塑料模设计课设
塑料模具设计课程教学方案计划
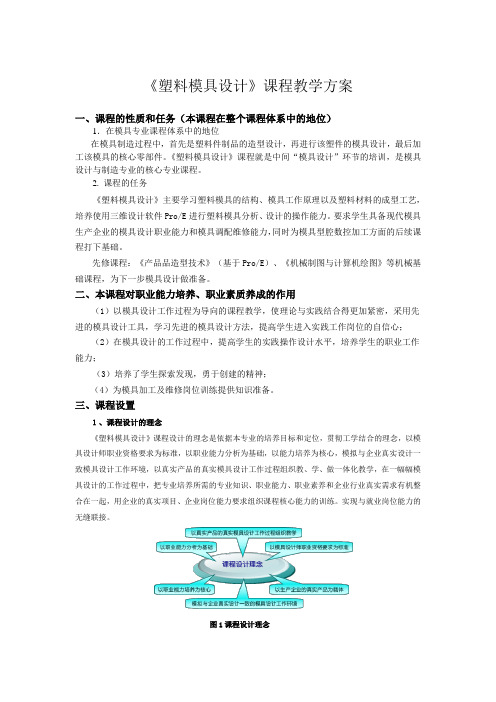
《塑料模具设计》课程教学方案一、课程的性质和任务(本课程在整个课程体系中的地位)1.在模具专业课程体系中的地位在模具制造过程中,首先是塑料件制品的造型设计,再进行该塑件的模具设计,最后加工该模具的核心零部件。
《塑料模具设计》课程就是中间“模具设计”环节的培训,是模具设计与制造专业的核心专业课程。
2. 课程的任务《塑料模具设计》主要学习塑料模具的结构、模具工作原理以及塑料材料的成型工艺,培养使用三维设计软件Pro/E进行塑料模具分析、设计的操作能力。
要求学生具备现代模具生产企业的模具设计职业能力和模具调配维修能力,同时为模具型腔数控加工方面的后续课程打下基础。
先修课程:《产品品造型技术》(基于Pro/E)、《机械制图与计算机绘图》等机械基础课程,为下一步模具设计做准备。
二、本课程对职业能力培养、职业素质养成的作用(1)以模具设计工作过程为导向的课程教学,使理论与实践结合得更加紧密,采用先进的模具设计工具,学习先进的模具设计方法,提高学生进入实践工作岗位的自信心;(2)在模具设计的工作过程中,提高学生的实践操作设计水平,培养学生的职业工作能力;(3)培养了学生探索发现,勇于创建的精神;(4)为模具加工及维修岗位训练提供知识准备。
三、课程设置1、课程设计的理念《塑料模具设计》课程设计的理念是依据本专业的培养目标和定位,贯彻工学结合的理念,以模具设计师职业资格要求为标准,以职业能力分析为基础,以能力培养为核心,模拟与企业真实设计一致模具设计工作环境,以真实产品的真实模具设计工作过程组织教、学、做一体化教学,在一幅幅模具设计的工作过程中,把专业培养所需的专业知识、职业能力、职业素养和企业行业真实需求有机整合在一起,用企业的真实项目、企业岗位能力要求组织课程核心能力的训练。
实现与就业岗位能力的无缝联接。
图1课程设计理念2、课程设计的思路(1)以模具设计师职业资格要求为标准,培养现代模具设计的职业能力目前,我国的模具制造企业发展迅速。
塑料模具课程设计指导书

塑料模具课程设计指导书(一)塑料模具课程设计的目的塑料模具课程设计是《塑料成型工艺与模具设计》课程中的最后一个实践性教学环节,也是一次对学生进行比较全面的塑料模具设计的训练,其目的是:(1)通过模具课程设计,要求学生综合应用《塑料成型工艺与模具设计》及其他相关课程的基本知识来解决工程实际中的具体设计问题,以进一步巩固和深化所学课程的知识。
(2)通过模具课程设计,学生进行了一次较为完整的塑料模具设计的实际训练,使学生初步掌握塑料模具设计的内容、步骤和基本方法,进一步提高学生的结构设计能力和独立工作能力,为毕业设计和今后从事模具设计与制造工作奠定基础。
(3)通过模具课程设计,提高学生查阅技术资料和手册的能力,熟悉并正确应用有关的技术标准。
(4)通过模具课程设计,培养学生认真负责、踏实细致的工作作风和严谨的科学态度,强化学生的质量意识和时间观念,使学生初步形成从业的基本素职。
