外圆磨
外圆磨的工艺

外圆磨的工艺
外圆磨是一种常见的金属加工工艺,用于将工件的外圆表面磨削成所需的尺寸、形状和精度。
以下是外圆磨的基本工艺步骤:
1. 选择磨削设备:根据工件的尺寸、材料和要求选择合适的外圆磨削设备,如圆柱磨床、中心磨床等。
2. 安装工件:将待磨工件安装在磨床的工作台或夹具上,确保工件稳固。
3. 调整磨削参数:根据工件的材料和要求,调整磨削参数,如磨削速度、进给量、切削深度等。
4. 开始磨削:启动磨床,使磨石或磨轮接触到工件表面,进行磨削。
通常情况下,磨削可以分为粗磨和精磨两个阶段。
5. 检查加工精度:使用测量仪器,如千分尺、测微计等,检查磨削后的工件尺寸和几何形状是否符合要求。
6. 调整和修正:根据测量结果,如有必要,调整磨削参数或重新磨削工件,以达到要求的尺寸和精度。
7. 清理和保养:磨削完成后,清理磨削区域,并进行设备的维护保养工作,如
更换磨石或磨轮等。
外圆磨工艺要求操作者熟悉磨削设备的使用方法和磨削技术,同时需要具备一定的磨削理论知识和经验。
为了提高加工效率和加工质量,通常需要进行不断的实践和改进。
数控外圆磨尺寸不稳定原因
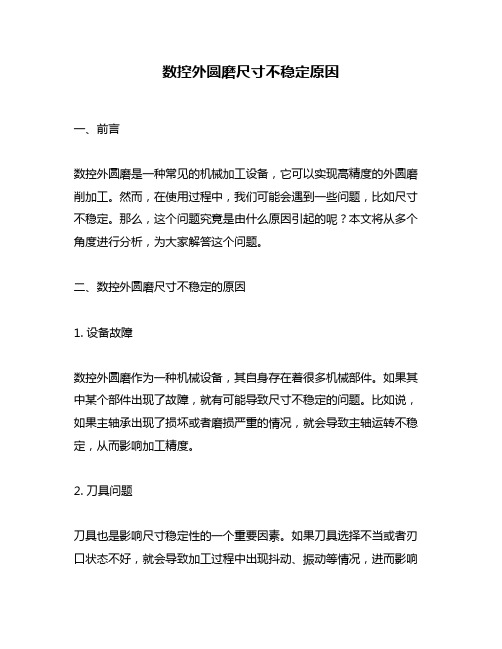
数控外圆磨尺寸不稳定原因一、前言数控外圆磨是一种常见的机械加工设备,它可以实现高精度的外圆磨削加工。
然而,在使用过程中,我们可能会遇到一些问题,比如尺寸不稳定。
那么,这个问题究竟是由什么原因引起的呢?本文将从多个角度进行分析,为大家解答这个问题。
二、数控外圆磨尺寸不稳定的原因1. 设备故障数控外圆磨作为一种机械设备,其自身存在着很多机械部件。
如果其中某个部件出现了故障,就有可能导致尺寸不稳定的问题。
比如说,如果主轴承出现了损坏或者磨损严重的情况,就会导致主轴运转不稳定,从而影响加工精度。
2. 刀具问题刀具也是影响尺寸稳定性的一个重要因素。
如果刀具选择不当或者刃口状态不好,就会导致加工过程中出现抖动、振动等情况,进而影响加工精度。
3. 工件材料问题工件材料也是影响尺寸稳定性的一个关键因素。
如果工件材料硬度过高或者材料本身存在缺陷,就会导致加工难度增大,从而影响加工精度。
4. 加工参数问题加工参数也是影响尺寸稳定性的一个重要因素。
如果加工参数设置不当,比如说进给速度过快、切削深度过大等,就会导致加工过程中出现抖动、振动等情况,进而影响加工精度。
5. 环境问题环境也是影响尺寸稳定性的一个因素。
如果环境温度过高或者过低、湿度过大或者过小等条件不符合要求,就有可能导致材料膨胀或者收缩,从而影响加工精度。
三、解决数控外圆磨尺寸不稳定的方法1. 维护设备首先,在使用数控外圆磨之前,需要对其进行维护和保养。
比如说,检查主轴承是否正常、刀具是否磨损严重等。
这样可以避免设备故障对加工精度造成的影响。
2. 选择合适的刀具其次,在选择刀具时,需要根据加工材料的特性和要求来选择合适的刀具。
比如说,对于硬度较高的材料,可以选择钨钢刀具等。
