汽车车身冲压件材料利用率提高研究
汽车冲压件材料利用率提升方法研究 肖祥发

汽车冲压件材料利用率提升方法研究肖祥发摘要:随着我国加大对汽车发动机等汽车关键生产技术的研究投入,我国汽车生产技术方面,也取得了质的飞跃,这使得我国汽车在生产质量方面,也获得了巨大的提高,汽车生产领域的快速发展,对于推动我国城市化建设进程,促进我国社会经济的健康可持续发展,有着重要作用。
然而随着汽车领域的不断发展,其存在的问题也不断显现出来,其中尤以其生产过程中金属材料消耗量居高不下,金属材料利用率低问题最为严峻,尤其是在汽车冲压件设备的制造中,其金属的消耗量十分巨大,其极大的影响着汽车生产制造成本的降低,阻碍汽车生产效益的总体提高,因此加大对汽车冲压件金属材料利用率的工艺方法的相关研究,有着积极意义。
关键词:汽车冲压件;材料利用率;提升方法1重视冲压件原材料的购配在选择材料的时候,要根据汽车冲压件的类型及使用特点,合理地选择材料,不能为了追求高质量盲目选好,也不能为了节省成本一味选差。
不同的冲压件在使用过程中的受力特性是不一样的。
一般来说,汽车冲压件的选材最基本的要求就是要满足汽车零部件的使用性能、工艺性能,其次才是原材料的经济性。
具体来说,企业应该做好以下几个方面的工作:第一,价格类比,实现材料供应商多元化。
目前,国内钢材以宝钢公司的价格最高(性能最好),因此在保证冲压件质量的前提下,对一些B/C类冲压件原材料供应商进行调整,比价论证鞍钢、马钢等在低牌号钢材中使用的可行性。
第二,优化材料牌号,防止原材料高牌号低用。
在冲压件设计过程中,可能会选择高牌号材料。
因此在保证冲压件质量的前提下将部分零件的材料由高牌号调整为低牌号,最大化的利用材料的本身机械性能。
第三,建立专业的采购团队。
确定其组织战略地位,并根据项目管理理念设定合理的采购流程。
同时,在供应商管理方面,要定期重构,并对采购价格进行管理和优化。
2提高汽车冲压件材料利用率的有效工艺方法2.1优化产品设计要想有效提高汽车冲压件金属材料利用率,首先必须对产品的结构进行优化设计,在充分体现其工艺性的同时,提升其设计的经济性。
关于汽车车身的冲压工艺以及模具关键技术应用分析
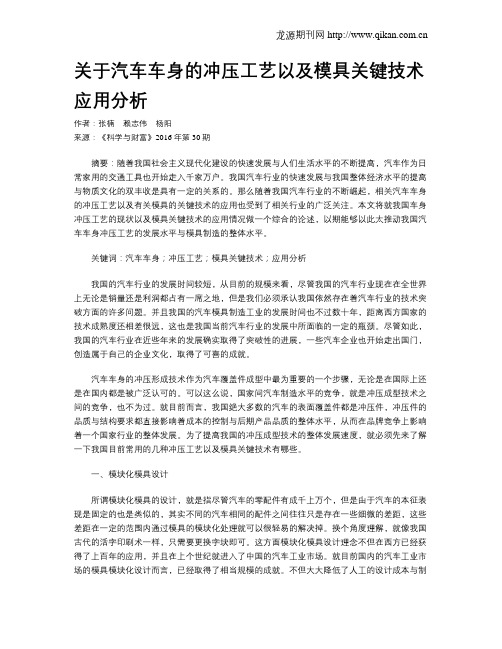
关于汽车车身的冲压工艺以及模具关键技术应用分析作者:张楠赖志伟杨阳来源:《科学与财富》2016年第30期摘要:随着我国社会主义现代化建设的快速发展与人们生活水平的不断提高,汽车作为日常家用的交通工具也开始走入千家万户。
我国汽车行业的快速发展与我国整体经济水平的提高与物质文化的双丰收是具有一定的关系的。
那么随着我国汽车行业的不断崛起,相关汽车车身的冲压工艺以及有关模具的关键技术的应用也受到了相关行业的广泛关注。
本文将就我国车身冲压工艺的现状以及模具关键技术的应用情况做一个综合的论述,以期能够以此太推动我国汽车车身冲压工艺的发展水平与模具制造的整体水平。
关键词:汽车车身;冲压工艺;模具关键技术;应用分析我国的汽车行业的发展时间较短,从目前的规模来看,尽管我国的汽车行业现在在全世界上无论是销量还是利润都占有一席之地,但是我们必须承认我国依然存在着汽车行业的技术突破方面的许多问题。
并且我国的汽车模具制造工业的发展时间也不过数十年,距离西方国家的技术成熟度还相差很远,这也是我国当前汽车行业的发展中所面临的一定的瓶颈。
尽管如此,我国的汽车行业在近些年来的发展确实取得了突破性的进展,一些汽车企业也开始走出国门,创造属于自己的企业文化,取得了可喜的成就。
