装配过程审核检查表
过程审核检查表示例(20200807032740).pdf

是否建立项目组织机构(项目管理),并为项目管理以及团队成员确定了各自的任务及权限1、在APQP控制程序里建立了项目管理的流程,确定了项目组成员职责是否为落实项目规划了必要的资源,相关的资源是否已经到位,并且说明了变更情况1、在新设备、工装清单上明确了有关顾客对产品追溯性要求所请购的喷码机;是否已经编制了一份项目计划表,并且与客户进行了协商沟通?1、编制了项目计划,具体的项目时间没有得到有效实施,没有严格按照项目进度更新项目计划的时间安排。
2、样品阶段的交期变更(例如产品的解冻试验未通过顾客要求),与顾客进行了沟通,但没有及时更新后续项目计划目前项目计划处于第三阶段,但未对各阶段展开评价,未确认各阶段项目的落实情况。
按照XX公司客户项目的进展,更新项目计划,重新评审项目计划工程部10/30项目管理机构是否可以在项目进行过程中提供可靠的变更管理?目前所有的产品结构,外观变更均通知顾客并得到批准,同时对变更后的结果进行了验证关闭。
对于涉及变更SOP的,应及时编制更改组织内部以及客户相关负责人是否已经纳入变更管理?1、查《工程变更控制程序》和《事态升级控制程序》能清晰规定变更的流程和事态升级的流程,对设计顾客和供应商的变更也会及时通知。
是否为项目编制了一份质量管理计划,该计划是否得到落实,落实情况是否被定期监查看APQP项目文件记录,看到在第一阶段编制了《产品质量保证计划》和在后续阶段里编制了产品生产的控制计控?划。
是否建立了事态升级过程,该过程是否得到有效的落实?建立了《事态升级控制程序》,其中描述了产品设计开发过程中涉及的事态升级的流程针对具体产品和过程的要求是否已经到位?1、建立了《合同评审控制程序》,明确了识别顾客要求的流程,建立了顾客特殊要求清单;但未能识别该产品有关的法规、技术规范要求收集有关产品的法律法规和行业规范,并作为外来文件进行管理业务部11/1* 在得到产品和过程要求的基础上,是否从总体上对可制造性开展了评价?1、根据以上识别的产品和过程要求清单,项目组展开了产品设计可行性分析、制造可行性分析。
过程审核检查表范例
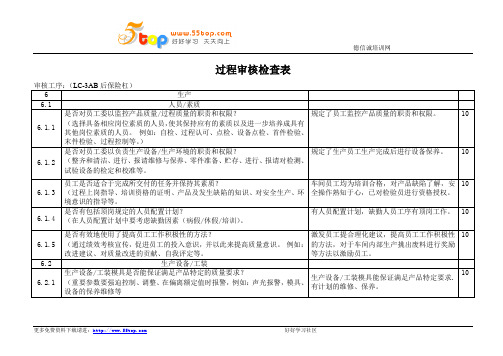
德信诚培训网过程审核检查表6 生产6.1 人员/素质6.1.1 是否对员工委以监控产品质量/过程质量的职责和权限?(选择具备相应岗位素质的人员,使其保持应有的素质以及进一步培养成具有其他岗位素质的人员。
例如:自检、过程认可、点检、设备点检、首件检验、末件检验、过程控制等。
)规定了员工监控产品质量的职责和权限。
106.1.2 是否对员工委以负责生产设备/生产环境的职责和权限?(整齐和清洁、进行、报请维修与保养、零件准备、贮存、进行、报请对检测、试验设备的检定和校准等。
规定了生产员工生产完成后进行设备保养。
106.1.3 员工是否适合于完成所交付的任务并保持其素质?(过程上岗指导、培训资格的证明、产品及发生缺陷的知识、对安全生产、环境意识的指导等。
车间员工均为培训合格,对产品缺陷了解,安全操作熟知于心,已对检验员进行资格授权。
106.1.4 是否有包括顶岗规定的人员配置计划?(在人员配置计划中要考虑缺勤因素(病假/休假/培训)。
有人员配置计划,缺勤人员工序有顶岗工作。
