Aerospace Materials
高温合金AMS-5663M-N07718
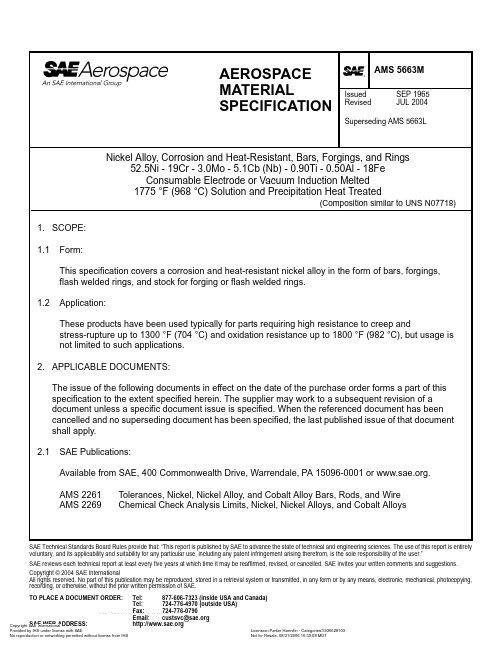
SAE Technical Standards Board Rules provide that: “This report is published by SAE to advance the state of technical and engineering sciences. The use of this report is entirely voluntary, and its applicability and suitability for any particular use, including any patent infringement arising therefrom, is the sole responsibility of the user.”SAE reviews each technical report at least every five years at which time it may be reaffirmed, revised, or cancelled. SAE invites your written comments and suggestions.Copyright © 2004 SAE InternationalAll rights reserved. No part of this publication may be reproduced, stored in a retrieval system or transmitted, in any form or by any means, electronic, mechanical, photocopying,recording, or otherwise, without the prior written permission of SAE.TO PLACE A DOCUMENT ORDER:Tel: 877-606-7323 (inside USA and Canada)T el: 724-776-4970 (outside USA)Nickel Alloy, Corrosion and Heat-Resistant, Bars, Forgings, and Rings52.5Ni - 19Cr - 3.0Mo - 5.1Cb (Nb) - 0.90Ti - 0.50Al - 18FeConsumable Electrode or Vacuum Induction Melted 1775 °F (968 °C) Solution and Precipitation Heat Treated(Composition similar to UNS N07718)1.SCOPE:1.1Form:This specification covers a corrosion and heat-resistant nickel alloy in the form of bars, forgings, flash welded rings, and stock for forging or flash welded rings.1.2Application:These products have been used typically for parts requiring high resistance to creep andstress-rupture up to 1300 °F (704 °C) and oxidation resistance up to 1800 °F (982 °C), but usage is not limited to such applications.2.APPLICABLE DOCUMENTS:The issue of the following documents in effect on the date of the purchase order forms a part of this specification to the extent specified herein. The supplier may work to a subsequent revision of a document unless a specific document issue is specified. When the referenced document has been cancelled and no superseding document has been specified, the last published issue of that document shall apply.2.1 SAE Publications:Available from SAE, 400 Commonwealth Drive, Warrendale, PA 15096-0001 or .AMS 2261Tolerances, Nickel, Nickel Alloy, and Cobalt Alloy Bars, Rods, and Wire AMS 2269Chemical Check Analysis Limits, Nickel, Nickel Alloys, and Cobalt AlloysAEROSPACE MATERIALSPECIFICATIONAMS 5663MIssued SEP 1965RevisedJUL 2004Superseding AMS 5663L2.1 (Continued):AMS 2371 Quality Assurance Sampling and Testing, Corrosion and Heat-Resistant Steels and Alloys, Wrought Products and Forging StockAMS 2374 Quality Assurance Sampling and Testing, Corrosion and Heat-Resistant Steel and Alloy ForgingsAMS 2750 PyrometryAMS 2806Identification, Bars, Wire, Mechanical Tubing, and Extrusions, Carbon and Alloy Steels and Corrosion and Heat-Resistant Steels and AlloysAMS 2808Identification, ForgingsAMS 7490Rings, Flash Welded, Corrosion and Heat-Resistant Austenitic Steels,Austenitic-Type Iron, Nickel, or Cobalt Alloys or Precipitation-Hardenable Alloys ARP1313 Determination of Trace Elements in High-Temperature Alloys2.2 ASTM Publications:Available from ASTM, 100 Barr Harbor Drive, P.O. Box C700, West Conshohocken, PA 19428-2959 or .ASTM E 8 Tension Testing of Metallic MaterialsASTM E 8M Tension Testing of Metallic Materials (Metric)ASTM E 10 Brinell Hardness of Metallic MaterialsASTM E 21 Elevated Temperature Tension Tests of Metallic MaterialsASTM E 103Rapid Indentation Hardness Testing of Metallic MaterialsASTM E 112Determining Average Grain SizeASTM E 139Conducting Creep, Creep-Rupture, and Stress-Rupture Tests of Metallic Materials ASTM E 292Conducting Time-for-Rupture Notch Tension Tests of MaterialsASTM E 354Chemical Analysis of High-Temperature, Electrical, Magnetic, and Other Similar Iron, Nickel, and Cobalt Alloys3.TECHNICAL REQUIREMENTS:3.1Composition:Shall conform to the percentages by weight shown in Table 1, determined by wet chemical methods in accordance with ASTM E 354, by spectrochemical methods, by the methods of ARP1313 for lead, bismuth, and selenium, or by other analytical methods acceptable to purchaser.3.1.1Determination not required for routine analysis.3.1.2Check Analysis: Composition variations shall meet the applicable requirements of AMS 2269.3.2Melting Practice:Alloy shall be multiple melted using consumable electrode practice in the remelt cycle or shall be induction melted under vacuum. If consumable electrode remelting is not performed in vacuum, electrodes which have been produced by vacuum induction melting shall be used for remelting.3.3Condition:The product shall be supplied in the following condition.3.3.1Bars: Hot or cold finished, solution and precipitation heat treated, and descaled except as specified in 3.3.1.1 and 3.3.1.2.TABLE 1 - CompositionElementmin maxCarbon -- 0.08Manganese -- 0.35Silicon-- 0.35Phosphorus -- 0.015Sulfur-- 0.015Chromium 17.0021.00Nickel50.0055.00Molybdenum2.803.30Columbium (Niobium)4.755.50Titanium 0.65 1.15Aluminum 0.200.80Cobalt-- 1.00Tantalum (3.1.1)-- 0.05Boron -- 0.006Copper -- 0.30Lead -- 0.0005 (5 ppm)Bismuth -- 0.00003 (0.3 ppm)Selenium -- 0.0003 (3 ppm)Ironremainder--`,,,```,,,,,`,,`,`,,`,,````-`-`,,`,,`,`,,`---3.3.1.1Hot finished round bars shall be ground or turned; all other hot finished bars shall be as hotfinished.3.3.1.2Cold finished round bars shall be ground or as cold finished; all other cold finished bars shall beas cold finished.3.3.2Forgings and Flash Welded Rings: Solution and precipitation heat treated and descaled.3.3.2.1Flash welded rings shall not be supplied unless specified or permitted on purchaser's partdrawing. When supplied, rings shall be manufactured in accordance with AMS 7490.3.3.3Stock for Forging or Flash Welded Rings: As ordered by the forging or flash welded ringmanufacturer.3.4Heat Treatment:Bars, forgings, and flash welded rings shall be solution and precipitation heat treated in accordance with 3.4.1 and 3.4.2; pyrometry shall be in accordance with AMS 2750.3.4.1Solution Heat Treatment: Heat to a temperature within the range 1725 to 1850 °F (941 to 1010 °C),hold at the selected temperature within ±25 °F (±14 °C) for a time commensurate withcross-sectional thickness, and cool at a rate equivalent to an air cool or faster.3.4.1.1If forgings are not to be machined all over, heat treatment shall be performed in a suitableprotective atmosphere or, when permitted by purchaser, a suitable protective coating may beapplied to the forgings in lieu of using a protective atmosphere.3.4.2Precipitation Heat Treatment: Heat to a temperature within the range 1325 to 1400 °F(718 to 760 °C), hold at the selected temperature within ±15 °F (±8 °C) for approximately 8 hours, cool at 100 °F ± 15 (56 °C ± 8) degrees per hour to a temperature within the range 1150 to 1200 °F (621 to 649 °C), hold at the selected temperature within ±15 °F (±8 °C) for approximately 8 hours, and air cool. Instead of the 100 °F (56 °C) degrees per hour cooling rate to 1150 to 1200 °F(621 to 649 °C), the product may be furnace cooled at any rate provided the time at1150 to 1200 °F (621 to 649 °C) is adjusted to give a total precipitation heat treatment time ofapproximately 18 hours.3.5Properties:The product shall conform to the following requirements:3.5.1Bars, Forgings, and Flash Welded Rings:3.5.1.1Average Grain Size: Shall be as follows, determined in accordance with ASTM E 112. In case ofdisagreement, the intercept (Heyn) procedure shall be used.