3. 优化加工参数再次,需要优化加工参数,根据加工材料的特性和要求来设置合适的进给速度、切削深度等参数。
这样可以避免因加工参数不当而导致的尺寸不稳定问题。
4. 控制环境条件最后,在进行数控外圆磨加工时,需要控制好环境条件。
外圆磨安全操作及保养规程
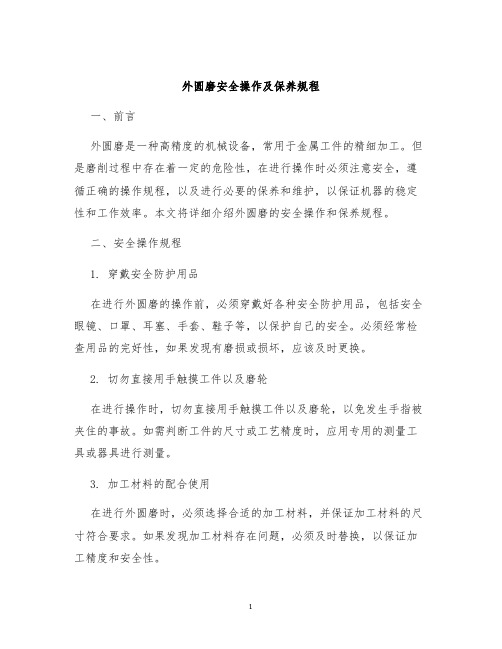
外圆磨安全操作及保养规程一、前言外圆磨是一种高精度的机械设备,常用于金属工件的精细加工。
但是磨削过程中存在着一定的危险性,在进行操作时必须注意安全,遵循正确的操作规程,以及进行必要的保养和维护,以保证机器的稳定性和工作效率。
本文将详细介绍外圆磨的安全操作和保养规程。
二、安全操作规程1. 穿戴安全防护用品在进行外圆磨的操作前,必须穿戴好各种安全防护用品,包括安全眼镜、口罩、耳塞、手套、鞋子等,以保护自己的安全。
必须经常检查用品的完好性,如果发现有磨损或损坏,应该及时更换。
2. 切勿直接用手触摸工件以及磨轮在进行操作时,切勿直接用手触摸工件以及磨轮,以免发生手指被夹住的事故。
如需判断工件的尺寸或工艺精度时,应用专用的测量工具或器具进行测量。
3. 加工材料的配合使用在进行外圆磨时,必须选择合适的加工材料,并保证加工材料的尺寸符合要求。
如果发现加工材料存在问题,必须及时替换,以保证加工精度和安全性。
4. 可靠固定工件在进行加工时,必须保证工件的安全可靠地固定在工作台上,避免出现移动或其他不良情况。
为此,在制定工艺前,应检查工作台以及夹具等配件是否符合加工要求,并适时调整。
5. 操作前检查磨轮在进行操作前,必须仔细地检查磨轮的磨损程度以及表面状况。
如果发现表面破损、出现裂纹或异物等情况,则不能继续操作,必须更换磨轮并做好检查工作。
6. 规范操作手法进行外圆磨的操作时,必须遵循正确的手法,并按照预制的工艺流程进行操作。
必须特别注意安全,并随时观察加工情况,以及运行状态,发现问题及时停机进行检查或调整。
三、外圆磨保养规程1. 清洁保养在进行外圆磨操作后,必须对机器进行清洁,并保证机器的干燥和清洁。
同时,必须经常对机器进行保养工作,包括清理切削液、油污、灰尘等,以及润滑各处轴承,保持机器的稳定性和运作效率。
2. 保持机器的稳定性为了确保机器的稳定性,必须定期检查各种零部件,包括轴承、传动件等,确保其功能完好。
同时,需要定期清洗齿轮、润滑剂管道、电器元件等,以保证机器的正常运作。
外圆磨理论培训资料

调整方法
调整工件的中心高,使其与砂轮中心一致。
调整工件的转速,以达到合适的切削速度。
常见故障及排除
砂轮不转或转速慢
检查砂轮的安装是否正确,如轴承是否损坏 。
检查电源线是否接触良好,电源是 否正常。
常见故障及排除
工件表面有划痕或烧伤
1
2
检查砂轮的粒度是否合适,如粒度过粗会导致划 痕。
3
检查工件夹具是否夹紧,切削液是否充足。
提高加工精度
通过采用更先进的数控系统 和优化磨削参数,可以提高 外圆磨的加工精度和稳定性
,减少误差和不良品率。
开发智能控制系统