汽车车身的冲压形成技术作为汽车覆盖件成型中最为重要的一个步骤,无论是在国际上还是在国内都是被广泛认可的。
可以这么说,国家间汽车制造水平的竞争,就是冲压成型技术之间的竞争,也不为过。
就目前而言,我国绝大多数的汽车的表面覆盖件都是冲压件,冲压件的品质与结构要求都直接影响着成本的控制与后期产品品质的整体水平,从而在品牌竞争上影响着一个国家行业的整体发展。
为了提高我国的冲压成型技术的整体发展速度,就必须先来了解一下我国目前常用的几种冲压工艺以及模具关键技术有哪些。
一、模块化模具设计所谓模块化模具的设计,就是指尽管汽车的零配件有成千上万个,但是由于汽车的本征表现是固定的也是类似的,其实不同的汽车相同的配件之间往往只是存在一些细微的差距,这些差距在一定的范围内通过模具的模块化处理就可以很轻易的解决掉。
汽车冲压件材料利用率提升方法研究 张鹏

汽车冲压件材料利用率提升方法研究张鹏摘要:在整个汽车开发过程中,冲压板料成本约占汽车白车身成本的36%,整车材料利用率每提升1%,整车的材料工艺消耗将减少约10kg,单车成本能降低55元,日韩车企在材料利用率方面明显优于国内车企,成本控制上优势明显。
以汽车车身上同样的20个关键冲压件的材料利用率为计算口径,日本丰田较好状态能达到63%,韩国现代较好状态能达到60%,而国内绝大部分车企是52%~57%,与日韩车企比较差距较大。
根据同步工程的分析,当利用率到达54%以上后,提高难度越来越大,需要在设计的初期投入更多时间和人力并开展前期同步工程对怎么提高利用率进行深入研究。
关键词:冲压件;工艺;材料利用率1材料利用率提升的价值据统计,整车材料利用率每提升百分之1,整车成本将降低 50~60 元。
当前主流车型的整车材料利用率为50~55,其中日韩车型的整车材料利用率较高,国内自主品牌车型的材料利用率较低。
整车材料利用率提升可以分为产品设计阶段、工艺设计阶段及模具调试阶段。
其中,模具调试阶段属于产品制造后期,对整车材料利用率提升贡献度最小;产品设计阶段和工艺设计阶段属于产品制造前期,对整车材料利用率提升贡献度大,应投入更多的资源进行提升。
2冲压成形节能优化方法分析冲压成形是通过对板料施加冲压力使其产生塑性成形的过程。
一般是通过成形装备(如液压机)对板料进行冲压加工。
成形过程中,在不同的工艺参数下金属的流变应力不同,冲压产品的成形能耗会随之变化,同时也对其成形质量有很大影响。
冲压成形装备是冲压产品加工的载体,也是其能量消耗的主要来源。
分析了冲压过程的能量流特性,建立了冲压成形过程的能量流模型,冲压成形的能量传递及转化过程如图1所示。
在冲压成形过程中,液压机通过一系列的能量传递与转化过程将电能转化为板料所需的成形能。
整个冲压过程的能量消耗包括板料的成形能耗、移动部件运动过程的能耗及控制系统的各能耗单元的能量损耗。
白车身材料利用率提升方案探讨

据的时候出现低级错误而引发一些施工的事故,导致质量降低。
4提高井下小修作业施工质量的方法4.1加大施工员工的培训力度,提高作业队伍的素质为了提高施工的质量,修井作业企业应该加强对施工员工的培训力度,通过提高作业队伍的素质,加强相关人员的质量意识,在进行作业操作培训之后,还需要定期或是不定期的对员工进行修井作业施工各要素的讲解,经过施工组织设计和工序的质量标准以及安全生产管理制度、技术等关键知识点的了解,让员工意识到油井质量保证的重要性,同时要加强相关的考核工作,以警醒相关的作业人员。
