单向点啮合蜗轮凸齿面接触状况分析
《机械设计》第12章 蜗杆传动
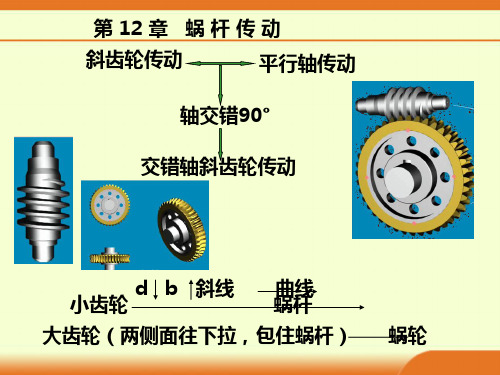
阿基米德蜗杆:αx=20°
标准值
法向直廓蜗杆、渐开线蜗杆:αn=20°
s
pz=zpx1 px1
2.蜗杆导程角γ和分度圆直径d1 螺纹
蜗杆
ψ πd1
tanψ =
s πd1
=
np πd1
∴ d1
=
Z1 tanγ
m
=
qm
γ πd1
tanγ
=
pZ πd1
=
πmZ πd1
1
=
mZ 1 d1
q
=
Z1 tanγ
具有良好的减摩性、耐磨性、跑合性和抗胶合能力
特点:软硬搭配
蜗杆硬:优质碳素钢、合金结构钢 经表面硬化及调制处理
蜗轮软:铸锡青铜、无锡青铜、灰铸铁
1、蜗杆材料
蜗杆一般采用碳素钢或合金钢制造。 对于高速重载的传动,蜗杆常用低碳合金钢, 如20Cr,20CrMnTi等,经渗碳淬火,表面硬度 HRC56~62,并应磨削。
MPa
= 12.86MPa < [σ F ]
齿根的弯曲疲劳强度校核合格。
(5)验算传动效率h
蜗杆分度圆速度为
v1
=
π d1n1
60×1000
=
3.14×112×1450 60×1000
m/
s
=
8.54m /
s
vs
= v1
cosλ
8.54
=
m / s = 8.59m / s
cos6.412°
查表4.9得
ρ v = 1°09′(1.15°)
h
(0.95
~
0.97)
tan tan( v)
H
480 d2
一起曳引机蜗轮轮齿失效的原因分析

一起曳引机蜗轮轮齿失效的原因分析作者:滕欣定陈俊陈勇鑫来源:《商品与质量·学术观察》2013年第10期摘要:介绍了一起因电梯曳引机蜗轮失效而发生轿厢冲顶事故,进而分析蜗轮蜗杆失效的机理及原因,为避免该类事故的发生提供了有益的参考。
关键词:电梯蜗轮蜗杆失效冲顶2012年12月初,浙江某厂发生一起因电梯曳引机蜗轮失效而发生轿厢冲顶事故,虽未造成重大经济损失。
但这起事故的原因仍值得大家分析和总结。
1.事故现场勘验情况发生事故的电梯,其额定载重是为2000kg,额定速度为0.5m/s,由湖州某公司制造。
在打开曳引机盖后,发现蜗杆表面良好,但是在蜗轮的接触表面不仅呈鳞片状,蜗轮轮齿全部折断(“剃光头”),如图1所示。
机油中发现金属粉末及丝状物。
经咨询维保单位,齿轮油一直未更换。
图1 蜗轮失效图2.事故原因分析2.1 蜗轮磨损的机理当蜗轮蜗杆传动时,由于两轮齿廓在啮合点的线速度不同,在齿廓之间必将产生相对滑动,所以就有滑动摩擦力的存在,既有相对滑动又有压力的两个接触平面必然会发生磨损。
由于蜗轮本身啮合的特点,以及处于低速重载的边界润滑状态(该电梯为载货电梯、吊运货物较重),啮合齿面会发生粗糙体之间的接触,在这种情况下,啮合齿廓的相对滑动就会引起齿面的滑动磨损。
本文认为该曳引机蜗轮轮齿失效过程大致如下:(1)轻微(初期)磨损:在边界润滑状态下,齿轮啮合时,表面凸峰会有较多的相互作用机会,它们会在齿面上产生犁削、剪切作用(不排除同时发生轻微粘着的可能性),多次犁沟便生成磨屑(轻微粘着将引起产生更多磨屑的后果),或生成“隆脊”,这种隆脊在后续的微凸体作用下变形和断裂,也会形成磨屑。
