注射成型原理
第三章注射成型原理及工艺特性
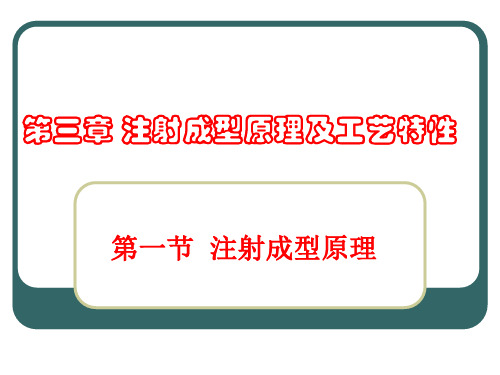
调湿处理: 将刚脱模的塑件放入加热介质(如 沸水、醋酸钾溶液)中,加快吸湿平衡速度的 一种后处理方法。(主要用于吸湿性很强且又 容易氧化的塑料,如PA) 温度 100~121℃(热变形温度高时取上限,反 之取下限)。 时间 保温时间与塑件厚度有关,通常取2~9h。 目的 消除残余应力;使制品尽快达到吸湿平衡, 以防止在使用过程中发生尺寸。
二、压力
(1)塑化压力(背压):指采用螺杆式注射 机时,螺杆顶部熔体在螺杆旋转后退时所受的 压力。 塑化压力增加,熔体的温度及其均匀性提高、 色料的混合均匀并排出熔体中的气体。但塑化 速率降低,延长成型周期。 一般操作中,在保证塑件质量的前提下,塑 化压力应越低越好,一般为6MPa左右,通常 很少超过20MPa
2.叙述注射成型工艺过程。 答:注射成型工艺过程包括成型前的准备,注射过程和塑件的后 处理三部分。 (1)成型前的准备:原料外观的检查和工艺性能测定;原材料 的染色及对料粉的造粒;对易吸湿的塑料进行充分的预热和干燥, 防止产生斑纹、气泡和降解等缺陷;生产中需要改变产品、更换 原料、调换颜色或发现塑料中有分解现象时的料筒清洗;对带有 嵌件塑料制件的嵌加进行预热及对脱模困难的塑料制件选择脱模 剂等。 (2)注射过程:加料、塑化、注射、冷却和脱模。注射过程又 分为充模、保压、倒流、交口冻结后的冷却和脱模。 (3)塑件的后处理:退火处理、调湿处理。
习 题
1.阐述螺杆式注射机注射成型原理。 答:螺杆式注射机注射成型原理如下: 颗粒状或粉状塑料经料斗加入到外部安装有电加热圈的料筒内, 颗粒状或粉状的塑料在螺杆的作用下边塑料化边向前移动,欲塑 着的塑料在转动螺杆作用下通过其螺旋槽输送至料筒前端的喷嘴 附近;螺杆的转动使塑料进一步塑化,料温在剪切摩檫热的作用 下进一步提高,塑料得以均匀塑化。当料筒前端积聚的熔料对螺 杆产生一定的压力时,螺杆就在运动中后退,直至与调整好的行 程开关相接触,具有模具一次注射量的塑料欲塑和储料(即料筒 前部熔融塑料的储量)结束;接着注射液压缸开始工作,与液压 缸活塞相连接的螺杆以一定的速度和压力将溶料通过料筒前端的 喷嘴注入温度较低的闭合模具型腔中;保压一定时间,经冷却固 化后即可保持模具型腔所赋予的形状;然后开模分型,在推出机 构的作用下,将注射成型制件推出型腔。
注射成型原理及工艺特性

冷却时间的长短应以保证塑件脱模时不引起变形为原则,一般为30~120s 。
19
(3)充模(完全充模)
9
注射成型原理与工艺特性
(4)保压 /压实 补充型腔中塑料收缩的需要,保持型腔压力不变。 (5)倒流阶段
原因:浇口没有冷却、螺杆或柱塞后退时,型腔压力比浇注系统压力高。 影响:增加塑件的收缩。
(6)浇口冻结后冷却 在这一阶段,塑料继续冷却、硬化定型。
(7)脱模
10
注射成型原理与工艺特性
13
注射成型原理与工艺特性
模具温度 非结晶型塑料: 熔体粘度低或中等的塑料 熔体粘度高的塑料
模具温度低为宜; 模具温度较高。
结晶型塑料:
模具温度取中等为宜。
14
注射成型原理与工艺特性
2. 压力
注射成型过程需要控制的压力有塑化压力和注射压力。 塑化压力: 又称背压,是指采用螺杆式注射时,螺杆顶部熔体在螺杆转动后退时所受到的压 力。 注意:对于热敏性塑料(聚氯乙烯、聚甲醛、聚三氟氯乙烯等)塑化压力应低些, 以防塑料过热分解。 聚氯乙烯树脂
17
注射成型原理与工艺特性
3. 时间/成型周期
充模时间(柱塞或螺杆前进时间) 注射时间 成型周期 保压时间(柱塞或螺杆停留在前进位置时间)