106.1.5 是否有效地使用了提高员工工作积极性的方法?(通过绩效考核宣传,促进员工的投入意识,并以此来提高质量意识。
例如:改进建议、对质量改进的贡献、自我评定等。
激发员工提合理化建议,提高员工工作积极性的方法,对于车间内部生产挑出废料进行奖励等方法以激励员工。
106.2 生产设备/工装6.2.1 生产设备/工装模具是否能保证满足产品特定的质量要求?(重要参数要强迫控制、调整、在偏离额定值时报警,例如:声光报警,模具、设备的保养维修等生产设备/工装模具能保证满足产品特定要求.有计划的维修、保养。
106.2.2 在批量生产使用的检测、试验设备是否能有效地监控质量要求?(测量精度/检具能力调查、数据采集和分析、检具检定的证明等检测、试验设备能有效地监控质量要求. 106.2.3 生产工位、检验工位是否符合要求?(工作环境条件(包括返工/返修工位)必须符合于产品及工作内容,以避免污染、损伤、混批、说明错误。
VDA6.3过程审核检查表
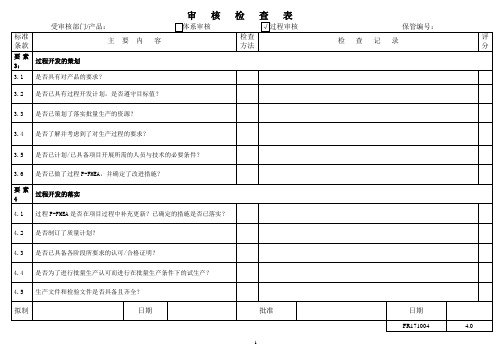
受审核部门/产品:
体系审核
标准 条款
主要内 容
6.1.1 是否对员工委以监控产品质量/过程质量的职责和权限?
检查表
√ 过程审核 检查 方法
6.1.2 是否对员工委以负责生产设备/生产环境的职责和权限?
6.1.3 员工是否适合于完成所交付的任务并保持其素质?
6.1.4 是否有包括顶岗规定的人员配置计划?
的改进措施?
5.6
是否对顾客提供的产品执行了与顾客商定的方法?
5.7
原材料库存(量)状况是否适合于生产要求?
5.8
原材料/内部剩余材料是否有合适的进料和储存方法?
5.9
员工是否具有相应的岗位培训?
要素 6 生产
分要素
6.1
人员/素质
拟制
日期
批准
2
保管编号:
检查记录
评 分
日期
FR171004
4.0
审核
6.1.5 是否有效地使用了提高员工工作积极性的方法?
分要素
6.2
生产设备/工装
6.2.1 生产设备/工装模具是否能满足产品特定的质量要求?
6.2.2 在批量生产中使用的检测、实验设备是否能有效地监控质量要求?
6.2.3 生产工位、检验工位是否符合要求?
6.2.4 生产文件和检验文件中是否标出所有的重要技术要求并坚持执行?
对已批量供货的产品是否具有所要求的批量生产认可并落实了所要求的对已批量供货的产品是否具有所要求的批量生产认可并落实了所要求的对已批量供货的产品是否具有所要求的批量生产认可并落实了所要求的改进措施
受审核部门/产品:
标准 条款
主要内 容
要素 过程开发的策划
3:
2016版VDA6.3过程审核检查表
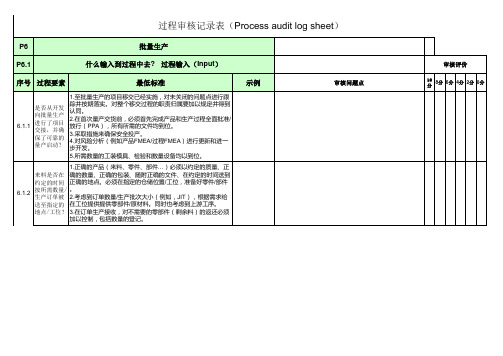
是否对原材 污染。仓储区/加工区/容器必须达到零部件/产品所需的必要的
料进行适当 整洁/清洁要求。要定义清洁周期,并且加以监控。
的仓储,所 3.加工工位/装配线上的零部件/物料的供应必须便与安全操作
6.1.3
使用的运输 。 工具/包装设 4.必须通过合适的方法,监控为特殊材料/零部件规定的仓储时
备是否适合 间以及使用有效期(最长、最短仓储时间,规定的中间临时仓
量要求? 性有影响的测量装置的校准。
4.对于影响到测量结果合试验的附属装置,要采取同样的方式
加以监控。
加工工位和
6.4.4
检验工位是 否满足具体
要求?