所以这是一个磨屑生成阶段,接触表面发生轻微磨损。
(2)较严重(中期)磨损:由于磨屑的积聚、或润滑时硬质微粒的侵入,摩擦副表面磨损进一步发展为犁削及本体磨料磨损兼而有之,随着硬质磨屑的逐步增多,最终磨料磨损成为主导磨损形式。
此时,齿面发生稳定的、较严重的磨损。
蜗轮蜗杆参数_蜗轮蜗杆传动特点
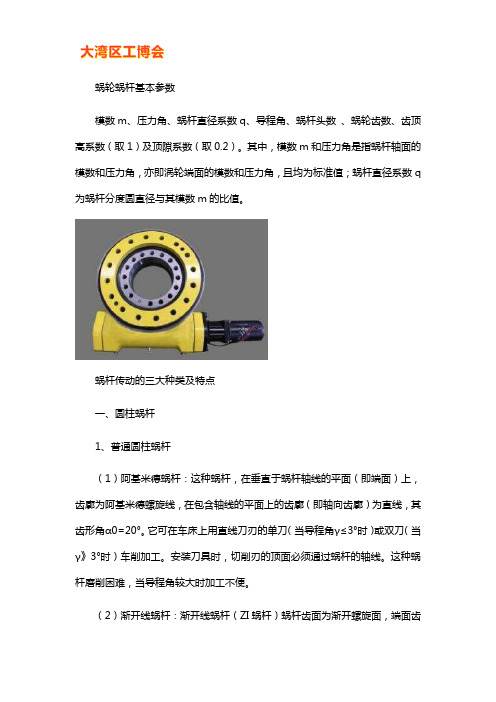
蜗轮蜗杆基本参数模数m、压力角、蜗杆直径系数q、导程角、蜗杆头数、蜗轮齿数、齿顶高系数(取1)及顶隙系数(取0.2)。
其中,模数m和压力角是指蜗杆轴面的模数和压力角,亦即涡轮端面的模数和压力角,且均为标准值;蜗杆直径系数q 为蜗杆分度圆直径与其模数m的比值。
蜗杆传动的三大种类及特点一、圆柱蜗杆1、普通圆柱蜗杆(1)阿基米德蜗杆:这种蜗杆,在垂直于蜗杆轴线的平面(即端面)上,齿廓为阿基米德螺旋线,在包含轴线的平面上的齿廓(即轴向齿廓)为直线,其齿形角α0=20°。
它可在车床上用直线刀刃的单刀(当导程角γ≤3°时)或双刀(当γ》3°时)车削加工。
安装刀具时,切削刃的顶面必须通过蜗杆的轴线。
这种蜗杆磨削困难,当导程角较大时加工不便。
(2)渐开线蜗杆:渐开线蜗杆(ZI蜗杆)蜗杆齿面为渐开螺旋面,端面齿廓为渐开线。
加工时,车刀刀刃平面与基圆相切。
可以磨削,易保证加工精度。
一般用于蜗杆头数较多,转速较高和较精密的传动。
(3)法向直廓蜗杆:这种蜗杆的端面齿廓为延伸渐开线,法面(N-N)齿廓为直线。
ZN蜗杆也是用直线刀刃的单刀或双刀在车床上车削加工。
车削时车刀刀刃平面置于螺旋线的法面上,加工简单,可用砂轮磨削,常用于多头精密蜗杆传动。
(4)锥面包络蜗杆:这是一种非线性螺旋曲面蜗杆。
它不能在车床上加工,只能在铣床上铣制并在磨床上磨削。
加工时,盘状铣刀或砂轮放置在蜗杆齿槽的法向面内,除工件作螺旋运动外,刀具同时绕其自身的轴线作回转运动。
这时,铣刀(或砂轮)回转曲面的包络面即为蜗杆的螺旋齿面,在I-I及N-N截面上的齿廓均为曲线。
这种蜗杆便于磨削,蜗杆的精度较高,应用日渐广泛。
2、圆弧圆柱蜗杆圆弧圆柱蜗杆传动和普通圆柱蜗杆传动相似,只是齿廓形状有所区别。
这种蜗杆的螺旋面是用刃边为凸圆弧形的刀具切制的,而蜗轮是用范成法制造的。
在中间平面(即蜗杆轴线和蜗杆副连心线所在的平面)上,蜗杆的齿廓为凹弧,而与之相配的蜗轮的齿廓则为凸弧形。
蜗轮蜗杆设计计算
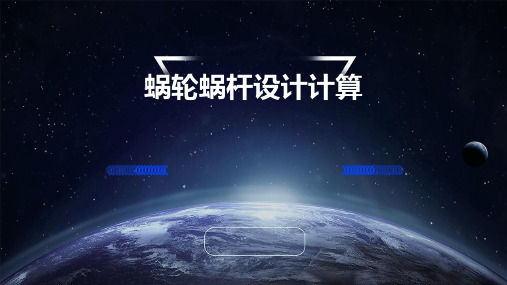
蜗杆传动的效率计算
总结词
根据蜗轮蜗杆的设计参数和工况,计算出蜗杆传动的效率。
详细描述
蜗杆传动的效率计算是评估蜗杆传动性能的重要指标之一。通过分析蜗轮蜗杆的设计参 数和工况,如蜗杆的导程角、模数、转速和载荷等参数,可以计算出蜗杆传动的效率。
蜗轮齿面接触疲劳强度的计算
总结词
根据蜗轮齿面上的载荷分布和材料属性 ,计算出蜗轮齿面的接触疲劳强度。
刚度分析
进行蜗轮蜗杆的刚度分析, 以减小传动过程中的变形 和振动。
可靠性设计
为确保自动化设备的可靠 性,对蜗轮蜗杆进行可靠 性设计和寿命预测。
THANKS
感谢观看
材料应具备较好的抗疲劳性能,以承受交 变载荷的作用;
