基于多体动力学的发动机连杆的结构优化
连杆的优化设计

连杆的优化设计1 前言随着汽车工业制造技术的发展,对于汽车发动机的动力性能及可靠性要求越来越高,而连杆的强度、刚度对提高发动机的动力性及可靠性至关重要。
因此,国内外各大汽车公司对发动机连杆的材料及制造技术的研究都非常重视。
“小体积、大功率、低油耗”的高性能发动机对连杆提出更新、更高的要求:(1)作为高速运动件重量要轻,减小惯性力,降低能耗和噪声;(2)强度、刚度要高,并且要有较高的韧性;这就意味着对连杆的设计和加工有着更高的要求。
其一,杆身有足够的刚度可以预防工作时发生弯曲变形;其二,连杆的大端和连杆盖有足够的刚度,以防大端变形时连杆螺栓承受附加的弯曲应力和大端失圆,使轴承润滑破坏。
同时,还要求连杆组具有足够的疲劳强度和冲击韧性。
[3]连杆的优化设计2 连杆机构2.1 连杆机构的特点连杆机构具有以下传送特点:1.连杆机构中的运动副一般均为低副(故又称其为低副机构,lower pair mechanism)。
其运动副元素为面接触,压力较小,承载能力较大,润滑好,磨损小,加工制造容易,且连杆机构中的低副一般是几何封闭,对保证工作的可靠性有利。
2.在连杆机构中,在原动件的运动规律不变的条件下,可用改变各构件的相对长度来使从动件得到不同的运动规律。
3.在连杆机构中,连杆上的各点的轨迹是各种不同形状的曲线(称为连杆曲线,coupler-pointcurve),其形状随着各构件相对长度的改变而改变,故连杆曲线的形式多样,可用来满足一些特定工作的需要。
利用连杆机构还可很方便地达到改变运动的传递方向、扩大行程、实现增力和远距离传动等目的。
连杆机构也存在如下一些缺点:1.由于连杆机构的运动必须经过中间构件进行传递,因而传动路线较长,易产生较大的误差累计,同时也使机械效率降低。
2.在连杆机构运动中,连杆及滑块所产生的惯性力难以用一般平衡方法加以消除,因而连杆机构不宜用于高速运动。
此外,虽然可以利用连杆机构来满足一些运动规律和运动轨迹的设计要求,但其设计十分繁难,且一般只能近似地满足。
汽车四缸汽油机的曲柄连杆机构设计(有全套图纸)
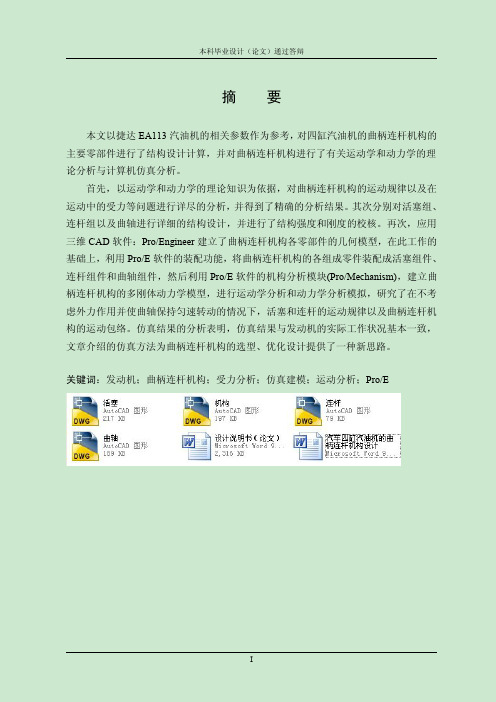
2.1.1 活塞位移······································································································5 2.1.2 活塞的速度··································································································6 2.1.3 活塞的加速度······························································································6 2.2 曲柄连杆机构中的作用力······················································································7 2.2.1 气缸内工质的作用力··················································································7 2.2.2 机构的惯性力······························································································7 2.3 本章小结················································································································14