1.加工工位及周边布置的条件环境适合于生产操作和产品的要 求,从而可以预防或避免污染、损伤、混料。 2.这也适用于临时的和永久的返工返修、拣选、检验工位。 3.除此以外,还根据具体的工作任务,在人机工程学的基础上 对加工工位设计进行了调整。
P6.2
工作内容/过程流程(所有生产过程是否受控?)
控制计划里 的要求是否 6.2.1* 完整,并且 得到有效实 施?
1.基于控制计划的生产和检验文件完备。其中必须对检验文件 、检验设备、检验方法、检验频度/周期、重新评定等加以规 定。 2.这些文件必须随时可获取。 3.对于影响到产品特性/质量的过程参数必须加以完整地描述。 过程参数和检验特性必须带有公差。 4.在过程控制图上规定控制限,控制限可探测、可追溯。 5.针对过程要求和检验特性,要对发现的不符合项以及启动的 措施加以记录。 6.对过程异常所要采取的措施(反应计划),相关责任人必须 清楚,实施措施并加以记录。 7.如产品对生产工艺有特殊要求,那么相关的机器/工装/辅助 设备的参数数据要在控制计划和/或生产检验文件中加以规定 。 8.详细规定返工条件,并且在过程中加以保障(零部件标识, 重新检验)
过程审核检查表

按VDA6.3编制的过程审核检查表批准:审核:编制:莱州市金雁机械制造有限公司2006/12/15发布 2007/01/01实施过程审核检查表使用说明审核检查表是过程审核员进行审核的依据。
在进行具体审核时审核员可以完全采用,也可从中选择一部分或增加一些提问,但是必须保持所要求的结构。
在过程审核时应优先从产品的角度来观察所审核的过程,因为过程对产品的影响特别重要。
公司产品实现过程不包括产品开发和产品设计,故对VDA6.3《过程审核》的A部分:《产品诞生过程》的要素1《产品开发的策划》、要素2《产品开发的落实》予以删减,列出要素1与要素2,是为了与标准保持一致。
审核检查表分为两部分:A部分产品诞生过程1 产品开发的策划2 产品开发的落实3 过程开发的策划4 过程开发的落实B部分批量生产5 供方/原材料6 生产6.1 人员/素质6.2 生产设备/工装6.3 运输/搬运/贮存/包装6.4 缺陷分析/纠正措施/持续改进7 服务/顾客满意程度序号审核项目/内容审核结果记录评分1.3 1.3 是否策划了落实产品开发的资源?要求/说明所要求的资源必须在报价阶段已调查并考虑到了。
在正式委托后,这些数据必须精确化。
在要求有更改时,如有必要必须重新进行资源调查。
必须策划并配齐必备的资源。
需考虑要点,例如:-- 顾客要求-- 具有素质的人员-- 缺勤时间-- 全过程时间-- 房屋,场地(用于试制及开发样件的制造)-- 模具/设备-- 试验/检验/实验室装置-- CAD,CAM,CAE。
1.4 1.4 是否调查了解并考虑了对产品的要求?要求/说明通过跨部门合作/行业水准比较(Benchmarking)来了解产品的要求,可使用例如:QFD(质量功能展开)、DOE(实验设计)等方法。
既往的经验与未来的期望必须予以考虑。
对产品的要求必须与市场要求和顾客期望相适应,产品必须具有竞争力。
需考虑要点,例如:-- 顾客要求-- 企业目标-- 同步工程-- 坚固的设计/受控的过程-- 定期的顾客/供方会谈-- 重要特性,法规要求-- 功能尺寸-- 装车尺寸-- 材料。
VDA6.3过程审核检查表(带示例_自动计算符合率)

一些重点工序的质控点没有对不良品运用统计 技术分析(P图或nP图)
X
M6.4.3 Are the causes of product and process nonconformities analyzed and the corrective actions rel checked for their effectiveness? 在与产品要求/过程要求有偏差时,是否分析原因 并检 查纠正措施的有效性?