04
材料应具有良好的工艺性能,易于加工制 造。
04
蜗轮蜗杆设计计算方法
蜗轮齿面载荷分布计算
总结词
根据蜗杆传动的实际工况,通过分析蜗轮齿面上的受力情况,计算出蜗轮齿面上的载荷分布。
详细描述
在进行蜗轮齿面载荷分布计算时,需要考虑蜗杆传动的实际工况,如传动比、转速、载荷大小和方向 等因素。通过分析蜗轮齿面上的受力情况,可以确定蜗轮齿面上的载荷分布,为后续的设计计算提供 基础。
蜗轮蜗杆设计计算
• 蜗轮蜗杆简介 • 蜗轮蜗杆设计参数 • 蜗轮蜗杆材料选择 • 蜗轮蜗杆设计计算方法 • 蜗轮蜗杆设计实例分析
01
蜗轮蜗杆简介
蜗轮蜗杆的定义
01
蜗轮蜗杆是一种常用的传动装置 ,由两个交错轴线、相互咬合的 齿轮组成,其中一个是蜗杆,另 一个是蜗轮。
02
蜗轮蜗杆具有传动比大、传动效 率高、传动平稳、噪音低等优点 ,因此在各种机械传动系统中得 到广泛应用。
VS
齿轮和蜗轮传动的装配

接触斑点
齿轮啮合时,齿的工作表面因互相滚压即留有可 见的痕迹,由此痕迹所显示的接触斑点,就可以判断 齿轮传动的装配质量。接触斑点可利用金属光泽或涂 色法来检查。 正常啮合的齿轮,接触斑点应均匀分布在齿的工 作侧面上(图4-38)。接触斑点按齿面展开图上接触痕 迹所占百分比大小而决定:
对于承受重载荷的齿轮以及在高温下工作 的齿轮,必须考虑到温度变化所引起的膨胀, 因此侧间隙需大一些。高速传动齿轮侧间隙的 确定必须保证正常的润滑条件,又要降低噪音 的产生。由于齿轮的磨损,侧间隙就会增大, 允许的最大极限侧间隙,一般取装配时侧间隙 的3-4倍。达到最大极限侧间隙值时,齿轮就应 该更换。
齿轮和蜗轮传动的装配 齿侧间隙 (1)齿侧间隙的作用 齿侧间隙是指一对 相互啮合齿轮的非工作表面沿法线方向的 距离,用Cn表示。其功用是补偿由于装配或 制造的不精确,传递载荷时受温度影响的 变形和弹性变形;并可在其中贮存一定的润 滑油,以改善齿表面的摩擦条件。
(2)标准保证齿侧隙(以DC表示)是基本的侧间隙规范。对于圆
齿轮和蜗轮传动的装配要求
齿轮传动机构的装配步骤是: 1)验收机件,并按图纸要求将齿轮装在轴上; 2)将齿轮轴部件装入箱体座孔中, 3)检查啮合质量并进行必要的调整。 蜗轮蜗杆传动机构的装配步骤是: 1)将蜗轮齿圈压在轮毂上,并用紧定螺钉固定; 2)将蜗轮装到轴上; 3)将蜗轮轴部件装到箱体上; 4)安装蜗杆,蜗杆轴线的位置由箱体孔确定。 齿轮和蜗轮传动的结构形式不同,装配工作的内容也不同。闭式传动且采用滚 动轴承支承的,两轴的中心距和相互位置精度(平行度和扭斜度),完全由箱 体轴承孔的加工精度来决定,装配工作只是通过钳工加工修整传动零件的制 造误差。若采用滑动轴承时,在轴瓦副研过程中,可以在较小范围内适当调 整两轴的中心距和位置误差。对具有单独轴承座的开式传动,在装配时,除 了通过钳工加工修整传动零件的制造误差外,还要正确安装齿轮轴。
偏置渐开线蜗杆单向点啮合传动凸齿面接触状况分析

第2 2卷
第 2期
长
春
大
学
学
报
Vo . 2 No 2 12 .
Fe b. 2 2 O1
21 0 2年 2月
J URNAL OF C O HANGC HUN UN VER I I S TY