(二)课程设计的任务塑料模具课程设计的题目,一般选择中等复杂程度的塑料注射模进行设计,要求学生在规定的时间内完成如下任务:(1)绘制塑料制件图一张(A4)(用计算机绘图)(2)绘制塑料注射模装配图一张(A1)(手工绘图)(3)绘制模具零件工作图2~3张(用计算机绘图)(4)编写设计说明书一份(三)塑料注射模具设计步骤1.塑件成型工艺分析(1)塑件成型特性的分析根据塑件图中标明的塑料品种,分析该塑料的使用性能及成型性能;查阅该塑料的比重、比容、收缩率及流动性等特性。
(2)塑件的结构工艺性分析认真阅读塑件图,审核塑件的几何形状、尺寸公差等级、表面粗糙度、塑件壁厚及其他技术要求,必要时还需阅读该塑件所属的部件图(或组件图)和了解该塑件的使用条件、使用寿命、载荷特性及其数值等。
据此分析塑料注射成型工艺的可行性和经济性。
(3)明确生产批量小批量生产时,为了降低成本,模具尽可能简单,通常采用单型腔;大批量生产时,应在保证塑件质量的前提下,尽量采用一模多腔或高速自动化生产,以缩短生产周期,提高生产率,因此对模具的推出机构、合模导向机构、塑件和浇注系统凝料的脱模以及凸、凹模的结构提出了严格的要求。
塑料成型与模具设计课程设计

塑料成型与模具设计课程设计
塑料成型与模具设计
一、教学目标
本课程的目的是让学生学会塑料成型工艺,了解塑料成型及其相关设备的工作原理,能够理解和设计塑料成型模具。
二、教学内容
1.塑料成型的基本原理:
了解塑料的热变性,成型工艺的温度控制,成型工艺和成型设备的选择。
2.塑料模具的设计:
理解塑料模具的设计原则,如冷却系统的设计、模具的结构、规格测量等。
3.塑料成型的表面处理:
介绍一些常用的塑料上表面处理的方法,如冲孔、抛光、喷砂、涂漆、电镀等。
4.塑料制品的检验与评价:
学习塑料成型和表面处理及制品检验标准的基本原理,学习塑料制品的检验方法和标准。
三、教学方法
1.讲授型:
采用讲授型加实践,以课堂讲解为主,讲述技术原理,并用图片、动画等形式加以讲解,以此深化学生对塑料成型工艺的理解;
2.实践型:
采用实际的方式,在实验室里实验各种塑料成型技术及表面处理的方法,以达到及时掌握手段,做到知行合一;
3.讨论型:
在实践型的基础上,结合实验室的实验结果进行研讨,全面解决学生在学习中面临的各种问题,达到增强学生对塑料成型及模具设计的理解程度。
四、教学评估
本课程采取了实训中心的考核方式,在课程中,学生需要进行平时的习题练习,不定期的考试,根据学生的考试成绩、平时作业、实践情况对学生进行考核。
最后,课程结束的时候,还会进行一次综合考试,对学生整个课程的学习情况进行全面评估。
塑料成型与模具课程设计

塑料成型与模具课程设计一、课程目标知识目标:1. 学生能理解并掌握塑料成型的基本概念、原理及常用工艺参数。
2. 学生能了解不同类型的模具结构及其在塑料成型中的应用。
3. 学生掌握模具设计的基本流程和注意事项,具备分析模具结构合理性的能力。
技能目标:1. 学生能运用CAD软件进行简单的模具设计,并能够进行模具零件的拆分和组装。
2. 学生通过实际操作,掌握注塑机的基本操作流程,具备独立完成塑料件成型的能力。
3. 学生能够运用所学知识,解决塑料成型过程中出现的问题,并提出改进措施。
情感态度价值观目标:1. 学生培养对塑料成型及模具设计专业的兴趣,激发创新意识,提高实践能力。
2. 学生通过课程学习,认识到模具在制造业中的重要性,增强对我国制造业的自豪感。
3. 学生在课程实践中,培养团队合作精神,提高沟通与协作能力。
本课程针对高年级学生,结合学科特点和教学要求,注重理论与实践相结合,以提高学生的实际操作能力和解决问题的能力。
