铝合金压铸工艺基础知识培训
压铸知识培训资料
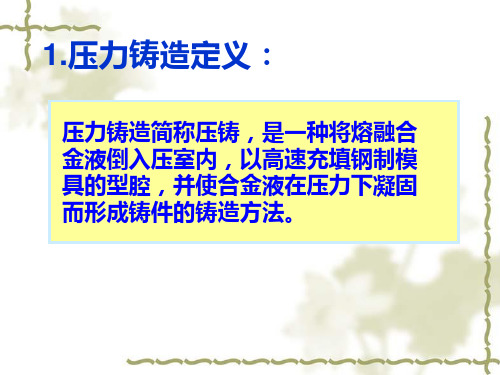
5.压铸机、压铸金属及压铸模具是组成压 铸工艺的3个要素。
卧式压铸机
立式压铸机
6.压铸机分类:
压铸机一般分为热压室压铸机和冷压室压铸机两大类。 冷压室压铸机按其压室结构和布置方式分为卧式压铸机 和立式压铸机(包括全立式压铸机)两种。 热压室压铸机(简称热空压铸机)压室浸在保温溶化坩 埚的液态金属中,压射部件不直接与机座连接,而是装 在坩埚上面。这种压铸机的优点是生产工序简单,效率 高;金属消耗少,工艺稳定。但压室,压射冲头长期浸 在液体金属中,影响使用寿命。并易增加合金的含铁量。 热压室压铸机目前大多用于压铸锌合金等低熔点合金铸 件,但也有用于压铸小型铝、镁合金压铸件。 冷室压铸机的压室与保温炉是分开的。压铸时,从保温 炉中取出液体金属浇入压室后进行压铸。
4.压力铸造适用材料及浇铸温度:
铝合金 铝硅系 610-650℃ 640-680℃ 600-620℃ 610650℃ 铝铜系 630-660℃ 660-700℃ 600-640℃ 630-660℃ 铝镁系 640-680℃ 660-700℃ 640-670℃ 650-690℃ 铝锌系 590-620℃ 620-660℃ 580-620℃ 600-650℃ 锌合金 420-440℃ 430-450℃ 400-420℃ 420-440℃ 镁合金 640-680℃ 660-700℃ 640-670℃ 650-690℃ 铜合金 普通黄铜 910-930℃ 940-980℃ 900-930℃ 900950℃ 硅黄铜 900-920℃ 930-970℃ 910-940℃ 910-940℃
7.压铸模具:
8.压铸工艺知识:
8-1、压力和速度的选择:按铸件结构确定。
8-2、浇注温度:从压定进入型腔时液态金属的平均温度。 8-3、压铸型的温度:在压铸前应进行预热。
压铸培训经典

压铸培训经典
内浇口速度对铸件的影响
l 内浇口速度高低与铸件机械性能的影响极大,内 浇口速度太低,铸件强度下降;速度提高,强度 上升;速度过高,强度又下降
压铸培训经典
冲头速度与内浇口速度的关系
l 根据连续性原理,在同一时间内金属流以速度 V1流过压室截面积为F1的合金液体积,应等于 以速度V2流过内浇口截面积为F2的合金液体积。
l 根据铸件的壁厚要求
l 在一般的情况下,压铸薄壁铸件时,型腔中的流动阻力 较大,内浇口也采用较薄的厚度,因此具有大的阻力, 故要有较大的填充比压,才能保证达到需要的内浇口速 度
l 对于厚壁铸件,一方面选定的内浇口速度较低,并且金
属的凝固时间较长,可以采用较小的填充比压;另一方
面,为了使铸件具有一定的致密度,还需要有足够的增
压铸培训经典
快压射速度的作用和影响
l 快压射对机械性能的影响
提高压射速度,动能转化为热能,提高了合金
熔液的流动性,有利于消除流痕,冷隔等缺陷, 提高了机械性能和表面质量,但速压铸培训经典
l 压射速度对填充特性的影响 压射速度的提高,使合金熔液在填充型腔时的 温度上升。流程增长,有利于改善填充条件,可 压铸出质量优良的复杂的薄壁铸件。但压射速度 过高时,填充条件恶化,在厚壁铸件中尤为显著。
压铸培训经典
持压时间
l 熔融金属充满型腔后,使熔融金属在增压比压作 用下凝固的这段时间,称为持压时间。
压铸培训经典
持压时间的作用
l 持压时间的作用是使压射冲头将压力通过还未凝 固的余料、及浇口部分未凝固的金属传递至型腔, 使正在凝固的金属在压力下结晶,从而获得致密 的铸件。