通过引入人工智能、机器学 习等技术,开发智能控制系 统,实现对外圆磨加工过程 的实时监控和自动调整,提
高加工效率和产品质量。
拓展应用领域
通过开发适用于不同材料和 不同类型零件的外圆磨,拓 展外圆磨的应用领域,满足 更多行业的需求。
1.谢谢聆 听
精度控制的方法
使用高精度的砂轮和刀具
选择高精度砂轮和刀具是提高加工精度 的关键。
控制冷却液的使用
选择合适的冷却液种类、流量、压力 等,以保证加工表面的质量和精度。
调整设备的精度
根据加工要求,调整设备的主轴精度 、导轨精度、传动系统精度等。
采用先进的加工工艺
采用先进的加工工艺,如超精加工、 镜面加工等,可以提高加工表面的质 量和精度。
常见故障及排除
01
02
03
切削液流量不足
检查切削液的管道是否堵塞,喷嘴是 否堵塞。
检查切削液的液位是否过低,及时添 加切削液。
维修保养建议
01
定期检查砂轮的硬度和粒度,如需更换砂轮应由专业人 员操作。
瑞士studer外圆磨技术参数
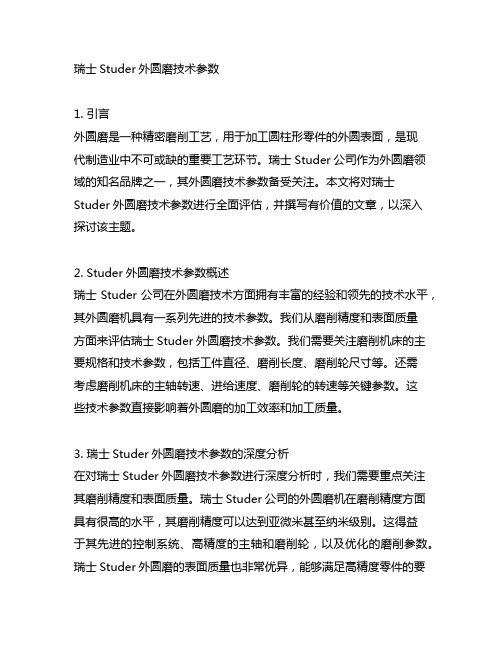
瑞士Studer外圆磨技术参数1. 引言外圆磨是一种精密磨削工艺,用于加工圆柱形零件的外圆表面,是现代制造业中不可或缺的重要工艺环节。
瑞士Studer公司作为外圆磨领域的知名品牌之一,其外圆磨技术参数备受关注。
本文将对瑞士Studer外圆磨技术参数进行全面评估,并撰写有价值的文章,以深入探讨该主题。
2. Studer外圆磨技术参数概述瑞士Studer公司在外圆磨技术方面拥有丰富的经验和领先的技术水平,其外圆磨机具有一系列先进的技术参数。
我们从磨削精度和表面质量方面来评估瑞士Studer外圆磨技术参数。
我们需要关注磨削机床的主要规格和技术参数,包括工件直径、磨削长度、磨削轮尺寸等。
还需考虑磨削机床的主轴转速、进给速度、磨削轮的转速等关键参数。
这些技术参数直接影响着外圆磨的加工效率和加工质量。
3. 瑞士Studer外圆磨技术参数的深度分析在对瑞士Studer外圆磨技术参数进行深度分析时,我们需要重点关注其磨削精度和表面质量。
瑞士Studer公司的外圆磨机在磨削精度方面具有很高的水平,其磨削精度可以达到亚微米甚至纳米级别。
这得益于其先进的控制系统、高精度的主轴和磨削轮,以及优化的磨削参数。
瑞士Studer外圆磨的表面质量也非常优异,能够满足高精度零件的要求。
瑞士Studer外圆磨机床的主要规格和技术参数也是其优越性能的重要保障。
其工件直径范围广泛,可以满足不同尺寸零件的加工需求;磨削长度和磨削轮尺寸的调整范围也很大,能够灵活应对各种加工任务。
瑞士Studer外圆磨的主轴转速、进给速度等参数都经过精心设计和优化,保证了磨削的稳定性和精度。
4. 总结和回顾通过对瑞士Studer外圆磨技术参数的全面评估,我们可以得出结论:瑞士Studer外圆磨技术参数在磨削精度、表面质量和机床性能方面表现出色。
其技术参数的优越性能,为高精度零件加工提供了有力保障。
在未来的制造业发展中,瑞士Studer外圆磨技术参数将继续发挥重要作用,并不断推动外圆磨技术的进步和发展。
