延长催化剂寿命,保证加氢装置长周期运行
裂解汽油加氢两段催化剂长周期运行
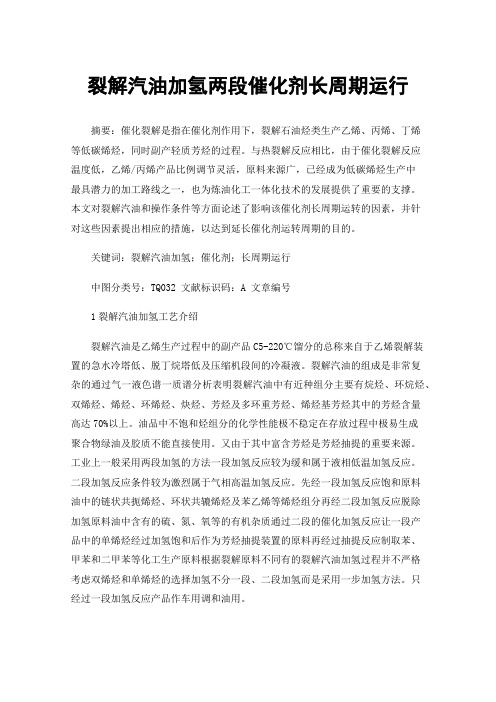
裂解汽油加氢两段催化剂长周期运行摘要:催化裂解是指在催化剂作用下,裂解石油烃类生产乙烯、丙烯、丁烯等低碳烯烃,同时副产轻质芳烃的过程。
与热裂解反应相比,由于催化裂解反应温度低,乙烯/丙烯产品比例调节灵活,原料来源广,已经成为低碳烯烃生产中最具潜力的加工路线之一,也为炼油化工一体化技术的发展提供了重要的支撑。
本文对裂解汽油和操作条件等方面论述了影响该催化剂长周期运转的因素,并针对这些因素提出相应的措施,以达到延长催化剂运转周期的目的。
关键词:裂解汽油加氢;催化剂;长周期运行中图分类号:TQ032 文献标识码:A 文章编号1裂解汽油加氢工艺介绍裂解汽油是乙烯生产过程中的副产品C5-220℃馏分的总称来自于乙烯裂解装置的急水冷塔低、脱丁烷塔低及压缩机段间的冷凝液。
裂解汽油的组成是非常复杂的通过气一液色谱一质谱分析表明裂解汽油中有近种组分主要有烷烃、环烷烃、双烯烃、烯烃、环烯烃、炔烃、芳烃及多环重芳烃、烯烃基芳烃其中的芳烃含量高达70%以上。
油品中不饱和烃组分的化学性能极不稳定在存放过程中极易生成聚合物绿油及胶质不能直接使用。
又由于其中富含芳烃是芳烃抽提的重要来源。
工业上一般采用两段加氢的方法一段加氢反应较为缓和属于液相低温加氢反应。
二段加氢反应条件较为激烈属于气相高温加氢反应。
先经一段加氢反应饱和原料油中的链状共扼烯烃、环状共辘烯烃及苯乙烯等烯烃组分再经二段加氢反应脱除加氢原料油中含有的硫、氮、氧等的有机杂质通过二段的催化加氢反应让一段产品中的单烯烃经过加氢饱和后作为芳烃抽提装置的原料再经过抽提反应制取苯、甲苯和二甲苯等化工生产原料根据裂解原料不同有的裂解汽油加氢过程并不严格考虑双烯烃和单烯烃的选择加氢不分一段、二段加氢而是采用一步加氢方法。
只经过一段加氢反应产品作车用调和油用。
在整个乙烯生产装置中裂解汽油加氢装置所处在的位置十分重要。
它处在热气裂解制乙烯装置和芳烃抽提装置之间起到了承卜启下的作用。
若解汽油加氢装置开得不好有可能迫使乙烯装置减产甚至停车进而影响到后面使用芳烃原料的装置运行如使苯酚丙酮装置、苯乙烯装置减产、停产。
汽油加氢装置操作工考试试题及答案二

汽油加氢装置操作工考试试题及答案二1、单选在恩氏蒸馏中,当馏出第一滴冷凝液时的气相温度称为()。
A、滴点B、沸点C、终馏点D、初馏点正确答案:D2、问答题氢分压对加氢反应有何(江南博哥)影响?正确答案:加氢反应是放热、消耗氢气和体积缩小的反应过程,提高氢分压,有利于反应化学平衡向正方向移动,从而提高加氢反应深度,防止催化剂结焦,提高产品质量,延长催化剂使用寿命。
氢分压地,则作用相反,原料油结焦催化剂积炭的速度加大。
3、填空题系统压力主要是由()的大小来调节的正确答案:新氢量4、问答题出入口气阀的作用是什么?它们是怎样工作的?正确答案:吸气阀和排气阀是压缩机完成其工作循环的重要部件之一,它的开闭运动应与活塞的往复运动相配合才能正确地完成压缩机的吸气、压缩、排气和余气膨胀过程。
在吸气过程中,当气缸内压力降低到低于管道内的压力时,吸气阀在内外压力差的作用下开启,气体进入气缸,在压缩过程中,吸、排气阀均保持密闭。
在排气过程中,当气缸内的压力升到高于排气管道内的压力时,排气阀开启。
在余气膨胀过程中,吸排气阀均保持密闭。
