齿面接触强度计算
① 按齿面接触的疲劳强度设计

① 按齿面接触的疲劳强度设计齿轮是一种常见的传动装置,不仅广泛应用于机床、汽车、船舶、飞机等工业领域,也被用于农业机械和家用电器等领域。
齿轮的设计需要综合考虑多种因素,其中疲劳强度是一项重要的考虑因素。
本文主要讨论按齿面接触的疲劳强度设计。
1. 齿轮疲劳破坏的原因齿轮在长时间使用过程中,可能会发生疲劳破坏,主要原因有以下三点。
1.1 循环载荷作用循环载荷是齿轮疲劳破坏的主要原因之一。
齿轮在运行过程中,由于受到循环载荷的作用,导致齿表表面和内部产生裂纹,最终导致齿轮疲劳破坏。
1.2 齿面接触疲劳齿轮在运行过程中,齿面之间不断摩擦接触,产生接触疲劳。
长时间的齿面摩擦作用会导致齿面磨损和裂纹,从而加速齿轮的疲劳破坏。
1.3 齿轮微小杂质齿轮制造过程中,可能会留下一些微小的杂质,这些杂质会影响齿轮的强度和寿命。
在齿轮运转过程中,这些杂质可能被挤入齿轮表面和内部,从而导致齿轮疲劳破坏。
2. 按齿面接触的疲劳强度指标2.1 等效应力法等效应力法基于最大主应力和平均应力在作用方向上的不同,通过等效应力来判断齿轮的疲劳寿命。
等效应力法是一种基于静态强度计算经验公式修正的方法,适用于齿轮低速、半精度、低载荷情况下的疲劳寿命预测。
等效应力法无法同时考虑多种载荷作用下的疲劳寿命,无法准确反映实际疲劳寿命。
2.2 AGMA方法AGMA方法是由美国齿轮制造商协会(AGMA)提出的一种疲劳分析方法。
通过综合考虑齿轮中各种载荷的作用,将其合成为一个等效载荷,然后根据这个等效载荷计算齿轮的疲劳寿命。
AGMA方法具有比等效应力法更高的精度和适用范围,适用于不同载荷作用下的齿轮疲劳分析。
3. 基于齿面接触的疲劳强度设计3.1 齿轮材料的选择齿轮材料的选择与齿轮的设计和使用相关联。
通常情况下,齿轮材料需要具有高强度、高韧性和高疲劳强度等特性。
传统的齿轮材料有合金钢、碳素钢和铸铁等,而现代材料则有硬质合金、陶瓷和高分子材料等。
同时需要考虑的是,齿轮材料的选择还应考虑到齿轮生产成本、机械加工性能和耐热性能等方面。
齿轮接触强度与弯曲强度
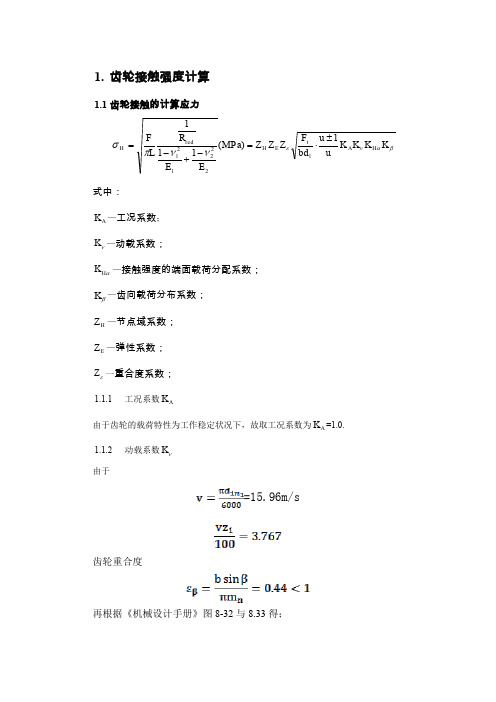
1. 齿轮接触强度计算1.1齿轮接触的计算应力βανεννπσK K K K uu bd F Z Z Z MPa E E R L FH A t E H red H1)(1111222121±⋅=-+-= 式中:A K —工况系数;νK —动载系数;αH K —接触强度的端面载荷分配系数;βK —齿向载荷分布系数;H Z —节点域系数;E Z —弹性系数; εZ 一重合度系数;1.1.1工况系数A K由于齿轮的载荷特性为工作稳定状况下,故取工况系数为A K =1.0. 1.1.2动载系数νK由于=15.96m/s齿轮重合度再根据《机械设计手册》图8-32与8.33得;)=1.48-0.44(1.48-1.22)=1.361.1.3端面载荷分配系数αH K查表8-120得21εαZ C K H H ∙=其中H C 查图8-34为0.865. 1.1.4齿向载荷分布系数βK查图8.35可得βK =1.13. 1.1.5节点域系数H Z式中:错误!未找到引用源。
为端面分度圆压力角;错误!未找到引用源。
为基圆螺旋角;错误!未找到引用源。