外圆磨工艺

外圆磨工艺
外圆磨工艺是一种高精度加工技术,主要用于加工圆柱形工件的外表面。
该工艺可用于加工各种金属和非金属材料,如钢、铝、铜、塑料、陶瓷等。
外圆磨工艺具有以下特点:
1. 高精度:外圆磨工艺可实现较高的加工精度,通常达到0.001毫米的级别,因此适用于对工件精度要求较高的领域。
2. 高效率:由于磨削过程采用高速旋转的磨轮进行,因此加工速度较快,生产效率高。
3. 无损伤:与其他加工方法相比,外圆磨工艺对工件的表面和内部都没有明显的损伤,能够保证工件的质量和寿命。
4. 广泛应用:外圆磨工艺可应用于各种工件的加工,如轴、齿轮、滚筒等,因此在机械制造、汽车制造、航空航天等领域都有广泛应用。
外圆磨工艺的操作过程包括磨削前准备、选择磨削工具、设定磨削参数、磨削操作以及检验与修整等环节。
在操作过程中需要注意磨削精度的控制、磨削液的使用以及设备的维护等问题。
- 1 -。
外圆磨安全操作规程
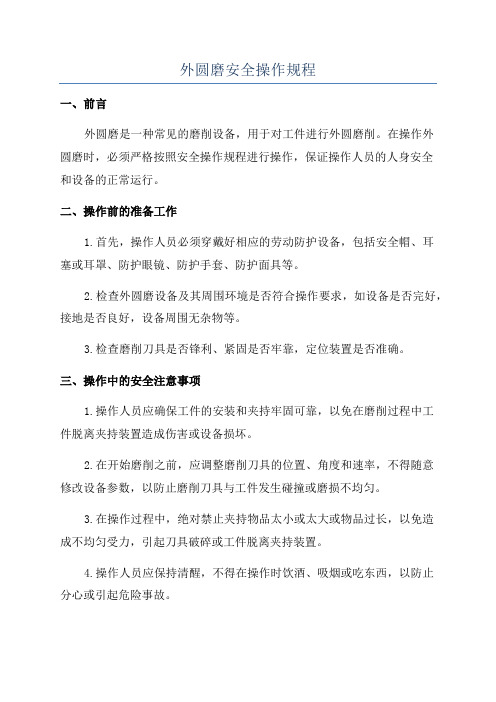
外圆磨安全操作规程一、前言外圆磨是一种常见的磨削设备,用于对工件进行外圆磨削。
在操作外圆磨时,必须严格按照安全操作规程进行操作,保证操作人员的人身安全和设备的正常运行。
二、操作前的准备工作1.首先,操作人员必须穿戴好相应的劳动防护设备,包括安全帽、耳塞或耳罩、防护眼镜、防护手套、防护面具等。
2.检查外圆磨设备及其周围环境是否符合操作要求,如设备是否完好,接地是否良好,设备周围无杂物等。
3.检查磨削刀具是否锋利、紧固是否牢靠,定位装置是否准确。
三、操作中的安全注意事项1.操作人员应确保工件的安装和夹持牢固可靠,以免在磨削过程中工件脱离夹持装置造成伤害或设备损坏。
2.在开始磨削之前,应调整磨削刀具的位置、角度和速率,不得随意修改设备参数,以防止磨削刀具与工件发生碰撞或磨损不均匀。
3.在操作过程中,绝对禁止夹持物品太小或太大或物品过长,以免造成不均匀受力,引起刀具破碎或工件脱离夹持装置。
4.操作人员应保持清醒,不得在操作时饮酒、吸烟或吃东西,以防止分心或引起危险事故。
5.警戒线必须设立在外圆磨设备周围,禁止非操作人员靠近设备,以免发生伤害事故。
6.禁止触摸或接近外圆磨刀具和磨削部位,以防止被夹持物品带动或磨削刀具碰撞造成伤害。
7.在磨削过程中,应注意保持工作区域的整洁,防止杂物进入到磨削刀具或夹持装置中。
四、操作后的注意事项1.停止外圆磨设备之前,应先停止给水系统,等待切削液完全停止流动后再切断电源。
2.磨削刀具和设备应进行及时的清洁和保养,以延长设备的使用寿命并保持磨削质量的稳定性。
3.操作结束后,应将设备周围的杂物清理干净,防止绊倒或其他意外事故的发生。
4.停机后,将外圆磨设备与电源断开,锁好开关箱,并将钥匙交给专人保管。
五、紧急事故的应急措施1.在外圆磨设备发生故障或异常情况时,应立即切断电源,并向维修人员报告。
2.发生人身伤害事故时,应立即停机、展开救援工作,保护受伤人员,并及时向医务人员求助。