5、填空题35万吨/年汽油加氢装置采用OCT-M选择性加氢脱硫工艺技术加工催化汽油,采用()催化剂生产满足国Ⅳ排放标准的汽油产品。
正确答案:FGH-21、FGH-316、问答题脱硫塔为什么要排烃?正确答案:在生产过程中,脱硫塔的原料气难免夹带有少量的轻烃或油,在这种油或烃积聚过多,就会使胺液产生大量的泡沫,影响脱硫效果;严重时,这种泡沫会沿塔而上,造成脱后气体带液和跑胺事故的发生,影响下游的操作。
所以,要定期对脱硫塔的胺液进行排烃,保持溶剂的清洁。
7、问答题如何做好加热炉火嘴的燃烧控制?正确答案:加热炉的大多数故障是因燃烧控制而引起的,必须加强控制、维护和管理,具体要求如下:①火焰形状应稳定、多火嘴、短火焰、齐火苗。
②火焰不应触及管壁和炉墙。
③火嘴的燃料气压力和温度应适当。
④火嘴口不得积焦和堵塞,如有积焦和堵塞则要清理干净。
原料油性质对柴油加氢装置长周期稳定运行的影响
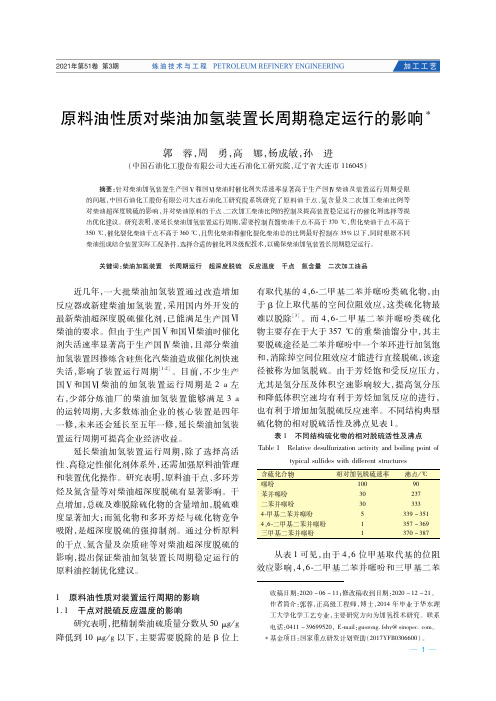
原料油性质对柴油加氢装置长周期稳定运行的影响郭 蓉,周 勇,高 娜,杨成敏,孙 进(中国石油化工股份有限公司大连石油化工研究院,辽宁省大连市116045)摘要:针对柴油加氢装置生产国Ⅴ和国Ⅵ柴油时催化剂失活速率显著高于生产国Ⅳ柴油及装置运行周期受限的问题,中国石油化工股份有限公司大连石油化工研究院系统研究了原料油干点、氮含量及二次加工柴油比例等对柴油超深度脱硫的影响,并对柴油原料的干点、二次加工柴油比例的控制及提高装置稳定运行的催化剂选择等提出优化建议。
研究表明,要延长柴油加氢装置运行周期,需要控制直馏柴油干点不高于370℃,焦化柴油干点不高于350℃,催化裂化柴油干点不高于360℃,且焦化柴油和催化裂化柴油总的比例最好控制在35%以下,同时根据不同柴油组成结合装置实际工况条件,选择合适的催化剂及级配技术,以确保柴油加氢装置长周期稳定运行。
关键词:柴油加氢装置 长周期运行 超深度脱硫 反应温度 干点 氮含量 二次加工油品 近几年,一大批柴油加氢装置通过改造增加反应器或新建柴油加氢装置,采用国内外开发的最新柴油超深度脱硫催化剂,已能满足生产国Ⅵ柴油的要求。
但由于生产国Ⅴ和国Ⅵ柴油时催化剂失活速率显著高于生产国Ⅳ柴油,且部分柴油加氢装置因掺炼含硅焦化汽柴油造成催化剂快速失活,影响了装置运行周期[1 2]。
目前,不少生产国Ⅴ和国Ⅵ柴油的加氢装置运行周期是2a左右,少部分炼油厂的柴油加氢装置能够满足3a的运转周期,大多数炼油企业的核心装置是四年一修,未来还会延长至五年一修,延长柴油加氢装置运行周期可提高企业经济收益。
延长柴油加氢装置运行周期,除了选择高活性、高稳定性催化剂体系外,还需加强原料油管理和装置优化操作。
研究表明,原料油干点、多环芳烃及氮含量等对柴油超深度脱硫有显著影响。
干点增加,总硫及难脱除硫化物的含量增加,脱硫难度显著加大;而氮化物和多环芳烃与硫化物竞争吸附,是超深度脱硫的强抑制剂。
通过分析原料的干点、氮含量及杂质硅等对柴油超深度脱硫的影响,提出保证柴油加氢装置长周期稳定运行的原料油控制优化建议。
催化装置长周期运行措施演讲稿

沉降器跑剂
·02年我厂二催化沉降器跑剂,坚持半年多后停
工。检查发现旋分升气管焊缝开裂。
·05年中石油某催化在处理系统停电时升气管上
热电偶的焦团脱落,堵塞料腿停工。
再生器跑剂: 再生器跑剂:
·我厂二催化再生器二级料腿曾出现两次料腿
