蜗轮齿根弯曲疲劳强度计算
《机械设计》第12章 蜗杆传动
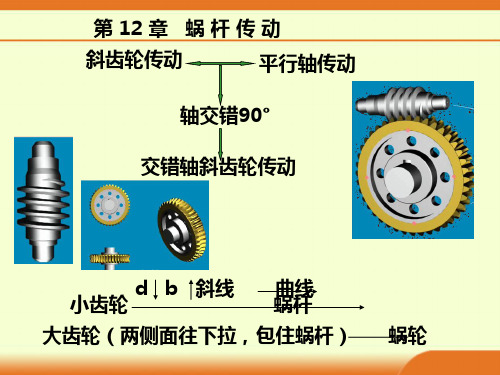
阿基米德蜗杆:αx=20°
标准值
法向直廓蜗杆、渐开线蜗杆:αn=20°
s
pz=zpx1 px1
2.蜗杆导程角γ和分度圆直径d1 螺纹
蜗杆
ψ πd1
tanψ =
s πd1
=
np πd1
∴ d1
=
Z1 tanγ
m
=
qm
γ πd1
tanγ
=
pZ πd1
=
πmZ πd1
1
=
mZ 1 d1
q
=
Z1 tanγ
具有良好的减摩性、耐磨性、跑合性和抗胶合能力
特点:软硬搭配
蜗杆硬:优质碳素钢、合金结构钢 经表面硬化及调制处理
蜗轮软:铸锡青铜、无锡青铜、灰铸铁
1、蜗杆材料
蜗杆一般采用碳素钢或合金钢制造。 对于高速重载的传动,蜗杆常用低碳合金钢, 如20Cr,20CrMnTi等,经渗碳淬火,表面硬度 HRC56~62,并应磨削。
MPa
= 12.86MPa < [σ F ]
齿根的弯曲疲劳强度校核合格。
(5)验算传动效率h
蜗杆分度圆速度为
v1
=
π d1n1
60×1000
=
3.14×112×1450 60×1000
m/
s
=
8.54m /
s
vs
= v1
cosλ
8.54
=
m / s = 8.59m / s
cos6.412°
查表4.9得
ρ v = 1°09′(1.15°)
h
(0.95
~
0.97)
tan tan( v)
H
480 d2
蜗杆传动的强度计算

三、蜗杆传动的强度计算1、蜗轮齿面接触疲劳强度计算,由赫其公式(Hertz )按主平面内斜齿轮与齿条啮合进行强度计算H n E H L KF Z ][σρσ≤=∑Fn ——法向载荷(N );L ——接触线长度(注意蜗杆蜗轮接触线是倾斜的,并计入重合度);∑ρ——综合曲率半径;Z E ——材料弹性线数,对钢蜗杆↔配青铜蜗轮αMP Z E 160=,代入蜗杆传动有关参数,并化简得 校核公式:H P E H a KT Z Z ][/32σσ≤⋅= Mpa式中,Z E ——材料的弹性系数,钢蜗杆配青铜蜗轮αMP Z E 160=Z P ——接触系数,Z P 为反映蜗杆传动接触线长度和曲率半径对接触强度的影响系数 βK K K K V A ⋅⋅=——载荷系数K A ——工况系数βK ——齿面载荷分布系数:1=βK ——载荷平稳6.1~3.1=βK ——载荷变化较大,或有冲击、振动时 K V ——动载荷系数 s m V K V /3,1.1~0.12≤=——精制蜗杆s m V K V /3,2.1~1.12>=——一般蜗杆设计公式:322][⎪⎪⎭⎫ ⎝⎛≥H P E Z Z KT a σmm ⇒定m,q ,H ][σ——蜗轮齿面许用接触应力(1)当蜗轮材料为铸铁或高强度青铜,ασMP B 300≥——失效形式为胶合(不属于疲劳失效),∴许用应力H ][σ与应力循环次数N 无关。
(2)若蜗轮材料ασMP B 300<(锡青铜)——失效形式为点蚀,H ][σ与应力循环次数N 有关。