外圆磨调锥度方法和过程
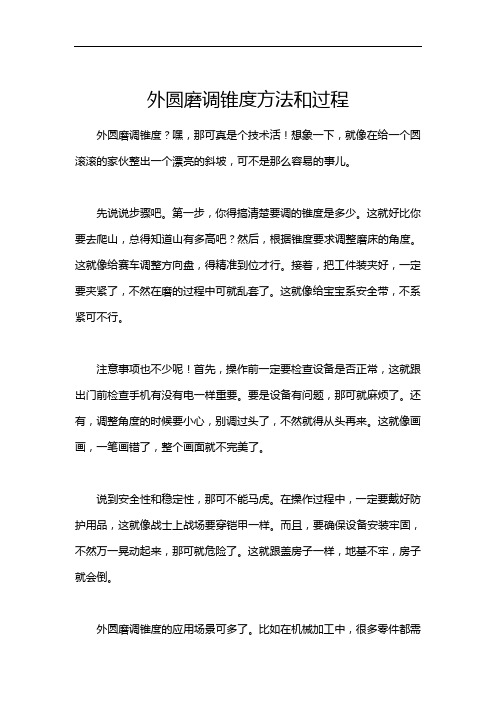
外圆磨调锥度方法和过程外圆磨调锥度?嘿,那可真是个技术活!想象一下,就像在给一个圆滚滚的家伙整出一个漂亮的斜坡,可不是那么容易的事儿。
先说说步骤吧。
第一步,你得搞清楚要调的锥度是多少。
这就好比你要去爬山,总得知道山有多高吧?然后,根据锥度要求调整磨床的角度。
这就像给赛车调整方向盘,得精准到位才行。
接着,把工件装夹好,一定要夹紧了,不然在磨的过程中可就乱套了。
这就像给宝宝系安全带,不系紧可不行。
注意事项也不少呢!首先,操作前一定要检查设备是否正常,这就跟出门前检查手机有没有电一样重要。
要是设备有问题,那可就麻烦了。
还有,调整角度的时候要小心,别调过头了,不然就得从头再来。
这就像画画,一笔画错了,整个画面就不完美了。
说到安全性和稳定性,那可不能马虎。
在操作过程中,一定要戴好防护用品,这就像战士上战场要穿铠甲一样。
而且,要确保设备安装牢固,不然万一晃动起来,那可就危险了。
这就跟盖房子一样,地基不牢,房子就会倒。
外圆磨调锥度的应用场景可多了。
比如在机械加工中,很多零件都需要有一定的锥度,这样才能更好地配合。
这就像拼图,只有形状合适了,才能拼在一起。
它的优势也很明显,能够精确地调整锥度,提高零件的精度和质量。
这就像给手机贴了个高清膜,看起来更清晰了。
我给你讲个实际案例吧。
有一次,我们接到一个订单,要求加工一批有锥度的零件。
刚开始大家都有点犯愁,不知道该怎么调锥度。
但是经过一番努力,我们终于找到了合适的方法。
最后加工出来的零件精度非常高,客户非常满意。
这就像打了一场胜仗,大家都特别有成就感。
外圆磨调锥度虽然有点难度,但是只要掌握了方法,注意安全,就能发挥出它的优势。
所以,大胆去尝试吧,你一定能成功!。
- 1、下载文档前请自行甄别文档内容的完整性,平台不提供额外的编辑、内容补充、找答案等附加服务。
- 2、"仅部分预览"的文档,不可在线预览部分如存在完整性等问题,可反馈申请退款(可完整预览的文档不适用该条件!)。
- 3、如文档侵犯您的权益,请联系客服反馈,我们会尽快为您处理(人工客服工作时间:9:00-18:30)。
用磨具以较高的线速度对工件表面进行加工的方法称为磨削。
磨削加工是一种多刀多刃的高速切削方法,它适用于零件精加工和硬表面的加工。
磨削的工艺范围很广,可以划分为粗磨、精磨、细磨及镜面磨。
各种磨削方案所能达到的经济加工精度和表面粗糙度值见表1。
表1 外圆表面加工方案磨削加工采用的磨具(或磨料)具有颗粒小,硬度高,耐热性好等特点,因此可以加工较硬的金属材料和非金属材料,如淬硬钢、硬质合金刀具、陶瓷等;加工过程中同时参与切削运动的颗粒多,能切除极薄极细的切屑,因而加工精度高,表面粗糙度值小。
磨削加工作为一种精加工方法,在生产中得到广泛应用。
目前,由于强力磨削的发展,也可以直接将毛坯磨削到所需要的尺寸和精度,从而获得了较高的生产率。