4.2加强施工作业人员的质量教育,提高作业人员质量意识为了提高施工作业人员的质量意识,我们需要不断加强对施工作业人员的质量教育,这不仅能够影响到修井企业的经济收入,更能够影响到整个企业的社会和经济效益,企业不仅仅要以自身作为出发点来加强施工作业人员的作业质量,也要对其他业主负责。
一个企业要想实现生存发展,首先就要保证企业的施工质量,所以修井单位需要严格的控制施工工序和相关的质量标准,通过培养人员的质量意识来加强施工队伍的质量建设,将拥有较强责任心的施工人员任命为班组长组织施工,提高队伍的施工技术,保证施工的质量。
4.3实行全面质量管理,提高质量控制管理水平在质量管理工作当中,最核心的问题就是质量保障,所以为了提高油井作业的质量控制和管理水平,就需要实行全面的质量管理,实现全员参加,以此来提高企业和业主的经济收益,以此来提高企业的竞争力。
通过全方位、全过程和全员参加的“三全管理”,来健全质量管理体系,保证井下作业施工的质量管理水平提高。
4.4加大下井工具管理力度油管企业一般都会对旧油管进行回收,但是在回收投入使用之前需要利用先进的设备和技术进行除垢处理,并且在处理之后对相关的参数进行检查,不合格的油管不能在油井作业地区投入使用。
油管在经过修复之后,需要将其与未修复的油管进行分开放置,并且建立相关的管理档案对油管进行科学的管理。
汽车车身冲压件材料利用率提高研究

大部分产 品工程师在设计零件 时, 往往使 零 件 有 突 出部 分 和一些 比较 尖锐 的 圆角 。
收稿 日期 : 00— 3—1 21 0 2
上海汽车
2 1 .5 0 00
・
4 ・ 7
进行 有效 排样 , 利用 率较 高 。 所 以我们 在 设 计 零 件 时 , 尽 量 将 零 件 设 计 应 成 成型类 零件 , 图 5 如 。零 件 经 过优 化 后 , 本来 需 要使 用拉 延工 艺 , 在 完 全可 用 成 型工 艺来 实 现 , 现 利 用率将 大 幅提升 。
~
况 一般 有两 种排 样方 式 , 图 1所示 。 如
40k 5 g左右 , 照 5 % 的材料 利用 率 , 按 0 需要 耗 费
70~ 0 g 0 90k的材 料 。若 能 提高利 用 率一 个 百分 点 的话 , 可 以节 约 原 材 料 将 近 1 2 g 这 在 当 则 5— 0k , 今汽 车车 型众 多 、 争 激烈 的市 场环 境 下 , 一 个 竞 是
汽 车 车 身 冲 压 件 材 料 利 用 率 提 高 研 究
曹力丰 李 正其 陈晓磊 ( 上汽集团股份有限公司技术中心, 上海 210) 084
【 摘要】 通过对数款车型白 车身材料利用率的 研究, 分析材料利用率优化的 可行性, 提出了 有效提高车
身材料利用率 的方案 。
【 bt c】 T r g es d e ti t n ao f I m t a,h a b i fh . A s at r ho ht uyo t i ao t W a rl t f s i y e m u h t f ul i rioB h z e i ee il ot i t
提高车身冲压件材料利用率的方法研究
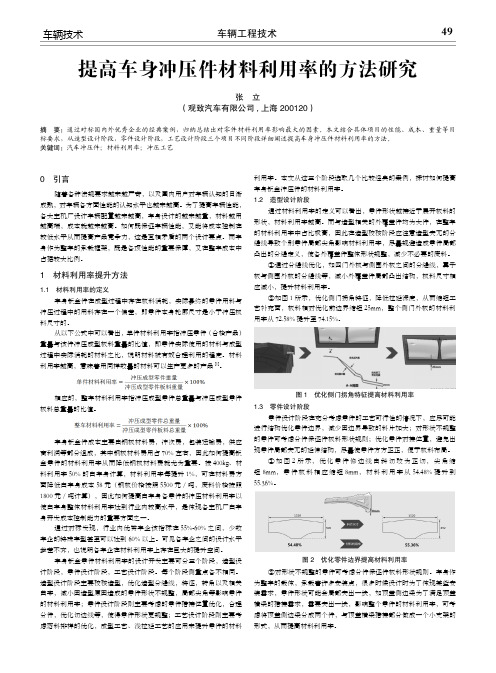
车辆工程技术49车辆技术0 引言随着各种法规要求越来越严苛,以及国内用户对车辆认知的日渐成熟,对车辆各方面性能的认知水平也越来越高。
为了提高车辆性能,各大主机厂设计车辆配置越来越高,车身设计的越来越重,材料越用越高端,成本就越来越高。
如何既保证车辆性能,又能将成本控制在较低水平从而提高产品竞争力,这是互相矛盾的两个设计要点。
而车身作为整车的承载框架,既是各项性能的重要保障,又在整车成本中占据较大比例。
