加氢裂化装置运行问题分析及经验总结
加氢裂化装置说明、危险因素及防范措施

加氢裂化装置说明、危险因素及防范措施1. 加氢裂化装置的原理和功能加氢裂化装置是炼油厂和化工厂中常用的重要设备之一,主要用于加氢作用和裂化反应。
其中加氢作用是将烃类化合物以及杂质中的硫、氮等异原子化合物与氢气反应,从而降低其含量并改善质量;裂化反应则是将高沸点的原料分子裂解成低沸点分子,以扩大产物种类和提高产量。
加氢裂化装置通常由反应器、加热器、冷却器、分离器等部分构成。
2. 危险因素由于加氢裂化装置操作强度大、工作条件极端,因此安全问题是设备运行过程中必须关注的问题。
加氢裂化装置的安全问题主要有以下几个方面:(1) 高温高压加氢裂化反应的温度一般在300 ~ 500℃,压力在0.5 ~ 5.0MPa,过程中产生大量的热量和压力,如果这些热量和压力不能得到有效控制,就会造成严重安全事故。
(2) 爆炸由于裂化反应的产物在高温高压下存在相当的不稳定性,稍有不慎就可能引发爆炸危险。
(3) 毒性气体泄露加氢裂化装置原料中含有大量的有毒有害物质,如硫化氢、苯、甲醛等,一旦泄露就会对人身造成巨大的危害。
3. 防范措施为确保加氢裂化装置的安全、稳定、顺畅运行,必须采取以下防范措施:(1) 设备压力检测应对设备各部位都配备相应的安全阀、爆破片、限压器等泄压装置,以保障设备用压力在安全范围内。
(2) 加热控制通过对加热器的温度、压力、通风等参数的控制,实现设备加热过程的安全和平稳。
(3) 有毒气体监控应使用封闭式设备,设有监测采样点,定期监测有毒气体的浓度值,并及时排除。
(4) 废气处理设施中应该设有废气处理设备,将产生的有毒气体通过处理实现安全排放。
对于裂解过程中产生的高浓度硫化氢、甲硫醇等有毒气体,应采取吸收、洗涤等措施。
(5) 人员安全教育操作人员必须经过专业的培训,了解加氢裂化装置的反应原理、安全措施和应急措施,并熟练掌握各种操作技能。
4. 结语加氢裂化装置是工业生产中不可或缺的设备之一,只有采取科学的防范措施,加强安全管理,才能做到安全生产、高效生产。
渣油加氢装置运行中存在问题及措施
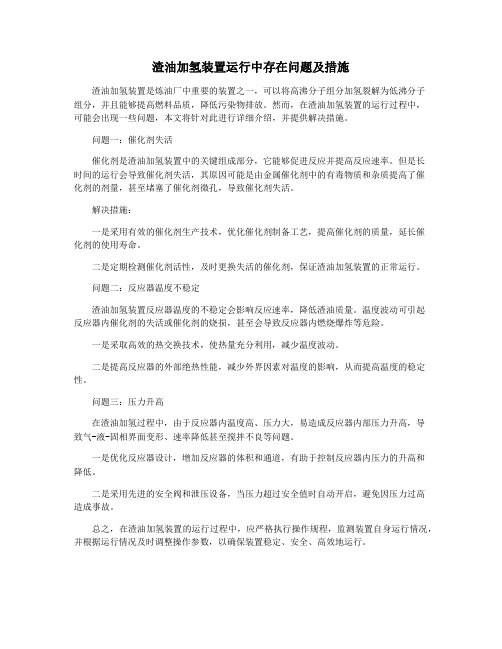
渣油加氢装置运行中存在问题及措施渣油加氢装置是炼油厂中重要的装置之一,可以将高沸分子组分加氢裂解为低沸分子组分,并且能够提高燃料品质,降低污染物排放。
然而,在渣油加氢装置的运行过程中,可能会出现一些问题,本文将针对此进行详细介绍,并提供解决措施。
问题一:催化剂失活催化剂是渣油加氢装置中的关键组成部分,它能够促进反应并提高反应速率。
但是长时间的运行会导致催化剂失活,其原因可能是由金属催化剂中的有毒物质和杂质提高了催化剂的剂量,甚至堵塞了催化剂微孔,导致催化剂失活。
解决措施:一是采用有效的催化剂生产技术,优化催化剂制备工艺,提高催化剂的质量,延长催化剂的使用寿命。
二是定期检测催化剂活性,及时更换失活的催化剂,保证渣油加氢装置的正常运行。
问题二:反应器温度不稳定渣油加氢装置反应器温度的不稳定会影响反应速率,降低渣油质量。
温度波动可引起反应器内催化剂的失活或催化剂的烧损,甚至会导致反应器内燃烧爆炸等危险。
一是采取高效的热交换技术,使热量充分利用,减少温度波动。
二是提高反应器的外部绝热性能,减少外界因素对温度的影响,从而提高温度的稳定性。