--` , , , ` ` ` , , , , , ` , , ` , ` , , ` , , ` ` ` ` -` -` , , ` , , ` , ` , , ` ---3.5.1.1.1Bars and flash welded rings under 9 square inches (58 cm2) in cross-sectional area shallexhibit an average grain size of ASTM No. 5 or finer. Due to the presence of nonrecrystallizedgrains, up to 20% of the cross section of the product may have an average grain size of ASTMNo. 3 to 5, determined by the intercept method of ASTM E 112.3.5.1.1.2Bars and flash welded rings 9 to 50 square inches (58 to 323 cm2), inclusive, in cross-sectionalarea and all forgings shall exhibit an average grain size of ASTM No. 4 or finer. Due to thepresence of nonrecrystallized grains, up to 20% of the cross section of the product may havean average grain size of ASTM No. 2 to 4, determined by the intercept method of ASTM E 112.3.5.1.2Microstructure: Product shall be free of Laves phase. Banding of acicular phase and amount ofacicular phase shall conform to standards acceptable to purchaser.3.5.1.3Tensile Properties: Product, 5.0 inches (127 mm) and under in least nominal cross-sectionaldimension, shall have the following properties:3.5.1.3.1At Room Temperature: Shall be as shown in Table 2, determined in accordance withASTM E 8 or ASTM E 8M.TABLE 2A - Minimum Room Temperature Tensile Properties, Inch/Pound UnitsSpecimen OrientationTensileStrengthksiYield Strengthat 0.2% OffsetksiElongationin 4D%Reduction ofArea%Longitudinal1851501215 Long-Transverse(Forgings)1801501012Transverse(Bars)180150 6 8 TABLE 2B - Minimum Room Temperature Tensile Properties, SI UnitsSpecimen OrientationTensileStrengthMPaYield Strengthat 0.2% OffsetMPaElongationin 4D%Reduction ofArea%Longitudinal127610341215 Long-Transverse(Forgings)124110341012Transverse(Bars)12411034 6 83.5.1.3.2At 1200 °F (649 °C): Shall be as shown in Table 3, determined in accordance withASTM E 21 on specimens heated to 1200 °F ± 5 (649 °C ± 3), held at heat for not less than 20 minutes before testing, and tested at 1200 °F ± 5 (649 °C ± 3).3.5.1.3.3Longitudinal requirements of 3.5.1.3.1 and 3.5.1.3.2 apply to specimens taken with the axis approximately parallel to the grain flow, to specimens taken in the radial direction and in the tangential direction at the rim of disc forgings, and to specimens taken in the circumferential direction from flash welded rings. All other specimens shall be considered to be in the transverse direction.3.5.1.3.4Transverse tensile properties apply only to product from which a test specimen not less than 2.50 inches (63.5 mm) long can be taken.3.5.1.3.5Specific locations of specimens from forgings and flash welded rings shall be as agreed upon by purchaser and vendor.TABLE 3A - Minimum Tensile Properties at 1200 °F, Inch/Pound Units Specimen Orientation Tensile Strength ksi Yield Strength at 0.2% OffsetksiElongation in 4D %Reduction ofArea %Longitudinal 1451251215Long-Transverse (Forgings)1401251012Transverse (Bars)140125 6 8TABLE 3B - Minimum Tensile Properties at 649 °C, SI UnitsSpecimen Orientation Tensile Strength MPa Yield Strength at 0.2% OffsetMPaElongation in 4D %Reduction ofArea %Longitudinal 10008621215Long-Transverse (Forgings)9658621012Transverse (Bars)965862 6 8--`,,,```,,,,,`,,`,`,,`,,````-`-`,,`,,`,`,,`---3.5.1.4Hardness: Shall be not lower than 331 HB, or equivalent (See 8.2), determined in accordancewith ASTM E 10 or ASTM E 103. Product shall not be rejected on the basis of hardness if thetensile property requirements of 3.5.1.3.1 are acceptable, determined on specimens taken from the same sample as that with nonconforming hardness or from another sample with similarnonconforming hardness.3.5.1.5Stress-Rupture Properties at 1200 °F (649 °C): Shall be as follows; testing of notched specimensand of combination smooth-and-notched specimens shall be performed in accordance withASTM E 292 and of smooth specimens in accordance with ASTM E 139:3.5.1.5.1 A standard cylindrical combination smooth-and-notched specimen conforming to ASTM E 292,maintained at 1200 °F ± 3 (649 °C ± 2) while a load sufficient to produce an initial axial stress of100 ksi (689 MPa) or higher is applied continuously, shall not rupture in less than 23 hours. Thetest shall be continued to rupture without change of load. Rupture shall occur in the smoothsection and elongation of this section after rupture, measured at room temperature, shall be notless than 4% in 4D for product 5.0 inches (127 mm) and under in nominal diameter or leastdistance between parallel sides.3.5.1.5.2As an alternate procedure, separate smooth and notched specimens, machined from adjacentsections of the same piece, with gage sections conforming to the respective dimensions shownin ASTM E 292 may be tested individually under the conditions of 3.5.1.5.1. The smoothspecimen shall not rupture in less than 23 hours and elongation after rupture, measured atroom temperature, shall be as specified in 3.5.1.5.1. The notched specimen shall not rupture inless time than the companion smooth specimen but need not be tested to rupture.3.5.1.5.3The tests of 3.5.1.5.1 and 3.5.1.5.2 may be conducted using incremental loading. In such case,the load required to produce an initial axial stress of 100 ksi (689 MPa) or higher shall be usedto rupture or for 23 hours, whichever occurs first. After the 23 hours and at intervals of8 hours minimum, thereafter, the stress shall be increased in increments of 5.0 ksi (34.5 MPa).Time to rupture, rupture location, and elongation requirements shall be as specified in3.5.1.5.1.3.5.2Forging Stock: When a sample of stock is forged to a test coupon and solution and precipitationheat treated as in 3.4, specimens taken from the heat treated coupon shall conform to therequirements of 3.5.1.1, 3.5.1.2, 3.5.1.3, 3.5.1.4, and 3.5.1.5. If specimens taken from the stock after solution and precipitation heat treatment as in 3.4 conform to the requirements of 3.5.1.1,3.5.1.2, 3.5.1.3, 3.5.1.4, and 3.5.1.5, the tests shall be accepted as equivalent to tests of a forgedcoupon.3.5.3Stock for Flash Welded Rings: Specimens taken from the stock after heat treatment as in 3.4 shallconform to the requirements of 3.5.1.1, 3.5.1.2, 3.5.1.3, 3.5.1.4, and 3.5.1.5.3.6Quality:The product, as received by purchaser, shall be uniform in quality and condition, sound, and free from foreign materials and from imperfections detrimental to usage of the product.