压铸技术基础
一体压铸工艺

一体压铸工艺一体压铸工艺是一种将金属或其他材料一次性压铸成形的工艺。
它是在传统压铸技术的基础上发展而来的。
与传统压铸相比,一体压铸具有更高的生产效率和更好的产品质量。
一体压铸工艺的基本流程包括:原料准备、模具设计、熔炼铸造、冷却、去毛刺、加工和表面处理等步骤。
其中,模具设计是关键步骤之一。
模具的质量将影响到产品的精度和表面质量。
一体压铸的模具通常由多个部分组成,包括模座、模芯、浇口、冷却系统等。
这些部分需要精密加工,以确保模具的高精度和长寿命。
在一体压铸工艺中,原材料通常是金属合金或高性能材料,如铝合金、镁合金、锌合金等。
这些材料具有高强度、耐腐蚀性和良好的导热性能,适合于一体压铸工艺的要求。
一体压铸的主要优点是可以一次性完成铸造、冷却、去毛刺和加工等多个步骤,从而节省了生产时间和成本。
此外,一体压铸还可以生产出更加复杂和精密的零件,如汽车发动机缸体、摩托车发动机壳体、电子设备外壳等。
在一体压铸中,熔炼铸造是关键步骤之一。
熔炼铸造需要控制好熔炼温度、熔炼时间和熔炼材料的比例等参数,以确保铸件的质量。
铸件的质量将影响到产品的性能和寿命。
一体压铸中还需要进行冷却和去毛刺等步骤,以消除铸件表面的缺陷和毛刺,提高产品的表面质量。
一体压铸工艺还需要进行后续的加工和表面处理等步骤。
加工包括铣削、钻孔、螺纹加工等,以形成最终的产品形态。
表面处理包括喷漆、喷砂、电泳涂装等,以提高产品的外观和耐腐蚀性能。
一体压铸工艺是一种高效、精密、高质量的制造工艺。
它可以生产出各种复杂和精密的零件,具有广泛的应用前景。
在未来,一体压铸工艺将在各个领域得到广泛的应用,为人们的生产和生活带来更多的便利和创新。
压铸技术手册阅读随笔

《压铸技术手册》阅读随笔一、压铸技术基础首次翻开《压铸技术手册》我怀着一颗探索与学习的热情之心。
我对压铸技术的初步理解得到了深化,并且获取了许多新的知识和见解。
以下是我对“压铸技术基础”这一部分的阅读随笔。
压铸是一种金属成型工艺,通过将熔融的金属在高压下注入模具型腔,实现快速成型。
它广泛应用于制造业,特别是汽车、电子和航空等领域。
压铸技术具有成型精度高、生产效率高、材料利用率高等特点。
它也具有一定的技术要求,包括模具设计、材料选择等。
这一部分详细介绍了压铸常用的金属材料,如锌、铝、镁等合金。
每种材料都有其独特的性能和适用场景,选择何种材料需要根据产品的使用需求、生产工艺和成本等多方面因素综合考虑。
工艺过程是压铸技术的核心,这一部分详细介绍了从金属熔化、模具准备、压铸操作到产品后处理的整个过程。
每一个步骤都需要精细控制,以保证产品的质量和性能。
模具是压铸工艺中的重要组成部分,模具设计需要考虑到产品的结构、材料、生产工艺等多方面因素。
合理的模具设计可以提高生产效率,降低生产成本,并保障产品的质量和性能。
随着制造业的发展,压铸技术在各个领域的应用越来越广泛。
特别是在汽车、电子、航空等领域,压铸技术发挥着不可替代的作用。
这一部分还提到了压铸技术的未来发展趋势,如智能制造、绿色制造等。