过程审核检查
NO: 版次: 修订号: 表格编号:
审核报告编号(Audit Report Nbr.)2005-001 审核日期(Audit-Date): 6/1~6/2
Process Step 2
描述(Description): 压铸过程 1 操作工不明白产品质量/过程质量的要求。 2 作业指导书要求对首件产品确认品质 实际没有检查记录(P图)
X
M6.2.2 Can the quality requirements be monitored
effectively during serial production with the rel implemented inspection measuring and test equipment?在批量生产中使 用的检测.试验设备 是否能有效地监控质量要求?
0 4 6 8 10 0 4 6 8 10
负责生产设备/生产环境的职责和权限。 负责生产设备的维修和保养职责。
X
M6.1.3 Are the employees suitable to perform the
required tasks and is their qualification rel maintained? 员工是否适合于完成所交付的任务并保持其素质?
VDA6.3过程检查表
编号:No(11)第_____
审核过程: 审核产品: 检查重点工序: 审核项目/内容 序号 6.1 人员/素质 6.1.1 是否对员工委以监控产品质量/过程质量的职责和权限?考虑要点,如:
1 2 3 4 工艺文件(SOP)中是否有自检的规定,员工是否遵守?(SOP文件、工序作业记录) 每班生产前过程认可的职责是否确定?(设备点检/首件检验/末件检验/IPQC专职巡检) 当班发现不合格品的处置流程如何?上报终止生产的权利? 质管/检验人员对质控点控制图的理解?能否作出反应?
评分
6.1.2 是否对员工委以负责生产设备/生产环境的职责和权限?考虑要点,如: 1 设备、环境的清洁?有无规范保证措施? 2 是否对设备进行点检?(包括每班正式生产前的清洁工作) 3 是否按维护计划对设备进行了维护? 4 是否准备关键设备备件,能随时得到? 5 检验器具的保养,检定和校准? 6.1.3 员工是否适合于完成所交付的任务并保持其素质?考虑要点,如: 1 过程上岗指导/培训/资格状况(是否熟悉加工步骤以及过程中的检验要求?) 2 安全注意事项是否被员工了解?意外事故时的处置方法是否向操作者讲明? 3 由目视判断观察人员是否持证上岗? 4 操作者是否了解自己填写的记录的填写内容、方法/存档要求?(查现场记录) 6.1.4 是否包括顶岗规定的人员配置计划?考虑要点,如: 1 根据生产班次计划配置人员?规定了岗位相关职责(包括设备、环境、过程监控的责任)? 2 关键岗位是否有顶岗人员?(如关键重点工序,模具安装,设备维修的关键技术人员)不同 产品的加工人员 是否有替代人员计划? 3 替代人员岗位素质证明是否表明具有替岗资格? 6.1.5 是否有效地使用了提高员工工作积极性的方法 ? 考虑要点如: 1 员工的工资是否与其生产数量或过程目标的完成情况相挂钩? 2 对质量改进的贡献(对质量/改进有显著奉献并取得一定成绩时,该员工是否给予适当奖励 和表彰)? 3 合理化建议被采纳后是否给予奖励和表彰?
过程审核检查表示例
查目前的合格供方,均对其展开了调查和评价,同时采购 部门提供了供应商的评价准则, 评价包括供应商质量保证PPM、供货、研发能力,但缺少汽车业务量(绝对值,以 及占总业务量的百分比) ,业务连续性规划(如:防灾准 备、应急计划)等的调查项目
修订供应商调查表, 增加对供应 商汽车业务量占比、 业务连续性 规划的项目调查
审核项目
审核发现
整改措施
责任部门
完成时间
是否建立项目组织机构(项目管理) ,并为项 目管理以及团队成员确定了各自的任务及权 限
1、在APQP控制程序里建立了项目管理的流程,确定了项目组成员职责
是否为落实项目规划了必要的资源,相关 的资源是否已经到位,并且说明了变更情况
1、在新设备、工装清单上明确了有关顾客对产品追溯性
过程参数,均采用正式量产所使用的
采购方面的计划任务是否得到有效的落实?