压铸操作工艺培训讲义(连载四)

压铸操作工艺培训讲义(连载四)五、国内外压铸铝合金1、国标牌号标注方法在国标中压铸铝合金的代号是用字母“YL”和其后的数字表示,“Y”及“L”分别为“压”、“铝”两字汉语拼音的第一个字母。
2、国内外主要压铸铝合金化学成分和力学性能如下表:压铸铝合金国家标准:压铸铝合金日本标准:压铸铝合金欧盟标准:压铸铝合金美国标准:3、合金中各元素的主要作用4、各元素对合金的影响①铝合金中硅的作用有两点,第一是增加流动性,但这点主要是对重力铸造等很低压强下的充填而言。
检测与实践都表明,不加硅的铝合金和加了硅的合金在超过1MPa的充型压强下,充型性能差异不大,而现在压铸生产中压射充型压强均达到30MPa以上,即使流动性最差的合金、如变形铝合金及变形镁合金,都不存在充型不足的困难。
第二点,也是铝合金中硅作用的最重要的一点,也是大家最容易忽略的一点。
硅的作用是减少“液-固”相的相变体积收缩率。
特别是高硅铝合金,当硅含量达到20%左右时如B390,ADC14铝合金,相变体积可以保持不变。
由于铝合金压铸属于单方向的高压强充型铸造,不具备有反向补缩作用。
正是这个原因压铸行业才特意配制相变收缩率比较低,含硅量高的铝合金牌号。
②硅含量的降低,压铸件毛坯在同样的压铸条件下,缩孔、疏松现象严重,合格率明显降低。
主要原因是硅含量的降低导致铝合金体积收缩率较大。
③硅及铜含量的降低,产品的机械强度降低,热裂倾向增加。
合金的延伸率增强,变得更软。
顶出时易变形甚至开裂。
一方面通过Mg和Mn 含量的配比提高机械强度,并在压铸工艺参数设定时,调整冷却时间、顶出速度及顶出力及脱模剂的喷涂,解决产品顶出时的变形及开裂的缺陷。
④元素Mn的作用,锰能阻止铝合金的再结晶过程,提高再结晶温度并能显著细化结晶晶粒。
再结晶的细化,主要是通过MnAl6化合物弥散质点对再结晶粒长大起阻碍作用。
过多的MnAl6能溶解杂质铁形成(Fe,Mn)Al6减少铁的有害影响。
故锰的含量也不能太高,控制在0.30-0.40%范围内。
压铸培训教程.pptx

r最大= h
R=r+h
压
铸
當h1=h時﹕
模
r≧ h+h1
设
3
计
R=r+ h+h1
2
2020/8/16
K值
鋅﹕1/4 鋁﹕1/2
Macherchen
10
四.成型工艺
(五)孔
鋅:0.8~1.5(最小直径)
鋁:2.0~2.5(最小直径)
(六)文字:凸凹纹﹐直纹
压
铸 例:平行纹(直纹)高0.7MM﹐间距1MM﹐角度60.5。
压 铸 模 设 计
2020/8/16
由喷射﹑喷射流转变为压力流
Macherchen
5
三.压铸制程溶汤的流动方式
(二)压力流
因冲撞,磨擦和气体阻力等(抽象),运动能量耗尽(常发生在加强筋,
凸台,远离浇口之部位),具有接受后继金属液中供给的压力能,从而使金
属液沿着型腔内壁前进的特性.利用这特性,可便以型腔排气.在压力流充
13
五.压铸合金及其性能
压 铸 模 设 计
2020/8/16
鋅合金種類
合 商業習用編號
No.3
金
ASTM
AG40A
代
UNS
Z33251
號
SAE
903
Die Cast Aged
抗拉強度(Kg/mm2) 28.8 24.6
機 降伏強度(Kg/mm2) --
--
伸長率(%)
10
16
械 剪切強率(Kg/mm2) 21.8
铸
模 均匀﹐保证足够强度与刚度的前提)
设
计
2020/8/16
Macherchen
压铸知识培训完整版doc

压铸知识培训完整版doc标题:压铸知识培训完整版一、引言压铸作为一种重要的金属成型工艺,被广泛应用于汽车、摩托车、家电、通讯、航空航天等行业。
