油漆涂装规范
喷漆的规章制度
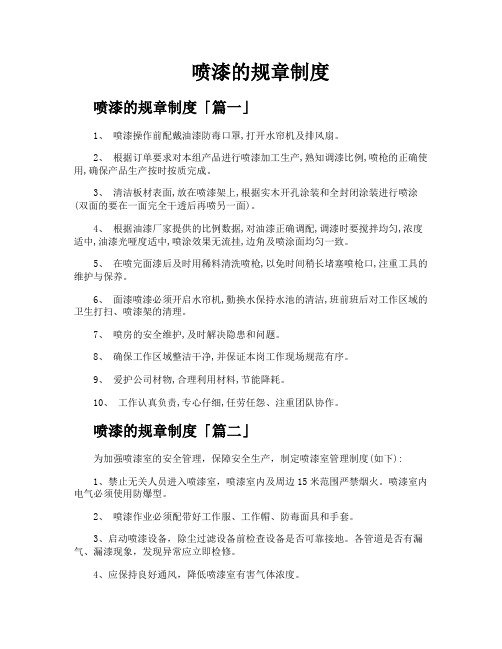
喷漆的规章制度喷漆的规章制度「篇一」1、喷漆操作前配戴油漆防毒口罩,打开水帘机及排风扇。
2、根据订单要求对本组产品进行喷漆加工生产,熟知调漆比例,喷枪的正确使用,确保产品生产按时按质完成。
3、清洁板材表面,放在喷漆架上,根据实木开孔涂装和全封闭涂装进行喷涂(双面的要在一面完全干透后再喷另一面)。
4、根据油漆厂家提供的比例数据,对油漆正确调配,调漆时要搅拌均匀,浓度适中,油漆光哑度适中,喷涂效果无流挂,边角及喷涂面均匀一致。
5、在喷完面漆后及时用稀料清洗喷枪,以免时间稍长堵塞喷枪口,注重工具的维护与保养。
6、面漆喷漆必须开启水帘机,勤换水保持水池的清洁,班前班后对工作区域的卫生打扫、喷漆架的清理。
7、喷房的安全维护,及时解决隐患和问题。
8、确保工作区域整洁干净,并保证本岗工作现场规范有序。
9、爱护公司材物,合理利用材料,节能降耗。
10、工作认真负责,专心仔细,任劳任怨、注重团队协作。
喷漆的规章制度「篇二」为加强喷漆室的安全管理,保障安全生产,制定喷漆室管理制度(如下):1、禁止无关人员进入喷漆室,喷漆室内及周边15米范围严禁烟火。
喷漆室内电气必须使用防爆型。
2、喷漆作业必须配带好工作服、工作帽、防毒面具和手套。
3、启动喷漆设备,除尘过滤设备前检查设备是否可靠接地。
各管道是否有漏气、漏漆现象,发现异常应立即检修。
4、应保持良好通风,降低喷漆室有害气体浓度。
5、盛装油漆、稀释剂的容器不使用时必须处于密闭状态。
6、喷漆室内外应配备使用的足量的消防器材,并摆放在明显位置,任何人不得随意挪动灭火器材的位置,喷漆人员应会使用各种消防器材。
7、喷漆及除尘设备在使用中发现异常,应立即停车并上报。
8、工作完毕后必须清洁设备及工作场所,关闭气、电开关。
9、除喷漆室工作人员和维修人员外,任何人不准启动喷漆室的所有设备。
10、操作人员进行喷漆作业时,还应遵守《喷漆工安全操作规程》。
喷漆的规章制度「篇三」1.0目的加强喷漆人员的安全管理,保障安全生产。
涂装通用技术条件
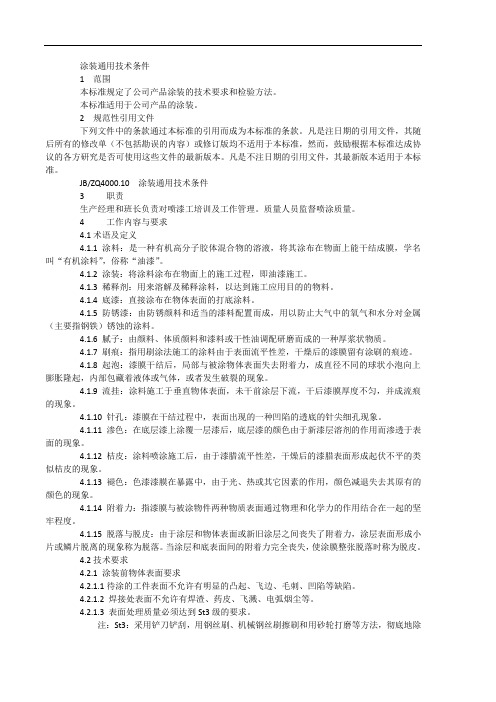
涂装通用技术条件1 范围本标准规定了公司产品涂装的技术要求和检验方法。
本标准适用于公司产品的涂装。
2 规范性引用文件下列文件中的条款通过本标准的引用而成为本标准的条款。
凡是注日期的引用文件,其随后所有的修改单(不包括勘误的内容)或修订版均不适用于本标准,然而,鼓励根据本标准达成协议的各方研究是否可使用这些文件的最新版本。
凡是不注日期的引用文件,其最新版本适用于本标准。
JB/ZQ4000.10 涂装通用技术条件3 职责生产经理和班长负责对喷漆工培训及工作管理。
质量人员监督喷涂质量。
4 工作内容与要求4.1术语及定义4.1.1 涂料:是一种有机高分子胶体混合物的溶液,将其涂布在物面上能干结成膜,学名叫“有机涂料”,俗称“油漆”。
4.1.2 涂装:将涂料涂布在物面上的施工过程,即油漆施工。
4.1.3 稀释剂:用来溶解及稀释涂料,以达到施工应用目的的物料。
4.1.4 底漆:直接涂布在物体表面的打底涂料。
4.1.5 防锈漆:由防锈颜料和适当的漆料配置而成,用以防止大气中的氧气和水分对金属(主要指钢铁)锈蚀的涂料。
4.1.6 腻子:由颜料、体质颜料和漆料或干性油调配研磨而成的一种厚浆状物质。
4.1.7 刷痕:指用刷涂法施工的涂料由于表面流平性差,干燥后的漆膜留有涂刷的痕迹。
4.1.8 起泡:漆膜干结后,局部与被涂物体表面失去附着力,成直径不同的球状小泡向上膨胀隆起,内部包藏着液体或气体,或者发生破裂的现象。
4.1.9 流挂:涂料施工于垂直物体表面,未干前涂层下流,干后漆膜厚度不匀,并成流痕的现象。
4.1.10 针孔:漆膜在干结过程中,表面出现的一种凹陷的透底的针尖细孔现象。