1. 压铸技术的定义与发展历程压铸技术是一种金属成型工艺,通过将熔融的金属或半液态的金属在高压下注入模具型腔,经过冷却固化后获得所需形状和尺寸的金属零件。
这种技术广泛应用于汽车、航空、电子、通讯、医疗和家电等各个领域,是制造业中不可或缺的一部分。
压铸技术的历史可以追溯到几千年前,早期的压铸工艺主要用于制作饰品和艺术品。
随着工业革命的来临,压铸技术得到了迅速的发展。
从最初的手工操作到半机械化,再到全自动化的压铸设备,其工艺技术和设备不断更新迭代。
20世纪初,压铸技术开始广泛应用于汽车、航空等重工业领域,对于材料性能、工艺稳定性和生产效率的要求越来越高。
压铸基础知识

压铸基础知识我们的锌铝合金属于其中的哪一种?2压力铸造简称压铸,是一种将熔融合金液倒入压室内,以高速充填钢制模具的型腔,并使合金液在压力下凝固而形成铸件的铸造方法。
压铸区别于其它铸造方法的主要特点是高压和高速。
压铸机、压铸合金与压铸模具是压铸生产的三大要素,缺一不可。
办公用品| 卫浴五金| 电子/| 机械| 五金|31.由于压入铸模内的合金液一般是在非真空的条件下急速冷却凝固的,如2.普通方法生产的压铸件不能进行高温热处理和焊接。
3.目前压铸某些内凹件、高熔点合金铸件还比较困难。
4.压铸设备价格高,模具制造需要一定周期,所以不宜单件或小批量生4的问题来源于模具,所以模具是我们生产最重要的工具。
5固定在壓鑄機定模安裝板上,有直澆道與固定在壓鑄機動模安裝板上,並隨動模安液體金屬在高壓下充滿型腔;借助於設在動模上的推出機構將鑄件推6使料液平稳且有序地填充到开腔中并在填充过程和凝固过程中把压力传迅到各个部位,以获得所需的组织紧密,外观清晰的产品母模仁公模仁7使料液平稳且有序地填充到开腔中并在填充过程和凝固过程中把压力传迅到各个部位,以获得所需的组织紧密,外观清晰的产品冷却料浇口主浇道8导套导柱9实现零件的正常脱模10实现与开模方向不一致的侧孔,11为满足成型工艺对模具温度要求,以保证各种零件的冷却定型循环水路循环水路12保证零件熔体在充填过程中模腔中的气体完全排出,以让零件熔体顺利充满型腔排气槽13模座垫块144 曲面分型1516指生產過程中因模具設計產生排气及生產過程中殘留於機台及地面指生產過程中從機台溶爐表面經過打渣劑而產生的浮渣料;指生產過程中出現的排渣及浮渣料經熔解產生的物料。
水口料17新格18康帅192021喷离型剂注汤中子退压进压退取件开模冷却成型射出合模中子进222324挥发;)性能稳定在空气中稀释剂不应挥发过决而变稠;2526时针月份标27台阶成型标准成型28高出293031磨砂机平面磨砂机32砂带按型号分有:60#、80#、120#、180#、240#、400#、1200#等;型号越大,表示表面砂粒越细,打磨的表面越光滑;通常在砂带内表面标示有砂带型号及砂带转动方向。
压铸工艺参数分析

压铸工艺参数分析1.注射压力:注射压力是指在铸造过程中,金属熔液被压入型腔的压力大小。
注射压力的大小对于铸件的排气、充盈、凝固过程以及零部件的尺寸稳定性有着重要的影响。
过高的注射压力会导致铸件内部气泡的形成、表面粗糙度增大等问题,而过低的注射压力则会导致型腔内充盈不充分。