--` , , , ` ` ` , , , , , ` , , ` , ` , , ` , , ` ` ` ` -` -` , , ` , , ` , ` , , ` ---3.6.1Grain flow of die forgings, except in areas which contain flash-line end grain, shall follow thegeneral contour of the forging showing no evidence of reentrant grain flow.3.7Tolerances:Bars shall conform to all applicable requirements of AMS 2261.4.QUALITY ASSURANCE PROVISIONS:4.1Responsibility for Inspection:The vendor of the product shall supply all samples for vendor's tests and shall be responsible for the performance of all required tests. Purchaser reserves the right to sample and to perform anyconfirmatory testing deemed necessary to ensure that the product conforms to specifiedrequirements.4.2Classification of Tests:4.2.1Acceptance Tests: The following requirements are acceptance tests and shall be performed oneach heat or lot as applicable:4.2.1.1Composition (3.1) of each heat.4.2.1.2Average grain size (3.5.1.1), tensile properties (3.5.1.3), hardness (3.5.1.4), and stress-ruptureproperties (3.5.1.5) of each lot of bars, forgings, and flash welded rings.4.2.1.3Microstructure (3.5.1.2) of each lot.4.2.1.4Tolerances (3.7) of bars.4.2.2Periodic Tests: Tests of forging stock (3.5.2) and of stock for flash welded rings (3.5.3) to --`,,,```,,,,,`,,`,`,,`,,````-`-`,,`,,`,`,,`---demonstrate ability to develop required properties and of grain flow of die forgings (3.6.1) areperiodic tests and shall be performed at a frequency selected by the vendor unless frequency of testing is specified by purchaser.4.3Sampling and Testing:Shall be as follows:4.3.1Bars, Flash Welded Rings, and Stock for Forging or Flash Welded Rings: In accordance withAMS 2371.4.3.2Forgings: In accordance with AMS 2374.4.4Reports:4.4.1The vendor of bars, forgings, and flash welded rings shall furnish with each shipment a reportshowing the results of tests and relevant information:4.4.1.1For each heat:Composition4.4.1.2For each lot:Average grain sizeMicrostructure resultsRoom temperature tensile properties1200 °F (649 °C) tensile propertiesHardnessStress-rupture properties.4.4.1.3 A statement that the product conforms to the other technical requirements.4.4.1.4Purchase order numberHeat and lot numbersAMS 5663MSizeQuantity.4.4.1.5If forgings are supplied, the size and melt source of stock used to make the forgings.4.4.2The vendor of stock for forging or flash welded rings shall furnish with each shipment a reportshowing the results of tests for the composition of each heat. This report shall include the purchase order number, heat and lot number, AMS 5663M, size, and quantity.4.5Resampling and Retesting:Shall be as follows:4.5.1Bars, Flash Welded Rings, and Stock for Forging or Flash Welded Rings: In accordance withAMS 2371.4.5.2Forgings: In accordance with AMS 2374.5.PREPARATION FOR DELIVERY:5.1Sizes:Except when exact lengths or multiples of exact lengths are ordered, straight bars will be acceptable in mill lengths of 6 to 24 feet (1.8 to 7.3 m) but not more than 25% of any shipment shall be supplied in lengths of 6 to 9 feet (1.8 to 2.7 m) except that for bars weighing over 25 pounds per foot(37 kg/m), short lengths down to 2 feet (610 mm) may be supplied.5.2Identification:Shall be as follows:5.2.1Bars: In accordance with AMS 2806.5.2.2Forgings: In accordance with AMS 2808.5.2.3Flash Welded Rings and Stock for Forging or Flash Welded Rings: As agreed upon by purchaserand vendor.5.3Packaging:The product shall be prepared for shipment in accordance with commercial practice and incompliance with applicable rules and regulations pertaining to the handling, packaging, andtransportation of the product to ensure carrier acceptance and safe delivery.6.ACKNOWLEDGMENT:A vendor shall mention this specification number and its revision letter in all quotations and whenacknowledging purchase orders.7.REJECTIONS:Product not conforming to this specification, or to modifications authorized by purchaser, will be subject to rejection.8.NOTES:8.1 A change bar (|) located in the left margin is for the convenience of the user in locating areas wheretechnical revisions, not editorial changes, have been made to the previous issue of a specification.An (R) symbol to the left of the document title indicates a complete revision of the specification, including technical revisions. Change bars and (R) are not used in original publications, nor inspecifications that contain editorial changes only.8.2Hardness conversion tables for metals are presented in ASTM E 140.8.3Terms used in AMS are clarified in ARP1917.--` , , , ` ` ` , , , , , ` , , ` , ` , , ` , , ` ` ` ` -` -` , , ` , , ` , ` , , ` ---AMS 5663M SAE AMS 5663M- 11 -8.4Dimensions and properties in inch/pound units and the Fahrenheit temperatures are primary;dimensions and properties in SI units and the Celsius temperatures are shown as the approximate equivalents of the primary units and are presented only for information.8.5Purchase documents should specify not less than the following:AMS 5663MForm and size or part number of product desiredQuantity of product desiredIf applicable, specific location of tensile specimens from forgings and flash welded rings (See 3.5.1.3.5).8.6Key Words:UNS N07718, solution heat treated, precipitation heat treated, bars, forgings, rings, stress-rupture, grain size, microstructure, 1200 °F tensilePREPARED UNDER THE JURISDICTION OF AMS COMMITTEE “F”Copyright SAE InternationalProvided by IHS under license with SAELicensee=Parker Hannifin - Categories/5936628103 Not for Resale, 08/31/2006 16:59:08 MDT No reproduction or networking permitted without license from IHS --`,,,```,,,,,`,,`,`,,`,,````-`-`,,`,,`,`,,`---。
AMS A-8625
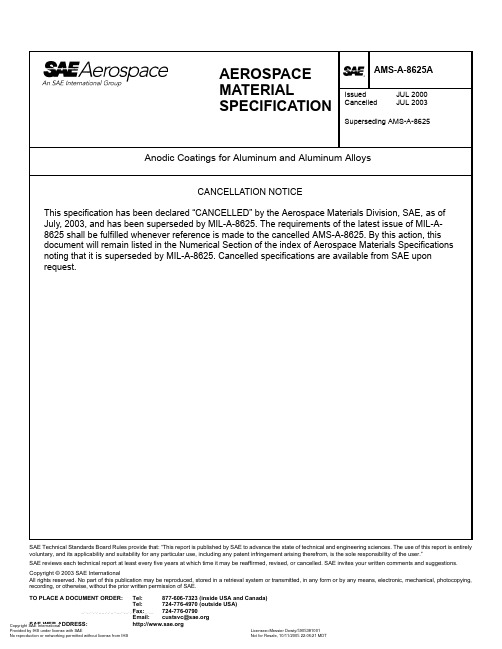
SAE Technical Standards Board Rules provide that: “This report is published by SAE to advance the state of technical and engineering sciences. The use of this report is entirely voluntary, and its applicability and suitability for any particular use, including any patent infringement arising therefrom, is the sole responsibility of the user.”SAE reviews each technical report at least every five years at which time it may be reaffirmed, revised, or cancelled. SAE invites your written comments and suggestions.Copyright © 2003 SAE InternationalAll rights reserved. No part of this publication may be reproduced, stored in a retrieval system or transmitted, in any form or by any means, electronic, mechanical, photocopying,recording, or otherwise, without the prior written permission of SAE.TO PLACE A DOCUMENT ORDER:Tel: 877-606-7323 (inside USA and Canada)Tel: 724-776-4970 (outside USA)Anodic Coatings for Aluminum and Aluminum AlloysCANCELLATION NOTICEThis specification has been declared “CANCELLED” by the Aerospace Materials Division, SAE, as of July, 2003, and has been superseded by MIL-A-8625. The requirements of the latest issue of MIL-A-8625 shall be fulfilled whenever reference is made to the cancelled AMS-A-8625. By this action, this document will remain listed in the Numerical Section of the index of Aerospace Materials Specifications noting that it is superseded by MIL-A-8625. Cancelled specifications are available from SAE upon request.AEROSPACE MATERIALSPECIFICATIONAMS-A-8625AIssued JUL 2000CancelledJUL 2003Superseding AMS-A-8625NOTICEThis document has been taken directly from U.S. Military Specification MIL-A-8625F and contains only minor editorial and format changes required to bring it into conformance with the publishingrequirements of SAE technical standards. The initial release of this document is intended to replace MIL-A-8625F. Any part numbers established by the original specification remain unchanged.The original Military Specification was adopted as an SAE standard under the provisions of the SAE Technical Standards Board (TSB) Rules and Regulations (TSB 001) pertaining to accelerated adoption of government specifications and standards. TSB rules provide for (a) the publication of portions of unrevised government specifications and standards without consensus voting at the SAE Committee level, and (b) the use of the existing government specification or standard format.Under Department of Defense policies and procedures, any qualification requirements and associated qualified products lists are mandatory for DOD contracts. Any requirement relating to qualified products lists (QPL’s) has not been adopted by SAE and is not part of this SAE technical document.