4.1.11 渗色:在底层漆上涂覆一层漆后,底层漆的颜色由于新漆层溶剂的作用而渗透于表面的现象。
4.1.12 桔皮:涂料喷涂施工后,由于漆腊流平性差,干燥后的漆腊表面形成起伏不平的类似桔皮的现象。
4.1.13 褪色:色漆漆膜在暴露中,由于光、热或其它因素的作用,颜色减退失去其原有的颜色的现象。
GB6514-2008涂装作业安全规程-涂漆工艺安全及其通风净化
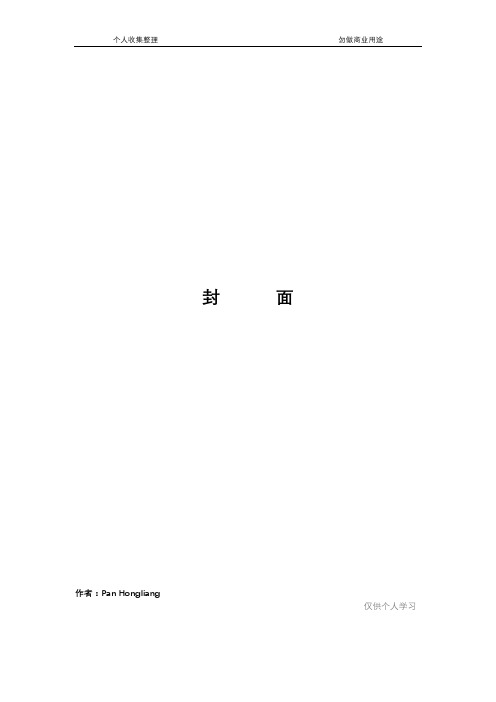
封面作者:Pan Hongliang仅供个人学习中华人民共和国国家标准涂装作业安全规程涂漆工艺安全及其通风净化GB 6514—2008代替GB 6514—1995 2008—12-11发布2009—10—01实施中华人民共和国质量监督检验检疫总局中国国家标准化管理委员会前言本标准除第1章、第2章、第3章为推荐性外,其余为强制性。
《涂装作业安全规程》系列国家标准已制订的共有12项:——GB 6514—2008《涂装作业安全规程涂漆工艺安全及其通风净化》;——GB 7691—2003《涂装作业安全规程安全管理通则》;——GB 7692—1999《涂装作业安全规程涂漆前处理工艺安全及其通风净化》;——GB 12367—2006《涂装作业安全规程静电喷漆工艺安全》;——GB 12942—2006《涂装作业安全规程有限空间作业安全技术要求》;——GB/T 1444 1—2008《涂装作业安全规程术语》;——GB 14443—2007《涂装作业安全规程涂层烘干室安全技术规定》;——GB 14444—2006《涂装作业安全规程喷漆室安全技术规定》;——GB 14773—2007《涂装作业安全规程静电喷枪及其辅助装置安全技术条件》;——GB 15607—2008《涂装作业安全规程粉末静电喷涂工艺安全》;——GB 17750—1999《涂装作业安全规程浸涂工艺安全》;——GB 20101—2006《涂装作业安全规程有机废气净化装置安全技术规定》。
本标准为《涂装作业安全规程》系列标准之一。
本标准对应于美国防火协会标准NFPA 33《易燃和可燃材料喷涂作业标准》(2007版),与NFPA 33:2007版一致性程度为非等效。
本标准修订并代替GB 6514—1995《涂装作业安全规程涂漆工艺安全及其通风净化》。
本标准与GB 6514—1995((涂装作业安全规程涂漆工艺安全及其通风净化》相比,主要差异如下:——增加、更新了引用的国家标准。
GB涂装作业安全规程涂漆工艺安全及其通风净化

中华人民共和国国家标准涂装作业安全规程涂漆工艺安全及其通风净化GB 6514—2008代替GB 6514—1995 2008—12-11发布2009—10—01实施中华人民共和国质量监督检验检疫总局中国国家标准化管理委员会前言本标准除第1章、第2章、第3章为推荐性外,其余为强制性。
《涂装作业安全规程》系列国家标准已制订的共有12项:——GB 6514—2008《涂装作业安全规程涂漆工艺安全及其通风净化》;——GB 7691—2003《涂装作业安全规程安全管理通则》;——GB 7692—1999《涂装作业安全规程涂漆前处理工艺安全及其通风净化》;——GB 12367—2006《涂装作业安全规程静电喷漆工艺安全》;——GB 12942—2006《涂装作业安全规程有限空间作业安全技术要求》;——GB/T 1444 1—2008《涂装作业安全规程术语》;——GB 14443—2007《涂装作业安全规程涂层烘干室安全技术规定》;——GB 14444—2006《涂装作业安全规程喷漆室安全技术规定》;——GB 14773—2007《涂装作业安全规程静电喷枪及其辅助装置安全技术条件》;——GB 15607—2008《涂装作业安全规程粉末静电喷涂工艺安全》;——GB 17750—1999《涂装作业安全规程浸涂工艺安全》;——GB 20101—2006《涂装作业安全规程有机废气净化装置安全技术规定》。