课程目标具体、可衡量,旨在使学生能够掌握塑料成型及模具设计的基本知识,具备模具设计与制造的基本技能,同时培养良好的职业素养和价值观。
二、教学内容1. 塑料成型基本原理:包括聚合物熔融、流动、冷却、固化等过程,以及成型过程中压力、温度、时间等参数对成型质量的影响。
教材章节:第一章 塑料成型理论基础2. 常用塑料成型工艺:介绍注塑、挤塑、吹塑等常用塑料成型工艺的特点和应用。
教材章节:第二章 塑料成型工艺3. 模具结构及设计:分析不同类型的模具结构,如两板模、三板模、热流道模等,讲解模具设计的基本流程和注意事项。
教材章节:第三章 模具结构与设计4. 模具CAD设计:教授CAD软件在模具设计中的应用,进行实际操作演练。
教材章节:第四章 模具CAD/CAM技术5. 注塑机操作与调试:介绍注塑机的结构、工作原理及基本操作流程,并进行实际操作。
教材章节:第五章 注塑机与设备6. 塑料件成型与质量控制:分析成型过程中可能出现的缺陷及原因,讲解质量控制方法。
挤出塑料模具课程设计

挤出塑料模具课程设计一、课程目标知识目标:1. 学生能理解并掌握塑料模具的基本概念、分类及挤出模具的工作原理。
2. 学生能够描述挤出塑料模具的设计流程,包括模具结构、材料选择和工艺参数的确定。
3. 学生了解塑料成型过程中的常见问题及解决办法。
技能目标:1. 学生能够运用CAD软件进行挤出模具的设计,具备初步的模具设计能力。
2. 学生能够运用实验设备进行挤出成型实验,掌握实验操作的基本技能。
3. 学生能够分析挤出模具设计中的问题,并提出合理的改进方案。
情感态度价值观目标:1. 培养学生对塑料模具设计和制造的兴趣,激发学生的创新意识。
2. 培养学生严谨、细致的学习态度,提高学生的团队协作能力。
3. 学生能够认识到塑料模具在工业生产中的重要性,增强学生的社会责任感。
本课程针对高年级学生,结合学科特点和教学要求,以实用性为导向,旨在培养学生的模具设计能力、实验操作技能和问题分析解决能力。
通过本课程的学习,学生能够将理论知识与实际应用相结合,为未来从事相关工作奠定基础。
二、教学内容本章节教学内容主要包括以下三个方面:1. 塑料模具基础知识:- 模具的分类、结构及其工作原理。
- 塑料材料的基本性能及选用原则。
- 挤出模具的设计原理和流程。
2. 挤出模具设计方法:- 模具结构设计:包括型腔、型芯、导向装置等。
- 模具材料选择:根据塑料性能和成型工艺选择合适的模具材料。
- 模具工艺参数确定:分析成型过程中压力、温度、速度等参数的影响。
3. 挤出成型实验与问题分析:- 实验设备操作:学会使用挤出机、模具等设备进行实验。
- 实验操作技能:掌握挤出成型过程中各项操作要领。
- 常见问题分析:分析成型过程中可能出现的缺陷,并提出解决方案。
教学内容参考教材相关章节,结合课程目标,按照以下进度安排:1. 塑料模具基础知识(2课时)2. 挤出模具设计方法(3课时)3. 挤出成型实验与问题分析(3课时)三、教学方法本章节采用以下多样化的教学方法,以激发学生的学习兴趣和主动性:1. 讲授法:在塑料模具基础知识部分,通过教师系统的讲解,使学生掌握模具的基本概念、分类和工作原理。
pp注塑模具课程设计
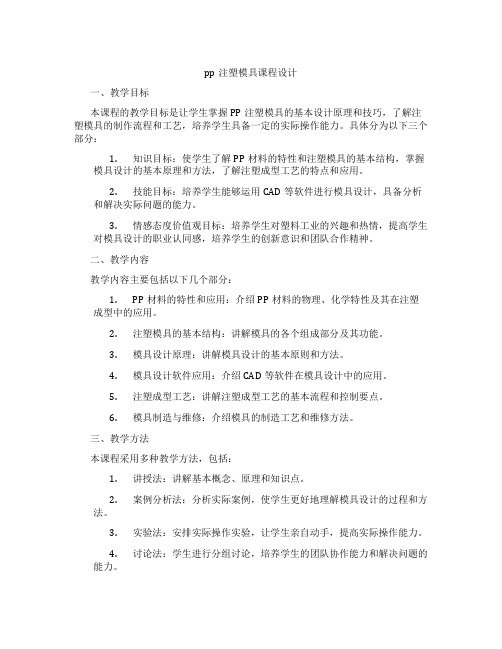
