动平衡分析过程
动平衡试验方法

动平衡试验方法全文共四篇示例,供读者参考第一篇示例:动平衡试验方法是一种用于检测机械设备是否平衡的方法,其原理是根据物体在平衡状态下所产生的惯性力和重力相互平衡的特性进行试验。
在现代工程领域中,动平衡试验是非常重要的一项工作,它能有效地检测出设备是否存在不平衡的问题,从而避免设备在运行过程中产生震动、噪声等不良影响,延长设备的使用寿命。
动平衡试验方法主要包括两种:静平衡试验和动平衡试验。
静平衡试验是通过在设备上放置配重来使设备保持平衡状态,通常适用于固定不动的设备,如风扇、轴承等。
动平衡试验则是通过在设备运行时进行试验来测量设备的振动情况,以判断是否存在不平衡问题,适用于旋转设备,如风车、发电机等。
在进行动平衡试验时,需要一些专业的技术和设备。
首先需要对设备进行全面的检查,包括轴承、联轴器、零部件等的检查,确保设备运行时没有其他故障。
其次需要安装好动平衡仪或振动测试仪,并调整好其参数,使其能够准确测量设备的振动情况。
然后需要根据试验数据进行分析,找出设备的不平衡量,并根据结果进行调整,直到设备达到平衡状态。
动平衡试验的重要性在于它能有效地检测出设备的不平衡问题,避免设备在运行过程中产生噪音、振动等负面影响,延长设备的使用寿命。
动平衡试验还可以提高设备的运行效率,降低能耗,提高生产效率,减少维修次数,降低维修成本。
动平衡试验是保证设备正常运行的重要环节,通过对设备进行动平衡试验可以及时发现并解决设备的不平衡问题,确保设备运行平稳、高效。
在进行设备维护和保养时,动平衡试验是一项必不可少的工作。
第二篇示例:动平衡试验方法是在机械设备制造和运行过程中广泛使用的一种重要技术手段。
它通过检测和调整设备旋转部件的质量分布,使设备在旋转时达到动态平衡,减少振动和噪音,提高设备的运行稳定性和安全性。
在工业生产中,动平衡试验方法被广泛应用于各种旋转机械设备的生产加工和维护保养过程中,是保证设备可靠运行的重要环节。
一、动平衡试验方法的基本原理动平衡试验方法的基本原理是根据平衡条件,通过测定旋转部件的振动和相位来诊断问题,并采取调整措施,使设备在旋转时避免不稳定的振动。
动平衡的原理和作用(一)

动平衡的原理和作用(一)动平衡的原理和作用什么是动平衡?动平衡是一种力学原理,它描述了一个物体在运动过程中保持平衡状态的能力。
在物体运动过程中,各个部分的质量分布会影响物体的平衡性。
动平衡通过调整物体的质量分布,使得物体在高速旋转或振动时不产生不稳定的情况。
动平衡的原理动平衡的原理可以总结为以下几点:1.质量平衡:物体的质量必须均匀分布在其周围,以避免产生不平衡的力矩。
2.力矩平衡:物体受到的合力矩必须为零,即物体的质心和旋转轴必须保持对称。
3.惯性平衡:物体的质心和旋转轴在运动中必须保持相对静止。
动平衡的作用动平衡在实际生活和工程中有广泛的应用,其作用主要体现在以下几个方面:1.提高稳定性:动平衡可以降低物体在高速旋转或振动时受到的不稳定力矩,提高物体的稳定性和安全性。
2.减少振动:动平衡可以减少物体在运动过程中的振动幅度,降低噪音和磨损,延长物体的使用寿命。
3.提高效率:动平衡可以降低能量损耗,提高物体的运动效率和整体性能。
4.预防事故:动平衡可以预防由于物体不平衡引起的事故,如机械设备的运转失灵等。
实现动平衡的方法实现动平衡可以采用以下几种方法:•质量调整:通过调整物体的质量分布,使得物体在旋转或振动时质心和旋转轴保持对称。
•平衡校正:通过添加或减少适当的质量来平衡不平衡的物体,以达到力矩平衡和惯性平衡。