本标准为《涂装作业安全规程》系列标准之一。
本标准对应于美国防火协会标准NFPA 33《易燃和可燃材料喷涂作业标准》(2007版),与NFPA 33:2007版一致性程度为非等效。
本标准修订并代替GB 6514—1995《涂装作业安全规程涂漆工艺安全及其通风净化》。
本标准与GB 6514—1995((涂装作业安全规程涂漆工艺安全及其通风净化》相比,主要差异如下:——增加、更新了引用的国家标准。
——引用GB 50016—2006中有关条文和表作为涂漆作业场所火灾危险性分类的依据。
涂装作业安全规程-涂漆工艺安全及其通风净化(GB6514—2008)

涂装作业安全规程涂漆工艺安全及其通风净化(GB6514—2008)1范围本标准规定了涂漆工艺及其通风净化的安全卫生技术要求。
本标准适用于涂漆工艺及其通风净化系统的设计、安装及使用.桥梁、建筑物、大型储罐、船舶等大型构件的室外涂漆工艺的通风净化亦可参照使用。
2规范性引用文件下列文件中的条款通过本标准的引用而成为本标准的条款。
凡是注日期的引用文件,其随后所有的修改单(不包括勘误的内容)或修订版均不适用于本标准,然而,鼓励根据本标准达成协议的各方研究是否使用这些文件的最新版本。
凡是不注日期的引用文件,其最新版本适用于本标准。
GB 7691 涂装作业安全规程安全管理通则GB8978 污水综合排放标准GB12367 涂装作业安全规程静电喷漆工艺安全GB12942 涂装作业安全规程有限空间作业安全技术要求GB/T14441 涂装作业安全规程术语GB/T14443—2007 涂装作业安全规程涂层烘干室安全技术规定GB14444—2006 涂装作业安全规程喷漆室安全技术规定GB14773涂装作业安全规程静电喷枪及其辅助装置安全技术条件GB15607—2008 涂装作业安全规程粉末静电喷涂工艺安全GB16297 大气污染物综合排放标准GB17750 涂装作业安全规程浸涂工艺安全GB20101 涂装作业安全规程有机废气净化装置安全技术规定GB50016—2006 建筑设计防火规范GB50057—2000 建筑物防雷设计规范GB50058 爆炸和火灾危险环境电力装置设计规范GB50140 建筑灭火器配置设计规范3术语和定义GB/T14441确立的以及下列术语和定义适用于本标准3。
1涂漆工艺painting process涂装作业中涂料涂覆的整个工艺过程。
包括涂料的调配、工件的输送、各种方法的涂覆、干燥或固化、打磨和刮腻子等工序。
3.2涂漆作业场所location of painting operations为涂漆作业专门设置的场地和特定的周围空间。
涂装作业安全规程涂装工程安全设施验收规范

涂装作业安全规程涂装工程安全设施验收规范(总7页)--本页仅作为文档封面,使用时请直接删除即可----内页可以根据需求调整合适字体及大小--涂装作业安全规程涂装工程安全设施验收规范AQ 5201-20071 范围本标准规定了新建、改建、扩建涂装工程(包括涂装设备、器械)和作业场所安全设施进行验收的基本原则。
本标准适用于使用涂料及有关化学品(包括有机溶剂)在金属或非金属表面的涂装工程,包括塑料制品、纺织品、皮革制品、木制品等非金属的涂装工程安全设施验收。
涂装工艺、涂装作业场所、涂装设备器械的设计、生产、制造和安装等的安全技术审查;露天涂装作业,建筑物、构筑物内外涂饰等涉及涂装工程安全的技术审查亦可参照本标准。
2 引用标准下列文件的条款通过本标准的引用而成为本标准的条款。
凡是注日期的引用文件,其随后所有的修改单(不包括勘误的内容)或修订版均不适用于本标准,然而,鼓励根据本标准达成协议的各方研究是否可使用这些文件的最新版本。
凡是不注日期的引用文件,其最新版本适用于本标准。