--``,,``,`,`,,,,,`,`,,``,,,``,,-`-`,,`,,`,`,,`---1.SCOPE:1.1Scope:This specification covers the requirements for six types and two classes of electrolytically formed anodic coatings on aluminum and aluminum alloys for non-architectural applications (see 6.1).1.2Classification:The anodic coating Types and Classes covered by this specification are as specified herein (see 6.2 and 6.21).1.2.1Types:Type I -Chromic acid anodizing, conventional coatings produced from chromic acid bath (see3.4.1)Type IB - Chromic acid anodizing, low voltage process, 22 ± 2V, (see 3.4.1)Type IC -Non-chromic acid anodizing, for use as a non-chromate alternative for type I and IBcoatings (see 3.4.1 and 6.1.2)Type II -Sulfuric acid anodizing, conventional coatings produced from sulfuric acid bath (see3.4.2)Type IIB -Thin sulfuric acid anodizing, for use as a non-chromate alternative for Type I and IB coatings (see 3.4.2 and 6.1.2)Type III -Hard Anodic Coatings (see 3.4.3)1.2.2Classes:Class 1 - Non-dyed (see 3.5.)Class 2 - Dyed (see 3.6.)2.APPLICABLE DOCUMENTS:The following specifications and standards form a part of this document to the extent specified herein.2.1U.S. Government Publications:Available from DODSSP, Subscription Services Desk, Building 4D, 700 Robbins Avenue,Philadelphia, PA 19111-5094.MIL-P-23377Primer Coating, Epoxy-Polyamide, Chemical and Solvent ResistantMIL-C-81706Chemical Conversion Materials for Coating Aluminum and Aluminum Alloys MIL-P-85582Primer Coatings: Epoxy, WaterborneQQ-A-250/4Aluminum Alloy 2024, Plate and Sheet --` ` , , ` ` , ` , ` , , , , , ` , ` , , ` ` , , , ` ` , , -` -` , , ` , , ` , ` , , ` ---2.1 (Continued):FED-STD-141Paint, Varnish, Lacquer, and Related Materials: Methods for Sampling andTestingFED-STD-151Metals; Test MethodsMIL-STD-105Sampling Procedures and Tables for Inspection by Attribute2.2ASTM Publications:Available from ASTM, 100 Barr Harbor Drive, West Conshohocken, PA 19428-2959.ASTM B 117Method of Salt Spray (Fog) TestingANSI/ASTM B 137Weight of Coating on Anodically Coated Aluminum, Measurement ofASTM B 244Thickness of Anodic Coatings on Aluminum and of Other NonconductiveCoatings on Nonmagnetic Basis Metals with Eddy Current Instruments,Measurement ofASTM D 822Light and Water Exposure Apparatus (Carbon-Arc Type) for Testing Paint,Varnish, Lacquer and Related Products, Standard Practice for Operating ASTM D 2244Color Differences of Opaque Materials, Instrumental Evaluation ofASTM G 23Standard Practice for Operating Light Exposure Apparatus (Carbon-Arc Type)With and Without Water for Exposure of Non-metallic Materials ASTM G 26Operating Light-Exposure Apparatus (Xenon-Arc Type) With and WithoutWater for Exposure of Non-metallic materials3.REQUIREMENTS:3.1Materials:The materials used shall be such as to produce coatings which meet the requirements of thisspecification.3.1.1Base metal: The base metal shall be free from surface defects, caused by machining, cutting,scratching, polishing, buffing, roughening, bending, stretching, deforming, rolling, sandblasting, vaporblasting, etching, heat treatment condition, alloy chemistry imbalance and inclusions, that will cause coated test panels or parts to fail any of the requirements of this specification. The base metal shall be subjected to cleaning, etching, anodizing and sealing procedures as necessary to yield coatings meeting all requirements of this specification.3.2Equipment and processes:The equipment and processes employed shall be such as to produce coatings which meet therequirements of this specification. Unless otherwise specified in the contract, purchase order or applicable drawing (see 6.2), process operating conditions shall be at the option of the supplier.--` ` , , ` ` , ` , ` , , , , , ` , ` , , ` ` , , , ` ` , , -` -` , , ` , , ` , ` , , ` -----``,,``,`,`,,,,,`,`,,``,,,``,,-`-`,,`,,`,`,,`---AMS-A-8625A SAE AMS-A-8625A3.3General:3.3.1Anodizing of parts and assemblies:3.3.1.1Anodizing of parts: Unless otherwise specified in the contract, purchase order or applicabledrawing (see 6.2), parts shall be anodized after all heat treatment, machining, welding, forming and perforating have been completed.3.3.1.2Anodizing of assemblies: Unless otherwise specified in the contract, purchase order orapplicable drawing, anodic coatings shall not be applied to assemblies which will entrap theelectrolyte in joints or recesses (components shall be anodized separately prior to assembly).When anodizing of assemblies is authorized by the contract, purchase order or applicabledrawing, the processing method used shall not result in subsequent damage to the assemblyfrom electrolyte entrapment (Type I or IA coatings shall be used unless another coating Type is specified). Assemblies which contain non-aluminum parts such as steel, brass or organicsubstances, which would be attacked by pretreatment or anodizing solutions or would preventuniform formation of the anodic coating, shall not be anodized as assemblies, unless the non-aluminum surfaces are masked or electrically insulated in a manner which produces anodiccoatings meeting the requirements of this specification.3.3.1.2Anodizing of complex shapes: When anodizing complex shapes which will entrap the electrolytein recesses, the processing method used shall not result in subsequent damage to the part from electrolyte entrapment (Type I or IA coatings shall be used unless another coating Type isspecified).3.3.2Handling and cleaning: Parts shall be so handled during all pretreatments, anodizing and posttreatments that mechanical damage or contamination will be avoided. Parts shall be free of allforeign substances, oxides and soils, such as greases, oil, paint and welding flux. Parts shall have oxide and other interfering films removed by the use of proper cleaning procedures so as to beclean and have water break free surfaces. Abrasives containing iron, such as steel wool, ironoxide rouge and steel wire, which may become embedded in the metal and accelerate corrosion of aluminum and aluminum alloys, are prohibited as a means of mechanical cleaning, prior toanodizing. If special cleaning requirements are required they shall be specified in the contract or purchase order (see 6.2).3.3.3Reflective surfaces: When specified in the contract or purchase order (see 6.2), parts fabricated toproduce a highly reflective surface shall be chemically or electrochemically brightened, prior toanodic coating (see 6.9).3.3.4Touch up (mechanical damage and contact marks): Unless otherwise specified (see 6.2),mechanically damaged areas from which the anodic coating has been removed without damage to the part may be touched up using chemical conversion materials approved on QPL-81706 forClass 1A coatings and the applicable method of application. Touch up shall apply only toinadvertent mechanical damage such as scratch marks. For Type III coatings, touch up shall only be allowed in areas which will not be subjected to abrasion (see 6.1.1). The mechanicallydamaged area(s) shall not exceed 5 percent of the total anodized area of the item or touch up shall not be permitted. When specified in the contract or purchase order (see 6.2), contact marks shall be touched up using the above method required for mechanical damage.3.4Coatings:Conventional anodic coatings as specified in the contract, purchase order or applicable drawings (see 6.2), shall be prepared by any process or operation to produce the specified coating onaluminum and aluminum alloys.3.4.1Type