•振动消除:针对振动问题,采用减振措施,如添加减振器、优化结构设计等方式来减少振动幅度。
•动态平衡:对于高速旋转的物体,采用动态平衡机等专用设备进行校正调整,以达到动平衡的要求。
结语动平衡是一项重要的力学原理,对于保证物体的稳定、安全和高效运行具有重要作用。
了解动平衡的原理和实现方法,可以帮助我们更好地应用于实践中,在工程设计和生产过程中提高产品的质量和性能。
动平衡理论与方法讲解
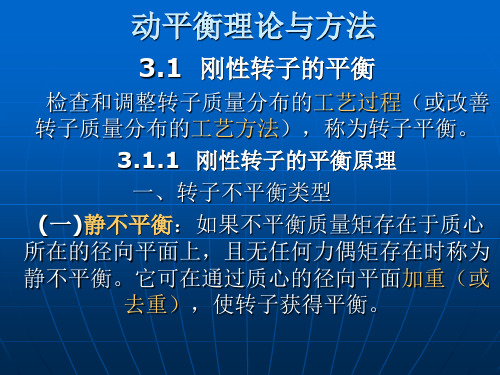
(二) 幅相影响系数法
对于转子——轴承系统,在确定的转速下, 转子的不平衡振动Ai与其不平衡量Uj之间可用一 系数 ij 相联系起来: Ai ij U j
式中 i 1,2,, P;j 1,2,, q , ij 反映了转子在i处的不平衡振 动和j处不平衡量之间的内在联系,称为线性影响系数,
• 单平面加重 设A轴承的原始振动为 A0 a0 在Ⅰ平面加试重 P P 后,A轴承的振动为 A01a01 因试重引起的振动变化应 为:M Mm A A
01 0
2. 影响系数计算
由定义得知:
AI
M m p Mm P Pp 10
M P
M 1m1 1 0
F11 、F12
如果转子上有多个不平衡离心力存在,亦可同样 分解到该选定的Ⅰ、Ⅱ平面上再合成,最终结果 都只有两个不平衡合力( A 、 B )(Ⅰ、Ⅱ平 面上各一个)。到此校正转子不平衡的任务就简 单了,即仅分别在Ⅰ、Ⅱ平面不平衡合力 A 、B 的对侧(反方向)加重(或去重),使其产生的 附加离心力与上述不平衡合力相等,这样转子就 达到了平衡。 (3) 分解为对称及反对称不平衡力(图3-8) 将Ⅰ、Ⅱ平面内的 A 、 B 力同时平移到某任一个 点0上,由矢量三角形、可以看出:; B Bs BD A As AD
式中:G为不平衡重量,F0为不平衡离心力,因 此,对于一失衡转子,若阻尼一定,r,w一定, 则不平衡离心力F0与不平衡重量G成线性(比例) 关系,即该系统的振幅y与不平衡重量G成线性 关系。(3-7)式还表明,对于已知体系,阻尼 和wn一定,当w不变时,扰动力与振幅之间的相 位差角也就一定了,即振动(振幅)滞后于干扰 力的角度不变(图3-18)。
动平衡原理及案例 PPT
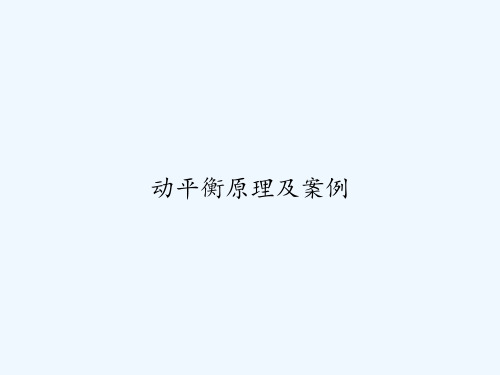
0.28 〈15KW 15-75KW 〉75KW
参考GB6075-85以及VDI2056,适用于转速在600-12000转/分的各种机器
振源分析-故障诊断
1.诊断方法之一:幅值谱分析
典型的不平衡频谱
2.诊断方法之二:轴频振动相位分析:
位移幅值 位移相位
垂直方向: 156
345
水平方向: 57 相位稳定性:好
2002-12-25振动测试数据(测点:轴承1)
加速度 速度 位移 高频加速度
峰值ms-2 有效值mm/s 峰峰值um 有效值ms-2
第一次 22.1
14.8
408
3.2
第二次 22.7
15.47 398
2.77
报警线 10
11.2
160
2.0
目前值 15
属不合 格设备
振动评价标准
ISO2372振动质量评级标准
动平衡操作过程中 要 注意什么?
o 确认是否动平衡问题:
看频谱和相位
旋
o 相位的计量方向:
转 方
迎着旋转方向看
向
正相位角 反光片
怎样选择动平衡测量参数?
中低速机器,用位移或速度测量 高速机器, 用速度或加速度测量
怎样判断试重是否可用?