问题三:压力升高在渣油加氢过程中,由于反应器内温度高、压力大,易造成反应器内部压力升高,导致气-液-固相界面变形、速率降低甚至搅拌不良等问题。
一是优化反应器设计,增加反应器的体积和通道,有助于控制反应器内压力的升高和降低。
二是采用先进的安全阀和泄压设备,当压力超过安全值时自动开启,避免因压力过高造成事故。
总之,在渣油加氢装置的运行过程中,应严格执行操作规程,监测装置自身运行情况,并根据运行情况及时调整操作参数,以确保装置稳定、安全、高效地运行。
加氢裂化技术问题研究报告

加氢裂化技术问题研究报告加氢裂化技术问题研究报告摘要:加氢裂化技术在石油化工工业中具有重要地位,但在实际应用中也存在一些问题。
本文针对加氢裂化技术存在的问题进行了深入分析和研究,探讨了其产生的原因,并给出了相应的解决方法和建议。
一、引言加氢裂化技术是一种重要的石油化工技术,它可以将重质石油馏分转化为轻质石化产品。
然而,在实际应用中,我们发现加氢裂化技术存在一些问题,包括产物选择性、催化剂失活、设备结焦等。
本文将对这些问题进行详细研究,以期为加氢裂化技术的进一步发展提供参考。
二、问题一:产物选择性在加氢裂化过程中,产物选择性是一个很重要的指标。
目前存在的问题是,由于催化剂表面存在一些缺陷,导致裂解反应选择性较低。
为了解决这个问题,我们采用了活性组分的改性方法,通过表面改性提高催化剂的选择性。
三、问题二:催化剂失活加氢裂化催化剂是实现反应的关键。
然而,在长时间使用后,催化剂会发生失活,导致反应效果下降。
我们的研究发现,催化剂失活主要是由于金属杂质的存在和随时间的积累所导致的。
因此,我们提出了一种定期热解和再生催化剂的方法,可以保持催化剂的活性和稳定性。
四、问题三:设备结焦加氢裂化设备中常常会出现结焦问题,严重影响了反应的进行。
造成设备结焦主要是因为反应温度过高、进料中含有杂质和反应气氛失控等原因。
为了解决这个问题,我们可以通过优化反应温度控制、改变进料组分和研究最佳反应气氛等措施,减少设备结焦的发生,提高设备稳定性。
五、问题四:环境污染加氢裂化技术在使用过程中产生的废气和废水对环境造成了一定的污染。
为了减少环境污染,我们提出了一种废气净化和废水处理的方法,通过物理和化学方法去除废气中的有害物质,并对废水进行深度处理,以达到排放标准。
六、结论与展望通过对加氢裂化技术问题的研究,我们发现了其产生的原因,并提出了相应的解决方法和建议,以期解决加氢裂化技术存在的问题,提高其效率和可靠性。
未来,我们将进一步研究和改进加氢裂化技术,推动其在石油化工领域的发展。
渣油加氢装置运行中存在问题及措施
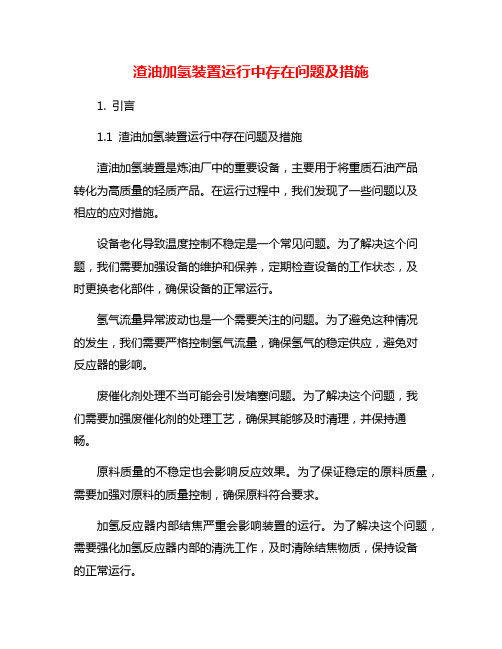
渣油加氢装置运行中存在问题及措施1. 引言1.1 渣油加氢装置运行中存在问题及措施渣油加氢装置是炼油厂中的重要设备,主要用于将重质石油产品转化为高质量的轻质产品。
在运行过程中,我们发现了一些问题以及相应的应对措施。
设备老化导致温度控制不稳定是一个常见问题。
为了解决这个问题,我们需要加强设备的维护和保养,定期检查设备的工作状态,及时更换老化部件,确保设备的正常运行。
氢气流量异常波动也是一个需要关注的问题。
为了避免这种情况的发生,我们需要严格控制氢气流量,确保氢气的稳定供应,避免对反应器的影响。
废催化剂处理不当可能会引发堵塞问题。
为了解决这个问题,我们需要加强废催化剂的处理工艺,确保其能够及时清理,并保持通畅。