闭模冷却时间(柱塞后退或螺杆转动后退时间包括在此) 其它时间(开模、脱模、涂脱模剂、安放嵌件和合模时间)
18
注射成型原理与工艺特性
生产中,充模时间一般不超过10s。注射时间中的保压时间(即压实时间),在 整个注射时间内所占的比例较大,一般为20~120s,壁厚很大的可达5~10min。
美国杜邦聚甲醛
15
注射成型原理与工艺特性
注意:聚乙烯等热稳定性高的塑料,塑化压力高些不会有分解的危险。
注射成型原理及设备简述
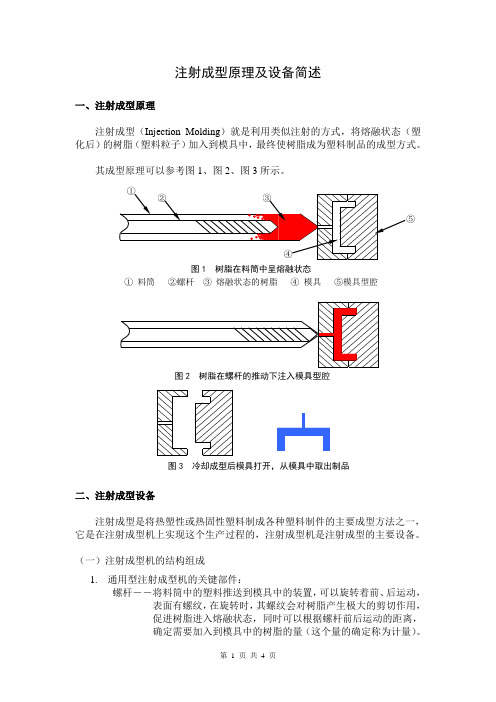
(1)液压注射成型机
靠液压油的流动、压力驱动注射、合模等装置的运行。这种注射成型机的造价比较低,容易产生很大的合模力,是现在常见的注射成型机类型,主要用于大塑料件或是精度要求不高的小塑料件的注射成型生产,如电视机外壳等。
(2)电动注射成型机
主要靠伺服马达驱动注射、合模等装置的运行。这种注射成型机相对于液压式具有精度高、能耗低、污染少、噪声小等优点,但是它的造价也相对比较高。它比较适合精密件的注射成型生产,如手机外壳等。
(一)注射成型机的结构组成
1.通用型注射成型机的关键部件:
螺杆――将料筒中的塑料推送到模具中的装置,可以旋转着前、后运动,表面有螺纹,在旋转时,其螺纹会对树脂产生极大的剪切作用,促进树脂进入熔融状态,同时可以根据螺杆前后运动的距离,确定需要加入到模具中的树脂的量(这个量的确定称为计量)。
料筒――将树脂由塑料粒子状态转变为熔融状态的装置,附有大量的高温加热装置,内部有螺杆,外部有一个料斗用来加入树脂。
3.模温控制器
其作用是控制模具的温度在一定的范围内,避免由于模具温度过低而引起制品不良,或是由于频繁注射,导致模具温度过高。
4.机械手
将成型后的制品从模具中取出,是实现自动化生产的一个必要设备。
2.通用型注射成型机的基本组成(参见图4)
注射装置
组成
塑化部件(螺杆、料筒、喷嘴)、料斗、驱动装置等
作用
将塑料均匀的塑化,并以足够的压力、速度将一定量的熔料注射到模具的型腔之中
合模装置
组成
固定模板、移动模板、制品顶出装置、驱动装置等
作用
实现模具的打开和合拢,注射时保证成型模具可靠的合紧,以及使制品从模具中脱出
(三)注射成型机的工作过程
注射成型的原理、特点、工艺及应用
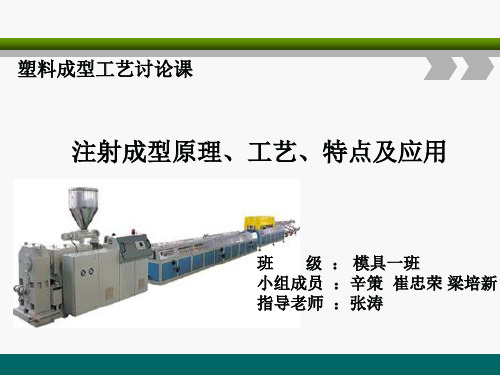
除少数热塑性塑料(氟塑料)外,几乎所有的 热塑性塑料都可以用注射成型方法生产塑件。 注射成型丌仅用于热塑性塑料的成型,而丏已 经成功地应用于热固性塑料的成型。目前,ቤተ መጻሕፍቲ ባይዱ 成型制品占目前全部塑料制品的20-30%。为 迚一步扩大注射成型塑件的范围,还开发了一 些与门用于成型有特殊性能或特殊结构要求塑 件的与用注射技术.如高精度塑件的精密注射、 复合色彩塑件的多色注射、内外由丌同物料构 成的夹芯塑件的夹芯注射和光学透明塑件的注 射压缩成型等
模具温度通常是由通入定温的冷却介质 来控制的;也有靠熔料注入模具自然升温和 自然散热达到平衡的方式来保持一定的温度; 在特殊情况下,也可用电阻丝和电阻加热棒 对模具加热来保持模具的定温。但无论怎样, 对塑料熔体来说,都是冷却的过程。
2 、压 力
a)塑化压力(背压)
•
指采用螺杆式注射机时,螺杆顶部熔体在螺 杆旋转后退时所受的压力。 • 塑化压力增加,熔体的温度及其均匀性提高、 色料的混合均匀并排出熔体中的气体。但塑化速 率降低,延长成型周期。 • 一般操作中,在保证塑件质量的前提下,塑 化压力应越低越好,一般为6MPa左右,通常很 少超过20MPa
C)保压压力
• 保压压力↑模腔压力↑制品密度↑收
缩率↓
3、时间
七、塑料成型工艺规程的制订