1.砂轮的特性与选择砂轮是磨削加工中最主要的一类磨具。
砂轮是在磨料中加进结合剂,经压坯、干燥和培烧而制成的多孔体。
由于磨料、结合剂及制造工艺等不同,砂轮的特性差别很大,因此对磨削的加工质量、生产率和经济性有着重要影响。
砂轮的特性主要是由磨料、粒度、结合剂、硬度、组织、外形和尺寸等因素决定的。
(1)磨料磨料是砂轮的主要组成成分,它应具有很高的硬度、耐磨性、耐热性和一定的韧性,以承受磨削时的切削热和切削力,同时还应具备锋利的尖角,以利磨削金属。
常用磨料代号、特点及应用范围见表2。
表2 常用磨料代号、特性及适用范围(2)粒度粒度是指磨料颗粒尺寸的大小。
粒度分为磨粒和微粉两类。
对于颗粒尺寸大于40μm的磨料,称为磨粒。
用筛选法分级,粒度号以磨粒通过的筛网上每英寸长度内的孔眼数表示。
如60#的磨粒表示其大小恰好能通过每英寸长度上有60孔眼的筛网。
对于颗粒尺寸小于40μm的磨料,称为微粉。
用显微丈量法分级,用W和后面的数字表示粒度号,其W后的数值代表微粉的实际尺寸。
如W20表示微粉实际尺寸为20μm。
砂轮的粒度对磨削表面的粗糙度和磨削效率影响很大。
磨粒粗,磨削深度大,生产率高,但表面粗糙度值大。
反之,则磨削深度均匀,表面粗糙度值小。
所以粗磨时,一般选粗粒度,精磨时选细粒度。
磨软金属时,多选用粗磨粒,磨削脆而硬材料时,则选用较细的磨粒。
粒度的选用见表3。
表3 磨料粒度的选用(3)结合剂结合剂是把磨粒粘结在一起组成磨具的材料。
砂轮的强度、抗冲击性、耐热性及耐腐蚀性,主要取决于结合剂的种类和性质。
常用结合剂的种类、性能及适用范围见表4。
表4 常用结合剂的种类、性能及适用范围(4)硬度砂轮硬度是指砂轮工作时,磨粒在外力作用下脱落的难易程度。
砂轮硬,表示磨粒难以脱落;砂轮软,表示磨粒轻易脱落。
砂轮的硬度等级见表5。
表5 砂轮的硬度等级及代号砂轮的硬度与磨料的硬度是两个完全不同的概念。
硬度相同的磨料可以制硬度成不同的砂轮,砂轮的硬度主要决定于结合剂性质、数目和砂轮的制造工艺。
例如,结合剂与磨粒粘固程度越高,砂轮硬度越高。
砂轮硬度的选用原则是:工件材料硬,砂轮硬度应选用软一些,以便砂轮磨钝磨粒及时脱落,露出锋利的新磨粒继续正常磨削;工件材料软,因易于磨削,磨粒不易磨钝,砂轮应选硬一些。
但对于有色金属、橡胶、树脂等软材料磨削时,由于切屑轻易堵塞砂轮,应选用较软砂轮。
粗磨时,应选用较软砂轮;而精磨、成形磨削时,应选用硬一些砂轮,以保持砂轮的必要外形精度。
机械加工中常用砂轮硬度等级为H至N(软2-中2)。
(5)组织砂轮的组织是指组成砂轮的磨粒、结合剂、气孔三部分体积的比例关系。
通常以磨粒所占砂轮体积的百分比来分级。
砂轮有三种组织状态:紧密、中等、疏松;细分成0~14中间,共15级。
组织号越小,磨粒所占比例越大,砂轮越紧密;反之,组织号越大,磨粒比例越小。
砂轮越疏松。
见表6。
表6 砂轮组织分类(6)外形与尺寸砂轮的外形和尺寸是根据磨床类型、加工方法及工件的加工要求来确定的。