原料质量的不稳定也会影响反应效果。
为了保证稳定的原料质量,需要加强对原料的质量控制,确保原料符合要求。
加氢反应器内部结焦严重会影响装置的运行。
为了解决这个问题,需要强化加氢反应器内部的清洗工作,及时清除结焦物质,保持设备的正常运行。
加强设备维护保养、严格控制氢气流量、加强废催化剂处理工艺、加强原料质量控制、以及强化加氢反应器内部清洗是解决渣油加氢装置存在问题的有效措施。
只有通过不断优化设备管理和操作措施,才能确保装置的安全稳定运行。
.2. 正文2.1 设备老化导致温度控制不稳定设备老化是渣油加氢装置运行中常见的问题之一,其主要表现在温度控制不稳定上。
随着设备的运行时间延长,设备中的热效率逐渐降低,导致温度控制不再精准,温度波动增多。
这种情况会严重影响加氢反应的效果,甚至可能导致设备停产。
出现温度控制不稳定的问题,首先需要对设备进行全面的检查和评估,查找可能引起问题的部位。
可能需要更换老化严重的部件,修复受损的管道,增加或更新温度控制系统等措施。
加强设备的日常维护保养工作,定期清洗设备,定期更换易损件,延长设备的使用寿命。
还需要加强设备运行人员的培训和监督,提高他们对设备运行情况的观察和反馈能力,及时发现问题并进行处理。
加氢裂化装置运行过程常见问题分析

加氢裂化装置运行过程常见问题分析及对策加氢裂化协作组秘书处二OO一年六月目录1. 工艺操作过程中常见问题分析及对策2. 设备运行过程中常见问题分析及对策3. 仪表和自动化中常见问题及对策4. 原料对装置运行的影响及对策5. 催化剂使用问题11. 工艺操作常见问题及对策1.1 对于全循环型流程的装置采用一次通过生产时,为了少排尾油,单程转化率控制多少较为合适?如果控制较高的单程转化率(如80%以上),对催化剂的性质及使用寿命会有影响吗?氢油比与空速的关系如何调配?答:从南京炼油厂的生产经验来看,考虑生产平稳率及操作控制因素,一般应控制在85%左右比较合适。
这样的产品分布、中间油品收率、氢耗均较为合理。
如果尾油无去处,90%的转化率亦是能够控制的,当然这还要看催化剂本身的性质。
一般来说单程转化率增加时,轻油及液态烃收率增加,柴油收率减少,而航煤收率不变或略有下降,所以转化率控制多少最适宜与分馏系统的脱丁烷塔及主分馏塔顶部负荷是否能满足有关。
控制较高的转化率会使反应温度升高、氢耗增加、催化剂的失活速率增大,长期这样操作必将缩短催化剂的使用寿命。
如果采取单程通过,进料在裂化反应器的空速变小,停留时间增加,这势必为二次裂化及生焦提供了有利条件。
因此,从这一方面考虑应增加氢油比,即转化率越高,氢油比应相应增高。
一般需在裂化反应器入口配入部分循环氢,保持总循环氢量与原全循环操作时相仿。
实际上,单程通过操作时,裂化反应器入口需配上大量循环氢,否则入口温度难以控制。
当加工高硫和高氮原油时尤其严重。
1.2 裂化反应器第一床层压降上升实例1:裂化反应器第一床层压降上升的主要原因及措施原因及分析:对于一次通过式流程,裂化反应器一床层的压降上升主要是催化剂生焦造成的,所以一般来说此床层的压降不会影响生产周期。
对于全循环流程,压降升高的另一原因是循环油中带入杂质引起的。
在开、2停工时,将分馏系统的杂质带入反应器,这种情况比较好解决,只要在开、停工时适当增加开路循环的时间,并在循环油线上增加过滤设施即可解决。
加氢裂化装置运行分析