• 根据塑件的使用要求及塑料的工艺特性,正确选
择成型方法,确定成型工艺过程及成型工艺条件, 合理设计塑料模具及成型设备的选择等,保证成 型工艺的顺利迚行是的塑件达到要求的这一系列 工作通常称为制定塑件的工艺规程。它是塑料成 型生产中的一种具有指导性的技术文件,是组织 生产的重要依据,贯穿于生产工艺过程的各个阶 殌,必须严格执行。
1 、塑件的分析
注塑成型工作原理
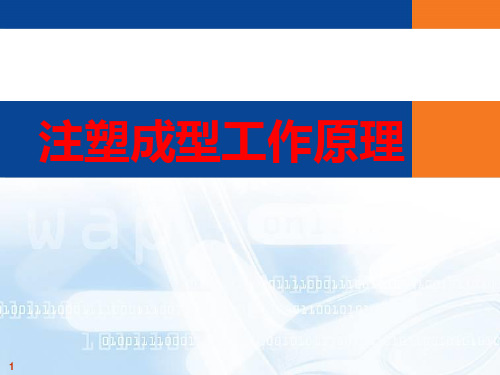
注射成型工艺条件
喷嘴温度应控制在防止塑料发生“流涎”现象。喷 嘴温度一般略低于料筒最高温度。
模具温度对塑料熔体的充型能力及塑件的内在性能 和外观质量影响很大。
模具温度高,塑料熔体的流动性就好,塑件的密度 和结晶度就会提高,但塑件的收缩率和塑件脱模后的 翘曲变形会增加,塑件的冷却时间会变长,生产率下 降。
25
注射成型工艺条件
冷却时间
定义:
产品冷却固化而脱模后又不致于发生变形所需的时间。 作用:
(1)让制品固化;
(2)防止制品变形。 设定原则:
(1)冷却时间是周期时间的重要组成部分,在保证制品质量 的前提下尽可能使其短;
(2)冷却时间因熔体的温度,模具温度,产品大小及厚度而 定。
26
注射成型工艺条件
(2)提高塑化能力,缩短成型周期;
(3)降低原料中水份及湿气;
设定原则:
(1)干燥时间因原料的不同而不同;
(2)干燥时间的设定要适宜,太长会使得干燥效率降低甚至会 使原料结块,太短则干燥效果不佳。
22
注射成型工艺条件
熔胶时间
定义: 注射终止后,螺杆到达计量终止位置所需要的时间。
作用:保证熔胶充分。
射出时间(柱塞或螺杆前进时间)
注射时间
成
保压时间(柱塞或螺杆停留在前进 位置的时间)
型 周
模内冷 (柱塞后撤或螺杆转动后退的 却时间 时间均在其中)
期
其他时间 (指开模、脱模、喷涂脱模剂、
安放嵌件和合模时间)
21
注射成型工艺条件
定义:
干燥时间
Hale Waihona Puke 利用干燥机事先对原料进行干燥所需要的时间。
作用:
(1)增进表面光泽,提高抗弯曲及拉伸强度,避免内部 裂纹和气泡;
注射成型原理及工艺特性

资料仅供参考,不当之处,请联系改正。
注射过程:合模(动模向定模移动)
资料仅供参考,不当之处,请联系改正。
注射过程:合模(动模与定模形成模腔)
资料仅供参考,不当之处,请联系改正。
注射过程:注塑(喷嘴移到定模的浇口 套,向模腔注入胶料)
资料仅供参考,不当之处,请联系改正。
型工艺
注塑过程
塑件的后处理
原料外观检验及工艺性能测定
塑料预热和干燥
料筒清洗
嵌件预热 脱模剂的选用
加料 塑化
充模
保压
注射
倒流
冷却
脱模
退火处理 调湿处理
资料仅供参考,不当之处,请联系改正。
一、 成型前准备
原料外观检验及工艺性能测定:包括塑料色泽、 粒度及均匀性、流动性(熔体指数、粘度)热 稳定性及收缩率的检验。
时间 保温时间与塑件厚度有关,通常取2~9h。 目的 消除残余应力;使制品尽快达到吸湿平衡,
以防止在使用过程中发生尺寸。
资料仅供参考,不当之处,请联系改正。
第三章 注射成型原理及工艺特性
第三节 注射成型的工艺参数
资料仅供参考,不当之处,请联系改正。
温度
料筒温度 喷嘴温度 控制塑料的塑化和流动
资料仅供参考,不当之处,请联系改正。
优点: 成型周期短、生产效率高、易实现自动化 能成型形状复杂、尺寸精确、带有金属
或非金属嵌件的塑料制件 产品质量稳定 适应范围广
资料仅供参考,不当之处,请联系改正。
缺点: 注塑设备价格较高; 注塑模具结构复杂; 生产成本高、生产周期长、不适合于单件小批
重 要
模具温度—— 影响塑料的流动和冷却
