
切削力的大小直接决定了切削刀具与工件的接触压力,因此它对刀具的切削能力和结构强度有着直接影响。
合理控制切削力的大小可以保证刀具稳定性和寿命。
其次,切削力还影响着金属切削加工中的能量消耗和热量积累。
在切削过程中,切削力会使工件和刀具之间产生摩擦,从而产生热量。
同时,切削过程中金属的塑性变形和形变也会产生热量。
切削力大小的控制可以有效减少热量积累,降低工件温度,从而减少刀具磨损和工件变形的风险。
此外,切削力的控制对于提高切削效率和降低能耗也非常重要。
切削力较大会增加加工的能耗,降低加工效率。
因此,通过合理调整切削参数,控制切削力的大小是提高加工效率的关键之一。
切削力的控制还能够降低切削过程对机床和刀具的负荷,延长其使用寿命,降低维修成本。
为了实现对切削力的控制,可以从以下的几个方面进行思考和优化:首先,合理选择切削刀具。
不同的切削材料和加工条件适合使用不同类型的切削刀具。
对于高速切削来说,刀具的结构和刀片的尺寸、刀具涂层等都需要进行选择和调整,以提高切削效率和寿命。
其次,优化切削参数。
切削速度、进给速度和进给量是影响切削力的重要因素。
通过调整这些切削参数,可以在保证切削质量的前提下,尽量降低切削力的大小。
在实际操作中,可以采用试切试验的方式,不断优化切削参数,以达到最佳的切削效果。
再次,改善切削冷却条件。
切削过程中产生的热量如果不能及时散出,会导致切削温度升高,从而增加切削力的大小。
因此,合理设计和改进切削冷却系统,选择合适的切削液和切削液的供给方式,可以有效降低切削温度,减小切削力。
高速切削技术在薄壁零件加工中的应用研究

高速切削技术是诞生 于 2 0世纪 3 0年代 的一项 先 进 制造技术 ,其 采用超 硬材料 刀具和模具 ,利用高精
度 、高 自动化和高柔性的制造设备实现 了高效率 、高 柔性和高质量 的切 削加工 ,被称 为是 2 世 纪机械 制 1
造业 的一 场技术革命 ,在工程领 域的应用逐 渐成 熟 。由于高 速切 削技 术具 有 高 主轴 转 速 、高 进 给速 度 、低切削力和高切削速度等特点 ,能有效地缩短加 工时 间并降低加工 成本 ,加 工精 度高且 表面 质量好 , 符合薄壁箱体 生产 的发展趋势 ,因而获得广泛应用 。 作者针 对薄壁箱体零 件的工艺特点及生产实 际要 求 ,对薄壁箱体零件高速切削 的可行性进行 了分析 与
高速切削技术在薄壁零件加工中的应用研究
周 文 ( 南通纺织职业技术学院,江苏南通 260 ) 207
摘要 :从 薄壁箱体的加工效率 、加工精度等 角度出发 ,分析薄壁箱体零 件高速切 削加工 的优 势和可行 性。针对其 工艺 特点及生 产实际要求 ,分析高速加工 中存在 的工 艺问题 ,给出具体 的解决 措施 。实践 表明 :采用 高速切削加 工技术加 工薄 壁 箱体 ,加工效率高 ,工件表面质量好 。 关键词 :高速切削技术 ;加工效率 ;加 工精度 ;薄壁箱体零件
nn , te me s r s w r u o wad t e o v h r c s rb e f ma h nn . T e p a t e h w t a h p l ai n o ih i g h a u e e e p tfr r o r s le t e p o e s p o lms o c i i g h r ci s s o h tt e a p i t fh g — c c o s e d ma h n n e h o o y i c i i g t i — i k e sb x d s a e o k ic sc n g i ih e ce c n o d s ra e q a i . p e c i i g t c n lg n ma hn n n t c n s o e — h p d w r p e e a an h g f in y a d g o u f c u t h h i l y