I, IB, and IC coatings: Type I and IB coatings shall be the result of treating aluminum andaluminum alloys electrolytically in a bath containing chromic acid to produce a uniform anodiccoating on the metal surface. Type IC coatings shall be the result of treating aluminum andaluminum alloys electrolytically in a bath containing mineral or mixed mineral/organic acids (non-chromic acid) to produce a uniform anodic coating on the metal surface. Unless otherwise --``,,``,`,`,,,,,`,`,,``,,,``,,-`-`,,`,,`,`,,`---specified in the contract, purchase order or applicable drawing, Type I coatings shall not be applied to aluminum alloys with a nominal copper content in excess of 5.0 percent; nominal siliconcontents in excess of 7.0 percent; or when the total allowable contents of nominal alloyingelements exceed 7.5 percent. Heat treatable alloys which are to receive a Type I, IB, or IC coating shall be in the required temper to receive a Type I, IB, or IC coating shall be in the required temper obtained by heat treatment, such as -T4, -T6, or T73, prior to anodizing.3.4.1.1Type IC coatings: Type IC coatings provide a non-chromate alternative to Type I and IB coatings.Unless approved by the procuring activity, substitution of a Type IC coating where Type I or IB is specified shall be prohibited.3.4.2Type II and IIB coatings: Type II and IIB coatings shall be the result of treating aluminum andaluminum alloys electrolytically in a bath containing sulfuric acid to produce a uniform anodiccoating on the metal surface. Heat treatable alloys shall be in the required temper obtained byheat treatment, such as -T4, -T6, or T73, prior to anodizing.3.4.2.1Type IIB coatings: Type IIB coatings provide a non-chromate alternative to Type I and IBcoatings. Unless approved by the procuring activity, substitution of a Type IIB coating whereType I or IB is specified shall be prohibited.3.4.3Type III coatings: Type III coatings shall be the result of treating aluminum and aluminum alloyselectrolytically to produce a uniform anodic coating on the metal surface. Type III coatings shall be prepared by any process operation to produce a heavy dense coating of specified thickness on aluminum alloys (see 3.7.2.1). Unless otherwise specified in the contract, purchase order orapplicable drawing, Type III coatings shall not be applied to aluminum alloys with a nominal copper content in excess of 5 percent or a nominal silicon content in excess of 8.0 percent. Alloys with a nominal silicon content higher than 8.0 percent may be anodized subject to approval of theprocuring activity. Heat treatable alloys shall be in a temper obtained by heat treatment, such as -T4, -T6, or T73, prior to anodizing.3.5Class 1:When class 1 is specified in the contract or purchase order, (see 6.2), the anodic coating shall not be dyed or pigmented. Any natural coloration resulting from anodic treatment with the various alloy compositions shall not be considered coloration. The characteristic color imparted by the sealing process shall also be considered as non-dyed.3.6Class 2:When class 2 is specified in the contract or purchase order, (see 6.2), the anodic coating shall be uniformly dyed or pigmented by exposure to a solution of a suitable type dye or stain. The color on wrought alloys shall be uniform. Cast alloys may exhibit dye bleed-out or lack of color (or color uniformity) associated with the inherent porosity of the casting. The dyes and pigments used shall not be damaging to the anodic coatings.3.6.1Dye color: When dyed or pigmented coatings are required, the color and color uniformityrequirements shall be as specified on the contract, purchase order or applicable drawing (see 6.2).3.6.1.1Casting alloys: Dyed casting alloys may show a slight lack of color uniformity. The degree ofnon-uniformity that is acceptable shall be established by the procuring activity (see 6.2).3.7Detail requirements:3.7.1Types I, IB, IC, II, and IIB coatings:3.7.1.1Weight of coating: Prior to dyeing or sealing, Type I, IB, IC, II, and IIB coatings shall meet thecoating weight requirements of Table I when tested in accordance with 4.5.2 (see 6.10.6).TABLE I. Types I, IB, IC, II, and IIB unsealed anodic coating weights3.7.1.2Corrosion resistance: After exposure to the salt spray test specified in4.5.3, specimens shall bevisually examined to determine that all of the following conditions are met:a.Test specimens shall show no more than a total of 15 isolated pits (see 6.19), none largerthan 0.031 inch in diameter, in a total of 150 square inches of test area grouped from five ormore test pieces. Areas within 0.062 inch from identification markings, edges and electrodecontact marks remaining after processing shall be excluded.b.Test specimens shall show no more than 5 isolated pits, none larger than 0.031 inch indiameter, in a total of 30 square inches from one or more test pieces. Areas within 0.062 inchfrom identification markings, edges and electrode contact marks remaining after processingshall be excluded.c.In addition to the requirements in (a) and (b) above, Type I and IB test specimens shall notexhibit patchy dark gray areas (spots, streaks, or marks).3.7.1.3Light fastness resistance: Class 2, dyed anodic coatings, shall show no more fading ordiscoloration than would be equivalent to a Delta (E) value of 3 when subjected to the lightfastness resistance test (see 4.5.4), unless otherwise specified in the contract or purchase order (see 6.2). Light fastness resistance shall be determined only when specified in the contract,purchase order or applicable drawing (see 6.2).3.7.1.4Paint adhesion: When tested in accordance with4.5.6, no intercoat separation shall occurbetween the paint system and the anodic coating or between the anodic coating and the basemetal. Paint adhesion shall be determined only when specified in the contract, purchase order or applicable drawing (see 6.2).3.7.2Type III coatings:3.7.2.1Thickness of coating: Unless otherwise specified in the contract, purchase order, or applicabledrawing (see 6.2), the nominal thickness of the coating shall be 0.002 inch (2 mils) (see 6.16,6.17 and 6.10 through 6.10.5). Unless otherwise specified, the thickness of the coating shall notvary by more than ± 20 percent for coatings up to 0.002 inches thick (2 mils) when tested inaccordance with 4.5.1. Coatings over 0.002 inches (2 mils) shall not vary by more than ± 0.0004 inches (0.4 mils) in thickness. A typical Type III coating thickness range is shown in Table IV.3.7.2.1.1Weight of coating: The coating weight may be determined in lieu of the coating thickness (see 3.7.2.1), at the option of the procuring activity. Unsealed Type III coatings shall have a minimum coating weight of 4320 milligrams per square foot for every 0.001 inch of coating when tested in accordance with 4.5.2 (see 6.2).3.7.2.2Abrasion resistance: When tested in accordance with 4.5.5, unsealed Type III coatings shall provide a hard abrasion resistant finish as specified herein (see 6.17). The anodic coating shall have a maximum wear index of 3.5 mg/1000 cycles on aluminum alloys having a copper content of 2 percent or higher (see 6.13). The wear index for all other alloys shall not exceed 1.5 mg/1000 cycles.3.8Sealing:3.8.1Types I, IB, IC, II, and IIB: All Types I, IB, IC, II, and IIB anodic coatings shall be completely sealed, unless otherwise specified in the contract, purchase order or applicable drawing (see 6.2). They shall be sealed in accordance with 3.8.1.1 or 3.8.1.2 as applicable. If wetting agents are used they shall be of the non-ionic type.3.8.1.1Class 1: When class 1 is specified, sealing shall be accomplished by immersion in a sealing medium such as a 5 percent aqueous solution of sodium or potassium dichromate (pH 5.0 to 6.0) for 15 minutes at 90°C to 100°C (194°F to 212°F), in boiling deionized water, cobalt or nickel acetate, or other suitable chemical solutions (see 6.15).3.8.1.2Class 2: When class 2 is specified, sealing shall be accomplished after dyeing by immersion in a sealing medium, such as a hot aqueous solution containing 0.5 percent nickel or cobalt acetate (pH 5.5 to 5.8), boiling deionized water, duplex sealing with hot aqueous solutions of nickel acetate and sodium dichromate (see 6.11), or other suitable chemical solutions.3.8.2Type III: Type III coatings shall not be sealed where the main function of application is to obtain the maximum degree of abrasion or wear resistance. Where Type III coatings are used for exterior non-maintained applications requiring corrosion resistance but permitting reduced abrasionresistance, the contract or purchase order shall specify that sealing is required. Sealing for such Type III coatings shall be accomplished by immersion in a medium, such as boiling deionizedwater, in a hot aqueous 5 percent sodium dichromate solution, in a hot aqueous solution containing nickel or cobalt acetate or other suitable chemical solutions (see 6.2). When Type III coatings are provided unsealed, parts shall be thoroughly rinsed in cold, clean water and dried after anodizing.3.9Dimensions of coated articles:Articles or parts shall comply with the dimensional requirements of the applicable drawings after application of the anodic coating (see 6.10.1). (For interference in close fits of parts or assemblies see 6.10.5).--``,,``,`,`,,,,,`,`,,``,,,``,,-`-`,,`,,`,`,,`---3.10Toxicity:The coatings and electrical/chemical processes used to develop these anodic coatings shall have no adverse effect on the health of personnel when used for their intended purposes. Questionspertinent to this effect shall be referred by the contracting activity to the appropriate departmental medical service who will act as an advisor to the contracting agency.3.11Painting/coating:Painting/coating operations shall be performed as soon as practical after the anodizing process on clean coatings. If parts require storage prior to painting/coating, they shall be stored in a manner that will avoid contamination. If the parts become contaminated, they shall be cleaned in a manner that will not be detrimental to the anodic coating or the base metal (see 6.3).3.12Dyeing or coloring:Anodic coatings shall not be allowed to dry before dyeing or coloring. Items to be dyed or colored should be preferably coated by the Type II anodizing treatment (see 6.12). Dyed or colored coatings shall not be allowed to remain in rinse waters for more than 5 minutes before sealing.3.13Workmanship:Except for touch up areas in accordance with 3.3.4 and as noted below, the applied anodic coating shall be continuous, smooth, adherent, uniform in appearance, free from powdery areas, loose films, breaks, scratches and other defects which will reduce the serviceability of anodized parts orassemblies. Differences in anodic coating appearance resulting from inherent base metaldifferences in a component such as the presence of welds, components containing cast andmachined surfaces, and differences in grain size within a forging shall not be cause to reject the anodic coating unless otherwise specified in the contract or purchase order (see 6.2). Slightdiscoloration from dripping or rundown of the sealing solution from designed crevices in acomponent shall be allowed.3.13.1Contact marks: The size and number of contact marks shall be at a minimum consistent with goodpractice (see 6.14). If a specific location for contact marks is desired, the location shall bespecified on the contract or purchase order (see 6.2).4.QUALITY ASSURANCE PROVISIONS:4.1Responsibility for inspection:Unless otherwise specified in the contract or purchase order, the contractor is responsible for the performance of all inspection requirements (examinations and tests) as specified herein. Except as otherwise specified in the contract or purchase order, the contractor may use his own or any other facilities suitable for the performance of the inspection requirements specified herein, unlessdisapproved by the Government. The Government reserves the right to perform any of theinspections set forth in the specification where such inspections are deemed necessary to ensure supplies and services conform to prescribed requirements.--``,,``,`,`,,,,,`,`,,``,,,``,,-`-`,,`,,`,`,,`---4.1.1Responsibility for compliance: All items must meet all requirements of Section 3. The inspectionset forth in this specification shall become a part of the contractor’s overall inspection system or quality program. The absence of any inspection requirements in the specification shall not relieve the contractor of the responsibility of ensuring that all products or supplies submitted to theGovernment for acceptance comply with all requirements of the contract. Sampling inspection, as part of manufacturing operations, is an acceptable practice to ascertain conformance torequirements, however, this does not authorize submission of known defective material, eitherindicated or actual, nor does it commit the Government to acceptance of defective material.4.2Classification of inspection:The inspection requirements specified herein are classified as follows:a.Process control inspection (see 4.3).b.Quality conformance inspection (see 4.4).4.3Process control inspection:--``,,``,`,`,,,,,`,`,,``,,,``,,-`-`,,`,,`,`,,`---4.3.1Process control document (PCD): The anodizer shall develop, maintain, and adhere to a PCDdescribing the anodizing process and procedures used to meet the requirements of thisspecification. As a minimum, the PCD shall describe the following:-All steps in the processing sequence.-Ranges for immersion time and temperature for each step in the process.-Chemical constituents used and allowable solution control ranges to be used for solution analysis (see 4.3.2) for each step in the process.