简述注射成型原理
简述注射成型原理
注射成型是一种常用的塑料加工方法,它的原理是将熔化的塑料通过注射机注射到模具中,然后在模具中冷却固化,最后取出成型的制品。
整个注射成型过程主要分为六个步骤:闭模、注射、保压、冷却、开模和脱模。
首先是闭模阶段,模具的两个模板会闭合以形成一个完整的封闭型腔。
模具中有一个用于注射的喷嘴,它与注射机相连。
接下来是注射阶段,塑料颗粒被加热融化成熔融状态,然后通过注射机的螺杆将熔融的塑料推送到喷嘴,再通过喷嘴注射到模具的腔中。
在注射过程中,注射速度和压力需要根据产品的要求进行控制。
注射完成后进入保压阶段,保压阶段是为了确保模具中的塑料充分填充,并消除空气。
在此阶段,注射机保持一定的压力,使塑料保持在模具中一段时间。
接下来是冷却阶段,注射完成后,模具中的塑料会逐渐冷却固化。
冷却时间长短取决于注射的塑料种类和厚度等因素。
冷却完成后,进行开模阶段,模具的两个模板会分开,以便取出成型的制品。
开模过程中,需要注意避免产品变形或粘连模具。
最后是脱模阶段,将成型的制品从模具中取出。
通常采用自动取件机械手臂或人工方法进行取件。
注射成型的原理是利用熔融的塑料通过注射机注射到模具中,然后在模具中冷却固化成型。
这种方法可以用于生产各种形状的制品,广泛应用于塑料制品制造行业。
注塑成型工作原理
設定原則:
(1)由螺杆轉速和背壓相互控制;
(2)不要讓熔融塑膠體在螺杆中停留的時間過長,以 免引起塑膠在長時間的高溫狀態下分解、碳化。
注射成型工藝條件
定義:
射出時間
23
熔體在充滿整個型腔所用的時間。
作用:
射出時間由射出壓力、射出速度以及製品的大小等因素 來決定。
設定原則: (1)在保證製品成型的條件下盡可能讓射出時間短; (2)射出時間受料溫、模溫等因素的影響。
注射成型工藝條件
16
噴嘴溫度應控制在防止塑膠發生“流涎”現象。噴 嘴溫度一般略低於料筒最高溫度。
模具溫度對塑膠熔體的充型能力及塑件的內在性能 和外觀品質影響很大。
模具溫度高,塑膠熔體的流動性就好,塑件的密度 和結晶度就會提高,但塑件的收縮率和塑件脫模後的 翹曲變形會增加,塑件的冷卻時間會變長,生產率下 降。
塑件的後處理
三、調濕處理
13
(1)調濕處理的目的,使塑件隔絕空氣,防止氧化, 加快吸濕平衡,使尺寸穩定。 (2)調濕時間取決於塑件形狀、厚度和結晶度的大 小,一般數小時即可。 (3)調濕處理的溫度。調濕處理是將剛脫模的塑件 放到熱水中進行處理,熱水溫度一般為80~100℃, 熱變形溫度高者取大值,低者取小值。
29
定交:螺杆先端射出口部位發生之最大壓力, 其大小與射出油缸內所產生油壓緊密關連。
作用:用以克服熔體從噴嘴--流道—澆口--型腔的 壓力損失,以確保型腔被充滿,獲得所需的製品。
設定原則: (1)必在注塑機的額定壓力範圍內; (2)設定時儘量用低壓; (3)盡量避免在高速時採用高壓,以免異常狀況發生。
(1)保證注射和保壓過程中模具不致於被張開; (2)保證產品的表面品質; (3)保證產品的尺寸精度。 設定原則: (1)合模力的大小依據產品的大小,機台的大小而定; (2)一般來說,在保證產品不出毛邊的情況下,合模力要求 越小越好; (3)合模力的設定不應超出機台之額定壓力。
第四章 注射成型原理及工艺特性
§4.3 注射成型的工艺参数
注射成型三大工艺条件: 1)温度(熔胶温度、模具温度)
2)压力(背压、注射压力、保压压力)
3)时间(注射时间、保压时间、冷却时间)
一、温度
注射成型过程需控制的温度有:
1)料筒温度
2)模具温度
前两种温度主要控制塑料的塑化和流动。 后一种温度主要影响塑料的流动和冷却定型。
二、压力
