机械外文翻译--分布式机床的设计
机械设计外文翻译--车床和铣床

中文4285字附录1LATHES & MILLINGA shop that is equipped with a milling machine and an engine lathe can machine almost any type of product of suitable size.The basic machines that are designed primarily to do turning,facing and boring are called lathes. Very little turning is done on other types of machine tools,and none can do it with equal facility. Because lathe can do boring,facing,drilling,and reaming in addition to turning,their versatility permits several operations to be performed with a single setup of the workpiece. This accounts for the fact that lathes of various types are more widely used in manufacturing than any other machine tool.Lathes in various forms have existed for more than two thousand years. Modern lathes date from about 1797,when Henry Maudsley developed one with a leads crew. It provided controlled,mechanical feed of the tool. This ingenious Englishman also developed a change gear system that could connect the motions of the spindle and leadscrew and thus enable threads to be cut.Lathe Construction.The essential components of a lathe are depicted in the block diagram of picture. These are the bed,headstock assembly,tailstock assembly,carriage assembly,quick-change gearbox,and the leadscrew and feed rod.The bed is the back bone of a lathe. It usually is made of well-normalized or aged gray or nodular cast iron and provides a heavy,rigid frame on which all the other basic components are mounted. Two sets of parallel,longitudinal ways,inner and outer,are contained on the bed,usually on the upper side. Some makers use an inverted V-shape for all four ways,whereas others utilize one inverted V and one flat way in one or both sets. Because several other components are mounted and/or move on the ways they must be made with precision to assure accuracy of alignment. Similarly,proper precaution should betaken in operating a lathe to assure that the ways are not damaged. Any inaccuracy in them usually means that the accuracy of the entire lathe is destroyed. The ways on most modern lathes are surface hardened tooffer greater resistance to wear and abrasion.The headstock is mounted in a fixed position on the inner ways at one end of the lathe bed. It provides a powered means of rotating the work at various speeds. It consists,essentially,of a hollow spindle,mounted in accurate bearings,and a set of transmission gears——similar to a truck transmission——through which the spindle can be rotated at a number of speeds. Most lathes provide from eight to eighteen speeds,usually in a geometric ratio,and on modern lathes all the speeds can be obtained merely by moving from two to four levers. An increasing trend is to provide a continuously variable speed range through electrical or mechanical drives.Because the accuracy of a lathe is greatly dependent on the spindle,it is of heavy construction and mounted in heavy bearings,usually preloaded tapered roller or ball types. Along- itudinal hole extends through the spindle so that long bar stock can be fed through it. The size of this hole is an important size dimension of a lathe because it determines the maximum size of bar stock that can be machined when the material must be fed through the spindle.The inner end of the spindle protrudes from the gear box and contains a means for mounting various types of chucks,face plates,and dog plates on it. Whereas small lathes often employ a threaded section to which the chucks are screwed,most large lathes utilize either cam-lock or key-drive taper noses. These provide a large-diameter taper that assures the accurate alignment of the chuck,and a mechanism that permits the chuck or face plate to be locked or unlocked in position without the necessity of having to rotate these heavy attachments.Power is supplied to the spindle by means of an electric motor through a V-belt or silent-chain drive. Most modern lathes have motors of from 5 to15 horsepower to provide adequate power for carbide and ceramic tools at their high cutting speeds.The tailstock assembly consists,essentially,of three parts. A lower casting fits on the inner ways of the bed and can slide longitudinally thereon,with a means for clamping the entire assembly in any desired location. An upper casting fits on the lower one and can be moved transversely upon it on some type of keyed ways. Thistransverse motion permits aligning the tailstock and headstock spindles and provides a method of turning tapers. The third major component of the assembly is the tailstock quill. This is a hollow steel cylinder,usually about2 to3 inches in diameter,that can be moved several inches longitudinally in and out of the upper casting by means of a hand wheel and screw. The open end of the quill hole terminates in a Morse taper in which a lathe center,or various tools such as drills,can be held. A graduated scale,several inches in length,usually is engraved on the outside of the quill to aid in controlling its motion in and out of the upper casting. A locking device permits clamping the quill in any desired position.The carriage assembly provides the means for mounting and moving cutting tools. The carriage is a relatively flat H-shaped casting that rests and moves on the outer set of ways on the bed. The transverse bar of the carriage contains ways on which the cross slide is mounted and can be moved by means of a feed screw that is controlled by a small hand wheel and a graduated dial. Through the cross slide a means is provided for moving the lathe tool in the direction normal to the axis of rotation of the work.On most lathes the tool post actually is mounted on a compound rest. This consists of abase,which is mounted on the cross slide so that it can be pivoted about a vertical axis,and an upper casting. The upper casting is mounted on ways on this base so that it can be moved back and forth and controlled by means of a short lead screw operated by a hand wheel and a calibrated dial.Manual and powered motion for the carriage,and powered motion for the cross slide,is provided by mechanisms within the apron,attached to the front of the carriage. Manual movement of the carriage along the bed is effected by turning a hand wheel on the front of the apron,which is geared to a pinion on the back side. This pinion engages a rack that is attached beneath the upper front edge of the bed in an inverted position.To impart powered movement to the carriage and cross slide,a rotating feed rod is provided. The feed rod,which contains a keyway through out most of its length,passes through the two reversing bevel pinions and is keyed to them . Either pinioncam be brought into mesh with amating bevel gear by means of the reversing lever on the front of the apron and thus provide “forward” or “reverse” power to the carriage. Suitable clutches connect either the rack pinion orthe cross-slide screw to provide longitudinal motion of the carriage or transverse motion of cross slide.For cutting threads,a second means of longitudinal drive is provided by a lead screw. Whereas motion of the carriage when driven by the feed-rod mechanism takes place through a friction clutch in which slippage is possible,motion through the lead screw is by a direct,mechanical connection between the apron and the lead screw. This is achieved by a split nut. By means of a clamping lever on the front of the apron,the split nut can be closed around the lead screw. With the split nut closed,the carriage is moved along the lead screw by direct drive without possibility of slippage.Modern lathes have a quick-change gear box. The input end of this gearbox is driven from the lathe spindle by means of suitable gearing. The out put end of the gear box is connected to the feed rod and lead screw. Thus,through this gear train,leading from the spindle to the quick-change gearbox,thence to the lead screw and feed rod,and then to the carriage,the cutting tool can be made to move a specific distance,either longitudinally or transversely,for each revolution of the spindle. A typical lathe provides,through the feed rod,forty-eight feeds ranging from 0.002 inch to0.118 inch per revolution of the spindle,and,through the lead screw,leads for cutting forty-eight different threads from 1.5 to 92perinch.On some older and some cheaper lathes,one or two gears in the gear train between the spindle and the change gear box must be changed in order to obtain a full range of threads and feeds.Milling is a basic machining process in which the surface is generated by the progressive formation and removal of chips of material from the workpiece as it is fed to a rotating cutter in a direction perpendicular to the axis of the cutter. .In some cases the workpiece is stationary and the cutter is fed to the work. In most instances a multiple-tooth cutter is used so that the metal removal rate is high,and frequently the desired surface is obtained in a single pass of the work.The tool used in milling is known as a milling cutter. It usually consists of a cylindrical body which rotates on its axis and contains equally spaced peripheral teeth that intermittently engage and cut the workpiece. In some cases the teeth extend part way across one or both ends of the cylinder.Because the milling principle provides rapid metal removal and can produce good surface finish,it is particularly well-suited for mass-production work,and excellent milling machines have been developed for this purpose. However,very accurate and versatile milling machines of a general-purpose nature also have been developed that are widely used in job-shop and tool and die work. A shop that is equipped with a milling machine and an engine lathe can machine almost any type of product of suitable size.Types of Milling Operations. Milling operations can be classified into two broad categories,each of