提升冲压材料利用率的工艺技术
冲压材料利用率

冲压材料利用率冲压材料利用率是指在冲压过程中,切割下来的材料与原始材料的比例。
冲压是一种加工方法,主要用于将金属板材或带材加工成所需形状和大小的零件或半成品。
由于冲压需要在材料表面施加压力,因此需要大量的材料来传递和分散压力,这导致了材料的利用率低下。
下面将分析冲压材料利用率的影响因素和改善方法。
影响冲压材料利用率的因素主要有以下几个:1. 材料的形状和大小:材料的形状和大小决定了冲压时需要切割的面积和数量。
如果材料的形状和大小与冲压零件相同或相近,利用率就会高。
2. 冲压模具的设计:模具的设计影响着冲压过程中材料的剪切情况和材料的累积变形程度。
如果模具设计得好,可以减少材料的浪费和强化材料的累积变形效应。
3. 冲压工艺参数的控制:材料的利用率还取决于冲压的工艺参数,比如压力、速度和温度等因素。
调整这些参数可以控制材料的变形和利用情况。
改善冲压材料利用率的方法可以从以下几个方面入手:1. 采用高效节材的技术:这种技术通常采用异型材以减少材料的浪费。
异型材的切口与零件形状相同或相似,因此可以最大限度地提高利用率。
2. 模具的设计与制造:模具的设计和制造是冲压过程中最关键的环节。
为了提高冲压材料的利用率,我们需要制造先进的模具,并在设计和制造过程中考虑到材料利用率的因素。
3. 控制冲压工艺参数:在控制冲压工艺参数的同时,也需要考虑到材料利用率的问题。
如果冲压工艺参数不合适,会导致材料的变形和浪费。
因此,需要在控制工艺参数的同时,根据材料的特性和工艺的特点,调整参数以实现更高的利用率。
总之,冲压材料利用率是生产过程中非常重要的一个环节。
通过采用合适的材料和模具设计,以及控制工艺参数,可以最大程度地提高材料利用率,进而降低生产成本,提高企业的竞争力。
冲压工艺的基础知识和详细介绍【完整】
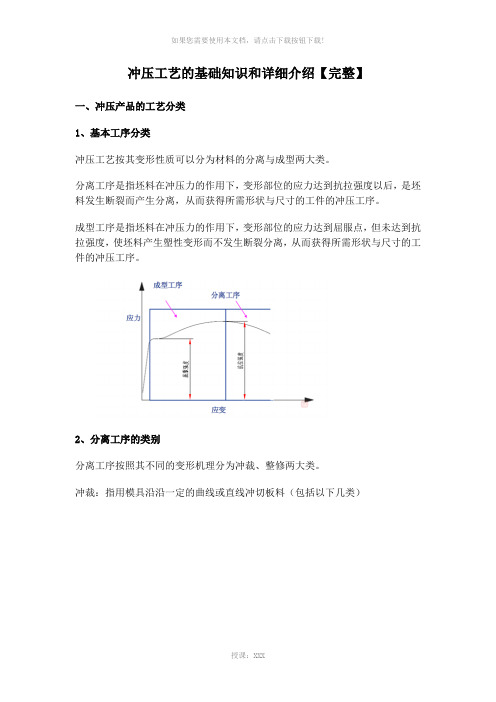
冲压工艺的基础知识和详细介绍【完整】一、冲压产品的工艺分类1、基本工序分类冲压工艺按其变形性质可以分为材料的分离与成型两大类。
分离工序是指坯料在冲压力的作用下,变形部位的应力达到抗拉强度以后,是坯料发生断裂而产生分离,从而获得所需形状与尺寸的工件的冲压工序。
成型工序是指坯料在冲压力的作用下,变形部位的应力达到屈服点,但未达到抗拉强度,使坯料产生塑性变形而不发生断裂分离,从而获得所需形状与尺寸的工件的冲压工序。
2、分离工序的类别分离工序按照其不同的变形机理分为冲裁、整修两大类。
冲裁:指用模具沿沿一定的曲线或直线冲切板料(包括以下几类)整修是对冲裁件的断面部分进行再加工的分离加工方法,整修变形是一种切削机理,其工件的尺寸精度和断面质量比冲裁件好。
3.成型工序的类别成型工序较多,包括:弯曲、拉深、翻边、胀形和挤压工艺等。
(具体如下:)二、冲裁1、冲裁产品的形态与成型过程介绍冲裁产品的形态。