pp注塑模具课程设计一、教学目标本课程的教学目标是让学生掌握PP注塑模具的基本设计原理和技巧,了解注塑模具的制作流程和工艺,培养学生具备一定的实际操作能力。
具体分为以下三个部分:1.知识目标:使学生了解PP材料的特性和注塑模具的基本结构,掌握模具设计的基本原理和方法,了解注塑成型工艺的特点和应用。
2.技能目标:培养学生能够运用CAD等软件进行模具设计,具备分析和解决实际问题的能力。
3.情感态度价值观目标:培养学生对塑料工业的兴趣和热情,提高学生对模具设计的职业认同感,培养学生的创新意识和团队合作精神。
二、教学内容教学内容主要包括以下几个部分:1.PP材料的特性和应用:介绍PP材料的物理、化学特性及其在注塑成型中的应用。
2.注塑模具的基本结构:讲解模具的各个组成部分及其功能。
3.模具设计原理:讲解模具设计的基本原则和方法。
4.模具设计软件应用:介绍CAD等软件在模具设计中的应用。
5.注塑成型工艺:讲解注塑成型工艺的基本流程和控制要点。
6.模具制造与维修:介绍模具的制造工艺和维修方法。
三、教学方法本课程采用多种教学方法,包括:1.讲授法:讲解基本概念、原理和知识点。
2.案例分析法:分析实际案例,使学生更好地理解模具设计的过程和方法。
3.实验法:安排实际操作实验,让学生亲自动手,提高实际操作能力。
4.讨论法:学生进行分组讨论,培养学生的团队协作能力和解决问题的能力。
四、教学资源教学资源包括:1.教材:选用权威、实用的教材,为学生提供系统、全面的知识体系。
2.参考书:提供相关领域的参考书籍,丰富学生的知识储备。
3.多媒体资料:制作课件、视频等多媒体资料,提高课堂教学效果。
4.实验设备:提供现代化的实验设备,为学生提供实践操作的机会。
5.网络资源:利用网络资源,为学生提供更多的学习资料和信息。
五、教学评估本课程的评估方式包括以下几个方面:1.平时表现:评估学生在课堂上的参与程度、提问回答等情况,占总评的20%。
注塑模具课程设计
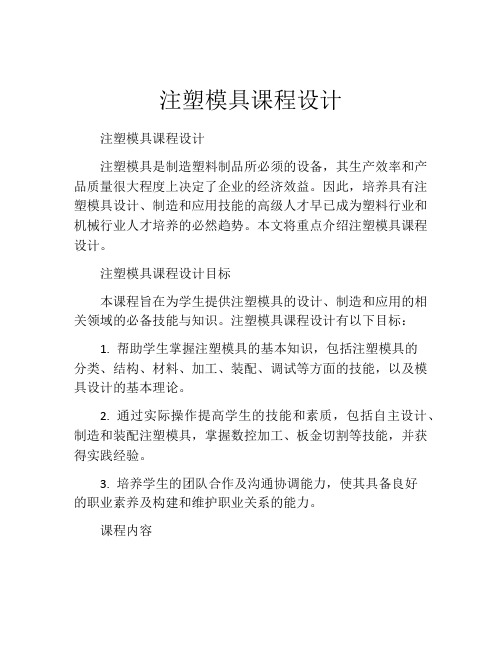
注塑模具课程设计注塑模具课程设计注塑模具是制造塑料制品所必须的设备,其生产效率和产品质量很大程度上决定了企业的经济效益。
因此,培养具有注塑模具设计、制造和应用技能的高级人才早已成为塑料行业和机械行业人才培养的必然趋势。
本文将重点介绍注塑模具课程设计。
注塑模具课程设计目标本课程旨在为学生提供注塑模具的设计、制造和应用的相关领域的必备技能与知识。
注塑模具课程设计有以下目标:1. 帮助学生掌握注塑模具的基本知识,包括注塑模具的分类、结构、材料、加工、装配、调试等方面的技能,以及模具设计的基本理论。
2. 通过实际操作提高学生的技能和素质,包括自主设计、制造和装配注塑模具,掌握数控加工、板金切割等技能,并获得实践经验。
3. 培养学生的团队合作及沟通协调能力,使其具备良好的职业素养及构建和维护职业关系的能力。
课程内容1. 注塑模具的基本知识:注塑模具的定义、分类和功能,模具的构成要素,模具材料及影响因素,注塑模具的制造工艺等。
2. 注塑模具的设计理论:模具的设计过程及其要素,模具设计参数的选取,模具外形及构造设计,模具零部件的设计,注塑模具设计的新技术和研究成果。
3. 模具制造工艺过程:模具制造工艺要点,模具金加工,模具板金工艺,模具装配及调试。
