注塑条件对塑件成型的影响
注塑成型各种缺陷的现象及解决方法

注塑成型各种缺陷的现象及解决方法.txt我爸说过的最让我感动的一句话:“孩子,好好学习吧,爸以前玩麻将都玩儿10块的,现在为了供你念书,改玩儿1块的了。
”注塑成型各种缺陷的现象及解决方法[塑料]一)熔接痕熔接痕是由于来自不同方向的熔融树脂前端部分被冷却、在结合处未能完全融合而产生的。
一般情况下,主要影响外观,对涂装、电镀产生影响。
严重时,对制品强度产生影响(特别是在纤维增强树脂时,尤为严重)。
可参考以下几项予以改善:l)调整成型条件,提高流动性。
如,提高树脂温度、提高模具温度、提高注射压力及速度等。
2)增设排气槽,在熔接痕的产生处设置推出杆也有利于排气。
3)尽量减少脱模剂的使用。
4)设置工艺溢料并作为熔接痕的产生处,成型后再予以切断去除。
5)若仅影响外观,则可改变烧四位置,以改变熔接痕的位置。
或者将熔接痕产生的部位处理为暗光泽面等,予以修饰。
二)放射纹放射纹(Jetting)1、表观从浇口喷射出,有灰黯色的一股熔流在稍微接触模壁后马上被随后注入的熔料包住。
此缺陷可能部分或完全隐藏在制品内部。
物理原因放射纹往往发生在当熔料进入到模腔内,流体前端停止发展的方向。
它经常发生在大模腔的模具内,熔流没有直接接触到模壁或没有遇到障碍。
通过浇口后,有些热的熔料接触到相对较冷的模腔表面后冷却,在充模过程中不能同随后的熔料紧密结合在一起。
除去明显的表面缺陷,放射纹伴随不均匀性,熔料产生冻结拉伸,残余应力和冷应变而产生,这些因素都影响产品质量。
在多数情况下不太可能只通过调节成型参数改进,只有改进浇口位置和几何形状尺寸才可以避免。
与加工参数有关的原因与改良措施见下表:1、注射速度太快降低注射速度2、注射速度单级采用多级注射速度:慢-快3、熔料温度太低提高料筒温度(对热敏性材料只在计量区)。
增加低螺杆背压与设计有关的原因与改良措施见下表:1、浇口和模壁之间过渡不好提供圆弧过渡2、浇口太小增加浇口3、浇口位于截面厚度的中心浇口复位位,采用障碍注射、工艺溢料是指用手工在模具上开一条深一些的排气槽,在生产时此槽产生出来的(批峰),又叫工艺批峰,主要是用来改善烧胶或熔接痕,可将烧胶或熔接痕调整到此批峰上,生产后将其切除。
探究注塑机塑化能力影响因素

探究注塑机塑化能力影响因素摘要:在塑料制品的加工过程中,注射成型是常用的加工方法之一,使用此类注塑机械加工出的塑件具有多方面的优点,包括易成型、尺寸精细且无需后续处理等,因此应用比较广泛,同时,其塑化能力对所得塑件的质量有着重要影响,本文分析了影响塑化机塑化能力的主要因素,并对其关系进行了进一步的分析。
关键词:注塑机;塑化能力;影响因素1引言注塑机是用于加工聚合物的常用设备,所得塑件的质量与注塑机的塑化能力以及塑化质量等机械本身的性能直接相关。
如果塑化机本身存在塑化效率低、塑化质量差等问题,则在操作过程中,材料可能会产生局部过热的情况,从而存在缺陷或者直接降解报废,而塑化质量又由螺杆结构、操作工艺参数以及聚合物种类等因素决定。
2试验部分2.1主要原料和设备试验需要的原材料与设备及其相关信息分别如表1、表2所示。
表1 原材料及相关信息2.2试验步骤(1)设定好机筒的加热温度并执行加热的操作,最高不能超过230℃,加热完毕后需保温20min;(2)完成储料与注射操作,待储料时间基本稳定以后再继续后续测试;(3)喷嘴孔径与速率分别取注塑机的标准孔径以及20%的标准速率,注射2.5倍的螺杆直径(D)的行程和全行程的注射量,记录相关参数数据,包括储料时间、熔融固化后的塑料质量等;(4)在机器达到稳定的状态后,分别取六次数据,然后将其取平均值,该值即为塑化能力值,最后再根据注射行程与塑料质量具体数值计算得到密度值。