OH HN H K ][][σσ=OH ][σ——基本许用接触应力HN K ——接触强度寿命系数,8710NK HN =,N 为应力循环次数,h L jn N 260=,n 2为蜗轮转速(r/min ),L h 为蜗轮总工作时数h ,j 为每转一圈每个轮齿啮合次数。
2、蜗轮齿根弯曲疲劳强度计算齿根折断一般发生在Z 2>90,及开式传动中,∴在闭式传动中弯曲强度计算作为校核计算对于重载传动,通过计算还可差别由于轮齿的弯曲变形量引起的轮齿弹性变形量是否过大而影响蜗杆传动的平稳性。
齿轮传动例题
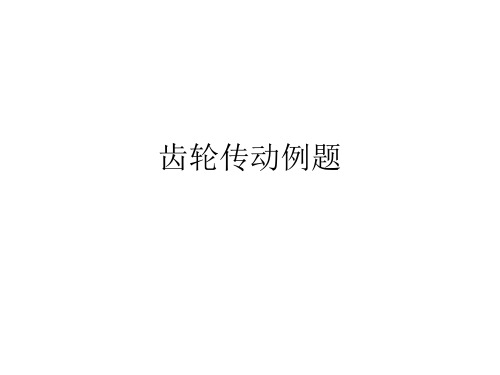
a0
F
F
F
F
F
•
•
4.齿轮受力方向的判别 圆周力 F :主动轮 与转动方向相反 从动轮 与转动方向相同 径向力F :各自指向轮心 轴向力F :圆锥齿轮 从小端指向大端 圆柱齿轮:主动轮 应用左(右)手定则,拇指方向即为轴向力方向 从动轮 与 主动轮的轴向力相反 5.根据给定工况,正确设计齿轮传动 熟悉不同工况下可能产生的主要失效形式(轮齿的折断、齿面疲劳点蚀、齿面磨损、 齿面胶合、轮齿塑性变形等,参见表4.1 ) ,正确确定设计准则,结合工况需求选择材 料、热处理方式及加工精度,在强度计算中,合理地选择各相关参数,掌握参数选择 原则,正确解释设计过程。 6.载荷系数引人的目的及主要影响因素 载荷系数K(K = K K K K )综合考虑了齿轮由于工作特性、制造及安装误差、 齿轮及其支承变形等因素引起的外部及内部附加动载荷、偏载及载荷分配不均等因素 对轮齿受力及应力的影响,利用计算载荷对齿轮进行强度计算,可以使所设计的齿轮 更安全、更符合实际工况需求。关于各系数引人的意义、主要影响因素及改进措施等 可参见表4.2。 7.熟练分析齿轮主要参数的选择原则 1 a m z z d m z (1)模数m和齿数 z 的选择。因为 , 2 当d 1 或a一定时,齿轮的接触 应力与m 和z的组合无关,因此软齿面闭式传动时,在满足齿根弯曲强度条件的基础上, m 尽可能取小值,而z尽可能取大值,常取 18-30 -2 z (但要注意传递动力时m 1.5 mm) ,因为齿数z多,可增大重合度 ,使传动平稳, m 小,可减小滑动速度,增加 z z 与z 应互质为好。在硬齿面闭式传动中,按齿根弯曲 耐磨和抗胶合性能。 z 且 z 17-20 ,以免传动尺寸过大。在开式传动中,由弯曲强度求得m 后应再 强度条件, =
蜗轮蜗杆设计计算
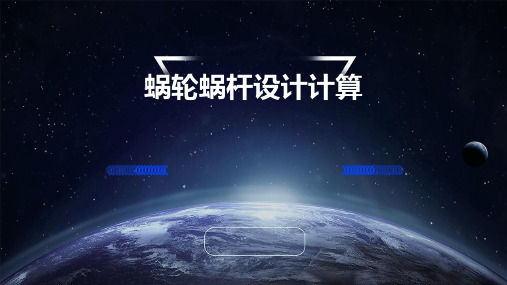
蜗杆传动的效率计算
总结词
根据蜗轮蜗杆的设计参数和工况,计算出蜗杆传动的效率。
详细描述
蜗杆传动的效率计算是评估蜗杆传动性能的重要指标之一。通过分析蜗轮蜗杆的设计参 数和工况,如蜗杆的导程角、模数、转速和载荷等参数,可以计算出蜗杆传动的效率。
蜗轮齿面接触疲劳强度的计算
总结词
根据蜗轮齿面上的载荷分布和材料属性 ,计算出蜗轮齿面的接触疲劳强度。
刚度分析
进行蜗轮蜗杆的刚度分析, 以减小传动过程中的变形 和振动。
可靠性设计
为确保自动化设备的可靠 性,对蜗轮蜗杆进行可靠 性设计和寿命预测。
THANKS
感谢观看
材料应具备较好的抗疲劳性能,以承受交 变载荷的作用;