为端面啮合角;经计算最后得到H Z =2.254 1.1.6弹性系数E Z带入各值后,得E Z =189.87错误!未找到引用源。
1.1.7重合度系数εZ与1.13的分母约去,不需考虑。
最后得到理论接触应力为:MPaZ mm mm N Z MPa H 67.124413.11865.036.11208.2208.3776.1572.7627.5265287.189254.2=⨯⨯⨯⨯⨯⨯⨯⨯⨯⨯=εεσ1.2 接触疲劳极限lim Hσ' W R V L N H HZ Z Z Z Z lim lim σσ=' 式中:'H l i m σ表示计算齿轮的接触疲劳极限; Hlimσ表示试验齿轮的接触疲劳极限;NZ 表示接触强度的寿命系数;L Z 表示润滑剂系数;VZ 表示速度系数;R Z 表示光洁度系数;WZ 表示工作硬化系数。
齿面接触强度计算
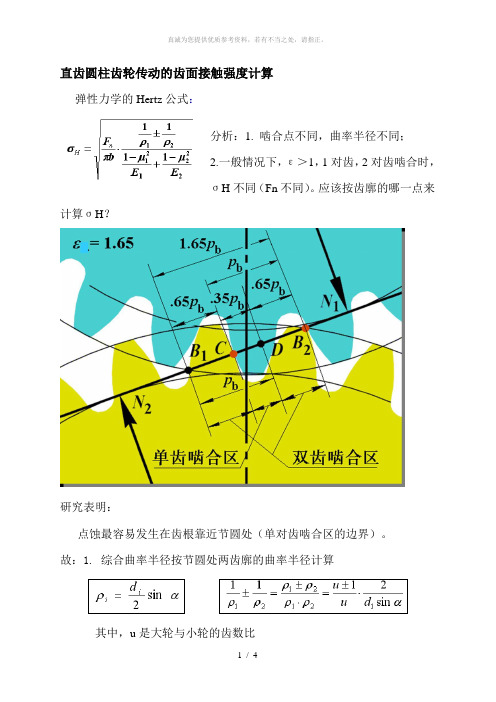
直齿圆柱齿轮传动的齿面接触强度计算
弹性力学的Hertz公式:
分析:1. 啮合点不同,曲率半径不同;
2.一般情况下,ε>1,1对齿,2对齿啮合时,
σH不同(Fn不同)。
应该按齿廓的哪一点来计算σH?
研究表明:
点蚀最容易发生在齿根靠近节圆处(单对齿啮合区的边界)。
故:1. 综合曲率半径按节圆处两齿廓的曲率半径计算
其中,u是大轮与小轮的齿数比
2. Fn按单对齿啮合计算
针对钢制齿轮,引入钢的泊松比μ1= μ2 =0.3,钢的弹性模量
E=2.06×105 MPa,载荷系数K,中心距a,得齿面接触强度的验算公式:令齿宽系数ψa =b/d1,代入上式得中心距:
分析:当一对齿轮的材料、传动比、齿宽系数一定时,接触应力σH 仅取决于分度圆直径d或中心矩a,与模数m无关。
即:两对分度圆直径对应相等的齿轮传动,具有相同的接触强度,与各自模数无关。
即:增大模数m(但d不改变),不能提高齿面接触强度。
关于齿宽系数ψa
理论上讲,ψa越大,a越小,结构越紧凑。
但实际上,ψa↑,可能降低结构的刚性,载荷分布越不均匀,轮齿更易折断。
许用接触应力按下式计算:
式中: σHlim为试验齿轮的接触疲劳强度
极限,按图11-7查得;
S H为齿面接触疲劳安全系数,查表11-4得到。
图11-7。
标准直齿圆柱齿轮齿面接触疲劳强度计算
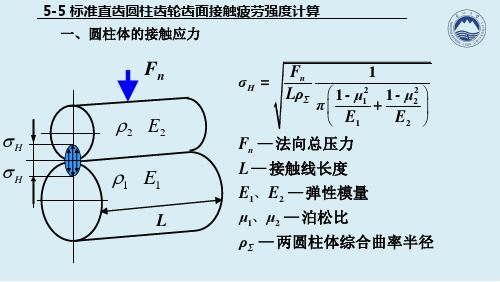
三、标准直齿圆柱齿轮齿面接触疲劳强度
1.齿轮齿面接触疲劳强度条件
H ZH ZE Z
2KT1 bd12
u u
1
[ H
]
2.按齿面接触疲劳强度的设计式
a
u 1
3
KT1
2 a u
ZH ZE Z
H
2
mm
d1
3
2KT1
d
u 1
u
ZH ZE Z
H
2
mm
a
b a
;
d
ห้องสมุดไป่ตู้
b d1
5-5 标准直齿圆柱齿轮齿面接触疲劳强度计算 三、标准直齿圆柱齿轮齿面接触疲劳强度
5-5 标准直齿圆柱齿轮齿面接触疲劳强度计算 一、圆柱体的接触应力
H
Fn 2 E2
σH =
Fn
1
LρΣ
π
1
- μ12 E1
+ 1 - μ22 E2
Fn — 法向总压力
H
1 E1
L — 接触线长度 E1、E2 — 弹性模量
L
μ1、μ2 — 泊松比
ρΣ — 两圆柱体综合曲率半径
5-5 标准直齿圆柱齿轮齿面接触疲劳强度计算
5-5 标准直齿圆柱齿轮齿面接触疲劳强度计算 二、标准直齿圆柱齿轮齿面接触应力 4.齿轮齿面接触应力