某型发动机连杆小头衬套故障分析与优化设计20150814

某8V柴油机连杆小头衬套故障分析与改进设计赵志强1王根全1王延荣1 张利敏1 许春光1(1.中国北方发动机研究所(天津),天津300400)摘要:针对某8V柴油机50h台架试验中出现的衬套磨损和松动的故障,在故障分析的基础上,从改善轴承润滑、提高衬套固持力和提高连杆小头刚度三方面入手,借助经验、理论计算及有限元仿真等手段开展结构改进分析进而提出改进方案,该方案经500h台架耐久性试验考核未重现上述故障,由此验证本文改进措施的有效性。
关键词:柴油机衬套改进设计试验验证连杆是往复活塞式内燃机动力传递的重要组件,它承受周期性交变载荷,把活塞旋转往复直线运动转化为曲轴的旋转运动,并将作用在活塞上的力传递给曲轴对外输出功率[1,2]。
连杆小头衬套作为连杆组件的关键零件,它与活塞销组成一对滑动轴承副,连杆小头衬套与连杆体采取过盈的方式紧固联接、小头衬套与活塞销为间隙配合,连杆衬套的磨损和松动是连杆的主要失效形式。
本研究对象为某8V柴油机连杆小头衬套,分析并确定其故障机理,基于经验、理论公式和有限元仿真软件技术确定出改进方案,最终经试验验证,找到衬套磨损和松动的解决措施。
1 某8V柴油机连杆小头衬套故障描述某8V柴油机在初样机阶段多台样机在50h 台架试验中发生衬套磨损和松动的故障,连杆小头衬套磨损故障见图1、连杆小头衬套松动见图2。
图1连杆小头衬套磨损故障图2连杆小头衬套松动故障2 故障分析依据经验分析,连杆衬套磨损、发黑一般应从润滑角度考虑;连杆小头衬套松动、脱出应该从衬套与连杆体固持力不足角度分析,但往往两者非独立故障导致衬套故障,存在一定关联关系影响。
如连杆轴承润滑不良,衬套和活塞销摩擦表面的摩擦磨损状态会发生剧变,衬套安装固持力和摩擦力会此消彼长,过度的磨损使衬套的固持力持续下降,而摩擦力持续增加,当衬套安装固持力和工作摩擦力发生逆转时,故障现象随即出现;而衬套固持力不足,衬套会发生松动和旋转现象,使衬套进油孔和连杆体进油孔位置错位,导致轴承润滑不畅发生衬套磨损和烧蚀故障。
发动机连杆的有限元分析及结构优化

23 网格划分 . 建 模 后须 对 模 型 进行 网格 划 分 。A WE不 仅 具 有 功 能 强 大 的 网 格 划 分 工 具 ,还 能 进 行 智 能 化 网
格划 分 ,生 成 形 状 特 性 较 好 的单 元 来 保 证 网格 质 量 ,给 使 用 者 节 省 了大 量 的 时 间 和精 力 。一 般 情 况 下 ,采 用 默认 网格 控 制 即 可 。有 时 ,为 了获 得 高 质 量 的 网 格 ,也 可 通 过 一 定 的控 制 使 其 尽 量 符
3 建 出连 杆 在 摆动 面 及 垂 直 摆 动 面 方 向 上 的截 面 ) 草 图 ,再 用 扫 略 命 令 切 出 圆弧 过 渡 区 。最 终 选 定
思 路 三 进 行 建 模 ,此 法 所 建 模 型 更接 近 实 物 ,且 所 需 指 定 的优 化 参 数 较 少 ,优 化 耗 时也 较 少 ,约
合 有 限 元 计 算 的 要 求 ,提 高计 算 精 度 。根 据 所 建 模 型 ,本 文 比较 了 四种 不 同 网格 尺 寸 对 计 算 结 果 的影 响 ,在 完全 采 用 默 认 控 制 的情 况 下 ,连 杆 上
图 1 网格 划 分 后 的实 体 模 型
242约束处理 .. 边 界 约 束 可 消除 整 体 模 型 的 刚性 位 移 和确 定
一
般 来 说 ,对 于 钢 、铜 、铝 等 塑 性 材 料 ,可
根 据第 四 强度理 论 ,选 用 V nMi s o s 等效 应力 进行 e 强 度校 核 。
24 A 中的连杆边界处理 . WE
241施 加载荷 ..