常用砂轮名称、外形简图、代号和主要用途见表7。
表7 常用砂轮外形、代号和用途砂轮的特性均标记在砂轮的侧面上,其顺序是:外形代号、尺寸、磨料、粒度号、硬度、组织号、结合剂、线速度。
例如:外径300mm,厚度50mm,孔径75mm,棕刚玉,粒度60,硬度L,5号组织,陶瓷结合剂,最高工作线速度35 m/s的平行砂轮,其标记为:砂轮1-300×55×75-A60L5V-35m/s GB2484-94。
2.外圆磨床的磨削方法外圆表面磨削一般在外圆磨床或无心外圆磨床上进行,也可采用砂带磨床磨削。
在外圆磨床上磨削工件外圆时,轴类零件常用顶尖装夹,其方法与车削时基本相同,但磨床所用顶尖不随工件一起转动。
这样,主轴与轴承的制造误差、轴承间隙、顶尖的同轴度误差等就不会反映到工件上,可进步加工精度。
盘套类工件则专心轴和顶尖装夹,所专心轴和车削心轴基本相同,只是外形和位置精度以及表面粗糙度要求较严格。
磨削短又无中心孔的轴类工件时,可用三爪自定心卡盘或四爪单动卡盘装夹。
在外圆磨床上上常用的磨削方法有:(1)纵磨法如图1(a),砂轮高速旋转起切削作用,工件旋转作圆周进给运动,并和工作台一起作纵向往复直线进给运动。
工作台每往复一次,砂轮沿磨削深度方向完成一次横向进给,每次进给(吃刀深度)都很小,全部磨削余量是在多次往复行程中完成的。
当工件磨削接近终极尺寸时(尚有余量0.005~0.01mm),应无横向进给光磨几次,直到火花消失为止。
纵磨法加工精度和表面质量较高,适应性强,用同一砂轮可磨削直径和长度不同的工件,但生产率低。
在单件、小批量生产及精磨中,应用广泛,特别适用于磨削细长轴等刚性差的工件。
图1 外圆磨床的磨削方法(2)横磨法(切进法)如图1(b),磨削时,工件不作纵向往复运动,砂轮以缓慢的速度连续或中断地向工件作横向进给运动,直到磨往全部余量。
横磨时,工件与砂轮的接触面积大,磨削力大,发热量大而集中,所以易发生工件变形、烧刀和退火。
横磨法生产效率高,适用于成批或大量生产中,磨削长度短、刚性好、精度低的外圆表面及两侧都有台肩的轴颈。
若将砂轮修整成形,也可直接磨削成形面。
(3)综合磨法如图1(c),先用横磨法将工件分段进行粗磨,相邻之间有5~15mm的搭接,每段上留有0.01~0.03mm的精磨余量,精磨时采用纵磨法。
这种磨削方法综合了纵磨和横磨法的优点,适用于磨削余量较大(余量0.7~0.6mm)的工件。
(4)深磨法如图1(d),磨削时,采用较小的纵向进给量(1~2mm/r)和较大的吃刀深度(0.2~0.6mm)在一次走刀中磨往全部余量。
为避免切削负荷集中和砂轮外圆棱角迅速磨钝,应将砂轮修整成锥形或台阶形,外径小的台阶起粗磨作用,可修粗些;外径大的起精磨作用,修细些。
深磨法可获得较高精度和生产率,表面粗糙度值较小,适用于大批大量生产中,加工刚性好的短轴。
3.无心外圆磨床的磨削方法在无心磨床磨削工件外圆时,工件不用顶尖来定心和支承,而是直接将工件放在砂轮和导轮(用橡胶结合剂作的粒度较粗的砂轮)之间,由托板支承,工件被磨削的外圆面作定位面,见图2(a)。