以上测试过程需要使用指定仪器记录下全程,以便以后根据视频中的螺杆位移计算相对密度与时间,然后进一步得到瞬时塑化能力,最后会使用指定的软件系统根据相应的数据绘制出模拟曲线与图表。
3结果与讨论3.1螺杆结构对塑化能力的影响注塑机的螺杆具有多种结构,且其内部参数也存在一定的差异,本测试主要是针对不同种类螺杆,然后在特定条件下,测试其塑化能力,如图1所示为不同类型的螺杆,D的数值都是140mm,长径比都是24。
论注塑成型工艺的相关因素

243 索退位 置 __
当螺杆 回料完停止滚动后 ,螺杆有一个 向后松退 的动作 , 称之为索退 ,也可称为抽胶 ,一般索退 间隔为 2—5m m,如果
口凝 固后则无影 响;保压过大会造成塑料件残余应力过大 。确 定保压压力的方法是先用较短 观 、尺寸 、重量 ,然后逐次延长保压 时间,直 至发现塑料件重量不再随保压时间的延长而增加为止 ,然后 以
2O 30 3 ~ 2 20 2O 0~ 5 2O 20 0 ~ 5
2O 3O O~ 2
2O 30 0~ 2 10 2O 5 ~ 1 1O 2 0 8 ~ 5
将导致制 品由于补缩不足而出现 凹陷及内部质量下 降,使制 品
收缩率加大 。但是过长的保 压时 间不仅会 延长 成型周期 、增加 能耗 ,而且会 引起浇 口处的应力集 中,造成制品断裂 。
烘料温度
( ℃)
4  ̄ 7 0 0 6 ~ 9 5 O 3 ~ 7 5 0
4 ~ 7 5 0
烘料 时间
() h
05 2 .~ 1 3 ~ O5 2 .~
05 2 ~
喷嘴温度
( ℃)
2O 2O 0 ~ 5 20 20 1~ 8 20 20 0 ~ 5
塞 ,或者 由于早凝料注人模腔而影 响零件的外观和性能 。
234 成 型周期 . .
完成一次注射模塑过程所需 的时间称为成型周期。成 型周 期包含 了前面所讲 的几段时间 ,即注射时 间、保压时间 、冷却
时 间。成型周期 直接影响劳动生产率 和设备利用率 ,因此在生
21 模 具 温度 .. 3
料粒子生产厂家 、等级 的不同 ,会存在很大的区别 ,料筒 的注 塑温度应保证在该胶料 的熔化温度与热分解温度之间。原料干
pbt注塑成型工艺条件
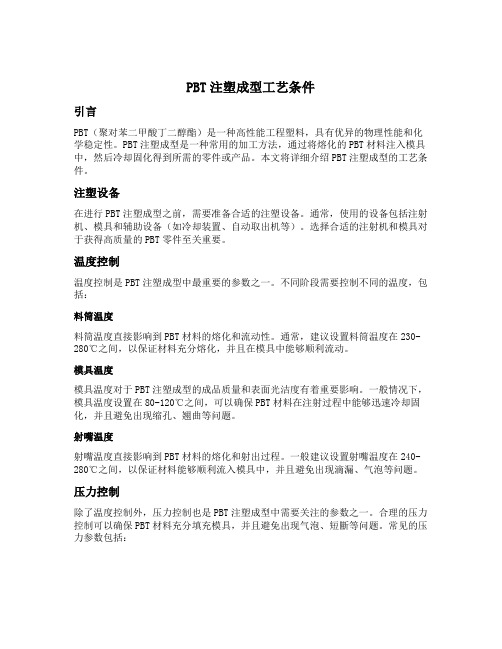
PBT注塑成型工艺条件引言PBT(聚对苯二甲酸丁二醇酯)是一种高性能工程塑料,具有优异的物理性能和化学稳定性。
PBT注塑成型是一种常用的加工方法,通过将熔化的PBT材料注入模具中,然后冷却固化得到所需的零件或产品。
本文将详细介绍PBT注塑成型的工艺条件。
注塑设备在进行PBT注塑成型之前,需要准备合适的注塑设备。
通常,使用的设备包括注射机、模具和辅助设备(如冷却装置、自动取出机等)。
选择合适的注射机和模具对于获得高质量的PBT零件至关重要。
温度控制温度控制是PBT注塑成型中最重要的参数之一。
不同阶段需要控制不同的温度,包括:料筒温度料筒温度直接影响到PBT材料的熔化和流动性。
通常,建议设置料筒温度在230-280℃之间,以保证材料充分熔化,并且在模具中能够顺利流动。
模具温度模具温度对于PBT注塑成型的成品质量和表面光洁度有着重要影响。