为了提高员工的专业技能和综合素质,使企业更好地适应市场需求,我们特举办本次压铸知识培训。
本文档将详细阐述压铸工艺的基本原理、设备、模具、原材料、工艺参数以及常见问题及解决方法等内容,旨在帮助员工全面了解压铸知识,提高实际操作能力。
二、压铸工艺基本原理1. 压铸定义:压铸是一种利用高压将熔融金属迅速注入模具型腔,并在压力作用下凝固成型的金属成型方法。
3. 压铸特点:压铸具有生产效率高、成型精度高、力学性能好、表面质量好、材料利用率高等优点。
三、压铸设备1. 压铸机:压铸机是压铸生产中的关键设备,主要由合模机构、注射机构、液压系统、电气控制系统等组成。
2. 辅助设备:辅助设备包括熔化炉、保温炉、输送系统、模具冷却系统、喷涂料装置等。
四、压铸模具1. 模具结构:压铸模具主要由动模、定模、型腔、浇注系统、冷却系统、顶出系统等组成。
2. 模具材料:模具材料应具备良好的导热性、耐磨性、抗热疲劳性、抗腐蚀性等性能。
3. 模具设计要点:模具设计应考虑产品结构、分型面、浇注系统、冷却系统、顶出系统等因素。
五、压铸原材料1. 常用压铸材料:压铸材料主要包括铝合金、锌合金、镁合金、铜合金等。
2. 材料选择原则:根据产品性能要求、生产成本、工艺特点等因素选择合适的压铸材料。
六、压铸工艺参数1. 压力:压力是压铸过程中的关键参数,包括合模力、注射力、保压力等。
2. 温度:温度控制对压铸产品质量具有重要影响,包括熔融金属温度、模具温度等。
3. 时间:时间参数包括填充时间、保压时间、冷却时间等。
七、压铸常见问题及解决方法1. 缩孔:增加浇注系统截面积、提高模具温度、降低注射速度等方法。
2. 气孔:优化模具设计、提高熔融金属温度、增加注射压力等方法。
3. 疲劳裂纹:选用高强度模具材料、提高模具表面质量、控制模具温度等方法。
压铸操作工艺培训讲义(连载一)

压铸操作工艺培训讲义(连载一)一、概述压力铸造是近代金属加工工艺中发展较快的一种少无切削的特种铸造方法。
它是将熔融金属在高压高速下充填铸型,并在高压下结晶凝固形成铸件的过程。
高压高速是压力铸造的主要特征。
常用的压力为数十兆帕,填充速度(内浇口速度)约为16~80米/秒,金属液填充模具型腔的时间极短,约为0.01~0.2秒。
由于用这种方法生产产品具有生产效率高,工序简单,铸件公差等级较高,表面粗糙度好,机械强度大,可以省去大量的机械加工工序和设备,节约原材料等优点,所以现已成为我国铸造业中的一个重要组成部分。
二、压铸过程中的主要参数在压力铸造的整个过程中,压力起到了主导作用。
熔融金属不仅在压力作用下充满压室进入浇注系统,而填充又在压力作用下凝固成型。
在压射过程中各个阶段,随着冲头位置的移动,压力也出现不同的变化,这个变化规律都会对铸件质量产生重大影响。
因此我们应对压铸过程中压力的作用与变化要有一个感性认识,这也是压铸技术的理论基础。
三、压铸工艺压铸工艺是将压铸机、压铸模和合金三大要素有机地组合而加以综合运用的过程。
而压铸时金属按填充型腔的过程,是将压力、速度、温度以及时间等工艺因素得到统一的过程。
同时,这些工艺因素又相互影响,相互制约,并且相辅相成。
只有正确选择和调整这些因素,使之协调一致,才能获得预期的结果。
因此,在压铸过程中不仅要重视铸件结构的工艺性,压铸模的先进性,压铸机性能和结构优良性,压铸合金选用的适应性和熔炼工艺的规范性;更应重视压力、温度和时间等工艺参数对铸件质量的重要作用。
在压铸过程中应重视对这些参数进行有效的控制。
(一)压力压力的存在是压铸工艺区别其他铸造方法的主要特点。