冲裁产品的的断面分为:塌角、光亮带、断裂带、毛刺,这四种形态是在产品冲裁过程中于不同的阶段,不同的部位、不同的应力作用下产生的。
如上图,1塌角 :高度约等于8%T至15%T ;2.光亮带 :高度约等于15%T至55%T ;3.断裂带 :高度约等于35%T至75%T ;4.毛刺 :高度约等于5%T至10%T1)弹性变形阶段受力分析:刃口部分材料受剪切力,力的大小小于弹性极限,若力消失,则材料恢复原始状态。
状态描述:凸模施加压力于材料,材料略挤入凹模刃口。
2)塑性变形阶段受力分析:材料受力由边及中心,逐渐超过弹性极限状态描述:凸模进一步深入材料,在本阶段冲裁件产生塌角以及光亮带3)剪裂阶段受力分析:材料靠近凹模刃口的部分应力首先达到材料的抗剪切强度,使凹模刃口旁边的材料产生的裂纹增大。
而此时凸模刃口部分材料还处于塑性变形阶段,随着冲头的进一步深入材料,冲头附近材料也达到剪切强度,也产生裂纹,再往后两裂纹重合,材料分离。
状态描述:材料分离,上下裂纹重合时相互撕扯产生毛刺三、与产品设计相关的冲裁工艺要点及设计举例1、冲裁产品的分类、作用及结构冲孔 piercing作用 1.作为一般过孔使用(要求较低);2.作为自攻牙底孔使用(产品设计要求光亮带比例较高);3.作为高精度转轴孔使用(要求无毛刺,少断裂带)(采用机械去毛刺的方式或模具倒面的方式)注意:设计冲孔时,由于受到凸模强度的限制, 孔的尺寸不宜太小(一般大于0.5T)落料 stamping作用 1.作为一般外形使用(要求较低);2.作为对接接头激光焊接装配使用(无毛刺、大的光亮带、小的断裂带间隙);3、作为软饰支架使用(要求卷边或者去毛刺)注意:1、产品设计时应该使冲裁件各直线或曲线的连接处有适当的圆角.(否则凹模应力集中,容易损坏);2、考虑到模具线切割的加工工艺,冲裁零件或者落料零件的最小R角不要小于R0.2。
汽车制造工艺冲压工艺
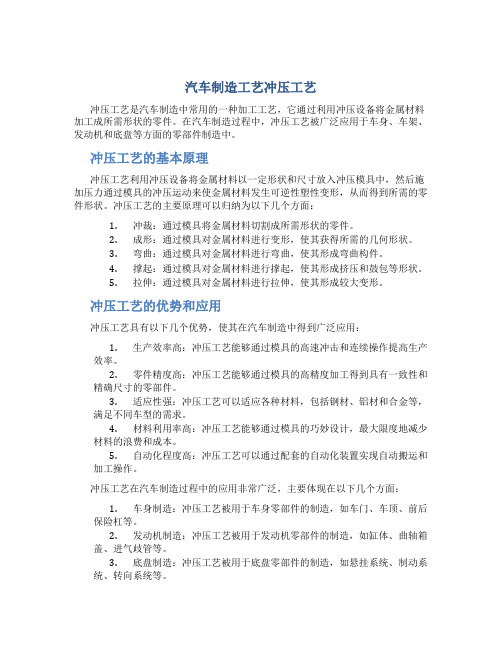
汽车制造工艺冲压工艺冲压工艺是汽车制造中常用的一种加工工艺,它通过利用冲压设备将金属材料加工成所需形状的零件。
在汽车制造过程中,冲压工艺被广泛应用于车身、车架、发动机和底盘等方面的零部件制造中。
冲压工艺的基本原理冲压工艺利用冲压设备将金属材料以一定形状和尺寸放入冲压模具中,然后施加压力通过模具的冲压运动来使金属材料发生可逆性塑性变形,从而得到所需的零件形状。
冲压工艺的主要原理可以归纳为以下几个方面:1.冲裁:通过模具将金属材料切割成所需形状的零件。
2.成形:通过模具对金属材料进行变形,使其获得所需的几何形状。
3.弯曲:通过模具对金属材料进行弯曲,使其形成弯曲构件。
4.撑起:通过模具对金属材料进行撑起,使其形成挤压和鼓包等形状。
5.拉伸:通过模具对金属材料进行拉伸,使其形成较大变形。
冲压工艺的优势和应用冲压工艺具有以下几个优势,使其在汽车制造中得到广泛应用:1.生产效率高:冲压工艺能够通过模具的高速冲击和连续操作提高生产效率。