偏 置渐开线蜗杆单 向点啮合传动 凸齿面接触状况 分析
赵 翼瀚
( 长春大学
摘
传 动 的性 能 。 因此 , 轮齿 面 的几 何参 数有 多种 不 同 的数 据可 以选 择 , 同参数 的蜗轮 齿面 与蜗 杆 啮合 时其 蜗 不
传 动 性 能 ( 重合 度 、 如 传动 效率 、 载能 力等 ) 承 将会 有 所不 同。 本 文讨论 了一种 分析 齿 面接 触状 况 的数值 计算 方法 , 以用来 评 估 传 动参 数 对 单 向 点 啮合 传 动 凸面 工 可 作 时实 际重 合度 、 载能 力等 的影 响 , 承 为选 择传 动参 数提 供依 据 。
1 偏 置 渐 开 线 蜗 杆 和 非 渐 开 线 齿 面 蜗 轮 的 啮 合 — — Ⅲ 型 传 动 的 啮 合
偏 置渐 开线 蜗杆 可 以和渐 开 线齿 面蜗 轮 啮合 实 现 直母 线 接 触 传 动 _ ( 为 I 传 动 ) 单 向点 啮 合传 2 称 型 或 动 ( 为 Ⅱ型传 动 ) 此外 , 置渐 开线 蜗杆 还 可 以和非 渐开 线齿 面 的蜗轮 啮合 实 现 曲线 接触 传 动 ( 为 Ⅲ 称 , 偏 称 型传 动 ) 。分 析 Ⅲ型这种 线接 触传 动有 利 于评估 偏 置渐 开线 蜗杆 点 啮合传 动 (I 1型传 动 ) 的性 能 , 过 来 , 反 分 析渐 开 线 蜗杆 点 啮合传 动 也有 利于 了解偏 置 渐开 线蜗 杆 和非渐 开线 齿 面蜗 轮线 啮合 ( Ⅲ型传 动 ) 的特 征 。 Ⅲ型传 动 的蜗 轮 凹齿 面 A 是 渐 开线 曲面 , 与蜗 杆齿 面 A 仍 是 直母 线 接 触 ; 蜗 轮 的 凸齿 面 T 不 是 它 但 :
蜗杆传动PPT幻灯片

80
•32
a=0.5(d1+d2)=0.5m(q+z2)
•13
§7—3 蜗杆传动的失效形式,材料和结构 一、齿面间滑动速度VS
、 分别为蜗杆、蜗轮 在节点C的速度 γ为蜗杆导程角
较大的VS引起: 1、易发生齿面磨损 和胶合 2、如润滑条件良好 (形成油膜条件)则较 大的VS则有助于形成 润滑油膜,减少摩擦、 磨损,提高传动效率
整体式蜗轮 配合式蜗轮 拼铸式蜗轮 螺栓联接式蜗轮
•19
•20
§7—4 蜗杆传动的强度计算
一、蜗杆传动的受力分析
蜗杆传动的受力分析与斜齿圆柱齿轮的受力分析相同,轮
齿在受到法向载荷Fn的情况下,可分解出径向载荷Fr、周向载 荷Ft、轴向载荷Fa。
Ft1
Fa
2
2T1 d1
Fa1 Ft2
2T2 d2
F r 1 F r 2 F t2t an
正确啮合条件
ma1=mt2=m
αa1=αt2=200
γ=β
•8
2、导程角
在m和d1为标准值时,z1↑→γ↑
γ越大传动效率越高,传递动力时要求效率高 γ=15 °-30 °且应采用多头蜗杆 γ越小传动效率越低,要求反行程自锁时 γ<=3°30'
3、传动比 I,蜗杆的头数z1,,蜗轮齿数z2
i n1 z2 d 2 n2 z1 d 1
Fn
2T2
d2cosn cos
•21
蜗杆传动受力方向判断
力的方向和蜗轮转向的判别
圆周力
径向力
Ft——主反从 同 轴向力