04
材料应具有良好的工艺性能,易于加工制 造。
04
蜗轮蜗杆设计计算方法
蜗轮齿面载荷分布计算
总结词
根据蜗杆传动的实际工况,通过分析蜗轮齿面上的受力情况,计算出蜗轮齿面上的载荷分布。
详细描述
在进行蜗轮齿面载荷分布计算时,需要考虑蜗杆传动的实际工况,如传动比、转速、载荷大小和方向 等因素。通过分析蜗轮齿面上的受力情况,可以确定蜗轮齿面上的载荷分布,为后续的设计计算提供 基础。
蜗轮蜗杆设计计算
• 蜗轮蜗杆简介 • 蜗轮蜗杆设计参数 • 蜗轮蜗杆材料选择 • 蜗轮蜗杆设计计算方法 • 蜗轮蜗杆设计实例分析
01
蜗轮蜗杆简介
蜗轮蜗杆的定义
01
蜗轮蜗杆是一种常用的传动装置 ,由两个交错轴线、相互咬合的 齿轮组成,其中一个是蜗杆,另 一个是蜗轮。
02
蜗轮蜗杆具有传动比大、传动效 率高、传动平稳、噪音低等优点 ,因此在各种机械传动系统中得 到广泛应用。
VS
涡轮蜗杆的技术要求
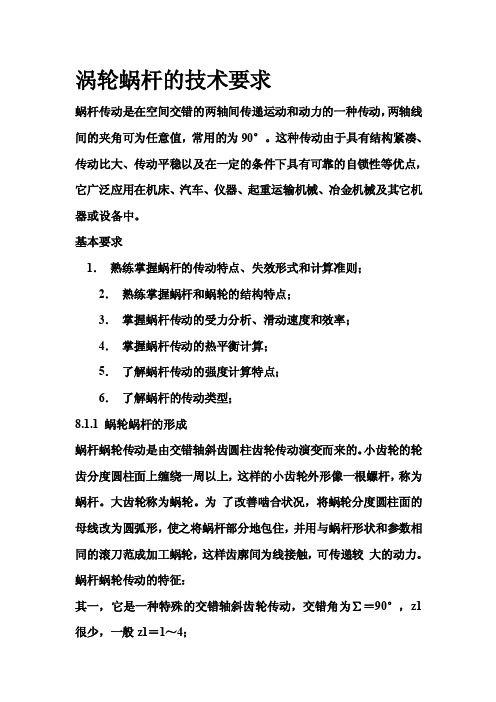
涡轮蜗杆的技术要求蜗杆传动是在空间交错的两轴间传递运动和动力的一种传动,两轴线间的夹角可为任意值,常用的为90°。
这种传动由于具有结构紧凑、传动比大、传动平稳以及在一定的条件下具有可靠的自锁性等优点,它广泛应用在机床、汽车、仪器、起重运输机械、冶金机械及其它机器或设备中。
基本要求1.熟练掌握蜗杆的传动特点、失效形式和计算准则;2.熟练掌握蜗杆和蜗轮的结构特点;3.掌握蜗杆传动的受力分析、滑动速度和效率;4.掌握蜗杆传动的热平衡计算;5.了解蜗杆传动的强度计算特点;6.了解蜗杆的传动类型;8.1.1 蜗轮蜗杆的形成蜗杆蜗轮传动是由交错轴斜齿圆柱齿轮传动演变而来的。
小齿轮的轮齿分度圆柱面上缠绕一周以上,这样的小齿轮外形像一根螺杆,称为蜗杆。
大齿轮称为蜗轮。
为了改善啮合状况,将蜗轮分度圆柱面的母线改为圆弧形,使之将蜗杆部分地包住,并用与蜗杆形状和参数相同的滚刀范成加工蜗轮,这样齿廓间为线接触,可传递较大的动力。
蜗杆蜗轮传动的特征:其一,它是一种特殊的交错轴斜齿轮传动,交错角为∑=90°,z1很少,一般z1=1~4;其二,它具有螺旋传动的某些特点,蜗杆相当于螺杆,蜗轮相当于螺母,蜗轮部分地包容蜗杆。
8.1.2 蜗杆传动的类型按蜗杆形状的不同可分:1.圆柱蜗杆传动-普通圆柱蜗杆(阿基米德蜗杆、渐开线蜗杆、法向直廓蜗杆、锥面包络蜗杆)和圆弧蜗杆2.环面蜗杆传动3.锥蜗杆传动8.1.3 蜗杆传动的特点传动比大,结构紧凑传动平稳,无噪声具有自锁性传动效率较低,磨损较严重蜗杆轴向力较大,致使轴承摩擦损失较大。
8.1.4 蜗杆传动的应用由于蜗杆蜗轮传动具有以上特点,故常用于两轴交错、传动比较大、传递功率不太大或间歇工作的场合。
当要求传递较大功率时,为提高传动效率,常取z1=2-4。
此外,由于当γ1较小时传动具有自锁性,故常用在卷扬机等起重机械中,起安全保护作用。
它还广泛应用在机床、汽车、仪器、冶金机械及其它机器或设备中;蜗杆传动由蜗杆相对于蜗轮的位置不同分为上置蜗杆和下置蜗杆传动。
滑动轴承
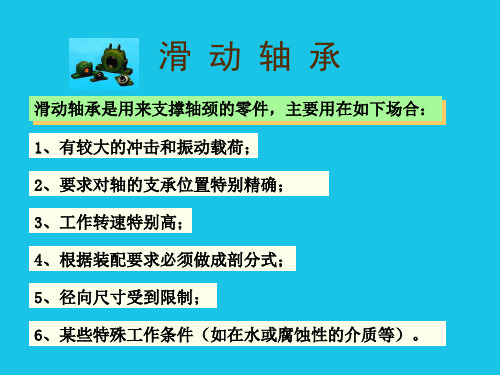