2.零件精度高:冲压工艺能够通过模具的高精度加工得到具有一致性和精确尺寸的零部件。
3.适应性强:冲压工艺可以适应各种材料,包括钢材、铝材和合金等,满足不同车型的需求。
4.材料利用率高:冲压工艺能够通过模具的巧妙设计,最大限度地减少材料的浪费和成本。
5.自动化程度高:冲压工艺可以通过配套的自动化装置实现自动搬运和加工操作。
冲压工艺在汽车制造过程中的应用非常广泛,主要体现在以下几个方面:1.车身制造:冲压工艺被用于车身零部件的制造,如车门、车顶、前后保险杠等。
2.发动机制造:冲压工艺被用于发动机零部件的制造,如缸体、曲轴箱盖、进气歧管等。
3.底盘制造:冲压工艺被用于底盘零部件的制造,如悬挂系统、制动系统、转向系统等。
4.内饰制造:冲压工艺被用于内饰零部件的制造,如仪表盘、门板、座椅架等。
冲压工艺的发展趋势随着汽车制造技术的不断发展,冲压工艺也在不断创新与改进。
未来冲压工艺的发展主要有以下几个趋势:1.模具技术的创新:通过模具技术的创新,提高冲压工艺的制造精度和生产效率。
五金冲压工艺技术介绍

五金冲压工艺技术介绍一、冲压工艺概述1.1 五金冲压的定义五金冲压是通过模具将金属材料加工成一定形状的工艺过程。
它是在冲压机的作用下,利用模具对金属材料施加压力,使其产生塑性变形,从而获得所需的形状和尺寸。
1.2 五金冲压的特点1.高效快速:冲压工艺具有高效生产的优点,能在短时间内完成大批量、高速度的生产加工。
2.精度高:由于冲压工艺采用模具加工,使得产品的尺寸精度高,形状一致性好。
3.可复杂成形:冲压工艺可以实现对复杂形状零件的生产加工,满足不同形状的产品需求。
4.节约原材料:冲压工艺可以高效利用原材料,减少浪费,提高资源利用率。
二、五金冲压的工艺流程2.1 工艺准备工艺准备是五金冲压的第一步,包括产品设计、材料选择、模具设计等。
产品设计要满足使用要求,选择合适的材料可以确保产品的质量和性能。
模具设计要考虑产品形状、尺寸及加工工艺要求。
2.2 材料准备材料准备是指将所需金属材料按照规定的尺寸切割成所需的工件片料。
2.3 冲压加工冲压加工是五金冲压的核心过程,包括取料、送料、冲压和卸料。
具体操作需要根据产品的设计要求和模具的结构来进行。
2.4 补偿工艺冲压加工中,由于材料的弹性变形和模具间隙的存在,产品可能会出现尺寸偏差。
补偿工艺是通过对模具结构进行调整,使产品尺寸与设计要求相符。
2.5 表面处理五金冲压后的产品一般需要进行表面处理,以提高产品的美观性、耐腐蚀性和耐磨性。
常见的表面处理包括电镀、喷涂等。
2.6 检测与包装最后一步是对冲压产品进行检测,确保产品质量。
合格产品经过检测后,进行包装,并进行出厂或入库。
三、五金冲压工艺中的关键技术3.1 模具设计技术冲压模具是五金冲压的重要组成部分,模具设计直接影响产品的成形质量和生产效率。
模具设计技术包括模具结构设计、模具材料选择、模具加工工艺等,要求专业知识和丰富经验。