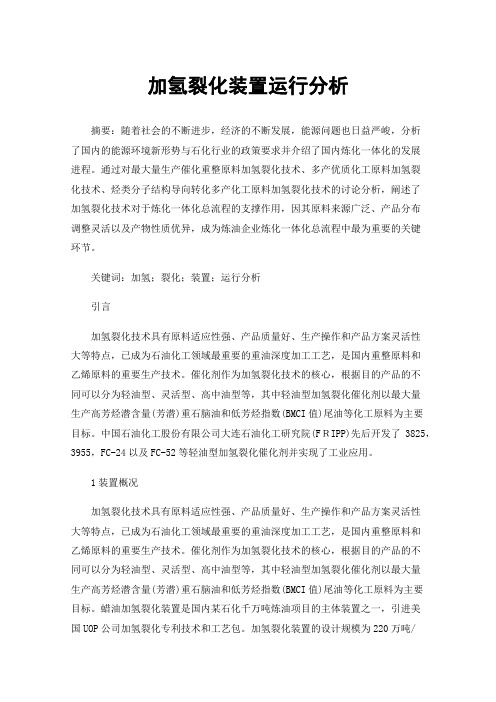
加氢裂化装置运行分析摘要:随着社会的不断进步,经济的不断发展,能源问题也日益严峻,分析了国内的能源环境新形势与石化行业的政策要求并介绍了国内炼化一体化的发展进程。
通过对最大量生产催化重整原料加氢裂化技术、多产优质化工原料加氢裂化技术、烃类分子结构导向转化多产化工原料加氢裂化技术的讨论分析,阐述了加氢裂化技术对于炼化一体化总流程的支撑作用,因其原料来源广泛、产品分布调整灵活以及产物性质优异,成为炼油企业炼化一体化总流程中最为重要的关键环节。
关键词:加氢;裂化;装置;运行分析引言加氢裂化技术具有原料适应性强、产品质量好、生产操作和产品方案灵活性大等特点,已成为石油化工领域最重要的重油深度加工工艺,是国内重整原料和乙烯原料的重要生产技术。
催化剂作为加氢裂化技术的核心,根据目的产品的不同可以分为轻油型、灵活型、高中油型等,其中轻油型加氢裂化催化剂以最大量生产高芳烃潜含量(芳潜)重石脑油和低芳烃指数(BMCI值)尾油等化工原料为主要目标。
中国石油化工股份有限公司大连石油化工研究院(FRIPP)先后开发了3825,3955,FC-24以及FC-52等轻油型加氢裂化催化剂并实现了工业应用。
1装置概况加氢裂化技术具有原料适应性强、产品质量好、生产操作和产品方案灵活性大等特点,已成为石油化工领域最重要的重油深度加工工艺,是国内重整原料和乙烯原料的重要生产技术。
催化剂作为加氢裂化技术的核心,根据目的产品的不同可以分为轻油型、灵活型、高中油型等,其中轻油型加氢裂化催化剂以最大量生产高芳烃潜含量(芳潜)重石脑油和低芳烃指数(BMCI值)尾油等化工原料为主要目标。
蜡油加氢裂化装置是国内某石化千万吨炼油项目的主体装置之一,引进美国UOP公司加氢裂化专利技术和工艺包。
加氢裂化装置的设计规模为220万吨/年,按年操作8400h考虑,装置的操作弹性为60%~110%。
该装置反应部分采用单段全循环、炉后混油和热高分工艺流程,并设置了循环氢脱硫塔,分馏系统采用四塔分离流程(脱硫化氢汽提塔、分馏塔、航煤汽提塔、柴油汽提塔)出柴油方案。
加氢裂化装置优化运行总结
加氢裂化装置优化运行总结周世岩,顾 望,刘 骅,赵恒凤(中国石油天然气股份有限公司华北石化分公司,河北省沧州市062550)摘要:随着催化剂性能的提升,可以根据市场需求灵活调整加氢裂化装置运行方案,提高了炼油企业减油增化的灵活性。
某石化公司加氢裂化装置首次开工使用灵活性加氢裂化催化剂,通过调整反应温度,重石脑油+喷气燃料收率可在45%~60%灵活调整;通过掺炼柴油增加装置负荷,柴汽比可降低0.15~0.20;通过增加尾油作有机热载体、新氢机间歇性运行等一系列优化运行措施,取得了良好的经济效益。
关键词:加氢裂化 喷气燃料 重石脑油 尾油 优化 柴汽比 加氢裂化工艺能够同时实现重油轻质化以及直接生产符合最新标准规范要求的中间馏分油[1],被越来越多的炼化企业选用。
某石化公司2.9Mt/a加氢裂化装置采用UOP工艺包,于2018年6月30日建成中交,2019年4月18日一次开车成功。
装置采用一段全循环、炉后混氢工艺,设计以常压蜡油为原料,生产重石脑油、喷气燃料和柴油。
首次开工使用DN3552+FX631催化剂组合方案,用于灵活生产重石脑油、喷气燃料。