1 材料利用率提升方法1.1 材料利用率的定义车身钣金件在成型过程中存在板料消耗,实际最终的零件用料与冲压过程中的用料存在一个偏差,即零件本身轮廓尺寸是小于冲压板料尺寸的。
从以下公式中可以看出,单件材料利用率指冲压零件(合格产品)重量与该件冲压成型板料重量的比值,即零件实际使用的材料与成型过程中实际消耗的材料之比,说明材料被有效合理利用的程度。
材料利用率越高,意味着用同样数量的材料可以生产更多的产品[1]。
相应的,整车材料利用率指冲压成型零件总重量与冲压成型零件板料总重量的比值。
车身钣金件成本主要由钢板材料费,冲次费,包装运输费,供应商利润等部分组成,其中钢板材料费用占70%左右,因此如何提高钣金零件的材料利用率从而降低钢板材料费就尤为重要。
按400kg、材料利用率50%的白车身计算,材料利用率每提升1%,可在材料费方面降低白车身成本58元(钢板价格按照5500元/吨,废料价格按照1800元/吨计算),因此如何提高白车身各零件的冲压材料利用率以使白车身整体材料利用率达到行业内较高水平,是体现各主机厂白车身开发成本控制能力的重要方面之一。
通过对标发现,行业内优秀车企该指标在55%-60%之间,少数车企的特殊车型甚至可以达到60%以上。
可见各车企之间的设计水平参差不齐,也说明各车企在材料利用率上存在巨大的提升空间。
车身钣金零件材料利用率的设计开发主要可分三个阶段,造型设计阶段,零件设计阶段,工艺设计阶段。
汽车冲压件材料利用率提升方法研究
汽车冲压件材料利用率提升方法研究摘要:随着人们生活水平的提高,人们对汽车的品质要求越来越高,导致汽车市场竞争日趋激烈,各汽车企业在追求先进制造技术提升自身产品竞争力的同时,成本压力越发增大,因此,成本控制成为各车企的重中之重。
对于汽车来说,冲压件作为整车构成的重要组成部分,占整车成本的10%~20%,占整车重量的30%~50%,所以,提高汽车车身冲压件的材料利用率,降低材料消耗,对降低整车成本,实现绿色制造意义重大。
关键词:汽车冲压件;材料利用率;提升方法引言目前由于汽车市场的竞争日益激烈,怎样有效降低汽车成本成为汽车制造企业重点研究内容之一,而汽车零部件中有大量的金属冲压零件,原材料成本又占了比较大的比重,一般一台白车身重量在300-450公斤左右,若按材料利用率50%计算,需用耗费600-900公斤的材料,如若提高材料利用率1个百分点,则可结余12-18公斤材料,在竞争激烈的市场环境下,是一个相当有效的降低成本手段和方法,所以怎样提高材料的利用率,其意义就变得重要起来。
下面根据目前国内汽车生产的工艺水平,结合多年生产实践经验,浅析一下提高材料利用率的具体工艺措施和方法。
1冲压件材料利用率技术表达式材料利用率是指合格品中包含的材料数量在材料(原材料)总消耗量中所占的比重,即已被利用的材料与实际消耗的材料之比,说明材料被有效利用的程度。
材料利用率越高,意味着用同样数量的材料可以生产更多的产品。
为贴合生产实际,本文对材料利用率术语作如下定义:材料利用率就是合格产品中某种材料的含量与制造该产品过程中该种材料耗用量的百分比率。
定义公式如下为:式中:r一材料利用率;N一合格产品中某种材料含量;W—制造过程中该种材料的耗用量。
2汽车冲压件材料利用率提升方法2.1废料再利用车身四门及侧围等含窗框或门洞部位的制件,可能产生较大片的废料,导致这些件的材料利用率极低。
针对某车型材料利用率低的现状,首先将该车型制件生产过程中产生较平整的边角料尺寸进行统计,形成数据库,对比现有制件规格明细,核查是否能废料再利用。
汽车冲压生产的排产优化研究