一般情况下,模具温度设置在80-120℃之间,可以确保PBT材料在注射过程中能够迅速冷却固化,并且避免出现缩孔、翘曲等问题。
射嘴温度射嘴温度直接影响到PBT材料的熔化和射出过程。
一般建议设置射嘴温度在240-280℃之间,以保证材料能够顺利流入模具中,并且避免出现滴漏、气泡等问题。
压力控制除了温度控制外,压力控制也是PBT注塑成型中需要关注的参数之一。
合理的压力控制可以确保PBT材料充分填充模具,并且避免出现气泡、短斷等问题。
常见的压力参数包括:注射压力注射压力直接影响到PBT材料的填充速度和填充效果。
通常建议设置注射压力在1000-2000bar之间,以保证材料能够充分填满模具。
保压压力保压压力用于确保PBT材料在冷却固化过程中不会出现缩孔、翘曲等问题。
一般建议设置保压压力在500-1000bar之间,以保证成品的质量和尺寸稳定性。
注塑速度注塑速度是指PBT材料从注射机进入模具的速度。
合理的注塑速度可以确保PBT材料充分填充模具,并且避免出现熔断、气泡等问题。
常见的注塑速度参数包括:射胶速度射胶速度是指PBT材料从注射机进入模具的速度。
常见的塑件问题分析及处理方法
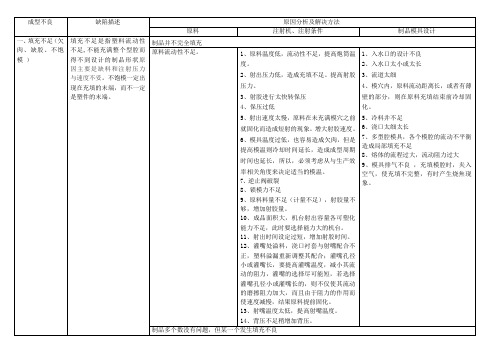
7、GATE以及流道小或变形,充填速度快,瞬间产生磨擦使温度急升造成原料分解。
六、流痕
在制品入水口为中心形成波幅,原料在模穴内流动时,在成品表面上出现以GATE为中心的年轮状细小的邹纹现象。
1、原料动性不够
2、塑料不洁或渗有其它料检查塑料
1、原料温度低,流动性不够,增加原料温度
13、射嘴温度太低,提高射嘴温度。
14、背压不足稍增加背压。
1、入水口的设计不良
2、入水口太小或太长
3、流道太细
4、模穴内,原料流动距离长,或者有薄壁的部分,则在原料充填结束前冷却固化。
5、冷料井不足
6、浇口太细太长
7、多型腔模具,各个模腔的流动不平衡造成局部填充不足
8、熔体的流程过大,流动阻力过大
2、原料润滑性不足够
1、料温太高
2、原料在料筒内滞留时间太长
3、注塑机料筒受损使原料积聚
1、入水口太细太长
四、云雾
制品表面的光洁度不良
1、塑料的稳定性不足够
1、料温太高
2、模温过低
3、原料在料筒滞留得太长
4、脱模剂使用不当
1、模具抛光太差
五、起疮:(银色条纹)
这是出现在制件表面熔料流动方向上的银白色纹理,这种现象的原因虽然很多,但主要是原料干燥不彻底,由水分或挥发成分造成的,因此,一般应在比树脂热变形温度低10~15度的条件下烘干。对要求较高的PMMA树腊系列,需要在75-85度左右的条件下烘干3~6h。特别是在使用自动烘干料斗时,需要根据成型周期(成型量)及干燥时间选用合理的容量,还应在注射开始前数小时先行开机烘料。
5、在熔接线出现的地方加冷料井
6、模具温度低,应适当提高模具温度或有目的地提高熔接缝处的局部温度,使原料在模具内的流动性增加,则原料会合时温度较高,使其会胶线减小。
注塑件常见缺陷及原因

注塑件常见缺陷及原因注塑件常见缺陷包括飞边、欠注、翘曲、黑点、气泡、起皮、焦痕、龟裂、色差、脆化、喷流纹等。
这些缺陷的形成原因有很多,具体如下:1.飞边:模具分型面或成型区域的设计尺寸不当,注塑压力过高,注射时间过早,注射位置离口模过远,注射位置离型腔面过远或浇口过大。
2.欠注:注塑机压力过低,注射时间过短,模具温度过低,熔体温度过高,模具浇注系统有堵塞现象。
3.翘曲:模具设计不当,冷却时间过短或过长,注塑温度或模具温度过高或过低,塑料材料的收缩率过大。