1 运行分析装置开工后运行平稳,各项运行参数正常、产品质量合格,但装置一直在55%~75%低负荷运行,能耗等技术经济指标与国内同类装置平均值相比偏差。
1.1 原料及主要运行参数混合进料主要性质见表1,装置主要运行参数见表2。
从表1可知,实际加工原料性质明显好于设计值,加工难度低。
表1 混合进料性质Table1 Propertiesofmixedfeeds表2 主要运行参数Table2 Mainoperationparameters 注:WABT为床层加权平均温度,下同。
1.2 产品分布及产品质量根据产品实际需求方案,调整反应温度,装置主要产品收率和性质见表3。
从表3可知,装置主要产品收率满足设计要求,质量优异。
1.3 能耗分析装置能耗情况见表4。
由表4可知,装置实际运行能耗优于设计值(1297.9MJ/t),比国内同类装置能耗平均值(低于1046.7MJ/t)略高,主要是受装置加工负荷低的影响。
71-燕山分公司炼油厂-燕山石化加氢裂化装置生产过程中遇到的几个问题
燕山石化加氢裂化装置生产过程中遇到的几个问题分析与总结杨有亮孙毅闫博(中国石化北京燕山分公司炼油厂第九作业部北京 102503)摘要:燕山石化炼油厂200万吨/年加氢裂化装置于2007年6月19日一次开车成功,至今已运行近一年,期间碰到原料沥青质超标,导致尾油变黑问题、反应进料切断阀自动关闭,导致瞬间切断进料、原料带水造成装置波动、原料氮含量超高,导致裂化一床层催化剂中毒、公用工程波动等问题,影响装置正常生产。
从以上所遇到的问题及处理过程进行分析与总结,加氢裂化装置在正常生产过程中要从源头上加强原料和公用工程系统的监控,且遇到问题要准确判断,处理及时。
关键词:原料;催化剂;处理;总结前言一套大型的炼油生产装置在运行过程中,总会出现一些新问题,重要的是出现新问题怎样准确判断、及时处理,之后归纳总结,防患于未然。
燕山石化炼油厂200万吨/年加氢裂化装置于2007年6月19日一次开车成功,至今已运行近一年,期间碰到原料、公用工程系统波动等问题,影响装置的正常生产。
分析总结发生的问题与处理过程,若在事故初发阶段,判断准确,处理及时,装置可以转危为安,将损失降低到最小;若判断失误,错过处理问题的最佳时期,将造成装置非计划停工,影响公司生产的整体物料平衡,造成重大的直接和间接经济损失。
为此将装置开工以来的问题总结,分析事故出现状态,优化处理过程,为以后事故处理提供可靠依据和保证。
1 原料沥青质超标,导致尾油变黑问题2007年6月19日下午由于加氢裂化上游常减压装置波动,导致常三线沥青质超标,原料变黑,以致于加氢裂化装置催化剂中毒,精制油、尾油颜色变黑。
1.1 事故经过加氢裂化装置6月19日22:40操作人员采样时发现尾油颜色变黑,立即向作业部汇报,作业部组织全面检查,采样分析精制油、尾油及滤后原料油,目测样品颜色,发现滤后原料本身是黑色,判断原料出现问题,立即通知罐区切换原料;提R-3101入口温度至340℃,5:45提R-3101入口温度至345℃,保护裂化催化剂。
加氢裂化装置高压换热器故障情况及原因分析
在 1 3 0— 2 1 0 q C) 在 注 水 点 之后 , 以保 护 E - 3 1 0 3 A
2 . 2 材 质理 化分 析及 垢物 分析
对失 效管 束 进 行 理化 分 析 , 结 果 表 明材 质 成