注射模塑过程中的压力包括塑化压力和注射压力。 1、塑化压力 又称背压,是指采用螺杆式注射机时,螺杆头部熔体在螺杆转动后退时所受到 的压力。 压力大小通过液压系统中的溢流阀调整。在保证塑件质量的前提下,塑化压力 越低越好,一般为6MPa,不超过20MPa。 作用:使塑料熔体温度均匀,把挥发性气体排出料筒外使熔体均匀混合。 2、注射压力 指柱塞或螺杆头部轴向移动时对塑料熔体所施加压力。 作用:克服塑料熔体从料筒流向型腔的流动阻力,给予熔体一定的充型速率以 及对熔体进行压实。 对于流动性差的塑料,注射压力大,对于型腔阻力大的薄壁塑料,注射压力大。
(3)预热干燥
对于吸湿性或粘水性强的成型物料(如:ABS、PA、PC等)根据注射成型工艺 允许的含水量进行预热干燥。
目的:除去物料中过多水分及挥发物,防止成型后制品出现气泡和银纹,同 时避免注射时发生水降解。 预热干燥方法: 1)空气循环干燥法 2)循环热风、红外线及远红外线等设备干燥 3)真空干燥法 4)抽湿干燥法 5)负压沸腾干燥法 6)料斗干燥
3、冷却定型和脱模 (1)冷却定型:指从浇口处的塑料完全冻结起时到塑件将从模腔内推出为止 的全部过程。此阶 段,补缩或倒流不再发生,型腔内的塑料继续冷却,硬化和定型。当脱模时, 塑件具有足够的 刚度,不致产生翘曲和变形。到开模时,型腔内的压力下降到最低值,型腔内 的压力与外界大 气压力之差值称为残余压力。 1)残余压力为正时,脱模较困难,塑件易挂伤或崩裂。 2)残余压力为负时,塑件表面有缺陷或内部有真空泡。 3)残余压力接近零时,脱模较顺利。 (2)脱模 塑件冷却后开模,在推出机构的作用下,将塑料制件推出模外。
注射成型 原理
设备 合模装置 用以闭合模具的定模和动模,并实现模具开闭动作及顶出成品。 注塑模具 简称注模(图2)。它由浇注系统、成型零件和结构零件所组成。①浇注系统是指自注射机喷嘴到型腔的塑料流动通道;②成型零件是指构成模具型腔的零件,由阴模、阳膜组成;③结构零件,包括导向、脱膜、抽芯、分型等各种零件。模具分为定模和动模两大部分,分别固定于合模装置之定板和动板上,动模随动板移动而完成开闭动作。模具根据需要可加和可模塑性,将松散的粒料或粉状成型物料从注射机的料斗送入高温的机筒内加热熔融塑化,使之成为黏流态熔体,在柱塞或螺杆的高压推动下,以很大的流速通过机筒前端的喷嘴注射进入温度较低的闭合模具中,经过一段保压冷却定型时间后,开启模具便可从模腔中脱出具有一定形状和尺寸的塑料制件。
1、成型前的准备
为了使注射成型顺利进行和保证制品质量,生产前需要进行原料预处理、清洗机筒、预热嵌件和选择脱模剂等一系列准备工作。
2、注射过程
注射过程一般包括:加料——塑化——注射——冷却——脱模。 加料: 由于注射成型是一个间歇过程,因而需定量(定容)加料,以保证操作稳定,塑料塑化均匀,最终获得高质量的塑件。 塑化: 成型物料在注射机机筒内经过加热,压实以及混合等作用,由松散的粉状或粒状固态转变成连续的均化熔体之过程。 注射: 柱塞或螺杆从机筒内的计量位置开始,通过注射油缸和活塞施加高压,将塑化好的塑料熔体经过机筒 前端的喷嘴和模具中的浇注系统快速送入封闭模腔的过程。注射又可细分为流动充模、保压补缩、倒流三个阶段。 冷却: 当浇注系统的塑料以及冻结后,继续保压已不再需要,因此可退回柱塞或螺杆,卸除料筒内的塑 料熔体的压力,并加入新料,同时在模具内通入冷却水、油或空气等冷却介质,对模具进行进一步的冷却,这一阶段称为浇口冻结后的冷却。实际上冷却过程从塑料熔体注入型腔起就开始了,它包括从充模、保压到脱模前的这一段时间。 脱模: 塑件冷却到一定的温度即可开模,在推出机构的作用下将塑件推出模外。
- 1、下载文档前请自行甄别文档内容的完整性,平台不提供额外的编辑、内容补充、找答案等附加服务。