3.2 材料选择与预处理材料的选择直接影响到产品的质量和性能。
不同的材料具有不同的特性,可以根据产品的使用要求选择合适的材料。
冲压工艺技术分析
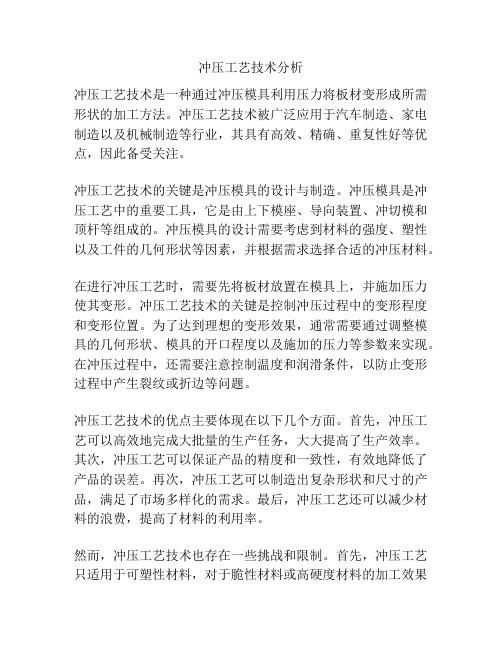
冲压工艺技术分析冲压工艺技术是一种通过冲压模具利用压力将板材变形成所需形状的加工方法。
冲压工艺技术被广泛应用于汽车制造、家电制造以及机械制造等行业,其具有高效、精确、重复性好等优点,因此备受关注。
冲压工艺技术的关键是冲压模具的设计与制造。
冲压模具是冲压工艺中的重要工具,它是由上下模座、导向装置、冲切模和顶杆等组成的。
冲压模具的设计需要考虑到材料的强度、塑性以及工件的几何形状等因素,并根据需求选择合适的冲压材料。
在进行冲压工艺时,需要先将板材放置在模具上,并施加压力使其变形。
冲压工艺技术的关键是控制冲压过程中的变形程度和变形位置。
为了达到理想的变形效果,通常需要通过调整模具的几何形状、模具的开口程度以及施加的压力等参数来实现。
在冲压过程中,还需要注意控制温度和润滑条件,以防止变形过程中产生裂纹或折边等问题。
冲压工艺技术的优点主要体现在以下几个方面。
首先,冲压工艺可以高效地完成大批量的生产任务,大大提高了生产效率。
其次,冲压工艺可以保证产品的精度和一致性,有效地降低了产品的误差。
再次,冲压工艺可以制造出复杂形状和尺寸的产品,满足了市场多样化的需求。
最后,冲压工艺还可以减少材料的浪费,提高了材料的利用率。
然而,冲压工艺技术也存在一些挑战和限制。
首先,冲压工艺只适用于可塑性材料,对于脆性材料或高硬度材料的加工效果不佳。
其次,冲压工艺在处理较大尺寸或薄板材料时容易出现变形问题,影响产品质量。
再次,冲压工艺的模具制造成本较高,需要投入大量的时间和精力。
最后,冲压工艺对操作人员的技能要求较高,需要具备丰富的经验和专业知识。
综上所述,冲压工艺技术是一种高效、精确的加工方法,广泛应用于各个制造行业。
通过合理的冲压模具设计和制造以及优化的工艺参数,可以实现高质量、高效率的冲压加工。
然而,冲压工艺技术也存在一些挑战和限制,需要进一步的研究和改进。
最新冲压工艺述职报告范本

最新冲压工艺述职报告范本尊敬的领导和同事们:今天,我将向大家汇报过去一年中我们在冲压工艺领域的最新进展和成果。
以下是我的述职报告:一、工艺技术创新1. 成功研发了新型冲压模具,提高了材料利用率,减少了废料产生。
2. 实施了精密冲压技术,提升了产品精度,减少了后续加工成本。
3. 引入了自动化冲压生产线,减少了人工操作,提高了生产效率和安全性。
二、质量控制与改进1. 建立了更为严格的质量检测流程,确保了产品质量的稳定性。
2. 通过持续的质量分析,发现并解决了多个潜在的工艺缺陷。
3. 实施了全面质量管理(TQM),提高了全员的质量意识。
三、成本控制与优化1. 通过优化材料采购策略,降低了原材料成本。
2. 实施了精益生产,减少了生产中的浪费,提高了成本效益。