1. 压射力压射力是压铸机压射机构中推动压射活塞运动的力。
它是反映压铸机功能的一个主要参数。
压射力的大小,由压射缸的截面积和工作液的压力所决定。
2. 铸造压力(增压比压)压室内熔融金属在单位面积上所受的压力称为比压。
压铸过程原理及压铸工艺技术培训
压铸过程原理及压铸工艺技术培训压铸是一种常见的金属加工工艺,广泛用于制造各种金属制品,如汽车零部件、电子设备外壳等。
本文将介绍压铸的原理及压铸工艺技术培训。
压铸的原理是通过将熔化的金属注入到金属模具中,然后在高压下快速冷却凝固,最后开模取出成品。
它主要包含以下几个步骤:1. 选择合适的金属材料:压铸常用的材料包括铝合金、镁合金、锌合金等。
不同材料的选择要考虑产品的用途、性能需求等因素。
2. 设计和制造模具:模具是压铸的关键。
它需要根据产品的形状和尺寸要求进行设计和制造。
模具通常由两个主要部分组成:注射系统和冷却系统。
3. 预处理金属材料:在熔化之前,金属材料需要经过一系列的处理,包括去除杂质、调整成分等。
这些步骤可以提高产品的质量和性能。
4. 熔炼金属材料:选择合适的炉子将固态的金属材料加热到熔点以上,使其变为流动的液态金属。
5. 铸造金属材料:将熔化的金属材料注入到预先准备好的金属模具中,然后通过高压使其充满整个模具腔体。
高压保证了产品的密实度和准确度。
6. 冷却和取出成品:在模具中的金属材料迅速冷却凝固,形成成品。
然后打开模具,取出成品,进行后续的处理和加工。
为了保证压铸的质量和效率,需要掌握一些压铸工艺技术:1. 模具设计和制造:模具的设计和制造应根据产品的形状和尺寸进行调整,以提高产品的质量和效率。
2. 温度控制:金属材料的熔炼和冷却过程都需要进行温度控制,以保证产品的性能和尺寸。
3. 压力控制:压力的大小会影响产品的密实度和形状,需要根据具体情况进行合理的控制。
4. 金属处理:金属材料的预处理是保证产品质量的重要环节,需要注意去除杂质和调整成分。
5. 质量控制:通过对成品进行检测和测试,及时发现和解决生产中出现的问题,提高产品的质量。
通过对压铸过程原理及压铸工艺技术的培训,可以提高职工的技术水平和工作效率,进一步提高产品的质量和竞争力。
压铸工艺技术的培训可以通过理论学习、实践操作和案例分析等多种方式进行,以帮助职工全面了解和掌握压铸的工艺要点和技术要求。
铝合金铸造基础知识课堂PPT
冷芯制芯
冷芯制芯:
将树脂砂填入冷芯模,而后吹气硬化制成坭芯。 根据使用的粘结剂和所吹气体及其作用的不同,而 有三乙胺法、SO2法、酯硬化法、低毒和无毒气体 促硬制芯法。
三乙胺法:一般用干燥的压缩空气或氮气作液态硬 化剂(三乙胺)的载体气体,稀释到约5%浓度,形 成三乙胺气雾,向冷芯模中填入树脂砂后再吹入三 乙胺气雾,树脂砂便能在数秒至数十秒内硬化制成 所需要强度的坭芯。
36
壳芯制芯
壳芯:进排气道
37
壳芯制芯
壳芯制芯的优点: ➢混制好的覆膜砂可以较长期贮存(三个月以上); ➢能获得尺寸精确的坭芯; ➢坭芯的强度高、质量轻、易搬运; ➢可用细的原砂得到光洁的铸件表面; ➢覆膜砂消耗量小。
38
壳芯制芯
壳芯制芯的缺点: (一)壳芯表面易疏松 覆膜砂流动性差; 排气不当,在深凹处疏松和缺肉的,多是排气不好; 射砂压力太低; 射砂时间太短; 覆膜砂所使用的原砂太粗。
42
冷芯制芯
冷芯:冒口芯
43
冷芯制芯
冷芯制芯的冷芯树脂(粘结剂)由两部分组成,组 分Ⅰ是酚醛树脂,组分Ⅱ是聚异氰酸酯。
硬化反应:
酚醛树脂+聚异氰酸酯 三乙胺 尿烷
采用三乙胺法制芯时,原砂采用干净的AFS的细度 50-60的硅砂。