磨穿失效跑剂停工。改进料腿方向并外包 衬里来解决。
·我厂三催化曾出现双动滑阀导轨失效,引起
·防止再生器开裂的措施:提高壁温
减少衬里厚度,由150mm降至120mm。再生器外 保温。 再生器材质用16MnR或20g,不用A3R。
2.3.3催化剂的使用和管理 . . 催化剂的使用和管理
·催化剂质量:活性、稳定性、选择性,流化性能
,平稳加料,少量多次。定期做分析,并建立技术 台帐。
·催化剂成像技术:对催化剂破碎、对催化剂跑损
中国石化茂名公司
催化装置长周期运行的措施
1. 装置长周期运行的主要障碍
1•1催化剂大量跑损, 系统无法维持 , 装置被 催化剂大量跑损,系统无法维持, 催化剂大量跑损 迫停工 跑损分两种: 跑损分两种: 设备失效跑损、流化问题跑损。 设备失效跑损: 设备失效跑损: 翼阀卡涩(高温变形、结焦)、料腿堵塞 (结焦、焦块、衬里脱落、催化剂架桥)、料腿 穿孔、旋分其它部位焊缝开裂,烟气(油气)走 短路。各种特阀—滑阀、塞阀、双动滑阀、放火 炬阀、蝶阀失效,如滑阀阀杆磨断,导轨脱落。
·分馏塔底设油浆急冷油搅拌,塔内加滤焦器,
塔底外加过滤器。
·油浆循环量尽可能大,提高换热器线速,下返
塔最大流量控制,塔底温度控330~350℃。
·缩短停留时间。塔液面控制30-50%。 ·加注油浆阻垢剂。
2.3提高管理水平,注重技术进步 . 提高管理水平 提高管理水平, 严格执行各项规章制度,按时修订操作 规程和工艺卡片。做好技术分析工作,根据 装置运行中出现的各种问题制定临时处理方 案。对生产过程中出现的疑难问题组织技术 攻关,聘请专家指导。认真学习同类型装置 长周期生产的好经验,总结或吸取经验教训 ,提高管理水平。
格尔木炼油厂催化装置长周期运行总结
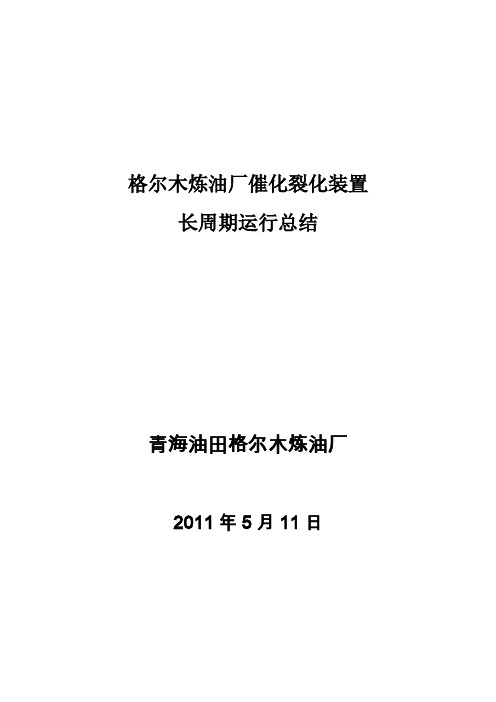
格尔木炼油厂催化裂化装置长周期运行总结青海油田格尔木炼油厂2011年5月11日格尔木炼油厂催化裂化装置长周期运行总结格尔木炼油厂始建于1991年,加工规模为100万吨/年,2009年经过产品质量升级改造以后,全厂炼油装置配套更加完善,加工规模有所增加。
其中催化装置由原来的60万吨/年扩至90万吨/年,原料也由加工常压渣油变为加工减压渣油。
现对装置近一个周期运行情况进行总结。
一、装置简介格尔木炼油厂催化裂化装置原由洛阳石化工程公司设计,采用沉降器与一再同轴、一再和二再高低并列的结构形式。
原设计处理量为60×104t/a,于1993年投产。
2009年装置改造进料改为大于460℃的减压渣油,残炭8.65(w%),装置处理量提高到90×104t/a。
装置主要由反应再生部分、分馏部分、吸收稳定部分、余热锅炉以及三机组和气压机组成。
针对改炼减压渣油后烧焦量增加的情况,在2009年改造时更换了第二再生器并在第二再生器底部增加后置烧焦罐,采用快速床+湍流床的再生形式,取消原脱气罐更换为再生斜管。
第二再生器旋分器由外置更换为内置三组两级旋分器。
第一、二再生器产生的烟气由改造前的合流改为分流。
原一再烟气管道利旧,新增二再烟气管道及二再三级旋风分离器、四级旋风分离器、降压孔板、双动滑阀及免维护临界流速喷嘴。
一、二再烟气分流后避免了烟气的二次燃烧,故取消原高温取热炉,新增一再CO余热锅炉,回收一再烟气中未完全燃烧产生的化学能。
二再烟气进入原余热锅炉进行余热回收。
