铝合金化学抛光三酸配方和优劣
四、铝的化学抛光

四、铝的化学抛光为了取得表面光亮的铝和铝合金,除了进行机械抛光外,对于光亮度要求较高的零件还需进行化学抛光,化学抛光的特点是设备简单,节省电能,效率高和成本低,而且不受零件形状和尺寸的限制、特小,特薄和形状复杂的零件以及异型管。
孔和槽的内腔均可加工。
不过化学抛光也还存在不少问题,例:在多数情况下,其质量还不能完全赶上电化学抛光,而且还有大量氮氧化合物气体产生。
化学抛光的反应过程是金属在电介质溶液中的自溶过程。
关于化学抛光的机理迄今尚无成熟理论。
一般认为与电化学抛光相似,化学抛光时金属表面显微凸起部分的溶解速度比凹下部分快得多,因而使表面变得平坦光亮。
在工业上用于化学抛光的溶液主要是磷酸、硝酸、硫酸、醋酸或其它化合物。
下面介绍常用化学抛光配方:1.适用高纯铝及铝镁合金化抛配方:磷酸(H3PO4)70% (容量比)硫酸(H2S04)20% (容量比)硝酸(HNO3)10% (容量比)温度90~115℃时间3~8分钟新溶液温度控制为90℃,(因溶液粘度小,离子活动快)。
老溶液温度控制为115℃,(因老溶液粘度大,离子活动慢)铝化学抛光质量于溶液中硝酸的含量多少有着极为重要的关系。
硝酸含量低于5%会引起铝件表面结晶腐蚀,大于12%,会引起点状腐蚀。
抛光溶液成份及工艺条件的影响:(1)磷酸含量的影响:一般磷酸含量约在50~85%之间,最佳范围在70%,过低的磷酸含量光洁度较差,过高含量抛光速度缓慢。
(2)硫酸含量的影响:在无硫酸条件下,同样可以得到光洁表面,但易产生点蚀,抛光速度慢,过多硫酸光亮度显著下降,表面易产生雾状,因此硫酸含量宜控制20%左右。
(3)硝酸含量的影响:硝酸含量在5%~10%,过多硝酸不但使铝制件表面出现点腐蚀,而在温度条件下产生乳白色,低于5%光亮度显著下降。
(4)铝离子含量的影响:铝离子含量有利于提高抛光整平性能,但不宜超过30克/升,否则抛光速度缓慢,使溶液的粘度增大,导致溶液的排泄困难,而洗涤后亦将引起表面斑渍。
高端镜面型材生产工艺之化学抛光

高档镜面抛光铝材生产技术之——化学抛光工艺铝材抛光是开发铝材多品种、多色系、光亮浅色调和多彩铝的基础。
是改变铝材色调单一现状,提高铝材表面装饰效果的关键工艺。
亦是铝材更新换代与增值的主要途径。
化学抛光具有工艺简单,抛光速度快,铝耗低。
可用于复杂工件,不用电力,投资少等特点。
因此,国外已应用了100多年。
三酸抛光可得到镜面光亮效果。
但在抛光过程中,产生有毒气体NO、NO2与酸雾,需妥善处理,同时槽液维护有一定的难度。
二酸抛光的光亮度略低于三酸抛光,但抛光工仵表面平滑细腻,光亮均匀的效果已很佳,仅次于三酸抛光。
由于抛光过程没有有毒气体产生,酸雾亦较轻,所以更具发展前途。
为了得到稳定的、高亮度品质及减少缺陷的产生,抛光工艺必须严格控制:三酸抛光配方、二酸抛光配方。
本人已在《澳金人》第二期上介绍过,本文不再论述。
本文重点探讨槽液成份比例、比重、温度、时间之间的关系及对质量的影响。
1. H3PO4(磷酸)含量:H3PO4是抛光槽液的主体,通过粘度效应,使铝表面形成镜面效果。
其含量越高,镜面效果越明显。