Fr——指向各自的轴线 左手或右手:ቤተ መጻሕፍቲ ባይዱ杆旋向
Fa1——蜗杆左右 手螺旋定则
蜗轮接触区

蜗轮齿面常见的接触斑点分布见图
图59-6a为正常接触,图中AB和CD分别表示轴线和中央截面,两个箭头所指处分别表示ab、a1b1两齿面的啮入口,根据运动精度分析,接触斑点最好分布在中央截面附近,略偏于啮入口一端,根据润滑条件分析,接触斑点略偏于啮出口一端有利于建立油膜。
若装配中心距大于加工时的中心距,接触斑点将发生在啮出口,形成如图59-6b所示的对角接触,反之,即装配中心距小于加工中心距,将形成啮入口的对角接触,若蜗杆轴线从c向B方向倾斜,也会出现啮出口的对角接触,见图59-6c。
若蜗杆轴线向A偏移,会造成如图59-6d所示的单向角接触,这些状况均可以按图59-6a所示的斑点,通过调整可调环节,调整轴承支座,刮研轴瓦,配磨蜗杆齿面等措施来解决。
图59-6e所示的接触斑点关于接触线分段接触(大致沿齿高方向),说明蜗轮或蜗杆沿齿高方向的齿形误差较大。
图59-6f所示的接触斑点为沿接触轴线分段接触,说明蜗杆沿齿长方向,蜗杆沿螺旋线方向的齿形误差较大。
这些状况往往通过配对研磨或加载跑合来纠正。
为了减少对角接触,使接触斑点发生在中央截面附近,在精滚蜗轮齿面时,常采用一些工艺措施。
例如:1)改变滚刀参数,即增大节径,或减小导程,或两者同时改变。
2)改变滚刀安装位置,使之不与蜗轮正交,向蜗轮齿螺旋角减小的方向偏转3)使滚刀在不同截面内滚切,即保持中心距不变,先在中央截面内滚切,然后分别在高于、低于中央截面的截面被滚切。
蜗轮齿面常见的接触斑点分布见图59-6.。
- 1、下载文档前请自行甄别文档内容的完整性,平台不提供额外的编辑、内容补充、找答案等附加服务。
- 2、"仅部分预览"的文档,不可在线预览部分如存在完整性等问题,可反馈申请退款(可完整预览的文档不适用该条件!)。
- 3、如文档侵犯您的权益,请联系客服反馈,我们会尽快为您处理(人工客服工作时间:9:00-18:30)。
偏置渐开线蜗杆单向点啮合传动凸齿面接触状况分析(共15页) 长春大学 赵翼瀚内 容 提 要本文讨论了单向点啮合传动蜗轮凸齿面工作时分析齿面接触状况的数值计算方法,用此方法计算所得数据,可以用来评估传动参数对实际重合度、承载能力等的影响,为选择传动参数提供依据。
关键词 Ⅰ型传动 Ⅱ型传动 Ⅲ型传动 Ⅲ型传动瞬时接触线 齿线 齿线侧隙 隐型接触点由文献 【3—1】的论述可知,文中讨论的单向点啮合传动,其蜗轮不仅凹齿面是渐开线曲面,而且与蜗杆点啮合的凸齿面也是渐开线曲面,此渐开线曲面是由啮合原理所确定的曲面,而非近似替代曲面;此齿面的几何特性,受到蜗杆锥角和齿形角、传动中心距和基圆柱切平面倾角等多个要素影响,每个要素的变动都要影响传动的性能。
因此,蜗轮齿面的几何参数有多种不同的数据可以选择,不同参数的蜗轮齿面与蜗杆啮合时其传动性能(如重合度、传动效率、承载能力等)将会有所不同。
本文讨论了一种分析齿面接触状况的数值计算方法,可以用来评估传动参数对单向点啮合传动凸面工作时实际重合度、承载能力等的影响,为选择传动参数提供依据。