无心外圆磨床有两种磨削方式。
图2 无心外圆磨削的加工示意图(1)贯串磨削法(纵磨法)如图2(b),磨削时将工件从机床前面放到托板上,推进磨削区,由于导轮轴线在垂直平面内倾斜α角(α=1-6°),导轮与工件接触处的线速度v导可以分解成水平和垂直两个方向的分速度v导水平和v导垂直,v导垂直控制工件的圆周进给运动;v导水平使工件作纵向进给。
所以工件进进磨削区后,便既作旋转运动,又作轴向移动,穿过磨削区,工件就磨削完毕。
α角增大、生产率高,但表面粗糙度值增大;反之,情况相反。
为保证导轮与工件呈线接触状态,需将导轮外形修整成回转双曲面形。
这种磨削方法不适用带台阶的圆柱形工件。
(2)切进磨削法(横磨法)光将工件放在托板和导轮之间,然后由工件(连同导轮)或磨削砂轮横向切进进给,磨削工件表面。
这时导轮的中心线仅倾斜很小角度(约30'),以便对工件产生一微小的轴向推力,使它靠住挡板,得到可靠轴向定位,见图2(c)。
切进磨法适用于磨削有门路或成形回转表面的工件,但磨削表面长度不能大于磨削砂轮宽度。
在磨床上磨削外圆表面时,应采用充足的切削液,一般磨钢件多用苏打水或乳化液;铝件采用加少量矿物油的煤油;铸铁、青铜件一般不用切削液,而用吸尘器清除尘屑。
4.M1432A型万能外圆磨床M1432A型万能外圆磨床主要用于磨削内外圆柱面、内外圆锥面、门路轴轴肩以及端面和简单的成形回转表面等。
它属于普遍精度级机床,磨削精度可达IT7~IT6级,表面粗糙度值在1.25~0.08μm之间。
这种机床万能性强,但自动化程度较低,磨削效率不高,适用于工具车间,维修车间和单件小批生产类型。
其主参数为:最大磨削直径为320mm。
1—床身 2—头架 3—内圆磨具 4—砂轮架 5—尾架 6—滑鞍 7—脚踏操纵板图3 M1432A型万能外圆磨床图3为M1432A型万能外圆磨床外形图。
由图可见,在床身1的纵向导轨上装有工作台8,台面上装有头架2和尾架5,用以夹持不同长度的工件,头架带动工件旋转。
工作台由液压传动沿床身导轨往复移动,使工件实现纵向进给运动。
工作台由上下两层组成,其上部可相对下部在水平面内偏转一定的角度(一般不大于±10°),以便磨削锥度不大的圆锥面。
砂轮架4安装在滑鞍6上,转动横向进给手轮7,通过横向进给机构带动滑鞍及砂轮架作快速进退或周期性自动切进进给。
内圆磨具3放下时用以磨削内圆(图示处于抬起状态)。
图4 万能外圆磨床典型加工示意图图4为万能外圆磨床的典型加工方法:图4(a)为用纵磨法磨削外圆柱面,图4(b)为扳转工作台用纵磨法磨削长圆锥面,图4(c)为扳动砂轮架用切进法磨削短圆锥面,图4(d)为扳动头架用纵磨法磨削圆锥面,图4(e)为用内圆磨具磨削圆柱孔。
分析M1432A型万能外圆磨床的典型加工方法可知,机床必须具备以下运动:外圆磨和内圆磨砂轮的旋转主运动;工件圆周进给运动;工件(工作台)往复纵向进给运动;砂轮横向进给运动。
此外,机床还应有两个辅助运动:砂轮横向快速进退和尾架套筒缩回,以便装卸工件。