普通圆柱蜗杆传动的主要参数
主要参数( 阿基米德蜗杆)
● 模数 m 和压力角α
中间平面
— 包含蜗杆轴线并垂直与蜗轮轴线的平面
的蜗蜗轮杆加蜗相工杆模同数轴—面滚刀蜗滚轮模制端数,面其蜗压几杆力标何轴角准面参模数数及蜗压直轮力径端角面与相配
在中间平面内相当于齿条与齿轮的啮合
正确啮合条件: mx1 = mt2 = m
滚动轴承的寿命计算
轴承寿命:轴承中任一滚动体或内、外圈滚道上出现疲劳点蚀 以前所经历的总转数或在一定转速下所经历的工作小时数。
轴承的基本额定寿命:一批相同的轴承,在相同的条件下运转, 其中90%的轴承不发生疲劳点蚀前所转过的总转数或在一定的 转速下运转的总小时数。
一、滚动轴承寿命计算的基本公式
轴承寿命的疲劳曲线:
Lh
106 60n
C P
h
C——基本额定动负荷,衡量轴承工作能力的主要指标。
基本额定动负荷有两种:
1、径向额定动负荷—主要承受径向负荷的向心轴承(深沟球 轴承、角接触球轴承、圆锥滚子轴承),用Cr表示;
2、轴向额定动负荷—主要承受轴向负荷的推力轴承,用Ca表示。
正常工作温度(1200C)时的额定动负荷C值可查有关手册。
抗冲击能力较差,高速时噪声 大,工作寿命不及液体摩擦滑 动轴承,径向尺寸比滑动轴承 大
滚动轴承的代号
前置代号
基本代号
后置代号
类型代号
尺寸系列代号
内径代号
前置代号:用于表示轴承的分部件,字母表示;
由轴承的宽度系列和直径系列代号
后字分又0用级136780置母别如— — — — —数—,调圆角圆推代或用:字深共心锥接锥力或沟号数轴C6球滚触滚球、字球个:字承轴子球子轴母轴A级用表的承轴轴轴承表C承别于示公承承承和示2,表;差B2表、依示如等2示次轴:级8内、内2由承接分( 宽 012350径11113— — — 、 、部-2度高的触别027524尺位 窄 正 宽 469系结、— —级结角为寸5数 ; 常 ;列5构特 特到构为2字 ;0:级宽 宽0的)低、1及; 。5、组不级0公5、4成0同,级差00000202。代d以10132直5。— —其、及/—0号345上和径特 轻— —代5材特系级轻 ;4中 重/轻号料0内列;;。、0;的分的径:6角级别特接、为殊触6:要x轴级/求P承2和,、, /P4、/P5、/P6、/P6x和/P0。
《机械设计基础》第7章 蜗杆传动
tanγ= z1/q d1 = q m q是d1与m的比值,不一定是整数。 m一定时,q越小(或d1越小)导程角γ越大,传动效率 越高,但蜗杆的强度和刚度降低。 设计蜗杆传动,在刚度准许的情况下,要求传动效率高 时q选小值;要求强度和刚度大时q选大值。
蜗杆直径系数q
q = d1/m
P1----蜗杆传动输入功率,kW;ks----为散热系数,根据箱体周围通风 条件,一般取ks =10~17[w/(m2·℃)];自然通风良好地方取大值,反 之取小值; η----传动效率;A----散热面积m2。 t0----周围空气温 度℃ 通常取20℃; [t1]----许可的工作温度,通常取70~90℃。
齿圈与轮芯用铰制孔螺栓联接。由于装拆方便,常用尺寸较大或磨损后 需要更换蜗轮齿圈的场合.