1 )在最 大 压 缩 工 况 下 ,应 力 集 中区 主 要分 布
内燃机连杆结构的最优化设计

仲恺农业工程学院2013-2014学年度第二学期《现代机械设计方法》期末课程考察报告报告题目: 内燃机连杆结构的最优化设计报告摘要(200字):连杆是内燃机的主要运动件之一,作用是将活塞的往复直线运动变成曲轴的回转运动,并在活塞和曲轴之间传递作用力。
针对这一课题本文简要介绍了结构优化相关的理论基础,主要将连杆设计分为三部分:小头、杆身、大头,而且对连杆各部位的静力进行分析确定连杆结构,并结合采用有限元法数值计算技术对连杆结构进行分析。
学院:机电工程学院专业:机械设计制造及其自动化班级:113班姓名:姚永俊、尹世和、余帅权、郑晓伟学号:201110824336、201110824337、201110824338、201110824339评分:LI录21连杆的组成及设计要求2 2连杆结构优化设计思路3优化设计步骤 3 1连杆小头设计 3 2连杆杆身设计 4 3连杆大头设计 5优化设计理论应用61内燃机连杆的最优化设计方法分析 6 1. 1连杆最优化设计模型 61.2目标函数的选取 6 1. 3设计变量的选取 7 1.4约束条件的确定 7 2计算结果与分析 7 优化总结91. 1. 1.2. 2. 2. 2.3.3. 3. 3. 3. 3. 3.4.1.前言连杆是内燃机的主要运动件之一,连杆的作用是将活塞的往复直线运动变成曲轴的回转运动,并在活塞和曲轴之间传递作用力,连杆的结构和性能直接影响内燃机的正常运转。
采用常规设讣难于使连杆达到既轻乂可靠的要求,而选用最优化方法并结合采用有限元法数值讣算技术对连杆结构进行分析,则可圆满完成这一任务,并得出连杆最优化设计后的结构形状。
本文就是针对这一课题研究了内燃机连杆的结构优化方法,简要介绍了结构优化相关的理论基础。
1.1连杆的组成及设计要求1.1.1连杆组成连杆由连杆小头、连杆大头、连杆杆身组成。
其中连杆小头由连杆体的小头部分和连杆衬套组成。
连杆大头山连杆体的大头部分、连杆螺钉(栓)、连杆轴瓦组成。
柴油机连杆的优化设计本科学位论文

毕业设计(论文)题目6108柴油机连杆的优化设计注意事项1.设计(论文)的内容包括:1)封面(按教务处制定的标准封面格式制作)2)原创性声明3)中文摘要(300字左右)、关键词4)外文摘要、关键词5)目次页(附件不统一编入)6)论文主体部分:引言(或绪论)、正文、结论7)参考文献8)致谢9)附录(对论文支持必要时)2.论文字数要求:理工类设计(论文)正文字数不少于1万字(不包括图纸、程序清单等),文科类论文正文字数不少于1.2万字。
3.附件包括:任务书、开题报告、外文译文、译文原文(复印件)。
4.文字、图表要求:1)文字通顺,语言流畅,书写字迹工整,打印字体及大小符合要求,无错别字,不准请他人代写2)工程设计类题目的图纸,要求部分用尺规绘制,部分用计算机绘制,所有图纸应符合国家技术标准规范。
图表整洁,布局合理,文字注释必须使用工程字书写,不准用徒手画3)毕业论文须用A4单面打印,论文50页以上的双面打印4)图表应绘制于无格子的页面上5)软件工程类课题应有程序清单,并提供电子文档5.装订顺序1)设计(论文)2)附件:按照任务书、开题报告、外文译文、译文原文(复印件)次序装订3)其它学生毕业设计(论文)原创性声明本人以信誉声明:所呈交的毕业设计(论文)是在导师的指导下进行的设计(研究)工作及取得的成果,设计(论文)中引用他(她)人的文献、数据、图件、资料均已明确标注出,论文中的结论和结果为本人独立完成,不包含他人成果及为获得重庆科技学院或其它教育机构的学位或证书而使用其材料。