分、 硬度 、 非金 属夹 杂 等指标 均 符合相 关 标 ( 能量色散 x射线荧 光光谱分析 ) , 分析结果显示 , 样品 中含有 c , N, O, S , C 1 , F e和 c r 等元 素 , 其 中氯元 素 质 量分 数 为
器结盐情况、 管柬腐蚀形貌 以及装置 原料腐蚀 介质 情况和 高压换 热器的 实际操作 情况 , 分析认 为
管 束 腐 蚀 原 因为 生 产 过 程 中 出现 氯 化 铵 盐 结 晶 , 氯 化 铵 盐 水 解 形 成 强 酸 对 不 锈 钢 产 生局 部 腐 蚀 。
根 据分析原 因, 目前采取调整运行操作 温度 , 改 变铵盐结 晶点位 置 , 同时采取科 学合 理的注水 工艺
防腐蚀措施 以减缓 高压换热 器的腐蚀风 险。装置 自2 0 1 4年 5月检修 开工后 , 按 此控制调 整 , 高压
换 热 器 目前 运 行 正 常 。 关键词 : 腐蚀 氯化铵盐 水解 结 晶
某 石化 公 司炼 油 系 统 高 压 加 氢 裂 化 装 置 于
1 高压 换热 器运 行及 泄漏情 况
2 0 0 7 年 7月投产 , 自2 0 0 9年 以来 , 热高分 之后
的 3台高 压 换 热 器 陆 续 出 现腐 蚀 泄 漏 问题 。对
加氢裂化常见问题分析及对策
加氢裂化常见问题分析及对策第一部分工艺操作常见问题分析及对策1、全循环流程的装置采用一次通过生产时的转化率控制及对催化剂性能的影响。
氢油比与空速关系的调配。
问题的提出:某些企业在扩能改造中,将工艺流程由原全循环改为一次通过,而在生产中尾油的需求量时有变化,为此提出如何优化操作问题。
分析与建议:从N炼油厂的生产经验来看,考虑到生产平稳及操作控制等因素,单程转化率一般应控制在85%左右比较合适,其产品分布、中间油品收率、氢耗等指标均较为合理。
如果尾油无下游用户,单程转化率可控制在90%,当然这与催化剂的性能有关。
一般来说单程转化率增加时,轻油及液态烃收率增加,柴油收率减少,而喷气燃料收率基本不变或略有下降。
所以转化率控制多少较为合适与分馏系统的脱丁烷塔及主分馏塔顶部负荷均有一定的关系。
控制较高的转化率会使反应温度升高、氢耗增加、催化剂的失活速率增大,长期这样操作必将会缩短催化剂的使用寿命。
因此,控制转化率高或低,要根据产品的市场需求和上下游平衡进行综合考虑,以获取最大的经济效益。
采取单程通过,进料在裂化反应器的空速变小,停留时间增加,为二次裂化及生焦提供了条件。
因此,从这一方面考虑应增加氢油比,即转化率增高,氢油比应相应增高。
一般需在裂化反应器入口增加部分循环氢流量,以保持总循环氢量与全循环操作相比不发生变化。
而在实际操作中,工业装置加工高硫和高氮原料油时,为了控制好裂化反应器的入口温度,所需的循环氢量还需进一步增加。
2、裂化反应器第一床层压降上升问题Z炼油厂1999年5月加氢裂化反应器(R302)催化剂全部更新为3974。
装置5月24日进油,26日全部产品质量合格。
平稳运转9个月,加工VGO 0.83 Mt 后,于2000年2月28日实测裂化反应器(R302)一床层压降高达0.40MPa,装置被迫降量;同时降低循环氢压缩机(C301)转速,维持低负荷运转。
装置于3月16-23日短期停工,实施裂化反应器(R302)催化剂撇头。
- 1、下载文档前请自行甄别文档内容的完整性,平台不提供额外的编辑、内容补充、找答案等附加服务。
- 2、"仅部分预览"的文档,不可在线预览部分如存在完整性等问题,可反馈申请退款(可完整预览的文档不适用该条件!)。