3. 对冲压设备进行了节能改造,有效降低了能耗。
四、团队建设与培训1. 加强了团队技能培训,提升了员工的专业技能和工作效率。
2. 引入了跨部门协作机制,增强了团队间的沟通与合作。
3. 举办了多次技术交流会,促进了知识的共享和技术的创新。
五、市场响应与客户服务1. 加快了新产品的研发速度,以快速响应市场需求。
2. 提供了定制化服务,满足了客户的个性化需求。
3. 建立了客户反馈机制,及时收集并处理客户的意见和建议。
六、未来规划1. 继续跟踪国际先进的冲压技术,不断进行技术创新。
2. 加强与科研机构的合作,共同开发新的冲压工艺。
3. 扩大自动化生产线,进一步提升生产效率和产品质量。
在过去的一年里,我们团队在冲压工艺方面取得了显著的成绩,但也面临着新的挑战和机遇。
我们将继续努力,不断提升我们的工艺水平,为客户提供更优质的产品和服务。
感谢大家的聆听,我愿意回答任何问题。
冲压件材料利用率提升方法

冲压件材料利用率提升方法
冲压件是一种常用的制造零部件的方法,但是在制造过程中存在着材料浪费的问题。
因此,提高冲压件材料利用率是制造业者的一个重要任务。
下面介绍几种提升冲压件材料利用率的方法:
1. 设计优化:优化冲压件的设计,使得在一张原材料板上能够冲压出更多的零部件。
可以通过优化零部件的形状、布局等方式来实现。
2. 材料选择:选择合适的材料,使得在冲压过程中减少物料的浪费。
例如,选择更均匀的厚度、更强的韧性等材料。
3. 制造工艺:改进制造工艺,使得在冲压过程中能够更有效地利用原材料。
例如,采用更高效的工艺流程、优化设备的配置等方式来实现。
4. 回收再利用:将冲压过程中产生的废料进行回收再利用,实现材料的最大化利用。
可以通过设计有效的回收系统、采用合适的回收设备等方式来实现。
通过实施以上措施,可以有效地提高冲压件材料的利用率,降低材料浪费,从而实现生产成本的降低,提高企业的竞争力。
- 1 -。
精冲简介介绍

3. 加载材料
将材料放入精冲机中,并固定 好。
5. 后处理
对精冲件进行清洗、热处理、 表面处理等,以满足产品要求 。
Байду номын сангаас
精冲的应用领域
01
02
03
04
汽车制造
精冲工艺在汽车零部件生产 中应用广泛,如发动机零件、
传动系统零件等。
电子产品
手机、电脑等电子产品中的 精密零件常采用精冲工艺生产
。
航空航天
高精度、高强度的航空零部 件需要通过精冲工艺来制造。
市场竞争和成本压力
激烈的市场竞争和成本压力要求精冲技术不断提高生产效率和降低成本。需要引入先进的 生产管理模式,提高设备利用率,降低原材料和能源消耗,提高精冲技术的经济效益。
未来精冲技术的研究与发展方向
超精密精冲技术 复合精冲技术 智能精冲技术 绿色精冲技术
研究更高精度的精冲工艺和装备,满足微电子、光电子等领域 对超精密零件的需求。
近年来,随着技术的进步,伺服冲床在精冲领域的应用逐渐增多。伺服冲床具 有高速、高精度、高稳定性等优点,能够大幅提高精冲生产的效率和质量。