浇铸式:(图7-10c) 该型式仅用于成批生产的蜗轮。齿圈最小厚度c=2m,但不小于10 mm
§7-4 蜗杆传动的强度 计算 蜗杆传动的受力分析
蜗轮旋转方向的判定
蜗轮旋转方向,按照蜗杆的螺旋线旋向和旋转方
蜗杆传动的特 点
§7-2 蜗杆传动的主要参数和几何尺 寸 概念(图7-6)
连心线:蜗杆轴线与蜗轮轴线的公垂线。 中间平面:圆柱蜗杆轴线和连心线构成的平面。 所以中间平面内蜗杆与蜗轮的啮合相当于渐开线 齿轮与齿条(直线)的啮合
规定:设计计算以中间平面参数及其几何尺寸关系为准。 主要参数
1.模数m和压力角α;2.传动比i,蜗杆头数z1和蜗 轮齿数z2 ; 3.蜗杆导程角γ; 4.蜗杆分度圆直径d1和蜗杆直径系数q ;5.中心距a。
5.中心距a。
标准蜗杆传动其中心距计算公式:
a=
d1+d2 2
= m (q+z2) 2
蜗杆传动的失效形式和设计准则1齿面相对滑动速度vs
式中:P1—蜗杆传动传递的功率(KW);Ks—散热系数,一般取 Ks=10~17[W/(m2·℃)];A—散热面积(m2),指箱体外壁与空气接 触而内壁被油飞溅到的箱壳面积,对于箱体上的散热片,其散热面积 按50%计算;t0—环境温度(℃),一般取20℃;t1—润滑油的工作温度 (℃) ;[t1]—润滑油许用温度(℃),一般取70~90 ℃。
一、蜗杆传动的效率
闭式蜗杆传动总效率包括: 考虑轮齿啮合齿面间摩擦损失时的效率;—(主要考虑) 考虑轴承摩擦损失的效率; 考虑浸入油池中的零件搅动润滑油时的溅油损耗率。 蜗杆传动的总效率为: (0.95~0.97 ) tan tan( v ) 其中 ——蜗杆导程角; v——当量摩擦角, v arctan fv , fv 为当量摩擦系 数,主要与蜗杆传动的材料、表面硬度和相对滑动速度有关。
机械设计基础第24页三蜗轮齿面弯曲疲劳强度计算由于蜗轮轮齿的齿形比较复杂通常近似地将蜗轮看作斜齿轮按圆柱齿轮弯曲强度公式来计算化简后齿根弯曲强度的校核公式为f2为蜗轮的齿形系数机械设计基础第25页155蜗杆传动的效率润滑和热平衡计算一蜗杆传动的效率闭式蜗杆传动总效率包括
机械设计基础
学习情境2:数控系统显示画面及操作
式中:T2=T1iη , η 为蜗杆传动的效率。
第21页
一、蜗杆传动的受力分析
机械设计基础
Ft 2
Ft1
⊙
Fr 2 Fx 2
Fx1
Fr1
第22页
机械设计基础
二、蜗轮齿面接触疲劳强度计算
对于钢制蜗杆对青铜或铸铁蜗轮(指齿圈),蜗轮齿 面接触疲劳强度的校核公式为 :
KT2 KT2 H 520 520 2 2 [ H ] 2 d1d 2 m d1 z2
《机械设计基础》第12章 蜗杆传动
3、摩擦磨损问题突出,磨损是主要 的失效形式。为了减摩耐磨,蜗轮齿圈常需用青铜制造,成本较高;
4、传动效率低,具有自锁性时,效率低于50%。
由于上述特点,蜗杆传动主要用于传递运动,而在动力传输中的应用受到限制。
其齿面一般是在车床上用直线刀刃的 车刀切制而成,车刀安装位置不同, 加工出的蜗杆齿面的齿廓形状不同。
γ
β
γ=β (蜗轮、蜗杆同旋向)
一、蜗杆传动的主要参数及其选择
1、模数m和压力角α
§12-2 蜗杆传动的参数分析及几何计算
ma1= mt2= m αa1=αt2 =α=20°
在蜗杆蜗轮传动中,规定中间平面上的模数和压力角为标准值,即:
模数m按表12-1选取,压力角取α=20° (ZA型αa=20º;ZI型αn=20º) 。
阿基米德蜗杆(ZA蜗杆) 渐开线蜗杆(ZI蜗杆)
圆柱蜗杆传动
环面蜗杆传动
锥蜗杆传动