高速切削技术研究
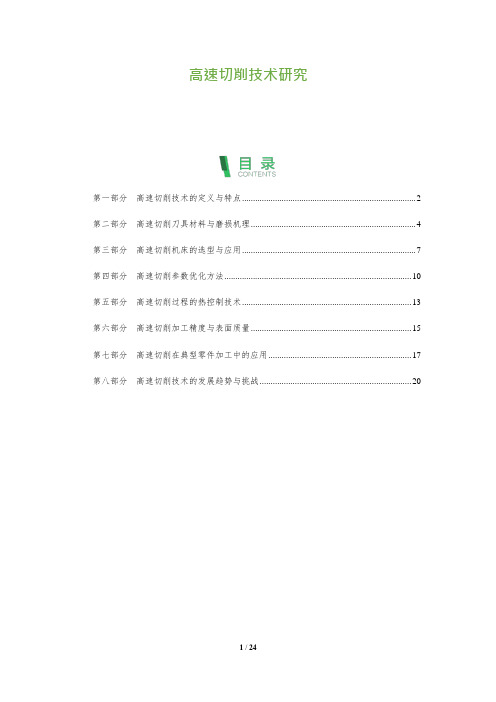
高速切削技术研究第一部分高速切削技术的定义与特点 (2)第二部分高速切削刀具材料与磨损机理 (4)第三部分高速切削机床的选型与应用 (7)第四部分高速切削参数优化方法 (10)第五部分高速切削过程的热控制技术 (13)第六部分高速切削加工精度与表面质量 (15)第七部分高速切削在典型零件加工中的应用 (17)第八部分高速切削技术的发展趋势与挑战 (20)第一部分高速切削技术的定义与特点高速切削技术是一种先进的制造工艺,它通过使用高转速的刀具和优化的切削参数来提高材料去除率、加工精度和表面质量。
该技术的核心在于实现高效率、高质量和高精度的加工过程。
在高速切削过程中,刀具以极高的速度旋转(通常超过每分钟数千转),同时进给速度也相应提高。
这种高速旋转产生的离心力有助于减小切削力和切削热,从而延长刀具寿命并减少工件的热变形。
此外,由于切削力的降低,高速切削还可以减少振动,进一步提高加工精度。
高速切削技术的优势主要体现在以下几个方面:1.高效率:与传统切削相比,高速切削可以显著提高材料去除率,缩短加工时间。
研究表明,高速切削可以提高生产效率达 30%至50%。
2.高精度:高速切削过程中的低切削力可以减少工件的振动,从而提高加工精度。
此外,由于切削热的影响较小,工件的热变形也得到了控制。
3.高质量表面:高速切削产生的切削热较低,这有助于减少工件的烧伤和裂纹,从而获得更好的表面质量。
4.刀具寿命延长:高速切削可以降低切削力,减少刀具磨损,从而延长刀具的使用寿命。
5.节能减排:高速切削技术可以实现更高的材料去除率,从而减少能源消耗和碳排放。
然而,高速切削技术也存在一些挑战,如刀具成本较高、对机床性能要求较高等。
因此,在实际应用中,需要根据具体加工需求和技术条件,合理选择切削参数和刀具,以确保高速切削技术的有效性和经济性。
总之,高速切削技术作为一种先进的制造工艺,具有高效率、高精度、高质量表面等优势,但在实际应用中需充分考虑其成本和设备要求。
铝合金的高速切削加工技术研究
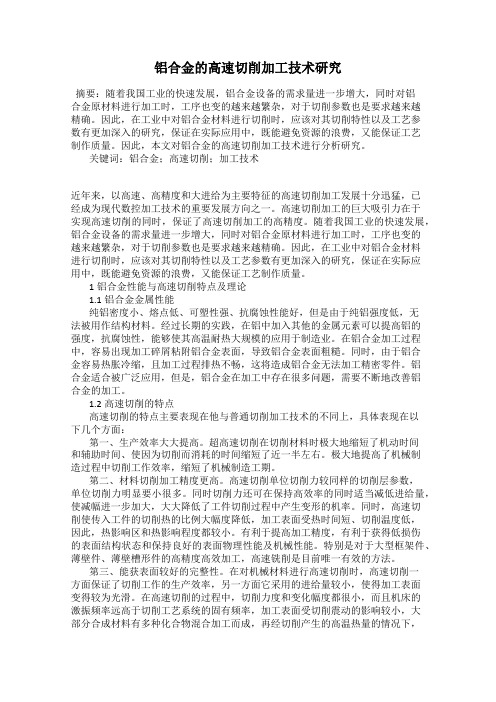
铝合金的高速切削加工技术研究摘要:随着我国工业的快速发展,铝合金设备的需求量进一步增大,同时对铝合金原材料进行加工时,工序也变的越来越繁杂,对于切削参数也是要求越来越精确。
因此,在工业中对铝合金材料进行切削时,应该对其切削特性以及工艺参数有更加深入的研究,保证在实际应用中,既能避免资源的浪费,又能保证工艺制作质量。
因此,本文对铝合金的高速切削加工技术进行分析研究。
关键词:铝合金;高速切削;加工技术近年来,以高速、高精度和大进给为主要特征的高速切削加工发展十分迅猛,已经成为现代数控加工技术的重要发展方向之一。
高速切削加工的巨大吸引力在于实现高速切削的同时,保证了高速切削加工的高精度。
随着我国工业的快速发展,铝合金设备的需求量进一步增大,同时对铝合金原材料进行加工时,工序也变的越来越繁杂,对于切削参数也是要求越来越精确。
因此,在工业中对铝合金材料进行切削时,应该对其切削特性以及工艺参数有更加深入的研究,保证在实际应用中,既能避免资源的浪费,又能保证工艺制作质量。
1铝合金性能与高速切削特点及理论1.1铝合金金属性能纯铝密度小、熔点低、可塑性强、抗腐蚀性能好,但是由于纯铝强度低,无法被用作结构材料。
经过长期的实践,在铝中加入其他的金属元素可以提高铝的强度,抗腐蚀性,能够使其高温耐热大规模的应用于制造业。