加 试 重 前 后 的幅 值 差 <25%幅 值 差 >25%
0.28 〈15KW 15-75KW 〉75KW
参考GB6075-85以及VDI2056,适用于转速在600-12000转/分的各种机器
平衡后风机轴承振动频谱 风机轴频振动已大幅下降到与电机轴频振动相当(平衡前为3倍)
(mm/s)
小型机器 中型机器 大型机器 透平机器
动平衡计算知乎

动平衡计算知乎
动平衡计算是一项涉及转子平衡的过程,该过程使用专门的设备来测量和校正转子的不平衡部分。
在执行动平衡检测前,需要了解动平衡检测专业术语和动平衡计算公式。
首先,让我们了解一下动平衡的相关术语:
- 转子平衡品质:这是衡量转子平衡优劣的指标,其公式为G=eper·Ω/1000,其中G表示转子平衡品质,单位是mm/s;eper代表转子允许的不平衡率,单位是gmm/kg或转子质量偏心距um;Ω代表转子最高工作转速的角度,单位是-2π·m/60。
- 转子单位质量的允许不平衡度(率):这个参数可以通过转子平衡品质和转子最高工作转速来计算,公式为eper=G·1000/Ω=G·1000·60/(2π·n)≈9549·G/n,单位是g·mm/kg或um。
接下来是不平衡量的简化计算公式:M=9549MG/r×n,其中M表示转子质量单位(kg),G表示精度等级选用,r表示校正半径单位(mm),n表示工件的工作转速单位(rpm),m表示不平衡合格量单位(g)。
1。
发电机现场动平衡过程及分析
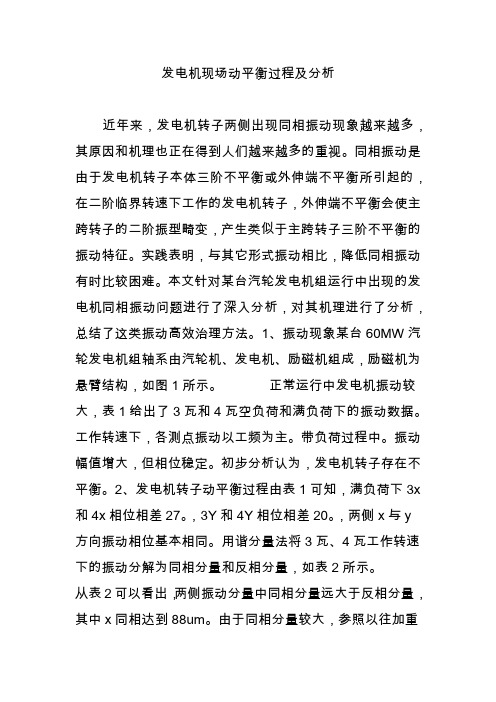
发电机现场动平衡过程及分析近年来,发电机转子两侧出现同相振动现象越来越多,其原因和机理也正在得到人们越来越多的重视。
同相振动是由于发电机转子本体三阶不平衡或外伸端不平衡所引起的,在二阶临界转速下工作的发电机转子,外伸端不平衡会使主跨转子的二阶振型畸变,产生类似于主跨转子三阶不平衡的振动特征。
实践表明,与其它形式振动相比,降低同相振动有时比较困难。
本文针对某台汽轮发电机组运行中出现的发电机同相振动问题进行了深入分析,对其机理进行了分析,总结了这类振动高效治理方法。
1、振动现象某台60MW汽轮发电机组轴系由汽轮机、发电机、励磁机组成,励磁机为悬臂结构,如图1所示。
正常运行中发电机振动较大,表1给出了3瓦和4瓦空负荷和满负荷下的振动数据。
工作转速下,各测点振动以工频为主。
带负荷过程中。
振动幅值增大,但相位稳定。
初步分析认为,发电机转子存在不平衡。
2、发电机转子动平衡过程由表1可知,满负荷下3x 和4x相位相差27。
,3Y和4Y相位相差20。
,两侧x与y方向振动相位基本相同。
用谐分量法将3瓦、4瓦工作转速下的振动分解为同相分量和反相分量,如表2所示。
从表2可以看出,两侧振动分量中同相分量远大于反相分量,其中x同相达到88um。
由于同相分量较大,参照以往加重经验,首先在发电机两端施加对称型式配重:P3=1.14kg∠24°,P4=1.05kg∠24°。
加重后,满负荷下振动明显减小,但是临界转速下振动增大。