分馏塔下层脱过热段为“人”字挡板,上部采用29层SUPER VI型塔盘,整个分馏塔设有顶循环回流、中段回流、油浆循环回流、回炼油循环回流;吸收稳定采用吸收与解吸双塔流程,主要设备有吸收塔、解吸塔、再吸收塔和稳定塔。
一再余热锅炉采用塔式模块结构形式,单锅筒自然循环,斜管排式和蛇形管式对流受热面;锅炉为正压运行,锅炉烟道四周为护板密封,设有燃气脉冲激波吹灰系统。
浆态床渣油加氢长周期运行问题及优化措施
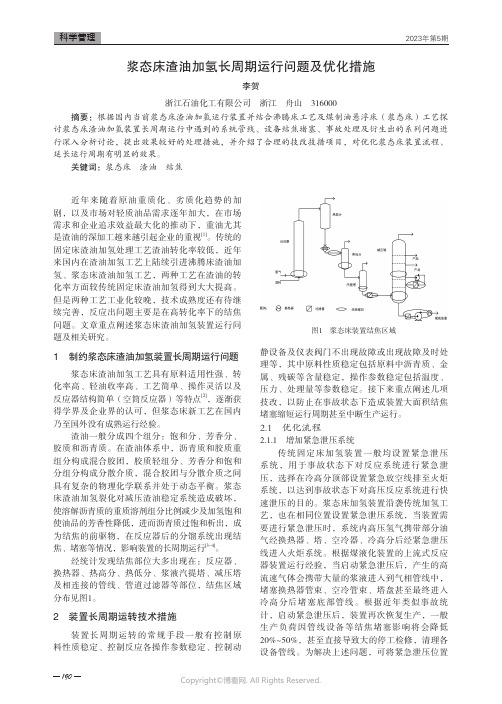
190近年来随着原油重质化、劣质化趋势的加剧,以及市场对轻质油品需求逐年加大,在市场需求和企业追求效益最大化的推动下,重油尤其是渣油的深加工越来越引起企业的重视[1]。
传统的固定床渣油加氢处理工艺渣油转化率较低,近年来国内在渣油加氢工艺上陆续引进沸腾床渣油加氢、浆态床渣油加氢工艺,两种工艺在渣油的转化率方面较传统固定床渣油加氢得到大大提高。
但是两种工艺工业化较晚,技术成熟度还有待继续完善,反应出问题主要是在高转化率下的结焦问题。
文章重点阐述浆态床渣油加氢装置运行问题及相关研究。
1 制约浆态床渣油加氢装置长周期运行问题浆态床渣油加氢工艺具有原料适用性强、转化率高、轻油收率高、工艺简单、操作灵活以及反应器结构简单(空筒反应器)等特点[2],逐渐获得学界及企业界的认可,但浆态床新工艺在国内乃至国外没有成熟运行经验。
渣油一般分成四个组分:饱和分、芳香分、胶质和沥青质。
在渣油体系中,沥青质和胶质重组分构成混合胶团,胶质轻组分、芳香分和饱和分组分构成分散介质,混合胶团与分散介质之间具有复杂的物理化学联系并处于动态平衡。
浆态床渣油加氢裂化对减压渣油稳定系统造成破坏,使溶解沥青质的重质溶剂组分比例减少及加氢饱和使油品的芳香性降低,进而沥青质过饱和析出,成为结焦的前驱物,在反应器后的分馏系统出现结焦、堵塞等情况,影响装置的长周期运行[3-4]。
经统计发现结焦部位大多出现在:反应器、换热器、热高分、热低分、浆液汽提塔、减压塔及相连接的管线、管道过滤器等部位,结焦区域分布见图1。
2 装置长周期运转技术措施装置长周期运转的常规手段一般有控制原料性质稳定、控制反应各操作参数稳定、控制动静设备及仪表阀门不出现故障或出现故障及时处理等,其中原料性质稳定包括原料中沥青质、金属、残碳等含量稳定,操作参数稳定包括温度、压力、处理量等参数稳定。
接下来重点阐述几项技改,以防止在事故状态下造成装置大面积结焦堵塞缩短运行周期甚至中断生产运行。
加氢岗位试题
常减压车间加氢岗位试题一、填空S浓度,提高脱硫反1、本装置设置循环氢脱硫设施,目的是降低循环氢中的H2应深度,一般要求脱硫后循环氢中硫化氢含量小于(100PPm)2、汽提塔顶设注缓蚀剂设施,以减轻塔顶流出物中( 硫化氢)对塔顶系统的腐蚀3、设置预分馏塔分离轻、重汽油,采用(中压蒸汽)作重沸热源。
4、为防止反应器因进料中的固体颗粒堵塞导致反应器(压降)过大,设原料油过滤器,脱除重汽油中大于25微米的固体颗粒,减缓反应器压降增长速度,延长装置操作周期。
5、加氢催化剂活性金属组分为氧化态,为了提高催化剂活性,新鲜的或再生后的催化剂在使用前都必须进行(预硫化)。