4. 数控加工及电脑辅助设计技术的应用:数控加工中心的技术原理、应用范围和特点,数控加工的编程,数控加工的优化及控制,电脑辅助设计及其基本原理。
5. 模具修理及维护:注塑模具的灰口维护,模具损坏原因的分析,维修工艺和维修方法。
6. 模具加工预备知识和实践:熟悉毛坯的形状和尺寸,了解机床的种类及其结构,掌握木模和模具板的基本手工操作,学会数控编程,掌握喷砂、喷粉末等加工技术。
教学方式1. 阅读注塑模具方面的图书和文献,了解模具设计、制造和应用的基本理论和方法。
2. 实验教学:针对注塑模具的基本操作技能和实用技术,进行实验教学。
3. 讲解教学:讲解注塑模具的设计原理、制造和应用方面的基本知识。
塑料模具课程设计实例
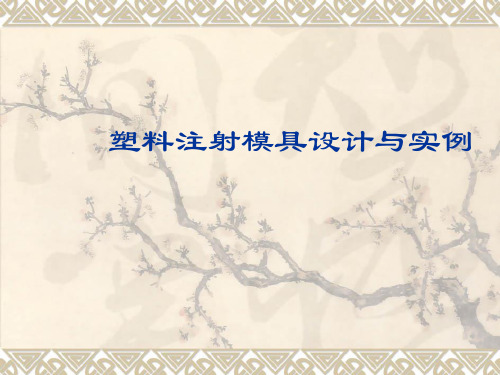
塑料注射模具设计与实例
本章基本内容
(2)模具钢
3Cr2Mo(P20)钢:可预硬化的塑料模具钢,预硬化后
硬度为36~38 HRC,适用于制作塑料注射模具型腔,其 加工性能和表面抛光性较好。 10Ni3CuAIVS(PMS)钢:析出硬化钢。预硬化后时效 硬化,硬度可达40~45 HRC。热变形极小,可做镜面抛 光,特别适合于腐蚀精细花纹。可用于制作尺寸精度高, 生产批量大的塑料注射模具。 6Ni7Ti2Cr钢:马氏体时效钢。在未加工前为固熔体 状态,易于加工。精加工后以480℃~520℃进行时效, 硬度可达50-57 HRC。适用于制造要求尺寸精度高的小 型塑料注射模具,可做镜面抛光。 8CrMnWMoVS(8CrMn)钢:为易切预硬化钢,可做镜面 抛光。其抗拉强度高,常用于大型注射模具。调质后硬 度为33-35 HRC,淬火时可空冷,硬度可达42-60 HRC。 25CrNi3MoAI钢:适用于型腔腐蚀花纹,属于时效硬 化钢。调质后硬度23 25 HRC,可用普通高速钢刀具加 工。时效后硬度38~42 HRC。可以做氮化处理,氮化处 理后表层硬度可达1100 HV。 Crl6Ni4Cu3Nb(PCR)钢:耐腐蚀钢。可以空冷淬火,
塑料注射模具制造特点 塑料注射模具零件常用加工方法和材料 塑料注射模具装配 塑料注射模具设计与制造实例
重点、难点
塑料注射模具制造特点 塑料注射模具零件常用加工方法和材料 塑料注射模具设计
- 1、下载文档前请自行甄别文档内容的完整性,平台不提供额外的编辑、内容补充、找答案等附加服务。
- 2、"仅部分预览"的文档,不可在线预览部分如存在完整性等问题,可反馈申请退款(可完整预览的文档不适用该条件!)。
- 3、如文档侵犯您的权益,请联系客服反馈,我们会尽快为您处理(人工客服工作时间:9:00-18:30)。
一、塑料的工艺性设计(1)、注塑模工艺干燥处理:如果储存适当则不需要干燥处理。
熔化温度:220~275℃,注意不要超过275℃。
模具温度:40~80℃,建议使用50℃。
结晶程度主要由模具温度决定。
注射压力:可大到1800b a r。
注射速度:通常,使用高速注塑可以使内部压力减小到最小。
如果制品表面出现了缺陷,那么应使用较高温度下的低速注塑。
流道和浇口:对于冷流道,典型的流道直径范围是4~7m m。
建议使用通体为圆形的注入口和流道。
所有类型的浇口都可以使用。
典型的浇口直径范围是1~1.5m m,但也可以使用小到0.7m m的浇口。