汽车冲压生产的排产优化研究摘要:汽车冲压工艺是汽车加工及制造的重要组成部分,汽车冲压件品质直接影响到汽车装配及实际使用性能,故对汽车冲压件工艺开发的控制至关重要。
关键词:汽车;冲压;优化引言汽车冲压件制造是汽车制造的重要组成部分,对冲压工艺技术质量的控制,有利于提升整个汽车制造质量。
冲压工艺是一种金属加工方法,利用冲压设备及模具对金属板料施加压力,使金属板料发生塑性变形及分离,从而获得设计预期的冲压零件。
汽车冲压件工艺的开发进程对整个项目进度有着重要的影响,在开发过程中应当严格把关,消除工艺及模具问题,尽可能降低冲压故障率,从而有效提升冲压件质量。
1冲压工艺定义在汽车的日常车身制造过程中,尤其对于大型的车身覆盖件来说,冲压成形工艺起到了关键作用。
因为大型的车身覆盖件尺寸结构较大,且形状较为复杂,相关的质量要求也较高,所以冲压工艺具有极大的优势。
当前轿车车身的覆盖件、客车各类骨架、载重货车货箱板、驾驶室以及车前钣金件等的制作都应用了冲压成形工艺。
2汽车冲压生产特点区别于普通的生产计划,汽车冲压生产有以下特点。
(1)模具准备时间长。
每种冲压零件都有一套专用模具,将模具从模具库中调运到生产线,并进行安置的准备时间需几十分钟到几小时不等,远长于单个零件几秒至十几秒的产出时间。
(2)大批量轮番生产。
由于模具的准备时间远长于单个零件的产出时间,并且准备过程对人力和能源的消耗均较大,因此在生产中应尽量减少换模,增大零件单次生产的批量,进行大批量轮番生产。
(3)换模时间不可忽略。
换模指在上一个零件生产完成后,将待生产零件的模具换上生产线并设置的过程。
换模时间在生产排产中需被纳入考虑。
(4)需求拉动。
汽车生产是典型的需求拉动型产业,冲压车间生产计划必须满足下游车间对零件的需求,否则将造成下游生产无法按计划进行。
基于以上几个特点,汽车冲压生产规则特殊,需求不固定,传统的生产计划和排产研究难以满足汽车冲压生产的排产需求。
浅析如何有效提高汽车车身冲压件材料利用率
浅析如何有效提高汽车车身冲压件材料利用率作者:郝腾蛟崔玉梅王天福来源:《科学与财富》2016年第16期摘要:本文主要论述了汽车车身冲压件材料利用率的问题,分析了在现有的技术条件下,如何更好的采取有效的措施来提高汽车车身冲压件材料利用率,希望能够为今后的相关工作提供参考。
关键词:汽车;车身;冲压件;材料利用率一、前言随着我国汽车行业的不断进步,很多部位的零部件研究也在不断深入,车身冲压件材料的利用率关乎汽车生产制造的品质和水平,因此,必须要针对汽车车身冲压件材料利用率进行分析。
二、我国汽车冲压件行业的现状随着汽车工业的快速发展,冲压加工作为最基本、最传统、最重要的金属加工方法之一,今后10~20年在我国汽车行业中将得到更好的发展。
在汽车的构成中,车身及发动机、底盘一起被称为汽车的三大总成。
据统计,客车、轿车和多数专用汽车车身质量约占整车自身重量40%~60%,轿车车身大约由400个左右的冲压件焊接而成。
钢板材料在不同车型中占汽车自身质量的51%~65%。
目前国内专业从事冲压件的大型企业很少,基本上是一些中小企业,冲压件以中小冲为主。
而汽车行业的大型冲压件,以拉深为主,在我国这部份冲压件主要集中在汽车厂、拖拉机厂、飞机制造厂等大厂,独立的大型冲压拉深厂还不多见。
而对我国汽车行业零部件类或车身中的中小冲压件类来讲,,随着汽车业的迅速发展而得到迅速发展,目前一些汽车厂或拖拉机厂的周围都有许多这样的小厂。