-Ranges for temperature, current density and anodizing time (or voltage ramps and hold times) as applied to individual alloys or alloy series.4.3.2Solution analysis: Solution analysis shall be performed on all the processing solutions in theanodizing line to determine if the solution controls are within the acceptable ranges established in the PCD (see 4.3.1). Solution analysis shall be performed at least once every two weeks unless otherwise specified by the procuring activity. The processor shall maintain a record of the history of each processing bath, showing all chemicals or treatment solutions added to the baths and the results of all chemical analysis performed. Upon request of the procuring activity, such records, as well as reports of the test results, shall be made available. These records shall be maintained for not less than one year after completion of the contract or purchase order.4.3.3Process control tests: To assure continuous control of the process, specimens shall be tested inaccordance with Table II. Process control tests are conducted to determine conformance of the anodic coatings with the requirements of this specification and are acceptable as evidence of the properties being obtained with the equipment and procedures employed.4.3.3.1Frequency of the process control tests: Process control tests shall be conducted at least onceevery month. In addition, the intervals between each monthly test shall not exceed 35 days. Ifproduction in accordance with this specification is not performed for a periodic of one month or longer, process control tests shall be conducted at the start of production.TABLE II. Process control tests4.3.3.2Process control test specimens: Production parts shall be used for process control inspectionprovided they can be adapted to the applicable test. If the production parts can not be adapted toa particular test, test panels shall be used. At the option of the supplier, test panels shall becomposed of either 2024-T3 per QQ-A-250/4 or the alloy representing the largest percent of work anodized during the monthly process control period. Whenever possible, the specimen panelsshall be anodized with an actual production run. Additional details for the specimen panels shall be as specified in 4.3.3.2.1 through 4.3.3.2.4.4.3.3.2.1Test specimens for coating weight: Coating weight shall be determined on undyed andunsealed production parts or specimen panels (see 4.3.3.2). When specimen panels are used,they shall have a minimum width of 3 inches, a minimum length of 3 inches, and a minimumnominal thickness of 0.032 inches.4.3.3.2.2Test specimens for coating thickness: Coating thickness shall be determined on Type IIIproduction parts or specimen panels (see 4.3.3.2). When specimen panels are used, they shallhave a minimum width of 3 inches, a minimum length of 3 inches, and a minimum nominalthickness of 0.032 inches.4.3.3.2.3Test specimens for corrosion and light fastness resistance: Corrosion resistance shall bedetermined on dyed (Class 2 only) and sealed production parts or specimen panels (see4.3.3.2). Light fastness testing is performed only on dyed (Class 2) coatings and only whenspecified (see 6.2). When specimen panels are used, they shall have a minimum width of 3inches, a minimum length of 10 inches, and a minimum nominal thickness of 0.032 inches. 4.3.3.2.4Test specimens for abrasion resistance: Abrasion resistance shall be determined on Type IIIproduction parts or specimen panels (see 4.3.3.2). When specimen panels are used, they shallhave a width of 4 inches, a length of 4 inches, and a minimum nominal thickness of 0.063inches.。
国外访学心得体会

国外访学心得体会范文一在美国的游学历程中,我用以下五个部分来简述归纳我的体会。
我的选择是华盛顿大学,在西雅图。
选学校的时候还是一二月份的事情,后来因为《北京遇上西雅图》的走红,本来并不算特别的一个选择,倒成了颇具意境的一个行程,于是我们上演了一次《北大遇上西雅图》,我也便用这个作为感想的题目。
一、学习体会我们在华盛顿大学的Foster商学院进行交换访学,老实说,短期的访学要学到太多东西是不现实的,更多的是体验不同的文化、方式、感受。
与北大光华相比较,其实国外的商学院从教授、教授内容等方面不一定有质的差别。
但是从西方的沟通习惯,教室直接是U字形排布,教授走到学生中间;鼓励思考鼓励对话;即时互动积极探讨没有正确答案等等方面,确实是一种不同的文化和方式,很好的鼓励了大家独立思考。
我们就是在这样的氛围中,体会了国外的MBA教学。
课堂中,教授们随时可能发起互动游戏,让同学的在参与中体验和分享,并鼓励同学们非常独立的思维,不受束缚,这可能是最深刻的一个感受。
同时,大家用极短的时间,分组完成了美国一个著名服装品牌A&F (就是那个著名的肌肉男赤裸上身招揽顾客的牌子)进军亚洲市场的案例。
这些案例的分析,没有对错,只讲逻辑和方法,美国的孩子从很小的时候就经历这样的思维锻炼,因此确实更加思维活跃和开放。
二、企业参观访学安排中另一重要内容是企业参观。
西雅图虽然并非美国最繁华的的城市,但是是美国最宜居的城市,同样集中了不少美国著名企业,其中最有名的四大企业总部是波音、星巴克、亚马逊、微软。
访学的正式安排我们走进了波音、星巴克,还跟随同学驱车到了微软的总部。
还是那句话,更多的体验教给你更多的生活。
在波音,我们主要体会了大工业时代,人类挑战极限的恢弘,而在星巴克,则是一个咖啡文化和星巴克文化之旅,用各种方式让你体验其文化内涵。
三、美式生活既然在美国居住,自然有机会体验美国人的生活。
除了体验吃、环境、购物外,我最大的收获周三意外发现的一个在UniversityVillage 举办的社区Party,比如美国人那种对生活的积极参与的态度,沉浸在音乐中欢快的起舞,非常自由的享受生活。
航空复合材料螺旋桨叶片制造工艺研究进展
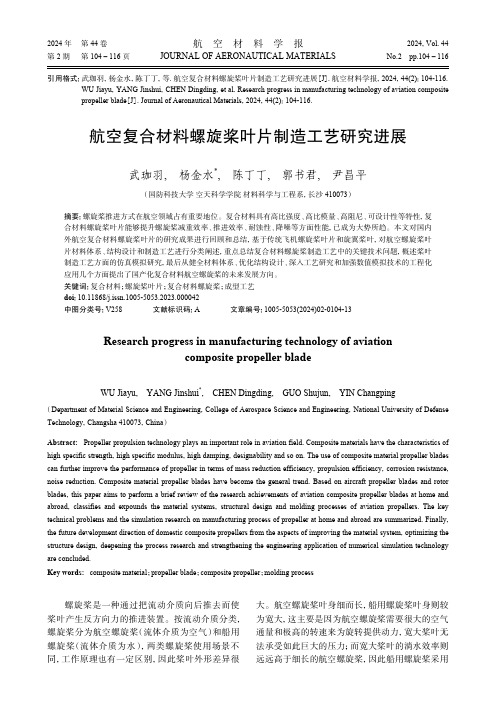
引用格式:武珈羽,杨金水,陈丁丁,等. 航空复合材料螺旋桨叶片制造工艺研究进展[J]. 航空材料学报,2024,44(2):104-116.WU Jiayu,YANG Jinshui,CHEN Dingding,et al. Research progress in manufacturing technology of aviation composite propeller blade[J]. Journal of Aeronautical Materials,2024,44(2):104-116.航空复合材料螺旋桨叶片制造工艺研究进展武珈羽, 杨金水*, 陈丁丁, 郭书君, 尹昌平(国防科技大学 空天科学学院 材料科学与工程系,长沙 410073)摘要:螺旋桨推进方式在航空领域占有重要地位。
复合材料具有高比强度、高比模量、高阻尼、可设计性等特性,复合材料螺旋桨叶片能够提升螺旋桨减重效率、推进效率、耐蚀性、降噪等方面性能,已成为大势所趋。
本文对国内外航空复合材料螺旋桨叶片的研究成果进行回顾和总结,基于传统飞机螺旋桨叶片和旋翼桨叶,对航空螺旋桨叶片材料体系、结构设计和制造工艺进行分类阐述,重点总结复合材料螺旋桨制造工艺中的关键技术问题,概述桨叶制造工艺方面的仿真模拟研究,最后从健全材料体系、优化结构设计、深入工艺研究和加强数值模拟技术的工程化应用几个方面提出了国产化复合材料航空螺旋桨的未来发展方向。
关键词:复合材料;螺旋桨叶片;复合材料螺旋桨;成型工艺doi:10.11868/j.issn.1005-5053.2023.000042中图分类号:V258 文献标识码:A 文章编号:1005-5053(2024)02-0104-13Research progress in manufacturing technology of aviationcomposite propeller bladeWU Jiayu, YANG Jinshui*, CHEN Dingding, GUO Shujun, YIN Changping (Department of Material Science and Engineering,College of Aerospace Science and Engineering,National University of Defense Technology,Changsha 410073,China)Abstract: Propeller propulsion technology plays an important role in aviation field. Composite materials have the characteristics of high specific strength,high specific modulus,high damping,designability and so on. The use of composite material propeller blades can further improve the performance of propeller in terms of mass reduction efficiency,propulsion efficiency,corrosion resistance,noise reduction. Composite material propeller blades have become the general trend. Based on aircraft propeller blades and rotor blades,this paper aims to perform a brief review of the research achievements of aviation composite propeller blades at home and abroad,classifies and expounds the material systems,structural design and molding processes of aviation propellers. The key technical problems and the simulation research on manufacturing process of propeller at home and abroad are summarized. Finally,the future development direction of domestic composite propellers from the aspects of improving the material system,optimizing the structure design,deepening the process research and strengthening the engineering application of numerical simulation technology are concluded.Key words: composite material;propeller blade;composite propeller;molding process螺旋桨是一种通过把流动介质向后推去而使桨叶产生反方向力的推进装置。
天宇航天新材料产品手册

天宇航天新材料产品手册As I started flipping through the pages of the Tianyu Aerospace New Materials Product Catalog, I couldn't help but feel a sense of awe at the innovative products and advanced technologies presented within. 这个产品手册呈现了许多创新产品和先进技术,让我不禁感到惊叹。
From cutting-edge composites to revolutionary coatings, Tianyu Aerospace is leading the way in developing materials that are essential for the future of space exploration. 天宇航天领先开发的复合材料和革命性涂料等产品,为未来太空探索提供了必不可少的材料。
One aspect of the product catalog that particularly caught my attention was the section on thermal protection materials. 这个产品手册中一个特别吸引我的地方是关于热防护材料的部分。
The innovative solutions offered by Tianyu Aerospace in this area are crucial for ensuring the safety of spacecraft as they re-enter the Earth's atmosphere. 天宇航天在这一领域提供的创新解决方案对于确保太空飞船在重新进入地球大气层时的安全至关重要。
航天航空材料在羽绒服上的应用

航天航空材料在羽绒服上的应用1.羽绒服使用航天航空材料制成,可以有效保暖和防水。
Down jackets made with aerospace materials can effectively insulate and resist water.2.轻质的航天材料使羽绒服更加舒适,不会给穿着者带来压力。
The lightweight aerospace materials make the down jacket more comfortable and do not put pressure on the wearer.3.航天航空材料在羽绒服上的运用使得服装更具有耐磨性和耐用性。
The application of aerospace materials on down jackets makes the clothing more abrasion-resistant and durable.4.羽绒服的外层材料采用航天航空材料,可以有效抵御风雨,保持穿着者干燥。
The outer layer of the down jacket is made of aerospace materials, which can effectively resist wind and rain, keeping the wearer dry.5.航天航空材料具有较好的透气性能,在羽绒服上可以增加穿着的舒适感。
Aerospace materials have good breathability and can increase the comfort of wearing down jackets.6.航天航空材料可以在极端环境下保持稳定性,为羽绒服的使用提供了更多可能。