2.注射速度:注射速度是指熔融金属进入模具腔体的速度。
适当的注射速度可以使熔融金属在型腔内充盈均匀,防止铸件出现疏松、夹杂等缺陷。
过高的注射速度会导致金属熔液的剪切力增加,容易产生气泡和金属破碎现象,而过低的注射速度则会导致金属熔液在充盈过程中受到阻力,形成冷障。
3.注射温度:注射温度是指金属熔液注入型腔时的温度。
注射温度的高低会直接影响到铸件的凝固形态和组织结构。
过高的注射温度会导致铸件的表面质量较差,因为金属熔液的冷却速度过快,易产生冷障和贝氏体组织。
而过低的注射温度则会导致金属熔液黏度增大,充盈性变差。
4.金属液温度:金属液温度是指金属熔体在注射之前的温度。
金属液温度的高低会直接影响到铸件的凝固过程和性能。
过高的金属液温度会导致铸件的组织粗大,出现热裂纹等问题。
而过低的金属液温度则会导致铸件的毛细孔增多,降低铸件的密实性。
5.压射机的闭模力:压射机的闭模力是指用于关闭型腔的力大小。
闭模力的大小会直接影响到铸件的尺寸稳定性和机械性能。
过高的闭模力会导致铸件的尺寸过大,形成表面凸起和冷障等问题。
而过低的闭模力则会导致铸件尺寸的不稳定性和机械性能的下降。
6.模具温度:模具温度是指模具在铸造过程中的温度。
模具温度的高低会直接影响到铸件的组织结构和表面质量。
适当的模具温度可以提高铸件的表面光洁度,减少气孔和缩松等问题。
过高的模具温度会导致铸件的热组织粗大,而过低的模具温度则会导致铸件充盈性差。
总结起来,压铸工艺参数对于铸件质量和性能有着直接的影响。
合理的控制和选择工艺参数可以有效地改善铸件的表面质量、减少缺陷率,提高铸件的力学性能和尺寸稳定性。
压铸模具基础知识介绍
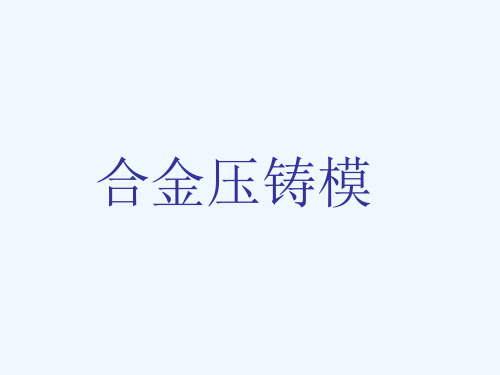
材料: T8A、T10A、H13 热处理: HRC 42~47
(6).限位块
作用: 滑块抽出后要求稳固保持在一定位置上,以便于再
次合模时斜销准确插入滑块斜孔,使滑块准确复位.
横浇道长度:取(直浇道)1/2 +(35~50) 横浇道长度尺寸不可以过短小,否那么使金属液起稳流和导
向作用不明显。
横浇道
3、内浇口:
内浇口应使金属液以最正确的流动状态充填型腔应先充填
型腔深腔部位,最后流向分型面,防止先封闭分型
面,防止金属液对型芯等薄弱部位冲击,易导致型
芯变形。
内浇口调整着从横浇道输送过来金属液速度,其位置和方向最
二 溢排系统:
据熔融金属在模具内填充情况,而开设排气通道。 用于容纳液态金属在充填过程中排出气体、杂物冷污合金等。
溢流槽
溢流槽的结构形式: (1)布置在模具分型面上的溢流槽 (2)布置在模具型腔内部的溢流槽。 其形式有: 杆形溢流槽 管形溢流槽 环形溢流槽 双级溢流槽 波纹状溢流槽
第二局部 压铸模浇排系统
一、 浇注系统:
引导金属液以一定的方式充填型腔,对金属液流动方向、 压力传递、充填速度、排气条件、模具的热平衡都能起 到控制和调节作用。 包括三个方面:
1。 直浇道 :
要求:有利压射力传递和金属液充填
平稳,。
对于冷室压铸模一般由压室和浇口套组成。
直浇道尺寸确实定是跟据铸件结构和重量等要 求来选择确立。