与我一同工作的同志对本设计(研究)所做的任何贡献均已在论文中作了明确的说明并表示了谢意。
毕业设计(论文)作者(签字):年月摘要连杆在现代汽车工业中所起到的作用无可替代,是发动机中主要传动部件之一。
但由于连杆工作情况的恶劣,传统的设计方法已经很难兼顾稳定性、经济性等方面,缺乏竞争力。
本文基于这一实际情况首先将完成6108型柴油机连杆各参数的设计计算并进行传统校核,校核均安全后运用CATIA和CAXA等软件分别建立三维和二维模型,完成连杆三维和二维的零件图和装配图。
abaqus连杆结构优化两例

连杆结构优化两例康黎云司庆九罗为(长安汽车股份有限公司动力研究院,重庆401120)摘要:本文通过对比两款不同发动机连杆的强度和疲劳分析结果,说明连杆不同设计形式采取的不同优化措施,同时归纳出一般性连杆分析时应关注的区域和设计要点,使用ABAQUS作为求解工具方便地实现以上目标。
关键词:连杆强度疲劳优化 ABAQUS1前言汽油机连杆作为关重的5C件之一,承受拉压和弯曲组合载荷作用,承载变化剧烈,设计上应保证其有足够的刚度和强度。
连杆组件主要结构包括:连杆体(也称为杆身)、连杆盖、连杆螺栓、大头轴瓦,有些连杆有小头衬套和定位销。
连杆螺栓有两种结构形式,如图1所示。
左图形式的螺栓从杆身肩部的螺纹孔穿入,另一端用螺母拧紧,连杆螺栓孔内并无内螺纹;右图形式的螺栓从连杆盖侧的螺栓孔穿入,杆身的螺栓孔内有内螺纹。
两种结构形式的最大区别是杆身肩部的几何,前者刚度较弱,是疲劳失效的关键区域之一。
本文将针对这两种不同形式连杆的强度及优化进行对比。
图1 连杆螺栓的两种不同形式(左图为连杆1,右图为连杆2)2分析过程由于连杆的对称性,一般有限元建模都只用1/2模型以降低求解规模,节省计算时间。
网格划分时连杆体、连杆盖、螺栓使用C3D10M单元,轴瓦、活塞销、曲柄销使用C3D8I 或者C3D6单元。
接触对包括:连杆体-连杆盖、螺栓头部-连杆体、螺帽-连杆盖(对第2种形式的螺栓为螺栓头部-连杆盖)、轴瓦-连杆、上瓦-下瓦、曲柄销-轴瓦、活塞销-连杆小头(或衬套)等。
螺栓预紧力采用最小螺栓轴力,在相应位置的接触对中设置过盈或间隙。
有限元模型如图2所示。
图2 连杆有限元模型2.1 边界条件&载荷步连杆的载荷主要以燃气爆发压力和惯性力为主,最大拉伸载荷出现在进气冲程开始的上止点附近,其数值为活塞组件和计算断面以上那部分连杆质量的往复惯性力2')1)((ωλr m m P s p t ++=[1]其中,m p 为活塞组件质量,m s 最大压缩载荷出现在膨胀冲程开始的上止点附近,其数值等于爆发压力减去上述的惯性力。
发动机曲柄连杆机构多体动力学建模的若干问题

在 ADAM S 2005 以前的版本要用“Move”将柔性 体移到与要替代的刚体相重合的位置上 ,建立约束和 运动副后 ,删除刚体 ,但 ADAM S 2005 新开发了一工 具 ,可直接将柔性体替换为刚性体 ,也可将柔性体替 换为柔性体 ,替换后刚性体或柔性体上的运动副 、载 荷等会自动转移到柔性体上 ,刚性体或柔性体上的 M arker点会转移到柔性体上与 M arker点最近的节点 上 [ 5 ] ,方便了柔性体的导入 。故建立准确的界面点 , 即可连接零件 ,而不会产生偏心力矩 ,从而提高了仿真 精度 。