Aerospace materials can maintain stability in extreme environments, providing more possibilities for the use of down jackets.7.羽绒服的内胆采用航天航空材料填充,可以轻盈保暖,不易形变。
关于陶瓷的英语单词

关于陶瓷的英语单词英文回答:Ceramics is a broad term that encompasses a wide range of materials and objects made from inorganic, non-metallic compounds, most commonly oxides, carbides, nitrides, and borides. Ceramics are typically hard, brittle, and heat-resistant, and they are used in a variety of applications, including pottery, tiles, bricks, and refractories.The word "ceramics" is derived from the Greek word "keramos," which means "burnt earth." This is because many ceramics are made by heating clay or other natural materials to a high temperature. The heat causes the materials to undergo a series of chemical reactions that result in the formation of a hard, durable material.Ceramics can be divided into two main categories: traditional ceramics and advanced ceramics. Traditional ceramics are made from natural materials, such as clay,feldspar, and quartz. Advanced ceramics are made from synthetic materials, such as alumina, zirconia, and silicon carbide.Traditional ceramics are typically used in low-temperature applications, such as pottery, tiles, and bricks. Advanced ceramics are typically used in high-temperature applications, such as aerospace components and cutting tools.Ceramics have a number of unique properties that make them useful for a wide variety of applications. These properties include:Hardness and strength.Brittleness and low toughness.High melting point.Resistance to heat and chemicals.Electrical and thermal insulation.Low coefficient of thermal expansion.Chemical inertness.Ceramics are used in a wide variety of applications, including:Pottery and tableware.Tiles for floors and walls.Bricks for building construction.Refractories for lining furnaces and kilns.Aerospace components.Cutting tools.Medical devices.Electrical insulators.Thermal barriers.Ceramics are a versatile and important class of materials that have a wide range of applications. They are used in everything from everyday household items to high-tech aerospace components.中文回答:陶瓷。
介绍航材的书籍
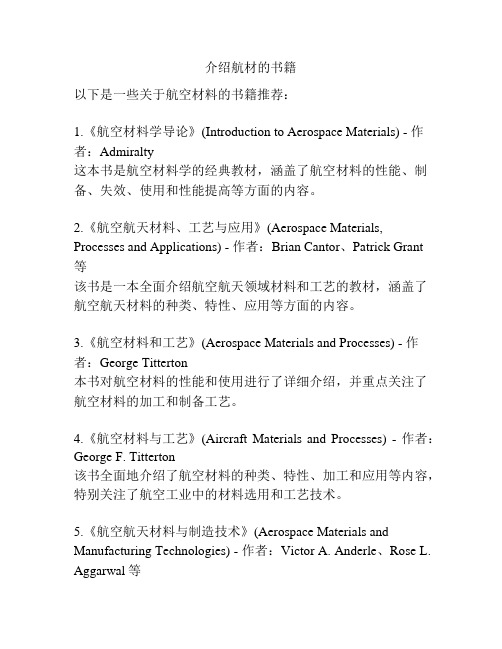
介绍航材的书籍以下是一些关于航空材料的书籍推荐:1.《航空材料学导论》(Introduction to Aerospace Materials) - 作者:Admiralty这本书是航空材料学的经典教材,涵盖了航空材料的性能、制备、失效、使用和性能提高等方面的内容。
2.《航空航天材料、工艺与应用》(Aerospace Materials, Processes and Applications) - 作者:Brian Cantor、Patrick Grant等该书是一本全面介绍航空航天领域材料和工艺的教材,涵盖了航空航天材料的种类、特性、应用等方面的内容。
3.《航空材料和工艺》(Aerospace Materials and Processes) - 作者:George Titterton本书对航空材料的性能和使用进行了详细介绍,并重点关注了航空材料的加工和制备工艺。
4.《航空材料与工艺》(Aircraft Materials and Processes) - 作者:George F. Titterton该书全面地介绍了航空材料的种类、特性、加工和应用等内容,特别关注了航空工业中的材料选用和工艺技术。
5.《航空航天材料与制造技术》(Aerospace Materials and Manufacturing Technologies) - 作者:Victor A. Anderle、Rose L. Aggarwal等这本书以航空航天材料和制造技术为中心,讲述了航空航天材料的种类、性能和应用,同时介绍了制造航空航天零部件的工艺。
这些书籍在航空航天材料领域具有一定的权威性和专业性,能够为读者提供全面的航材知识和相关技术。
无论是对航空航天专业学生还是从业人员都是有价值的参考工具。
- 1、下载文档前请自行甄别文档内容的完整性,平台不提供额外的编辑、内容补充、找答案等附加服务。
- 2、"仅部分预览"的文档,不可在线预览部分如存在完整性等问题,可反馈申请退款(可完整预览的文档不适用该条件!)。
- 3、如文档侵犯您的权益,请联系客服反馈,我们会尽快为您处理(人工客服工作时间:9:00-18:30)。
3
Metal Alloys for Aerospace Application
An alloy is a mixture or solid solution of two or more metals. The atoms of one replace the atoms of the other or occupy interstitial positions between the atoms. • • • • • • Aluminum alloys Titanium alloys Steels Magnesium alloys Nickel alloys Beryllium alloys
6
Aluminum Alloy Characteristics
• Aluminum alloys are the most widely used materials in aircraft structures. • Al alloys are easily formed and machined. • Al alloys are relatively inexpensive. • Al alloys experience a significant reduction in strength at higher temperatures, limiting their application in supersonic aircraft.
7
Aluminum Alloys
Aluminum alloys are identified by a four-digit numbering system that signifies the primary alloying element. • • • • • • • 1000 2000 3000 4000 5000 6000 7000 99% elemental Al Copper Manganese Silicon Magnesium Magnesium and Silicon Zinc
Shear:
σsu = Ultimate Stress G = Modulus of Rigidity
4
Material Forms for Metals
• Sheet and plate – a rolled, flat product
– Sheet thickness less than 0.250 in. – Plate thickness 0.250 in. or greater
• Extrusion – uniform cross section created by forcing metal through a series of dies • Forging – shape created by plastically deforming metal by compression, usually in closed dies. Forging creates high-strength, tough part with efficient use of material. • Casting – created by solidification of liquid material in a mold
5
Applications for Material Forms
• Sheet and plate
– Sheets are used in skin of fuselage, wings, control surfaces, etc. – Plates are machined to varying thickness create optimum shapes in high-cost parts
Aerospace Materials
• Selection of materials for a given application • Aerospace metal alloys – Properties – Relative costs • Composite materials – Material properties – Analysis methods – Manufacturing
• Group 7000: Compression applications or where static strength is more important than fatigue or damage tolerance
– – – – Upper wing surfaces Wing ribs Floor beams 7075-T6, especially in military jets
11
Steel Alloys
Steel alloys are identified by a four-digit numbering system. The first two digits identify the primary alloying elements, while the last two signify the carbon content. • 4130 • 4340 Cr-Mo with 0.3% C Ni-Cr-Mo with 0.4% C
8
Aluminum Alloys for Airframe Structures
• Group 2000: Primarily in tension applications where fatigue and damage-tolerant design are critical
– Lower wing skins – Pressurized fuselage skins – Standard material has been 2024-T3
9
Titanium Alloys
• Titanium alloys offer, with their higher strength, offer higher structural efficiencies than Al alloys. • Ti alloys are offer selected due to high temperature endurance. • Ti alloys are significantly more expensive than Al (high material cost, more difficult to form and machine). • Galvanic corrosion resistance for fastening composite structures. • The most common alloy is Ti-6Al-4V.
1
Material Selection
The first factor to be considered in selection of a material for a given component is the application. • Operational features – principal function of the component; description of principal loads and environment • Design Criteria – most important design properties for satisfying the operational features • Manufacturing Processes – Material form and fabrication processes.
12
Mechanical Properties
Most common metallic materials used for aerospace design are Aluminum, Steel, and Titanium. The properties for these materials are contained in MIL-HDBK-5. Typical data includes:
10
Steel Alloys
• Steel contains iron with a small percentage of carbon (0.02 to 1.7%). Other alloying elements are added to achieve specific properties such as strength, toughness, or corrosion resistance. • The mechanical properties of steels can be varied significantly by heat treating. • Some steels offer very high strength. • Steel alloys are not widely used in airframe structures except where very high strength is needed.
Processing used to produce specific properties (such as heat treatment) are designated by a dashed suffix following the four-digit alloy, e.g., 2024-T3.
• Extrusion – used for uniform cross section parts (e.g., stiffeners on spars, ribs) where higher strength is needed • Forging – nonuniform cross section parts where highstrength is needed. • Casting – lower cost parts in noncritical areas