原砂必须干燥,水分超过0.1%(质量分数)就会减 少树脂砂的可使用时间,降低坭芯的抗拉强度,也 会增加铸件针孔缺陷。
第三章 铝液的熔化 及精炼处理
47
熔炼炉的操作
➢第一节 熔炼炉的简介 ➢第二节 铝合金熔炼理论知识
48
熔炼炉的简介 熔炼炉的分类:
熔炼炉
火焰炉
感应炉
电阻炉
49
熔炼炉的简介
铝合金铸造基础知识
2、变质机理 变质是通过一定手段的采用,使铝-硅共晶合金的铝硅共晶中的硅晶体 组织的细化。从而提高溶液的铸造性。共晶组织中硅晶体呈粗针状或片状,过共
晶合金中还有少量初生硅,呈块状--塑性较低,不实用,需要细化组织;一般需
要采用变质处理,以改变共晶硅的形态,使硅晶体细化和颗粒化。
ZL102变质前:σb =140MPaδ= 3% 后: σs= 180MPa δ= 8%
2、常用铸造铝合金的热处理工艺特点
热处理主要由固溶处理和时效强化两部分组成:
⑴、固溶强化:纯铝中加入合金元素,形成铝基固溶体,造成晶格畸变,阻碍 了位错的运动,起到固溶强化的作用,可使用其强度提高。 一般固溶处理加热温度 应尽可能选高一些,是合金元素充分溶入α固溶体中并加快溶解速度。但同时要考 虑此系合金的α+Si+Mg2Si三相共晶温度为555℃。故温度不宜过高。当加热温度超 过此共晶温度时,就会发生“过烧”,也就是在合金组织中局部低熔点共晶处发生 熔化。严重过烧时,局部熔体挤出铸件表面形成黑色小珠。 ⑵、时效强化:在α-AL中过饱和的溶质最终将会析出,但是这一过程在室温进
⑵、工艺文件的更改 :工艺文件一经批准发布,即有法律效力,应保 持相对稳定,不宜经常变动,但遇到产品结构的材料,设备和工装等有变 更时,应对生产工艺进行相应的变更,工艺文件进行修改。更改时应由技 术部工艺员进行修改,做出标记,签名要注明更改日期。 ⑶、工艺文件的保管和发放应符企业文件、资料、档案管理制度。 ⑷工艺文件作用: ①、组织生产,建立生产秩序; ②、指导技术,保证产品质量; ③、编制生产计划,考核工时定额; ④、调整劳动组织; ⑤、安排物资供应; ⑥、工具、工装、模具管理; ⑦、经济核算的依据; ⑧、巩固工艺纪律。
铝合金铸造 基础知识培训
《压铸工艺技术培训》PPT课件
h
2
压铸基本原理
h
3
压铸材料
压铸所用材料多为有色合金,如铝合金、锌合金、镁合金、铜合金,因我公司都
是铝合金,所以介绍压铸铝合金的材料。
牌号
Si
Fe
Cu
Mn
Mg
Ni
Zn
其他杂质总
和
Tin
Ti
A380
7.5-9.5 0.8max 3.0-4.0 0.5max 0.1max 0.5max 3.0max 0.35 max /
h
C
椭圆中心详见局部视图 椭圆 2 (长轴 22mm,短轴 21.4mm) 椭圆 1 (长轴 15.6 mm,短轴 14.6mm)
16
压铸件设计
九、压铸件设计中的嵌入嵌件设计 压铸件中能铸入金属或非金属嵌件,主要为了提高局部的强度耐磨性或形成难以
成型的内腔,嵌件埋入金属的部分要设计防转和防止轴向移动的形状同时要考虑嵌件 放入模具的方便性和承受金属液冲击的稳定性
0.5 max
383
9.5-11.5 0.8max 2.0-3.0 0.5max 0.1max 0.3max 3.0max 0.15 max /
0.5 max
ADC10
7.5-9.5
0.8ma x
2.0-4.0
0.5max 0.3max 0.5max 1.0max
0.2max 余量
ADC12
9.6-12.0
压铸件常见缺陷
铸件表面上 呈现的光滑条纹, 肉眼可见,但用 手感觉不出,颜 色不同于基体金 属的纹路.