which has several variations:1.In peripheral milling a surface is generated by teeth located in the periphery of the cutter body;the surface is parallel with the axis of rotation of the cutter. Both flat and formed surfaces can be produced by this method. The cross section of the resulting surface corresponds to the axial contour of the cutter. This procedure often is called slab milling.1.In face milling the generated flat surface is at right angles to the cutteraxis and is thecombined result of the actions of the portions of the teeth located on both the periphery and thewith the face portions providing a finishing action.The basic concepts of peripheral and face milling are illustrated in Fig. Peripheral milling operations usually are performed on machines having horizontal spindles,whereas face milling is done on both horizontal-and vertical-spindle machines.Surface Generation in Milling. Surfaces can be generated in milling by two distinctly different methods depicted in Fig. Note that in up milling the cutter rotatesagainst the direction of feed the workpiece,whereas in down milling the rotation is in the same direction as the feed .As shown in Fig., the method of chip formation is quite different in the two cases. In up milling the c hip is very thin at the beginning, where the tooth first contacts the work,and increases in thickness, be-coming a maximum where the tooth leaves the work. The cutter tends to push the work along and lift it upward from the table. This action tends to eliminate any effect of looseness in the feed screw and nut of the milling machine table and results in a smooth cut. However, the action also tends to loosen the work from the clamping device so that greater clamping forcers must be employed. In addition, the smoothness of the generated surface depends greatly on the sharpness of the cutting edges.In down milling,maximum chip thickness occurs close to the point at which the tooth contacts the work. Because the relative motion tends to pull the workpiece into the cutter,all possibility of looseness in the table feed screw must be eliminated if down milling is to be used. It should never be attempted on machines that are not designed for this type of milling. In as mush as the material yields in approximately a tangential direction at the end of the tooth engagement,there is much less tendency for the machined surface to show tooth marks than when up milling is used. Another consider able advantage of down milling is that the cutting force tends to hold the work against the machine table,permitting lower clamping force to be employed. This is particularly advantageous when milling thin workpiece or when taking heavy cuts.Sometimes a disadvantage of down milling is that the cutter teeth strike against the surface of the work at the beginning of each chip. When the workpiece has a hard surface,such as castings do,this may cause the teeth to dull rapidly.Milling Cutters. Milling cutters can be classified several ways. One method is to group them into two broad classes,based on tooth relief,as follows:1. Profile-cutters have relief provided on each tooth by grinding a small land back of the cutting edge. The cutting edge may be straight or curved.2.In form or cam-relieved cutters the cross section of each tooth is an eccentric curve behind the cutting edge,thus providing relief. All sections of the eccentric relief,parallel with the cutting edge,must have the same contour as the cutting edge. Cutters of this type are sharpened by grinding only the face of the teeth,with the contour of the cutting edge thus remaining unchanged.Another useful method of classification is according to the method of mounting the cutter. Arbor cutters are those that have a center hole so they can be mounted on an arbor. Shank cutters have either tapered or straight integral shank. Those with tapered shanks can be mounted directly in the milling machine spindle,whereas straight-shank cutters are held in a chuck. Facing cuttersusually are bolted to the end of a stub arbor.Types of Milling Cutters. Plain milling cutters are cylindrical or disk-shaped,having straight or helical teeth on the periphery. They are used for milling flat surfaces. This type of operation is called plain or slab milling. Each tooth in a helical cutter engages the work gradually,and usually more than one tooth cuts at a given time. This reduces shock and chattering tendencies and promotes a smoother surface. Consequently,this type of cutter usually is preferred over one with straight teeth. Side milling cutters are similar to plain milling cutters except that the teeth extend radially part way across one or both ends of the cylinder toward the center. The teeth may be either straight or helical. Frequently these cutters are relatively narrow,being disklike in shape. Two or more side milling cutters often are spaced on an arbor to make simultaneous,parallel cuts,in an operation called straddle milling.Interlocking slotting cutters consist of two cutters similar to side mills,but made to operate as a unit for milling slots. The two cutters are adjusted to the desired width by inserting shims between them.Staggered-tooth milling cutters are narrow cylindrical cutters having staggered teeth,and with alternate teeth having opposite helix angles. They are ground to cut only on the periphery,but each tooth also has chip clearance ground on the protruding side. These cutters have a free cutting action that makes them particularly effective in milling deep slots. Metal-slitting saws are thin,plain milling cutters,usually from 1/32 to 3/16 inch thick,which have their sides slightly“dished”to provide clearance and prevent binding. They usually have more teeth per inch of diameter than ordinaryplain milling cutters and are used for milling deep,narrow slots and for cutting-off operations.附录2车床和铣床车间里拥有一台车床和一台普通铣床就能加工出具有适合尺寸的各种产品。
机械类外文文献及翻译
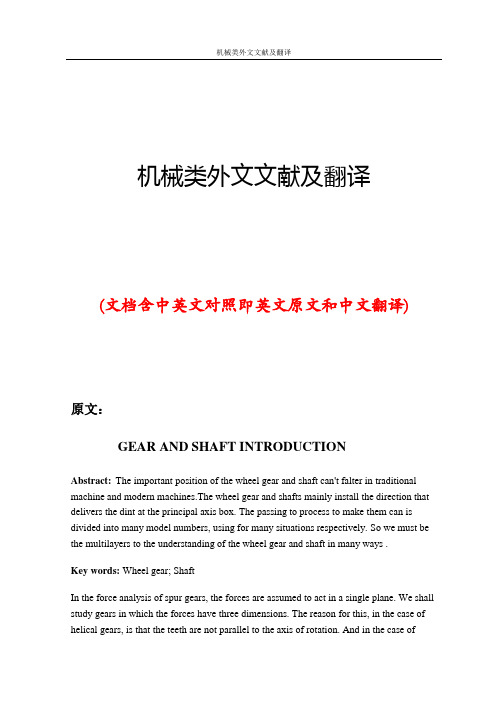
机械类外文文献及翻译(文档含中英文对照即英文原文和中文翻译)原文:GEAR AND SHAFT INTRODUCTIONAbstract:The important position of the wheel gear and shaft can't falter in traditional machine and modern machines.The wheel gear and shafts mainly install the direction that delivers the dint at the principal axis box. The passing to process to make them can is divided into many model numbers, using for many situations respectively. So we must be the multilayers to the understanding of the wheel gear and shaft in many ways .Key words: Wheel gear; ShaftIn the force analysis of spur gears, the forces are assumed to act in a single plane. We shall study gears in which the forces have three dimensions. The reason for this, in the case of helical gears, is that the teeth are not parallel to the axis of rotation. And in the case ofbevel gears, the rotational axes are not parallel to each other. There are also other reasons, as we shall learn.Helical gears are used to transmit motion between parallel shafts. The helix angle is the same on each gear, but one gear must have a right-hand helix and the other a left-hand helix. The shape of the tooth is an involute helicoid. If a piece of paper cut in the shape of a parallelogram is wrapped around a cylinder, the angular edge of the paper becomes a helix. If we unwind this paper, each point on the angular edge generates an involute curve. The surface obtained when every point on the edge generates an involute is called an involute helicoid.The initial contact of spur-gear teeth is a line extending all the way across the face of the tooth. The initial contact of helical gear teeth is a point, which changes into a line as the teeth come into more engagement. In spur gears the line of contact is parallel to the axis of the rotation; in helical gears, the line is diagonal across the face of the tooth. It is this gradual of the teeth and the smooth transfer of load from one tooth to another, which give helical gears the ability to transmit heavy loads at high speeds. Helical gears subject the shaft bearings to both radial and thrust loads. When the thrust loads become high or are objectionable for other reasons, it may be desirable to use double helical gears. A double helical gear (herringbone) is equivalent to two helical gears of opposite hand, mounted side by side on the same shaft. They develop opposite thrust reactions and thus cancel out the thrust load. When two or more single helical gears are mounted on the same shaft, the hand of the gears should be selected so as to produce the minimum thrust load.Crossed-helical, or spiral, gears are those in which the shaft centerlines are neither parallel nor intersecting. The teeth of crossed-helical fears have point contact with each other, which changes to line contact as the gears wear in. For this reason they will carry out very small loads and are mainly for instrumental applications, and are definitely not recommended for use in the transmission of power. There is on difference between a crossed heli : cal gear and a helical gear until they are mounted in mesh with each other. They are manufactured in the same way. A pair of meshed crossed helical gears usually have the same hand; that is ,a right-hand driver goes with a right-hand driven. In the design of crossed-helical gears, the minimum sliding velocity is obtained when the helix angle areequal. However, when the helix angle are not equal, the gear with the larger helix angle should be used as the driver if both gears have the same hand.Worm gears are similar to crossed helical gears. The pinion or worm has a small number of teeth, usually one to four, and since they completely wrap around the pitch cylinder they are called threads. Its mating gear is called a worm gear, which is not a true helical gear. A worm and worm gear are used to provide a high angular-velocity reduction between nonintersecting shafts