因此,H3PO4含量是保持抛光亮度的关键因素。
一般生产上要求H3PO4≥65%。
配槽初期,H3PO4浓度较容易控制在65%以上,随着AL3+及杂质含量的增高,H3PO4浓度就难达到以上要求。
当AL3+含量达到上限时,H3PO4浓度会降到55%左右,影响了抛光效果。
这时可通过增加H2SO4或提高比重来维持槽液的粘度。
因此,必须通过对槽液的日常维护及槽液合理的更新做到科学化管理,才能保持化抛工艺的稳定性。
2. HNO3(硝酸)、H2SO4(硫酸)、及AL3+、CU2+含量:HNO3是直接参与反应的主要成份,其含量必须严格控制,一般为3.2~3.7%, HNO3浓度太高,不仅会产生大量黄烟,而且反应过于剧烈,难以控制,容易产生过腐蚀,起砂以及流痕等缺陷。
HNO3浓度偏低,难以达到最佳亮度。
其性能活跃,较易挥发。
槽液不生产时,尽量降低温度。
三 酸 抛 光 槽 硝 酸 浓 度 分 析
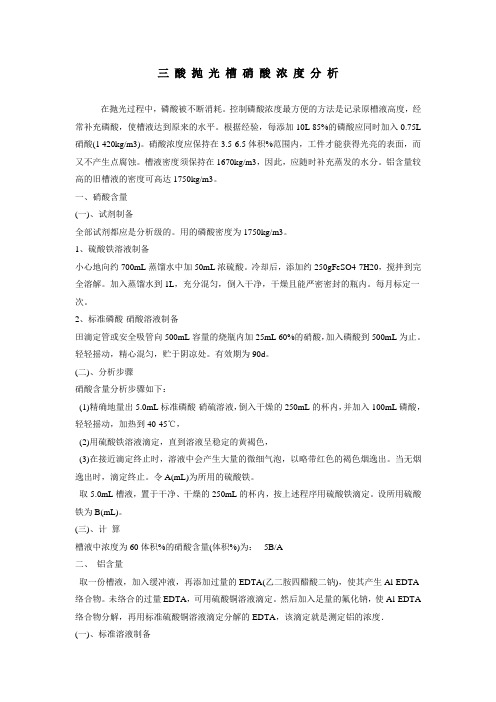
三酸抛光槽硝酸浓度分析在抛光过程中,磷酸被不断消耗。
控制磷酸浓度最方便的方法是记录原槽液高度,经常补充磷酸,使槽液达到原来的水平。
根据经验,每添加10L 85%的磷酸应同时加入0.75L 硝酸(1 420kg/m3)。
硝酸浓度应保持在3.5-6.5体积%范围内,工件才能获得光亮的表面,而又不产生点腐蚀。
槽液密度须保持在1670kg/m3,因此,应随时补充蒸发的水分。
铝含量较高的旧槽液的密度可高达1750kg/m3。
一、硝酸含量(一)、试剂制备全部试剂都应是分析级的。
用的磷酸密度为1750kg/m3。
1、硫酸铁溶液制备小心地向约700mL蒸馏水中加50mL浓硫酸。
冷却后,添加约250gFeSO4·7H20,搅拌到完全溶解。
加入蒸馏水到1L,充分混匀,倒入干净,干燥且能严密密封的瓶内。
每月标定一次。
2、标准磷酸-硝酸溶液制备田滴定管或安全吸管向500mL容量的烧瓶内加25mL 60%的硝酸,加入磷酸到500mL为止。
轻轻摇动,精心混匀,贮于阴凉处。
有效期为90d。
(二)、分析步骤硝酸含量分析步骤如下:(1)精确地量出5.0mL标准磷酸·硝硫溶液,倒入干燥的250mL的杯内,并加入100mL磷酸,轻轻摇动,加热到40-45℃,(2)用硫酸铁溶液滴定,直到溶液呈稳定的黄褐色,(3)在接近滴定终止时,溶液中会产生大量的微细气泡,以略带红色的褐色烟逸出。
当无烟逸出时,滴定终止。
令A(mL)为所用的硫酸铁。
取5.0mL槽液,置于干净、干燥的250mL的杯内,按上述程序用硫酸铁滴定。
设所用硫酸铁为B(mL)。
(三)、计算槽液中浓度为60体积%的硝酸含量(体积%)为: 5B/A二、铝含量取一份槽液,加入缓冲液,再添加过量的EDTA(乙二胺四醋酸二钠),使其产生Al-EDTA 络合物。
未络合的过量EDTA,可用硫酸铜溶液滴定。
然后加入足量的氟化钠,使Al-EDTA 络合物分解,再用标准硫酸铜溶液滴定分解的EDTA,该滴定就是测定铝的浓度.(一)、标准溶液制备所用的全部试剂都应是分析试剂级的。
铝及铝合金化学抛光体系简介一