三 加热和冷却系统: 压铸模具在压铸生产前应进行充分地预热,并在压
铸过程中保持在一定温度范围内。 压铸生产中模具的温度由加热与冷却系统进行控制
压铸基础知识压铸的优缺点
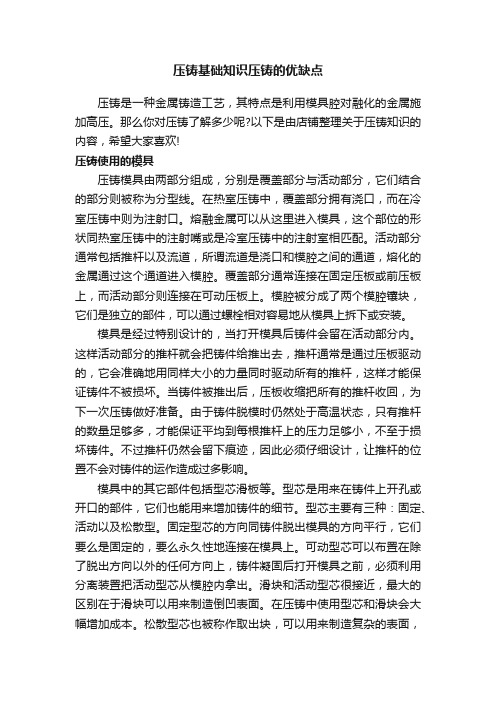
压铸基础知识压铸的优缺点压铸是一种金属铸造工艺,其特点是利用模具腔对融化的金属施加高压。
那么你对压铸了解多少呢?以下是由店铺整理关于压铸知识的内容,希望大家喜欢!压铸使用的模具压铸模具由两部分组成,分别是覆盖部分与活动部分,它们结合的部分则被称为分型线。
在热室压铸中,覆盖部分拥有浇口,而在冷室压铸中则为注射口。
熔融金属可以从这里进入模具,这个部位的形状同热室压铸中的注射嘴或是冷室压铸中的注射室相匹配。
活动部分通常包括推杆以及流道,所谓流道是浇口和模腔之间的通道,熔化的金属通过这个通道进入模腔。
覆盖部分通常连接在固定压板或前压板上,而活动部分则连接在可动压板上。
模腔被分成了两个模腔镶块,它们是独立的部件,可以通过螺栓相对容易地从模具上拆下或安装。
模具是经过特别设计的,当打开模具后铸件会留在活动部分内。
这样活动部分的推杆就会把铸件给推出去,推杆通常是通过压板驱动的,它会准确地用同样大小的力量同时驱动所有的推杆,这样才能保证铸件不被损坏。
当铸件被推出后,压板收缩把所有的推杆收回,为下一次压铸做好准备。
由于铸件脱模时仍然处于高温状态,只有推杆的数量足够多,才能保证平均到每根推杆上的压力足够小,不至于损坏铸件。
不过推杆仍然会留下痕迹,因此必须仔细设计,让推杆的位置不会对铸件的运作造成过多影响。
模具中的其它部件包括型芯滑板等。
型芯是用来在铸件上开孔或开口的部件,它们也能用来增加铸件的细节。
型芯主要有三种:固定、活动以及松散型。
固定型芯的方向同铸件脱出模具的方向平行,它们要么是固定的,要么永久性地连接在模具上。
可动型芯可以布置在除了脱出方向以外的任何方向上,铸件凝固后打开模具之前,必须利用分离装置把活动型芯从模腔内拿出。
滑块和活动型芯很接近,最大的区别在于滑块可以用来制造倒凹表面。
在压铸中使用型芯和滑块会大幅增加成本。
松散型芯也被称作取出块,可以用来制造复杂的表面,例如螺纹孔。
在每个循环开始之前,需要先手动安装滑块,最后再同铸件一起被推出。
压铸模具基本结构分析
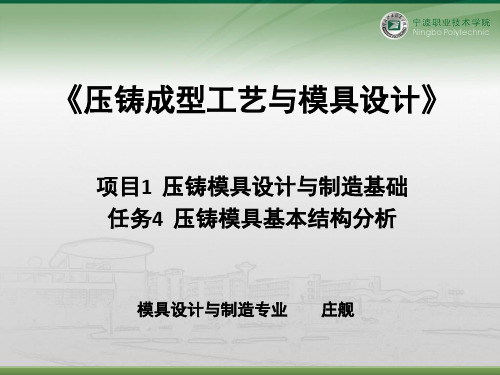
分流锥
装内饰浇盖道
横浇道 直浇道
材料的分析 模具的型腔布置
中心浇口浇中注心系浇统口
浇注装系饰统的盖设计
减速抽器芯盖机构 减速器盖
活动型芯
滑块、侧斜向滑分块型的设计 斜销、抽弯芯销机、构齿设轴计 楔紧块、楔紧销
限位钉、限位块
1 模具结构
序号 零件名称 1 压射冲头杆 2 压射冲头 3 压室 4 压铸机定模板 5 定模套
25 固定型芯
形成压铸件的凹陷区域(内表面)。
26
压 铸 模 具 型 压铸件在其中凝固成形。 腔
27
浇注及溢出 系统
浇注系统是金属液进入型腔的通路,排溢系统用于排出型腔内气体 及储存前端冷金属及涂料灰烬等。
1 模具结构