which are usually at right angle. The worm gear is not a helical gear because its face is made concave to fit the curvature of the worm in order to provide line contact instead of point contact. However, a disadvantage of worm gearing is the high sliding velocities across the teeth, the same as with crossed helical gears.Worm gearing are either single or double enveloping. A single-enveloping gearing is onein which the gear wraps around or partially encloses the worm.. A gearing in which each element partially encloses the other is, of course, a double-enveloping worm gearing. The important difference between the two is that area contact exists between the teeth of double-enveloping gears while only line contact between those of single-enveloping gears. The worm and worm gear of a set have the same hand of helix as for crossed helical gears, but the helix angles are usually quite different. The helix angle on the worm is generally quite large, and that on the gear very small. Because of this, it is usual to specify the lead angle on the worm, which is the complement of the worm helix angle, and the helix angle on the gear; the two angles are equal for a 0-deg. Shaft angle.When gears are to be used to transmit motion between intersecting shaft, some of bevel gear is required. Although bevel gear are usually made for a shaft angle of 0 deg. They may be produced for almost any shaft angle. The teeth may be cast, milled, or generated. Only the generated teeth may be classed as accurate. In a typical bevel gear mounting, one of the gear is often mounted outboard of the bearing. This means that shaft deflection can be more pronounced and have a greater effect on the contact of teeth. Another difficulty, which occurs in predicting the stress in bevel-gear teeth, is the fact the teeth are tapered.Straight bevel gears are easy to design and simple to manufacture and give very good results in service if they are mounted accurately and positively. As in the case of squr gears, however, they become noisy at higher values of the pitch-line velocity. In these cases it is often go : od design practice to go to the spiral bevel gear, which is the bevel counterpart of thehelical gear. As in the case of helical gears, spiral bevel gears give a much smoother tooth action than straight bevel gears, and hence are useful where high speed are encountered.It is frequently desirable, as in the case of automotive differential applications, to have gearing similar to bevel gears but with the shaft offset. Such gears are called hypoid gears because their pitch surfaces are hyperboloids of revolution. The tooth action between such gears is a combination of rolling and sliding along a straight line and has much in common with that of worm gears.A shaft is a rotating or stationary member, usually of circular cross section, having mounted upon it such elementsas gears, pulleys, flywheels, cranks, sprockets, and other power-transmission elements. Shaft may be subjected to bending, tension, compression, or torsional loads, acting singly or in combination with one another. When they are combined, one may expect to find both static and fatigue strength to be important design considerations, since a single shaft may be subjected to static stresses, completely reversed, and repeated stresses, all acting at the same time.The word “shaft” covers numerous v ariations, such as axles and spindles. Anaxle is a shaft, wither stationary or rotating, nor subjected to torsion load. A shirt rotating shaft is often called a spindle.When either the lateral or the torsional deflection of a shaft must be held to close limits, the shaft must be sized on the basis of deflection before analyzing the stresses. The reason for this is that, if the shaft is made stiff enough so that the deflection is not too large, it is probable that the resulting stresses will be safe. But by no means should the designer assume that they are safe; it is almost always necessary to calculate them so that he knows they are within acceptable limits. Whenever possible, the power-transmission elements, such as gears or pullets, should be located close to the supporting bearings, This reduces the bending moment, and hence the deflection and bending stress.Although the von Mises-Hencky-Goodman method is difficult to use in design of shaft, it probably comes closest to predicting actual failure. Thus it is a good way of checking a shaft that has already been designed or of discovering why a particular shaft has failed in service. Furthermore, there are a considerable number of shaft-design problems in which the dimension are pretty well limited by other considerations, such as rigidity, and it is only necessary for the designer to discover something about the fillet sizes, heat-treatment,and surface finish and whether or not shot peening is necessary in order to achieve the required life and reliability.Because of the similarity of their functions, clutches and brakes are treated together. In a simplified dynamic representation of a friction clutch, or brake, two in : ertias I and I traveling at the respective angular velocities W and W, one of which may be zero in the case of brake, are to be brought to the same speed by engaging the clutch or brake. Slippage occurs because the two elements are running at different speeds and energy is dissipated during actuation, resulting in a temperature rise. In analyzing the performance of these devices we shall be interested in the actuating force, the torque transmitted, the energy loss and the temperature rise. The torque transmitted is related to the actuating force, the coefficient of friction, and the geometry of the clutch or brake. This is problem in static, which will have to be studied separately for eath geometric configuration. However, temperature rise is related to energy loss and can be studied without regard to the type of brake or clutch because the geometry of interest is the heat-dissipating surfaces. The various types of clutches and brakes may be classified as fllows:. Rim type with internally expanding shoes. Rim type with externally contracting shoes. Band type. Disk or axial type. Cone type. Miscellaneous typeThe analysis of all type of friction clutches and brakes use the same general procedure. The following step are necessary:. Assume or determine the distribution of pressure on the frictional surfaces.. Find a relation between the maximum pressure and the pressure at any point. Apply the condition of statical equilibrium to find (a) the actuating force, (b) the torque, and (c) the support reactions.Miscellaneous clutches include several types, such as the positive-contact clutches, overload-release clutches, overrunning clutches, magnetic fluid clutches, and others.A positive-contact clutch consists of a shift lever and two jaws. The greatest differences between the various types of positive clutches are concerned with the design of the jaws. To provide a longer period of time for shift action during engagement, the jaws may be ratchet-shaped, or gear-tooth-shaped. Sometimes a great many teeth or jaws are used, and they may be cut either circumferentially, so that they engage by cylindrical mating, or on the faces of the mating elements.Although positive clutches are not used to the extent of the frictional-contact type, they do have important applications where synchronous operation is required.Devices such as linear drives or motor-operated screw drivers must run to definite limit and then come to a stop. An overload-release type of clutch is required for these applications. These clutches are usually spring-loaded so as to release at a predetermined toque. The clicking sound which is heard when the overload point is reached is considered to be a desirable signal.An overrunning clutch or coupling permits the driven member of a machine to “freewheel” or “overrun” bec ause the driver is stopped or because another source of power increase the speed of the driven. This : type of clutch usually uses rollers or balls mounted between an outer sleeve and an inner member having flats machined around the periphery. Driving action is obtained by wedging the rollers between the sleeve and the flats. The clutch is therefore equivalent to a pawl and ratchet with an infinite number of teeth.Magnetic fluid clutch or brake is a relatively new development which has two parallel magnetic plates. Between these plates is a lubricated magnetic powder mixture. An electromagnetic coil is inserted somewhere in the magnetic circuit. By varying the excitation to this coil, the shearing strength of the magnetic fluid mixture may be accurately controlled. Thus any condition from a full slip to a frozen lockup may be obtained.齿轮和轴的介绍摘要:在传统机械和现代机械中齿轮和轴的重要地位是不可动摇的。
机械外文文献及翻译
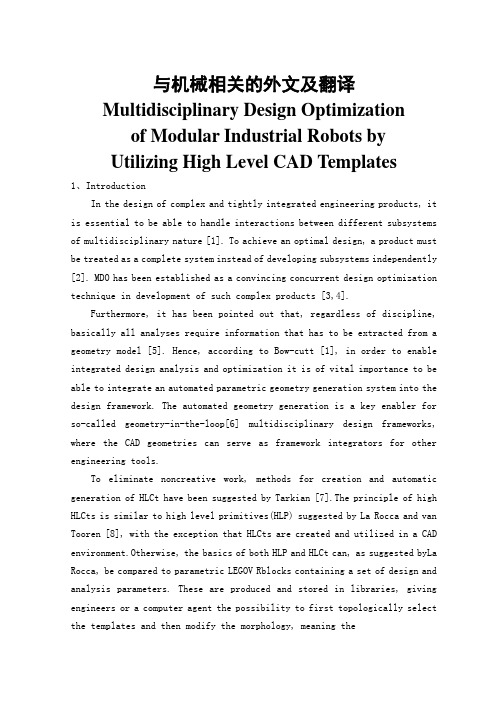