弹性系数:ZE
1
[(1 12 ) (1 22 )]
E1
E2
表5 5
节点区域系数:ZH
2
sin cos
齿轮齿面接触应力
H ZH ZE Z
2KT1 u 1 bd12 u
N/mm2
5-5 标准直齿圆柱齿轮齿面接触疲劳强度计算
机械设计(6.14.1)--变位齿轮传动的强度计算
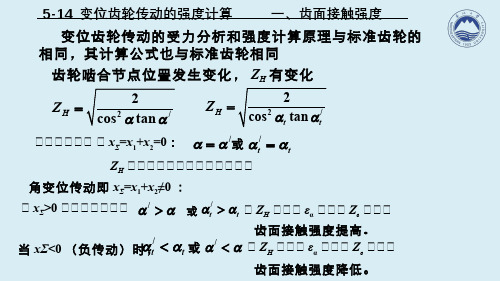
变位齿轮传动的受力分析和强度计算原理与标准齿轮的相同,其计算公式也与标准齿轮相同
齿轮啮合节点位置发生变化,Z H 有变化
2/
2cos tan H Z a a =2/2cos tan H t t Z a a =/a a =/t t a a =高高高高高高 高x Σ=x 1+x 2=0:
Z H 高高高高高高高高高高高高高
或/a a >/t t a a >/a a </t t
a a <高x Σ>0高高高高高高高高Z H 高高高εα高高高Z ε高高高
高Z H 高高高εα高高高Z ε高高高或齿面接触强度提高。
当xΣ<0(负传动)时,或齿面接触强度降低。
角变位传动即x Σ=x 1+x 2≠0 :
二、齿根弯曲强度齿根弯曲强度:
变位使齿形变化,齿根厚度和齿根圆角半径变化,引起计算系数Y Fa 和Y sa 的变化,影响齿根弯曲强度。
正变位齿轮的齿厚增大,Y Fa 减小,
齿根圆角半径减小,Y sa 增大。
正变位齿轮的齿根弯曲强度可有提高。
负变位使齿根弯曲强度降低。
变位使端面重合度系数εa 变化,Y ε也发生变化。
圆柱齿轮传动强度的计算

圆柱齿轮传动的强度计算1 直齿圆柱齿轮传动的强度计算1.齿面接触疲劳强度计算为了保证在预定寿命内齿轮不发生点蚀失效,应进行齿面接触疲劳强度计算。
因此,齿轮接触疲劳强度计算准则为:齿面接触应力σH小于或等于许用接触应力σHP,即σH≤σHP赫兹公式由于直齿轮在节点附近往往是单对齿啮合区,轮齿受力较大,故点蚀首先出现在节点附近。
因此,通常计算节点的接触疲劳强度。
图a表示一对渐开线直齿圆柱齿轮在节点接触的情况。
为了简化计算,用一对轴线平行的圆柱体代替它。
两圆柱的半径ρ1、ρ2分别等于两齿廓在节点处的曲率半径,如图b所示。
由弹性力学可知,当一对轴线平行的圆柱体相接触并受压力作用时,将由线接触变为面接触,其接触面为一狭长矩形,在接触面上产生接触应力,并且最大接触应力位于接触区中线上,其数值为式中σH-接触应力(Mpa)Fn-法向力(N)L-接触线长度(mm)rS-综合曲率半径(mm);±-正号用于外接触,负号用于内接触ZE-材料弹性系数(),,其中E1、E2分别为两圆柱体材料的弹性模量(MPa);m1、m2分别为两圆柱体材料的泊松比。
上式表明接触应力应随齿廓上各接触点的综合曲率半径的变化而不同,且靠近节点的齿根处最大(图c、d)。
但为了简化计算,通常控制节点处的接触应力。
节点处的参数(1)综合曲率半径由图可知,,代入rE公式得式中:,称为齿数比。
对减速传动,u=i;对增速传动,u=1/i。
因,则有(2)计算法向力(3)接触线长度L引入重合度系数Ze,令接触线长度将上述参数代入最大接触应力公式得接触疲劳强度计算公式令,称为节点区域系数。