冲压件是汽车的重要组成部分,据数据统计,平均每辆车上包含1500多个冲压件,除了大型覆盖件外,还包括车门、侧围、盖板、底架、地板等,其中每辆车中车身冲压件(不包括焊接)的平均价格在1.5万元左右,底盘、发动机等部分的冲压件价格平均在1万元左右。
而目前国内冲压设备的利用率一般在85%左右,产能情况为:一般冲压4~4.5次/min,多工位压机11~15次/min,级进模20~25次/min。
由此可知,我国的冲压件行业的发展前景非常乐观。
如何提高汽车冲压件材料利用率探究
如何提高汽车冲压件材料利用率探究通过介绍汽车金属冲压件工艺措施和方法,改进提高材料的利用率,从而达到降低成本,提高经济效益的最终目的。
标签:汽车;冲压件;材料利用率目前由于汽车市场的竞争日益激烈,怎样有效降低汽车成本成为汽车制造企业重点研究内容之一,而汽车零部件中有大量的金属冲压零件,原材料成本又占了比较大的比重,一般一台白车身重量在300-450公斤左右,若按材料利用率提高材料利用50%计算,需用耗费600-900公斤的材料,如若提高材料利用率1个百分点,则可结余6-18公斤材料,在竞争激烈的市场环境下,是一个相当有效的降低成本手段和方法,所以怎样提高材料的利用率,其意义就变得重要起来。
根据目前国内汽车生产的工艺水平,结合多年生产实践经验,浅析一下提高材料利用率的具体工艺措施和方法。
1 提高产品设计的工艺性和经济性产品设计时应充分考虑材料的合理利用,采用合理的总成分块和零件结构,充分考虑产品的加工工艺性和经济性。
工艺人员在工艺性审核时,除审核期加工工艺性外,还要认真分析产品的经济性,对材料利用率低的零件提出合理建议,并同产品设计员共同研究,改进产品的设计结构。
合理的产品结构,是提高材料利用率的必要条件。
图12 采用最经济的工艺方法工艺设计时,应合理利用材料,用最经济的工艺方法加工合格的产品,合理的工艺设计,是提高材料利用率的重要环节其具体措施如下:(1)优先采用少无废料的排样法冲裁在确定排样的工艺方案时,优先采用少,无废料冲裁。
如图1。
如产品结构不易于少无废料冲裁时,工艺人员应同产品设计人员共同研究产品结构提出改进,以便取得更高的材料利用率。
(2)确定最佳的工艺排样工艺设计时应该做多种排样方案进行比较分析在,从中选择出最经济利用率最高的排样方案。
确定落料搭边时,在保证模具不受损伤和产品质量的前提下选用小的搭边值。
(3)充分利用套裁工艺设计时,根据材料的性能和零件的形状、尺寸规格,要充分考量在某个零件产生的余(废)料进行生产其它产品,可在落料序可同时冲出两种零件,这样不但可节约材料,也可节约工装设计、制造费用及加工工时。
- 1、下载文档前请自行甄别文档内容的完整性,平台不提供额外的编辑、内容补充、找答案等附加服务。
- 2、"仅部分预览"的文档,不可在线预览部分如存在完整性等问题,可反馈申请退款(可完整预览的文档不适用该条件!)。
- 3、如文档侵犯您的权益,请联系客服反馈,我们会尽快为您处理(人工客服工作时间:9:00-18:30)。
由于有这 些突出部分存在, 零件 无法更紧密 地排样, 导致利用率不够理想。优化方案如图 2, 设计时可尽量避免零件有突出部分以及尽可能加 大圆角。 1. 2 分离零件
在车身设 计时也会存在这样的零件, 有突出 部分, 但为了 保证零件 功能无法 将其直接 去掉。 对于这样的零件可以考虑将其拆成两 个零件, 如 图 3所示。
参考文献
1 刘惟信. 汽车设计 [ M ] . 北京: 清华大学出版社, 2001. 2 [ 德 ] F. S chm elz等著, 伍德荣等译. 万向节与传动轴 [ M ] . 北京: 北京理工大学出版社, 1997.