与机械相关的外文及翻译Multidisciplinary Design Optimization of Modular Industrial Robots by Utilizing High Level CAD Templates1、IntroductionIn the design of complex and tightly integrated engineering products, it is essential to be able to handle interactions between different subsystems of multidisciplinary nature [1]. To achieve an optimal design, a product must be treated as a complete system instead of developing subsystems independently [2]. MDO has been established as a convincing concurrent design optimization technique in development of such complex products [3,4].Furthermore, it has been pointed out that, regardless of discipline, basically all analyses require information that has to be extracted from a geometry model [5]. Hence, according to Bow-cutt [1], in order to enable integrated design analysis and optimization it is of vital importance to be able to integrate an automated parametric geometry generation system into the design framework. The automated geometry generation is a key enabler for so-called geometry-in-the-loop[6] multidisciplinary design frameworks, where the CAD geometries can serve as framework integrators for other engineering tools.To eliminate noncreative work, methods for creation and automatic generation of HLCt have been suggested by Tarkian [7].The principle of high HLCts is similar to high level primitives(HLP) suggested by La Rocca and van Tooren [8], with the exception that HLCts are created and utilized in a CAD environment.Otherwise, the basics of both HLP and HLCt can, as suggested byLa Rocca, be compared to parametric LEGOV Rblocks containing a set of design and analysis parameters. These are produced and stored in libraries, giving engineers or a computer agent the possibility to first topologically select the templates and then modify the morphology, meaning theshape,of each template parametrically.2、Multidisciplinary Design FrameworkMDO is a “systematic approach to design space exploration”[17], the implementation of which allows the designer to map the interdisciplinary relations that exist in a system. In this work, the MDO framework consists of a geometry model, a finite element(FE) model, a dynamic model and a basic cost model. The geometry model provides the analysis tools with geometric input. The dynamic model requires mass properties such as mass, center of gravity, and inertia. The FE model needs the meshed geometry of the robot as well as the force and torque interactions based on results of dynamic simulations.High fidelity models require an extensive evaluation time which has be taken into account. This shortcoming is addressed by applying surrogate models for the FE and the CAD models. The models are briefly presented below. 2.1 High Level CAD Template—Geometry ModelTraditionally, parametric CAD is mainly focused on morphological modifications of the geometry. However, there is a limit to morphological parameterization as follows:•The geometries cannot be radically modified.•Increased geometric complexity greatly increases parameterization complexity.The geometry model of the robot is generated with presaved HLCts, created in CATIA V5. These are topologically instantiated with unique internal design variables. Topological parameterization allows deletion, modification, and addition of geometricelements which leads to a much greater design space captured.Three types of HLCts are used to define the industrial robot topologically; Datum HLCt which includes wireframe references required for placement for the Actuator HLCTs and Structure HLCts, as seen Fig.2.Fig. 2 An industrial robot (left) and a modular industrial robot(right) The names of the references that must be provided for each HLCt instantiation are stored in the knowledge base (see Appen-dix A.4), which is searched through by the inference engine. In Appendix A, pseudocode examples describes how the references are retrieved and how they are stored in the knowledge base.The process starts by the user defining the number of degrees of freedom (DOF) of the robot (see Fig. 3) and is repeated until the number of axis (i) is equal to the user defined DOF.In order to instantiate the first Structure HLCt, two Datum and two actuator instances are needed. References from the two Datum instances help orienting the structure in space, while the geometries of the actuator instances, at both ends of the link, are used to construct the actuator attachments, as seen in Figs. 2 and 3. For the remaining links, only one new instance of both datum and actuator HLCts are required, since the datum and actuator instances from adjacent links are already available.Appendix A.2 shows a pseudocode example of an instantiation function. The first instantiated datum HLCt is defined with reference to the absolute coordinate system. The remaining datum HLCt instances are placed in a sequential order, where the coordinate system of previous instances is used as reference for defining the position in space according to user inputs (see also AppendixA.3). Furthermore, the type of each actuator and structure instance is user defined.Fig. 3 The high level CAD template instantiation process Since it is possible to create new HLCts in the utilized CAD tool, the users are not forced to merely choose from the templates available. New HLCts can be created, placed in the database and parametrically inserted into the models.2.2 Dynamic ModelThe objective of performing dynamic simulation of a robot is to evaluate system performance, such as predicting acceleration and time performance, but it also yields loads on each actuated axis, needed for actuator lifetime calculations and subsequent stress analysis based on FE calculations. Thedynamic model in the outlined framework is developed in Modelica using Dymola, and it constitutes a seven-axis robot arm based on the Modelica Standard library [18].The dynamic model receives input from the geometry model,as well as providing output to the FE model, which is further described in Sec. 2.3. However, to better understand the couplings between the models, the Newton –Euler formulation will be briefly discussed. In this formulation, the link velocities and acceleration are iteratively computed, forward recursivelyWhen the kinematic properties are computed, the force and torque interactions between the links are computed backward recursively from the last to the first link2.3 FE Surrogate ModelTo compute the structural strength of the robot, FE models for each robot link is created utilizing CATIA V5, see Fig. 4. For each HLCt, mesh and boundary conditions are manually preprocessed in order to allow for subsequent automation for FE-model creation. The time spent on preprocessing each FE-model is thus extensive. Nonetheless, the obtained parametric FE-model paves way for automated evaluation of a wide span of concepts. Each robot link is evaluated separately with the load conditions extracted from the dynamicmodel. The force (fi-11and fi) and torque (ţi-1and ti) are applied on the surfaceswhere the actuators are attached.2.4 Geometric Surrogate Models.Surrogate models are numerically efficient models to determine the relation between inputs and o utputs of a model [19]. The input variables for the proposed application are the morphological variables thickness and link height as well as a topological variable actuator type. The outputs of the surrogate models are mass m, Inertia I, and center of gravity ri,ci.To identify the most suitable type of surrogate model for the outlined problem, a range of surrogate models types are created and evaluated using 50 samples. The precision of each surrogate model is compared with the values of the original model with 20 new samples. The comparison is made using the relative average absolute error (RAAE) and relative maximum absolute error (RMAE) as specified by Shan et al. [20], as well as the normalized root mean square error (NRMSE), calculated as seen in Eq. (3). All precision metrics are desired to be as low as possible, since low values mean that the surrogate model is accurateThe resulting precision metrics can be seen in Appendix B and the general conclusion is that anisotropic kriging [21], neural networks [22], and radialbasis functions [23] are the most promising surrogate models. To investigate the impact of increasing number of samples, additional surrogate models of those three are fitted using 100 samples, and the results compiled in Appendix B. The resulting NRMSEs for 50 and 100 samples for anistotropic kriging, neural networks, and radial basis functions can be seen in Fig.5. The figures inside the parentheses indicate the number of samples used to fit the surrogate models.Fig. 5 Graph of the NRMSEs for different surrogate models,fitted using 50 and 100 samplesAccording to Fig. 5, anisotropic kriging outperforms the other surrogate models and the doubling of the number of samples usedfor fitting the surrogate model increases the precision dramatically.2.5 FE Surrogate ModelsFor generating FE surrogate models, the anisotropic kriging was also proven to be the most accurate compared to the methods evaluated in Sec. 2.4. Here, one surrogate model is created for each link. Inputs are thickness,actuators, force (fi-11and fi) and torque (ţi-1and ti). The output for eachsurrogate model is maximum stress (MS).A mean error of approximately 9% is reached when running 1400 samples for each link. The reason for the vast number of samples, compared to geometry surrogate models, has to do with a much larger design space.利用高水平CAD模板进行模块化工业机器人的多学科设计优化1 介绍指出,除了规则,基本上所有的分析都需要信息,而这些信息需要从一个几何模型中提取。
机械设计外文文献翻译、中英文翻译

机械设计外文文献翻译、中英文翻译unavailable。
The first step in the design process is to define the problem and XXX are defined。
the designer can begin toXXX evaluated。
and the best one is XXX。
XXX.Mechanical DesignA XXX machines include engines。
turbines。
vehicles。
hoists。
printing presses。
washing machines。
and XXX and methods of design that apply to XXXXXX。
cams。
valves。
vessels。
and mixers.Design ProcessThe design process begins with a real need。
Existing apparatus may require XXX。
efficiency。
weight。
speed。
or cost。
while new apparatus may be XXX。
To start。
the designer must define the problem and XXX。
ideas and concepts are generated。
evaluated。
and refined until the best one is XXX。
XXX.XXX。
assembly。
XXX.During the preliminary design stage。
it is important to allow design XXX if some ideas may seem impractical。
they can be corrected early on in the design process。
机床行业中英文对照