本文讨论的齿面接触状况的数值计算方法包含三个方面的内容:偏置渐开线蜗杆和非渐开线齿面蜗轮的啮合及其齿面接触线;固定截面上蜗杆、蜗轮齿面的齿廓曲线;固定截面上蜗杆、蜗轮齿廓曲线侧隙的数值分析。
(一)偏置渐开线蜗杆和非渐开线齿面蜗轮的啮合——Ⅲ型传动的啮合偏置渐开线蜗杆可以和渐开线齿面蜗轮啮合实现直母线接触传动【3—2】(称为Ⅰ型传动)或单向点啮合传动【3—1】(称为Ⅱ型传动),此外,偏置渐开线蜗杆还可以和非渐开线齿面的蜗轮啮合实现曲线接触传动(称为Ⅲ型传动)。
分析Ⅲ型这种线接触传动有利于评估偏置渐开线蜗杆点啮合传动(Ⅱ型传动)的性能,反过来,分析渐开线蜗杆点啮合传动也有利于了解偏置渐开线蜗杆和非渐开线齿面蜗轮线啮合(Ⅲ型传动)的特征。
Ⅲ型传动的蜗轮凹齿面A 2是渐开线曲面,它与蜗杆齿面A 1仍是直母线接触;但蜗轮的凸齿面T 2不是渐开线曲面,凸齿面T 2也可和蜗杆齿面T 1实现线接触传动。
现 在以右旋蜗杆与蜗轮啮合(参阅图3—1a )为例, 讨论Ⅲ型传动T 1和T 2齿面的啮合问题。
1、渐开线蜗杆T 1齿面的矢函数(1) 基圆柱Q T1上右旋螺旋线L T1的矢函数 图3—1如图3—1b 所示,坐标架σ1(d )=[()()()()1111,,d d d d oi j k ;] 是一个与蜗杆T 1齿面基圆Q T1固联的绕蜗杆轴线转动的坐标架,——1——()()()111d d d i j k 、、分别是坐标轴X 1(d)、Y 1(d)、Z 1(d)上单位矢量。
在σ1(d )中,螺旋线L T1上任意一点M 的矢径()()()()()()()111111()()01()sin ()d d d d d d d T T JT JT d d T r COS i r j z p z ρρϕϕϕϕ==+++ (3—1)式中r JT1:基圆柱Q T1的半径;φ(d):点M 的矢径()1d T ρ 在O 1(d)X 1(d)Y 1(d)平面上投影的有向角(以X 1(d)轴为基线计);z 0:螺旋线起始点M 0在z 1((d)轴上的坐标(M 0点是螺旋线L T1与o 1(d )X 1(d)Z 1(d)平面的第一个交点(自o 1X 1Y 1平面 计),它在o 1(d )Z 1(d)轴的坐标 Z 1(d) =z 0 );螺旋线参数P T =s T /2π , s T 为螺线螺距。
(2)螺旋线L T1的切线矢量())()()()()()1111111()sin d d d d d d d T JT JT T d d T r i r COS j p k d ρϕϕϕ==-++( (3—2)()1d T (3—3) 螺旋线L T1的切线单位矢量()()()()()()111111()1cos sin cos cos d d d d d d T T d T i j T αλϕλϕ⎛⎫ ⎪==-+ ⎪ ⎪⎝⎭+(3—4)式中1cos T λ= 1sin T λ=(3) 蜗杆T 1齿面矢量函数 ()()()()()11111(,)d d d d d T T TT T T R R ϕμρμα==+(3—5)式中μT1是参数,它是齿面上的点沿其所在齿面母线至母线与基圆柱切点之间的一段母线长度值,以后简称“母线段长”。