GB 935 高温作业允许持续接触热时间限值GB 4064 电气设备安全设计导则GB 5083 生产设备安全卫生设计总则GB 6514-1995 涂装作业安全规程涂漆工艺安全及其通风净化GB 7691-2003 涂装作业安全规程安全管理通则GB 7692-1999 涂装作业安全规程涂漆前处理工艺安全及其通风净化GB 12942-2006 涂装作业安全规程有限空间作业安全技术要求GB/T 14441-1993 涂装作业安全规程术语GB 14443 涂装作业安全规程涂层烘干室安全技术规定GB 14444-2006 涂装作业安全规程喷漆室安全技术规定GB 14773 涂装作业安全规程静电喷枪及其辅助装置安全技术条件GB 15607-1995 涂装作业安全规程粉末静电喷涂工艺安全GB 16297 大气污染物综合排放标准GB 20101-2006 涂装作业安全规程有机废气净化装置安全技术规定GB 50016 建筑设计防火规范GB 50057 建筑物防雷设计规范GB 50058-1992 爆炸和火灾危险环境电力装置设计规范GB Z1-2002 工业企业设计卫生标准GB Z2-2002工作场所有害因素职业接触限值3 术语和定义标准GB/T 14441中确立的术语和定义适用于本标准。
GB6514_2008涂装作业安全规程_涂漆工艺设计安全和通风净化
中华人民共和国国家标准涂装作业安全规程涂漆工艺安全及其通风净化GB 6514—2008代替GB 6514—19952008—12-11发布2009—10—01实施中华人民共和国质量监督检验检疫总局中国国家标准化管理委员会前言本标准除第1章、第2章、第3章为推荐性外,其余为强制性。
《涂装作业安全规程》系列国家标准已制订的共有12项:——GB 6514—2008《涂装作业安全规程涂漆工艺安全及其通风净化》;——GB 7691—2003《涂装作业安全规程安全管理通则》;——GB 7692—1999《涂装作业安全规程涂漆前处理工艺安全及其通风净化》;——GB 12367—2006《涂装作业安全规程静电喷漆工艺安全》;——GB 12942—2006《涂装作业安全规程有限空间作业安全技术要求》;——GB/T 1444 1—2008《涂装作业安全规程术语》;——GB 14443—2007《涂装作业安全规程涂层烘干室安全技术规定》;——GB 14444—2006《涂装作业安全规程喷漆室安全技术规定》;——GB 14773—2007《涂装作业安全规程静电喷枪及其辅助装置安全技术条件》;——GB 15607—2008《涂装作业安全规程粉末静电喷涂工艺安全》;——GB 17750—1999《涂装作业安全规程浸涂工艺安全》;——GB 20101—2006《涂装作业安全规程有机废气净化装置安全技术规定》。
本标准为《涂装作业安全规程》系列标准之一。
本标准对应于美国防火协会标准NFPA 33《易燃和可燃材料喷涂作业标准》(2007版),与NFPA 33:2007版一致性程度为非等效。
本标准修订并代替GB 6514—1995《涂装作业安全规程涂漆工艺安全及其通风净化》。
本标准与GB 6514—1995((涂装作业安全规程涂漆工艺安全及其通风净化》相比,主要差异如下:——增加、更新了引用的国家标准。
——引用GB 50016—2006中有关条文和表作为涂漆作业场所火灾危险性分类的依据。
产品油漆涂装技术规范及验收标准N
产品油漆涂装技术规范及验收标准NO:1303(上海吉飞国际贸易有限公司技术文件)前言:油漆:是将金属工件涂覆漆层来保护金属及产品改观外观的一种方法, 将金属工件表面处理后涂覆底漆及有色面漆,以达到金属产品防腐及良好的外观的一种手段。