机床行业中英文对照下面是机床行业中常见的英文对照:- 机床行业:Machine tool industry- 机床:Machine tool- 数控机床:Computer Numerical Control (CNC) machine tool - 金属切削机床:Metal cutting machine tool- 金属加工机床:Metal processing machine tool- 金属成型机床:Metal forming machine tool- 车床:Lathe- 铣床:Milling machine- 钻床:Drilling machine- 磨床:Grinding machine- 塑料加工机床:Plastic processing machine tool- 精密机床:Precision machine tool- 自动化机床:Automated machine tool- 机床控制系统:Machine tool control system- 数控系统:Numerical control system- 机床加工能力:Machine tool processing capacity- 加工精度:Processing accuracy- 切削速度:Cutting speed- 进给速度:Feed rate- 主轴转速:Spindle speed- 工件夹紧:Workpiece clamping- 工件定位:Workpiece positioning- 刀具选择:Tool selection- 刀具更换:Tool change- 冷却液:Coolant- 刀柄:Tool holder- 加工中心:Machining center- 排屑:Chip removal- 刀具磨损:Tool wear- 折弯机:Bending machine- 冲床:Punching machine- 压力机:Press machine- 剪板机:Shearing machine- 抛光机:Polishing machine- 螺纹机床:Thread cutting machine tool - 铸造机床:Casting machine tool- 灰铁:Gray iron- 球墨铸铁:Ductile iron- 铝合金:Aluminum alloy- 不锈钢:Stainless steel- 最大加工尺寸:Maximum processing size - 机床设计:Machine tool design- 机床制造:Machine tool manufacturing - 机床市场:Machine tool market- 机床出口:Machine tool export- 机床进口:Machine tool import- 机床行业协会:Machine tool industry association。
机械组合机床设计外文文翻译、中英文翻译、外文翻译
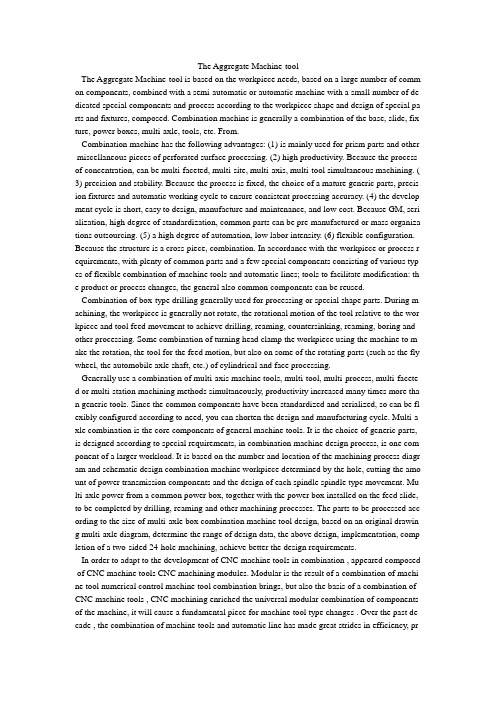
The Aggregate Machine-toolThe Aggregate Machine-tool is based on the workpiece needs, based on a large number of comm on components, combined with a semi-automatic or automatic machine with a small number of de dicated special components and process according to the workpiece shape and design of special pa rts and fixtures, composed. Combination machine is generally a combination of the base, slide, fix ture, power boxes, multi-axle, tools, etc. From.Combination machine has the following advantages: (1) is mainly used for prism parts and other miscellaneous pieces of perforated surface processing. (2) high productivity. Because the process of concentration, can be multi-faceted, multi-site, multi-axis, multi-tool simultaneous machining. ( 3) precision and stability. Because the process is fixed, the choice of a mature generic parts, precis ion fixtures and automatic working cycle to ensure consistent processing accuracy. (4) the develop ment cycle is short, easy to design, manufacture and maintenance, and low cost. Because GM, seri alization, high degree of standardization, common parts can be pre-manufactured or mass organiza tions outsourcing. (5) a high degree of automation, low labor intensity. (6) flexible configuration. Because the structure is a cross-piece, combination. In accordance with the workpiece or process r equirements, with plenty of common parts and a few special components consisting of various typ es of flexible combination of machine tools and automatic lines; tools to facilitate modification: th e product or process changes, the general also common components can be reused.Combination of box-type drilling generally used for processing or special shape parts. During m achining, the workpiece is generally not rotate, the rotational motion of the tool relative to the wor kpiece and tool feed movement to achieve drilling, reaming, countersinking, reaming, boring and other processing. Some combination of turning head clamp the workpiece using the machine to m ake the rotation, the tool for the feed motion, but also on some of the rotating parts (such as the fly wheel, the automobile axle shaft, etc.) of cylindrical and face processing.Generally use a combination of multi-axis machine tools, multi-tool, multi-process, multi-facete d or multi-station machining methods simultaneously, productivity increased many times more tha n generic tools. Since the common components have been standardized and serialized, so can be fl exibly configured according to need, you can shorten the design and manufacturing cycle. Multi-a xle combination is the core components of general machine tools. It is the choice of generic parts, is designed according to special requirements, in combination machine design process, is one com ponent of a larger workload. It is based on the number and location of the machining process diagr am and schematic design combination machine workpiece determined by the hole, cutting the amo unt of power transmission components and the design of each spindle spindle type movement. Mu lti-axle power from a common power box, together with the power box installed on the feed slide, to be completed by drilling, reaming and other machining processes. The parts to be processed acc ording to the size of multi-axle box combination machine tool design, based on an original drawin g multi-axle diagram, determine the range of design data, the above design, implementation, comp letion of a two-sided 24-hole machining, achieve better the design requirements.In order to adapt to the development of CNC machine tools in combination , appeared composed of CNC machine tools CNC machining modules. Modular is the result of a combination of machi ne tool numerical control machine tool combination brings, but also the basis of a combination of CNC machine tools , CNC machining enriched the universal modular combination of components of the machine, it will cause a fundamental piece for machine tool type changes . Over the past de cade , the combination of machine tools and automatic line has made great strides in efficiency, productivity , flexibility and the use of concurrent engineering to develop a more rational, more savi ngs programs. With the development of digital technology, electronic technology , the combinatio n of machine mechanical structure and control system has undergone great changes. With a combi nation of the following development tools : 1 NC . Combination of CNC machine tools emerge , n ot only changed in the past by the relay circuit consisting of a combination of machine tool control systems , but also make head or even a combination of the mechanical structure of the machine co mponents of general criteria huge change occurred . 2 modular . NC modular greatly enriched the common combination of components of the machine, it will cause a fundamental change occurred for machine tool parts , according to the principles of modular design , based on the functional ana lysis division of the combination of multi- axle box for each machine level modules. 3 speed. As t he high-speed processing can reduce the surface roughness and cutting force components , reducin g the cutting temperature , improve productivity, so the speed of the machine is just beginning rese arch , especially the main movement of CNC machine tools and feed velocity has reached a very h igh speed . Conform to the trend of high-speed machine tools , machine tool 's speed will be highe r. 4 , precision . Because the CNC machine to achieve , so more and more high machining accurac y . 5, full protection technology . Now the machine is fully enclosed features a large , almost all m echanical housings are fully closed . Fully enclosed protection, not only to make the machine mor e attractive appearance and its production line , but also improves the safety, reliability and ease of maintenance . Combination machine with both the advantages of low cost and high efficiency in l arge volume production has been widely used, and can consist of automated production lines. .组合机床组合机床是根据工件加工需要,以大量通用部件为基础,配之以少量的专用部件和按工件形状和加工工艺设计的专用部件和夹具,组成的半自动或自动的专用机床。
机械类车床外文翻译
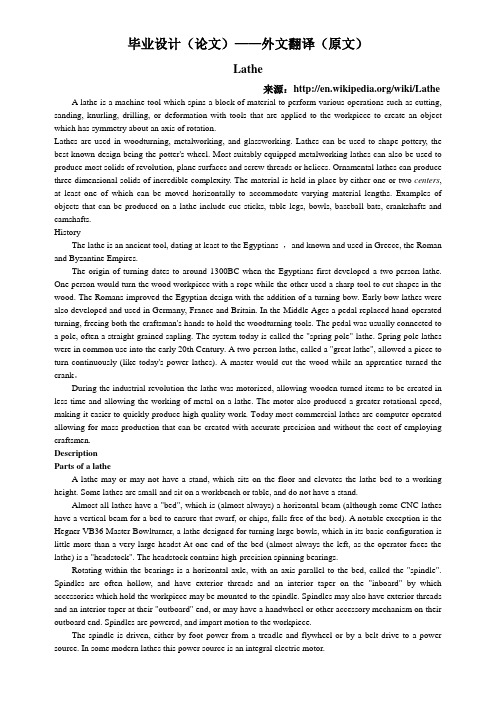
毕业设计(论文)——外文翻译(原文)Lathe来源:/wiki/LatheA lathe is a machine tool which spins a block of material to perform various operations such as cutting, sanding, knurling, drilling, or deformation with tools that are applied to the workpiece to create an object which has symmetry about an axis of rotation.Lathes are used in woodturning, metalworking, and glassworking. Lathes can be used to shape pottery, the best-known design being the potter's wheel. Most suitably equipped metalworking lathes can also be used to produce most solids of revolution, plane surfaces and screw threads or helices. Ornamental lathes can produce three-dimensional solids of incredible complexity. The material is held in place by either one or two centers, at least one of which can be moved horizontally to accommodate varying material lengths. Examples of objects that can be produced on a lathe include cue sticks, table legs, bowls, baseball bats, crankshafts and camshafts.HistoryThe lathe is an ancient tool, dating at least to the Egyptians ,and known and used in Greece, the Roman and Byzantine Empires.The origin of turning dates to around 1300BC when the Egyptians first developed a two-person lathe. One person would turn the wood workpiece with a rope while the other used a sharp tool to cut shapes in the wood. The Romans improved the Egyptian design with the addition of a turning bow. Early bow lathes were also developed and used in Germany, France and Britain. In the Middle Ages a pedal replaced hand-operated turning, freeing both the craftsman's hands to hold the woodturning tools. The pedal was usually connected to a pole, often a straight-grained sapling. The system today is called the "spring pole" lathe. Spring pole lathes were in common use into the early 20th Century. A two-person lathe, called a "great lathe", allowed a piece to turn continuously (like today's power lathes). A master would cut the wood while an apprentice turned the crank。
机床常见英语英汉对照