在铝合金加工过程中,容易出现加工碎屑粘附铝合金表面,导致铝合金表面粗糙。
同时,由于铝合金容易热胀冷缩,且加工过程排热不畅,这将造成铝合金无法加工精密零件。
铝合金适合被广泛应用,但是,铝合金在加工中存在很多问题,需要不断地改善铝合金的加工。
1.2高速切削的特点高速切削的特点主要表现在他与普通切削加工技术的不同上,具体表现在以下几个方面:第一、生产效率大大提高。
超高速切削在切削材料时极大地缩短了机动时间和辅助时间、使因为切削而消耗的时间缩短了近一半左右。
极大地提高了机械制造过程中切削工作效率,缩短了机械制造工期。
数控高速切削加工技术的发展与应用研究
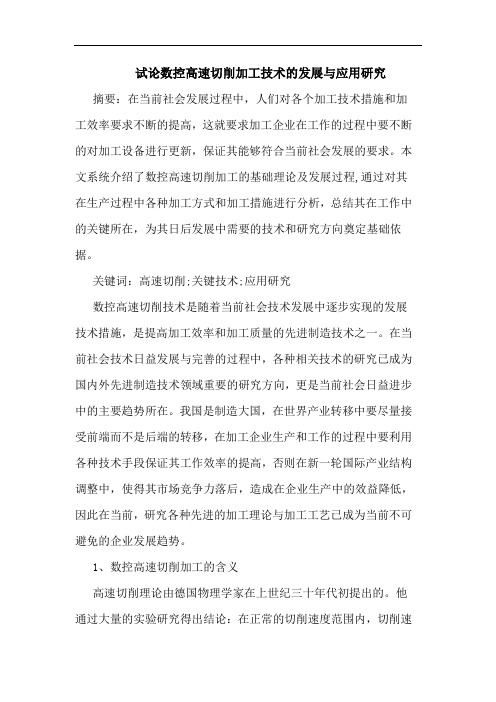
试论数控高速切削加工技术的发展与应用研究摘要:在当前社会发展过程中,人们对各个加工技术措施和加工效率要求不断的提高,这就要求加工企业在工作的过程中要不断的对加工设备进行更新,保证其能够符合当前社会发展的要求。
本文系统介绍了数控高速切削加工的基础理论及发展过程,通过对其在生产过程中各种加工方式和加工措施进行分析,总结其在工作中的关键所在,为其日后发展中需要的技术和研究方向奠定基础依据。
关键词:高速切削;关键技术;应用研究数控高速切削技术是随着当前社会技术发展中逐步实现的发展技术措施,是提高加工效率和加工质量的先进制造技术之一。
在当前社会技术日益发展与完善的过程中,各种相关技术的研究已成为国内外先进制造技术领域重要的研究方向,更是当前社会日益进步中的主要趋势所在。
我国是制造大国,在世界产业转移中要尽量接受前端而不是后端的转移,在加工企业生产和工作的过程中要利用各种技术手段保证其工作效率的提高,否则在新一轮国际产业结构调整中,使得其市场竞争力落后,造成在企业生产中的效益降低,因此在当前,研究各种先进的加工理论与加工工艺已成为当前不可避免的企业发展趋势。
1、数控高速切削加工的含义高速切削理论由德国物理学家在上世纪三十年代初提出的。
他通过大量的实验研究得出结论:在正常的切削速度范围内,切削速度如果提高,会导致切削温度上升,从而加剧了切削刀具的磨损;然而,当切削速度提高到某一定值后,只要超过这个拐点,随着切削速度提高,切削温度就不会升高,反而会下降,因此只要切削速度足够高,就可以很好的解决切削温度过高而造成刀具磨损不利于切削的问题,获得良好的加工效益。
随着社会发展中,对制造业要求的不断提高,高速切削加工逐步的被应用在各个加工企业和加工生产当中,更是被诸多单位广泛的重视。
在此理论基础上逐渐形成了数控高速切削技术研究领域,使得其在生产的过程中能够有效的保证加工产品的质量和加工效益,是各个企业生产和加工过程中主要探索的目标和追求方向。
高速切削加工技术的研究及其推广应用
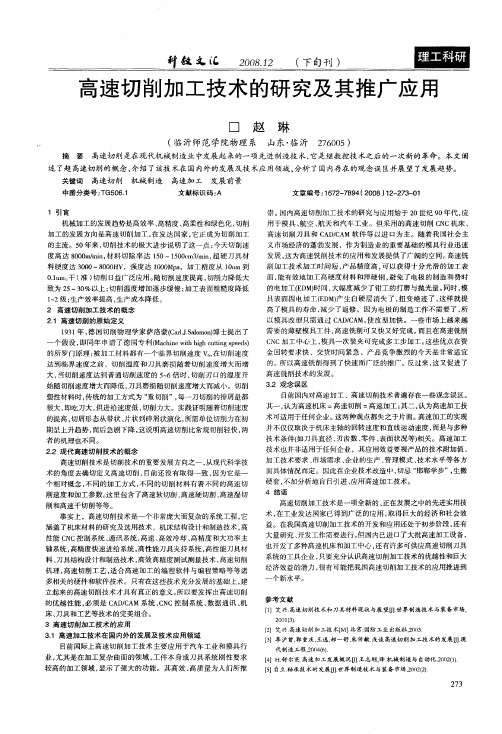
22 现 代 高速 切 削技 术 的概 念 .
目前 国内对高速加工 、高速切削技术普遍 存在一些观念误 区。
其一 , 认为高速机床 = 高速切削 = 高速加工 ; 二 , 为高速加工技 其 认 术可适用于任何企业。 这两种观点都失之于片面 。 高速加工的实现 并不仅仅取决于机床主轴的 回转速度和直线运 动速度 , 而是与多种 技术条 件( 如刀具直径 、 齿数 、 刃 零件 、 表面状况等) 。高速加工 相关 技术也并非适用于任何企业 ,其应 用效 益要视 产品的技术附加值 、 加工技术要求 、 市场需求 、 企业的生产 、 理模式 、 管 技术水平 等各方
一
个假设 , 即同年 申请 了德国专 利( c ie 『 hg IL g pe s Mahn h ihctn ed) li s