6、加氢催化剂活性金属组分为氧化态,为了提高催化剂活性,新鲜的或再生后的催化剂在使用前都必须进行预硫化,使用的硫化剂为DMDS,其分解温度为( 200℃)7、过高的反应温度导致产品辛烷值的下降,在实际操作中,在满足产品质量要求的情况下,尽可能使反应温度(降低)8、反应器的一段温度主要通过调节 ( 加热炉出口温度 )进行控制,二段温度由( 冷氢 )进行控制9、随着加氢脱硫反应的进行,会伴随一定的烯烃饱和反应,烯烃饱和为强放热过程,释放出的热量会引起( 床层温度 )上升10、如果装置需要降低处理量,则应遵循(先降温后降量的原则),避免高温低空速操作;反之,先提高处理量,后适当提高反应温度11、在催化剂预硫化过程中,循环氢中的氢浓度应维持( 80%)以上。
12、精馏塔内上升气相速度过高,会产生( 雾沫夹带 )。
13、、蒸汽再沸器降温速率一般不大于( 30 )℃/h,防止因降温不均匀出现泄漏。
14、精馏操作中,若回流比增加,则( 塔顶轻组分含量升高、塔顶产品纯度上升 )。
15、原料油过滤器的作用是除去原料中的机械杂质,目的是为了(减少原料杂质),(降低床层压降),(保护催化剂)。
16、汽油中的烯烃加氢饱和后,辛烷值变(小)。
17、如何在加氢脱硫的同时,减少(烯烃的饱和)是催化裂化汽油选择性加氢脱硫技术核心。
高稳定性超深度脱硫催化剂RS-3100在柴油加氢装置的工业应用
石油炼制与化工PETROLEUM PROCESSING AND PETROCHEMICALS2021年6月第52卷第6期催化剂高稳定性超深度脱硫催化剂RS-3100在柴油加氢装置的工业应用邹圣武,罗凯(中国石化九江分公司,江西九江332004)摘要:RS-3100催化剂是中国石化石油化工科学研究院开发的高稳定性超深度加氢脱硫催化剂,首次在中国石化九江分公司1.20Mt/a柴油加氢装置进行了工业应用。
该装置于2020年4月一次开车成功,加工焦化汽柴油、催化裂化柴油和直馏柴油的混合原料,产品柴油硫质量分数小于10pg/g,多环芳烃质量分数小于7%,达到了国可车用柴油标准的要求。
工业标定结果表明,RS-3100催化剂具有良好的活性和稳定性,能够处理二次加工油比例为50%的劣质原料,稳定生产国可柴油。
关键词:柴油加氢超深度脱硫催化剂高稳定性汽车尾气所造成的环境污染问题已在全球范围内引起了广泛重视。
柴油作为重要的车用燃料,燃烧后排放废气中所含有的硫氧化物(SOJ、氮氧化物(NOJ和颗粒物(PM)等是导致大气污染的重要原因[1]。
根据我国已经完成的第一批城市大气细颗粒物(PM2.5)源解析结果,柴油车排放是北京、上海、广州、深圳和杭州等大城市PM2.5的首要来源2。
因此,生产环境友好的低硫或超低硫柴油已成为世界各国政府和炼油企业普遍重视的问题。
美、日、欧等国家和地区的炼油厂已经普遍在向市场供应硫质量分数不大于10pg/g的超低硫柴油产品。
我国于2017年1月1日实施了国V柴油标准,2019年1月1日实施了国巾柴油标准,国巾标准要求柴油中的硫质量分数不大于10pg/g,多环芳烃质量分数不大于7%。
柴油加氢精制是实现柴油质量升级的最有效手段,但柴油产品低硫、低芳烃的要求导致工业加氢装置运转周期大幅缩短,严重影响企业效益。
根据现有装置条件,使用高活性、高稳定性的柴油超深度脱硫催化剂是实现柴油质量升级的最有效途径。
MTBE装置长周期平稳运行探讨
一
一
…
艺与
第4 1卷第 3期
杨 开研 ,等 :M B T E装置长周期平稳运行探讨
27 5
12 催 化 剂反 应原 理 . 目前合 成 MT E的催 化剂 有分 子筛 催化 剂 、填 B