- 3、如文档侵犯您的权益,请联系客服反馈,我们会尽快为您处理(人工客服工作时间:9:00-18:30)。
加氢裂化装置运行问题分析及经验总结
摘要:某石化公司120万吨/年加氢裂化装置在本周期运行期间出
现加氢精制反应器床层压降上涨问题,影响装置安全平稳长周期运行。
本文对加氢精制反应器床层压降上涨问题产生原因进行深入分析,对
处理措施及检修施工等进行说明,对日常生产问题的处理有一定的指
导借鉴作用。
关键词:催化剂;加氢裂化;撇头;压降;重石脑油氮含量
1 导言
某石化公司120万吨/年加氢裂化装置加氢精制反应器(R-101)第一床层
(保护剂和催化剂)压降自2017年7月起上涨趋势明显,最高值达到0.58MPa,
严重影响了装置正常平稳运行。
根据整体生产平衡安排,120万吨/年加氢裂化装
置于2017年12月25日停工撇头检修,2018年1月4日投料开车成功,消除了
制约装置平稳运行的瓶颈。
2 加氢裂化装置概况
某石化公司120万吨/年加氢裂化装置由中国石化工程建设有限公司总体设计,采用中国石油化工股份有限公司大连(抚顺)石油化工研究院一段串联全循
环加氢裂化技术,原设计加工能力80万吨/年,于1999年6月建成投产;2005
年扩能改造至120万吨/年,改为一次通过操作模式。
加氢精制反应器(R-101)
装填FRIPP研发的FF-66精制催化剂,加氢裂化反应器(R102)装填FRIPP研发
的FC-60裂化催化剂。
3 加氢精制反应器压降上升原因分析
120万吨/年加氢裂化装置加氢精制反应器(R-101)第一床层(保护剂和催化剂)压降自2017年7月起上涨趋势明显,最高值达到0.58MPa,严重影响了装置正常平稳运行。
3.1 反应系统紧急泄压造成初始压降偏高
自2016年装置检修开工以来,该装置反应系统在三个月内经历了三次紧急泄压,分别为:
(1)2016年检修开工阶段,因高压换E105泄漏启动紧急泄压。
R101压降维持在0.25Mpa;
(2)2016年10月29日,脱丁烷塔底泵P203密封泄漏启动紧急泄压。
R101压降维持在0.35 Mpa左右;
(3)2016年12月30日,高分安全阀故障起跳,造成反应系统泄压。
R101压降维持在0.41 Mpa左右。
2016年检修期间,加氢精制反应器R-101除第四床层更换FRIPP最新研发的FF-66型精制剂外,其它床层均为FF-46再生剂,再生剂在机械强度等方面与新剂有差距,加之经过连续紧急泄压,容易造成催化剂粉化,导致精制反应器初始压降偏高。
3.2 原料蜡油性质变化、掺炼污油
2017年6月下旬至7月上旬,上游常减压装置加工伊重原油,期间常减压装置以5%-7%(最高为10%)的比例掺炼污油。
加氢裂化装置加氢精制反应器压降在此期间上涨趋势明显。
原料性质是影响反应器床层压降上升的重要原因,由于原料中的杂质如重金属、胶质沥青质、污染物等汇集在催化剂床层上部及床层空隙,当达到一定数量后,就会在催化剂上部形成一层高密度的“结盖”,造成催化剂孔隙率下降,堵塞流体流道,造成床层压降上升。
3.3 反冲洗过滤器运行异常造成机械杂质带入反应器
该加氢裂化装置反冲洗过滤器SR-101为美国 PALL公司生产,由15个程控阀组成,滤芯精度17μm,能过滤掉原料油中大部分杂质。