在发电机两端加同相配重导致工作转速和临界转速下的振动出现矛盾,无法兼顾。
去掉发电机加重,改在励磁机上加重pA=250g∠60°如图2所示。
本次加重后,满负荷下振动明显降低而临界转速下振动变化不大,轴系振动达到优秀,动平衡工作至此结束。
表3给出了机组动平衡过程。
3、发电机同相振动的深入分析本次动平衡,在发电机和励磁机上的两次加重均降低了工作转速下的振动。
但是,发电机本体上的加重却使临界转速下振动明显增大,3x振动达136um,而励磁机上加重后I临界转速下振动变化不大。
单缸柴油机动平衡机的原理
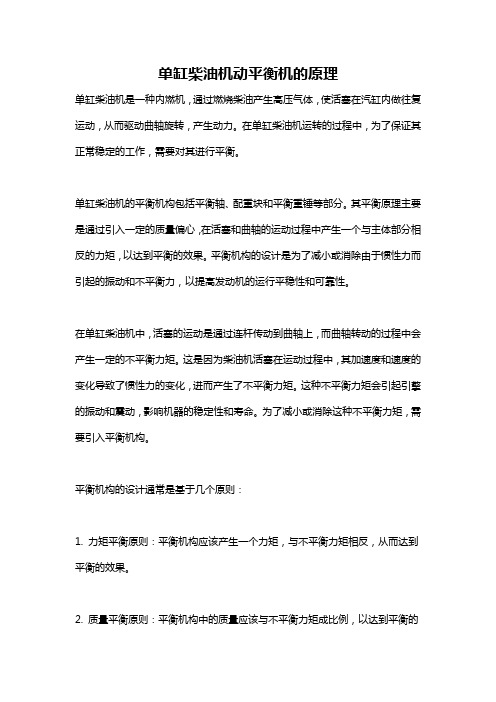
单缸柴油机动平衡机的原理单缸柴油机是一种内燃机,通过燃烧柴油产生高压气体,使活塞在汽缸内做往复运动,从而驱动曲轴旋转,产生动力。
在单缸柴油机运转的过程中,为了保证其正常稳定的工作,需要对其进行平衡。
单缸柴油机的平衡机构包括平衡轴、配重块和平衡重锤等部分。
其平衡原理主要是通过引入一定的质量偏心,在活塞和曲轴的运动过程中产生一个与主体部分相反的力矩,以达到平衡的效果。
平衡机构的设计是为了减小或消除由于惯性力而引起的振动和不平衡力,以提高发动机的运行平稳性和可靠性。
在单缸柴油机中,活塞的运动是通过连杆传动到曲轴上,而曲轴转动的过程中会产生一定的不平衡力矩。
这是因为柴油机活塞在运动过程中,其加速度和速度的变化导致了惯性力的变化,进而产生了不平衡力矩。
这种不平衡力矩会引起引擎的振动和震动,影响机器的稳定性和寿命。
为了减小或消除这种不平衡力矩,需要引入平衡机构。
平衡机构的设计通常是基于几个原则:1. 力矩平衡原则:平衡机构应该产生一个力矩,与不平衡力矩相反,从而达到平衡的效果。
2. 质量平衡原则:平衡机构中的质量应该与不平衡力矩成比例,以达到平衡的效果。
3. 角度平衡原则:平衡机构中的质量应该根据曲轴的旋转角度进行调整,以达到平衡的效果。
在实际的设计中,常见的平衡机构包括平衡轴、配重块和平衡重锤等。
平衡轴是一个与曲轴平行的轴,可以通过传动装置与曲轴连接。
它的作用是在运动过程中产生一个与曲轴不平衡力矩相反的力矩,从而达到平衡的效果。
配重块和平衡重锤是通过在曲轴或连杆上增加一定的质量偏心,以减小或消除由于活塞和连杆的运动产生的不平衡力矩。
平衡机构的设计需要考虑多个因素,包括活塞质量、连杆长度、曲轴半径等。
这些因素与柴油机的排量、功率和转速密切相关。
在实际设计过程中,需要根据柴油机的工作条件和性能要求,通过数学建模和实验验证,确定最佳的平衡机构参数。
总之,单缸柴油机动平衡机的原理是通过引入一定的质量偏心,产生一个与不平衡力矩相反的力矩,从而减小或消除由于活塞和连杆运动所产生的不平衡力矩。
风机叶轮动平衡方法
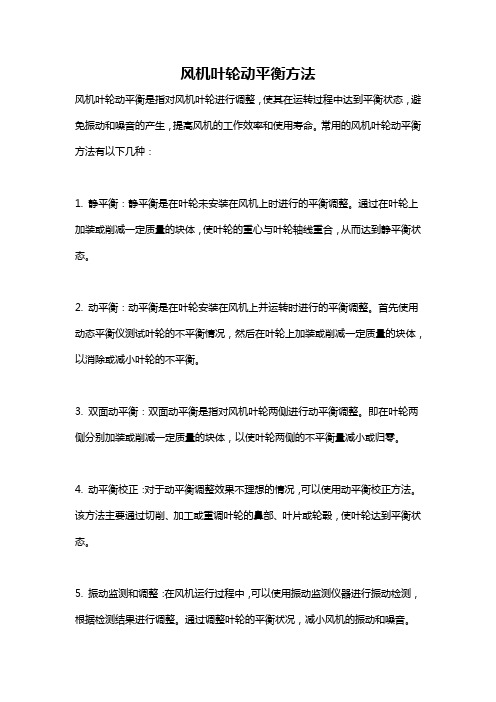
风机叶轮动平衡方法
风机叶轮动平衡是指对风机叶轮进行调整,使其在运转过程中达到平衡状态,避免振动和噪音的产生,提高风机的工作效率和使用寿命。
常用的风机叶轮动平衡方法有以下几种:
1. 静平衡:静平衡是在叶轮未安装在风机上时进行的平衡调整。