催化剂 中的活性基 团磺酸根结合 ,变成磺酸盐 ,使 其失 去 酸 I 生而失 活 ;甲醇 原料如 果呈 弱碱 性 ,与酸 性催化剂反应 ,也会使其中毒而失活。所以 , 要严 格控 制 c 原料 中金 属离 子 , 选择 购买 符合 生产要 求
9
化剂 用 量 为 4 ,装 填情 况如 表 1 3t 所示 。
表 1 MT E装 置 催 化 剂 装 填 量 B
9 8 1 9 9 2 9 9 8 9 8 3
催化 蒸馏 塔催 化剂 床层 会 出现短 时 间超温 现象 。通
9 9 6
甲基叔 丁基 醚 ( B 是 一种无 色 透 明液体 , MT E)
者混 合后 ,经 反应进 料 过滤器 除 杂后 ,于 醚化反 应
具有 较 高 的辛 烷值 (O , N 11 , 毒 无腐 R N 17 MO 0) 无 1 蚀 , 可 以降低 汽油尾 气 的污染 。 他 具有 十分 良好 的抗 爆 炸性 能和较 好 的化学 稳定 性 ,是优 良的含 氧 、无 铅 、低 芳 烃 新 配 方 汽 油 的优 良调 和 组 分 。另 外 , MT E 有较 好 的化 学 稳 定性 ,难 于 氧化 ,在作 为 B具 反应 溶 剂 、 取剂 和色谱 液 等方 面也具 有 多种 用途 。 萃
M 3 产 品 出 装 置 T1 E
1C - 4原 料罐 ;2 甲醇 原料 罐 ;3 预过 滤器 ;4 醚化 反应 器 ;5 催 - 一 一 - 化 蒸 馏塔 ;6催 化 蒸 馏塔 回流罐 ;7 甲醇 萃 取塔 ;8 甲醇 回收塔 ;9 一 - - 一 甲醇 回收塔 回流罐
长周期运行管理办法(综合版)(1)
炼化公司生产装置长周期运行管理办法(讨论稿)第一章总则第一条为了进一步加强炼化公司生产管理,大力降低生产成本,努力较减少非计划停工,提高装置运行效率和公司整体经济效益,激发职工的工作热情和积极性,实现公司炼油化工装置长周期运行的目标,特制订本办法。
第二条本办法适用于公司炼油(常压、催化裂化、重整、苯抽提、柴油加氢)、化工(聚丙烯、液化气及干气精制、气体分馏、MTBE、乙苯/苯乙烯)等主要生产装置。
第三条本办法对公司各厂炼油化工装置的运行周期实行统一计算,分级考核的管理办法,炼化公司机动设备部负责公司长周期运行管理和考核。
各厂机动科为本厂生产装置长周期运行日常管理部门。
第四条装置长周期运行的原则是在安全和经济效益的前提下,采用科学的手段和方法,保持和维护设备、设施性能,延长运行周期,确保装置实现安全、平稳、优质、高效运行。
第二章长周期运行的有关定义和指标计算第五条装置运行周期:是指装置在两个停工大修之间的运行时间段(从停工大检修后连续装置进料开始至切断进料准备停工大检修止),以天计算。
“三年两修”是指装置连续运行17个月,运行周期不低于510天,安排一次大修;“两年一修”是指装置连续运行23个月,运行周期日不低于690天,安排一次大修;“三年一修”是指装置连续运行35个月,运行周期日不低于1050天,安排一次大修;“四年一修”是指装置连续运行47个月,运行周期日不低于1410天,安排一次大修;第六条生产装置可靠度1、可靠度=(运行周期日-非计划停工-装置临修)/运行周期日×100%2、生产装置可靠度“三年两修”应不低于98.5%“两年一修”应不低于98%“三年一修”应不低于98%“四年一修”应不低于98%第七条非计划停工:是指因设备(含电气、仪表)故障或事故、操作失误以及水、电、气、风等系统公用工程等突发性原因造成生产装置切断进料;公司根据物料平衡情况及其它非装置自身原因安排的停工也属于非计划停工。