1 模具结构
1 模具结构
1 模具结构
结束语
好的模具就是让傻瓜都能使用
分流锥
内浇口 横浇道 直浇道
中心浇口浇注系统
装饰盖
抽芯机构
减速器盖
活动型芯 滑块、斜滑块 斜销、弯销、齿轴 楔紧块、楔紧销 限位钉、限位块
4冲50型汽缸盖
推杆、推管、卸料板 推出
推板、推杆、固定板 机构
复位杆、导柱、管接口
导套、限位钉
模脚垫块、座板
压 铸 模 具
模模 架体
开发方案的制定
压铸材料型的腔分析
6 浇口套
7 动模镶块
8 分流锥(器) 9 顶杆 10 动模套板
说明
连接压射冲头与压射活塞杆,进行压射动作。 推动金属液进入型腔,由于直接与金属液接触,容易磨蚀,需经常更换。 压射冲头一般用铸铁、钢材或铍青铜等材料制造。
容纳金属液,其内径与压射冲头配合。压射冲头在其中进行压射及复位 动作,压室材料为耐热钢。 机架的一部分,安装定模及压室。 定模外框,安装及固定定模镶块24、浇口套6等结构件。定模套板承受 锁模力及胀型力,故其强度在设计时应予校核计算,所用材料一般为结 构钢或球墨铸铁等。
压铸件缺陷和产生的原因

中国压铸技术基础(二)2010-3-24压铸件缺陷和产生的原因压铸生产中遇到的质量问题很多,其原因也是多方面。
生产中必须对产生的质量问题作出正确的判断。
找出真正的原因,才能提出相应切实可行的有效的改进措施,以便不断提高铸件质量。
压铸件生产所出现的质量问题中,有关缺陷方面的特征、产生的原因(包括改进措施)分别叙述于后。
一、欠铸压铸件成形过程中,某些部位填充不完整,称为欠铸。
当欠铸的部位严重时,可以作为铸件的形状不符合图纸要求来看待。
通常对于欠铸是不允许存在的。
造成欠铸的原因有:1)填充条件不良,欠铸部位呈不规则的冷凝金属Ø当压力不足、不够、流动前沿的金属凝固过早,造成转角、深凹、薄壁(甚至薄于平均壁厚)、柱形孔壁等部位产生欠铸。
Ø模具温度过低Ø合金浇入温度过低Ø内浇口位置不好,形成大的流动阻力2)气体阻碍,欠铸部位表面光滑,但形状不规则Ø难以开设排溢系统的部位,气体积聚Ø熔融金属的流动时,湍流剧烈,包卷气体3)模具型腔有残留物Ø涂料的用量或喷涂方法不当,造成局部的涂料沉积Ø成型零件的镶拼缝隙过大,或滑动配合间隙过大,填充时窜入金属,铸件脱出后,并未能被完全带出而呈现片状夹在缝隙上。
当之种片状的金属(金属片,其厚度即为缝隙的大小)又凸于周围型面较多,便在合模的情况下将凸出的高度变成适为铸件的壁厚,使以后的铸件在该处产生穿透(对壁厚来说)的沟槽。
这种穿透的沟槽即成为欠铸的一种特殊形式。
这种欠铸现象多在由镶拼组成的深腔的情况下出现。
Ø浇料不足(包括余料节过薄)。
Ø立式压铸机上,压射时,下冲头下移让开喷嘴孔口不够,造成一系列的填充条件不良。
二、裂纹铸件的基体被破坏或断开,形成细长的缝隙,呈现不规则线形,在外力作用下有发展的趋势,这种缺陷称为裂纹。
在压铸件上,裂纹是不允许存在的。
造成裂纹的原因有:1.铸件结构和形状Ø铸件上的厚壁与薄壁的相接处转变避剧烈Ø铸件上的转折圆角不够Ø铸件上能安置推杆的部位不够,造成推杆分布不均衡Ø铸件设计上考虑不周,收缩时产生应力而撕裂。