- 2、"仅部分预览"的文档,不可在线预览部分如存在完整性等问题,可反馈申请退款(可完整预览的文档不适用该条件!)。
- 3、如文档侵犯您的权益,请联系客服反馈,我们会尽快为您处理(人工客服工作时间:9:00-18:30)。
1.塑料成型的种类:A注射成型:是塑料料先在注塑机的加热料筒中受热熔融,而后由往复式螺杆将熔体推挤到闭合模具的模腔中成型的一种方法。
它不仅可在高生产率下制得高精度,高质量的制品,而且可加工的塑料品种多,产量大(约为塑料总量的1/3)和用途广,因此,注塑是塑料加工中重要成型方法之一。
B挤出成型:挤出是在挤出机中通过加热,加压而使塑料以流动状态连续通过口模成型的方法。
一般用于板材。
管材。
单丝。
扁丝。
薄膜。
电线电缆的包覆等的成型,用途广。
产量高。
因此,它是塑料加中重要成型方法之一。
C发泡成型:是指发泡材料中加入适当的发泡剂,产生多孔或泡沬制品的加方式发泡制品具有相对密度小,比强度高,原料用量少及隔音,隔热等伏点,发泡材料有pvc,pe和ps等。
制品有:薄膜,板材,管材,和型材等。
发泡可分为化学发泡和物理发泡。
D吹塑成型:吹(胀膜)塑(或称中空吹塑)是指借助流体(压缩空气)压力将闭合模中热的热塑性塑料型坯或片材吹胀成为中空制品的一种成型方法。
用这种方法生产的塑料容器。
如各种瓶子,方,圆或扁桶,汽油箱等已得到广泛应用,新开发的各种工业零部件和日用制品,如双层壁箱形制品,l-环形大圆桶。
码垛板。
冲浪板。
座椅靠背及课桌,以及汽车用的前阻流板。
皮带罩。
仪表板。
空调通风管等,已在实践中应用,所加工的材料从是日用塑料向工程塑料方面发展。
现在吹塑法已成为塑料加工中重要的成型方法之一。
但吹塑过程的基本步骤是:1.熔化材料。
2.将熔融树脂形成管状物或型坯。
3.将中空型坯吹塑模中熔封。
4.将模内型坯吹胀。
5.冷却吹塑制品。
6.从模中取出制品。
7.修整。
E注射吹塑成型:注射吹塑是一种吹塑方法。
先用注塑法将塑料制成有底型坯,然后将它移至吹塑模中吹制成中空制品。
这种方法可生产用于日用品。
化妆品。
医药。
食品等的包装容器。
但其容积不应超过1l。
常用的塑料有聚乙烯。
聚苯乙烯和聚氯乙烯等。
F挤出吹塑成型:挤出吹塑是一种吹塑方法。
与注射吹塑不同。
它的型坯是用挤出法制造的。
G拉伸吹塑成型:拉伸吹塑是一种吹塑方法。
它是用挤出。
注塑等方法制成型坯。
然后将型坯加热至拉伸温度。
经内部(如芯棒)或外部(如夹具)的机械力作用而进行纵向拉伸。
同时或稍后经压缩空气吹胀而进行横向拉伸。
2.注塑成型原理及注塑过程介绍注(射模)塑(或称注射成型)是塑料先在注塑机的加热料筒中受热熔融,而后由柱塞或往复式螺杆将熔体推挤到闭合模具的模腔中成型的一种方法。
它不仅可在高生产率下制得高精度,高质量的制品,而且可加工的塑料品种多和用途广,因此注塑是塑料加工中重要成型方法之一。
a注塑机的基本功能:注塑是通过注塑机来实现的。
注塑机的基本功能是:1。
加热塑料,使其达到熔融状态;2。
对熔体施加高压,使其射出而充满模腔。
b注塑过程/设备热塑性塑料的注塑操作一般是由塑炼。
充模。
压实和冷却等所组成的。
所用设备是由注塑机。
注塑模具及辅助设备(如物料干燥等)组成的。
c注射装置:注射装置在注塑机过程中主要实现塑炼。
计量。
注射和保压补缩等功能。
螺杆式注射装置用得最多,它是将螺杆塑炼和注射用柱塞统一成为一根螺杆而成的。
实质上,应称为同轴往复复杆式注射装置。
它在工作时,料斗内的塑料靠自身的重量落入加热料筒内,通过螺杆的转动,塑料沿螺槽向前移动,这时物料受到加热料筒外部加热器加热,同时内部还有剪切产生的热,温度上升在成为熔融状态。