4.黑点:塑料材料中含有杂质,螺杆转速过高,螺杆温度过高,塑料受热时间过长。
5.气泡:塑料材料中含有水分或挥发物,料温过高或过低,注射压力过小,流道和浇口的尺寸过大。
6.起皮:塑料材料中水分和挥发物含量高,料温过高或过低,注射压力过小,模具温度过高或过低。
7.焦痕:塑料材料中水分和挥发物含量高,料温过高或过低,注射压力过大或过小,模具排气不良。
8.龟裂:塑料材料中水分和挥发物含量高,料温过低,注射压力过小,模具温度过低。
9.色差:塑料材料中水分和挥发物含量高,料温过高或过低,注射压力过小或过大,模具温度过高或过低。
10.脆化:塑料材料中水分和挥发物含量高,料温过高或过低,注射压力过小或过大。
11.喷流纹:塑料材料中水分和挥发物含量高,料温过高或过低,注射压力过小或过大。
此外,注塑件缺陷的形成原因还可能包括设备原因、模具设计问题、原料问题等。
解决注塑件缺陷的方法包括调整操作条件、检查设备及模具设计、更换原料等。
如何避免注塑件常见的缺陷产生,可以从以下几个方面进行改进:材料准备:设定适当的干燥条件,避免过长的干燥时间和过高的干燥温度,以免塑料内挥发物被驱离。
同时,根据产品需求选择适当的塑料材料,如高强度和热稳定性良好的塑料。
模具设计:改善模具排气系统,特别是在流动路径的末端和盲孔位置。
确保排气孔大小合适,结晶性塑料和非结晶性塑料的排气孔大小应有所区别。
注塑成型工艺参数对注塑件缩痕影响的研究

影 响 。 不 同 的工 艺 参 数 进 行 了分 析 , 定 出 用于 注 塑 成 型 的 较 合 适 的 工艺 参 数 。 研 究 结 果 表 明 : 体 温 度 、 具 温 度 的 对 确 熔 模
太多 , 设计 的效 率低 , 计 的 时 间周 期太 长 , 设 留给 制造
调 试 的时间太短 。设 计 过 程 中缺 乏 先 进 的技 术手 段 ,
对 产 品 、 具进行 分 析 、 拟 , 具 制 造 后试 模 的合 格 模 模 模
( . o g i uXix Go g h n ,S axn c t n l& T c nclC l g ,S axn 1 0 0,Chn ; 1 T n xn y n i n c e gXi h oigVo ai a o e h ia ol e h oig3 2 0 e ia
prc sig pa a ees wee o t n d. Th e ul fr s ac s o t tde r a ig m ett mp r tr o esn r m tr r baie e r s t o e e r h h w ha c e sn l e e au e, mo d tmpe au e s l e r t r
潼 塑 威 型 参 数 对 潼 塾 件 缩 疲 影 响 研 究
傅 建 钢 傅 晓锦 ,
( . 兴职业技 术 学院 通信 与信 息 工程 系 , 江 绍兴 3 2 0 ; 1绍 浙 10 0 2 上 海 电机 学 院 机械 学院 , 海 2 0 4 ;. . 上 0 2 5 3 绍兴文 理 学院 ,浙江 绍兴 3 2 0 ) 10 0
ABS注塑成型收缩率的几点关系

来源于:注塑塑料网/ABS注塑成型收缩率的几点关系塑料收缩率直接关系到制品的形状和尺寸精度。
塑料制品特性、模具设计、工艺条件控制等影响成型收缩率和后收缩的各因素,对注塑制品及其稳定性影响极大[门。
目前模具尺寸的设计通常运用公差带或平均收缩率的方法计算,模具在试模后,根据试制出的制品尺寸来修正模具,然而一些高硬度。