针对顾客提出的特殊设备、工装、材料均能按时交付产线 使用
为了对正式投产提供保障,是否对项目交
接进行了控制?
查XX公司项目时,生产部门能提供新产品制作的SOP、
图纸、工装、设备等的验收记录,品质部门提供了产品的 检验规范
是否只和获得批准且具备质量能力的供应商
按照XX公司客户项目的进展, 更新项目计划, 重新评审项目计 划
工程部
10/30
项目管理机构是否可以在项目进行过程中
提供可靠的变更管理?
目前所有的产品结构,外观变更均通知顾客并得到批准, 同时对变更后的结果进行了验证关闭。
对于涉及变更SOP的,应及时编制更改
组织内部以及客户相关负责人是否已经纳
入变更管理?
但未能识别该产品有关的法规、技术规范要求
收集有关产品的法律法规和行 业规范, 并作为外来文件进行管 理
VDA 过程审核检查表及打分表—
日期:发现/背离等级生产 (工序 2 - 10)退火6.1.人员/素质6.1.1.是否对员工委以监控产品质量/过程质量的职责和权限?10查:明确授予了操作人员、车间主任的质量职责及质量管理员的过程监控职责6.1.2.是否对员工委以负责生产设备/生产环境的职责和权限?10查:球化退火炉,设备编号完好,标识牌上明确责任人为卜科平6.1.3.员工是否适合于完成所交付的任务并保持其素质?8查:现场记录与作业指导书相符6.1.4.是否有包括顶岗规定的人员配置计划?8查:有员工技能矩阵图及人员能力评价记录6.1.5.是否有效地使用了提高员工工作积极性的方法?10查:有员工奖罚制度,行政部能提供奖励及处罚记录。
6.2.生产设备/工装6.2.1.生产设备/工装模具是否能保证满足产品特定的质量要求?10查:能提供设备保养规程、保养计划、保养记录、维修记录;查:能提供工装管理规定、保养记录、精度检查记录。
关注易损零件/易损部位的定期更新记录。
查:能提供设备履历、工装履历等。
查:能提供工装验收记录并与工装设计文件比较。
包括易损件/部位的更换/维修周期的规定及实施。
6.2.2.在批量生产中使用的检测,试验设备是否能有效地监控质量要求?10查:提供《2017年检测设备外校检定证书台账》、《2017年计量器具外校检定计划》、《计量器具内校计划》及校准台账查:现场使用是千分尺,编号:45186,合格证上的校准日期为:2017/5/19,有效期为2018/5/18;6.2.3.生产工位,检验工位是否符合要求?8查:根据生产流程制定生产、检验工位,符合要求6.2.4.生产文件与检验文件中是否标出所有的重要技术要求,并坚持执行?10查:09118-08015《控制计划》与《作业指导书》该工序,没有特殊特性要求。
6.2.5.对产品调整/更换是否有必备的辅助器具?8查:配备有相关的辅助器具,如提升机等6.2.6.是否进行批量生产起始认可,并记录调整参数或偏差情况?10查:35K退火工艺记录参数符合《作业指导书》规定6.2.7.是否按时落实要求的纠正措施并检查其有效性?10查:质量目标未达标,每天在QRQC会议通报,并进行原因分析、制定改进措施,在后续会议中汇报实施结果日期:日期:日期:日期:6.1.1.是否对员工委以监控产品质量/过程质量的职责和权限?查:明确授予了操作人员、车间主任的质量职责及质量管理员的过程监控职责6.1.2.是否对员工委以负责生产设备/生产环境的职责和权限?查:设备标识是完好、正确有效,明确了设备责任人6.1.3.员工是否适合于完成所交付的任务并保持其素质?查:员工对本岗位作业指导书能理解和执行(首件记录、设备点检、工装服役档案等),符合。
S5-设施设备管理工装过程检查表
率
达到目标要求如是何改进的?