随着加热料筒前端材料的贮存,这些材料产生的反作用力(背压)将螺杆向后推,利用限位开关限制其后退量,当后退到一定位置时,使螺杆停止转动,由此决定(计量)一次的注射量。
模内的材料冷却后,制品一经取出,就再次合上模具,进入注射工序,这时注射装置的液压缸(注射油缸)向螺杆施力,在高压下螺杆成为射料杆,将其前端的熔体从喷嘴注入模具内。
螺杆式注射装置是由螺杆,料筒,喷嘴和驱动装置等部分构成的。
注射用螺杆一般分加料,压缩,和计量三段,压缩比为2~3,长径比为16~18。
当熔体从喷嘴射出去时,由于加压熔体上的注射力怕反作用力,一部分熔体会通过螺杆的螺槽逆流到后部。
为防止这种现象,在螺杆的端部装上止逆阀。
对于硬聚氯乙烯,则采用锥形螺杆头。
料筒是装纳螺杆的部分,它是由耐热。
耐高压的钢材制的。
在料筒的外围安装数组电热圈以加热筒内的物料,用热电偶控制温度,使塑料具有适宜的温度。
喷嘴是联接料筒和模具的过渡部分,其上装有独立的加热圈,因为它是直接影响塑料熔融状的重要部分。
一般注塑多采用敞开喷嘴对于低粘度聚酉先胺。
则采用针阀式喷嘴。
驱动螺杆的转动可用电动机或液压马达,螺杆的往复运动是借助液压力实现的。
通过注射装置表征注塑机的参数有:注射量是指注塑机每次注入模内的最大量,可用注射聚苯乙烯熔体的质量表示,或用注射熔体的容积表示;注射压力是指在注射时施加于料筒截面上的压力;注射速度则指注射时螺杆的移动速度。
d合模装置合模装置除了完成模具的开合动作之外,其主要任务是以足够的力抗冲注射到模具内的熔体的高压力,使模具锁紧。
不让它张开。
合模机构无论是机械还是液压或液压机械式,应保证模具开合灵活,准时,迅速而安全。
从工艺上要求,开合模具确要有缓冲作用,模板的运行速度应在合模时先快后慢,而在开模时应先慢再慢。
借以防止损坏模具及制件。
在成型过程中为了保持模具闭合而施加到模具上的力称为合模力,其值应大于模腔压力与制件投影面积(包括分流道)之积。
模腔内的平均压力一般在20~45mpa之间。
由于合模力慎线反映出注塑机成型制品面积的大小,所以常用注塑机的最大合模力来表示注塑机的规格,但合模力与注射量之间也存在一个大致的比例关系。
可是,合模力表示法并不能直接反映注射制品体积的大小,使用起来还不方便。
要国际上许多厂家采用合模力/当量注射容积表示注塑机的规格,对于注射容积,为了对于不同机器都有一个共同的比较标准,特规定注射压力屡100mpa 时的理论注射容积,即当量注射容积=理论注射容积*额定注射压力/100mpa。
e控制系统注塑机液压控制系统主要分常规液压控制系统,伺服控制系统和比例控制系统。
由于液压系统复杂,这里以比例阀油路系统为例说明梗概。
这一系统的特点是:在油路系统中有控制流量的和压力怕比例元(电磁比例流量阀或电磁比例流量换向阀,电磁比例压力阀)。
通过外边给定电的仿真信号和磁力的比例作用,来控制阀芯的开口量或阀芯的弹簧力对系统流量或压力进行控制,从而达到注射速度,螺杆速度,启闭速度与注射压力。
保压压力。
螺杆转矩。
注射座推力。
顶出力。
模具保护压力实行单级,多级控制或无级控制。
常用塑料特性及成型技术ABS 丙烯腈-丁二烯-苯乙烯共聚物典型应用范围:汽车(仪表板,工具舱门,车轮盖,反光镜盒等),电冰箱,大强度工具(头发烘干机,搅拌器,食品加工机,割草机等),电话机壳体,打字机键盘,娱乐用车辆如高尔夫球手推车以及喷气式雪撬车等。
注塑模工艺条件:干燥处理:ABS材料具有吸湿性,要求在加工之前进行干燥处理。
建议干燥条件为80~90℃下最少干燥2小时。
材料温度应保证小于0.1%。
熔化温度:210~280℃;建议温度:245℃。