则得(1) 齿面接触疲劳强度的校核公式齿面接触疲劳强度的校核公式为(2) 齿面接触疲劳强度设计公式设齿宽系数,并将代入上式,则得齿面接触疲劳强度的设计公式式中:d1-小齿轮分度圆直径(mm);ZE-材料弹性系数(),按下表查取;注:泊松比m1=m2=0.3Z H-节点区域系数,考虑节点处轮廓曲率对接触应力的影响,可由下左图查取。
齿轮齿面接触强度及齿根弯曲强度核算
齿面接触强度及齿根弯曲强度核算在设计产品过程中,经常会选用齿轮作为传动力及扭矩的原件。
在大部分成型产品改造或调整过程中,关于齿轮的强度校核这一步骤就可以用类比法代替,从而节省设计人员的精力,缩短了设计周期。
但得出的结果没有书面依据以及理论方面的支持。
所以当进行多次类比之后,所设计出来的齿轮与理论计算得出的齿轮偏差会较大。
其原理类似于累计偏差。
所以应该进行强度校核方面的计算。
齿轮强度校核计算,在实际应用中,主要是两方面的核算:1、齿面接触强度的核算。
2、齿根弯曲强度的核算。
1.齿面接触强度核算-分度圆直径计算参考文献:在初步设计齿轮时,根据齿面接触强度,可按照下列公式估算齿轮传动的尺寸。
(机械设计手册P14-133)a≥A a(μ±1)·√KT1ψaσHP23①d1≥A d·√KT1ψdσHP2·μ±1μ3②公式①为两齿轮中心距的计算;公式②为齿轮分度圆直径的计算。
由于本次计算的是齿轮齿条传动。
所以,中心距a= d1/2其中:d1为齿轮分度圆直径,只需要核算齿轮分度圆直径d1首先,要确定公式②中各个符号代表的含义及数值选取。
d1—齿轮分度圆直径;A d—常系数;K—载荷系数;μ—齿数比;σHP—许用接触应力;ψd—齿宽系数;T1—电机减速机输出扭矩;d1:齿轮分度圆直径,待求;A d:常系数值;A d值在表14-1-65中,通过螺旋角角度β的数值求得。
齿轮的螺旋角β=11.655°,则A d = 756。
载荷系数K,常用值K=1.2~2(机械设计手册P14-133),当载荷平稳,齿宽系数较小,轴承对称布置,轴的刚性较大,齿轮精度较高(6级以上),以及齿轮的螺旋角较大时取较小值;反之取较大值。
根据对比后的结果在K的常用范围内选取。
此次选择K=1.8(载荷平稳,齿宽系数较小,轴为非对称分布,轴的刚性不大,齿轮精度不高)u:传动比。
当齿轮之间为外啮合的时候,选取“+”;当齿轮之间为内啮合的时候,选取“-”,本次计算为齿轮齿条,不影响计算结果。
接触强度计算的尺寸系数
接触强度计算的尺寸系数
(3)受载时,主、从齿轮接触力的大小相等,接触面积
也相等,故两配对齿轮接触应力是相同的,即σH1=σH2。
但因两齿轮的材料不同、热处理方法不同,其许用应力不同,即:[σH1]≠[σH2 ]。
因此按接触疲劳强度进行设计计算时,只须将[σH1]和[σH2 ]中较小者代入公式即可。
其含义
是齿轮的几何尺寸参数决定于接触强度较弱者。
(4)直齿
圆柱齿轮传动按公式计算出中心距α后,初选齿数z1 ,
z2, 然后按m=2α/(z1+z2)计算出模数m,并圆整为标准值;
斜齿圆柱齿轮传动按公式计算出中心距α后,初选齿数z1 ,z2 以及mn(或β)再按β=arccos[mn(z1+z2)/2α]计算β,或按mn= 2αcosβ/(z1+z2)计算法面模数mn,并圆整为标准值;圆锥齿轮按公式计算出锥距Re后,初选齿数z1 ,z2,再
按计算出大端模数,并圆整为标准值。
(5)在其它参数相同的条件下,齿轮的接触疲劳强度与中心距α或齿轮的分度圆直径d1和d2有关。