铝及铝合金化学抛光体系简介--三酸抛光体系推荐理由:文章主要讲述了三酸体系化学抛光铝表面的作用机理,以及酸抛光技术的工艺要求等。
从文章中可以看出三酸体系在化学抛光处理过程中一些弊端,即在三酸化学抛光体系中需要进行工艺优化的地方。
从而能够让人发起思考:在铝及铝合金材料的抛光处理中,除了三酸处理体系,还能出现其他哪些处理体系呢?一、化学抛光的作用铝材阳极氧化前的预处理能够提供光亮外观。
从铝材质来讲,纯铝的抛光性能最好,铝硅合金的抛光性最差。
为了获得高标准光亮的精饰的表面,除了选择纯度高的铝材,常采用机械抛光、化学抛光和电化学抛光相结合的方式。
化学抛光使铝材表面平整光滑,能除去铝材表面较轻微的模具痕迹和擦伤条纹,能除去机械抛光中可能生成的摩擦条纹、热变形层、氧化膜层等,使粗糙的表面趋于光滑,同时可提高铝材的镜面反射性能,提高光亮度。
而在早期化学抛光的抛光液体系中,三酸体系比较主流,但是随着碱性氧化铝抛光液的出现三酸体系逐渐失去主导地位。
这里对三酸抛光体系作简单的介绍。
二、总机理总机理是铝的酸性浸蚀过程—钝化过程—黏滞性扩散层的扩散过程。
三酸抛光:磷酸---硫酸---硝酸。
原理:铝浸到热的浓酸中时,发生强烈的酸性浸蚀反应,并溶解除去铝材表面的一层铝,此时抛光液中的某种成分遏制酸性浸蚀反应,发生氧化反应,形成一层几十个原子层厚度的氧化铝的钝化覆盖在铝表面上,产生钝化作用,铝表面暂时受保护。
而氧化膜不断被酸溶解,然后又受钝化,又溶解这样的反复过程,凸处不断被整平和凹处达到同一个平面,此时达到抛光目的。
三、三酸抛光的优缺点:(一)装料要求高:装料量应少,铝材间距大,倾斜度大,才能使气体尽快逸出。
化学抛光液的比重很大,铝很轻,在抛光过程中还要防止铝材上浮,漂在面上,造成光亮度不均匀。
应加重导电梁防止铝材上浮;对高光亮度要求的装饰面应该向外垂直装料,使气体尽快逸出;装料要稳固,采用夹具时安放在非装饰面上,避免留下痕迹。
铝或铝合金“三酸”化学抛光产生“黄烟”的净化措施

本工艺依据 NOx 废气成分复杂、浓度高、难于治理的特性,系统中设计三个 阶段即三级废气净化(吸收)塔,以增加 NOx 与吸收液传质过程,有充分的反应 时间使 NOx 废气扩散于液相,被吸收溶解与净化。同时,废气净化设备要建立加 药泵、pH 值感应器、液量传感及补水运行的 PCL 自动监控系统,确保净化设备 的正常运行和废气净化效果,达到达标排放的要求。
工艺方案和净化设备十分重要。笔者进行了现场调研,多数企业仍以湿法为主。 根据工厂实践经验,湿法净化黄龙,认为采用“氢氧化钠、双氧水、硫化钠”的 三级吸收塔的吸收效率最高,三级串联填料塔的吸收流程见图 3,供同行参考。
第一级塔的吸收液为氢氧化钠(吸收作用)。它与氮的氧化物的反应实质上 是不可逆的酸碱中和反应,生成了硝酸钠(NaNO3)和亚硝酸钠(NaNO2)。一般以 5% 氢氧化钠水溶液的吸收效果为好,但它不会和一氧化氮发生反应。如果氢氧化钠 水溶液度超过 5%或低于 1%时,吸收效率就会急剧下降,因此,当氢氧化钠的浓 度降低到 1%以下时需要更换新液。
化学抛光

化学抛光-Bright DipBright, Dip化学抛光是利用铝和铝合金制作在酸性或碱性电解质溶液中的选择性自溶解作用,来整平抛光制年表面,以降低其表面粗糙度、PH的化学加工方法。