我司的产品如各类舱盖\滚轮\绞车\及其它凡需涂油漆的产品:分无面漆(只有底漆)及有底漆又有面漆两种.现分别作出如下规定及验收标准:一:引用文件:JB/ZQ4000.10-86 GB1720-89 GB1771-91 GB1763-89 GB1865-89以及客户提出的技术要求:二:油漆工艺基本要求:1:被漆件漆前处理:(被漆件漆前处理好坏直接影响到镀层质量)1.1被漆件表面必须除锈以及清除焊接部位的焊渣,必要时进行抛丸及喷砂处理,表面处理的标准应达到以下要求:a.船用产品因其使用环境要求,其表面处理质量必须达到sa21/2级或SSPC-SP.6—7级的要求。
b.在轻度腐蚀性环境中的产品其表面处理质量必须达到sa2级或SSPC-SP.6级。
c.如产品要与高温环境接触,其表面处理质量必须达到st2级。
e.尺寸与重量较大的产品应达到st3级除锈要求。
g.铸钢及锻件产品涂装前表面的平度在任意方向600mm长度上不得大于3mm,并不允许有名显的凸起、飞边、毛刺、浇冒口等缺陷。
h.焊接件涂装的表面不允许有焊渣、飞溅、药皮、电弧烟尘及机械加工残留的飞边及毛刺。
1.2被漆件必须通过脱脂工艺去除表面的油污(可以采用化学去污挥发剂)1.3被漆件由于抛丸及喷砂处理后可能产生浮锈,所以镀前工件必须酸洗或人工打磨除锈。
1.4酸洗后的工件应按规定科学去酸及清洗1.5工件表面缺陷不允许用腻子修补,应用电焊按规范修补,焊补处应打磨光滑。
1.6客户有注明要求打底漆的产品必须按规范打底漆,底漆的涂覆不少于2道。
底漆厚度不小于30—40um.。
2: 涂装油漆2.1漆的质量要求:涂装所用的漆必须国标产品,应能满足或优于客户技术要求,船舶装备的油漆必须符合船用油漆标准。
ISO9001-2015油漆喷涂质量检验规范
油漆喷涂质量检验规范
(ISO9001:2015)
1 目的
本检验作业指导书规定了油漆涂层的检验内容与技术要求。
2 范围
本检验作业指导书适用于公司自制件及所有外委、外协制件的油漆涂装质量检验。
3 引用标准
下列标准包括的条文,通过在本检验作业指导书中的引用而构成本检验作业指导书的条文。
在本检验作业指导书发布时,所示版本均为有效。
所有标准都会被修订,使用本检验作业指导书的各方应探讨使用下列标准最新版本的可能性。
Q/LQB Y-4-2011 《汽车涂层标准》
GB/T 13452.2-2008 《色漆和清漆漆膜厚度的测定》
GB/T 6739-2006 《硬度铅笔测试法》
GB/T 9286-1998 《漆和清漆漆膜的划格实验》
《自然耐候性试验标准》
4 检验条件
4.1 检验环境
检验在生产现场的检验工位进行。
当异地检验存在争议时,选用的检验场地应符合下列条件:4.1.1 环境整洁,空气清新,不应有明显影响检验作业的热气、湿气、烟尘。
汽车车身油漆涂装检验规范
汽车车身油漆涂装检验规范1主题内容与适用范围本标准规定了汽车车身油漆涂装检验的检验内容、技术要求、检验方法以及检验记录要求。
2引用标准下列标准所包含的条文,通过在本标准中引用而构成本标准的条文。
在标准出版时,所示版本均为有效,所有标准都会被修订,使用本标准的各方应探讨使用下列标准最新版本的可能性。
QC/T484 汽车油漆涂层GB 1728 涂膜、腻子干燥时间测定方法GB 1764 漆膜厚度测定方法GB 1743 漆膜光泽测定法GB 1720 漆膜附着力测定法3用语解释3.1漆后车身漆后车身是指油漆涂层涂装施工完成后的车身。
3.2油漆涂层缺陷用语4 检验条件4.1 检验环境4.1.1 环境整洁,空气清新。
不应有明显影响检验作业的热气、湿气、烟尘,噪声不得高于70dB(A)。
4.1.2 采用带反射板自然纯正色日光灯照明,照度(1000~2000)lx。
4.2 检验人员检验人员辩色力正常,视力在0.8以上(含校正后)。
检验人员应具有较丰富的油漆涂装检验知识和实践经验,了解涂装工艺规程及技术要求。
检验时,着中性颜色工装。
4.3检验仪器及量器具4.3.1 检验仪器:磁性测厚仪、光电光泽仪、划格器等。
4.3.2 量器具:钢板尺、中华牌高级绘图铅笔(H、HB、B三种规格)、单面刀片等。
4.3.3 所用仪器及量具应符合计量检定要求,并在有效检定周期内。