将模态中性文件读入 ADAM S /V iew后 ,系统将其 原点放在整体惯性坐标系的原点上 ,且与其他零件没 有任何关系 ,其位置不一定是所要的位置 ,定义运动副 和载荷也不方便 ,同时考虑到一些约束 、力 、力矩及柔 性连接不可直接加到柔性体上 ,则需要通过创建虚构 件 (Dummy Part)以建立柔性体与其他件之间的连接 关系 。
定义刚体时 ,利用 Pro / E灵活的装配功能可将相 互没有运动的零件组成一个装配体 ,以方便刚体的定 义 ,如 :将气环 、油环 、活塞销挡圈 、活塞组成一个装配 体 ,连杆和连杆盖组成一个装配体 ,选择定义刚体时 , 将活塞装配体 、连杆装配体 、曲轴和飞轮分别选为一个 刚体 ,可大大减少运动副施加 , 提高求解速度 、仿真 效率 。
- 1、下载文档前请自行甄别文档内容的完整性,平台不提供额外的编辑、内容补充、找答案等附加服务。
- 2、"仅部分预览"的文档,不可在线预览部分如存在完整性等问题,可反馈申请退款(可完整预览的文档不适用该条件!)。
- 3、如文档侵犯您的权益,请联系客服反馈,我们会尽快为您处理(人工客服工作时间:9:00-18:30)。
基于多体动力学的某一发动机连杆的结构优化分析
杨怀刚
(长安汽车工程研究院CAE所)
摘要:本文通过应用A VL EXCITE软件对公司新研发的某款发动机连杆进行多体动力学分析;
然后利用分析结果对连杆进行一个工作循环的动应力分析,该结果与连杆的装配应力叠加进行疲劳分析。
通过分析发现,该连杆的大头肩部设计存在安全隐患。
为此,设计部门对连杆设计进行了改进;通过第二轮的CAE分析发现,其结果有了明显的改善,基本上达到了各项评价指标。
关键词:连杆; EXCITE; 多体动力学; 结构优化
主要软件:A VL EXCITE
1 前言
连杆组件包括连杆体、连杆盖、连杆螺栓、小头衬套和连杆轴瓦等件。
活塞的往复运动要经过连杆和曲拐转换成曲轴的旋转运动,因而连杆组件要承受缸内气体作用力和自身的惯性力。
本文对长安公司新开发的某款发动机连杆进行数值仿真分析:通过建立连杆组件的三维有限元模型,对其进行装配应力、模态压缩、多体动力学、动应力以及疲劳分析;分析结果表明该连杆的设计存在安全隐患;为此提出改进方案并得到设计部门的认可。
2分析方法
首先计算连杆的装配应力;然后应用EXCITE计算连杆组件多体动力学,分别计算4500、5000、5500、6000rpm四种工况。
然后计算最为恶劣工况的动应力,并与静力结果叠加,利用SMITH图解法求得连杆关键部位节点的疲劳安全系数。
2.1分析模型
连杆FE模型由连杆杆身、连杆大头轴承盖、连杆轴瓦以及螺栓四部分组成(图1)
应用Nastran103求解器对连杆FE模型进行模态压缩,并通过EXCITE将模态压缩结果文件转换为EXCITE可以识别的压缩模型的自由度、质量、刚度矩阵以及几何尺寸的文件。
图1 FE模型图2 EXCITE多体动力学模型
连杆的静力学计算包括连杆轴瓦最大、最小过盈量与最大、最小螺栓预紧力的四种组合工况(见表1)。
表1 静力学分析方案
轴瓦过盈量(μm) 螺栓预紧力(KN)
工况一 34 21.4
工况二 83 21.4
工况三 34 32.7
工况四 83 32.7
2.3 连杆的EXCITE计算设置参数
设置发动机连杆组件的数据资料:连杆长度;冲程;气缸直径;对于气缸套而言,将它简化为刚体,缩减节点的位置与自由度由手工添加。