这种抛光方法具有设备简单、不用电源,不受制件外型尺寸限制,抛兴速度高和加工成本低等优点。
铝及铝合金的纯度对化学抛光的质量具有很大的影响,它的纯度愈高,抛光质量愈好,反之就愈差。
化学抛光就是采用简要的粘性液膜理论进行的。
抛光液配方和工艺条件:配方一:(重量份)浓磷酸75% ;浓硫酸8.8%;浓硝酸8.8%;尿素3.1%;硫酸胺4.4%;硫酸铜0.02%。
温度100-200度时间2-3MIN配方二:(重量份)浓磷酸85%;浓硝酸5%;冰乙酸10%。
温度90-105度时间2-5MIN抛光液的配制方法:1、先把磷酸、硫酸和硝酸按照一定的(%)重量,逐渐依次倒入抛光槽内,小心拦匀。
2、再按配方的成分,分别用水溶解一定(%)重量的冰乙酸、尿素、硫酸胺、硫酸铜加入槽内拌匀。
3、然后,在搅拌状态下,逐渐调节上述抛光液至各配方所需的温度范围,即可进行化学抛光。
化学抛光,原理差不多,只不过它采用放在一定温度的溶液里面,这样子粒子排列会更加整齐,溶液的主要成分是草酸或者磷酸最佳抛光液组成和操作条件如下: 磷酸硫酸体积比80∶20,硫酸镍1.0g/L,YG05添加剂0.6g/L,水含量小于等于15g/L,温度75℃,抛光时间4min. 生产应用表明,磷酸硫酸体系抛光液及其抛光工艺具有铝合金表面光亮度高、反应温度低和无黄烟等优点,完全可以代替用磷酸硫酸硝酸体系抛光液对铝合金的化学抛光.参考0:一、对铝制品表面进行机械抛光:1、机械抛光工序为:粗磨、细磨、抛光、抛亮、喷砂、刷光或滚光等,根据制表面的粗糙程度来适当采取不同的工序。
二、化学除油:化学除油过程是借着化学反应和物理化学作用,除去制件表面的油污。
化学除油采用弱碱性溶液中进行。
化学除油液的配方和工艺条件:1、配方:氢氧化钠30-50G/L,工业洗涤剂0.5-1ML/L,水70-125G。
铝及铝合金化学抛光工艺(收藏)

铝及铝合金化学抛光工艺(收藏)概述化学抛光经过机械抛光后的铝合金工件虽然已经获得光亮的表面,但若将机械抛光后的工件直接进行阳极氧化,所得到的只是一个平滑的表面而得不到反光系数较高的膜层,所以经机械抛光后的工件还必须进行化学抛光或电抛光,以除去工件表面在机械抛光时所形成的晶体变形层,从而获得光亮、细致的表面。
化学抛光是通过抛光溶液对工件微观凹凸表面的膜层形成及溶解速率不同而达到抛光的目的。
铝合金的化学抛光可分为酸性抛光和碱性抛光两种。
酸性化学抛光酸性化学抛光的主要原料是磷酸、硫酸、硝酸、乙酸、氟化氢铵等,但在化学抛光中仅有这些基本原料组成的配方并不能很好地满足于生产需求,还需要有目的地在抛光溶液中添加一些旨在提高其光泽度及平滑度的添加物质。
这些添加物质可分为两大类:一是无机盐;二是有机物。
1添加剂的作用在铝合金的化学抛光中添加剂起着不可估量的作用,其作用主要表现在以下四个方面:一是提高光亮度和平滑度;二是增加抛光表面的透光度;三是减慢抛光溶液对铝合金基体的腐蚀速率;四是降低抛光过程中的氮氧化物气体的产生。
2酸性化学抛光常用的方法磷酸-硫酸-硝酸法、磷酸-硝酸-乙酸、磷酸-硝酸法、磷酸-硫酸法、硝酸-氟化氢铵法等。