5检验内容5.1表面油漆涂层质量表面油漆涂层质量检验包括:生锈、起泡、脱落、裂纹、露底、桔皮、油漆损伤、流痕、发花、色差、针孔、颗粒、絮状丝、砂纸纹、板金凸凹、缩孔、划伤、流挂、漆薄、灰印、湿印、油点、斑痕、痱子等缺陷,并检验漆膜硬度、厚度、附着力、光泽性能等。
5.2隔音绝热涂层及密封耐磨涂层质量隔音绝热涂层及密封耐磨涂层质量检验包括:漏涂、脱落、堆积(结块)、开裂等缺陷,并检验涂层干燥状况及厚度等。
6检验程序及方法6.1涂装表面检验区域划分根据各涂装表面对质量影响的程度,把车身表面划分为A、B、C、D、E五个检验区域。
- 1、下载文档前请自行甄别文档内容的完整性,平台不提供额外的编辑、内容补充、找答案等附加服务。
- 2、"仅部分预览"的文档,不可在线预览部分如存在完整性等问题,可反馈申请退款(可完整预览的文档不适用该条件!)。
- 3、如文档侵犯您的权益,请联系客服反馈,我们会尽快为您处理(人工客服工作时间:9:00-18:30)。
********有限公司*********项目油漆与涂料规范书控制表*文件状态关键编码A=工作可能进行B=修订。
加入指出的变动。
不要求再次提交。
工作可能进行。
C=修订并再次提交。
工作可能进行,综合业主意见。
D=修订并再次提交。
工作不可能进行。
E=不要求审查。
工作可能进行。
目录1 范围 (3)2 定义 (3)3 例外 (3)4 可适用的标准和技术规范 (3)5 油漆供应商 (3)6 一般要求 (3)7 工作规范 (3)7.1 表面处理 (3)7.2 对碳素钢表面进行喷砂清理 (4)7.3 对不锈钢表面进行喷砂清理 (4)8 操作规程、限制和质量 (4)9 与混凝土接触或包裹在混凝土内的碳素钢表面 (5)10 修复 (5)11 涂层系统 (5)11.1 概要 (5)11.2 油漆原料 (5)12 检验与试验 (6)12.1 涂层厚度 (6)12.2 粘附力试验 (6)13 安全 (6)14 成品搬运和装运 (7)15 报告和合同文档 (7)16 担保 (7)17 文档列表 (7)1 范围防火技术规范不包含在本范围内。
2 定义•项目:•业主:•承包商:•卖方:•工地:•涂漆公司:负责涂漆工作的公司•材料:油漆、树脂、涂剂、硫化剂、稀释剂、溶剂、磨料、粘合剂等。
•涂漆工序:实施多个涂层,达到防锈效果。
•检验员:负责涂漆工作的人员3 例外由不锈钢或有色金属等耐腐蚀材料制成的设备,除非另有说明。
完全与大气成分隔绝的过程与非过程区域的内表面,除非另有说明。
4 可适用的标准和技术规范附录A列出的规范和标准。
偏离下文列出的文档的地方应通过变更控制程序以书面形式确定下来。
5 油漆供应商•合格的油漆供应商名单:AMERON(亚美隆)、INTERNATIONAL(“国际”牌)、CARBOLINE(大连卡宝拉因油漆有限公司)、JOTUN(佐敦)。
在书面申请之后,其他公司也可能获准成为本项目的油漆供应商。
6 一般要求a) 涂漆公司应基于当前的技术规范,向承包商提交它自己的涂漆工艺规程。
b) 在所有热处理、压力试验和检查完成之后,应对设备和管道进行涂漆。
c) 除非事先得到承包商/业主和油漆制造商的书面许可,否则不得置换或更改本技术规范详细说明的原料和使用方法。
d) 依照本技术规范的规定及其附录、可适用标准列表,对绝缘和无绝缘设备和管道进行特别处理和涂漆。
持续低温装置(及低于低温绝缘)中的设备、容器和管道不得涂漆。
7 工作规范7.1 表面处理a) 清除油料、油脂、蜡、杂质和其他外来杂质,去除裸金属的油脂。
b) 在喷磨之前,应按照ISO 12944-3标准规定的机械法冲洗和磨平所有毛边、陡沿、裂片、叠层及其他表面缺陷。
所有火焰切割区域应磨光,使表面呈现均匀平整的状态,去处硬层,以达到规定的光洁度。
c) 容器、管道及其他附属部件的开口必须保护好,避免磨料进入。