装置1999年开工初期每组过滤器装有112根PALL原厂滤芯,2005年装置扩容改造后,滤芯增加到每组166根(厂家上海博洽)。
2016年检修开工以来,加氢裂化装置反冲洗过滤器运行异常。
A组过滤器能够通过压差高(120Kpa)进行切换,但B组过滤器只能通过设定时间进行切换。
针对反冲洗过滤器运行异常情况,车间进行了以下排查:
(1)2017年8月14日,将过滤器滤芯清洗回装,但回装后A组在设定时间内压差变化很小,B组过滤器压差变化略有上涨趋势(最大压差达到50Kpa),但
未达到过滤器切换条件(120Kpa)。
9月11日将过滤时间由3小时延长至12小时,压差仍未见明显上涨。
(2)将反冲洗过滤器滤芯进行拆出检查,未发现滤芯有明显破损,随机抽
取部分旧滤芯返厂家进行试验、剖解及检查过滤效果,厂家答复送检滤芯未见明
显异常。
对反冲洗过滤器工艺副线阀及设备副线阀前后进行了热成像及超声波检测,基本判断工艺、设备副线阀不存在内漏现象。
(3)9月26日,对A组过滤器更换PALL原厂滤芯,更换后,A组过滤器运
行时压差几乎无变化,始终维持在30Kpa左右。
B组过滤器前期运行时压差也几
乎无变化,但自10月1日起,B组过滤器在运行期间压差逐渐上升,运行5-7小
时后,压差就能涨至120Kpa。
达到切换条件。
反冲洗过滤器要保证>25μm杂质脱除率在95%以上,加强对过滤器操作运
行的检查,定期抽芯检查。
保证过滤器的正常工作,严禁长期开过滤器副线运行!尽可能防止机械杂质带入反应器床层。
4 现场检修施工情况
将加氢精制反应器(R-101)顶部头盖打开后,对器内保护剂和催化剂进行撇头,由催化剂研发厂家FRIPP和催化剂制造厂家山东公泉对卸出催化剂状态进行判定,最终将第一、二床层保护剂和催化剂全部撇出换剂,第三床层保留原催化剂使用,具体如下:
(1)入口扩散器拆出后未发现异常,分配器表面的一层薄薄的垢粉属正常现象。
(2)扩散器下部的泡罩分配盘经过检查未发现有过多的垢物,表面比较干净。
(3)泡罩分配盘下部的保护剂表面有结盖现象,类似于冰面垢层(结盖厚度约2CM),用撬棍敲击,能够敲碎。
(4)一床保护剂下面的催化剂经过抽真空抽出后,有粉末和催化剂破损现象,但是从反应器内部直接采样来看,外观较完整。
(5)二床中部催化剂经过抽真空抽出后还有部分粉末和催化剂破损现象,但从反应器内部采样观察催化剂表面完整、无明显破损。
(6)二床层中下部及三床层表面催化剂较为完整,没有明显破损情况。
5 经验与建议
(1)严格控制原料蜡油性质,常减压装置严格控制干点、残碳,有效降低VGO中铁离子和沥青质。
(2)做好反冲洗过滤器运行操作,严禁过滤器长期走副线,必要时可再串联一组过滤器。
(3)精心操作,保证催化剂床层不超温,避免反应系统紧急泄压。
(4)由于本次停工消缺正值冬天,而且因原料系统和分馏系统均有施工无法实现循环,防冻防凝工作尤为重要。
本次停工原料系统首先将蜡油退净,然后引柴油进原料系统冲洗置换,确保了原料系统无冻凝。
因分馏系统脱丁烷塔有施工,首先将塔内存油压至下游主分馏塔,然后引部分柴油冲洗置换后继续向下游压净存油。
减压塔收满油,每半小时至一小时间断外送尾油,流量计变化即可停送,以保证尾油线无冻凝。
若分馏系统收满柴油,开工前需将柴油退净重新引蜡油垫塔,否则分馏升温过程中分馏塔底部泵将频繁抽空,延缓开工进度。
参考文献
[1] 方向晨.加氢裂化工艺与工程(第二版). 北京:中国石化出版社,2017。