低粗糙度模具的表面尺寸修正起来相当困难,且费工费时,有时甚至无法修正,造成巨大的损失。
所以,要得到所需尺寸的精密注塑件,同时又能尽量减少对模具的修正,就需要充分了解成型收缩率随工艺条件的变化规律,预先精确测定成型收缩率。
(丙烯膨丁二惭苯乙烯)三元共聚物(ABS)塑料综合了丙烯睛的耐化学药品性、耐油性、刚度和硬度,丁二烯的韧性和耐寒性及苯乙烯的电性能,被广泛应用于汽车、电器仪表和机械工业中,是目前通用工程塑料中应用最广泛的品种之一[z]。
国外对塑料成型收缩率的研究开始得较早,且取得了比较丰富的研究成果「3-7],国内专门从事塑料成型收缩率研究的并不多[8-11]。
因此,笔者采用xsrn n oss-so标准测定了^ss塑料在不同工艺条件下注射模塑的成型收缩率,得出了ABS塑料的成型收缩率随工艺条件的变化规律,为制订合理的工艺条件进行正确的工艺控制和模具设计从而生产出合格尺寸的制品提供了重要依据。
一、实验部分(一)主要原材料ABS:IH-100,上海高桥石化公司。
(二)主要设备干燥料斗:FNH-A型,日本日永化工株式会社;模温调节机:NT-55型,日本日永化工株式会社;注塑机:PS40SESASE型,日本日精树脂l业株式会社;模具:按ASTM D 955-89制造,长条模、圆片模,自制。
(三)测试方法试样分别为长条门27.045 mm x 10•000 mm X3.200 mm)和圆片(o101.975 mm)。
测试时运用带百分表的靠模,精度为0.of mm,测试长条形试样在平行于流动方向及圆片形试样在平行和垂直于流动方向上的尺寸变化。
- 1、下载文档前请自行甄别文档内容的完整性,平台不提供额外的编辑、内容补充、找答案等附加服务。
- 2、"仅部分预览"的文档,不可在线预览部分如存在完整性等问题,可反馈申请退款(可完整预览的文档不适用该条件!)。
- 3、如文档侵犯您的权益,请联系客服反馈,我们会尽快为您处理(人工客服工作时间:9:00-18:30)。
注塑条件对制品成型的影响
1). 塑料材料
塑料材料性能的复杂性决定了注射成型过程的复杂性。
而塑料材料的性能又因品种不同、牌号不同、生产厂家不同、甚至批次不同而差异较大。
不同的性能参数可能导致完全不同的成型结果。
2). 注射温度
熔体流入冷却的型腔,因热传导而散失热量。
与此同时,由于剪切作用而产生热量,这部分热量可能较热传导散失的热量多,也可能少,主要取决于注塑条件。
熔体的粘性随温度升高而变低。
这样,注射温度越高,熔体的粘度越低,所需的充填压力越小。
同时,注射温度也受到热降解温度、分解温度的限制。
3). 模具温度
模具温度越低,因热传导而散失热量的速度越快,熔体的温度越低,流动性越差。
当采用较低的注射速率时,这种现象尤其明显。
`4). 注射时间
注射时间对注塑过程的影响表现在三个方面:
(1)缩短注射时间,熔体中的剪应变率也会提高,为了充满型腔所需要的注射压力也要提高。
(2)缩短注射时间,熔体中的剪应变率提高,由于塑料熔体的剪切变稀特性,熔体的粘度降低,为了充满型腔所需要的注射压力也要降低。
(3)缩短注射时间,熔体中的剪应变率提高,剪切发热越大,同时因热传导而散失的热量少,因此熔体的温度高,粘度越低,为了充满型腔所需要的注射压力也要降低。
以上三种情况共同作用的结果,使充满型腔所需要的注射压力的曲线呈现“U”形。
也就是说,存在一个注射时间,此时所需的注射压力最小。