√
9.过程指标实现 情况
9.2模具保养及时 模具保养及时率是什么?有无达到目标要求?未达到
率
目标要求如是何改进的?
√
9.3关键设备故障 关键设备故障率是什么?有无达到目标要求?未达到
率
目标要求如是何改进的?
√
制造工程
查《2019年目标与实绩对照表》《目标未 达成改善计划表》
查《设备日常点检和定期保养项目参照表 》
√
6.设施设备维护 保养
6.2日常点检
是否依照《设备日常点检和定期保养项目参照表》和
设施操作规程进行日常点检,并填写《设备点检保养
记录表》?
√
日常点检或使用过程中发现设施设备异常时,如何处
理?
√
相关部门
查2019.6装配、冲压、注塑设备点检保养 记录表
√
是否依照《设备日常点检和定期保养项目参照表》和 6.3定期维护保养 设施操作规程规定之保养项目与周期进行定期维护保 √
√
询问
审核地点
检查结果记录
管理部 由各部门提交各部门设施设备需求
管理部
查采购设施有附产品合格证及说明书等资 料
结果判定
符合
不 符合
√
√
2.安装和验收
设施设备到厂后,设施设备职责管理部门是否填写《 固定资产收货单》?
√
2.1设施设备试运
行验收
设施设备到厂后,设施设备职责管理部门是否填写《
固定资产收货单》?安装、调试合格后是否填写《设 √
养,并填写《设备点检保养记录表》?
√
相关部门
查2018.7装配、冲压、注塑设备点检保养 记录表
- 1、下载文档前请自行甄别文档内容的完整性,平台不提供额外的编辑、内容补充、找答案等附加服务。
- 2、"仅部分预览"的文档,不可在线预览部分如存在完整性等问题,可反馈申请退款(可完整预览的文档不适用该条件!)。
- 3、如文档侵犯您的权益,请联系客服反馈,我们会尽快为您处理(人工客服工作时间:9:00-18:30)。
序审核项目工序分值问题工序详细说明
1
人员/素质(审核结束后对操作和回答不符合的员工培训情况统一
确认)
1.1
对照作业指导书,观察员工操作与作业指导书一致性?(连续观察3
台以上)
1.2
提问员工,本岗位设备保养、点检有哪些要求,如何做?点检发现
异常如何处理?
1.3
员工对本岗位的作业指导书的要求是否清楚?有哪些特殊特性要
求?是否了解特殊特性符号及意义?
1.4
提问员工,对本岗位的生产质量要求是否清楚?(外观、扭矩、涂
胶、涂油、自检、互检、清洁度等)
1.5
人员对不合格品的处理流程是否了解?
1.6
员工是否了解本岗位的质量风险及其对顾客(包括下到工序)的影
响?(螺栓未打紧、零件密封面磕碰、气门间隙超差、正时标记偏
等、漏涂油、漏涂胶、密封面不清洁等)
1.7
对有测量的岗位,员工是否清楚测量仪器的使用方法?记录要求?
测量不合格处理?
2
设备/工装
2.1
生产设备/工装是否干净整洁,运转正常,设备管理标示牌、防护,
按钮、电线等是否完好。
2.2
是否按要求点检、保养,并记录,点检异常如何处理?
2.3
工艺参数(压力、温度等)是否有效监控,设备能否防错(自动报
警、停机等)?并有措施保证其有效性?
3
物料:运输/搬运/贮存/包装
3.1
物料清洁度防护控制手段有效,符合工艺要求;
3.2
物料是否按要求贮存?运输器具/包装方法是否按物料的特性而定?
3.3
废品、返修件和不合格件以及车间内的剩余料是否分别贮存与并标
识,可追溯?
3.4
整个物流是否能确保不混批、不混料并保证可追溯性?