d) 喷砂前后,应严格检查所有焊缝,仔细查看是否存在焊剂、溅出物、裂片、夹杂物、叠片和隐藏的轧制铁鳞。
应采用机械的方法去除缺陷,纠正焊缝气孔和焊接小孔,并重新对相关区域进行喷砂。
待涂层的表面在进行各项涂层工序之前,应先利用洁净的干燥空气或工业用真空清洁器吹拂表面,去除所有灰尘。
按照ISO 8502-3标准,对钢铁表面的灰尘等级进行评定,可接受的最高级:2级。
7.2 对碳素钢表面进行喷砂清理a) 涂层时,应遵照ISO 8501-1 喷砂级别SA 2.½或SA3,对碳钢表面进行喷砂清理,除非另有说明。
b) 遵照ISO 8503-1要求,以及各道油漆系统对光洁度的要求,或供应商/制造商(附录B)规定的要求,检查表面光洁度。
c) 喷砂磨料应干燥、洁净、不含污染物,且类型和大小应可呈现符合油漆制造商底漆数据表规定的总体光洁度。
喷磨操作应远离涂层操作的区域和未干的贴合表面。
d) 不得在项目有关机械、带活动件的设备以及可调节仪器附近进行喷磨。
e) 喷砂应在预加工期间在截短区域(cutback area)进行,但不用涂漆(用胶带保护)。
焊接之后,根据第7.2.f段的说明对截断区域进行喷砂,并依照本技术规范进行涂漆。
f) 表面喷砂应深入25毫米,与之前的贴合表面联接。
g) 之前涂层的边缘应立即采用喷砂清理(或用砂纸擦光)的方法变平整。
h) 喷磨之后,刷第一遍底漆之前,不得在表面应用任何酸性冲洗液、洗涤液、溶剂或禁止的防锈冲洗液。
i) 磨料不得含有杂质或污染物,而且应遵守所有可适用的地方或国家卫生法规。
j) 在钢铁的表面温度没有比空气露点高3°C(5°F)以上或表面湿润的情况下,不得进行喷砂。
k) 为喷砂操作供应的压缩空气不得含有油水。
应按照ASTM D 4285标准开展试验。
应提供调压器、过滤器、分离器和捕集器,并经常进行检查和清空。
l) 只可在日间进行喷砂工作,而且只能在当天日落之前将上第一遍底漆的表面上进行喷砂(不适用于封闭式车间。
在这种情况下,应当控制气候条件)。
m) 喷砂之前,应采用适当的方法对法兰表面进行保护。
n) 如果不可能进行喷砂清理,或者喷砂清理会危及附近安全(安全原因,靠近机械设备等),应采用人工或机械(动力工具)清洁方式。
这一工序将去除杂质、铁锈、散落的轧屑,并通过人工砂轮清理、废弃、钢刷清理等方式,或者,尽可能采用钢丝刷或撞针枪等符合ISO 8504-3动力工具清理级别ST 3的动力工具,对金属表面进行预处理。
完成之后,表面应泛发出金属的光彩。
一般而言,要求获得承包商的许可。
7.3 对不锈钢表面进行喷砂清理第7.1段、7.2段为可适用的规定。
喷砂磨料不得含有铁素颗粒,类型和大小应可呈现ISO 8503-1 to 4 visual M标准要求的光洁度。
喷砂操作应在独立的区域(喷砂室)进行,并避免任何铁素污染。
8 操作规程、限制和质量a) 应根据油漆制造商的要求进行涂漆。
必须注意稀释、搅拌和连续涂层之间的固化时间。
应进行溶剂摩擦试验,在上末道漆之前检查无机硅酸锌涂料的固化情况。
b) 应刷涂表面,使表面涂层看起来平滑、均匀。
不得存在过厚涂漆或有害的刷痕。
所有缝隙和角落都应着色。
在干燥之前,应去除喷涂过量之处。
c) 在涂抹规定的涂层之前,应刷掉所有区域的外部角落和边缘、焊接处、螺栓、螺母和裂缝(除了镀锌表面),确保这些区域达到规定的最低薄膜厚度,并保证表层的连续性。
d) 在涂漆之后应进行焊接的所有区域应在喷砂清理之后盖上。
可以采用合适的胶带掩盖。
胶带可在待焊接区域的各个方向延伸至少50毫米。
涂漆之后应去掉掩盖物。
e) 在下列情况下,不得进行涂层操作:- 表面温度没有比空气露点高出3°C以上。
- 环氧涂层的空气相对湿度在85%以上,锌硅酸盐涂层的空气相对湿度在90%以上(根据制造商的建议);或操作之后两个小时之内气候变化可能导致温度低于规定的温度(在+10°C 和+49°C之间或制造商建议的温度)或者导致水分以雨水或冷凝物的形式沉积在表面。