10外观和使用功能即使有特殊的要求需要机械加工也应合理控制加工余量减少加工时间和暴漏气孔的机会一般加工余量都控制在08以下为了尽量减少机械加工一就要求合理制订图纸的公差能保证零件的安装即可不适当的公差范围就会增加后续的机械加工二是合理设计减少零件的收缩变形三是有角度的安装孔可以考虑对接异形孔压铸件设计九压铸件设计中的嵌入嵌件设计压铸件中能铸入金属或非金属嵌件主要为了提高局部的强度耐磨性或形成难以成型的内腔嵌件埋入金属的部分要设计防转和防止轴向移动的形状同时要考虑嵌件放入模具的方便性和承受金属液冲击的稳定性压铸件常见缺陷压铸件常见缺陷压铸件常见缺陷压铸件常见缺陷谢谢大家
- 1、下载文档前请自行甄别文档内容的完整性,平台不提供额外的编辑、内容补充、找答案等附加服务。
- 2、"仅部分预览"的文档,不可在线预览部分如存在完整性等问题,可反馈申请退款(可完整预览的文档不适用该条件!)。
- 3、如文档侵犯您的权益,请联系客服反馈,我们会尽快为您处理(人工客服工作时间:9:00-18:30)。
二、压铸过程主要工艺参数
杭
州
顶
正 包
3. 2 压射速度
材
➢ 压射速度又分为两级,一级压射速度亦称慢压射速度, 这级速度是指冲头起始动作直至冲头将室内的金属液送 入内浇口之前的运动速度,在这一阶段中要求将压室中 的金属液充满压室,在既不过多地降低合金液温度又有 利于排除压室中的气体的原则下。
正
➢包材 压铸工艺是将压铸机、压铸模、和压铸合金三大要素有 机的组合而加 以综合运用的过程。
➢ 压铸时金属按填充型腔的过程,是将压力、速度、温度 以及时间等工艺因素得到动态平衡的过程。
➢ 这些工艺因素既相互制约,且相辅相成,只有正确选择 和调整这些因素,使之协调一致,才能获得预期的结果
➢ 压铸过程中,不仅重视铸件结构的工艺性,铸型的先进 性,压铸机性能和结构优良性,压铸合金选用的适应性 和熔炼工艺的规范性。更应重视压力、速度、和时间等 工艺参数对铸件质量的重要作用。
➢ 比压对铸件机械性能的影响 :比压增大,结晶细,细 晶层增厚,由于填充特性改善,表面质量提高,气孔影 响减轻,从而抗拉强度提高。
➢ 对填充条件的影响:合金熔液在高比压下填充型腔,合 金温度升高,流动性改善,有利于铸件质量的提高。
二、压铸过程主要工艺参数
杭
州 顶
3. 速度
正 ➢ 压铸过程中,压射速度受压力的直接影响,又与压力共
速度
➢ 通常采用的内浇口速度范围为15-70米/秒。
➢ 内浇口速度高低与铸件机械性能的影响极大,内浇口速 度太低,铸件强度下降;速度提高,强度上升;速度过 高,强度又下降
二、压铸过程主要工艺参数
➢ 将填充时的比压称为填充比压又称压射比压。增压阶 段的比压称为增压比压这两个比压的大小同样都是根
据压射力来确定的
二、压铸过程主要工艺参数
杭
州 顶
2. 3 压力的作用和影响
正
包 ➢ 填充比压是克服浇注系统和型腔中的流动阻力,特别是
材 内浇口处的阻力,使金属液流保证达到需要的内浇口速
度。
➢ 增压比压则是决定了正在凝固的金属所受到的压力以及 这时所形成的胀型力的大小
压铸机选择
州
顶 2. 计算胀型力
正
包 材
F= A×P/10
式中— F: 胀型力(KN,注:1T=10KN)
A: 铸件在分型面上的投影面积,多腔模
则为各腔投影面积之和,一般另加
30%作为浇注系统和溢流排气系统的
面积(cm2)。
P: 比压( MP a )
二、压铸过程主要工艺参数
杭 州
顶 1.压铸工艺简介
F压=P液XA缸
二、压铸过程主要工艺参数
杭
州 顶
2. 2 比压
正
包➢ 压室内熔融金属在单位面积上所受的压力称为比压。比