3.5
物料摆放整齐,稳固,数量、标识清楚,可追溯;
3.6
物料,运输器具/包装方法合理,不会造成产品的倒塌、损坏、锈蚀
3.7
现场有合适的堆放物料、工具、产品的地方、工作台等?生产工位
物料堆放整齐,摆放合理,不超位,不过位,各物料标识清楚;能
确保不混,不乱。
3.8
岗位物料防护符合要求、物料间不存在磕碰、划伤风险;
3.9
对不合格品有控制办法,职责分明,能对不合格品有效隔离、标识
、记录和处理。
4
标准作业
4.1
作业指导书、检验指导书是否受控?是否为最新版?是否与控制计
划一致?
4.2
首检、自检、巡检、专检等记录是否与控制计划一致?是否按要求
记录?不合格处理结果?
装配过程审核检查表
审核员: 日期: 陪同人员:
评分标准:10---完全符合要求;8---绝大部分符合要求,有少量偏差;6---部分符合要求,有较大偏差;4----少部分符合要求,偏差严重;0---完全不符合要求; ★对每
一大项全部满分(10),或每一小项(6分)以下,要陈述情况,并说明证据(照片);
1
序审核项目工序分值问题工序详细说明
装配过程审核检查表
审核员: 日期: 陪同人员:
评分标准:10---完全符合要求;8---绝大部分符合要求,有少量偏差;6---部分符合要求,有较大偏差;4----少部分符合要求,偏差严重;0---完全不符合要求; ★对每
一大项全部满分(10),或每一小项(6分)以下,要陈述情况,并说明证据(照片);
4.3
是否有措施保证标准化作业的执行?(如过程巡查)
4.4
通知单按照要求执行,并留有通知单执行记录。工艺变更有记录、
记录符合要求。
4.5
工艺文件覆盖当前生产所有机型、所有加工/装配工艺、所有加工/
装配工序,工艺步骤要求具体、明确、可执行;
4.6
特殊特性工序检验要求符合工艺要求,特殊特性工艺文件一致性满
足要求;
4.7
变更是否符合制造过程变更流程,是否经过批准。过程变更记录齐
全,文件固化符合要求;
5
环境
5.1
员工作业时是否会受到其他安全方面的影响?
5.2
现场的照明是否充足,是否适合作业\检查等操作?
6
测量、缺陷分析、纠正措施、持续改进(KVP)
6.1
每个工序测量工具配置齐全,并符合测量的需求
6.2
测量工具是否有校验标识,测量工具完好、准确,是否在有效期?
6.3
作业员\检查员是否按规定频率和样本数量使用指定工具检查?
6.4
测量记录完整,准确、有效?(无涂改、数值错误等)
6.5
产品流转卡完整,各工序记录清晰,与产品要求相符,签名、记录
6.6
质量检验点标识明确,清楚,检验样板、文件、资料、记录齐全;
6.7
质量检验人员熟悉产品检验要求,检验规范;
6.8
质量检验人员对测量工具、设施熟悉并掌握,接受过MSA分析确认
6.9
所有检验工具有明确的合格标识,并定期进行了校准;
6.10
检验记录数据完整、有效,真实;放行产品有检验人员签字;
6.11
对不合格进行了专门的记录,并进行了处理;
6.12
对维修、返工的产品进行了重新检验,并能提供记录;
6.13
对经常会出现质量问题的生产过程采取了纠正措施或防错措施,提
供措施及实施的记录。
7
综合管理
7.1
定期对生产各岗位的情况进行检查,并记录(多久一次)
7.2
对各岗位生产问题,进行处理,并对结果进行验证和记录?
7.3
不良品的确认和评审职责是否清晰,不良品是否进行了统计和缺陷
7.4
关键质量控制点设置明确,具有标识;规定了测量和分析的要求
7.5对返修、报废等在作出可否使用的判断时,是否作了评审?
7.6
总成以及组件返修时的折卸顺序,返修顺序、返修方法是否明确?
8
清洁度
8.1
工装/辅具清洁,无明显油污、杂质等。
8.2
油盒清洁,无杂质等。
8.3
料盒清洁,无明显油污、杂质等,且防尘装置完好。
8.4
劳保清洁度良好。
8.5
夹持/检测机构无明显油污、杂质等。
8.6
量具清洁,无明显油污、杂质等。
2