# 50#
上海汽车 20101 05
=主题词 > 材料利用率 冲压 汽车
0 引言
由于汽车市场竞争的日益加剧, 怎样有效降 低汽车成本成为企业着重考虑的内容。而汽车零 件中有大量的钣金冲压零件, 原材料成本又占了 比较大的比重, 一般一台白车身的钣金重量在 350 ~ 450 kg左右, 按照 50% 的材料利用率, 需要耗费 700~ 900 kg的材料。若能提高利用率一个百分点 的话, 则可以节约原材料将近 15 ~ 20 kg, 这在当 今汽车车型众多、竞争激烈的市场环境下, 是一个 相当可观的降本资源, 所以怎样更好地优化和提 高材料利用率, 其意义就变得十分重大。
1 车身设计时的材料利用率优化
在车身早期造型和零件设计时, 零件的利用 率常常会被忽视。经过对 现有车型的研究, 我们 在新车型的设计中提出几点有效控制材料利用率 的优化方案。 1. 1 局部调整零件形状
大部分产品工程师在设计零件时, 往往使零 件有突出部分和一些比较尖锐的圆角。
针对此类零件根据不同模具制造商的具体情 况一般有两种排样方式, 如图 1所示。
工艺材料
必要的废料产生, 利用率有较大提升。 第一种方 式: 将料片形状优化后 可进行连续
落料, 灰色部分为每落一次料可节省的料片面积, 如图 9。
图 7 小零件与大零件结合
2 冲压模具工艺设计优化
在零件设计完成后, 就需要 对零件进行模具 工艺的设计, 工艺制定的好坏也会对材料利用率 产生较大的影响。经过对多款车身零件模具工艺 的研究, 提出以下几个方面的优化建议。 2. 1 改变坯料形状
以尾门外板为例, 很多模具制造商为了方便, 大多使用方形料片。
但是如果将工艺进一步优化, 将方形料片改 为梯形, 可将利用率提高约 5% 左右。
如图 8, 门外板两块大型的三角形废料将会省 下来, 材料利用更合理。
图 8 门外板形状
2. 2 增加落料 在拉延工艺前增加落料工序, 可有效控制不
图 9 优化料片形状
通过对两种方案零件排样方案的 对比, 我们 可以明显地看出分成两个零件后, 废料较少, 利用 率相对较高。
当然变成两个零件后, 模具费用增加了, 不过 根据零件所用的材料的单价 不同, 当汽车产量达 到一定数值后, 在材料上节省的费用就会显现出 来, 如图 4所示。
图 5 优化零件结构
1. 4 造型优化 车身造型 的优劣 也直 接影响 到整 车的 利用
图 11是使用手工方式进行排样后的结果, 图 12是计算机算出来的利用率最高的排样方式, 利 用率提高了近 12% 。
上海汽车 20101 05
# 49#
工艺材料
图 11 手 工排样
图 12 计算机排样
3 冲压过程中的废料再利用
很多大型零件如侧围、门板等零件落料后产
生的废料较大。经统计这样的大型废料单车重量 约 13 kg, 如在生产过程中进行有效的收集, 可使用 其它材料和 料厚相同 的小零 件对其 进行再 次利 用, 从而提升整车的材料利用 率。这个方案我们 已经在现有上市的车型上进行操作了, 先找到材 料和料厚相同的小零件, 然后在大型废料上制定 排样方式, 目前侧围废料已经被再次利用起来了。
工艺材料
汽车车身冲压件材料利用率提高研究
曹力丰 李正其 陈晓磊 (上汽集团股份有限公司技术中心, 上海 201804)
=摘要 > 通过对数款车型白车身材料利用率的研究, 分析材 料利用率优 化的可行性, 提出 了有效提 高车
身材料利用率的方案。
=Ab stract> T hrough the study of the ut ilization ratio of B IW m ateria,l the feasib ility of the improvem en t o f the utilizat ion ra tio is ana lyzed, and som e so lut ions are prov ided.