机床行业常见英语英汉对照(1):按英文字母排序3-Jaws indexing spacers 三爪、分割工具头A.T.C.system 加工中心机刀库Aluminum continuous melting & holding furnaces 连续溶解保温炉Balancing equipment 平衡设备Bayonet 卡口Bearing fittings 轴承配件Bearing processing equipment 轴承加工机Bearings 轴承Belt drive 带传动Bending machines 弯曲机Blades 刀片Blades,saw 锯片Bolts,screws & nuts 螺栓,螺帽及螺丝Boring heads 搪孔头Boring machines 镗床Cable making tools 造线机Casting,aluminium 铸铝Casting,copper 铸铜Casting,gray iron 铸灰口铁Casting,malleable iron 可锻铸铁Casting,other 其他铸造Casting,steel 铸钢Chain drive 链传动Chain making tools 造链机Chamfer machines 倒角机Chucks 夹盘Clamping/holding systems 夹具/支持系统CNC bending presses 电脑数控弯折机CNC boring machines 电脑数控镗床CNC drilling machines 电脑数控钻床CNC EDM wire-cutting machines 电脑数控电火花线切削机CNC electric discharge machines 电脑数控电火花机CNC engraving machines 电脑数控雕刻机CNC grinding machines 电脑数控磨床CNC lathes 电脑数控车床CNC machine tool fittings 电脑数控机床配件CNC milling machines 电脑数控铣床CNC shearing machines 电脑数控剪切机CNC toolings CNC刀杆CNC wire-cutting machines电脑数控线切削机Conveying chains 输送链Coolers 冷却机Coupling 联轴器Crimping tools 卷边工具Cutters 刀具Cutting-off machines 切断机Diamond cutters 钻石刀具Dicing saws 晶圆切割机Die casting dies 压铸冲模Die casting machines 压铸机Dies-progressive 连续冲模Disposable toolholder bits 舍弃式刀头Drawing machines 拔丝机Drilling machines 钻床Drilling machines bench 钻床工作台Drilling machines,high-speed 高速钻床Drilling machines,multi-spindle 多轴钻床Drilling machines,radial 摇臂钻床Drilling machines,vertical 立式钻床drills 钻头Electric discharge machines(EDM) 电火花机Electric power tools 电动刀具Engraving machines 雕刻机Engraving machines,laser 激光雕刻机Etching machines 蚀刻机Finishing machines 修整机Fixture 夹具Forging dies 锻模Forging,aluminium 锻铝Forging,cold 冷锻Forging,copper 铜锻Forging,other 其他锻造Forging,steel 钢锻Foundry equipment 铸造设备Gear cutting machines 齿轮切削机Gears 齿轮Gravity casting machines 重力铸造机Grinder bench 磨床工作台Grinders,thread 螺纹磨床Grinders,tools & cutters 工具磨床Grinders,ultrasonic 超声波打磨机Grinding machines 磨床Grinding machines,centerless 无心磨床Grinding machines,cylindrical 外圆磨床Grinding machines,universal 万能磨床Grinding tools 磨削工具Grinding wheels 磨轮Hand tools 手工具Hard/soft and free expansion sheet making plant 硬(软)板(片)材及自由发泡板机组Heat preserving furnaces 保温炉Heating treatment funaces 熔热处理炉Honing machines 搪磨机Hydraulic components 液压元件Hydraulic power tools 液压工具Hydraulic power units 液压动力元件Hydraulic rotary cylinders 液压回转缸Jigs 钻模Lapping machines 精研机Lapping machines,centerless 无心精研机Laser cutting 激光切割Laser cutting for SMT stensil 激光钢板切割机Lathe bench 车床工作台Lathes,automatic 自动车床Lathes,heavy-duty 重型车床Lathes,high-speed 高速车床Lathes,turret 六角车床Lathes,vertical 立式车床Lubricants 润滑液Lubrication Systems 润滑系统Lubricators 注油机Machining centers,general 通用加工中心Machining centers,horizontal 卧式加工中心Machining centers,horizontal & vertical 卧式及立式加工中心Machining centers,vertical 立式加工中心Machining centers,vertical double-column type 立式双柱加工中心Magnetic tools 磁性工具Manifolds 集合管Milling heads 铣头Milling machines 铣床Milling machines,bed type 床身式铣床Milling machines,duplicating 仿形铣床Milling machines,horizontal 卧式铣床Milling machines,turret vertical 六角立式铣床Milling machines,universal 万能铣床Milling machines,vertical 立式铣床Milling machines,vertical & horizontal 立式及卧式铣床Mold & die components 模具单元Mold changing systems 换模系统Mold core 模芯Mold heaters/chillers 模具加热器/冷却器Mold polishing/texturing 模具打磨/磨纹Mold repair 模具维修Molds 模具Nail making machines 造钉机Oil coolers 油冷却器Overflow cutting machines for aluminium wheels 铝轮冒口切断机P type PVC waterproof rolled sheet making plant P型PVC高分子防水PCB fine piecing systems 印刷电器板油压冲孔脱料系统Pipe & tube making machines 管筒制造机Planing machines 刨床Planing machines vertical 立式刨床Pneumatic hydraulic clamps 气油压虎钳Pneumatic power tools 气动工具Powder metallurgic forming machines 粉末冶金成型机Presses,cold forging 冷锻冲压机presses,crank 曲柄压力机Presses,eccentric 离心压力机Presses,forging 锻压机Presses,hydraulic 液压冲床Presses,knuckle joint 肘杆式压力机Presses,pneumatic 气动冲床Presses,servo 伺服冲床Presses,transfer 自动压力机Pressing dies 压模Punch formers 冲子研磨器Quick die change systems 速换模系统Quick mold change systems 快速换模系统Reverberatory furnaces 反射炉Rollers 滚筒Rolling machines 辗压机Rotary tables 转台Sawing machines 锯床Sawing machines,band 带锯床Saws,band 带锯Saws,hack 弓锯Saws,horizontal band 卧式带锯Saws,vertical band 立式带锯shafts 轴Shapers 牛头刨床Shearing machines 剪切机Sheet metal forming machines 金属板成型机Sheet metal working machines 金属板加工机Slotting machines 插床spindles 主轴Stamping parts 冲压机Straightening machines 矫直机Switches & buttons 开关及按钮Tapping machines 攻螺丝机Transmitted chains 传动链Tube bending machines 弯管机Vertical hydraulic broaching machine 立式油压拉床Vises 虎钳Vises,tool-maker 精密平口钳Wheel dressers 砂轮修整器Woven-Cutting machines 织麦激光切割机Wrenches 扳手(2):按中文拼音字母排序铝轮冒口切断机Overflow cutting machines for aluminium wheels离心压力机Presses,eccentric六角立式铣床Milling machines,turret vertical六角车床Lathes,turret螺栓,螺帽及螺丝Bolts,screws & nuts螺纹磨床Grinders,thread冷却机Coolers冷锻Forging,cold 冷锻冲压机Presses,cold forging立式双柱加工中心Machining centers,vertical double-column type立式铣床Milling machines,vertical立式油压拉床Vertical hydraulic broaching machine立式刨床Planing machines vertical立式车床Lathes,vertical立式带锯Saws,vertical band立式加工中心Machining centers,vertical立式及卧式铣床Milling machines,vertical & horizontal立式钻床Drilling machines,vertical联轴器Coupling连续溶解保温炉Aluminum continuous melting & holding furnaces连续冲模Dies-progressive链传动Chain drive切断机Cutting-off machinesCNC刀杆CNC toolings曲柄压力机presses,crank修整机Finishing machines舍弃式刀头Disposable toolholder bits润滑系统Lubrication Systems润滑液Lubricants熔热处理炉Heating treatment funaces三爪、分割工具头3-Jaws indexing spacers 伺服冲床Presses,servo输送链Conveying chains手工具Hand tools砂轮修整器Wheel dressers蚀刻机Etching machines外圆磨床Grinding machines,cylindrical搪磨机Honing machines搪孔头Boring heads卧式铣床Milling machines,horizontal卧式带锯Saws,horizontal band卧式加工中心Machining centers,horizontal 卧式及立式加工中心Machining centers,horizontal & vertical万能铣床Milling machines,universal万能磨床Grinding machines,universal镗床Boring machines弯曲机Bending machines弯管机Tube bending machines通用加工中心Machining centers,general铜锻Forging,copper铣头Milling heads铣床Milling machines无心磨床Grinding machines,centerless无心精研机Lapping machines,centerless压模Pressing dies压铸冲模Die casting dies压铸机Die casting machines油冷却器Oil coolers造链机Chain making tools造线机Cable making tools造钉机Nail making machines印刷电器板油压冲孔脱料系统PCB fine piecing systems摇臂钻床Drilling machines,radial硬(软)板(片)材及自由发泡板机组Hard/soft and free expansion sheet making plant辗压机Rolling machines液压元件Hydraulic components液压冲床Presses,hydraulic液压动力元件Hydraulic power units液压工具Hydraulic power tools液压回转缸Hydraulic rotary cylindersP型PVC高分子防水P type PVC waterproof rolled sheet making plant刨床Planing machines牛头刨床Shapers其他铸造Casting,other其他锻造Forging,other模芯Mold core模具Molds模具维修Mold repair模具打磨/磨纹Mold polishing/texturing模具单元Mold & die components模具加热器/冷却器Mold heaters/chillers磨轮Grinding wheels磨削工具Grinding tools磨床Grinding machines磨床工作台Grinder bench平衡设备Balancing equipment气油压虎钳Pneumatic hydraulic clamps气动冲床Presses,pneumatic 气动工具Pneumatic power tools轴shafts轴承Bearings轴承配件Bearing fittings轴承加工机Bearing processing equipment 肘杆式压力机Presses,knuckle joint铸铝Casting,aluminium铸铜Casting,copper铸造设备Foundry equipment铸钢Casting,steel铸灰口铁Casting,gray iron织麦激光切割机Woven-Cutting machines 重力铸造机Gravity casting machines重型车床Lathes,heavy-duty主轴spindles扳手Wrenches拔丝机Drawing machines保温炉Heat preserving furnaces插床Slotting machines齿轮Gears齿轮切削机Gear cutting machines冲压机Stamping parts冲子研磨器Punch formers超声波打磨机Grinders,ultrasonic车床工作台Lathe bench磁性工具Magnetic tools传动链Transmitted chains床身式铣床Milling machines,bed type带传动Belt drive带锯Saws,band带锯床Sawing machines,band电脑数控镗床CNC boring machines电脑数控弯折机CNC bending presses电脑数控铣床CNC milling machines电脑数控线切削机CNC wire-cutting machines电脑数控磨床CNC grinding machines电脑数控车床CNC lathes电脑数控电火花线切削机CNC EDM wire-cutting machines电脑数控电火花机CNC electric discharge machines电脑数控雕刻机CNC engraving machines 电脑数控机床配件CNC machine toolfittings电脑数控剪切机CNC shearing machines电脑数控钻床CNC drilling machines电动刀具Electric power tools电火花机Electric discharge machines(EDM) 雕刻机Engraving machines刀片Blades刀具Cutters倒角机Chamfer machines多轴钻床Drilling machines,multi-spindle锻铝Forging,aluminium锻压机Presses,forging锻模Forging dies仿形铣床Milling machines,duplicating粉末冶金成型机Powder metallurgic forming machines反射炉Reverberatory furnaces钢锻Forging,steel高速车床Lathes,high-speed高速钻床Drilling machines,high-speed管筒制造机Pipe & tube making machines滚筒Rollers工具磨床Grinders,tools & cutters攻螺丝机Tapping machines弓锯Saws,hack虎钳Vises换模系统Mold changing systems夹盘Chucks夹具Fixture夹具/支持系统Clamping/holding systems剪切机Shearing machines加工中心机刀库A.T.C.system激光切割Laser cutting激光雕刻机Engraving machines,laser激光钢板切割机Laser cutting for SMT stensil集合管Manifolds矫直机Straightening machines金属板成型机Sheet metal forming machines 金属板加工机Sheet metal working machines锯片Blades,saw锯床Sawing machines卷边工具Crimping tools 晶圆切割机Dicing saws精密平口钳Vises,tool-maker精研机Lapping machines可锻铸铁Casting,malleable iron快速换模系统Quick mold change systems 卡口Bayonet开关及按钮Switches & buttons钻石刀具Diamond cutters钻头drills钻模Jigs钻床Drilling machines钻床工作台Drilling machines bench自动压力机Presses,transfer金属切削metal cutting机床machine tool金属工艺学technology of metals刀具cutter摩擦friction联结link传动drive/transmission轴shaft弹性elasticity频率特性frequency characteristic误差error响应response定位allocation机床夹具jig动力学dynamic运动学kinematic静力学static分析力学analyse mechanics拉伸pulling压缩hitting剪切shear扭转twist弯曲应力bending stress强度intensity三相交流电three-phase AC磁路magnetic circles变压器transformer异步电动机asynchronous motor几何形状geometrical精度precision正弦形的sinusoid交流电路AC circuit机械加工余量machining allowance变形力deforming force变形deformation应力stress硬度rigidity热处理heat treatment退火anneal正火normalizing脱碳decarburization渗碳carburization电路circuit半导体元件semiconductor element反馈feedback发生器generator直流电源DC electrical source门电路gate circuit逻辑代数logic algebra外圆磨削external grinding内圆磨削internal grinding平面磨削plane grinding变速箱gearbox离合器clutch绞孔fraising绞刀reamer螺纹加工thread processing螺钉screw铣削mill铣刀milling cutter功率power工件workpiece齿轮加工gear mechining齿轮gear主运动main movement主运动方向direction of main movement进给方向direction of feed进给运动feed movement合成进给运动resultant movement of feed合成切削运动resultant movement of cutting 合成切削运动方向direction of resultant movement of cutting切削深度cutting depth前刀面rake face刀尖nose of tool 前角rake angle后角clearance angle龙门刨削planing主轴spindle主轴箱headstock卡盘chuck加工中心machining center车刀lathe tool车床lathe钻削镗削bore车削turning磨床grinder基准benchmark钳工locksmith锻forge压模stamping焊weld拉床broaching machine拉孔broaching装配assembling铸造found流体动力学fluid dynamics流体力学fluid mechanics加工machining液压hydraulic pressure切线tangent机电一体化mechanotronics mechanical-electrical integration气压air pressure pneumatic pressure稳定性stability介质medium液压驱动泵fluid clutch液压泵hydraulic pump阀门valve失效invalidation强度intensity载荷load应力stress安全系数safty factor可靠性reliability螺纹thread螺旋helix键spline销pin滚动轴承rolling bearing滑动轴承sliding bearing弹簧spring制动器arrester brake十字结联轴节crosshead联轴器coupling链chain皮带strap精加工finish machining粗加工rough machining变速箱体gearbox