- 1、下载文档前请自行甄别文档内容的完整性,平台不提供额外的编辑、内容补充、找答案等附加服务。
- 2、"仅部分预览"的文档,不可在线预览部分如存在完整性等问题,可反馈申请退款(可完整预览的文档不适用该条件!)。
- 3、如文档侵犯您的权益,请联系客服反馈,我们会尽快为您处理(人工客服工作时间:9:00-18:30)。
延长催化剂寿命,保证加氢装置长周期
运行
摘要:本文介绍了影响催化剂寿命的几个主要因素,并结合自己对加氢装置
管理的工作经验,着重从改善原料性质、合理调整反应温度及做好催化剂前期预
处理等方面进行了论述,从而为提高装置长周期运行提供一定的参考。
关键词:加氢;催化剂;寿命
1 前言
石油一厂目前有两套石蜡加氢装置,其中15万吨/年中压加氢装置投产于1997年,20万吨/年高压加氢装置投产于2005年。
两套装置在历年生产中,因
设备原因而影响长周期运行的情况较少见,装置的运行周期主要取决于催化剂活
性高低。
而催化剂始终保持较高活性,又会保证装置的反应温度及反应压力始终
处于较低的状态下,从而为延长设备的使用周期及节能降耗创造良好的条件。
15
万吨/年中压加氢装置催化剂历史最好寿命15.85吨/Kg。
2012年5月至2015年
10月)。
20万吨/年高压加氢装置催化剂历史最好寿命30.23吨/kg,在中石油
内部5套石蜡加氢装置使用寿命属于最好。
2012-2016年9月末寿命25.8吨/kg,按目前状态能继续使用到2017年4月底,2017年5月(全公司大检修)装置进
行检修换剂,预计每月加工量1.9万吨,到2017年5月催化剂寿命为30.23吨
/kg。
追平石油一厂老区加氢创造了的使用周期4年且寿命达到30.3 t/kg的全
国同类装置最好水平。
下面就原料质量、原料自身杂质、操作工艺条件等方面简
单分析一下我们在延长催化剂寿命方面所取得的一些有益尝试。
2 催化剂使用情况及原因分析
2.1 原料质量的影响
在催化剂寿命的影响因素中,最主要的莫过于原料性质了,石油一厂15万
吨/年中压加氢装置在2011年搬迁开工后。
反应器压降在开工之初就上升较快,
最高达到2.3MPa,严重地影响安全生产和产品质量。
产品比色(赛勃特号)在开
工半年后就出现波动,时而达不到全炼蜡和食品蜡标准。
产生上述问题的原因,
主要有以下两个方面。
2.1.1 原料中外来杂质的影响。
据有关资料介绍,原料中外来杂质主要含Fe3+粒子、糠醛、丁酮等极性物质,极易吸附在催化剂表面,占据催化剂活性中心而影响催化剂活性。
我厂30万脱
蜡脱油装置在搬迁后,部分设备管线腐蚀严重,开工初期装置部分设备与管线由
于在开工期间水冲洗和吹扫不彻底,产品脱油蜡中还有Fe3+粒子,Fe3+粒子含量
平均为30~50ppm,带入15万吨/年中压加氢反应器中,导致加氢产品蜡呈棕红色,且溶剂含量在0.01~0.05%,严重地影响了石蜡加氢的正常生产。
其直接原因就是
原料质量太差,导致催化剂活性下降,压差增大。
2.1.2 原料自身杂质含量的影响。
原料自身杂质主要指稠环芳烃、胶质、氮化物等,这些物质的含量一般随着
原料干点的增加而成倍的增加,抽样分析如表1所示:
表1 原料自身杂质与干点对比
随着原料中芳烃、胶质、氮化物等含量的增加,精制效果变差,即脱色、脱
芳和安定性变差。