( 上接第 46页 )
5 结语
通过对早期以及现代转向管柱 的设计变化, 分析了万向节引入到管柱设 计中的原因, 同时分 析了各种万向节的工作原理 及发展趋势, 总结为 以下几点。
( 1) 万向节主要被应用在轿车的零部件开发 中, 驱动轴、转向管柱都包含不同的万向节结构。
( 2) 十字轴万向节是最被广泛 费用节省
1. 3 优化零件结构 根据模具工艺的设计原理, 拉延工艺一般是
压料后成型, 在拉延设计时, 需要增加大量的工艺 补充面, 废料较多, 利用率相应较低, 而成型工艺 是在落料后直接成型, 不需要压料面, 而且落料可
# 48#
图 6 优化方案
1. 5 零件合并制造 在设计大 型零件时, 我们常常会 发现有大片
收稿日期: 2010- 03- 12 上海汽车 20101 05
# 47#
工艺材料
图 2 优化方案
进行有效排样, 利用率较高。 所以我们 在设计零件时, 应尽量 将零件设计
成成型类零件, 如图 5。零件经过优化后, 本来需 要使用拉延工艺, 现在完全可用成型工艺来实现, 利用率将大幅提升。
图 3 零件拆分
第二种方式: 一张板料出两件, 和一张板料出 单个零件相比较, 阴影部分的废料将被节省下来, 如图 10。
图 10 优化料片
这些方案 由于需要增加一套落料模 具, 故一 般针对大中型零件, 如前盖内外板等。 2. 3 利用排样软件
由于车身 零件一般结构复杂, 在 坯料展开后 形状千奇百怪。如果以传统的设计方法手工来排 样的话, 不仅效率低, 误差大, 而且利用率常常也 无法得到保证。而使用计算机辅助技术则能更快 更精确地找到最优化排样方案。
率, 车身几乎所有的大 型覆盖件都在造型锁定的 同时, 外形轮廓也相应被锁定 了。零件和零件之 间的分隔线决定了零件的形状, 也决定了零件利 用率的高低。图 6是翼子板、前盖、侧围之间分隔 线的一个比较典型的案例, 优化方案是通过调整 分隔线将翼子板上面局部分离出来给 侧围, 这样 翼子板不但利用率有大幅提高, 而且工艺也相对 简单多了, 另对其他两个零件没有太大的影响。
4 结语
综上所述, 能提升车身材料利用 率的方案有 很多, 且在设计的前期考虑利用率优化是最有效, 节省成本最多, 越到后 面材料利用率的优化越是 困难。所以我们在设计的初期就应该投入更多时 间和人力对怎样提高利用率进行研究, 对降低整 车成 本, 有效 提 升自 主品 牌竞 争力 有 着重 大的 意义。
材料浪费, 如门板的窗框部分、顶盖和顶盖加强板 的天窗部分等, 为了利用这些部分, 可采用套材。 如图 7, 在空白区域加上一个小型零件与大零件一
上海汽车 20101 05
起冲压制造, 有效提高 利用率。而这个方案必须 在前期产品工程师设计零件 时就要得到重视, 为 了配合大零件, 不至于影响合做后的成型性, 小零 件需要做一些成型性的调整。
( 3) 单十字万向节非等速万向节, 需要通过两 个万向节并在一定工作条件下才能实现等速。
( 4) 等速万向节中的球笼式等速万向节以及 双联式万向节已经用于转向管柱的开发中。
( 5) 等速万向节是未来管柱开发的趋势, 最新 开 发的汤普森万向节在摩擦和振动方面都超过普
通等速万向节, 未来也有可能规模化应用。