分度圆直径d1和d2分别相等的两对齿轮,不论其模数是否相等,均具有相同的接触强度。
模数m不能作为衡量齿轮接触强度的依据。
例如有两对齿
轮传动,其参数分别为m=2,Z1=40,Z2=80和m=4,
Z1=20,Z2=40,则此两对齿轮接触疲劳强度是相同的。
齿轮的强度计算
直齿圆柱齿轮的强度计算受力分析:圆周力F t =112d T 径向力αtan ∙=t r F F 法向载荷αcos t n F F = 1T :小齿轮传递的转矩,mm N ∙ 1d :小齿轮的节圆直径,mm α:啮合角,对标准齿轮, 20=α齿根弯曲疲劳强度的计算: 校核公式:[]F d Sa Fa Sa Fa F z m Y Y KT bmd Y Y KT σφσ≤==21311122 计算公式:[]32112F d Sa Fa z Y Y KT m σφ≥d φ:齿宽系数,1d b d =φ Fa Y :齿形系数 Sa Y :应力校正系数齿面接触疲劳强度的计算: 校核公式:[]H E H uu bd KT Z σσ≤±∙=125.2211 设计公式:[]3211132.2⎪⎪⎭⎫ ⎝⎛∙±∙=H E d Z u u KT d σφ标准斜齿圆柱齿轮的强度计算 受力分析: 圆周力:112d T F T = 径向力:βαcos tan n t r F F ∙= 轴向力:βtan ∙=t a F F齿根弯曲疲劳强度计算: 校核公式:[]F n Sa Fa t F bm Y Y Y KF σεσαβ≤=设计计算:[]32121cos 2F Sa Fa d n Y Y z Y KT m σεφβαβ∙=齿面接触疲劳强度计算: 校核计算:H E H Z Z uu bd KT ∙±∙=111αεσ 设计计算:[]321112⎪⎪⎭⎫ ⎝⎛∙±∙≥H Sa Fa d Y Y u u KT d σεφαu :齿数比标准锥齿轮的强度计算 受力分析:11212m t t d T F F == 121cos tan δαt a r F F F == 121cos tan δαt r a F F F == αcos 1t n F F =齿根弯曲疲劳强度计算: 校核公式:()[]F R Sa Fa t F bm Y Y KF σφσ≤-=5.01 设计公式:()[]32212115.014F Sa Fa R R Y Y u z KT m σφφ∙+-≥齿面接触疲劳强度计算: 校核公式:()[]H R R E H u d KT Z σφφσ≤-=31215.015设计公式:[]()321215.0192.2u KT Z d R R H E φφσ-∙⎪⎪⎭⎫ ⎝⎛≥。
齿轮传动的强度设计计算
1. 齿面接触疲劳强度的计算齿面接触疲劳强度的计算中,由于赫兹应力是齿面间应力的主要指标,故把赫兹应力作为齿面接触应力的计算基础,并用来评价接触强度。
齿面接触疲劳强度核算时,根据设计要求可以选择不同的计算公式。
用于总体设计和非重要齿轮计算时,可采用简化计算方法;重要齿轮校核时可采用精确计算方法。
分析计算表明,大、小齿轮的接触应力总是相等的。
齿面最大接触应力一般出现在小轮单对齿啮合区内界点、节点和大轮单对齿啮合区内界点三个特征点之一。
实际使用和实验也证明了这一规律的正确。
因此,在齿面接触疲劳强度的计算中,常采用节点的接触应力分析齿轮的接触强度。