通过在叶轮上加装或削减一定质量的块体,使叶轮的重心与叶轮轴线重合,从而达到静平衡状态。
2. 动平衡:动平衡是在叶轮安装在风机上并运转时进行的平衡调整。
首先使用动态平衡仪测试叶轮的不平衡情况,然后在叶轮上加装或削减一定质量的块体,以消除或减小叶轮的不平衡。
3. 双面动平衡:双面动平衡是指对风机叶轮两侧进行动平衡调整。
即在叶轮两侧分别加装或削减一定质量的块体,以使叶轮两侧的不平衡量减小或归零。
4. 动平衡校正:对于动平衡调整效果不理想的情况,可以使用动平衡校正方法。
该方法主要通过切削、加工或重调叶轮的鼻部、叶片或轮毂,使叶轮达到平衡状态。
5. 振动监测和调整:在风机运行过程中,可以使用振动监测仪器进行振动检测,根据检测结果进行调整。
通过调整叶轮的平衡状况,减小风机的振动和噪音。
需要注意的是,风机叶轮动平衡的方法选择要根据具体情况和要求,有时可能需要结合不同的方法进行调整。
同时,在进行叶轮动平衡调整时,要保证操作安全,并严格按照相关标准和规范进行操作。
- 1、下载文档前请自行甄别文档内容的完整性,平台不提供额外的编辑、内容补充、找答案等附加服务。
- 2、"仅部分预览"的文档,不可在线预览部分如存在完整性等问题,可反馈申请退款(可完整预览的文档不适用该条件!)。
- 3、如文档侵犯您的权益,请联系客服反馈,我们会尽快为您处理(人工客服工作时间:9:00-18:30)。
QX-C184动平衡分析过程一.创建三维模型
1)曲轴
2)滚子
3)主平衡块
4)副平衡块(考虑到实际情况,取4片副平衡块)
5)铝脚
二.按实际情况Proe装配(注意基体,销钉连接,圆柱连接等)
三.每个零件单位和密度设置(注意更改单位,保证单位统一)
1)整体质量M
2)质心至转动轴距离L
3)使用关系式建立不平衡量关系式(U=重量M*质心至转动轴距离L)
四.敏感度分析
变量:主平衡块突出高度H
目标值:不平衡度U(即关系式里的b)
五.敏感度分析结果
从分析结果看,当主平衡块突出高度H=6.1mm时(即总高度H总=16.1mm),
QX-C184有最小不平衡度U=5.7g*mm,完全满足国家微型电机转动标准。
说明:以上只是针对只有一个变量(主平衡块)的设计过程,但实际情况:变量有主平衡块和副平衡两个同时变化,这时候的设计过程就更难了。
由于难度较大,未能列出。
大体情况如下;
1)PROE三维建模(曲轴、滚子、主平衡块、副平衡块、铝脚)
2)PROE装配(注意更改单位、基体、销钉连接、圆柱连接)
3)进入Mechanica分析模块,创建伺服电动机(2850r/min),重力矩G,外力F,弹簧阻尼C等;
4)执行伺服电动机,动态分析,测量旋转质心的径向力F和径向力矩M,创建测量参数;
5)进入标准模块,运动分析,建立最大径向力Fmax和和最大径向力矩Mmax; 6)进行多目标多变量优化设计(目标值:Fmax、Mmax和总重量M总;变量值:主平衡块突出高度H主和副平衡块总高度H副)
7)最后经过计算机的对阵组合计算,得到最优值,并最终确定主副平衡块
尺寸。