casing腐蚀rust氧化oxidation磨损wear耐用度durability随机信号random signal离散信号discrete signal超声传感器ultrasonic sensor集成电路integrate circuit挡板orifice plate残余应力residual stress套筒sleeve扭力torsion冷加工cold machining电动机electromotor汽缸cylinder过盈配合interference fit热加工hotwork摄像头CCD camera倒角rounding chamfer优化设计optimal design工业造型设计industrial moulding design有限元finite element滚齿hobbing插齿gear shaping伺服电机actuating motor铣床milling machine钻床drill machine镗床boring machine步进电机stepper motor丝杠screw rod导轨lead rail组件subassembly可编程序逻辑控制器Programmable Logic Controller PLC电火花加工electric spark machining电火花线切割加工electrical discharge wire - cutting相图phase diagram热处理heat treatment固态相变solid state phase changes有色金属nonferrous metal陶瓷ceramics合成纤维synthetic fibre电化学腐蚀electrochemical corrosion车架automotive chassis悬架suspension转向器redirector变速器speed changer板料冲压sheet metal parts孔加工spot facing machining车间workshop工程技术人员engineer气动夹紧pneuma lock数学模型mathematical model画法几何descriptive geometry机械制图Mechanical drawing投影projection视图view剖视图profile chart标准件standard component零件图part drawing装配图assembly drawing尺寸标注size marking技术要求technical requirements刚度rigidity内力internal force位移displacement截面section疲劳极限fatigue limit断裂fracture塑性变形plastic distortion脆性材料brittleness material刚度准则rigidity criterion垫圈washer垫片spacer直齿圆柱齿轮straight toothed spur gear斜齿圆柱齿轮helical-spur gear直齿锥齿轮straight bevel gear运动简图kinematic sketch齿轮齿条pinion and rack蜗杆蜗轮worm and worm gear虚约束passive constraint曲柄crank摇杆racker凸轮cams共轭曲线conjugate curve范成法generation method定义域definitional domain值域range导数\\微分differential coefficient求导derivation定积分definite integral不定积分indefinite integral曲率curvature偏微分partial differential毛坯rough游标卡尺slide caliper千分尺micrometer calipers攻丝tap二阶行列式second order determinant逆矩阵inverse matrix线性方程组linear equations概率probability随机变量random variable排列组合permutation and combination气体状态方程equation of state of gas动能kinetic energy势能potential energy机械能守恒conservation of mechanical energy动量momentum桁架truss轴线axes余子式cofactor逻辑电路logic circuit触发器flip-flop脉冲波形pulse shape数模digital analogy液压传动机构fluid drive mechanism机械零件mechanical parts淬火冷却quench 淬火hardening回火tempering调质hardening and tempering磨粒abrasive grain结合剂bonding agent砂轮grinding wheel舍弃式刀头Di osabletoolholderbits润滑系统Lubricatio ystems润滑液Lubricants熔热处理炉Heatingtreatmentfunaces三爪、分割工具头3-Jawsindexing acers伺服冲床Pre es,servo输送链Conveyingchai手工具Handtools砂轮修整器Wheeldre ers蚀刻机Etchingmachines外圆磨床Grindingmachines,cylindrical搪磨机Honingmachines搪孔头Boringheads卧式铣床Millingmachines,horizontal卧式带锯Saws,horizontalband卧式加工中心Machiningcenters,horizontal 卧式及立式加工中心Machiningcenters,horizontal&am amp amp vertical万能铣床Millingmachines,universal万能磨床Grindingmachines,universal镗床Boringmachines弯曲机Bendingmachines弯管机Tubebendingmachines通用加工中心Machiningcenters,general铜锻Forging,co er铣头Millingheads铣床Millingmachines无心磨床Grindingmachines,centerle无心精研机La ingmachines,centerle压模Pre ingdies压铸冲模Diecastingdies压铸机Diecastingmachines油冷却器Oilcoolers造链机Chainmakingtools弯管机Tubebendingmachines通用加工中心Machiningcenters,general铜锻Forging,co er铣头Millingheads铣床Millingmachines无心磨床Grindingmachines,centerle无心精研机La ingmachines,centerle压模Pre ingdies压铸冲模Diecastingdies压铸机Diecastingmachines油冷却器Oilcoolers手工具Handtools砂轮修整器Wheeldre ers蚀刻机Etchingmachines外圆磨床Grindingmachines,cylindrical搪磨机Honingmachines搪孔头Boringheads卧式铣床Millingmachines,horizontal卧式带锯Saws,horizontalband卧式加工中心Machiningcenters,horizontal 卧式及立式加工中心Machiningcenters,horizontal&am amp amp vertical万能铣床Millingmachines,universal万能磨床Grindingmachines,universal镗床Boringmachines修整机Finishingmachines舍弃式刀头Di osabletoolholderbits润滑系统Lubricatio ystems润滑液Lubricants熔热处理炉Heatingtreatmentfunaces三爪、分割工具头3-Jawsindexing acers伺服冲床Pre es,servo输送链Conveyingchai手工具Handtools砂轮修整器Wheeldre ers蚀刻机Etchingmachines外圆磨床Grindingmachines,cylindrical搪磨机Honingmachines搪孔头Boringheads卧式铣床Millingmachines,horizontal卧式带锯Saws,horizontalband卧式加工中心Machiningcenters,horizontal 卧式及立式加工中心Machiningcenters,horizontal&am amp amp vertical万能铣床Millingmachines,universal 万能磨床Grindingmachines,universal 镗床Boringmachines弯曲机Bendingmachines弯管机Tubebendingmachines常见数控机床参数英语词汇AC 交流电AMP 安培APC 自动托盘交换装置APL 自动部件装载机ASCII 美国信息交换标准法规ATC 自动刀具交换装置ATC FWD 自动刀具交换装置前进ATC REV 自动刀具交换装置后退AWG 美国线规BHCS 圆头帽螺钉CAD 计算机辅助设计CAM 计算机辅助制造(辅助加工)CB 断路开关CC 立方厘米CCW 逆时针CFM 每分钟立方英尺CNC 计算机数控CNCR SPINDLE 与轴运动同步的芯轴CRC 循环冗余码校验数字CRT 阴极射线管CTS 清除发送CW 顺时针DB 牵引杆DC 直流电DGNOS 诊断DHCP 动态主机配置协议DIR 目录DNC 直接数字控制DOS 磁盘操作系统DTE 数据终端设备ENA CNVR 启动输送机EOB 块结束EOF 文件结束EPROM 可擦可编程只读存储器E-STOP 紧急停机FADAL 其他人FHCS 平头帽螺钉FT 英尺FU 保险丝FWD 前进GA 量规HAAS 正确的刀具HHB 六角头螺钉HP 马力HS 卧式系列加工中心ID 内径IGBT 隔离栅双极晶体管IN 英寸IOPCB 输入输出印刷电路板LAN 局域网LB 磅LED 发光二极管LO CLNT 冷却剂低压LOW AIR PR 低气压LVPS 低电压电源MB 兆字节(1百万)MCD RL Y BRD M-代码继电器盘MDI 手动数据输入MEM 存储器M-FIN M-代码完成MM 毫米MOCON 电动机控制器MOTIF 电动机接口MSG 信息MSHCP 公制插座帽螺钉NC 数字控制NC 常闭合NO 常开OD 外径OPER 操作员P 袋PARAM 参数PCB 印制电路板PGM 程序POR 通电复位POSIT 位置PROG 程序PSI 每平方英寸磅PWM 脉冲宽度调制RAM 随机存取存储器REPT RIG TAP 围盘轧制刚性螺丝攻RET 返回,回车REV CNVR 回动输送机RJH 遥控摇柄RPDBDN 旋转式托盘拉杆放下RPDBUP 旋转式托盘拉杆提起RPM 每分钟转数RIS 请求输送RXD 接收数据S 芯轴转速SDIST 伺服机构分配印制电路板SFM 每分钟平方英尺SHCS 套筒扳手头帽螺钉SIO 串行输入/输出SKBIF 串行键盘接口印制电路板SMTC 侧挂式刀具交换装置SP 芯轴T 刀具编号TC 刀具交换装置TIR 总指示偏转TNC 刀尖偏差TRP 刀具释放活塞IS 尾架ISC 通过芯轴的冷却剂TXD 发送数据VDI 德国工程师协会VF 立式铣床(第一台)VF-E 立式铣床-扩展型VMC 立式加工中心WAN 广域网。
- 1、下载文档前请自行甄别文档内容的完整性,平台不提供额外的编辑、内容补充、找答案等附加服务。
- 2、"仅部分预览"的文档,不可在线预览部分如存在完整性等问题,可反馈申请退款(可完整预览的文档不适用该条件!)。
- 3、如文档侵犯您的权益,请联系客服反馈,我们会尽快为您处理(人工客服工作时间:9:00-18:30)。
中文2805字出处:Proceedings of International Conference on. IEEE, 1996: 250-260毕业设计(论文)外文资料翻译系部:机械工程系专业:机械工程及自动化姓名:学号:外文出处:Design of the DistributedArchitecture of aMachine-tool附件: 1.外文资料翻译译文;2.外文原文。
指导教师评语:签名:年月日分布式机床的设计FIP现场总线的用途Daping SONG, Thierry DIVOUX,费朗西斯勒帕热自动化中心研究所的Nancy摘要:本文中我们基于FIP现场总线上提出了一种分布式控制系统。
它将取代传统的CNC(计算机数字控制装置)用于机床上。
该系统是由一套以微处理机为基础的模块(PC机、运动控制器、I/O接口) 利用FLP实时网络相互联接的。
这主要是使每个模块智能化以提高整个系统的灵活性和容错能力。
每个模块都是一个分控系统,用于实现自己的分控任务,其中有些模块用于运动控制,另一些模块用于传感器评价和执行器调节。
FIP决定了这些模块之间的通讯(信息交流和同步),同时执行任务分配以及设备布局分布。
我们讨论一些分布标准并描述实验的执行。
1.引言近几年,一直对分布式体系结构进行了许多研究。
分布式体系结构在系统集成上发挥主要作用。
在机床控制域,目前CNC技术有它内在的缺点。
将几根固定数量的轴容入CIM环境中是非常费时,灵活和不易的。
超大规模集成电路微处理器技术和通信网络的迅速发展使分布式控制成为可能。
虽然逐步扩展没有完全替代硬件更换但分布式控制系统的性能,模块化,完整性和可靠性正在提高。
它为替代控制系统架构提供了一个很好的前景。
本文致力于对分布式机床结构的研究。
它建立在智能设备与通信相联系的基础上。
分布式机床的特点是分布式任务和分布式数据,且具有独特的控制方法。
它是结合标准设备和FIP系统总线设计而成,通过实验证明该系统具有可执行性,在实验中该系统控制了复合轴系,成功执行坐标之间的关系同时也反应了对传感器值的变化。
该论文结构如下:第2部分描述了机床控制系统构架。
第3部分简要介绍了FIP 现场总线。
第4部分概述了我们实验的实施。
最后,我们在第5部分总结了一些一般性意见和今后的研究前景。
2.机床控制系统架构该机床控制系统是一个实时多任务系统。
其功能结构如图1所示。
它包括三种单元:用户接口/ 监控单元/规划单元,伺服单元,传感器/制动器单位。
这个系统的主要功能是用来控制工件的加工。
它包括两个不同的和相关的任务: ● 为了确保轨迹的准确性和对机床移动部件的速度控制● 为了调查定位(跟踪)过程的正确执行,环境变化的影响与指定操作的执行或机床机件的运动同样重要。
例如:工具开关,冷却,润滑等。
CAM 的制造日期图1:架构功能 按时间顺序,这项任务也可分为两个步骤:规划控制程序规划和执行控制程序。
第一步,机床机件没有直接的方向,只有运动和被指定执行的操作,这是“数据采集和预处理”的一步。
虽然在第二步,是控制的有效执行。
值得指出的是:在第二步由于多任务的性质,并行处理是可行的。
3.FIP 现场总线FIP 系统被用来满足分布式机床上实时通信的需要。
在这一节中,我们简要地解释一下FIP 系统的技术性能。
FIP (工厂仪表协议)是网络系统用于传感器的驱动器和控制设备如PLCS ,CNCS 或机器人控制器之间的信息交换。
FIP 系统的结构采用所谓的密封性以减少OSI 模型(物理层,数据链路层和应用层),这种结构使实时通信和常规的信息沟通之间有明显的区别。
在数据链路层中,相关服务一方面与其他传递信息服务可变转让。
在应用层中,我们可区分工作规划/编程(轨迹,工具的选择,其他加工参数采集) 基本替换计算 轴伺服控制系统 机床构件 传感器/制动器环境自动安全监测加工MPS服务(制造周期/非制造性规范),它采用来自数据链路层的信息设备所支持的MMS设备。
FIP支持两个传输媒体:屏蔽双绞线和光纤。
FIP允许各种各样的布局,最长部分可达500米,至少有4个部分被中继器代替。
3种比特率被确定为:31.25k.比特/秒,1兆位/秒和2.5兆位/秒。
FIP介质访问控制是集中的。
所有转让都由the Bus Arbiter控制,时间安排转移必须遵守时间要求。
变量和信息之间的传递可采用定期配置或根据站的要求来转让,而在我们的应用中,FIP只采用可变转让。
FIP采用生产者和消费者的模样来产生可变交流。
变量对于生产者和消费者而言,是被确定的一个独特的识别标志,一套制作和消费变量可以集结在一个站,但是这些识别标志不涉及任何物理地址站。
图2显示了变化信息。
广播的BA标识符认识的人 P和一些消费者ç生产者发出的日期 P所有消费者接受的数据 C图2:FIP系统的MAC图象首先,the Bus Arbiter 广播持有可变的标示符,所有的节点接受帧并检查变数是生产还是消费产生的或不给予影响。
第三步:作为生产者的站必须响应包含数据的帧。
第四步:获取消费者的变化价值并存储。
当更新产生时,消费者和生产者便形成了。
FIP有两种类型的数据交流:周期性和非周期性的。
在这两种情况下,汇率发生情况如上图(图2)。
在第一种情况下,the Bus Arbiter根据从配置要求价值相应的标识定期转移。
第二种情况下,the Bus Arbiter 可根据现有的带宽产生转让请求信号。
在我们的应用中,实时的限制是非常严格的。
为了使机床遵守给定的轨迹,轴的控制必须同步。
这就要求和网络连接的控制节点应该同时接受开始命令,因此网络必须播出命令。
为了确保相同的瞬时命令能同时被几个接受器接受,稳定的传输是非常必要的。
因此,一些传感器例如运动控制传感器就应该要求定期调查限位开关以使网络能定期无重大延误的传输数据。
一句话,像分布式机床的操作,像数据广播的要求,时间和空间的一致性,定期传输不能满足任何一般用途的网络。
然而,实时网络例如FIP就是数据一种好的解决方法。
4.实验实施如图3所示,我们的应用目标是要实现一个分布式的两轴机床控制系统。
它由以下设备分布在FIP总线的四个节点上。
节点1:微机(i80486 微处理器)。
它作为运营商终端。
节点2.3:两个相同的节点。
每个均由微机(i80486)配备了运动控制器(克莱斯勒PCIOO + 克莱斯勒三菱商事100)。
节点4:一个带有传感器/制动器作为辅助业务的可编程控制器(低温100)。
网络:FIP和1比特/秒的双绞线介质间的选择。
软件架构的执行系统是基于概念的多层次分布式控制。
它有三种层次结构,其中第二和第三层次可实现分配。
它包括以下层次:分析层:控制任务的执行选择它被映射到微机的提供用户界面的节点上。
用来处理计划收购和储存,不同业务模式(手动和自动模式)的交换,起始点和终点以及其它各节点之间的计算和发送。
惯例层:确定某一任务的控制算法它被映射到2种其他微机上(节点2和节点3)。
这两种微机具有根据给定的参数和命令(轨迹类型,速度,加速度等)进行基本位移计算(插补)的功能。
每个轴的插补算法是软件设计的困难之一,因为轴控制分布后,每个中间坐标轴的计算是独立的。
正确的算法设计可保证这些轴的连贯性。
工艺层:执行控制它包含两种运动:运动控制器和可编程控制器。
这些设备执行伺服系统运动控制,处理加工件的举行/紧缩政策,传感器的评定和驱动器的调节使工具切换任务和监控系统更安全。
为了验证拟议的架构是否与时间限制和网络能力相适应,预期流量的估计是必要的。
主要有两种性质的信息交流:●命令从中央决定站(节点)传到其它站。
●统计信息由站(节点)与站之间产生。
例如:在我们的实验平台上,一些变数分布如下:FIP系统节点1节点2 节点4 节点3FIP系统 FIP系统运动控制运动控制传感器和制动器X轴 Y轴图3:硬件执行5.结论本文中为满足CIM的要求,我们的研究通过实验实施进一步达到审定。
我们现在正致力于用来证明符合执行实时限制的经营架构的仿真和性能分析的工作。
我们的目标不仅是一个试样样机,更是研究设计、优化的分布式系统理论方案的发展。