对于边缘浇口,最小的浇口深度应为壁厚的一半;最小的浇口宽度应至少为壁厚的两倍。
P P材料完全可以使用热流道系统。
成型时间:注射时间20s~60s高压时间0s~3s冷却时间20s~90s总周期50s~160s(2)、化学和物理特性P P是一种半结晶性材料。
它比P E要更坚硬并且有更高的熔点。
由于均聚物型的P P温度高于0℃以上时非常脆,因此许多商业的P P材料是加入1~4%乙烯的无规则共聚物或更高比率乙烯含量的钳段式共聚物。
共聚物型的P P材料有较低的热扭曲温度(100℃)、低透明度、低光泽度、低刚性,但是有更强的抗冲击强度。
P P的强度随着乙烯含量的增加而增大。
P P的维卡软化温度为150℃。
由于结晶度较高,这种材料的表面刚度和抗划痕特性很好。
P P不存在环境应力开裂问题。
通常,采用加入玻璃纤维、金属添加剂或热塑橡胶的方法对P P进行改性。
P P的流动率M F R范围在1~40。
低M F R的P P材料抗冲击特性较好但延展强度较低。
对于相同M F R的材料,共聚物型的强度比均聚物型的要高。
由于结晶,P P的收缩率相当高,一般为 1.8~2.5%。
并且收缩率的方向均匀性比P E-H D等材料要好得多。
加入30%的玻璃添加剂可以使收缩率降到0.7%。
均聚物型和共聚物型的P P 材料都具有优良的抗吸湿性、抗酸碱腐蚀性、抗溶解性。
然而,它对芳香烃(如苯)溶剂、氯化烃(四氯化碳)溶剂等没有抵抗力。
P P也不象P E那样在高温下仍具有抗氧化性。
(3)、塑件的尺寸与公差1、塑件的尺寸塑件尺寸的大小受制于以下因素:a)取决于用户的使用要求。
b)受制于塑件的流动性。
c)受制于塑料熔体在流动充填过程中所受到的结构阻力。
2、塑件尺寸公差标准a)影响塑件尺寸精度的因素主要有:塑料材料的收缩率及其波动。
b)塑件结构的复杂程度。
c)模具因素(含模具制造、模具磨损及寿命、模具的装配、模具的合模及模具设计的不合理所可能带来的形位误差等)。
d)成型工艺因素(模塑成型的温度T、压力p、时间t及取向、结晶、成型后处理等)。
e)成型设备的控制精度等。
其中,塑件尺寸精度主要取决于塑料收缩率的波动及模具制造误差。
题中没有公差值,则我们按未注公差的尺寸许偏差计算,查表取M T5。
3、塑件的表面质量塑件的表面质量包括塑件缺陷、表面光泽性与表面粗糙度,其与模塑成型工艺、塑料的品种、模具成型零件的表面粗糙度、模具的磨损程度等相关。
模具型腔的表面粗糙度通常应比塑件对应部位的表面粗糙度在数值上要低1-2级。
二、注射成型机的选择估算V=58.5g塑制品的正面投影面积S=103.81c m2V公=82c m3注射机为上海橡塑机厂的X S-Z Y-500卧试注塑机。
查表注射压力为104M P a,合模力为350×104N,注射方式为螺杆式,喷嘴球半径R为18m m,喷嘴口直径为7.5m m(一般工厂的塑胶部都拥有从小到大各种型号的注射机。
中等型号的占大部分,小型和大型的只占一小部分。
所以我们不必过多的考虑注射机型号。
具体到这套模具)。
三、型腔布局与分型面设计(1)、型腔数目的确定型腔数目的确定,应根据塑件的几何形状及尺寸、质量、批量大小、交货长短、注射能力、模具成本等要求来综合考虑。