连杆活塞销、活塞以及环组的质量都等效的加在连杆小头上。
连杆小头通过四个GUID导向单元与缸套连接。
连杆大头轴承的结构尺寸与特性参数如表2:
表2 连杆大头轴承的特性
轴承宽度 17mm
轴承直径 38mm
径向间隙 0.027mm
供油压力 4.5bar
气穴压力 0.5bar
油 温 130degC
润滑油类型 SAE 10W-30
接触条件 粗暴
粗 糙 度 1微米
弹性模量 5.77e11N/mm2
摩擦系数 0.01
2.4 EXCITE多体动力学所施加的气体爆发压力
图3 缸压爆发压力
3计算结果及评估
静力学计算主要考察连杆大头的刚度(通过结合面的滑移量来评估,见图4),装配应力分布(图5),以及结合面的压应力与剪应力(图6-7)等。
分析结果发现,连杆肩部的倒圆处存在应力过大的现象,这可能是肩部刚度偏低或螺栓预紧力过大引起的;并且连杆大头的刚度偏低。
图4 结合面滑移量图5 工况三的装配应力分布
图6 结合面压应力图7 结合面剪应力
3.2 EXCITE计算结果
对计算结果截取一个工作循环进行后处理。
主要分析曲柄销合成力(图8)、连杆大头轴承最小油膜厚度(图9)、最大油膜压力(图10)、最大接触压力(图11)、摩擦损失功率(图12-13)、摩擦力距(图14)、轴心轨迹(图15)等。
图8 图 9
图10 图11
图12 图13
图14 图15
然后应用A VL—IMPRESS软件考察液力轴承工作状态的的3维动画(见图16-19)。
图16 油膜填充率图17 油膜径向间隙
图18 总油膜压力图19 接触油膜压力
参照有关的评估标准,该连杆大头轴承具有较好的润滑状态。
3.3连杆的动应力计算结果
利用连杆EXCITE计算的结果,计算连杆在一个工作循环的动应力,并与装配应力叠加。
并考察大头结合面是否具有足够的压应力。
图20 一个工作循环内连杆的第一主应力最大值 图21 一个工作循环内连杆的第三主应力最小值
图22 结合面的动应力与工况一装配应力叠加的压应力、剪应力图
3.4 疲劳分析
根据以上动应力与静应力的叠加应力,对连杆的主要部位取一定数量的节点,应用SMITH 图解法作疲劳寿命分析(安全系数)。
计算发现,连杆原设计的肩部的安全系数低于 1.5;而后,通过对增加肩部壁厚的设计作再次分析发现,其安全系数有显著的提高,达到评估标准。
图23 安全系数的SMITH 图解法
4 改进方案
通过对连杆原设计方案的仿真分析提出改进方案(见图24): 1、增加连杆肩部的壁厚;2、延长大头盖的加强筋。
并减小最大轴瓦过盈配合。
图24 连杆的结构改进
5 结论
通过对公司新开发发动机连杆的多体动力学分析、装配应力、动应力以及疲劳分析,找出连杆设计的不合理之处;提出改进方案,消除了安全隐患,提高了连杆结构的可靠性。
通过本次分析,也证明了A VL —EXCITE 是发动机零部件多体动力学仿真的理想软件。
参考文献
1 AVL EXCITE-ConrodAnalysis_UsersGuide.pdf,Mar.2003;
2 AVL EXCITE-Primer.pdf,Mar.2003;
3 汽车发动机设计,陆际清等编著,清华大学出版社,1992。
Material:40Cr(bending)SigF:1080 SigSc:830 SigW:480
Material:40Cr SigF:785 SigSc:780 SigW:450。