其中磷酸-硫酸-硝酸法是目前最为常用的抛光方法,也称为三酸抛光法。
常用三酸抛光溶液成分及操作条件见表1、表2。
表1 常用三酸抛光溶液成分及操作条件溶液成分材料名称化学式含量配方1 配方2 配方3 配方4 磷酸/(mL/L)H3PO4850 800 750 700硫酸/(mL/L)H2SO4100 100 250 200 硝酸/(mL/L)HNO350~100 100 50~100 50~100硫酸铵(NH4)2SO40~20 0~20 0~20 0~20/(g/L)硝酸铜/(g/L) Cu(NO3)2·3H2O 0.2~2 0.2~2 3~6 —硫酸镍/(g/L) NiSO4·6H2O 5~20 ———硝酸银/(mg/L) AgNO310~80 10~80 ——硼酸/(g/L) H3BO3——4~8 —操作条件温度/℃90~105 95~115 时间视要求而定搅拌工件摆动表2 常用三酸抛光溶液成分及操作条件溶液成分材料名称化学式含量配方5 配方6磷酸/(mL/L) H3PO4600 500硫酸/(mL/L) H2SO4200 400硝酸/(mL/L) HNO3200 80~120硫酸铵/(g/L) (NH4)2SO40~20 0~20硝酸铜/(g/L) Cu(NO3)2·3H2O ——硫酸镍/(g/L) NiSO4·6H2O ——硝酸银/(mg/L) AgNO3——硼酸/(g/L) H3BO3——操作条件温度/℃100~120 时间视要求而定搅拌工件摆动☆注意事项:三酸抛光对抛光质量影响较大的并不是这三种酸的含量,而在于这三中酸的配合比例。
铝材化学磨砂抛光技术连载(一)

一、研究背景铝材化学磨砂抛光技术是在整平光亮技术和光亮酸蚀技术的基础上,成功开发出的又一项独家专有技术。
近几年来,研发部门对铝材阳极氧化前处理各项传统工艺,如碱蚀、酸蚀、三酸抛光等进行了详细研究,结果发现:1、铝材亮度:三酸抛光液中,由于硝酸等强氧化剂的存在,使铝材表面很容易被氧化出一层含致密氧化铝的钝化层,据此形成镜面,因而三酸抛光最亮;碱蚀无钝化作用,没有抛光效果,但却能保留金属色;酸蚀最暗,铝材表面被一层酸蚀灰覆盖,完全没有金属光泽。
2、机械纹:酸蚀液中,反应产物粘附在铝材表面并填平机械纹沟底,沟底的铝材与酸蚀液完全隔绝,反应速度几乎为零,而沟表面的粘附产物较薄,酸蚀液可与铝材接触,反应可快速进行。
这样,沟表面与沟底产生了很大的反应速度差,从而实现了最强的去机械纹能力;碱蚀也具备较强的去机械纹能力,但利用的是粘性理论,即沟底的铝离子浓度高于沟表面的铝离子浓度,决定了沟表面的反应速度快于沟底的反应速度,从而实现了后车追上前车,消除机械纹的目的。
由于沟底的反应速度只是被减缓,而不是象酸蚀那样被彻底抑制,因而碱蚀去机械纹能力比酸蚀弱得多,且铝耗是酸蚀的五倍以上。
三酸抛光含有一定浓度的强氧化剂,使铝材表面产生钝化膜,因而不具备去机械纹能力。
3、砂面:酸蚀与碱蚀形成砂面的机理不同,因而生成的砂粒各异。