根据注射机的额定锁模力F的要求来确定型腔数目n,即n式中F——注射机额定锁模力(N)P——型腔内塑料熔体的平均压力(M P a)A1、A2——分别为浇注系统和单个塑件在模具分型面上的投影面积(m m2)大多数小型件常用多型腔注射模,面高精度塑件的型腔数原则上不超过4个,生产中如果交货允许,我们根据上述公式估算,采用一模二腔。
(2)、型腔的布局考虑到模具成型零件和抽芯结构以及出模方式的设计,模具的型腔排列方式如下图所示:图(1)(3)、分型面的设计分型面位置选择的总体原则,是能保证塑件的质量、便于塑件脱模及简化模具的结构,分型面受到塑件在模具中的成型位置、浇注系统设计、塑件的结构工艺性及精度、嵌件位置形状以及推出方法、模具的制造、排气、操作工艺等多种因素的影响,因此在选择分型面时应综合分析比较具体可以从以下方面进行选择。
a)分型面应选在塑件外形最大轮廓处。
b)便于塑件顺利脱模,尽量使塑件开模时留在动模一边。
c)保证塑件的精度要求。
d)满足塑件的外观质量要求。
e)便于模具加工制造。
f)对成型面积的影响。
g)对排气效果的影响。
h)对侧向抽芯的影响。
图(2)四、浇注系统设计(1)、主流道设计主流道是一端与注射机喷嘴相接触,可看作是喷嘴的通道在模具中的延续,另一端与分流道相连的一段带有锥度的流动通道。
形状结构如图(3)所示,其设计要点:图(3)a)主流道设计成圆锥形,其锥角可取2°~6°,流道壁表面粗糙度取R a=0.63μm,且加工时应沿道轴向抛光。
b)主流道如端凹坑球面半径R2比注射机的、喷嘴球半径R1大1~2 m m;球面凹坑深度3~5m m;主流道始端入口直径d比注射机的喷嘴孔直径大0.5~1m m;一般d=2.5~5m m。
c)主流道末端呈圆无须过渡,圆角半径r=1~3m m。
d)主流道长度L以小于60m m为佳,最长不宜超过95m m。
e)主流道常开设在可拆卸的主流道衬套上;其材料常用T8A,热处理淬火后硬度53~57H R C。
(2)、主流道衬套的固定因为采用的有托唧咀,所以用定位圈配合固定在模具的面板上。
定位圈也是标准件,外径为Φ150m m,内径Φ31.5m m。
具体固定形式如图(4)所示:图(4)(3)、分流道的设计a)分流道是脱浇板下水平的流道。
为了便于加工及凝料脱模,分流道大多设置在分型面上,分流道截面形状一般为圆形梯形U形半圆形及矩形等,工程设计中常采用梯形截面加工工艺性好,且塑料熔体的热量散失流动阻力均不大,一般采用下面的经验公式可确定其截面尺寸:(式1)(式2)式中B―梯形大底边的宽度(m m)m―塑件的重量(g)L―分流道的长度(m m)H―梯形的高度(m m)质量大约58.5g,分流道的长度预计设计成190m m长,且有2个型腔,所以取B为15m m=10取H为10m m 根据实践经验,P P塑料分流道截面直径为 4.8~9.5。
所以我们可以选择截面直径为9.5m m,H=6.3m m。
梯形小底边宽度取8m m,其侧边与垂直于分型面的方向约成7°。
另外由于使用了水口板(即我们所说的定模板和中间板之间再加的一块板),分流道必须做成梯形截面,便于分流道和主流道凝料脱模。
如下图(5)所示:图(5)b)分流道长度分流道要尽可能短,且少弯折,便于注射成型过程中最经济地使用原料和注射机的能耗,减少压力损失和热量损失。
将分流道设计成直的,总长190m m。