其蜗杆体在轴向的外形是以凹弧面为母线所形成的旋转曲面,这种蜗杆同时啮合齿数多,传动平稳;齿面利于润滑油膜形成,传动效率较高。
同时啮合齿数多,重合度大;传动比范围大(10~360);承载能力和效率较高。
三、分类
在轴剖面上齿廓为直线,在垂直于蜗 杆轴线的截面上为阿基米德螺旋线。
§12-5 圆柱蜗杆传动的强度计算
一、蜗轮齿面接触疲劳强度的计算
1、校核公式:
2、设计公式:
式中:a—中心距,mm;T2 —作用在蜗轮上的转矩,T2 = T1 iη; zE—材料综合弹性系数,钢与铸锡青铜配对时,取zE=150;钢与铝青铜或灰铸铁配对时, 取zE=160。 zρ—接触系数,由d1/a查图12-11,一般d1/a=0.3~0.5。取小值时,导程角大,故效率高,但蜗杆刚性较小。 kA —使用系数,kA =1.1~1.4。有冲击载荷、环境温度高(t>35oC)、速度较高时,取大值。
史上最好用机械计算与非标选型—蜗轮蜗杆强度计算与校核
n1 n2
59269.66 表4 T2=ηuT1
班次*班时*天数*年限
应力循环次数N
寿命系数KHN 材料弹性影响系数ZE(MP1/2)
d1/a值
即2q/(q+z2)
接触系数Zρ
基本许用应力[σH]'
许用应力[σH]
5.09E+07 0.82 160 0.35 2.90 268 218.66
验算d1/a
蜗轮材料
铸造方法
单侧工作
双侧工作
铸锡青铜 砂型铸造
40
29
ZCuSn10P1 金属模铸造
56
40
铸锡锌铅青铜 砂型铸造
26
22
ZCuSnSPB5Zn5 金属模铸造
32
26
铸铝铁青铜 砂型铸造
80
57
ZCuAl10Fe3 金属模铸造
90
64
灰铸铁
HT150砂型铸造 40
28
HT200砂型铸造 48
34
返回目录
蜗轮蜗杆强度计算与校核
蜗轮按齿面接触疲劳强度计算最小中心距
参数与条件 载荷分布系数 K=KA*KV*Kβ= 1.2075
蜗杆类型
使用系数KA 动载系数KV 齿向载荷分布Kβ
数值 1.15
备注 表1
1.05
表2
1
表3
ZI/ZA/ZN/ZK螺杆 左侧下拉菜单选择
蜗轮材料
压力角α
传动比u 蜗杆头数Z1 蜗轮齿数Z2
均取206GPa I=πdf14/64 [y]=d1/1000
热平衡核算(闭式蜗轮蜗杆)
箱体表面传热系数αd=8.15~17.45
17.00
- 1、下载文档前请自行甄别文档内容的完整性,平台不提供额外的编辑、内容补充、找答案等附加服务。
- 2、"仅部分预览"的文档,不可在线预览部分如存在完整性等问题,可反馈申请退款(可完整预览的文档不适用该条件!)。
- 3、如文档侵犯您的权益,请联系客服反馈,我们会尽快为您处理(人工客服工作时间:9:00-18:30)。
2
第9章 蜗杆传动
2. 蜗轮齿根弯曲疲劳强度计算
蜗轮齿根弯曲疲劳强度校核公式
设计公式
1.53KT2 cos F YF [ ]F 2 d1z2m
1.53KT2 cos m d1 YF z2 [ ]F
2
式中:YF——蜗轮齿形系数,是考虑轮齿的几何形状对齿根弯曲 z2 应力的影响而引入的系数。 zv 2 3
缺点:效率低,当蜗杆主动时,效率一般为0.7~0.8; 由 于齿面相对滑移速度大,易磨损和发热,不适于传递大功率; 为减小磨损, 蜗轮齿圈常用铜合金制造,故其成本较高;蜗杆 传动对制造安装误差比较敏感, 对中心距尺寸精度要求较高。
综上所述, 蜗杆传动常用于传递功率在50 kW以下, 滑动 速度在15 m/s以下的机械设备中。
第9章 蜗杆传动
9.4
1. 蜗轮齿面接触疲劳强度计算 蜗轮齿面接触疲劳强度校核公式