其原因是芳烃、胶质等物质极易吸咐于催化剂表面而不易被加氢,使催化剂酸度和比表面降低,从而降低了催化剂的活性。
2.2 操作工艺条件的影响
石蜡加氢精制工艺条件主要有反应温度、反应压力、空速、氢油比等,工艺
条件对加氢蜡质量影响最大的是氢分压,其次是温度和空速。
从理论上讲,氢分
压越大对加氢反应越有利,但受设备条件的制约,氢分压也不能无限提高,只能
控制在一个合理的水平。
目前高压加氢装置反应压力控制12.0Mpa,中压加氢生
产全炼蜡压力控制在7.0Mpa。
空速的高与低取决于装置处理量的多少,直接影响
装置的经济效益,因此在尽可能的情况下,都尽量使其控制在催化剂的使用上限。
所以工艺条件选择最终归结为反应温度的确定。
3 我们在生产实践中总结的经验
3.1 控制原料含水和杂质含量
由表1看出在含油大体相当的情况下,随着原料蜡干点的上升原料中胶质、
总氮等杂质的含量明显增加。
而随着原料中芳烃、胶质、氮化物等含量的增加,
加氢精制效果变差,即脱色、脱芳和安定性变差。
首先做好加氢原料罐脱水、延
长沉降时间,确保原料不带水和杂质。
其次在加氢前先进行一下白土精制预处理
过程,可通过活性白土的吸附作用以物理的方法将其去除,所以事先对原料进行
白土精制的预处理过程,既可延长催化剂寿命又可提高产品质量。
但随着国家对
环境问题的重视程度日益加强,白土及废白土的处理成本也越来越高,而且原料
蜡经白土精制后的损耗也明显高于加氢精制。
因此建议在实际生产中,当原料蜡
熔点在58℃以下时,可不加白土或加入少量的白土,以减少白土消耗及石蜡的损失。
当蜡熔点在60℃以上时,还要加入适量的白土且白土的加入量要随原料质量
变差而逐渐增加,以减少高熔点石蜡中重组分对加氢催化剂的损害。
3.2 确定合理反应温度
反应温度在加氢精制工艺参数中占非常重要的地位。
提高反应温度可提高反
应速度,但温度提高后会使装置燃料量及冷却用水量上升,而且温度过高还会使
产品含油量上升。
实际生产中应视不同原料,其它工艺条件及催化剂活性选择适
宜的反应温度。
通过近年来催化剂使用情况看,选择较低的起始反应温度230℃时。
实践表明较低的温度不利于胶质、沥青质等杂质的脱除反应,一段时间后反
应器压降不断上升,产品质量也受到了影响。
即便后来不断提高反应温度也很难
去除催化剂内吸附的胶质、沥青质等重垢杂质,反应器压降仍比较高。
选择了较
高的起始反应温度270℃时,实践表明在高反应温度下,催化剂活性稳定周期较短,且一旦活性下降就得不断提高反应温度,不利于催化剂的长期使用及装置的
节能降耗。
3.3 提高催化剂预处理效果
我们要严格按照催化剂厂家提供的催化剂干燥和预硫化方做好催化剂的干燥
和预硫化工作,要延长催化剂干燥时间,合理分配干燥温度,对催化剂干燥彻底,做好恒温干燥脱水工作,保证催化剂的干燥效果。
提高催化剂预硫化效果,
控制好硫化温度和二甲基二硫的注入量,引入氢气之前,床层最高温度应控制在150℃以下,并引入氮气进行置换,防止催化剂还原。
做好尾氢硫化氢浓度分析,确保硫化效果,保证催化剂活性。
4 结论
通过采取以上控制方法,本周期石油一厂两套加氢装置催化剂运行良好,完
全可保证3年-5年一换剂的需要。
参考文献
[1] 林世雄. 石油炼制工程.
[2] 魏成邦,邱焕达. 石蜡加氢工艺技术探讨:高凝原油加工技术文.
作者简介:王彬,男,1982年02月,单位:中国石油抚顺石化公司石油一厂,工程师,研究方向:加氢精制工艺。