将式(3—1)、(3—4)代入(3—5)得到 蜗杆T 1齿面矢量函数 ——2——()11sin d T K λ()()()()11111()()()1111()()1011(sin )(sin )(sin )d d d d T JT T T d d d JT T T d d T T T R r COS COS i r COS COS j Z p k ϕμλϕϕμλϕϕμλ=-+++++ (3—6)2、T 1齿面法线单位矢量由于()()1()()1111()()()()()11111(sin cos cos )(cos cos sin )d d T d d JT T T d d d d d JT T T T R r i r j p k ϕμλϕϕϕμλϕ∂=-+∂+- + (3—7)(d)()()T1()()11111()11R cos sin cos cos sin d d d d T T T d T i j k λϕλϕμλ∂=-+∂+ (3—8)所以齿面法线矢量()()()111()1()()()()()111111221(sin cos )d d d T T T d T d d d d d JT T T T JT JT TR R N r p i p j r k r p μϕμϕϕ∂∂=⨯∂∂=-+-+ (3—9)()1d T r μ= N (3—10)齿面法线单位矢量())()()()1()()11111()11sin cos )d d d d d T d d T T T JT d T N n p i p j r k N ϕϕ==-+-( ()()()()()1111111sin sin sin cos cos d d D d d T T T i j K λϕλϕλ=-+- (3—11)3、 T 1和T 2齿面接触点的相对速度在蜗杆齿面T 1和蜗轮齿面T 2在接触点处,蜗杆接触点相对蜗轮接触点的相对速度12V在动坐标系σ1(d )中的矢函数(请读者参阅参考文献【3-3】自行推导)表达式为——3——()()()()()121111210111[(sin cos cos )cos (sin )]d d d d d JT T T T T T V r Z p i ωϕμλϕωϕμλ=-++Ω++()()()()1111121011[(cos cos sin )sin (sin )]d d d d JT T T T T T r Z p j ωϕμλϕωϕμλ+--Ω++ ()()()1211111[cos()cos sin()]d d d JT T T r a k ωϕμλϕ-+Ω-+Ω- (3—12)上式中Ω1 是动坐标架的O 1((d)X 1((d)轴与不动坐标架的O 1X 1轴之间所夹的有向角;ω1、ω2分别是蜗杆、蜗轮的角速度。
4、渐开线蜗杆T 1齿面和蜗轮非渐开线凸齿面T 2啮合(Ⅲ型传动)的啮合函数 由式(3—11)、(3—12)可得啮合函数(参阅【3-4】、【3—5】、【3—6】) ()()112d d T T n VΦ=∙=()()1212111sin()[cos()cos d d T JT T r μωϕωϕλ-+Ω++Ω ()()201121()sin sin()cos d d T T T z p a ωϕλϕωλ-++Ω-11cos ]T T p ωλ+ (3—13) 5、渐开线蜗杆和非渐开线凸齿面蜗轮啮合(Ⅲ型传动)的齿面接触线渐开线蜗杆和非渐开线凸齿面蜗轮(Ⅲ型传动)啮合传动时,在坐标系σ1(d)中,蜗杆T 1齿面上的瞬时接触线由下面的方程组确定【3—4】 :()()()111(,)d d d T T T T R R ϕμ=Φ = 0(3—14)将啮合函数式(3—13)代入啮合方程 ФT =0 经整理后得()121101()1cos ()sin sin()d T T T T T d i p z p λμϕλϕ-++Ω=111()()11cos cos tan()sin()T T JT d d r aλλϕϕ+-+Ω+Ω (3—15)(注 式(3—15)也可由文献【3—3】的式(25)导出,读者可自行验证)蜗杆齿面接触线上各点的参数(μT1 ,φ(d))满足 式(3—15)所列条件。
Ⅲ型传动蜗杆T 1齿面上的接触线可由式(3—14)确定,并可据此进而确定蜗轮的齿面矢函数【3—3】。
式(3—15)是由式(3—1)及(3—12)推导来的。
为了灵活、准确地使用式(3—15)确定蜗杆齿面上的接触线,这里要强调两个要点:(1) 在式(3—1)中,Z 0是蜗杆基圆柱Q T1上的螺旋线L T1与坐标平面O 1(d)X 1(d)Z 1(d) 的第一个交点M 0(参看图3-1b )在O 1(d)Z 1(d)轴的坐标值。
σ1(d) =[o 1(d ); ()()()111,,d d d i j k ]是与蜗杆基圆柱Q T1相固联的坐标架,它们联接前可绕O 1(d) Z 1(d) 轴相对转动,两者可以选择任意一个相对位置进行联接,显然,Z 0的数值与联接的相对位置有关。
因此,蜗杆基圆——4——柱Q T1上同一条螺旋线L T1的矢函数式(3—1)中,其Z 0的数值可能是不同的,并且螺旋线 L T1上同一点的φ(d) 数值也要随联接的相对位置变动而变动。
(2) 式(3—12)中的1Ω是动坐标架σ1(d)的()1d i与固定坐标架σ11111[;,,]o i j k =的1i (111i j k、、是坐标轴x 1、y 1、z 1上的单位矢量)之间的有向角。
有时,为了研究或计算的方便,要求蜗杆转至某一位置时,1Ω有一个特定的数值,所以,蜗杆上的同一点其式(3—12)中的1Ω的数值也可能是不同的。
从上面的分析可知,由于蜗杆基圆柱Q T1与坐标架σ1(d)的相对位置不同,基圆柱Q T1上的同一根螺旋线L T1,其矢函数表达式中的Z 0值可能是不同的,同时蜗杆齿面上同一点所对应的φ(d)及1Ω的数值也会不同,但是,螺旋线L T1的几何特性及蜗杆、蜗轮的相对运动不会因此发生改变;同时,根据式(3—14)、(3—15)所确定的蜗杆齿面上的瞬时接触线也不会发生改变。
(二)Ⅲ型传动经过蜗杆齿面特定点的T 1齿面接触线的计算如图3—2所示,点J (J 1,J 2) 是偏置渐开线蜗杆与渐开线齿面蜗轮凸齿面点啮合传动(Ⅱ型传动)运转时的某一时刻t ,蜗杆与蜗轮齿面的接触点,J 1点是蜗杆齿面上的点,它应在倾角为θ1的蜗杆基圆柱Q T1的切平面РT1上, РT1上的N ——N 线是齿面接触点的轨迹,即啮合线,点J 1在N ——N线上。