KT2 KT2 H 500 500 2 2 [ ]H 2 d1d 2 m d1 z2
经过整理得到接触疲劳强度设计公式
500 m d1 KT2 z [ ] 2 H
2
是蜗杆在啮合点所受轴向力Fa1的方向, 也就是蜗杆相对与蜗轮
的移动方向。而事实上蜗杆是不能轴向移动的,故蜗轮在啮合 点的速度方向应指向相反方向,即Fa1的相反方向,既拇指的相 反方向。
第9章 蜗杆传动
9.2.2 蜗杆传动的基本尺寸计算 表9-3 标准阿基米德蜗杆传动的基本尺寸计算
第9章 蜗杆传动
设蜗杆传动在单位时间内损失的功率变成的热量为 Q1 ,同时间 由箱体表面散出的热量为Q2, 则热平衡条件为
Q1=Q2
因为 Q1=1000P1(1-η),Q2=SKS(t-t0)
第9章 蜗杆传动
所以热平衡时的油温t为
1000P 1 (1 ) t t0 SKS
风良好时取大值;
(9-15) ), 通
第9章 蜗杆传动
9.1.2 蜗杆传动的类型
图9-2 (a) 圆柱蜗杆传动; (b) 环面蜗杆传动; (c) 锥蜗杆传动
第9章 蜗杆传动
圆柱蜗杆由于其制造简单,因此有着广泛的应用。环面蜗 杆传动润滑状态良好,传动效率高,制造较复杂,主要用于大
功率传动。
按普通圆柱蜗杆螺旋面的形状可分为阿基米德( ZA )蜗
杆(普通蜗杆)、渐开线(ZI)蜗杆、法向直齿廓(ZN)蜗杆(延
伸渐开线蜗杆)和圆锥包络(ZK)蜗杆。
第9章 蜗杆传动
1. 阿基米德蜗杆 如图9-3所示,阿基米德蜗杆一般是在车床上用成型车刀切 制的。在垂直轴线的端面上,其齿形为阿基米德螺线。这种蜗 杆加工工艺性好,应用最广泛,缺点是磨削蜗杆及蜗轮滚刀时
蜗杆传动中,蜗轮蜗杆必须满足的啮合条件是
ma1 ma 2 m a1 a 2
(9-1)
第9章 蜗杆传动
2. 传动比i、蜗杆头数z1和蜗轮齿数z2
蜗杆传动比
n1 z2 i n2 z1
式中:n1,n2——为蜗杆蜗轮的转速;
z1,z2——蜗杆头数、 蜗轮齿数。
有理论误差, 精度不高。
第9章 蜗杆传动
图9-3 阿基米德蜗杆
第9章 蜗杆传动
2. 渐开线蜗杆
图9-4 渐开线蜗杆
第9章 蜗杆传动
9.2 普通圆柱蜗杆传动的主要参数和几何尺寸计算
图9-5 蜗杆传动的基本尺寸
第9章 蜗杆传动
9.2.1 蜗杆传动的主要参数及其选择
1. 模数m和压力角α
标准模数m查表, 标准压力角α=20°
第9章 蜗杆传动
第9章 蜗杆传动
9.1
9.2
9.3 蜗杆传动的失效形式、 设计准则和材料选择
9.4 蜗杆传动的强度计算
9.5 蜗杆传动的效率、 润滑和热平衡计算
9.6 蜗杆和蜗轮的结构
习题
第9章 蜗杆传动
9.1 蜗杆传动概述
图9-1 蜗杆传动
第9章 蜗杆传动
9.1.1 优点:大的传动比、结构紧凑;传动平稳、噪声低;在一 定条件下, 该机构可以自锁。
第9章 蜗杆传动
2. 螺栓联接式 青铜齿圈与铸铁轮芯可采用过渡配合或间隙配合,如H7/ j6或 H7/h6 。用普通螺栓或铰制孔用螺栓联接 ( 如图 9-11 (b) 所示),蜗轮圆周力由螺栓传递。 螺栓的尺寸和数目必须经过
强度计算。铰制孔用螺栓与螺栓孔常用过盈配合 H7/r6
。螺
栓联接式蜗轮工作可靠,拆卸方便,多用于大尺寸或易于磨损 的蜗轮。
第9章 蜗杆传动
3. 主要用于铸铁蜗轮、 铝合金蜗轮以及直径小于100mm的青 铜蜗轮。
第9章 蜗杆传动
4.
将青铜齿圈铸在铸铁轮芯上, 然后切齿(如图9-11(c)所 示)。 只用于成批制造的蜗轮。
图9-11 蜗轮的结构形式
第9章 蜗杆传动
习 题
9-1 蜗杆传动的主要参数?