的所罗 门原理 : 被加 l 材料都有一个临界切削速度 v , T 在切削速度 达到临界速度之前 ,切 削温度 和刀具磨 损随着切削速度增 大而增 大, 当切 削速度达到普通切 削速度 的 5 6倍 时, ~ 切削刃 口的温度 开 始随切削速度增大而降低 , 刀具磨损随切削速度增大而减小。切削
塑性材料时 , 传统 的加工方式为 “ 重切削”, 每一刀切削的排屑量都 很大 , 即吃刀大 , 但进给速度低 , 切削力大。实践证明随着切削速度 的提高 , 切屑形态从带状 、 片状到碎屑状演化 , 所需单 位切削力在初 期呈上升趋势 , 而后急剧下降 , 这说明高速切削 比常规切削轻快 , 两
面具体情况而定。因此在企业技 术改造 中 , 切忌 “ 邯郸学步”, 生搬 硬套 , 不加分析地 盲 目引进 、 应用 高速加 工技术 。
4 结 语
高速切削技术是切削技术的重要发展方向之一 , 从现代科学技 术的角度去确切定 义高速切削 , 目前还 没有取得一致 , 因为它是一 个相对概念 , 同的加 工方式 , 不 不同 的切 削材料有着不 同的高速切
- 1、下载文档前请自行甄别文档内容的完整性,平台不提供额外的编辑、内容补充、找答案等附加服务。
- 2、"仅部分预览"的文档,不可在线预览部分如存在完整性等问题,可反馈申请退款(可完整预览的文档不适用该条件!)。
- 3、如文档侵犯您的权益,请联系客服反馈,我们会尽快为您处理(人工客服工作时间:9:00-18:30)。
赵 立 (沈 阳铁路 机械 学校 ,沈 阳 1 10036) Aniysis of cutting forces compoments and friction high speed machining
ZHAO Li
(Shenyang Railroad Mechanical School,Shenyang 1 loo36,China)
Key words:High speed m achining;Cutting forces;Orthogonal cutting;friction
中图分类 号 :TH16 文献标 识码 :A
1前 言
变 化 。
由于 目前高速机床在机械加工行业 的应用 ,提高的切 削速 2试 验 装 置 Experimental Device
【摘要 】通过采用一种新型的试验装置 ,可重现在 了较大的切 削速度范围内(从 15~100m/s),正交 切 削 下的切 削过 程 。该 试验设 备 可 以记 录在 正 交切 削下 的切 削过 程 中法 线 方向上 和切 线 方 向上 的作 用 力数值 。从 而在 很 大 的切 削速度 范 围 内,可 以对刀具 和切 屑之 间的摩 擦 力进行 分 析 。给 出 了切 削力 的 分力 变化 和摩 擦 系数 变化 的情 况 。此 外 ,通 过 可 以使 用一 台高速摄 影机 ,记 录 了高速加 工 中 ,切屑 的 形成过 程 的 图像 。
Fig-1 Schematic description of the experimental setup
受到限制。现有装置 可使得现在可 以在正交 切削 中,对两个分力
刀具 的夹 紧装置 的新型设计 ,使得推进分力 Fr的测量成
进行测量。本文首次给出 了在中碳钢 (42Cr Mo4)上取得 的结果 为可能 。
交 和 准 、稳 状 态 上 。
在工业过程 中,这些条件很少能够达到 ,因为在一般情况
下 ,会出现多个切削刃的情况 (特别是在铣削工艺 中),而切削刃
的方 向又是倾斜 的。然而通过这样 的简化 ,可 以有助于分析和理
解 上 述 现 象 。
这种试验装置使这一分析得 以进行 ,不会 出现通常加工测