强度条件为:大、小齿轮在节点处的计算接触应力均不大于其相应的许用接触应力,即:⑴圆柱齿轮的接触疲劳强度计算1)两圆柱体接触时的接触应力在载荷作用下,两曲面零件表面理论上为线接触或点接触,考虑到弹性变形,实际为很小的面接触。
两圆柱体接触时的接触面尺寸和接触应力可按赫兹公式计算。
两圆柱体接触,接触面为矩形(2axb),最大接触应力σHmax位于接触面宽中线处。
计算公式为:接触面半宽:最大接触应力:•F——接触面所受到的载荷•ρ——综合曲率半径,(正号用于外接触,负号用于内接触)•E1、E2——两接触体材料的弹性模量•μ1、μ2——两接触体材料的泊松比2)齿轮啮合时的接触应力两渐开线圆柱齿轮在任意一处啮合点时接触应力状况,都可以转化为以啮合点处的曲率半径ρ1、ρ2为半径的两圆柱体的接触应力。
在整个啮合过程中的最大接触应力即为各啮合点接触应力的最大值。
节点附近处的ρ虽然不是最小值,但节点处一般只有一对轮齿啮合,点蚀也往往先在节点附近的齿根表面出现,因此,接触疲劳强度计算通常以节点为最大接触应力计算点。
参数直齿圆柱齿轮斜齿圆柱齿轮节点处的载荷为综合曲率半径为接触线的长度为,3)圆柱齿轮的接触疲劳强度将节点处的上述参数带入两圆柱体接触应力公式,并考虑各载荷系数的影响,得到:接触疲劳强度的校核公式为:接触疲劳强度的设计公式为:•KA——使用系数•KV——动载荷系数•KHβ——接触强度计算的齿向载荷分布系数•KHα——接触强度计算的齿间载荷分配系数•Ft——端面内分度圆上的名义切向力,N;•T1——端面内分度圆上的名义转矩,N.mm;•d1——小齿轮分度圆直径,mm;•b ——工作齿宽,mm,指一对齿轮中的较小齿宽;•u ——齿数比;•ψd——齿宽系数,指齿宽b和小齿轮分度圆直径的比值(ψd=b/d1)。
- 1、下载文档前请自行甄别文档内容的完整性,平台不提供额外的编辑、内容补充、找答案等附加服务。
- 2、"仅部分预览"的文档,不可在线预览部分如存在完整性等问题,可反馈申请退款(可完整预览的文档不适用该条件!)。
- 3、如文档侵犯您的权益,请联系客服反馈,我们会尽快为您处理(人工客服工作时间:9:00-18:30)。
直齿圆柱齿轮传动的齿面接触强度计算
弹性力学的Hertz公式:
分析:1. 啮合点不同,曲率半径不同;
2.一般情况下,ε>1,1对齿,2对齿啮合时,
σH不同(Fn不同)。
应该按齿廓的哪一点来计算σH?
研究表明:
点蚀最容易发生在齿根靠近节圆处(单对齿啮合区的边界)。
故:1. 综合曲率半径按节圆处两齿廓的曲率半径计算
其中,u是大轮与小轮的齿数比
2. Fn按单对齿啮合计算
针对钢制齿轮,引入钢的泊松比μ1= μ2 =0.3,钢的弹性模量
E=2.06×105 MPa,载荷系数K,中心距a,得齿面接触强度的验算公式:令齿宽系数ψa =b/d1,代入上式得中心距:
分析:当一对齿轮的材料、传动比、齿宽系数一定时,接触应力σH 仅取决于分度圆直径d或中心矩a,与模数m无关。
即:两对分度圆直径对应相等的齿轮传动,具有相同的接触强度,与各自模数无关。
即:增大模数m(但d不改变),不能提高齿面接触强度。
关于齿宽系数ψa
理论上讲,ψa越大,a越小,结构越紧凑。
但实际上,ψa↑,可能降低结构的刚性,载荷分布越不均匀,轮齿更易折断。
许用接触应力按下式计算:
式中: σHlim为试验齿轮的接触疲劳强度
极限,按图11-7查得;
S H为齿面接触疲劳安全系数,查表11-4得到。
图11-7。