在酸蚀液中,以阴极相(Mg2Si,AlFeSi等)为中心,与之周边相邻的阳极相(纯铝相)被不断溶解,铝离子进入槽液,形成砂坑;同时,氟离子有可能与一些金属阳离子络合,借助氟作为运载工具,在阴极相析出,形成砂峰;由此可见,阴极相是形成砂粒的砂源,其在合金中的均匀、细腻的分布程度直接决定酸蚀砂面的外观质量;为此,国内很多厂家采用掺复锭的方法,人为引人杂质金属,形成均匀细腻的阴极相,从而生产出比仅用纯铝锭漂亮得多的酸蚀砂面材!在碱蚀液中,铝的反应方式略有不同。
首先,按原电池原理,阴极相周围的纯铝相(阳极相)被不断溶解,形成砂坑;但由于没有氟离子作为运载工具,阴极相区域没有析出,不能形成较尖的砂峰;另外,在碱性条件下,由于没有象酸性条件下的钝化反应制约,碱蚀反应可以毫无障碍地快速进行,相邻砂坑可能连通,形成较大砂坑;因此,碱蚀砂因其砂峰不尖,砂坑过大而远没有酸蚀砂漂亮!三酸抛光是在酸性条件下进行,强氧化剂的存在使铝材表面的钝化反应非常明显,几无去机械纹和起砂能力。
- 1、下载文档前请自行甄别文档内容的完整性,平台不提供额外的编辑、内容补充、找答案等附加服务。
- 2、"仅部分预览"的文档,不可在线预览部分如存在完整性等问题,可反馈申请退款(可完整预览的文档不适用该条件!)。
- 3、如文档侵犯您的权益,请联系客服反馈,我们会尽快为您处理(人工客服工作时间:9:00-18:30)。
铝合金化学抛光三酸配方和优劣
在我国传统的铝合金化学抛光溶液中,应用较为广泛的是磷酸-硫酸-硝酸化学抛光液。
根据其磷酸相对含量的不同,可分为甲类(磷酸相对含量较低)和乙类(磷酸相对含
量较高)。
其三酸抛光液成分和抛光温度如下。
长期的工业生产发现,三酸基本可以满足产品要求,但是也有些致命缺陷,如产生黄
烟(毒性气体,污染环境),达不到环保要求。
因此,我总结罗列了一些缺陷特点。
1、氧化严重失光,质量大打折扣。
三酸抛光,一般都能形成镜面,一经阳极氧化,光泽大打折扣。
2、硝酸分解太快,大量黄烟污染严重,处理成本昂贵。
硝酸为强氧化剂,在高温条件下,遇到铝这种还原性很强的金属,分解速度之快令人难以想象:大量黄烟象着火一
样瞬间溢出,抽风都困难,彻底吸收更难!此外,硝酸浓度的上下波动,势必造成抛光铝合金表面亮暗交替,成品率低。
3、不能起砂、去机械纹。
铝合金成型过程中,表面有许多机械纹,经三酸抛光处理后,纹路更加明显,严重影响铝合金外观质量。
除了用效率较低的机械方法(如喷砂,机抛)等进行预处理外,近几十年来,没有开发出用化学方法进行去纹和起砂配套处理、然
后再行抛光的成熟技术,制约了抛光技术的推广。
4、滴流时间太短、药剂消耗太大、成品率太低。
因此,尽管抛光工艺如此简捷,但成本却是所有氧化前处理技术之最!高达6000-8000元/吨材。
铝合金离开抛光液后,在
空中滴流时间一般不得超过30秒,否则会出现流痕,产生废品。
抛光材的流痕问题,是困扰铝加工行业的世界难题。
如此短的滴流时间,势必造成两大严重后果:其一是
药剂消耗太大,竟然高达400-600kg/吨材,还要为如此高的废酸处理增加约800Kg
片碱处理废水!其二是成品率太低,一般不到70%,大部分废品是由于流痕或花材造成,进一步增加了生产成本。
目前一般使用的方法是用化学抛光去冲孔剂添加剂用于抛光
原液中,以此解决流痕问题。
随着研究的深入,市面上已经有很多厂家在使用无烟两酸化学抛光高光光亮剂,主要是磷酸和硫酸组成,不会产生黄烟,能满足环保要求。