正交切削的定义是由 Merchant提 出的,即切削刀具产生的平 面 的摩擦系数值。该试验装置 的一项重要性能就是具有很高的刚
和被切削物体原先的平面平行 ,且其切削刃的设 置与刀具 和工 性 。因而 ,在短暂 的时间后 ,达到 的切削条件并精确地保持在正
件 之 间相 对 运 动 方 向垂 直 。
维普资讯
第 1期 2008年 1月
机 械 设 计 与 制 造
Machinery Design & Manufacture
文章 编 号 :1001~3997(2008)O1—0155—03
高速 切 削加 工 中切 削力 的应 用研 究
一 155 一
度和材料 的性能 已成为机械加工技术的发展趋势 。因此 ,非常有
本文给出 了实验装置 的主要性能 。是可以测量 出切削力的
必要对高速切削过程进行试验分析 。
推进分力和纵向分力 。
主要介绍采用 一种新 型试验装置对正交 切削进行 了分析 。
图 1为示意简 图。由这些测 量可以估算 出刀具一切屑界面
关键词 :高 速加 工 :切 削 力 ;正 交切 削 ;摩擦 力 【Abstract】A n original experimental device is used to reproduce conditions of orthogonal cuttingfor
a wide range of cutting speeds(from 15 to about 100m/s).The device makes it possible to record both va l— u s of normal and tangentialforces in orthogona l cutting.An a na lysis o f the tool-chipfriction i s then pos— sible for a large range of cutting speeds。Th e evolution o f cuttingforce components∞ well∞ the evolution Q厂£船 friction coeff icient a re presented and a nalyzed In addition,the process of c formation during 劬 speed machining is illustrated by photographic recording with a 劬 speed c
和切屑形成过程 中的照片记录来说 明了切削速度下切屑形状 的
图 2所示 为位于气 动管入 口处夹紧装置的详 细情况 。两个
-k来稿 日期 :2007—06—13
维普资讯
一
56一
赵 立 :高速切 削加 工 中切 削力的应 用研 究
第 1期
刀具对称地布置在刀具夹 紧装置上 ,这样 可以同时对工件试样 而切削速度在整Байду номын сангаас过程 中接近定值 ,并且实现准、稳状态切削条
的两侧进行加工。由气动装置推动 的气动头承载试样 。各 刀具分 件 。为达到该 目的 ,有必要采用 同样几fq ̄'t-形但是质量密度不同
别安装在横梁上 ,该横梁 的截面足够大 ,以保证很高的刚性 。切 的气动射头(钢 、铝、聚合 物)。气 动射头 的速度和加速度 通过在
试 中发生的局限。因此 ,通过保持装 置高度刚性并限制附加的振
动 ,可以在 15至 lOOm/s的切削速度范 围进行分析 。此外 ,由于
装置具有 良好的开放性 ,可以对切削过程进行理想的观察 。也已
经有大量采用相关仪器对高速加工进行研究 的报道 ,但 是它们
图 1试验装置的示意图
要么在切削速度上受到限制 ,要么在作用力 的各个分力测量上