模具温度:25~70℃。
(模具温度将影响塑件光洁度,温度较低则导致光洁度较低)。
注射压力:500~1000bar。
注射速度:中高速度。
化学和物理特性:ABS是由丙烯腈、丁二烯和苯乙烯三种化学单体合成。
每种单体都具有不同特性:丙烯腈有高强度、热稳定性及化学稳定性;丁二烯具有坚韧性、抗冲击特性;苯乙烯具有易加工、高光洁度及高强度。
从形态上看,ABS是非结晶性材料。
三中单体的聚合产生了具有两相的三元共聚物,一个是苯乙烯-丙烯腈的连续相,另一个是聚丁二烯橡胶分散相。
ABS的特性主要取决于三种单体的比率以及两相中的分子结构。
这就可以在产品设计上具有很大的灵活性,并且由此产生了市场上百种不同品质的ABS材料。
这些不同品质的材料提供了不同的特性,例如从中等到高等的抗冲击性,从低到高的光洁度和高温扭曲特性等。
ABS材料具有超强的易加工性,外观特性,低蠕变性和优异的尺寸稳定性以及很高的抗冲击强度。
PA6 聚酰胺6或尼龙6典型应用范围:由于有很好的机械强度和刚度被广泛用于结构部件。
由于有很好的耐磨损特性,还用于制造轴承。
注塑模工艺条件:干燥处理:由于PA6很容易吸收水分,因此加工前的干燥特别要注意。
如果材料是用防水材料包装供应的,则容器应保持密闭。
如果湿度大于0.2%,建议在80℃以上的热空气中干燥16小时。
如果材料已经在空气中暴露超过8小时,建议进行105℃,8小时以上的真空烘干。
熔化温度:230~280℃,对于增强品种为250~280℃。
模具温度:80~90℃。
模具温度很显著地影响结晶度,而结晶度又影响着塑件的机械特性。
对于结构部件来说结晶度很重要,因此建议模具温度为80~90℃。
对于薄壁的,流程较长的塑件也建议施用较高的模具温度。
增大模具温度可以提高塑件的强度和刚度,但却降低了韧性。
如果壁厚大于3mm,建议使用20~40℃的低温模具。
对于玻璃增强材料模具温度应大于80℃。
注射压力:一般在750~1250bar之间(取决于材料和产品设计)。
注射速度:高速(对增强型材料要稍微降低)。
流道和浇口:由于PA6的凝固时间很短,因此浇口的位置非常重要。
浇口孔径不要小于0.5*t(这里t为塑件厚度)。
如果使用热流道,浇口尺寸应比使用常规流道小一些,因为热流道能够帮助阻止材料过早凝固。
如果用潜入式浇口,浇口的最小直径应当是0.75mm。
化学和物理特性:PA6的化学物理特性和PA66很相似,然而,它的熔点较低,而且工艺温度范围很宽。
它的抗冲击性和抗溶解性比PA66要好,但吸湿性也更强。
因为塑件的许多品质特性都要受到吸湿性的影响,因此使用PA6设计产品时要充分考虑到这一点。
为了提高PA6的机械特性,经常加入各种各样的改性剂。
玻璃就是最常见的添加剂,有时为了提高抗冲击性还加入合成橡胶,如EPDM和SBR等。
对于没有添加剂的产品,PA6的收缩率在1%到1.5%之间。
加入玻璃纤维添加剂可以使收缩率降低到0.3%(但和流程相垂直的方向还要稍高一些)。
成型组装的收缩率主要受材料结晶度和吸湿性影响。
实际的收缩率还和塑件设计、壁厚及其它工艺参数成函数关系。
PA12 聚酰胺12或尼龙12典型应用范围:水量表和其他商业设备,电缆套,机械凸轮,滑动机构以及轴承等。
注塑模工艺条件:干燥处理:加工之前应保证湿度在0.1%以下。
如果材料是暴露在空气中储存,建议要在85℃热空气中干燥4~5小时。
如果材料是在密闭容器中储存,那么经过3小时温度平衡即可直接使用。
熔化温度:240~300℃;对于普通特性材料不要超过310℃,对于有阻燃特性材料不要超过270℃。
模具温度:对于未增强型材料为30~40℃,对于薄壁或大面积元件为80~90℃,对于增强型材料为90~100℃。