精冲模具技术
模具结构设计
精冲模具是精冲过程中的核心部件,其结构设计直接影响 精冲件的精度和表面质量。合理的模具结构能够降低材料 变形和开裂的风险,提高产品良品率。
将精冲技术与其他加工方法(如激光切割、电火花加工等)相 结合,形成复合精冲工艺,解决复杂零件的高效高精度加工问
题。
引入人工智能、大数据等先进技术,实现精冲过程的智能化监 控和优化控制,提高生产效率和产品质量。
研究环保材料和低能耗润滑方式,降低精冲过程中的环境污染 和资源消耗,实现精冲技术的绿色可持续发展。
- 1、下载文档前请自行甄别文档内容的完整性,平台不提供额外的编辑、内容补充、找答案等附加服务。
- 2、"仅部分预览"的文档,不可在线预览部分如存在完整性等问题,可反馈申请退款(可完整预览的文档不适用该条件!)。
- 3、如文档侵犯您的权益,请联系客服反馈,我们会尽快为您处理(人工客服工作时间:9:00-18:30)。
提升冲压材料利用率的工艺技术
汽车零部件约70%的金属零部件是通过冲压加工得到的,对于冲压而言,材料利用率高低直接影响着经济效益的高低。
应从以下方面提升其利用率。
1、工艺改进
1)料边缩减
对成品件和拉延件进行对比,利用AutoForm软件、UG软件等对拉延工艺进行成形分析,确认是偶减少工艺补充,或将拉延筋向里移动是否能实现该产品,已节约材料,并最终经过实验验证确认。
2)减少冲裁废料
冲裁所产生的废料为结构废料和工艺废料。
减少工艺废料有效措施是:设计合理的排样方案;选择合适的板料结构和合理的裁板法;利用废料做小零件等。
3)拉延改起伏成形
拉延是把平直毛料或工序件变为曲面形的一种冲压工序。
起伏成形时依靠材料的延伸使工序件形成局部凹陷或凸起的工序。
起伏成形中材料厚度的改变为非意图性的。
可以将拉延-修边-冲孔改为落料-成形-(冲孔+修边),以减小工艺补充,减低材料使用。
2、余料再利用
又称套材,是将使用后的多余来生产其它制件的方法,分为直接再利用和增大后再利用两种形式。
1)余料直接再利用
对较大的余料进行简单的工艺分析,进行简单的模具制造设计后,直接生产出较小制件。
2)增大余料后再利用
余料仅比制件小一点而不能被使用时,可以核算将余料增大,至能再利用生产出制件大小的定额,以节约材料。
3、新工艺
1)激光拼焊
拼焊技术经过多年的发展,技术逐渐成熟,采用拼焊板技术可以使零件数量减少66%,大大减少了模具数量,提高了材料的利用率。
常见拼焊的材料有钢板、铝合金板、夹层板和镁合金板。
2)摆剪
冲压制件形状各异,可以调整毛坯料形状达到材料利用率提升。
目前,开卷设备具有摆剪功能,可以通过设备实现梯形结构,也可以使用剪板机通过对定位方式改变进行角度剪切,实现直角梯形。
3)开卷落料模
目前,开卷设备普遍具有通过模具落料功能,可以通过增加落料模具实现弧度板料,实现材料利用率的提升。
(钢讯)
本文来源锌钢百叶窗:。