9-2蜗杆传动的失效形式有哪些?
第9章 蜗杆传动
9.3.2
1. 蜗杆常用材料
表9-4 蜗 杆 材 料
第9章 蜗杆传动
2. 蜗轮的常用材料
(1) 铸造锡青铜。常用的有 ZCuSn10Pl 、 ZCuSn5Pb5Zn5 。其 中后者常用于vs<12 m/s的传动。
(2) 铸造铝青铜。常用的有ZCuAl10Fe3、ZCuAl10Fe3Mn2等。
(2) 提高散热系数。在蜗杆轴端安装风扇强迫通风,如图99(a)所示。 (3)加冷却装置。 在箱体油池内装蛇形冷却水管(如图9-9 (b)),或用循环油冷却(如图9-9(c))。
第9章 蜗杆传动
图9-9 蜗杆传动的散热方式
第9章 蜗杆传动
9.6 蜗杆和蜗轮的结构
9.6.1 蜗杆的结构形式
图9-10 蜗杆的结构形式
z1 pa1 z1m z1 tan d1 d1 q
式中:pa1——蜗杆的轴向齿距。
(9-4)
第9章 蜗杆传动
图9-6 蜗杆导程
第9章 蜗杆传动
5. 当已知蜗杆的螺旋方向和转动方向时, 可利用判断斜齿轮 轴向力方向的“主动轮左、右手定则”(见图 8-44 )来确定蜗 轮的转动方向:四指沿着蜗杆转动方向弯曲, 则拇指的指向就
9.3 蜗杆传动的失效形式、 设计准则和材料选择
9.3.1
主要有轮齿的点蚀、弯曲折断、磨损及胶合失效等。 蜗杆传动的设计准则为:开式蜗杆传动以保证蜗轮齿根弯 曲疲劳强度进行设计;闭式蜗杆传动以保证蜗轮齿面接触疲劳 强度进行设计,并校核齿根弯曲疲劳强度;此外因闭式蜗杆传 动散热较困难,故需进行热平衡计算。
(9-2)
需要ቤተ መጻሕፍቲ ባይዱ出的是, 蜗杆传动的传动比不等于蜗轮、 蜗杆分 度圆直径之比。
第9章 蜗杆传动
2. 蜗杆分度圆直径d1和蜗杆直径系数q
蜗杆分度圆直径d1与模数m的比值称为蜗杆直径系数,用q 表示。
d1 q m
第9章 蜗杆传动
3. 蜗杆导程角γ
按照螺纹形成原理,将蜗杆分度圆柱展开,如图 9-6 所示。 得到蜗杆在分度圆柱上的导程角γ为
cos
第9章 蜗杆传动
9.5.1 蜗杆传动的效率
tan (0.95 ~ 0.97) tan( V )
(9-14)
式中:γ——蜗杆导程角;
ρV——当量摩擦角,ρV =arctanfV,fV为当量摩擦系数,其值可
根据滑动速度vs由表9-8查取。
第9章 蜗杆传动
9.5.3 热平衡计算
式中:KS——箱体表面散热系数,KS=10~18 W/(m2·℃
S——散热面积(m2),指内壁被油浸溅到且外壁与流通空气接 触的箱体外表面积。对于箱体上的散热片,其散热面积按 50 %
t0——环境温度,通常取t0=20℃。
第9章 蜗杆传动
当t>75~85℃时, (1) 增加散热面积。 箱体上铸出或焊上散热片。
9-3
9-4
9-5
9-6
第9章 蜗杆传动
9-7 标出题9-7图中未注明的蜗杆或蜗轮的旋向及转向 (均为蜗杆主动),画出蜗杆和蜗轮受力的作用位置及方向。
题9-7图 蜗杆传动
第9章 蜗杆传动
9-8 有一蜗杆传动,模数m=8mm,蜗杆分度圆直径d1=110
mm,蜗杆齿数z1=1,蜗轮齿数z2=47,计算蜗轮和蜗杆的主要
第9章 蜗杆传动
9.6.2 1. 这种结构由青铜齿圈及铸铁轮芯组成 (如图9-11(a)所示), 齿圈与轮芯常采用过盈配合H7/s6或H7/r6,加热齿圈或加压 装配。蜗轮圆周力靠配合面摩擦力传递。为可靠起见,沿配合
面装置4 ~8个螺钉,为便于钻孔,应将螺孔中心线由配合缝偏
向材料较硬的轮芯部分2~3 mm。这种结构多用于中等尺寸及 工作温度变化较小的蜗轮,以免因热胀冷缩而影响过盈配合。