f) 进行喷砂清理之前应将铭牌盖上,避免接触喷砂磨料和油漆。
g) 固化的涂层不得存在小孔、空隙、气泡、大龟裂或其他“涂层缺陷”。
h) 难以进行适当的涂层操作/检验的表面应在最后组装之前进行涂漆。
具体地说,必须在最后组装之前,为法兰和螺栓孔涂漆。
i) 在进行新一道涂抹工序之前,所有涂层在现场周围条件下的干燥时间不得短于涂层制造商规定的最短时间,也不得长于现场周围条件下上末道漆之前的最长时间。
上一道涂层还未全干时不得上新的涂料。
除非湿碰湿涂装工序可行。
j) 无机锌涂层的受损区域应在清洁之后进行涂漆,应依照技术规范,刷上一层环氧富锌底漆。
k) 户外表面处理和涂漆应在日间进行(不适用于封闭式车间)。
l) 不上涂料的表面应适当保护起来,避免接触喷磨和涂层工序。
应小心地去除沉积在表面的油漆。
9 与混凝土接触或包裹在混凝土内的碳素钢表面在组装之前,与混凝土接触的所有碳素钢表面都应根据本技术规范进行预处理和喷漆(油漆系统n°I)。
包裹在混凝土内的碳素钢应采用以下方式上漆:•如果包裹在碳素钢内的部分小于150毫米,那么应该全部上漆;•如果包裹在碳素钢内的部分大于150毫米,那么只需要对150毫米区域上漆(从表面延伸150毫米至混凝土内)被包裹的碳素钢的表面处理和油漆系统,参见附件n°XVII工序的描述。
10 修复只要有可能,就应对涂层缺陷或损坏之处进行修复,使表面涂层符合本技术规范的要求。
不遵照本技术规范的修复工艺规程应在开展工作之前,以书面形式提交给承包商批准。
该工艺规程应考虑所有表面处理的要求,确保实现完整的底层和涂层间附着。
.11 涂层系统11.1 概要。
涂漆公司应证明其工场或分包商敷涂工场的专业人员可以像现场操作一样很好地开展油漆工作。
碳素钢螺栓应镀锌或镀镉,并采用重铬酸盐末道漆。
依照相关标准,安装之前应涂上底漆,紧固之后再上其他涂层。
11.2 油漆原料11.2.1 概要•任何系统的所有涂料产品都应由同一架涂料公司提供。
11.2.3 最后涂层的颜色色彩设计见业主要求。
如果必须刷一道中间涂层,那么必须采用比外涂层浅的色调,以便增加可检查性。
12 检验与试验应制订检验试验计划,包含但不仅限于:a) 表面处理和涂层操作的所有阶段都取决于检验活动。
b) 涂漆公司应记录下表面涂层采用的相应油漆的批号。
c) 在周围温度下进行喷砂或涂层操作之前,应测量空气露点和相对湿度,并记录在涂漆公司涂层检验报告中。
应采用干湿计测量相对湿度。
d) 采用电子测微仪或其他认可的方法测量干膜厚度。
按照NFT 30-124等级A的要求采用电子测微仪或其他认可的方法测量干膜厚度。
e) 为了开展这些试验,涂漆公司应为其检验员提供以下认可的检验设备:- 干湿计- 表面温度计- DFT电子测微仪用于测量碳素钢和有色金属(涡流)- 湿膜计量器- 轮廓量规- 露点计算器- 横切测试器如果涉及一些小的项目涉,应为额外的三张钢板(250x150x10毫米)上涂料,同时允许进行破坏性试验。
12.1 涂层厚度根据以下指示,并依照ISO 2808标准,检查涂层厚度:•碳素钢板应与管道同时进行喷砂。
钢板用于校准厚度的测量装置。
按照对管道的规定,碳素钢板的光洁度为10-15μm。
•装置应利用厚度等于或稍微高于规定的涂层厚度的塑料垫片进行校准。
校准频率为每班两次。
•每节管道的最低测量次数为20次。
必须在3点、6点、9点、12点定期进行测量。
•每次测量,厚度都不得小于规定厚度的80%。
规定厚度和80%规定厚度之间的差数不得多于20%的测量尺寸。
如果厚度测量结果低于80%的规定数值,那么应对这对之后的区域进行检查,判断缺陷程度。
确定缺陷之后,应根据本技术规范对该区域进行修复。
每道涂层的最大容许厚度参见油漆制造商的数据(敷涂工艺规程应说明涂料制造商为每道涂层或产品,以及整个系统规定的最大容许厚度)。