材 压是压射力与压室截面积的比值其计算公式如下:
P比=P射/A室
➢ 比压是熔融金属在填充过程中各阶段实际得到的作用力 的大小的表示方法,反映了熔融金属在填充的各个阶段 以及金属流经各个不同截面积时的力的概念。
铸型,并在高压下结晶凝固形成铸件的过程。
高压高速是高压铸造的主要特征。常用的压力为数十 兆帕,填充速度(内浇口速度)约为16~80米/秒,金属 液填充模具型腔的时间极短,约为0.01~0.2秒。
由于用这种方法生产产品具有生产效率高,工序简单 ,铸件公差等级较高,表面粗糙度好,机械强度大,可以 省去大量的机械加工工序和设备,节约原材料等优点,所 以现已成为铸造业中的一个重要组成部分
但速度过快时,合金熔液呈雾状和气体混合,产生严重裹
包气,机械性能下降。
铝合金
抗 拉 强 度
压射锤头速度
二快压射正确,慢压射将压室内空气排净,使合金液 二、压铸过程主至要内工浇艺口参处数
杭 州 顶 正 包 材
二快压射起点正确
二、压铸过程主要工艺参数
杭
州
顶 正
3. 4 内浇口速度
包
材 ➢ 熔融金属进Βιβλιοθήκη 内浇口导入型腔时的线速度,称为内浇口
杭 州 顶 正 包
材 铝合金高压铸造工艺基础知识培训
杭
州
顶
正 包
目
录
材
一、压铸概述
二、压铸过程主要工艺参数
三、压铸件设计
四、压铸件常见缺陷产生原因及解决方法
五、压铸件质量问题解决案例
杭
州 顶
高压铸造概述
正
包 材
高压铸造是近代金属加工工艺中发展较快的一种少无
切削的特种铸造方法。它是将熔融金属在高压高速下充填
杭
州 顶
压铸循环生产过程:
正
包
材
合模
金属液浇入压室
压射
喷水、吹气
铸件出模
开模
压铸过程
杭 州 顶 正 包 材
压铸过程
杭 州 顶 正 包 材
压铸过程
杭 州 顶 正 包 材
压铸过程
杭 州 顶 正 包 材
压铸过程
杭 州 顶 正 包 材
压铸过程
杭 州 顶 正 包 材
压铸过程
杭 州 顶 正 包 材
包 材
同对铸件内部质量,表面要求和轮廓清晰程度起着重要
的作用。压力是速度的基础
➢ 速度的表示形式分为冲头速度和内浇口速度两种。
3. 1 冲头速度与内交口速度的关系
➢ 根据连续性原理,在同一时间内金属流以速度V1流过 压室截面积为F1的合金液体积,应等于以速度V2流过 内浇口截面积为F2的合金液体积
F1室V1射=F2内V2内
二、压铸过程主要工艺参数
杭
州
顶 正
2. 压力
包➢ 压力的存在是压铸工艺区别于其他铸造方法的主要特点
材 。压力是使铸件获得组织致密和轮廓清晰的因素
➢ 压力的表示形式有压射力和比压两种。
2. 1 压射力
➢ 压射力是压铸机压射机构中推动压射活塞运动的力。压 射力是反映压铸机功能的一个主要参数。
➢ 压射力的大小是由压射缸的截面积和压射腔内工作液 的压力所决定。压射力的公式如下:
➢ 二级压射速度又称 快压射速度,这个速度由压铸机的 特性所决定,压铸机所给定的最高压射速度一般在4-5 米/秒范围内 。
二、压铸过程主要工艺参数
杭
州
顶 正
3. 3 快压射速度的作用和影响
包 材
快压射速度对合金机械性能的作用和影响,提高压射
速度,动能转化为热能,提高了合金熔液的流动性,有利
于消除流痕,冷隔等缺陷,提高了机械性能和表面质量,
压铸机选择
杭
州
顶 正
1. 确定比压
包
材
比压推荐值( MPa )
一般件
承载件 耐气密性件或 大平面薄壁件
电镀件
锌合金 13~20 20~30 25~40 20~30
铝合金 30~50 50~80 80~120
镁合金 30~50 50~80 80~100
铜合金 40~50 50~80 60~100
杭