Design of the Distributed Architecture of a Machine-toolUsing FIP FieldbusDaping SONG, Thierry DIVOUX, Francis LEPAGECentre de Recherche en Automatique de NancyUniversite de Nancy I, BP239, 54506 Vandoeuvre-les-Nancy cedex, France Abstract: In this paper we propose a distributed control system based on FIP fieldbus. It is applied to machine-tool as a replacement for the traditional CNC (Computerized Numerical Controller). The system is composed of a set of microprocessor-based modules (PCs, motion controllers, I/OS, . ..) interconnected by FLP real-time network. The main idea is to enable each module to be intelligent, improving thus the flexibility and the fault tolerant capability of the whole system. Each module being a sub-control system, accomplishes its own control task, some of them for motion control and others for evaluating sensors and regulating actuators. The communication (information exchanges and synchronization) among these modules is ensured by FLP. This system allows both task distribution as well as equtpment topological distribution. We discuss some distribution criteria and describe an experimental implementation.1. IntroductionDistributed system architecture has been the subject of many research activities in recent years. It plays a major role in systems integration. In the machine-tool control domain, present CNC technology has its inherent shortcomings. It is centralized, limited to a fixed number of axis time-consuming, inflexible and difficult to be integrated in CIM environment. The rapid development of VLSI microprocessor technology and communication network enables the distributed control to be considered. Distributed control systems present the advantage of improving performance, modularity, integrity and reliability while allowing incremental expansion without complete hardware replacement. It offers a promising alternative to control system architecture.This paper is dedicated to study a distributed machine-tool architecture. It is based on intelligent devices interconnected on communication link. It is characterized by distributed tasks and distributed data, but with unique control access system. It isdesigned by using standard devices and FIP fieldbus and verified by a experimental implementation, in which the system controls a multi-axis machine to successfully execute a coordinated motion as well as to respond to sensors values changes.The paper is organized as follows. In section 2, the machine-tool control system architecture is described. Section 2 gives a brief description of FIP and Section 3 outlines our experimental implementation. We conclude in section 4 with some general remarks and future research perspectives.2. Machine-tool control system architectureThe machine-tool control system is a real-time and multitask system. Its classical functional architecture is shown in Fig.1. It consists of three units: userinterface/supervisiou/programming unit, servo unit, and sensors/actuators unit. The main mission of this system is to control workpart machining. It includes two different and related tasks aspects:●to ensure the precise trajectory and speed control of the mobile organs of machine-tool.●to survey the correct execution of this positioning (tracking) process, to react on environment changes as well as to perform the specified operations or actions upon machine-tool mechanics. such as tool switching, cooling, lubricating, etc.Fig. 1 Functional architectureChronologically, this mission is also divided into two steps: control program planning and control program executiug. In the first step, there is no direct action onmachine-tool multitask nature: “data acquisition and preprocessing” step. While in the second step, the control is effectively executed. It is worth to note that in the second step, the parallelization is possible due to the mechanics, only the motions as well as the operations to be performed are specified. This is the “data acquisition and preprocessing” step. While in the second step, the control is effectively executed. It is worth to note that in the second step, the parallelization is possible due to the multitask nature.3.FIP fieldbusTo meet the real-time communication need in our distributed machine-tool, FIP is adopted. In this section, we briefly explain the main technical properties of FIP.FIP (Factory Instrumentation Protocol) is an industrial network designed for the exchange of information between sensors, actuators and control devices such as PLCs, CNCs or robotcontrollers. The architecture of FIP follows the so-calkd reduced OS1 model (Physicallayer, Data link layer and Application layer). This architecture makes a cleardistinction between real-time communication and conventional message communication. At Data Link layer, there are services associated to variable transfers on the one hand and conventional messaging services on the other hand. At Application layer, we distinguish the MPS (Manufacturing Periodic/aperiodic Specification) services which use variable transfers of Data Link layer from the MMS services which are supported by the messaging services of the Data Link layer.FlP supports two transmission media: shielded twisted pair and optical fiber. It allows for a wide variety of topologies. The maximum length of a segment is 500 m ;and at most 4 segmentsare authorized with repeaters. Three bit rates have been defined: 31.25 K.bit/s, 1 Mbit/s and 2.5 Mbit/s.FIP medium access control is centralized. All transfers are under control of the Bus Arbiter that schedules transfers to comply with timing requirements. Transfers of variables and messages may take place periodically according to system configuration or aperiodicalIy under request from any station. In our application, only variable transfer of FIP is used.For variable exchanges, FIP uses the producer-consumer model. …Variables ar e identified by a unique identifier known from the producer and the consumers. A set of produced and consumed variables can be regrouped in one station, but the identifier is not related to any physical address of stations. Fig. 2 shows the broadcast of a variable.Fig2 Principle of MAC protocol of FIPFirst, the Bus Arbiter broadcasts a frame that holds the identifier of the variable. All nodes receive the frame and check whether they are producer or consumer of the variable or not concerned. In a third step, the station that recognizes itself as the producer replies with a response frame that contains the data. In a fourth step, all the consumers of this variable capture the value and store it. The consumers and the producer are formed when the update takes place.FlP defines two types of data exchanges: periodic and aperiodic. In both cases, the exchange takes place as indicated above (Fig. 6). In the first case, the Bus Arbiter knows from the configuration that it has to request periodically the transfer of the value corresponding to an identifier. In the second case, transfer requests are signaled to the Bus Arbiter that will serve them according to the available bandwidth.For our application, the real-time constraints are very stringent. To make themachine-tool to follow an accurate trajectory, the control of the axis must besynchronized. This requires that the control nodes connected by a network should simultaneously receive the starting order, so the network should be able to broadcast orders. To ensure that an order of the same instant is received by several receivers, a spacec onsistency statue is also necessary. For responsiveness reason, some sensors like movement-limit switches should be polled periodically requiring that the network be able to transmit periodic data without important delays.In one word, for an application like distributed machine-tool, the requirements like broadcast of data , the time and space consistencies, the periodic transmission can not be met by any general-purpose networks, a real-time network like FIP is then a good solution.4. Experimental implementationAs shown in Fig. 3, our application is aiming to realize a distributed two-axis machine-tool control system. It is composed of the following devices distributed on four nodes over FIP fieldbus:node1: a microcomputer (i80486 microprocessor). It is used as operator terminal,node 2. 3: two identical nodes. Each consists of a microcomputer (i80486) equipped with a motion controller (DCX PClOO+DCX MC 100).node 4: a PLC (LT 100) with sensors/actuators for auxiliary operations.network: FIP with 1Mbits/s over twisted pair medium is chosen.The software architecture of the implemented system is based on the concept of multilayered distributed control. It has a three-level hierarchy and the distribution is realizes at the second and the third levels. It consists the following layers:Analysis layer: performs selection of the control tasksIt is mapped on to the microcomputer of node 1 which provides an user interface. It deals with the program acquisition and storage, switches the different operational modes (manual and automatic modes), computes and sends the start and arrival points coordinates as well as other orders to each other node respectively.Rule layer: determines the control algorithms for a given task.It is mapped on to the two other microcomputers (node 2 and 3) which functionis elementary displacements calculation (by interpolation) according to the given parameters and orders ( trajectory type, speed, acceleration,. etc.).One of the software design difficulties is the interpolation algorithms for each axis. Because after axis control distribution, the calculation of the intermediate coordinates of each axis becomes independent, the coherence of these axis should be ensured by correct algorithm design.Process layer: executes the control.It includes the two motion controllers and the PLC. These devices executes servo systemmotion control, handles the workpart holding/tightening, tools switch tasks and monitors system safety by evaluation of sensors and regulation of actuators.In order to verify if the proposed architecture is suitable with time constraints and network capacity, in is necessary to estimate the expected traffic.There are mainly two natures of information exchanges:●orders from central decision station (node 1) to other stations.●state information produced by the stations ( node1) to other stations.For example concerning our experimental platform, we have delined some variables distributed as following:Fig3 Hardware implementation5. Conclusionln this paper, we investigated a distributed machine-tool architecture in order to meet CIM requirements. Our research reached the step of validation through the realization of anexperimental implementation. We currently work on the simulation and performance analysis of the operating architecture to justify that the implementation meetsreal-time constraints. Our objectiveis not only an experimental prototype, but also the development of the theoreticalmethodology for the design, optimization of this distributed system.。