c)分流道表面粗糙度由于分流道中与模具接触的外层塑料迅速冷却,只有中心部位的塑料熔体的流动状态较为理想,因面分流道的内表面粗糙度R a并不要求很低,一般取 1.6μm左右既可,这样表面稍不光滑,有助于塑料熔体的外层冷却皮层固定,从而与中心部位的熔体之间产生一定的速度差,以保证熔体流动时具有适宜的剪切速率和剪切热。
d)分流道表面粗糙度分流道在分型面上的布置与前面所述型腔排列密切相关,有多种不同的布置形式,但应遵循两方面原则:即一方面排列紧凑、缩小模具板面尺寸;另一方面流程尽量短、锁模力力求平衡。
本模具的流道布置形式采用平衡式,如图(1)所示。
(4)、浇口的设计浇口亦称进料口,是连接分流道与型腔的通道,除直接浇口外,它是浇注系统中截面最小的部分,但却是浇注系统的关键部分,浇口的位置、形状及尺寸对塑件性能和质量的影响很大。
a)浇口的选用它是流道系统和型腔之间的通道,这里我们采用点浇口:✧浇口在成形自动切数断,故有利于自动成形。
✧浇口的痕迹不明显,通常不必后加工。
✧浇口之压力损失大,必须高之射出压力。
✧浇口部份易被固化之残锱树脂堵隹。
它常用于成型中、小型塑料件的一模多腔的模具中,也可用于单型腔模具或表面不允许有较大痕迹的塑件。
b)浇口位置的选用模具设计时,浇口的位置及尺寸要求比较严格,初步试模后还需进一步修改浇口尺寸,无论采用何种浇口,其开设位置对塑件成型性能及质量影响很大,因此合理选择浇口的开设位置是提高质量的重要环节,同时浇口位置的不同还影响模具结构。
总之要使塑件具有良好的性能与外表,一定要认真考虑浇口位置的选择,如图(6)所示。
通常要考虑以下几项原则:✧尽量缩短流动距离。
✧浇口应开设在塑件壁厚最大处。
✧必须尽量减少熔接痕。
✧应有利于型腔中气体排出。
✧考虑分子定向影响。
✧避免产生喷射和蠕动。
✧浇口处避免弯曲和受冲击载荷。
✧注意对外观质量的影响。
图(6)c)浇注系统的平衡对于中小型塑件的注射模具己广泛使用一模多腔的形式,设计应尽量保证所有的型腔同时得到均一的充填和成型。
一般在塑件形状及模具结构允许的情况下,应将从主流道到各个型腔的分流道设计成长度相等、形状及截面尺寸相同(型腔布局为平衡式)的形式,否则就需要通过调节浇口尺寸使各浇口的流量及成型工艺条件达到一致,这就是浇注系统的平衡。
显然,我们设计的模具是平衡式的,即从主流道到各个型腔的分流道的长度相等,形状及截面尺寸都相同。
d)排气的设计排气槽的作用主要有两点。
一是在注射熔融物料时,排除模腔内的空气;二是排除物料在加热过程中产生的各种气体。
越是薄壁制品,越是远离浇口的部位,排气槽的开设就显得尤为重要。
另外对于小型件或精密零件也要重视排气槽的开设,因为它除了能避免制品表面灼伤和注射量不足外,还可以消除制品的各种缺陷,减少模具污染等。
那么,模腔的排气怎样才算充分呢?一般来说,若以最高的注射速率注射熔料,在制品上却未留下焦斑,就可以认为模腔内的排气是充分的。
适当地开设排气槽;可以大大降低注射压力、注射时间。
保压时间以及锁模压力,使塑件成型由困难变为容易,从而提高生产效率,降低生产成本,降低机器的能量消耗。
其设计往往主要靠实践经验,通过试模与修模再加以完善,此模我们利用模具零部件的配合间隙及分型面自然排气。
五、成型零件的设计模具中决定塑件几何形状和尺寸的零件称为成型零件,包括凹模、型芯、镶块、成型杆和成型环等。